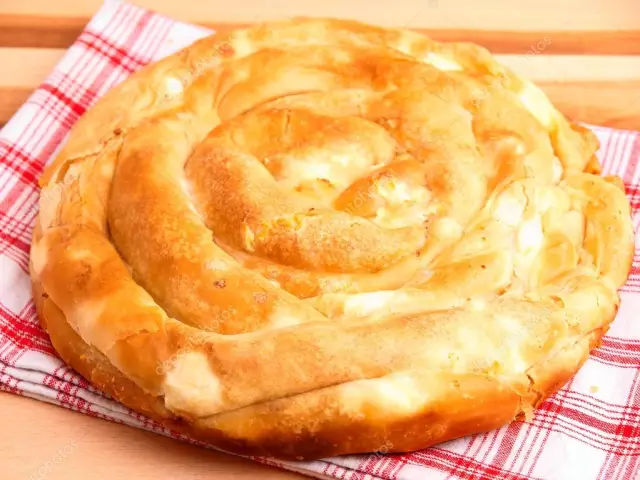
Inhaltsverzeichnis:
2025 Autor: John Day | [email protected]. Zuletzt bearbeitet: 2025-01-23 12:53
Dieses Instructable besteht hauptsächlich aus Schrottmaterialien und kostete mich etwa 20 australische Dollar von meiner lokalen Hardware für diese "einigen zusätzlichen Bits".
Das Prinzip dieser Konstruktion ist, dass als Blase ein Reifen verwendet wird und dieser über eine Kurbel (in meinem Fall handbetrieben mit der Option, motorisch angetrieben werden) auf und ab bewegt wird. Luft wird mit einfachen Einwegventilen durch den Reifen geleitet, während der Reifen mechanisch angehoben und expandiert wird Luft wird durch die Einwegventile (Einlassseite) in den Reifen gesaugt. Wenn die Kurbel den Reifen dann in eine gequetschte Position zwingt, wird die Luft durch das untere Einwegventil und zu Ihren Rohrleitungen gedrückt. Verwendungen für dieses Projekt könnten sein: Luft für eine Gießerei, Belüftung von Wasser, Füllen von Ballons, Pumpen von Wasser usw. Mit dieser Wiederverwendung eines Reifens können Sie ihn in beide Richtungen skalieren und großartige Ergebnisse erzielen, z. Ein kleiner Modellflugzeugreifen, der an einen 12-V-Motor angeschlossen ist, wäre ein großartiger Sauerstoffspender für Aquarien, oder eine größere LKW-Reifenversion könnte ein Aquakulturunternehmen belüftet halten. Diejenigen, die bereit sind, die Ventile zu wechseln, könnten auch Wasser pumpen. Auch wenn Sie dies langfristig verwenden möchten, empfehle ich die Verwendung der richtigen Buchsen- und Lagertechniken, da ich diese nicht für eine lange Verwendung konzipiert habe.
Schritt 1: Dinge, die Sie brauchen
DINGE, DIE SIE BENÖTIGEN Reifen und Schlauch, Schubkarrenrad in meinem Modell. Schrauben aus eigener Sammlung oder im Fachhandel, passender Schlauchanschluss, passend zu Ihrer Rohrleitung 3mm (1/8) Stahlblech, Unterlegscheiben, 40mm x 3mm Flachstahl ca. 1 Meter, Stahlrohr 75mm x 38mm ca. 2,5 Meter, Nieten und passende Unterlegscheiben, Silikondichtmittel, 70 mm ID-Rohr (50 mm lang) TEILE, DIE SIE HERSTELLEN Basis, fünf Ankerpunkte, mindestens drei Ventile, Kipphebel, Kurbel (optionaler Motorantrieb), Luftkammer, zwei Reifenankerplatten. WERKZEUGE Schweißer / oder technische Schrauben, wenn Sie es anders machen möchten, Bohrer, Feile, Karton, Schleifer, Schraubenschlüssel, 20 mm Bohrer mit reduziertem Schaft 12 mm Bohrer Klemme
Schritt 2: Vorsichtsmaßnahmen
Tragen Sie geeignete Sicherheitsausrüstung.
Feilen Sie scharfe Kanten nach dem Schneiden. Geschweißter Stahl ist heiß. Schützen Sie alle Gummiteile vor Schweißspritzern.
