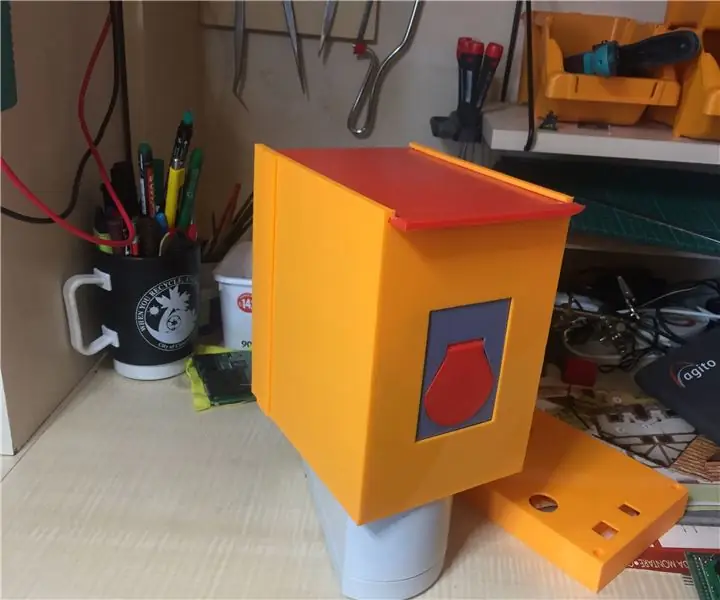
Inhaltsverzeichnis:
2025 Autor: John Day | [email protected]. Zuletzt bearbeitet: 2025-01-23 12:52
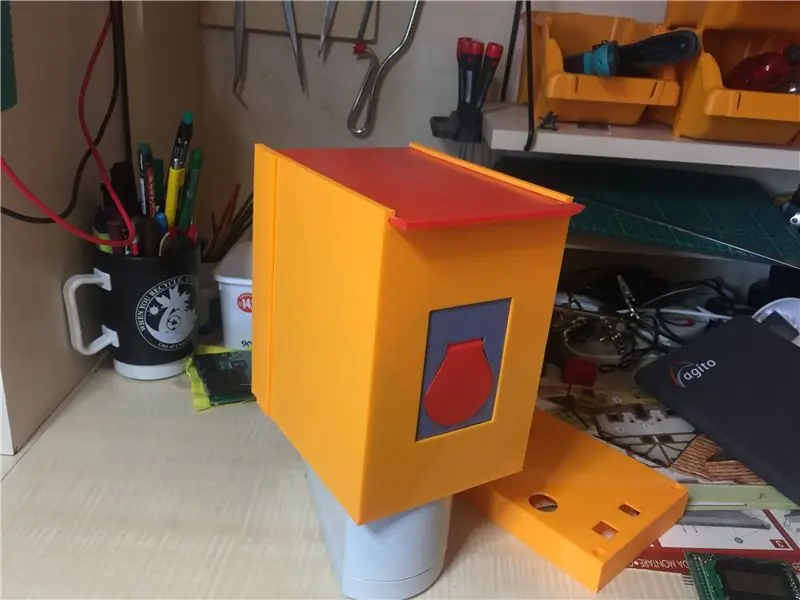
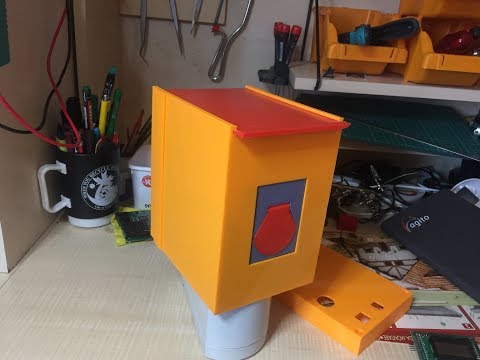
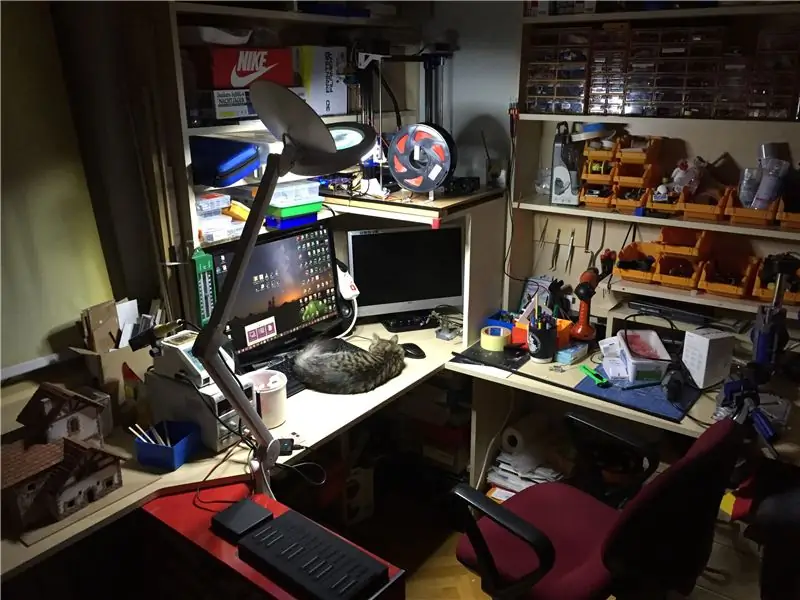
Fusion 360-Projekte »
Wenn Sie die Futtermenge, die Ihre Katze frisst, nicht kontrollieren, kann dies zu Überernährung und Übergewicht führen. Dies gilt insbesondere, wenn Sie nicht zu Hause sind und Ihrer Katze zusätzliches Futter hinterlassen, das sie nach ihrem eigenen Zeitplan aufnehmen kann. Manchmal stellen Sie vielleicht fest, dass Sie vergessen, ihr Futter rechtzeitig zu geben, und es unmöglich ist, nach Hause zurückzukehren.
