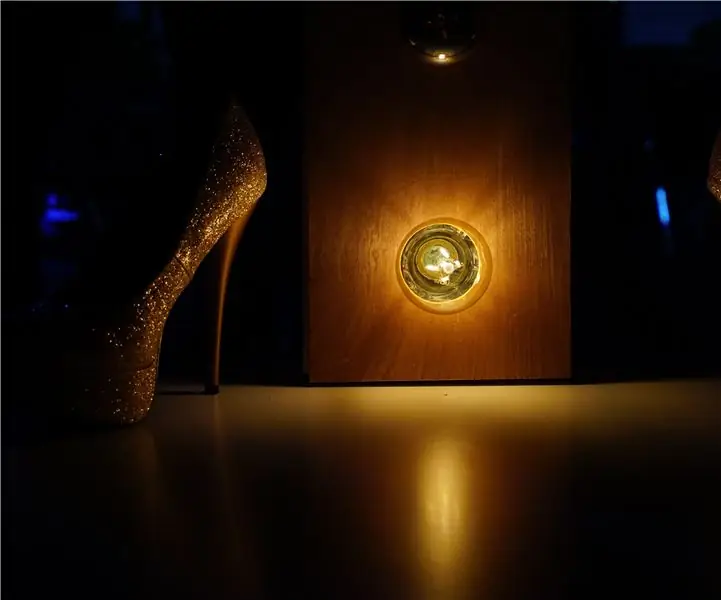
Inhaltsverzeichnis:
- Lieferungen
- Schritt 1: 5V-Schaltung: Arduino
- Schritt 2: Entwerfen der Box
- Schritt 3: Aufbau der Box
- Schritt 4: Installieren der Steckdosen in der Box
- Schritt 5: Löten der Niederspannungselektronik
- Schritt 6: Anschließen der 220V-Komponenten
- Schritt 7: Magnetschnapper (optional)
- Schritt 8: Was ich anders machen würde
2025 Autor: John Day | [email protected]. Zuletzt bearbeitet: 2025-01-23 12:52
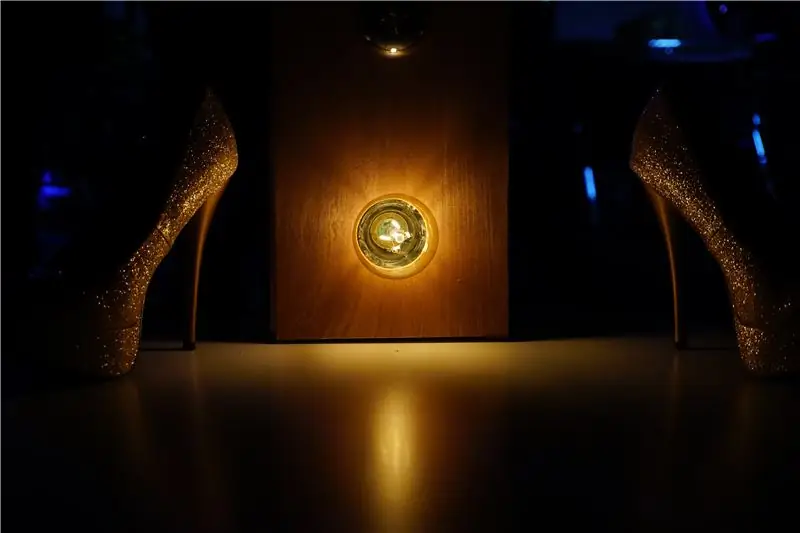
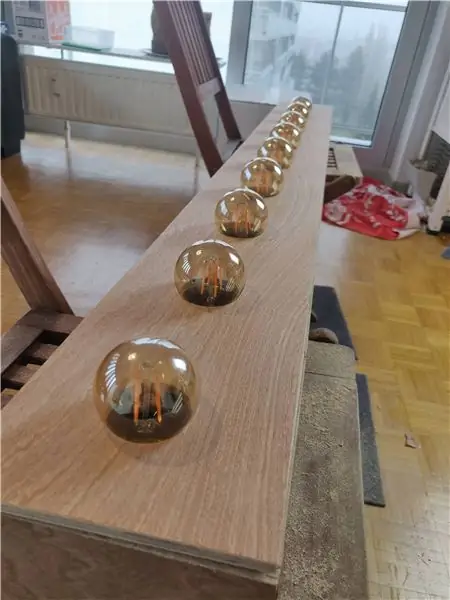
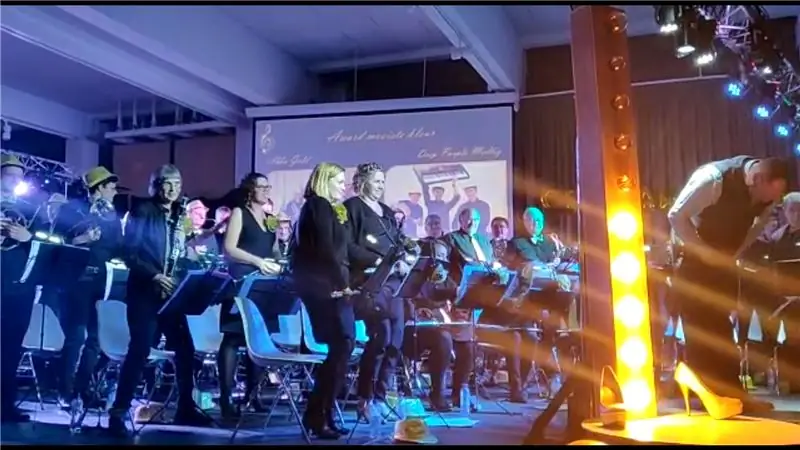
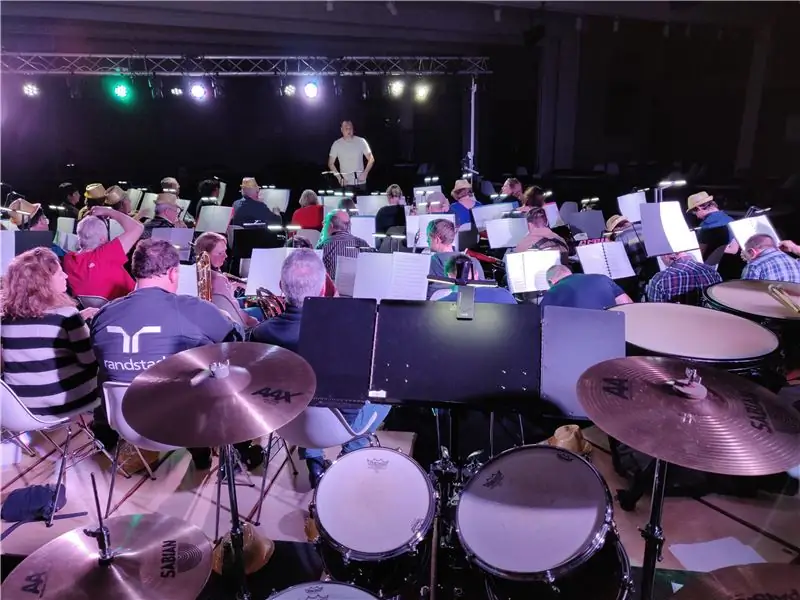
Seit ungefähr dem Jahr 2001 habe ich angefangen Schlagzeugunterricht zu nehmen. Nach zehn Jahren, im Jahr 2011, trat ich meiner ersten Konzertband bei und war begeistert. Gemeinsam Musik zu machen und bei einem Konzert zu spielen, ist berauschend. Jetzt bin ich schon seit über 5 Jahren in einer anderen Konzertband. Wir haben zwei Konzerte pro Jahr und mehrere Aufträge nebenbei.