Schritt 3: Ankerpunkte
Schneiden Sie fünf Stücke von 40 mm x 3 mm Flacheisen mit einer Länge von 70 mm zu und bohren Sie ein Loch, das für Ihre Schrauben geeignet ist, ca. 10 mm von einem Ende. (Das Abrunden der Ecken an diesem Lochende ist ein schönes Finish).
Schritt 4: Die Basis
Für die BASE habe ich 38mm x 75mm verzinktes Rohr verwendet, dieses Stück ist die Mitte und lässt auch Luft zum Schlauchanschluss (Mittelrohr) strömen, der Reifen wird in mittlerem Abstand von beiden Enden platziert. Die zweite ist als T-Form mit dem Sockel (luftdicht) im 90 Grad Winkel zum mittleren Rohrende verschweißt und dient zur Stabilisierung der Pumpe. Das dritte Rohrstück ist am unteren Ende der T-Form angeschweißt (luftdicht) und unterstützt die Verankerungspunkte für den KIPPARM (siehe Schritt Nummer 7). Zum Verbinden und Verankern des Reifens. Bohren Sie ein 20 mm Loch in die Mitte des mittleren Rohres und schweißen Sie dann ein 50 mm langes Stück 70 mm Innendurchmesser senkrecht über das Loch (luftdicht). Für einen Platz für den Schlauchanschluss. Bohren Sie ein Loch in das mittlere Rohr in einem guten Abstand von der Stelle, an der sich der Reifen befinden wird und nicht vom vertikalen Rohr. Anschluss über Loch schweißen (luftdicht). Reifenverankerungsplatten: Schneiden Sie zwei Stücke von 3 mm Stahlplatte mit einem Durchmesser von 50 mm (2'') größer als der Innendurchmesser Ihres Reifens (der Teil, der die Felge verbindet). Ich habe an meinem Schubkarrenrad einen Durchmesser von ca. 230 mm gemessen, also habe ich einen Durchmesser von 280 mm geschnitten. (Verwenden Sie eine dickere Platte, wenn Sie größere Reifen verwenden) Nehmen Sie EINE der 3 mm Platten und bohren Sie ein zentrales 20 mm Loch und feilen Sie die Grate. Schweißen Sie diese Platte über das 70-mm-Innenrohr, das Sie an die Basis geschweißt haben. Luftdicht verschweißen und versuchen, die Dinge ziemlich zentral zu halten. Dies wird jetzt als BASISREIFENANKERPLATTE bezeichnet. Für die zweite Platte mit 280 mm Durchmesser. Einen ANKERPUNKT von SCHRITT 3 an die Mittellinie schweißen. Dies wird jetzt zur TOP-REIFENANKERPLATTE.
Schritt 5: Ventile
Ventile waren am schwierigsten zu konstruieren, da viele Optionen verfügbar waren, einschließlich des Kaufs einiger teurer Messingtypen (nicht schweißbar). Vielleicht kennen Sie diese Ventile auch als: Membranventile, Rückschlagventile, Klappenventile, Rückschlagventile. Diese Einwegventile verwenden ein Stück bewegliches Material als Ventil. Gummi in meinem Design (Leder oder Flachfederstahl würde funktionieren). Dieses Ventil wird in eine Richtung gegen die Dichtfläche gedrückt, wenn die Flüssigkeit versucht, durch das Ventil rückwärts zu fließen. Wenn der Druck auf der Einlassseite des Ventils höher ist als auf der Auslassseite, öffnet das Ventil, da es keine physische Barriere auf der Auslassseite gibt, die es geschlossen hält. Bei umgekehrtem und ausgangsseitig höherem Druck wird das Ventilmaterial gegen die Dichtfläche (kleinere Bohrung der KEEPER PLATE) gepresst, so dass die Flüssigkeit nicht durchfließen kann. AUSLASSVENTIL 1. Das Auslassventil in der Basis sollte sich in der Mitte des Reifens befinden. Markieren Sie diesen Punkt und bohren Sie ein 20 mm (3/4 Zoll) Loch, um raue Kanten abzufeilen. 