Der automatische Diy-Katzenfutterspender kann zu jeder von Ihnen voreingestellten Zeit eine präzise Menge an Trockenfutter bedienen und ausgeben und kann mit Ihrem Mobiltelefon überall auf der Welt gesteuert werden.
Dieses Projekt ist ein komplettes Lernprojekt vom 3D-Druck bis zum Design in fusion360, von der Arduino-Programmierung bis zu den IOT-Grundlagen, vom Elektronikdesign in Eagle bis zur DIY-zweiseitigen Leiterplattenproduktion.
Hauptkapitel dieses anweisbaren sind
Workshop: Dieser Teil steht nicht in direktem Zusammenhang mit der eigentlichen Produktion, kann aber Leser mit kleinen Immobilien begeistern. Alle Designs, 3D-Druck, PDB-Produktion, Prototypen, Elektronikdesign und Fertigung werden in einer 2x2m großen Werkstatt durchgeführt.
Prototypen: Perfektes Design ist kaum zu erreichen. Jede -fehlgeschlagene- Design-Iteration bringt jedoch neue Ideen, löst Probleme und hebt Design auf ein höheres Niveau. Obwohl ein Befehlssatz normalerweise keine fehlgeschlagenen Versuche enthält, habe ich sie kurz aufgenommen, weil sie den Fortschritt und die Gründe für das endgültige Design zeigen.
Mechanische Konstruktion: Konstruktion von Mechanik und Behälter.
Elektronikdesign: Dieses Projekt basiert auf dem Arduino Mega Board. Ein Netzteil, eine Uhreinheit, eine Gleichstrommotorsteuereinheit und eine ESP8266-WLAN-Einheit sind auf einer speziell entwickelten Leiterplatte montiert. Hier finden Sie verwandte Instructable
Programmierung: Einige grundlegende Arduino-Programmierung. Ein bisschen ESP8266 Programmierung. Mit Hilfe von Arduino und esp8266 wurde ein kleiner Webserver erstellt.
Produktion: 3D-Druck aller von fusion360 entworfenen Teile und deren Montage. Die meisten Teile sind 3D gedruckt. außer Plastik gibt es eine Metallstange und mehrere Metallschrauben. Rest ist Elektronik und ein Gleichstrommotor.
Schritt 1: Werkstatt
Der Workshop enthält alle notwendigen Werkzeuge für die Herstellung elektronischer Schaltungen, die Leiterplattenherstellung, den 3D-Druck, die Modellmalerei und einige andere kleine Produktionsarbeiten. Es gibt einen Windows-Desktop-Computer, der an einen 3D-Drucker angeschlossen ist und auch zum elektronischen Musikmachen verwendet wird.
Natürlich ist mehr Platz für einen Bastler immer besser. Eine dichte Platzierung von Werkzeugen und einige clevere Tricks wie das Platzieren von 3D-Druckern über den Computermonitoren können jedoch einen praktikablen und angenehmen Arbeitsplatz schaffen.
Obwohl ein Workshop möglicherweise nie der direkte Teil eines Instructable ist, ist es hier als Hauptphase des Prozesses erwähnenswert.