Als Thema unseres Neujahrskonzertes wollten wir eine Preisverleihung für die besten Songs, die wir gespielt haben, veranstalten. Das Setup war, dass wir in jeder Kategorie zwei Songs spielten. Zum Beispiel "Ice versus Fire", für das wir ein Medley aus "Frozen" und eines aus "How to train your dragon" gespielt haben. Das Publikum sollte dann für den besten Song stimmen, der dann mit einem maßgeschneiderten 3D-gedruckten Preis ausgezeichnet wird.
Beim Brainstorming während der Vorbereitungen hatten wir viele Ideen, wie das Publikum abstimmen kann, von Papiervotings bis hin zu Apps. Aber all diese Vorschläge erfordern, dass die Show für jede Auszeichnung unterbrochen wird, während das Publikum ernsthaft abgelenkt wird. Als ein Applausmesser vorgeschlagen wurde, wussten wir alle, dass wir Gold gefunden hatten. Einige Online-Recherchen ergaben jedoch keine wirklich einsatzbereite Lösung. Also stand ich mutig auf, erklärte mich zum Anfänger und behauptete, ich könnte mit einem eher kleinen Budget leicht einen von Grund auf neu bauen.
Oh Junge, war ich unvorbereitet auf das Kaninchenloch, in das ich fallen würde.
Lieferungen
Werkzeuge
- Ihr liebster Akku-Bohrschrauber
- Rundbohrer und andere Bits
- Schraubendreher
- 3D-Drucker (optional)
Fall
- Sperrholz. (Ich wähle 8mm Multiplex, aber im Nachhinein hätte ich 12mm oder noch dicker nehmen sollen)
- 4 X Magnetischer Türverschluss (im Nachhinein optional)
- Schrauben
Elektronik (5V)
- Arduino Nano
- Elektret-Mikrofonverstärker - MAX4466 mit einstellbarer Verstärkung (oder ähnlich, je nach Bedarf)
- 2 x 5V 8-Kanal-Relaismodul
- 220V auf 5V Transformator
- Drähte, viele kurze, und ein vieradriger mehrere Meter langer Draht für die 'Fernsteuerung'
- zwei Schalter
Elektronik (220V)
- Standard-Elektrokabel (Reste aus dem Hausbau sind ideal, aber am besten flexibel)
- Abgesicherte Wechselstromsteckdose (optional, aber dringend empfohlen)
- Glühbirnen nach Wahl
- Lampenfassungen
Schritt 1: 5V-Schaltung: Arduino
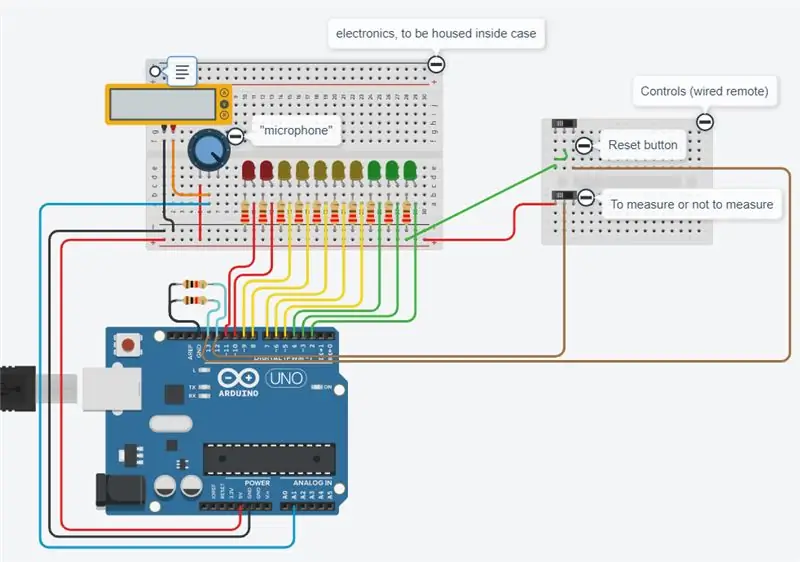
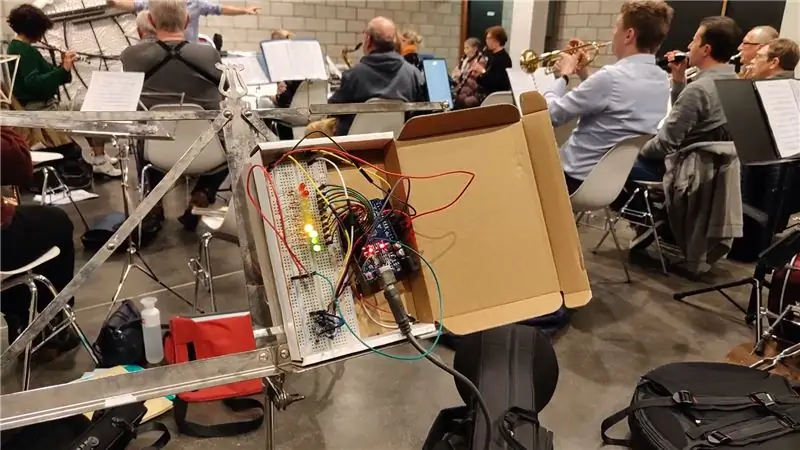
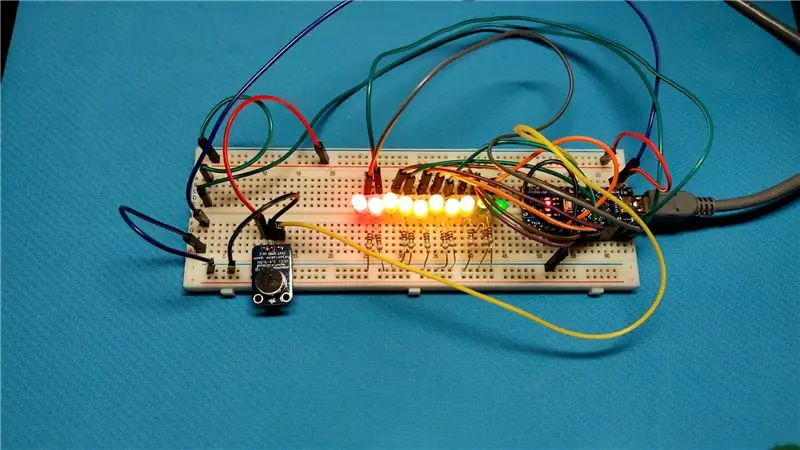
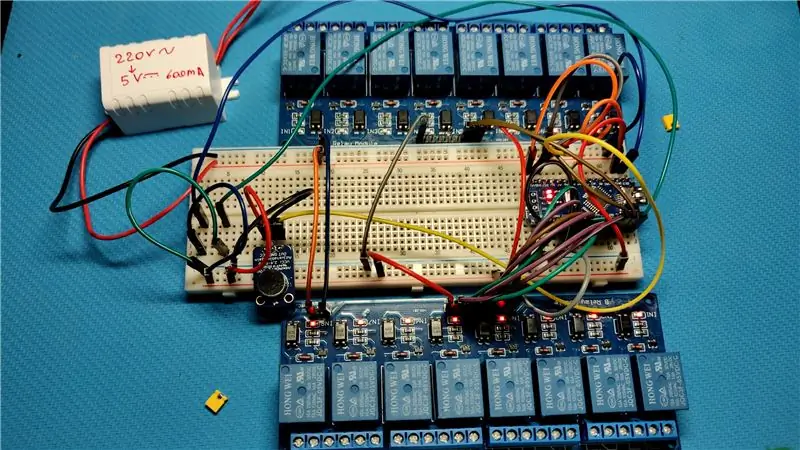
Es gibt drei Hauptteile dieses Builds: (1) die 5V-Elektronik, die das "harte Denken" übernimmt: Zuhören und entscheiden, wann und welche Lichter eingeschaltet werden sollen; (2) das Gehäuse, um alles gut einzupassen, versteckt alle "Verbrechen" und (3) die 220-V-Schaltung, die von der 5-V-Schaltung gesteuert wird.
