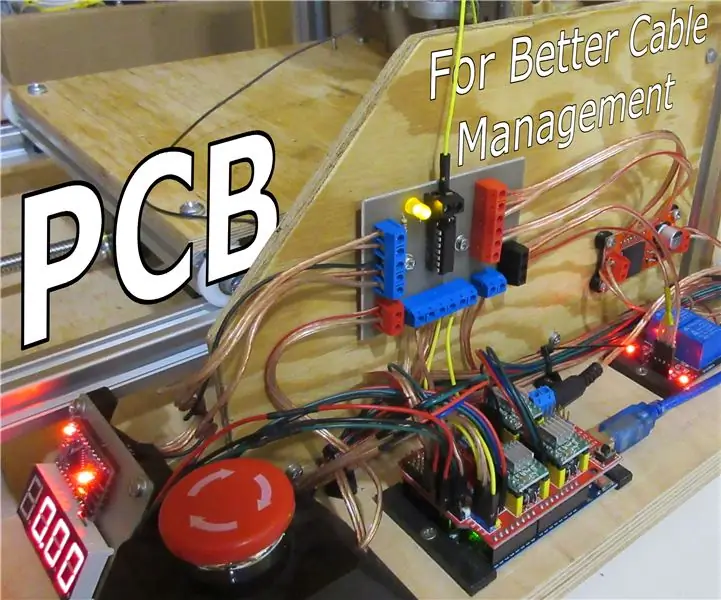
Inhaltsverzeichnis:
2025 Autor: John Day | [email protected]. Zuletzt bearbeitet: 2025-01-23 12:52
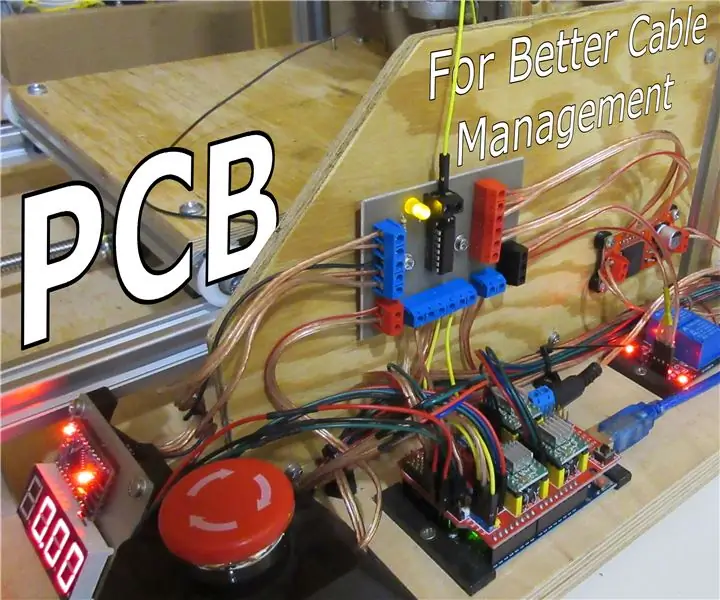
Vor einiger Zeit habe ich eine benutzerdefinierte Desktop-CNC-Fräse hergestellt. Seitdem habe ich es mit neuen Komponenten aufgerüstet. Letztes Mal habe ich ein zweites Arduino mit 4-stelliger Anzeige hinzugefügt, um die Drehzahl meiner Spindel mit der PID-Schleife zu steuern. Ich musste es mit 5 Drähten mit dem primären Arduino-Board verbinden, damit sie kommunizieren können. Aber bei meinem ersten Test habe ich einen Motorcontroller kaputt gemacht, also habe ich einen neuen, stärkeren gekauft. Es hatte auch 5 weitere Drähte, die ich anschließen musste. Zu diesem Zeitpunkt war der +5V-Pin auf der Hauptplatine in 4 separate Anschlüsse aufgeteilt und ich hatte einfach keine Lust, den Draht wieder aufzuteilen. Also habe ich etwas anderes gemacht.