Schritt 2: Prototypen
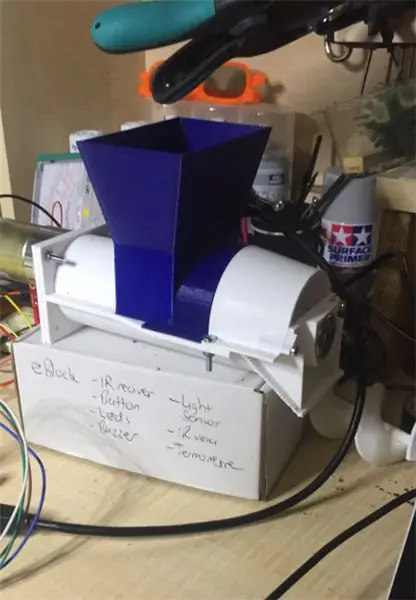
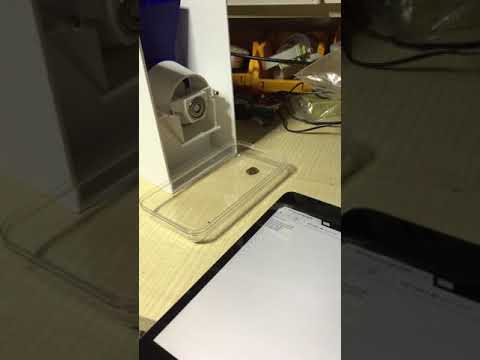
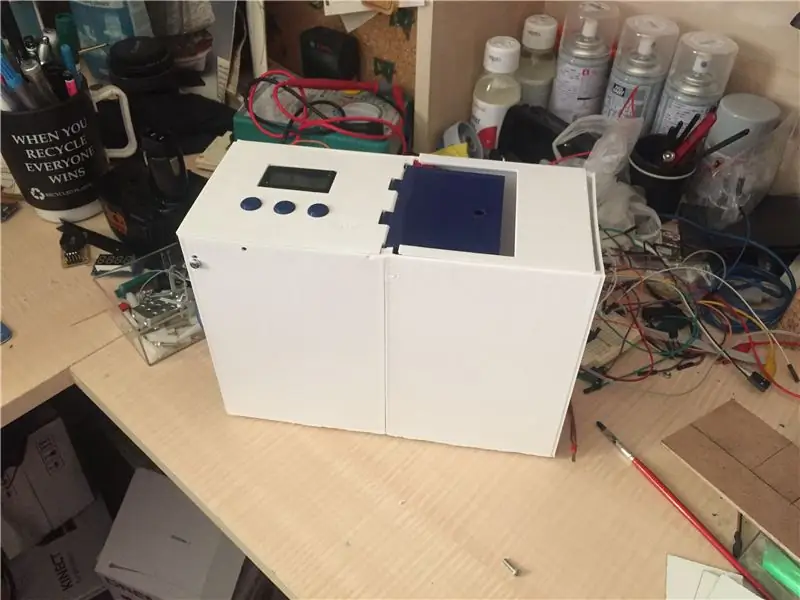
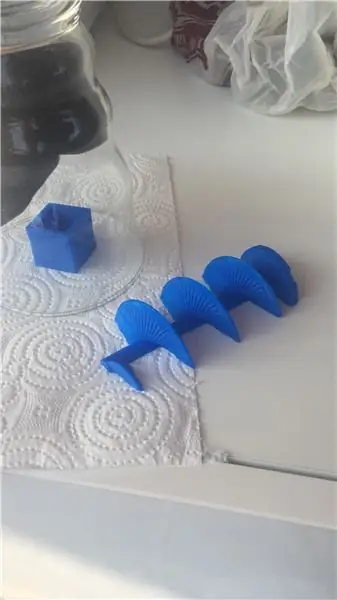
Die Dauer dieses Projekts wurde völlig unterschätzt. Es begann mit einer Schätzung von drei bis fünf Wochen. Es wurde in mehr als 40 Wochen fertiggestellt. Da ich keine kontinuierliche Zeit für dieses Projekt investieren konnte, kann ich nicht sicher sein, wie viel Zeit für das Projekt aufgewendet wurde, aber ich bin mir sicher, dass jeder Teil dieses Projekts mehr als erwartet gedauert hat.
Ich habe viel Zeit mit Prototypen verbracht.
Archimedesschraube
Das Prototyping begann mit Archimedes-Schrauben. Dies war auch mein erstes Fusion 360-Projekt. Ich habe mindestens 8 verschiedene Schrauben hergestellt und gedruckt, während ich die großartige Software namens Fusion 360 gelernt habe. (Fusion 360 ist eine kostenlose Software für Bastler und während Sie ziemlich anspruchsvolle Dinge machen können, ist die Lernkurve nicht so steil) Die ersten wurden von der Mitte in zwei geschnitten. Ich konnte keine Möglichkeit finden, ein vertikales Stück Schraube in 3D zu drucken. Nachdem ich zwei Hälften gedruckt hatte, klebte ich sie zusammen, was eine sehr ineffiziente und stielige Art ist, eine Archimedes-Schraube herzustellen. Dann wurde mir klar, dass sich die vertikale Druckqualität verbessert, wenn ich dem Drucker "Fan Ducks" hinzufüge. Es gibt viele verschiedene Arten von "Fan-Enten", also musste ich durch Versuch und Irrtum die beste Kombination finden. Schließlich landete ich eine fast perfekte Archimedes-Schraube, die als ein Stück gedruckt wurde.
Futterbehälter
Eine weitere Herausforderung war die Gestaltung des Futterbehälters. Flüssigkeiten können problemlos durch die Schnecke gefördert werden. Feste Materialien wie Trockenfutter für Katzen waren jedoch aufgrund von Marmeladen ein Problem. Ich habe versucht, einen Sicherheitsraum zu schaffen, um Staus zu vermeiden, und habe auch festgestellt, dass die Hinzufügung der Rückwärtsbewegung für jede Vorwärtsbewegung der Schraube die Staus erheblich verringert. Die Halbrohrform des endgültigen Designs und die softwaregesteuerte Rückwärtsbewegung beseitigten das Risiko eines Verklemmens vollständig.