Beginnen wir mit der 5V-Schaltung, da wir diese in kleinem Maßstab aufbauen können.
Es war keine leichte Aufgabe, Online-Ressourcen zu finden. Ich stellte mir zehn Lichter vor, die entsprechend der Lautstärke des Applauses aufleuchteten, aber das schien noch nie jemand getan zu haben. Also habe ich klein angefangen; Auf tinkerCAD baue ich eine Online-Simulation, wie die 5V-Elektronikteile aussehen sollen. Mein sehr rudimentäres Design mit Code findet ihr hier: https://www.tinkercad.com/things/8mnCXXKIs9M oder unten auf dieser Seite als "Applause_1.0.ino" Datei.
Das Erstellen einer Entwurfsversion online und das Testen mehrerer Arduino-Codes in dieser Simulation hat mir wirklich geholfen, einen besseren Überblick darüber zu bekommen, was für diesen Build benötigt wird. Auf diese Weise experimentierte ich mit dem Hinzufügen einer Möglichkeit, das Verhalten des Programms zu steuern: Am Ende hatte ich zwei Schalter. Ein Schalter schaltet die Messung ein und aus, der andere setzt den Score auf 0/10 zurück.
Ich habe alle notwendigen Komponenten bereitgestellt: Einige LEDs, Widerstände, ein Arduino und vor allem ein Arduino-kompatibles Mikrofon.
Ich habe die Schaltung aufgebaut und bei der nächsten Probe alles getestet, nur um festzustellen, dass das von mir gekaufte Mikrofon für meinen Einsatz viel zu empfindlich war. Nur ein Klatschen in angemessener Nähe oder nur die spielende Band würde das Mikrofon sättigen und eine Punktzahl von 10/10 ergeben. Dies hat mich dazu gebracht, nach einem Mikrofon mit variabler Verstärkung zu suchen. Ich habe mich schließlich für den Elektret-Mikrofonverstärker MAX4466 entschieden. Es hat auf der Rückseite eine sehr kleine Schraube, mit der man die Verstärkung einstellen kann. (Randnotiz: Ich habe auch den Arduino uno ohne besonderen Grund gegen einen Arduino Nano ausgetauscht).
Der MAX4466 schnitt besser ab, erreichte aber auch das Maximum beim Klatschen aus nächster Nähe, daher entschied ich mich, auch die Klatschzeit als Variable in die Formel aufzunehmen, anstatt nur die Lautstärke des Applauses. Für diese Version 2.0 der Software habe ich auch etwas eleganteren Code geschrieben (auch wenn ich das selbst sage). Bei Überschreiten einer Lautstärkeschwelle ging nur das erste Licht an, gefolgt von einer kurzen Pause, in der kein Licht mehr angehen konnte. Nach dem Warten würde der Arduino hören, ob der Ton noch laut genug war, damit das zweite Licht aufleuchtet, wenn ja, dann schaltet sich das Licht ein und die nächste Wartezeit würde ausgelöst. Die Wartezeit verlängerte sich jedes Mal, wenn ein neues Licht aufleuchtete. Ein Applaus müsste bei voller Lautstärke 22,5 Sekunden dauern, damit die Lichter 10/10 anzeigen. Sie finden den Code auf tinkerCAD https://www.tinkercad.com/things/lKgWlueZDE3 oder unten als Datei "Applause_2.0.ino"
Ein Schnelltest mit angeschlossenen Relaismodulen anstelle der LEDs lehrte mich, dass die Relais EIN waren, wenn das Signal LOW war und AUS, wenn das Signal HIGH war. Kein Problem, einfach ein paar ONs und OFFs im Code vertauschen und schon konnte es losgehen.
Wenn das alles geklärt ist. Ich könnte anfangen, alles zusammenzulöten. Aber ich musste wissen, wie lang alle Verbindungen in der Box sein sollten. Also bauen wir zuerst die Außenbox und ordnen alle Komponenten darin an.