Schritt 1: Skizzieren von Verbindungen
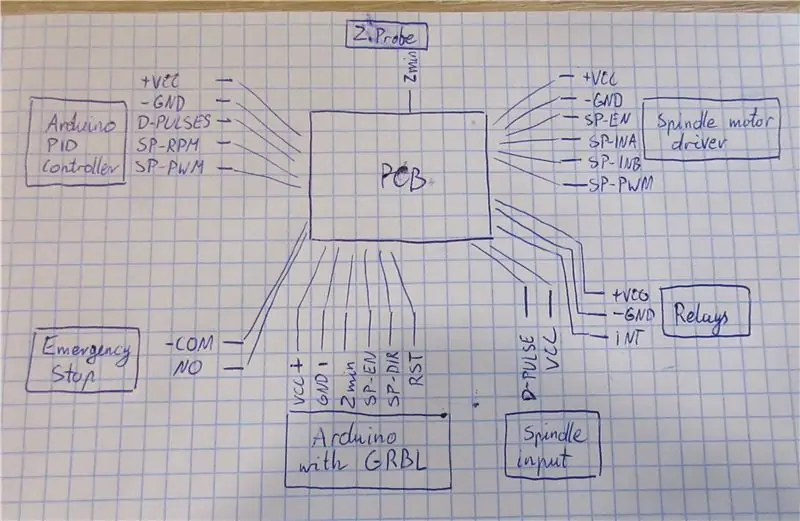
Ich habe alle benötigten Verbindungen skizziert (ohne Motor- und Endstoppkabel, da sie direkt zum GRBL-Controller und nirgendwo anders führen). Ich habe auch einige Änderungen an bereits bestehenden Verbindungen vorgenommen - der Not-Aus setzt jetzt auch den Haupt-Arduino zurück und verwendet nur den Schließerkontakt, wo zuvor sowohl NO als auch NC zur Steuerung eines Relais verwendet wurden. Mit dem neuen Motorcontroller wurde auch der Anschluss an Relais vereinfacht.
Schritt 2: Verbindungsprobleme
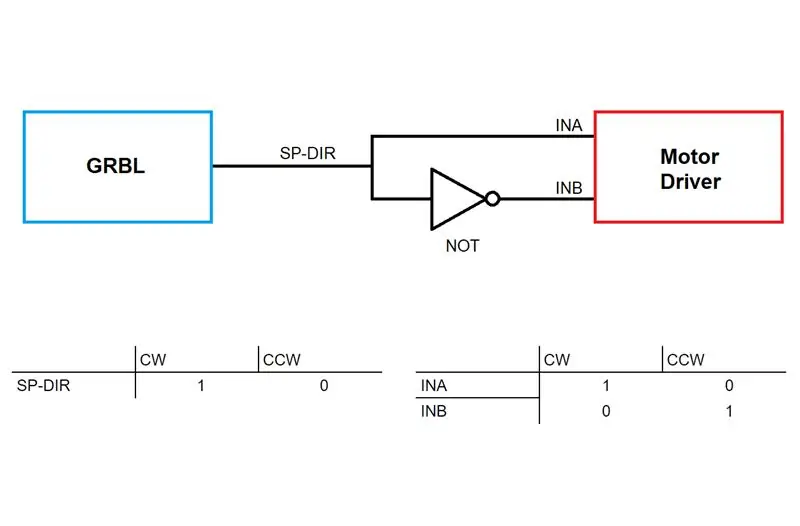
Der vorherige Motorcontroller, den ich verwendet habe, war eine einfache Platine mit Optokoppler und einem Mosfet. Es konnte die Spindel nur in eine Richtung drehen, so dass der Richtungsstift nicht verwendet werden musste. Neue ist etwas komplizierter. Es hat Pins namens INA und INB, und je nachdem, ob ich im Uhrzeigersinn oder gegen den Uhrzeigersinn drehen möchte, muss ich einen davon auf VCC ziehen. Es klingt nicht so kompliziert, das Problem ist, dass GRBL nur einen Pin namens SP-DIR (Spindelrichtungspin) hat, der für eine Bewegung im Uhrzeigersinn auf VCC und für eine Bewegung gegen den Uhrzeigersinn auf GND gezogen wird. Ich weiß nicht, ob dies in GRBL geändert werden kann (es ist ein bisschen zu kompliziert für mich), also habe ich dies mit einer anderen Methode gemacht.