2. Schneiden Sie 3 Stück Schlauchgummi ca. 70 mm² ab. Zwei für Einlassventile Ich fand, dass zwei auf der Einlassseite das Pumpen einfacher machten und es nicht notwendig war, zwei auf der Auslassseite zu benötigen. Markieren Sie diese in der Mitte mit einem 20mm runden Objekt. Ein hilfreicher Hinweis zum Zusammenbau der Ventilstücke ist die Markierung der Mitte dieses Gummistücks mit einem weißen Punkt (für Schritt 4). Schneiden Sie eine Hufeisenform um den 20 mm Kreis, den Sie markiert haben, siehe Foto 3 (der Außendurchmesser ist etwas größer als 20 mm und der Innendurchmesser etwas kleiner, testen Sie die Innengröße des Hufeisenausschnitts auf freie Bewegung im 20 mm Loch der Basis-REIFENANKERPLATTE) Hinweis, wenn die natürliche Krümmung des Gummis (Innenrohr) sich zurück zur Dichtungsoberfläche (nicht weg von) wölbt, schien eine bessere Abdichtung zu erzielen, flaches Gummi spielte keine Rolle, wie hoch es war. HALTERPLATTE / Loch in Oberflächengröße abdichten 3. 3 Stück 3 mm Stahlplatte 70 mm x 70 mm (zwei für Einlassventile) zuschneiden, ein 12 mm Loch in der Mitte bohren und entgraten. Dies ist ein kleineres Loch, so dass eine Dichtfläche für die Ventilklappe vorhanden ist, auf der sie abdichten kann. 4. Platzieren Sie den Gummi so, dass die Klappe mittig ist und sich über das 20-mm-Loch frei bewegen kann, dann legen Sie die Halteplatte vorsichtig, ohne den Gummi zu bewegen, mit einem weißen Punkt über den Gummi, um die Mitte auszurichten, Halten Sie den Halter fest (ich habe Multigrips verwendet) und bohren Sie vier Nieten ca. 12 mm von den Kanten der HALTERPLATTE entfernt. 5. Testen Sie das Ventil, indem Sie durch das 12-mm-Loch blasen, und versuchen Sie dann, Luft einzusaugen. Sollte dies nicht möglich sein, bedeutet dies, dass Ihr Ventil funktioniert. Siehe Bild 2, warten Sie auf das Abkühlen, bevor Sie versuchen:) EINLASSVENTIL (wie die Auslassventile, außer) 1. Einlassventile befinden sich auf der OBEREN REIFENANKERPLATTE 2. Stellen Sie sicher, dass die Ventile weit von der Dichtkante der Ankerplatte entfernt sind (siehe Foto.) 3. Wiederholen Sie die Schritte 4 und 5 von AUSLASSVENTIL
Schritt 6: DER Reifen
Ich musste den Reifen auf Undichtigkeiten überprüfen, als ich ihn von einem Schrotthaufen holte und hatte keine Ahnung, in welchem Zustand er war. Ich stellte fest, dass es viele Löcher gab. Silizium, was würden wir ohne Silizium machen. Ich verteile Silikon über den gesamten Innenreifen mit einer Dicke von ca. 1 mm mit einem Stück praktisch geformter Pappe. Lassen Sie die Silikonhaut darüber (trocken, aber weich unter der Haut). Drücken Sie eine Dichtlippe des Reifens über die BASISREIFENANKERPLATTE. Drehen Sie die Basis auf den Kopf, das Silikon und die Nieten an die Dichtlippe des Reifens, so dass es eine luftdichte Verbindung ist. Verwenden Sie eine Unterlegscheibe an den Nieten, um zu verhindern, dass sie durch die Gummireifenwand ziehen. Wiederholen Sie dies oben für die OBERE REIFENANKERPLATTE und stellen Sie sicher, dass Sie den geschweißten ANKERPUNKT so ausrichten, dass er mit dem MITTLEREN ROHR Ihrer Basis und später mit dem KIPPARM (nächster Schritt) für die Ungeduldigen verläuft. Sie können Ihren neuen Reifenbalg vorsichtig anheben und absenken, um zu sehen, wie alles läuft. Stören Sie das Silikon jedoch nicht zu sehr.
Schritt 7: Kipphebel
Um den Kipphebel herzustellen, schneiden Sie ein Stück 75 mm x 38 mm Rohr mit der gleichen Länge wie die Gesamtlänge der Basis.
