
Inhaltsverzeichnis:
2025 Autor: John Day | [email protected]. Zuletzt bearbeitet: 2025-06-01 06:08
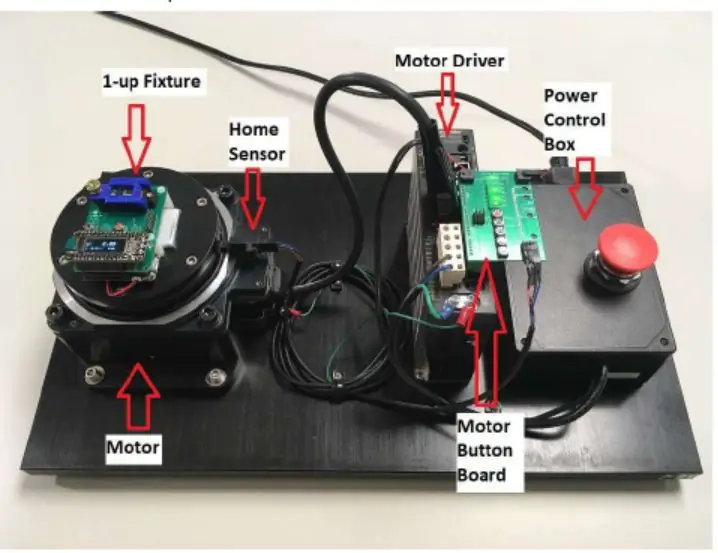
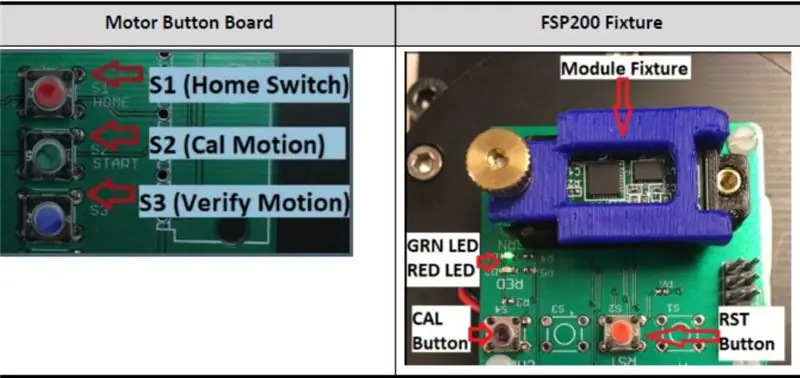
Der FSP200 ist ein Prozessor für 6-Achsen-Trägheitsmesseinheiten, der Kurs- und Richtungsausgaben bereitstellt. Es führt eine Fusion von Beschleunigungsmesser und Kreiselsensoren für einen stabilen und genauen Kurs und Richtung durch. Der FSP200 eignet sich für den Einsatz in Roboterprodukten wie Bodenreinigungsprodukten, Garten- und Rasenrobotern, Poolreinigern sowie im Gastgewerbe und im medizinischen Bereich. Assistent Roboter.
Hier stellen wir den Werkskalibrierungs- und F&E-Anwendungstestprozess der FSP200-Sensormodulfabrik von Shanghai Runxin Technology vor. Werkskalibrierung des FSP200-Moduls Das einfache Kalibrierungssystem besteht aus einem einzigen Satz von Vorrichtungen, Motoren, Motorantrieben, Ausgangspositionssensoren, Motortastenfeldern und Leistungssteuerkästen, wie in Abbildung 1 gezeigt.
Stellen Sie vor Beginn der Kalibrierung sicher, dass das einfache Kalibriersystem FSP200 waagerecht steht, wie in Abbildung 2 gezeigt.
Schritt 1: Kalibrierung starten: CAL-Taste drücken:
Die grüne LED beginnt zu blinken und zeigt damit an, dass sich das Modul im „Kalibrierungs“-Modus befindet.
Schritt 2: Bewegung kalibrieren (den Motor um 180 Grad drehen):
Drücken Sie S2 (grüne Taste) auf dem Motortastenfeld, um den Regler um 180 Grad gegen den Uhrzeigersinn zu bewegen. Warten Sie, bis sich der Motor um 180 Grad dreht, bevor Sie mit dem nächsten Schritt fortfahren.