Ich habe gerade ein NOT-Logikgatter in den Schaltplan eingefügt, das das SP-DIR-Signal invertiert und auf INB setzt. Daher ist, wenn der DIR-Pin hoch ist, INA auch hoch (sie sind miteinander verbunden) und INB wird auf niedrig (CW) invertiert, und wenn DIR niedrig ist, ist INA ebenfalls niedrig und INB ist hoch (CCW).
Schritt 3: Intelligentes, aber nicht so einfaches Design
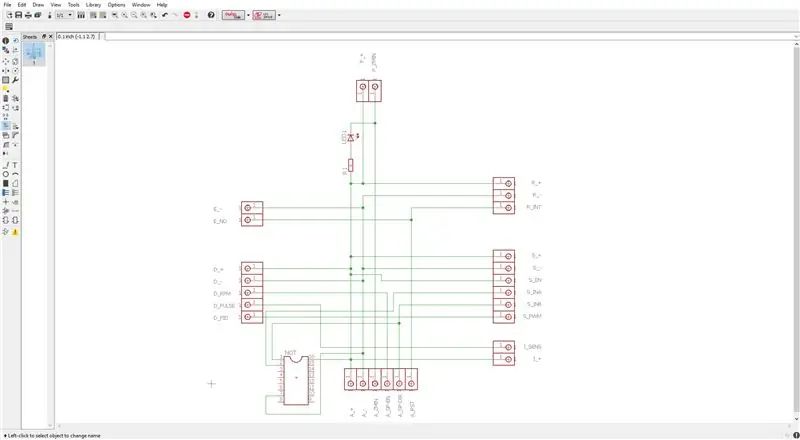
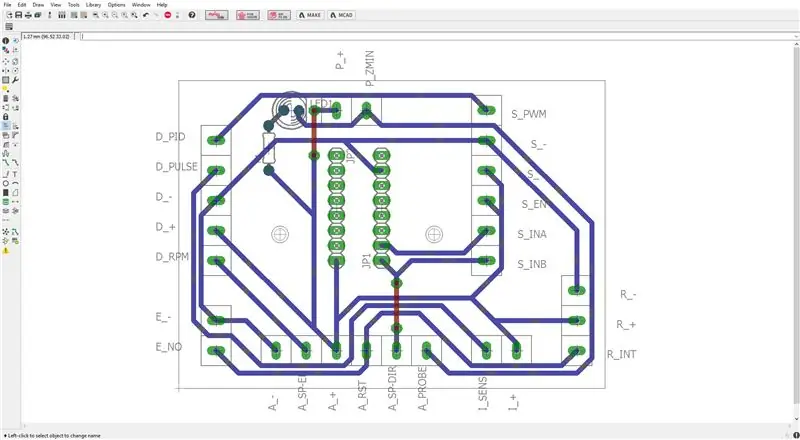
Dann habe ich in Eagle eine Platine entworfen, die alle notwendigen Verbindungen enthält. Aber bei so vielen Drähten war das nicht so einfach.
Zuerst habe ich eine benutzerdefinierte Eagle-Bibliothek für meine Klemmenblöcke erstellt. Es ist sehr einfach, es ist im Grunde nur ein normaler Stift, nur größer - 5,08 mm (0,2 ) Abstand.