Die Kiste
Zu Beginn des Projekts habe ich die ganze Box im Drucker ausgedruckt. Da die Größe des Druckers kleiner war als die Größe des Kartons, musste ich ihn in Stücke teilen, was den Karton sehr schwach und hässlich machte. Dann dachte ich an eine Holzkiste. Die Wände des zweiten Prototyps waren aus Holz. Einige Produktionsschwierigkeiten (ich hatte keinen geeigneten Platz und keine geeigneten Werkzeuge zum Schneiden und Umformen von Holz) Ich beschloss, die vollständig bedruckte Box für den dritten Prototyp (oder das endgültige Design) zu überdenken. Ich habe das Design effizienter und kleiner gemacht, damit ich es als ein Stück drucken konnte. Theoretisch wurde dieser Ansatz bearbeitet. In der Praxis nimmt das Drucken großer Objekte zu viel Zeit in Anspruch und jedes Problem mit dem Drucker kann das Endprodukt jederzeit sogar am 14. zerstören. Stunde des Drucks. In meinem Fall musste ich den Druck stoppen, bevor er fertig war, und musste fehlendes Segment als zusätzliches Teil entwerfen und drucken. Für den nächsten Prototyp überlege ich, Plexi für die Wände der Box zu verwenden.
Arduino
Ich habe mit Uno angefangen. Es war kleiner und sah für meine Zwecke ausreichend aus. Allerdings habe ich die Komplexität der Softwareentwicklung unterschätzt. Uno hat nur einen seriellen Ausgang und da ich diesen Ausgang für esp8266-Kommunikationen verwendet habe, hatte ich keinen Debug-Port zum Protokollieren von Variablen usw. und es stellte sich heraus, dass es ohne Echtzeit-Debugging fast unmöglich war, selbst einen kleinen Webdienst zu programmieren. Ich bin auf Arduino Mega umgestiegen. (was das Design der Box verändert hat)
Anzeigen
Während der Entwicklung des Projekts habe ich fast alle Arten von Displays auf dem Markt ausprobiert, einschließlich eines kleinen Oled-Displays. Jeder von ihnen hatte Vor- und Nachteile. Oled war nett, sah aber klein aus und war im Vergleich zum Gesamtdesign teuer. 7-Segment-LED-Displays waren hell, aber wenig vorhanden, wenig Informationen. Also habe ich für das endgültige Design ein 8x2-LCD-Display verwendet. Die zukünftigen Designs enthalten möglicherweise kein Display oder ein größeres Display, das gut aussieht.
Tasten
In den ersten Prototypen habe ich drei Tasten zur Steuerung des Geräts verbaut. Dann entschied ich mich, sie in den folgenden Designs nicht zu verwenden, da der Zusammenbau Zeit in Anspruch nimmt, ich sie nicht stabil genug machen konnte und sie die Benutzerfreundlichkeit des Geräts zusätzlich komplex machten.
Elektronik-Prototypen
Ich habe mehrere Elektronik-Prototypen gemacht. Einige von ihnen waren auf dem Steckbrett, einige auf einem Kupfer-Steckbrett. Für das endgültige Design habe ich eine benutzerdefinierte Leiterplatte mit einem modifizierten 3D-Drucker erstellt. (Hier ist das instructable für dieses Projekt)
Schritt 3: Entwerfen Sie die Kunststoffteile
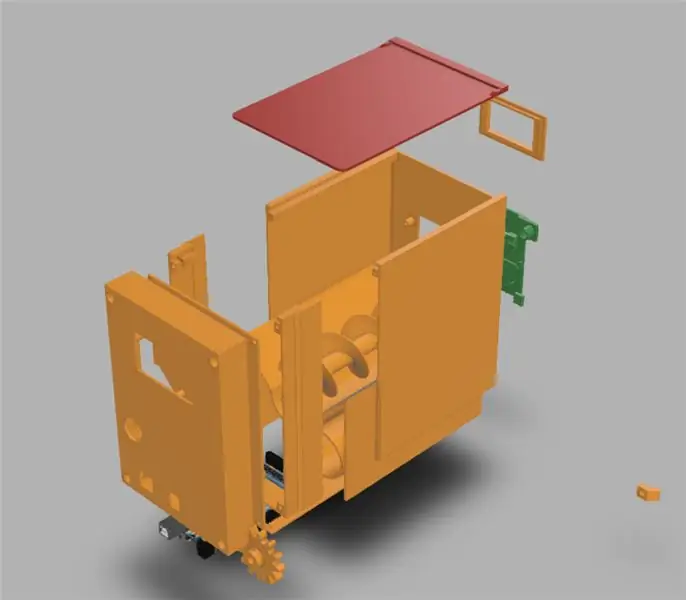
Sie können das Design aller 3D-Teile in diesem Dingverse-Link finden.