Schritt 3: Schließen Sie die Kalibrierung ab:
Drücken Sie die CAL-Taste erneut, um den Kalibrierungsmodus zu beenden. Die Kalibrierungsergebnisse sehen den Status der roten und grünen LED-Anzeigen an: Wenn das Modul kalibriert ist, wird die grüne LED grün; Wenn die Kalibrierung des Moduls fehlschlägt, wird die rote LED rot.
Schritt 4: Überprüfen Sie die Kalibrierungsfunktion:
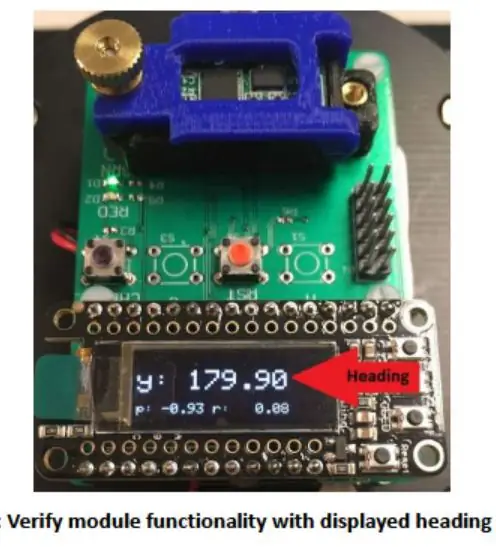
Drücken Sie die RST-Taste auf der FSP200-Befestigungsplatte, um sicherzustellen, dass das Display den Kurs des Moduls anzeigt (sollte in der Nähe von 0,00 Grad liegen). Drücken Sie die Taste S3 (blaue Taste) auf der Motortastentafel, um den Motor um 180 Grad im Uhrzeigersinn zu bewegen, und warten Sie, bis der Motor stoppt., sehen Sie sich das Display an. Stellen Sie sicher, dass die Kursablesung 180 +/- 0,45° (179,55 bis 180,45°) betragen sollte.
Wie in Abbildung 3 gezeigt:
Schritt 5: Kalibrierung ist nicht erfolgreich:
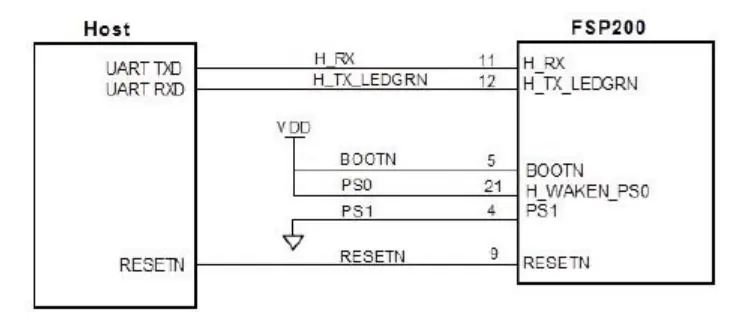
Leuchtet die rote LED „result“zu irgendeinem Zeitpunkt während des Kalibriervorgangs, liegt ein Fehler vor.
Wenn die Ergebnisanzeige nicht leuchtet, liegt möglicherweise ein Verbindungsproblem oder ein Problem mit der Stromversorgung vor. Die Modulkalibrierung schlägt fehl, wenn der im Überprüfungsschritt angezeigte Wert außerhalb des angegebenen akzeptablen Bereichs liegt.
Wenn einer dieser Fehler auftritt, entfernen Sie das Modul aus dem Gerät, installieren Sie es wieder am Gerät und versuchen Sie es erneut. Tritt der Fehler wiederholt auf, ist das Modul defekt; Wenn das Modul besteht, ist das Modul gut.
Beispiel für einen F&E-Anwendungstestprozess Um den besten Leistungseffekt der Kehrroboternavigation zu erzielen, müssen wir neben der Kalibrierung des Sensors selbst im Werk auch viele Fehlerreduktionstests in der Anfangsphase durchführen praktische Anwendung: durch maximale Umsetzung der empfohlenen Operation Fehlerquelle reduzieren und Kursfehlerschätzung verbessern.