Ich würde es auf der CNC fräsen und deshalb wollte ich, dass es ein einseitiges Brett ist. Aber mit 26 Klemmenblöcken und einigen internen Verbindungen zum Logikgatter war es eine schwierige Aufgabe, es zu entwerfen. Es könnte getan werden, aber mit vielen Überbrückungsdrähten. Das ist der Grund, warum alle meine Klemmenblöcke (in Eagle) nur ein einzelner Pin sind. Auf diese Weise kann ich sie im Board-Arbeitsbereich verschieben und die Verwendung von Überbrückungsdrähten vermeiden. Der Nachteil ist, dass die Position einiger Verbindungen zufällig erscheint. Unten sieht man zum Beispiel GND, dann SP-EN und dann VCC, was sehr ungewöhnlich ist. Aber auf diese Weise konnte ich die Anzahl der Überbrückungsdrähte auf nur 2 reduzieren und es ist für mich einfacher, die Leiterplatte herzustellen.
Auch die Namen der Klemmenblöcke sind speziell. Sie wurden gruppiert, so dass zum Beispiel A für Arduino steht, also sollten alle Schraubklemmen namens A_ auf der Unterseite der Platine platziert werden, da Arduino mit GRBL unter der Platine platziert ist.
Am Ende habe ich auch eine einfache LED hinzugefügt, um den Z-Sondenstatus anzuzeigen.
Schritt 4: Herstellung des Boards
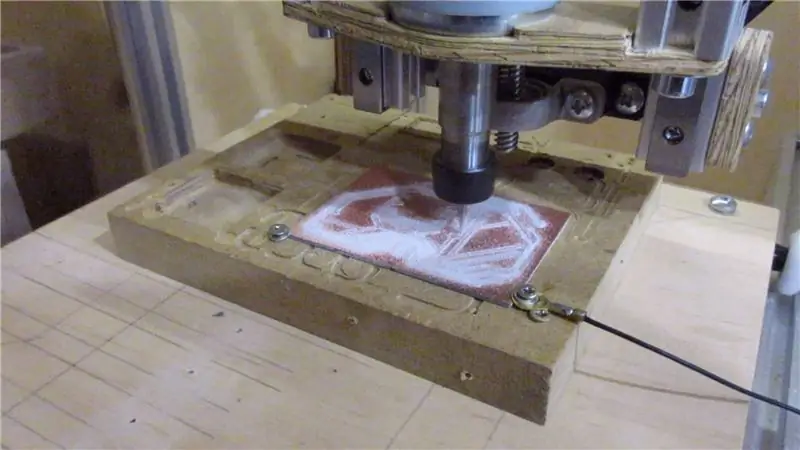
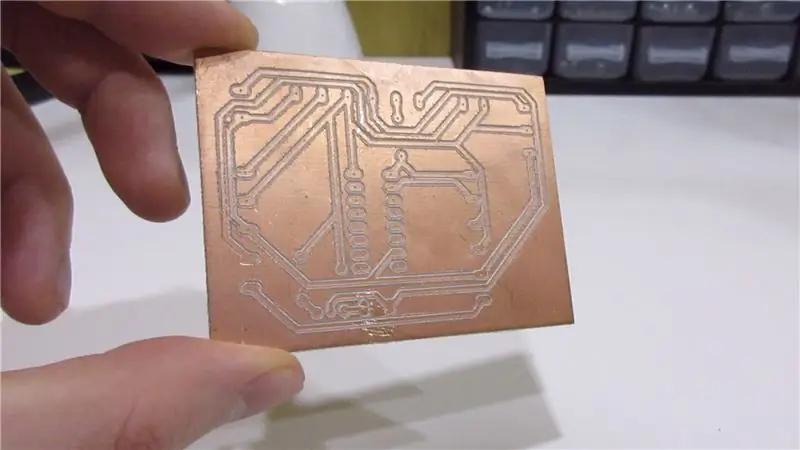
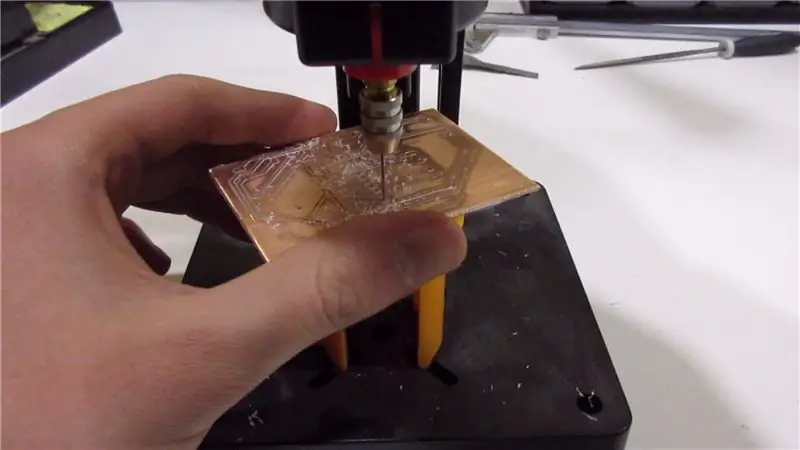
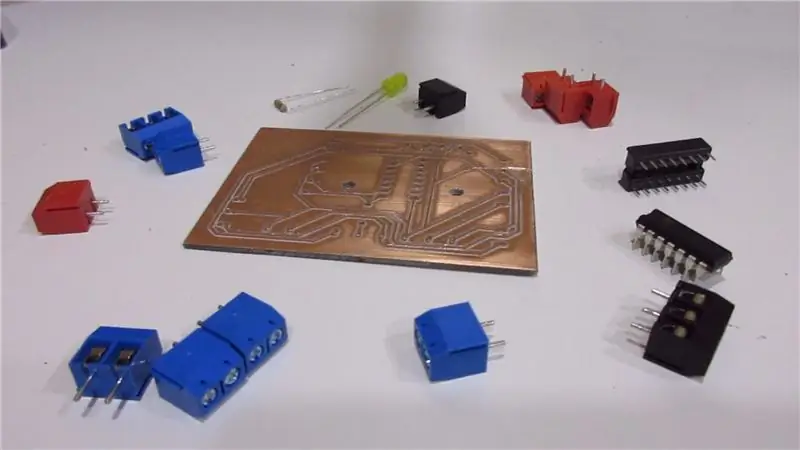
Wie ich schon sagte, habe ich die Platine auf meiner DIY-CNC gefräst, die Löcher gebohrt und alle Komponenten gelötet. Der Prozess war nichts Besonderes und machte PCB wie jedes andere.
Wenn Sie keine CNC haben, können Sie die Leiterplatte im Thermotransferverfahren herstellen oder bei einem professionellen Hersteller bestellen.
Vergessen Sie auch nicht, alle Verbindungen mit dem Multimeter zu überprüfen, um Fehler zu finden und zu beheben.