Sie erreichen das Fusion 360-Design auch unter:
Schritt 4: Drucken Sie die Teile
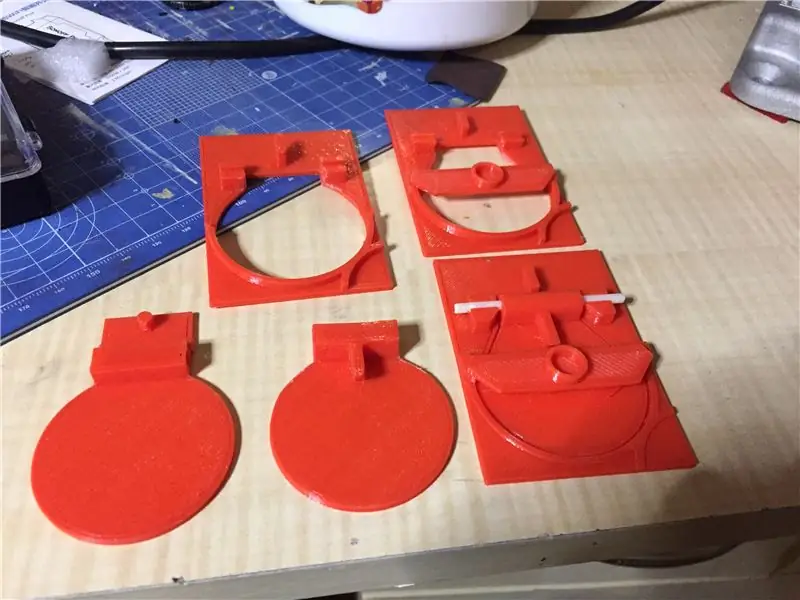
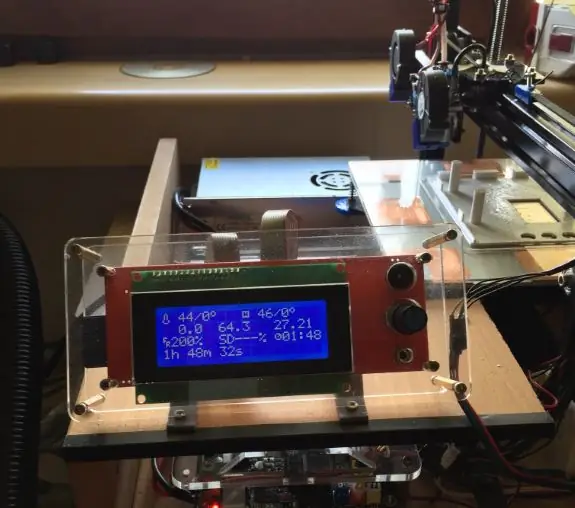
Alle 3D-Druckerteile finden Sie hier:
Sei vorsichtig. Drucken braucht Zeit. Der größte Teil der Umverpackung kann bis zu 14 Stunden dauern.
Die Schraube von Archimedes ist das besondere Teil, das Sie vertikal drucken müssen. Möglicherweise benötigen Sie ein gutes Luftgebläse (Fun Duck), um geschmolzenes Filmanet abzukühlen, wenn es aus der Düse strömt.
Schritt 5: Schaltung entwerfen und Leiterplatte herstellen
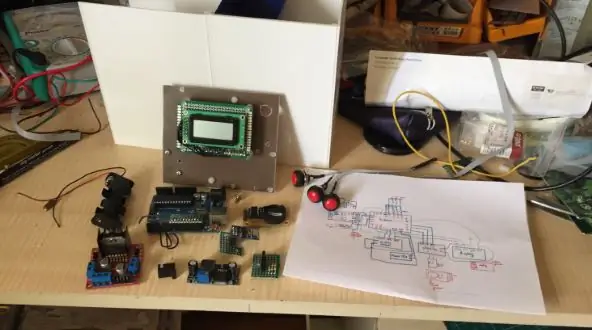
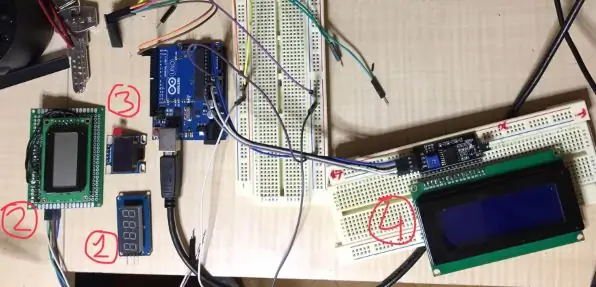
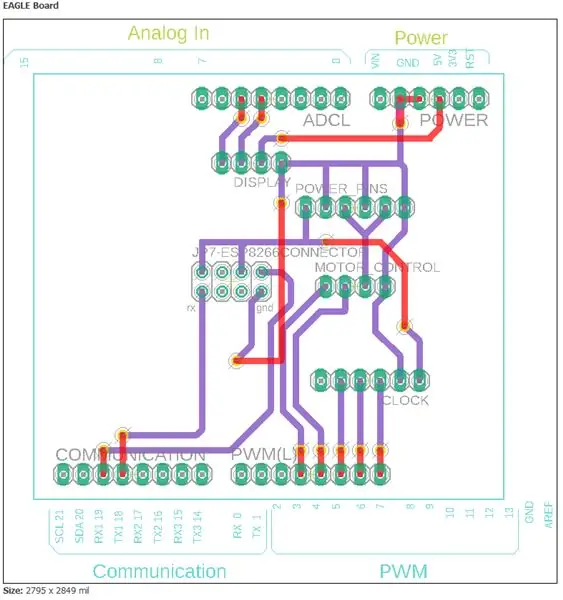
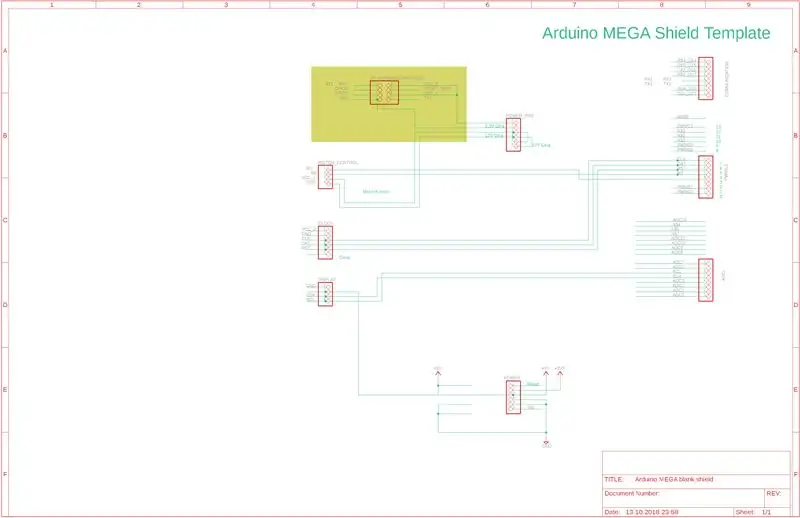
Die Leiterplattenherstellung für dieses Projekt wird hier beschrieben.
EAGLE-Schaltungsdesigndateien sind
Die meisten Teile sind Elektronikmodule wie:
- Uhr,
- Gleichstrommotorsteuerung,
- Anzeigesteuerung,
- Anzeige,
- esp8266,
- arduino mega
- Stromwandler
Es gibt viele verschiedene Varianten dieser Module. Die meisten von ihnen haben ähnliche Ein-/Ausgänge, so dass es einfach ist, das aktuelle Eagle-Design anzupassen. Es können jedoch einige Modifikationen erforderlich sein.