Die Kursfehlerschätzung wird aufgrund der Zeitdauer, aufgrund von Gyroskop-Skalierungs- (oder -Empfindlichkeits-)Fehlern kurzfristig und des Gyroskop-Offsets (ZRO, Nullraten-Offset) variieren. Sie kann aus den folgenden Berechnungen gelernt werden: Kursfehlerschätzung = Skalenfehler x nicht entfernte Drehung + Nullratenversatz x Zeit
Der FSP200 bietet drei Schnittstellen: UART-RVC (PS0=0, PS1=1 wie in Abbildung 4) UART-SHTP (PS0=1, PS1=0) UART-RVC -DEBUG (PS0=0, PS1=0) Wenn Beim Entwerfen der Hardware ist es am besten, mit diesen drei Schnittstellenmodi kompatibel zu sein, um Umschalttests zu erleichtern.
Schritt 6:

Kehrmaschinen werden im UART-RVC-Modus in Massenproduktion hergestellt. Die Möglichkeit, die Modulleistung zu testen, ist interaktives Softwaretesten und nicht interaktives Testen. Im Folgenden werden die beiden folgenden Testverfahren zur Verbesserung von ZRO beschrieben:
1) HOST verwendet keinen interaktiven Softwaretestprozess wie folgt: 1: Nachdem der FSP200 RVC-Modus auf dem Testrack kalibriert wurde, verbinden Sie den seriellen Port mit dem PC und verwenden Sie motionStudio2, um die RVC-Daten zu öffnen. Diese Daten haben sich jedoch geändert, daher ist es am besten, den Anfang und 180 Grad nach dem normalen seriellen Port-Tool aufzuzeichnen. Kehren Sie zum Wert dieses Endpunkts von 0 Grad zurück (insgesamt 360 Grad), öffnen Sie dann das LOG und nehmen Sie den Wert der beiden hexadezimalen Daten RAW und dividieren Sie ihn durch 180 Grad. Wenn der Prozentsatz weniger als 25 % beträgt, ist die Anforderung erfüllt. Je kleiner desto besser.
(Die letzten Daten - die Anfangsdaten sind im Allgemeinen 0 nach dem Zurücksetzen) / 180 < 25%, was ein besseres Kalibrierungsmodul ist. 2: Wählen Sie 5 bis 10 Modulstücke mit dem kleinsten Fehler im visuellen Modul aus, legen Sie es auf die Kehrmaschine, fixieren Sie es mit Klebstoff, schalten Sie den RVC-Modus ein und laden Sie die Kehrmaschine eine halbe Stunde lang auf. Nachdem der Ladevorgang abgeschlossen ist, setzen Sie das Modul zurück und speichern Sie das Modul, um den aktuellen Temperaturmodus zu lernen. Wenn sich ein Modul nach dem Laden nicht abschaltet, können Sie ohne Zurücksetzen direkt auf der Kehrmaschine laufen. Führen Sie den nächsten Test durch.
3: Bewegen Sie die Kehrmaschine zum Standort, markieren Sie die Startposition, warten Sie 2 Sekunden, bis das Modul eingeschaltet ist, und schließen Sie das Modul an den Computer an. Verwenden Sie motionStudio2, um die RVC-Echtzeitdaten zu öffnen, lassen Sie den Sweeper 20 Minuten lang die Wortleitung durchlaufen, halten Sie dann an und gehen Sie zurück, um aufzunehmen. Position, RAW-Winkel anzeigen, 20-Minuten-Durchschnittsfehler berechnen. Setzen Sie dann das Modul zurück und speichern Sie die vom Modul gelernten Daten für nur 20 Minuten.
4: Ändern Sie die PS1 und PS0 des Moduls, nachdem Sie den SHTP-Modus gelernt haben, verbinden Sie sich mit dem Computer, führen Sie „sh2_ftdi_logger.exe test.dsf --raw --calibrated --uncalibrated --mode=all“aus?, und extrahieren Sie die DSF-Datei zur Analyse. Überprüfen Sie den tatsächlichen DCD-Testmodulfehler. 5: Nummerieren Sie das Modul, notieren Sie den Fehler und wechseln Sie das Modul in den RVC-Modus. Je kleiner der Fehler ist, desto besser ist die Leistung des Moduls. Das Modul mit guter Leistung wird ausgewählt, um in die Reinigungstestphase der Kehrmaschine einzutreten, und dann den Modulkonsistenztest, Hoch- und Niedertemperaturtest, beurteilen Die Gesamtwirkung des Moduls, dynamische Kalibrierungswirkung bei Temperaturänderungen.