Schritt 2: Entwerfen der Box
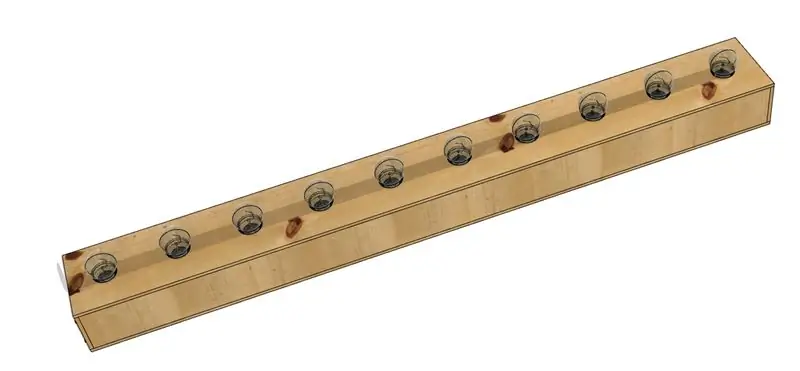
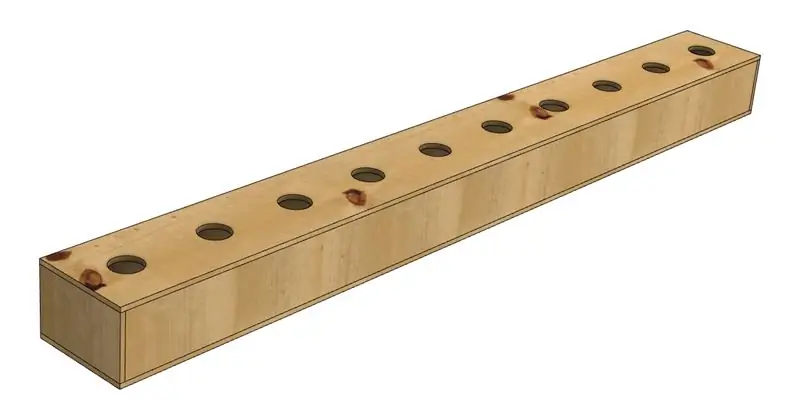
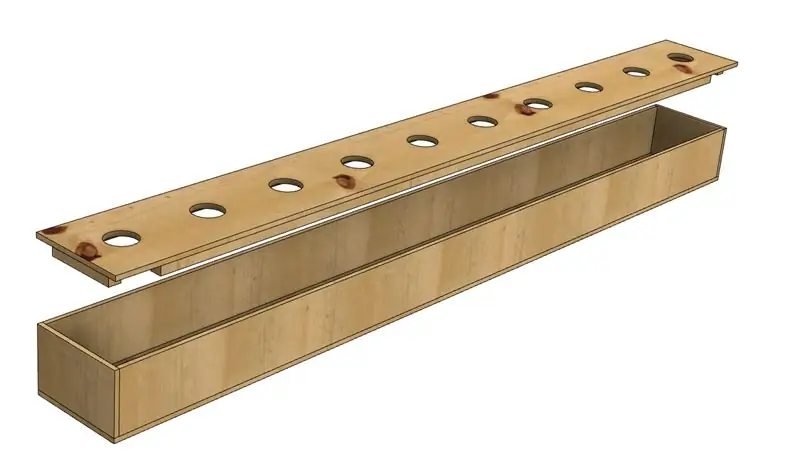
Ein zweiter Aspekt dieses Builds war seine Ästhetik. Der Applausmesser würde im Mittelpunkt der Aufmerksamkeit stehen, also musste er zumindest gut aussehen. Ich habe mich für den Bau einer Holzkiste entschieden, da ich die grundlegenden Werkzeuge dafür habe und es relativ einfach ist.
Nachdem ich bei tinkerCAD gelernt habe, dass das Experimentieren in der digitalen Welt sehr lehrreich ist, habe ich vor dem Kauf der erforderlichen Materialien auch die Applaus-Meter-Box im beliebten 3D-CAD-Programm Fusion360 entworfen.
Im Laufe mehrerer Iterationen habe ich mich schließlich für dieses Design entschieden (siehe Bilder). Es ist eine einfache rechteckige Box, bei der die Lichter aus runden Löchern in der Frontplatte herausragen.
Hässliche Schrauben in der Frontplatte wurden vermieden, indem an der Innenseite der Frontplatte einige Halteleisten angebracht wurden, in die später magnetische Türschnapper eingeschraubt wurden. Das Magnetverschlusssystem ist im Nachhinein eher ein Sicherheitsfeature als ein wirklich notwendiges, da die Riegel die Frontplatte allein durch Reibung festhalten, prima.
Ich habe auch die Elektronik zu meinem digitalen Design hinzugefügt. Dadurch hat sich einiges geändert, sodass es sich bereits ausgezahlt hat, dass ich es zuerst in Fusion360 entworfen habe. Zum Beispiel musste die Box etwas breiter als die anfänglichen 15 cm sein, damit die Relais seitlich passen. Am Ende habe ich auch Kunststoffhalter für die Lampenfassungen modelliert und 3D-gedruckt, die ihrerseits die Lichter an Ort und Stelle halten würden. Dies schien mir die Option zu sein, die mir genügend Spielraum für zukünftige Fehler geben würde. (Ich weiß, dass diese Halter auch als solche gekauft werden können, aber das hat mich dreimal mehr gekostet und ich hatte ein begrenztes Budget)
Ich habe die F360-Datei meines endgültigen Designs hier hinzugefügt, damit Sie darauf verweisen und herumspielen können.
Schritt 3: Aufbau der Box
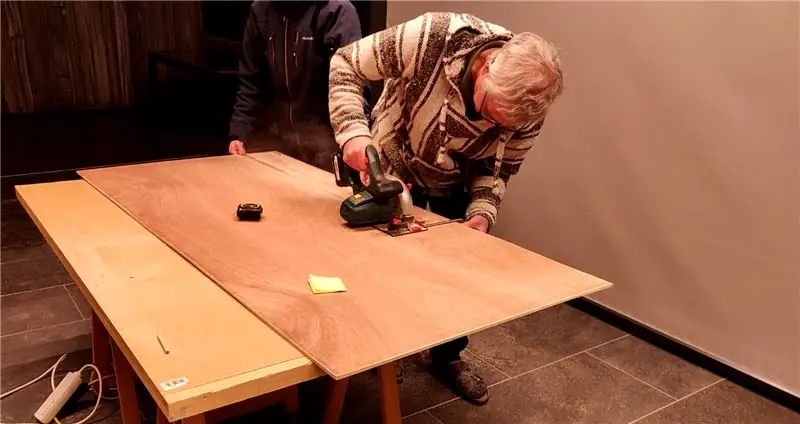
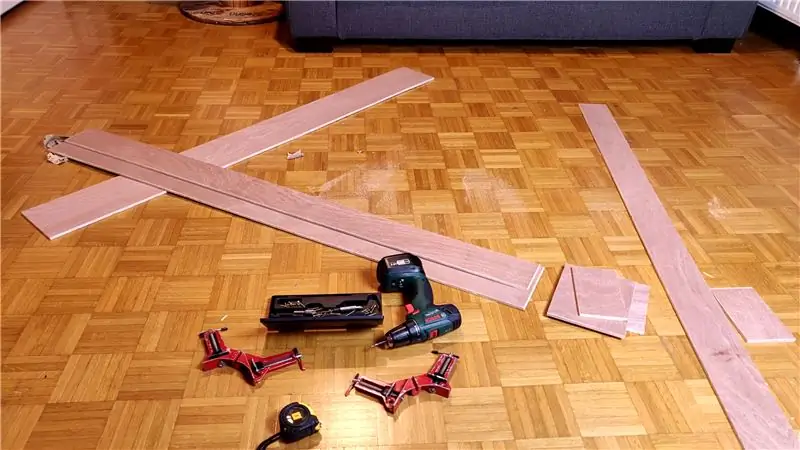
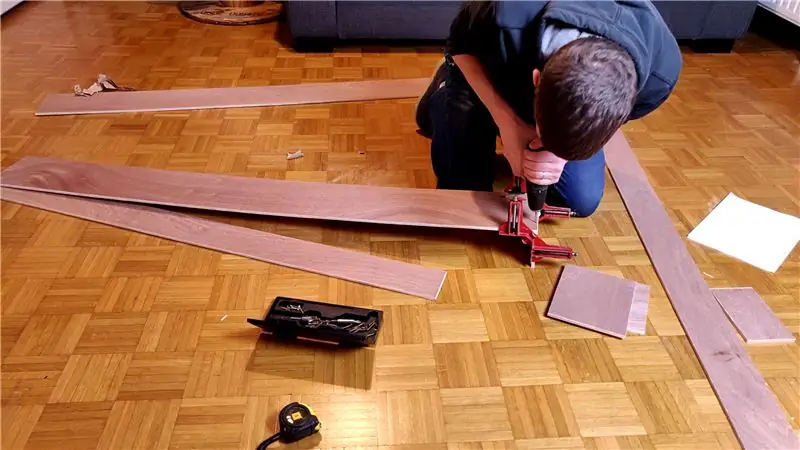
Nachdem das digitale Design fertiggestellt war, war es an der Zeit, in den Baumarkt zu gehen, eine große Sperrholzplatte zu kaufen und mit dem Schneiden zu beginnen. Da ich nicht wirklich so "ausgefallene" Werkzeuge besitze, ging ich eines Wochenendes zu meinen Eltern und schnitt dort das Holz zurecht.