Schritt 6: Software schreiben
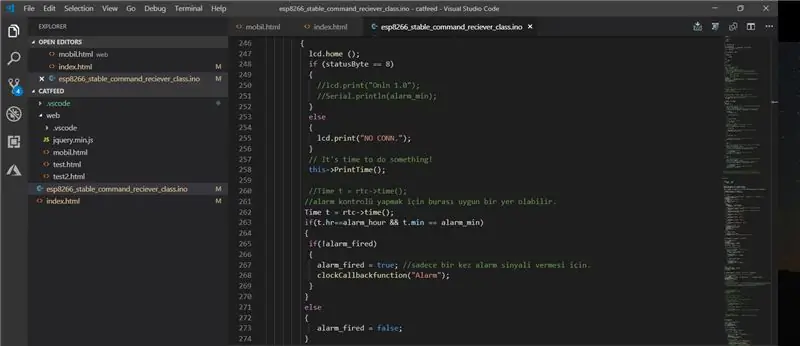
Den vollständigen Code finden Sie hier.
Dieser Code funktioniert möglicherweise nicht bei einigen Arduino-Board-Definitionen. Ich habe Arduino AVR Boards 1.6.15 verwendet. Neuere funktionierten nicht (oder funktionierten mit einigen kleineren oder größeren Problemen)
Ich habe auch etwas HTML-Beispielcode hinzugefügt. HTML-Seiten können verwendet werden, um die WLAN-Verbindungsfähigkeiten des Geräts zu testen.
Das Gerät akzeptiert einfache HTML-URL-Befehle. Zum Beispiel: Um mit der Fütterung zu beginnen, können Sie einfach "https://192.168.2.40/?pin=30ST" aus dem Browser senden. (IP kann sich je nach Ihren lokalen Netzwerkeinstellungen ändern) ıNeben dem Starten und Stoppen des Geräts können Sie die Uhrzeit und den Wecker im gleichen Format mit unterschiedlichen Parametern einstellen.
Dieser HTML-Befehl wird von esp8266 empfangen und von der Software geparst. Software fungiert als einfacher Webserver. Es führt Befehle aus und gibt 200 zurück, wenn es erfolgreich ist.