2) HOST verwendet den interaktiven Softwaretestprozess wie folgt:
1: Nach Erhalt des werkseitig kalibrierten Moduls muss der RSP200 auf den RVC_Debug PS0=0, PS1=0 Modus eingestellt werden. Verbinden Sie über die PC-Software ftdi_binary_logger_RVC_Debug die serielle Schnittstelle des Moduls, um die LOG. BIN-Daten der Kehrmaschine für 2 bis 3 Minuten zu erhalten. Die Kehrsoftware muss die lokale Statik so einstellen, dass nur die größte Lüfter- und Walzenbürstenaktion geöffnet wird. Die LOG. BIN-Daten werden analysiert, um den nachfolgenden HOST zu beurteilen. Wie viel Zeit setzt die Endsoftware ein, um den dynamischen Kalibrierungsbefehl auszuführen.
2: Es gibt vier Arten von Benachrichtigungen für die erwartete Bewegung des Geräts, die vom Host an den FSP200 gesendet werden: 0 ist der vom Sensor-Hub eingenommene Anfangszustand, 1 ist statisch ohne Vibration, 2 ist eine statische Bürstenrollvibration und 3 ist normale Reinigung. Jedes Mal, wenn ein Zustand umgeschaltet wird, wird ein entsprechender Statusbefehl an den FSP 200 gesendet und die Rückkopplungsinformationen des FSP 200 werden gelesen, um zu bestimmen, ob der dynamische Kalibrierungsbefehl ausgeführt werden soll. Nachdem die Software eingerichtet wurde, wird die Flugleine des FSP200-Moduls (VCC, GND, RX, TX) an die serielle Schnittstelle des PCs angeschlossen. Es ist zu beachten, dass das Modul in die Maschine geladen werden muss, um es zu reparieren. Schalten Sie den Computer ein und schalten Sie die ftdi_binary_logger_RVC_Debug-Software ein, um die Kehrmaschine vom Anfang bis zum Ende des Reinigungsbereichs zu bewegen. Die Umsetzung der Bewegungsdaten wird automatisch als LOG. BIN-Datei gespeichert und die LOG. BIN-Datei wird verwendet, um zu analysieren, ob die interaktiven Softwareeinstellungen auf der HOST-Seite korrekt sind.
3: Wenn die interaktive Software richtig eingestellt ist, schalten Sie den FSP200 RVC-DEBUG-Modus auf den RVC PS0=0, PS1=1-Modus, führen Sie mehrere Maschinenreinigungstests durch, zeichnen Sie den Maschinenbetrieb auf 1 Stunde Positionswinkelfehler, je kleiner der Fehler, die Modulleistung Je besser, der Modulkonsistenztest, Hoch- und Niedertemperaturtest, beurteilen die Gesamtwirkung des Moduls, dynamische Kalibrierungswirkung bei Temperaturänderungen.