Mein Design führte jedoch zu einem ziemlich exotischen Einzelblatt:
- 2 mal 16,6x150cm für Vorder- und Rückseite
- 2 mal 16,6x10,2cm für oben und unten
- 2 mal 10,2x148,4cm für die Seiten
Die Stützleisten an der Innenseite der Frontplatte waren Reste und wurden als solche verwendet, ansonsten wäre die bevorzugte Länge 134cm und 12cm gewesen.
Zuhause angekommen legte ich alle Teile auf dem Boden aus und begann mit Hilfe einiger (geliehener) Eckzwingen, Löcher vorzubohren und die Bretter zusammenzuschrauben. Denken Sie daran, dass Schrauben nur für rein ästhetische Reaktionen in die Ober-, Unter- und Rückseite des Messgeräts passen.
Das Pilotbohren der Löcher und das Zusammenschrauben aller Bretter war eine prekäre Aufgabe, da das Sperrholz nur 8 mm dünn ist. Ich habe mich oft verflucht, weil ich dachte, 8 mm wären dick genug.
Die Frontplatte benötigte einige sorgfältig beabstandete Löcher von etwa 5 cm Durchmesser. Ich markierte die Mittellinie der Frontplatte und begann von einer Seite. Die Mitte des ersten Lochs war 8 mm (die Materialstärke) + 75 mm (die Hälfte von 150 mm) vom Rand der Platte entfernt. Alle anderen Löcher sind 150 mm voneinander entfernt. Am Ende lag ich nur 2 mm daneben, als ich das zehnte Loch markierte… es war ein guter Tag!
Der einzige kreisförmige Bohrer, den ich mir ausleihen konnte, war 51 mm, mehr als nah genug, um glücklich mit dem Bohren zu beginnen.
Die Frontplattenführungen wurden mit einfachem Holzleim auf die Innenseite der Frontplatte geklebt.
Schritt 4: Installieren der Steckdosen in der Box
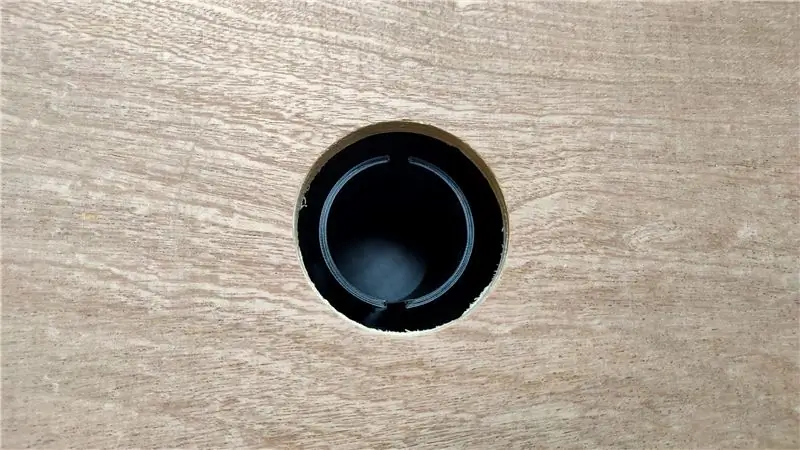
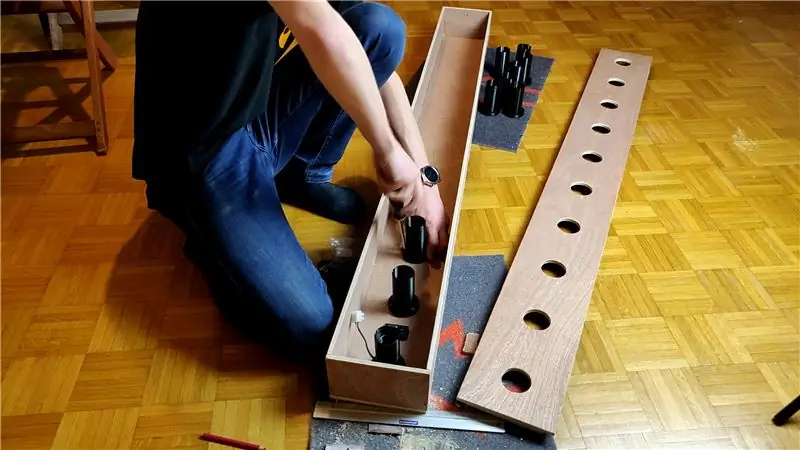
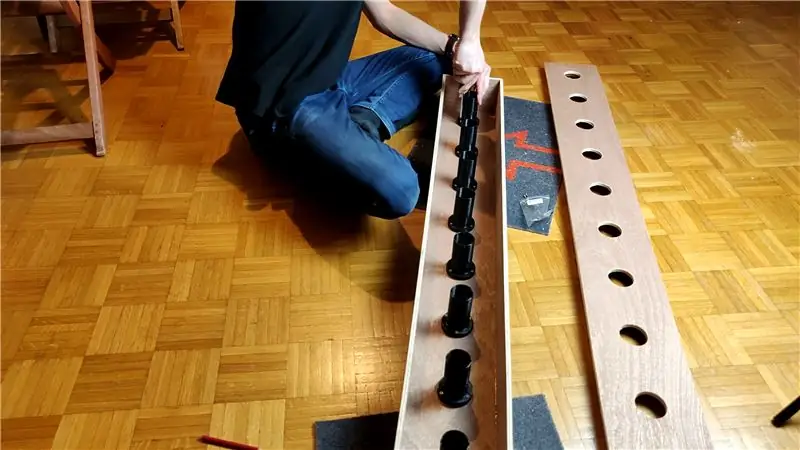
Die ersten Komponenten, die in unsere neu gebaute Box eingebaut werden, sind die Lampenfassungen. Der Grund dafür ist, dass die Halter mittig unter jedem Loch in der Frontplatte positioniert werden sollten. Denn der Halter hält die Lampenfassungen in Position, in die wiederum die Glühbirnen eingeschraubt werden, und die Glühbirnen ragen buchstäblich als einziges aus der Frontplatte heraus und sind somit das einzige, was nicht bewegt werden kann eine andere Position in unserer Box. Da ihre Position feststeht, sollten sie zuerst reingehen, damit ich später keinen dummen Fehler mache.