Bohren Sie ein Loch durch die Länge von 75 mm und 20 mm vom Ende des gleichen Durchmessers, wie Sie Ihre ANKERPUNKTE gebohrt haben (dieses Loch ist der Drehpunkt für den KIPPARM). Holen Sie sich eine lange Schraube und befestigen Sie einen ANKERPUNKT auf beiden Seiten des KIPPARMS, platzieren Sie die ANKERPUNKTE über der VERTIKALEN BASIS ca. 20 mm nach unten. Klemmen und schweißen Sie die Punkte, wenn der KIPPARM mit der Mittellinie des Reifens ausgerichtet ist. Richten Sie einen weiteren ANKERPUNKT am KIPPARM über der Reifenmitte aus und schweißen Sie. Dieser ist für die VERBINDUNGSSTANGE zwischen dem KIPPARM und dem TOP-REIFENANKERPUNKT. Den letzten ANKERPUNKT mit dem gleichen Abstand wie zwischen dem KIPPARM-SCHWENKPUNKT und dem mittleren ANKERPUNKT an den KIPPARM anschweißen. Stellen Sie zwei VERBINDUNGSSTANGEN (2) 40 mm x 3 mm Flacheisen her. Um den Abstand der Lochmitten zu ermitteln, drücken Sie die OBERE REIFENANKERPLATTE etwa 5 mm von der BASISREIFENANKERPLATTE nach unten. Messen Sie dann mit einer Wasserwaage oben auf dem KIPPARM den Abstand zwischen dem mittleren ANCHOR POINT-Loch und dem Reifen ANCHOR POINT-Loch (evtl. benötigen Sie einen Helfer). Addieren Sie 40 mm zu Ihrem Maß als Gesamtlänge der VERBINDUNGSSTANGEN. Bohren Sie Löcher 20 mm von den Enden, um Ihren Schraubengrößen zu entsprechen.
Schritt 8: KURBEL
Kurbellänge, die Sie für Ihr Design erarbeiten müssen. Der Reifen muss sich dehnen und zusammenziehen können, ohne die beiden REIFENANKERPLATTEN zu berühren oder zu stark gedehnt zu sein, siehe KIPPHEBEL Schritt 7. Mit dem oberen KIPPHEBEL am Drehpunkt verschraubt und der mittleren VERBINDUNGSSTANGE befestigt. Drücken Sie den Kipphebel nach unten, bis sich die OBERE ANKERPLATTE auf der UNTEREN ANKERPLATTE befindet (quetschen Sie den Reifen platt), dann heben Sie ihn 5 mm (ca.) an. Messen Sie zwischen dem Boden und der Oberseite des KIPPHEBELS. Heben Sie den KIPPHEBEL an, um den Reifen so weit zu dehnen, dass eine weitere Dehnung bei normalem Pumpenbetrieb die Reifendichtungen brechen könnte. Subtrahiere den ersten Abstand vom zweiten Maß und dividiere durch 2 gleich dem Abstand zwischen dem Kurbelzapfen (einer auf die Scheibe geschweißten Schraube) und der Kurbelwelle. Ich habe mehr 78mm x38mm Rohr für die Unterstützung meiner Kurbel verwendet. Die Mittenhöhe des Kurbelzapfens und die Länge des Kurbelarms müssen sich in einem Abstand über der Basis befinden, damit Sie bei Verwendung der Option Handbetrieb nicht mit den Fingerknöcheln auf dem Boden knacken. Sie müssen keine runde Scheibe verwenden, wie ich es getan habe, mehr flacher Stab würde tun.
Schritt 9: Letztes Blaha
Schließen Sie einen Schlauch an, füllen Sie eine Wanne oder einen Eimer mit Wasser, legen Sie den Schlauch in Wasser und kurbeln Sie den Griff. Ich weiß, dass Sie diesen Schritt bereits übersprungen haben. Dieses Projekt wurde an einem Tag abgeschlossen, wie Sie vielleicht auf den Fotos gesehen haben. Ich hoffe, Sie genießen diese einfache Pumpe, die möglicherweise eine Antwort auf viele Probleme bietet. Fügen Sie Fett und Distanzscheiben um bewegliche Gelenke hinzu.