Schritt 5: Alles miteinander verbinden
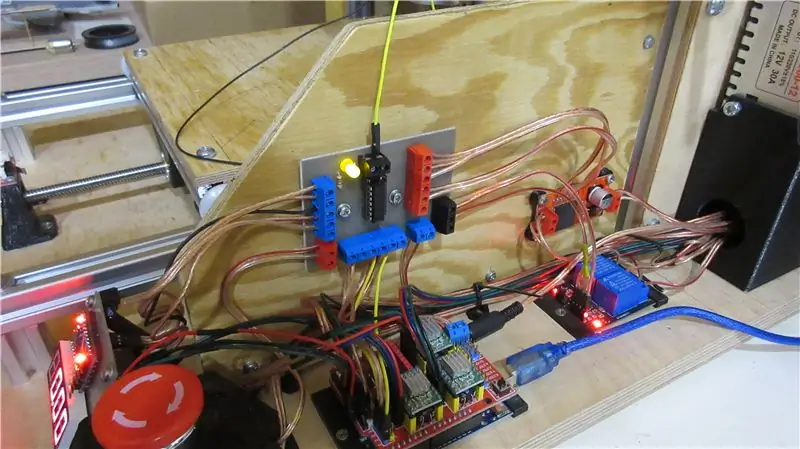
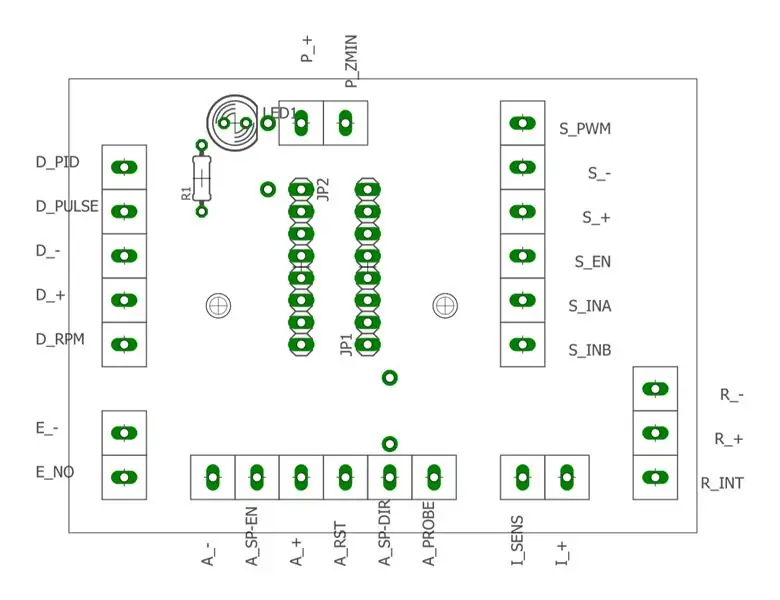
Einer der letzten Schritte bestand darin, die fertige Leiterplatte in die Maschine zu legen und alle Drähte anzuschließen. Ich habe einen kleinen Schaltplan gedruckt, der mir hilft, jeden Draht dort anzuschließen, wo er sein sollte. Nach nochmaliger Überprüfung der Anschlüsse war es bereit zum Testen!
Empfohlen:
DIY So zeigen Sie die Zeit auf dem M5StickC ESP32 mit Visuino an - Einfach zu tun: 9 Schritte
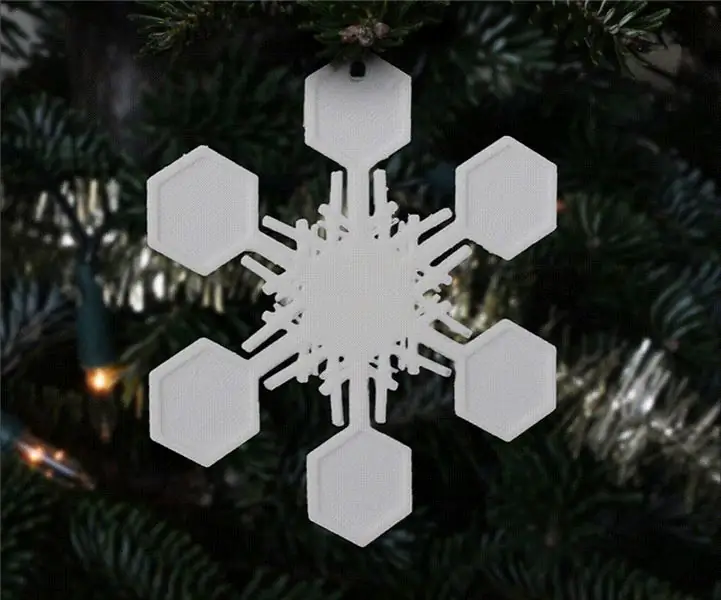
DIY So zeigen Sie die Zeit auf dem M5StickC ESP32 mit Visuino an - Einfach zu machen: In diesem Tutorial lernen wir, wie Sie den ESP32 M5Stack StickC mit Arduino IDE und Visuino programmieren, um die Zeit auf dem LCD anzuzeigen