Wie bereits erwähnt, gibt es im Handel erhältliche Lampenfassungen mit integrierter Halterung, um sie senkrecht an einer Wand zu montieren, aber diese kosten 4-mal mehr als die einfachen, die nur zum Aufhängen von der Decke gemacht sind, ohne auch nur einen schwachen Versuch zu machen schön aussehen. Also habe ich mich für billige und 3D-gedruckte Halterungen für die Steckdosen entschieden. (STL-Datei unten). Beim Erstellen des 3D-Designs habe ich darauf geachtet, dass genügend Spielraum vorhanden ist, um die Steckdosen in verschiedenen Tiefen zu platzieren.
Ich habe nur einen Halter gedruckt, um das Design zu überprüfen. Danach druckte ich 9 Halter auf einmal, füllte meine gesamte Bauplatte vollständig aus und dauerte mehr als 50 Stunden.
Ich habe willkürlich die Ober- und Unterseite der Frontplatte und der Box markiert (denken Sie daran, dass ich eine satte 2 mm Abweichung zwischen digitalem Design und Realität hatte). Dann begann ich den mühsamen Prozess, einen Halter mit aufgesetztem Deckel zu zentrieren, die Vorderseite vorsichtig anzuheben, ihre Position mit Bleistift zu markieren und zum nächsten Halter zu gehen. Als alles gesagt und getan war, habe ich jede Position noch einmal überprüft, bevor ich sie schließlich in die Rückplatte geschraubt habe.
Ein Hinweis zu den Schrauben: Mein Halterdesign hat eine ziemlich dicke Basis, dies wurde absichtlich gemacht, um sicherzustellen, dass meine 16mm langen Schrauben nicht aus der Rückseite meiner 8mm Rückplatte herausragen. Ein weiterer Grund, sich für dickeres Sperrholz zu entscheiden. (Vergiss "lebe, liebe, lache", es heißt "lebe, liebe und lerne").
Jedenfalls waren die Lampenfassungen als nächstes dran. Ich wählte die bevorzugte Höhe, in der die Glühbirnen über der Frontplatte herausragen sollten, und maß dann die Tiefe, in der sich die Fassungen befinden sollten. Ein kleines Detail: Ich musste zuerst von allen Buchsen, die beim scheußlichen Hängen von der Decke als Zugentlastung für die Kabel dienten, ein Stück des Kabelendes abschrauben und abbrechen, aber da ich sie in individuell bedruckten Halterungen montierte, sie dienten mir überhaupt nicht. Schlimmer noch, die Zugentlastung führte dazu, dass die Kabel der engen Biegung, die ich sie zwang, standhalten und so ihre Aufgabe perfekt erfüllten, … also musste die Zugentlastung entfernt werden, damit die Buchsen so in die Halterungen passen, wie ich es wollte.
Ich klebte alle Fassungen in die Halter und ließ es über Nacht mit Gummibändern festhalten. Natürlich habe ich fabelhaft vergessen, dass ich 9 normale Glühbirnen und eine dicke für das zehnte Licht gekauft habe, diese größere Leuchte ist eher kugelförmig als birnenförmig und erfordert eine Fassung, die näher an der Vorderseite der Box platziert ist als alle anderen Leuchten.(Lebe und lerne)
Ich war daher gezwungen, den Kleber zu brechen (nur meinen 3D-Druck leicht zu zerbrechen), um die Steckdose freizugeben und neu zu positionieren. Nach reichlich Klebstoff, um den Halter zu fixieren und in der richtigen Höhe mit der Fassung zu verbinden, war die Montage der Fassungen abgeschlossen.
Außerdem habe ich die Stecker der Lichtsteckdosen an eine der Seiten der Rückplatte geschraubt.
Schritt 5: Löten der Niederspannungselektronik
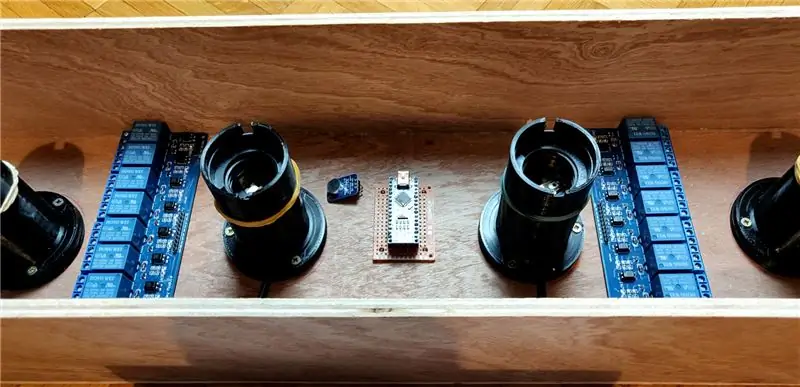
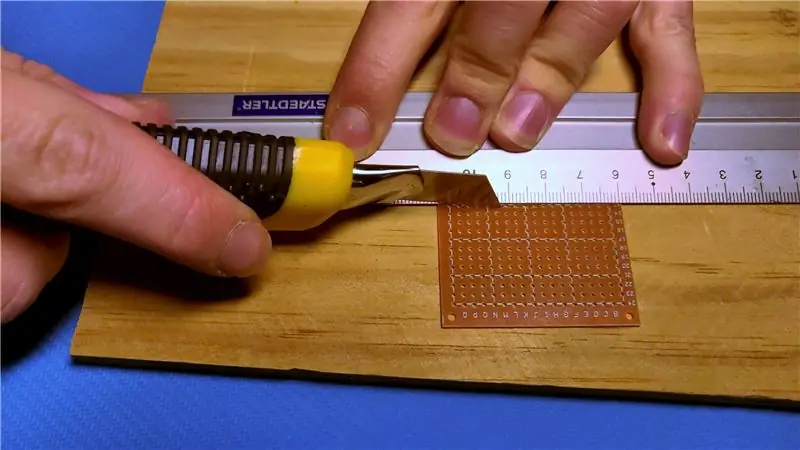
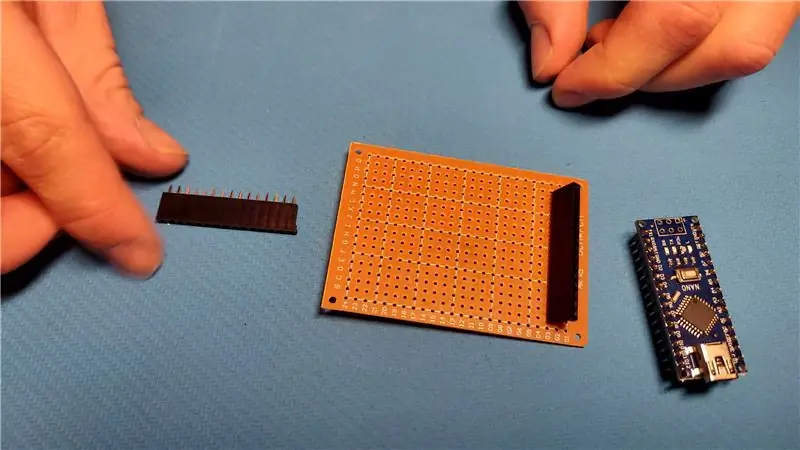
Der nächste Auftrag besteht darin, die gesamte Niederspannungselektronik in der Box "trocken zu montieren", um eine Vorstellung davon zu bekommen, wie lange die Lötverbindungen zwischen den Teilen sein sollten.