Diese Steuerungsmethode ist nicht die eleganteste Art, iot-Geräte zu steuern. Hier finden Sie bessere Möglichkeiten der IOT-Kommunikation wie MQTT. Ich plane, die Software zu überarbeiten, um ein besseres Protokoll aufzunehmen.
Als Editor habe ich Microsoft Visual Code verwendet. Ich begann mit Arduino IDE, wechselte aber zu VSCode. Ich empfehle dringend, dass Sie, wenn Sie Code für mehr als 100 Zeilen schreiben, nicht einmal daran denken, Arduino IDE zu verwenden.
Schritt 7: Zusammenbauen
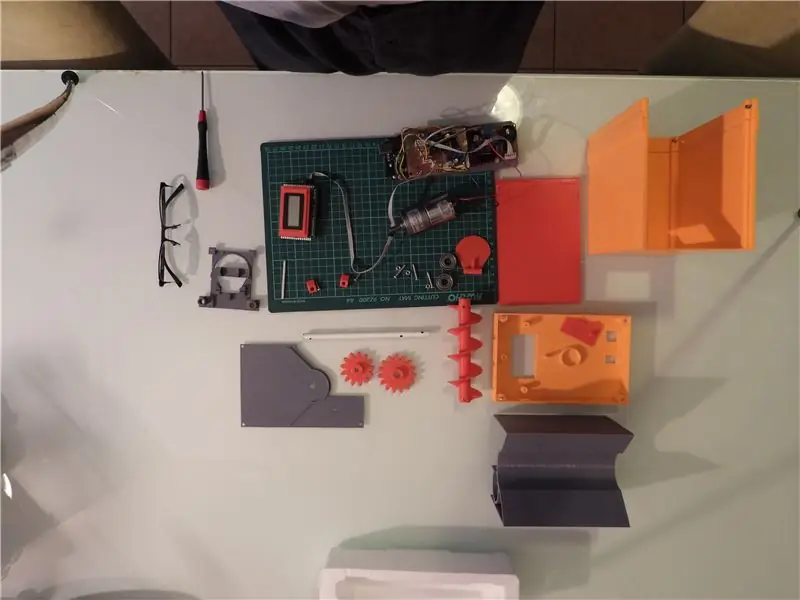
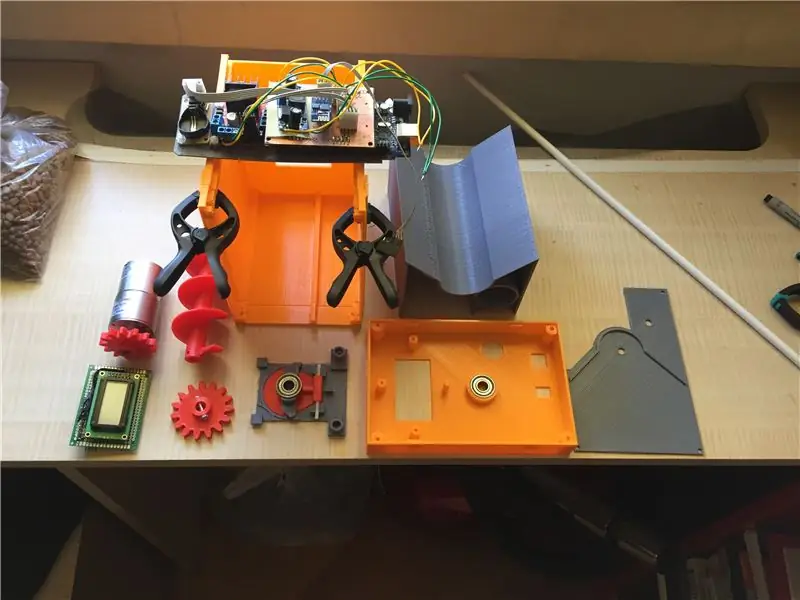
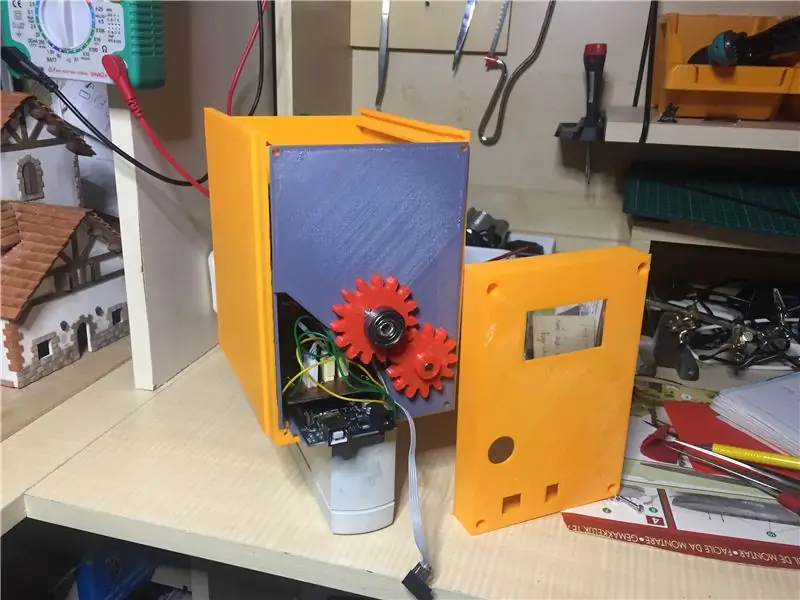
Detailliertes Montagevideo und funktionierendes Prototypvideo ist hier
Empfohlen:
Automatischer Anrufbeantworter V1.0: 17 Schritte (mit Bildern)
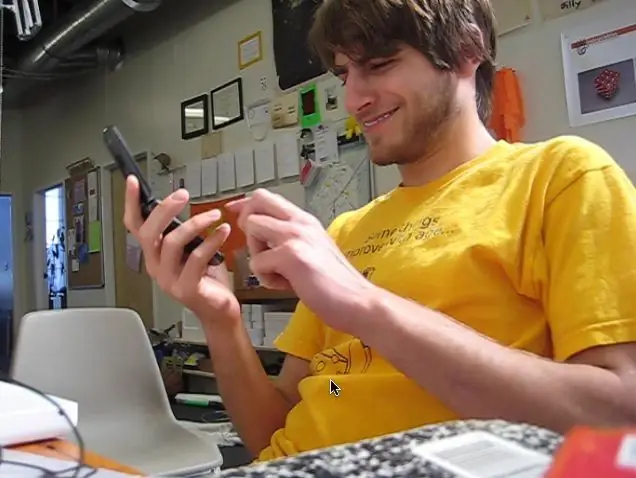
Automated Answering System V1.0: Manchmal habe ich einfach keine Lust, ans Telefon zu gehen. Okay, okay… die meiste Zeit ist es mir wirklich egal, ans Telefon zu gehen. Was soll ich sagen, ich bin ein beschäftigter Mann. Ich habe mir schon lange ein System gewünscht, das dem ähnlich ist, das die Telefongesellschaft für die