Empfohlen:
Entwicklung des Drivemall-Boards: 5 Schritte
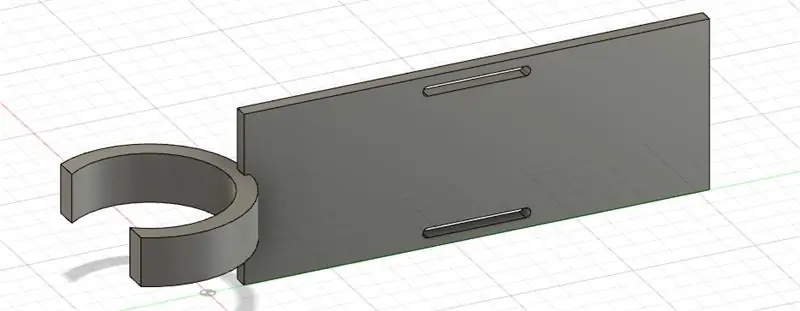
Entwicklung des Drivemall Boards: In diesem Tutorial sehen wir die grundlegenden Schritte zum Erstellen eines benutzerdefinierten Arduino-Boards. Die verwendete Software ist KiCad für das Boarddesign und die Arduino IDE für das Erstellen und Laden der Firmware für das Board
Installieren des Windows-Subsystems für Linux (WSL): 3 Schritte

Installieren des Windows-Subsystems für Linux (WSL): Diese Anleitung soll Benutzern helfen, das Windows-Subsystem für Linux auf ihrem Windows 10-Computer zu installieren. Die spezifische Linux-Distribution, die dieser Befehlssatz verwendet, heißt Ubuntu. Schauen Sie hier für eine Übersicht über die verschiedenen Linux
Kennenlernen des "Professional ILC8038 Function Generator DIY Kit": 5 Schritte
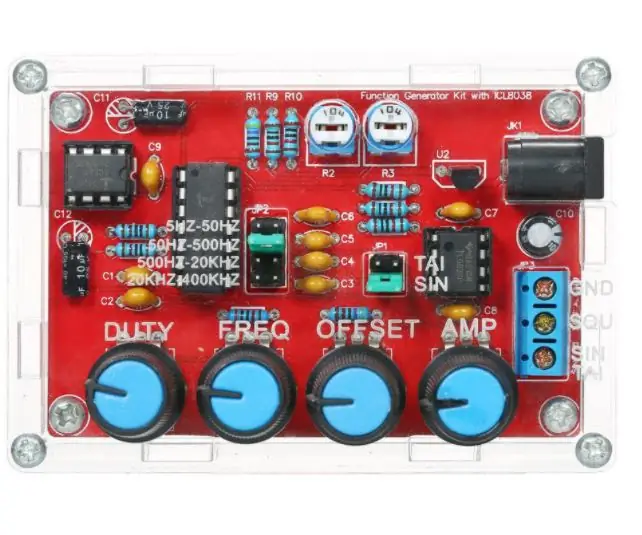
Kennenlernen des "Professional ILC8038 Function Generator DIY Kit": Auf der Suche nach neuen Elektronikprojekten bin ich auf ein süßes kleines Funktionsgenerator-Kit gestoßen. Es wird als „Professional ILC8038 Function Generator Sine Triangle Square Wave DIY Kit“bezeichnet und ist bei einer Reihe von Anbietern erhältlich
Überprüfung des JDM-Programmierers: 9 Schritte
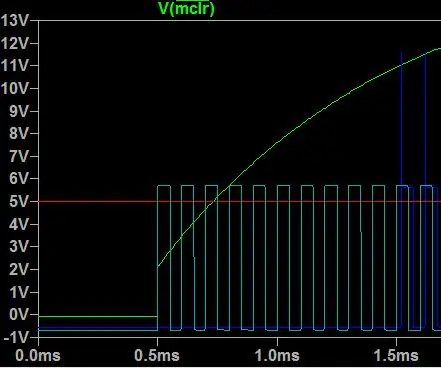
JDM Programmer Review: JDM ist ein beliebter PIC-Programmierer, da er einen seriellen Port, ein Minimum an Komponenten und keine Stromversorgung verwendet. Aber es gibt Verwirrung da draußen, mit vielen Programmiervarianten im Netz, welche funktionieren mit welchen PICs? In diesem „Instru
Wie man eine Babygewichtsmaschine mit Arduino Nano, HX-711 Wägezelle und OLED 128X64 herstellt -- Kalibrierung des HX-711: 5 Schritte
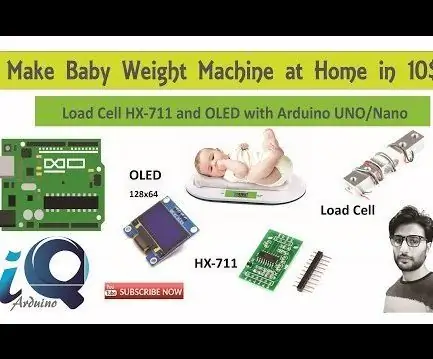
Wie man eine Babygewichtsmaschine mit Arduino Nano, HX-711-Wägezelle und OLED 128X64 herstellt || Kalibrierung von HX-711: Hallo Instructables, vor wenigen Tagen wurde ich Vater eines süßen Babys?. Als ich im Krankenhaus war, stellte ich fest, dass das Gewicht des Babys so wichtig ist, um das Wachstum des Babys zu überwachen. Also ich habe eine Idee? um eine Babygewichtsmaschine von meinem Selbst zu machen. In diesem Instructable ich