Ich begann damit, den Arduino in der Mitte zwischen Licht 5 und 6 zu platzieren und die Relais an den benachbarten Stellen oben und unten anzuordnen.
Mir wurde klar, dass keine Holzschrauben durch die Löcher im Arduino Nano passen würden. Dies ist schnell gelöst, indem einige Buchsenleisten auf eine lötbare Steckplatine gelötet werden. Die Header halten das Arduino und einige gebohrte Löcher in der Platine nehmen die Holzschrauben ohne Beanstandungen auf. Diese lötbare Platine beherbergt auch die Stiftleisten für das anzuschließende Mikrofon, die Anschlüsse (mit Kabeln) für die Relais und das lange Kabel für die Fernbedienungsbox.
Über die Remote-Box; Ich brauchte zwei Schalter am Ende eines sehr sehr langen Kabels. Ich stehe als Perkussionist ganz hinten auf der Bühne, während das Metrum ganz vorne auf der Bühne steht. Ich habe 20 m 4 Litzendraht gekauft, der normalerweise zum Löten von LED-Streifen verwendet wird. Um die beiden Schalter unterzubringen, habe ich eine einfache Box entworfen und in 3D gedruckt (STL- und F360-Dateien unten), aber jede rechteckige Box mit einigen Ausschnitten für die Komponenten und Drähte wird die Arbeit erledigen.
Nachdem ich den Abstand zwischen den Komponenten gemessen und einen großzügigen Überschuss auf diesen Abstand genommen hatte, erhitzte ich den Lötkolben und begann mit dem Löten.
Das Löten aller Verbindungen erfordert etwas Geduld und vor allem etwas Konzentration, um es richtig zu machen. Ich habe das Verdrahtungsschema beigefügt, mit dem ich alle Verbindungen hergestellt habe, aber beachten Sie, dass Ihre Verdrahtung etwas anders sein kann, wenn Sie verschiedene Komponenten verwenden. (Oder wenn ich einen Fehler in meinem Diagramm gemacht habe)
Am Ende sah meine Verkabelung aus, als ob ein Vogel dort nisten wollte. Trotzdem wurden wie durch ein Wunder keine Fehler gemacht und beim Einschalten fing auch nichts an zu rauchen.
Mit allem angeschlossen konnte ich jede Platine auf 3D-gedruckten Abstandshaltern an die Rückwand schrauben. Diese Abstandshalter haben zwei Funktionen: (1) Es ist immer eine gute Idee, etwas Platz zwischen den Leiterplatten und der Platte zu lassen, auf der Sie sie montieren. Und (2) habe ich mich schon beschwert, dass ich 16mm Schrauben und 8mm Sperrholz habe und dadurch ständig Gefahr laufe, Schrauben quer durch das Holz zu schrauben? Ja, die Abstandshalter sorgten auch dafür, dass meine Schrauben nicht das andere Ende der Sperrholzkiste erreichten.
[HINWEIS] Im Nachhinein würde ich tatsächlich empfehlen, 5 Relais pro Relaismodul zu verwenden. Meine Idee, zwei 8-Kanal-Relaismodule zu verwenden, war, ein defektes Relais zu berücksichtigen, in diesem Fall müsste ich nur die Anschlüsse austauschen und der Applauszähler wäre wieder in Betrieb. Dadurch würden sich auch die 220V-Anschlüsse etwas besser auf die beiden Module aufteilen, wodurch das Kabelmanagement etwas … überschaubarer wird. (Lebe und lerne)
Schritt 6: Anschließen der 220V-Komponenten
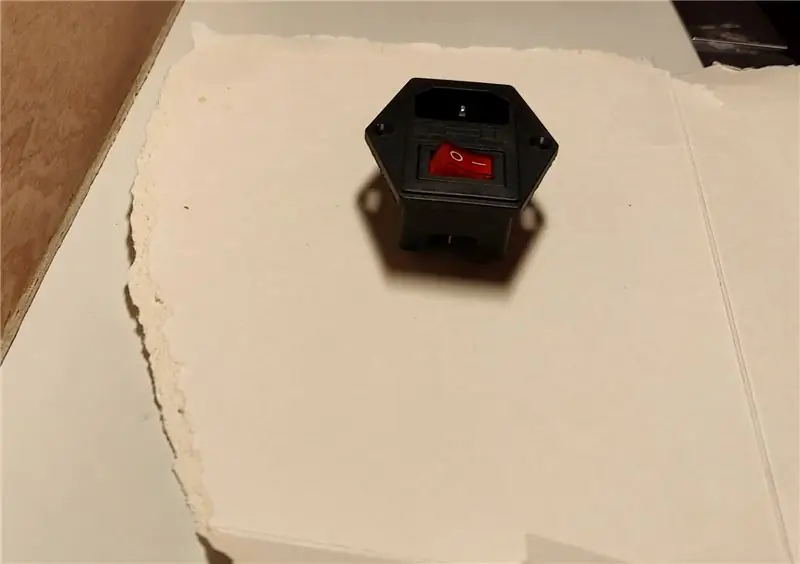
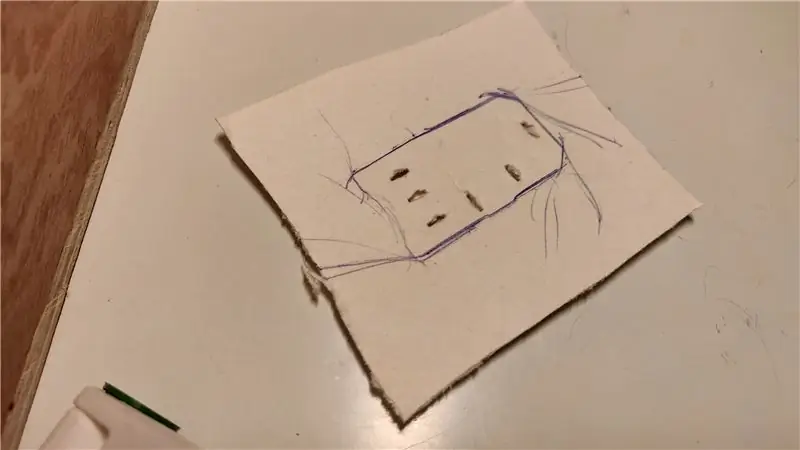
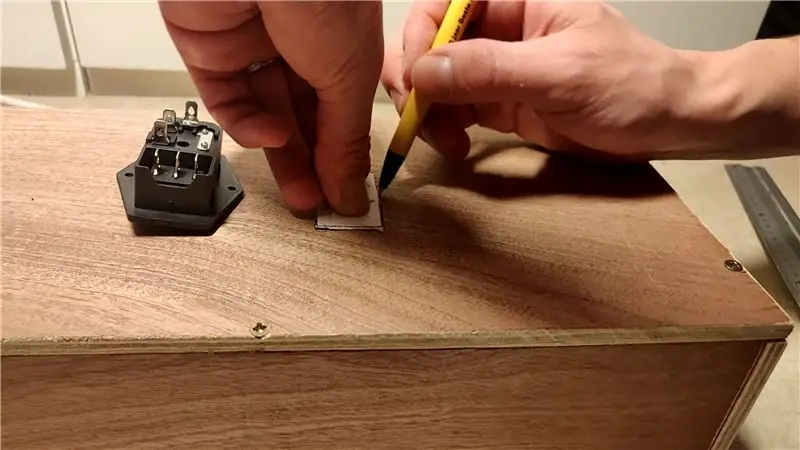
Wenn alle Niederspannungskomponenten vorhanden sind, ist es Zeit für die ernsthafte Arbeit und die Installation des Hauptspannungskreises.