So verbinden Sie die Android-Anwendung mit AWS IOT und verstehen die Spracherkennungs-API: 3 Schritte
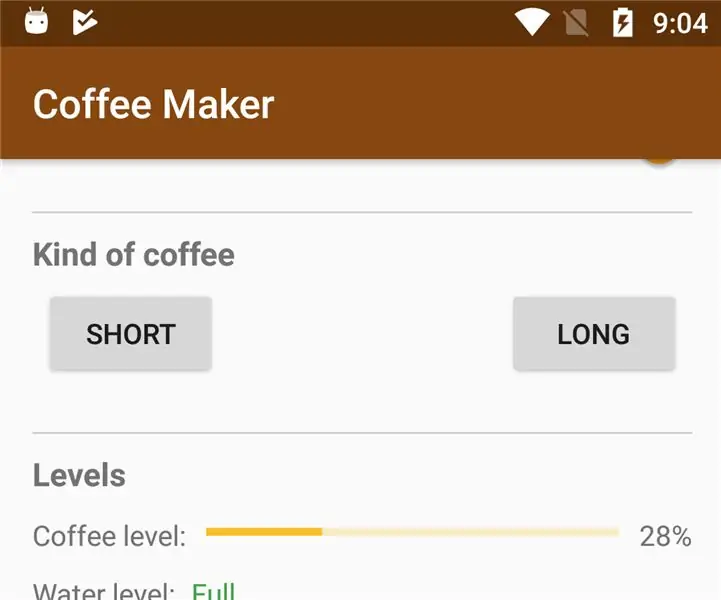
So verbinden Sie die Android-Anwendung mit AWS IOT und verstehen die Spracherkennungs-API: In diesem Tutorial erfahren Sie, wie Sie die Android-Anwendung mit dem AWS IOT-Server verbinden und die Spracherkennungs-API verstehen, die eine Kaffeemaschine steuert. Die Anwendung steuert die Kaffeemaschine über Alexa Sprachdienst, die c
Hilfreiche Hände beim Löten günstig machen – wikiHow
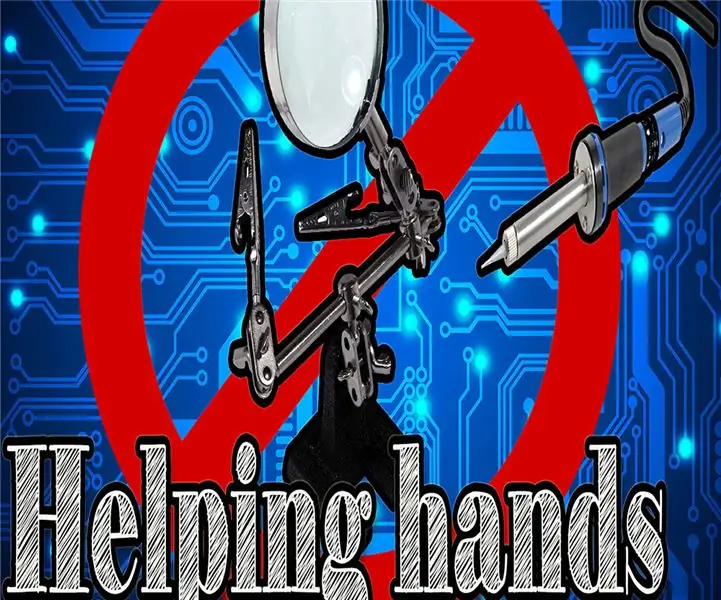
Wie man helfende Hände beim Löten billig macht: Wie man zu Hause eine helfende Hand zum Löten macht und sehr billig kann jeder es tun, wenn Sie Hilfe beim Löten haben möchten, machen Sie die dritte Hand super einfach