Automatischer Sucher: 4 Schritte
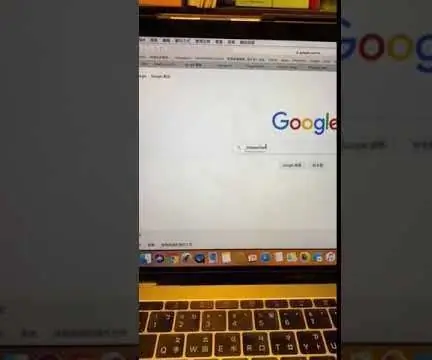
Auto-Searcher: Also las ich eines Tages Fanfiction in meinem Bett, um meinen Stress abzubauen. Aber ich hatte das Gefühl, dass es ein bisschen mühsam war, die Seite weiter zu scrollen, um weiterzulesen. Ich muss auch klicken, um das nächste Kapitel zu sehen und das Ganze vorher suchen
Automatischer Gartenbewässerer - 3D gedruckt - Arduino: 10 Schritte (mit Bildern)
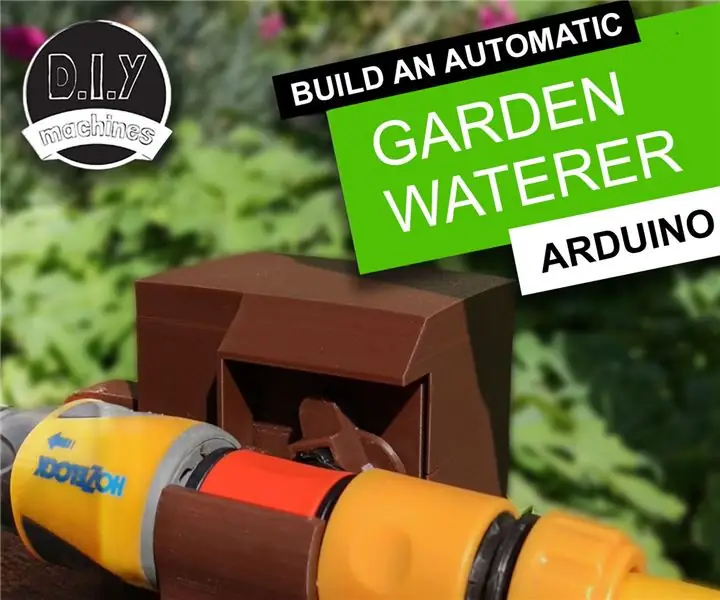
Automatischer Gartenbewässerer | 3D gedruckt | Arduino: Ich bin ein begeisterter Gärtner, aber Ihre Pflanzen während Trockenperioden von Hand zu gießen, dauert einige Zeit. Dieses Projekt befreit mich vom Gießen, damit ich an meinen anderen Projekten arbeiten kann. Es ist auch großartig, sich um den Garten zu kümmern, während Sie nicht zu Hause sind, und die Pflanze