So beheben Sie das Problem beim Scrollen mit der Xiaomi-Maus – wikiHow
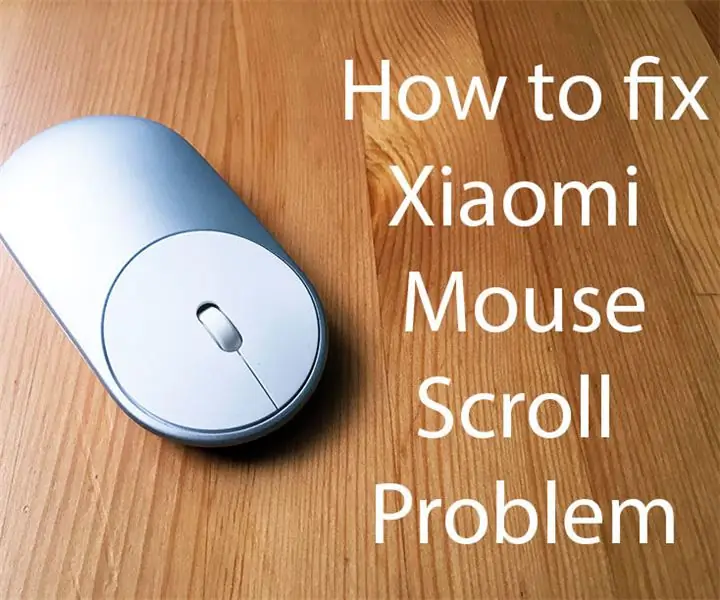
So beheben Sie das Xiaomi-Maus-Scroll-Problem: Wie bei jedem anderen Tool würde eine Computermaus aufgrund ihrer ständigen Verwendung irgendwann gewartet werden müssen. Die typische Abnutzung des Produkts führt dazu, dass es weniger effizient funktioniert als zu der Zeit, als es einst
So bauen Sie eine Uhr, die die Zeit an die Wand projiziert – wikiHow
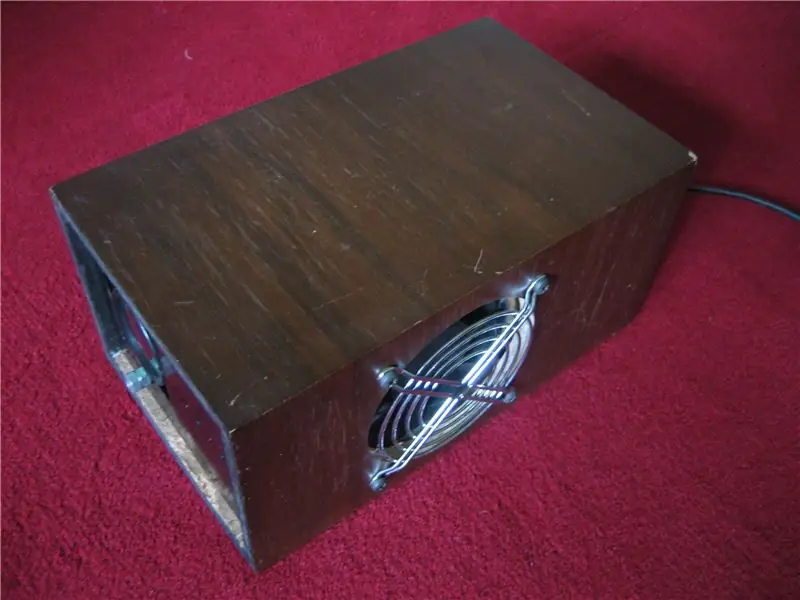
So bauen Sie eine Uhr, die Zeit an die Wand projiziert: Dieses Instructable zeigt Ihnen, wie Sie eine Projektoruhr bauen. Mit diesem Gerät können Sie die Zeit an die Wand projizieren. Basierend auf einem kleinen LCD-Wecker (nicht zu klein, sondern kann nicht projiziert und bearbeitet werden) ist dies eine gute Möglichkeit