Es versteht sich von selbst, dass Sie während der Arbeit mit den Drähten diese unter keinen Umständen an das Stromnetz anschließen !!!!!
Gemeinsam mit dem Techniker, der die Show-Lights für unser kommendes Konzert installieren und steuern würde, haben wir uns entschieden, eine abgesicherte Steckdose als Stromeingang für das Applausmeter zu verwenden. Dadurch wurde sichergestellt, dass jedes Kabel beliebiger Länge in unser Messgerät passt und es mit Strom versorgt.
Auch dies würde unserem Setup eine zusätzliche Sicherheitsebene verleihen: Diese Anschlüsse sind mit einer Sicherung ausgestattet, die ab einer bestimmten Stromstärke durchbrennt, um sicherzustellen, dass nichts Feuer zwischenspeichert, wenn es nicht sollte.
Für die Installation dieses Steckers benötigten wir seine genauen Maße. Es hat jedoch eine ziemlich komplexe Form. Am einfachsten ist es also, den Netzstecker auf ein Stück Pappe zu drücken und die Konturen des Steckers nachzuzeichnen. Die Konturlinien können dann ausgeschnitten werden, um eine Schablone zu erhalten, die auf das Holz übertragen werden kann.
Beachten Sie beim Anzeichnen und Ausschneiden der Position für den Stecker, dass im Inneren des Zählers bereits Komponenten installiert sind, die nicht mehr bewegt werden können, wodurch die möglichen Stellen eingeschränkt werden, an denen der Stecker aus der Box herausragen kann. Gleiches gilt für das Austrittsloch des 20m langen Drahtes für die 'Fernsteuerung'.
Normalerweise würde man das Loch mit einer Stichsäge schneiden, aber ich besitze so ein Gerät nicht und war ungeduldig, also habe ich einfach Löcher entlang der Konturen gebohrt und das Loch einfach mit einer scharfen Klinge ausgeschnitten. Das funktioniert, aber ich kann es nicht empfehlen, da ich mir fast die Finger abgeschnitten habe.
Jetzt geht es nur noch darum, alles miteinander zu verkabeln. Ich habe einen Schaltplan der 220-V-Schaltung zur einfachen Bezugnahme erstellt. Der heiße Draht wird an alle Leuchten parallel angeschlossen, während der Neutralleiter von den Relais unterbrochen wird, bevor er an die Leuchten angeschlossen wird. So einfach ist es. Stellen Sie einfach sicher, dass Sie das richtige Licht an das richtige Relais anschließen, oder Sie müssen entweder das 5-V-Steuerende oder die 220-V-Kabel wieder anschließen, um Ihren Fehler zu beheben.
Es gibt eine Anleitung, wie Sie Ihre Drähte an die abgesicherte Steckdose anschließen, die alles besser erklärt, als ich es jemals könnte. Up-a-Sicherte-AC-Stecker-Steckdose/)
[HINWEIS] Um die Neutralleiter an die zentral platzierten Relais anzuschließen, habe ich einen Draht an die abgesicherte Buchse angeschlossen und ihn in zehn geteilt, bevor ich ihn an die Relais anschließe. Ich hatte vor, die Neutralkabel an den Relais zu durchlaufen und jeden Relaiseingang parallel miteinander zu verbinden. Die Relaisklemmen akzeptierten jedoch nicht mehr als ein Kabel, was mich zwang, eine andere Lösung zu finden. Um diese Aufteilung vorzunehmen, wird empfohlen, einen Verbinder irgendeiner Art zu verwenden. Das hatte ich nicht (und ich war ungeduldig) und habe einfach alle Kabel zu einem großen Knoten zusammengebunden, bevor ich es zum Teufel isolieren konnte. Ich empfehle diesen 'Knoten' aus Gründen der elektrischen Sicherheit nicht. BESONDERS aufgrund seiner Nähe zum Arduino-Board. Es scheint jedoch gut zu funktionieren.
Schritt 7: Magnetschnapper (optional)
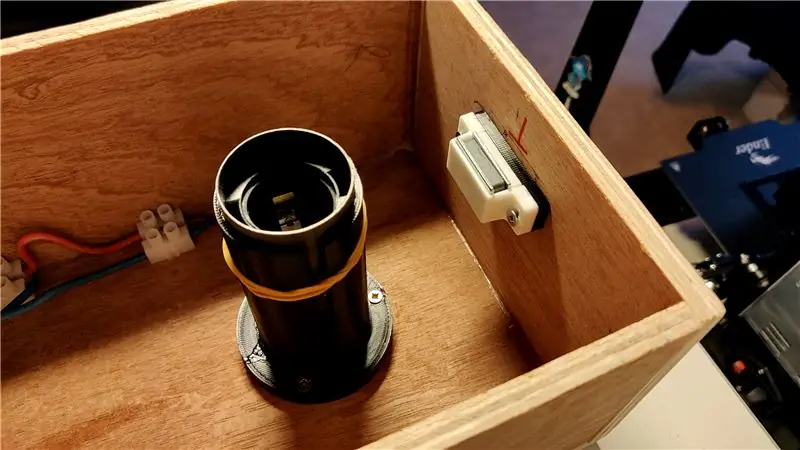
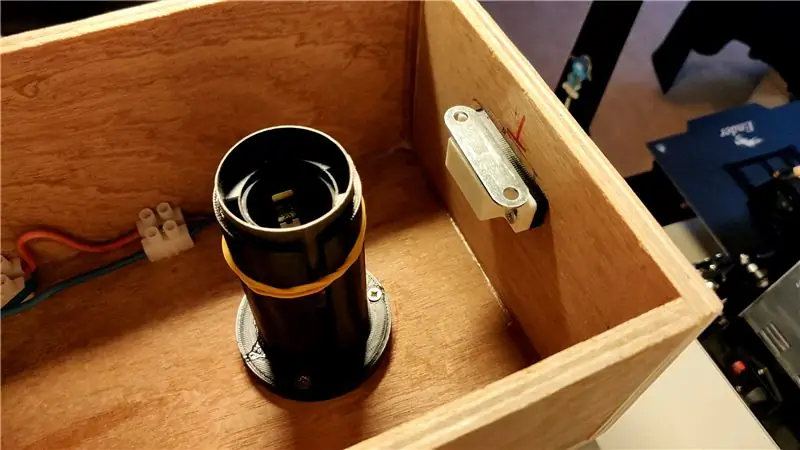
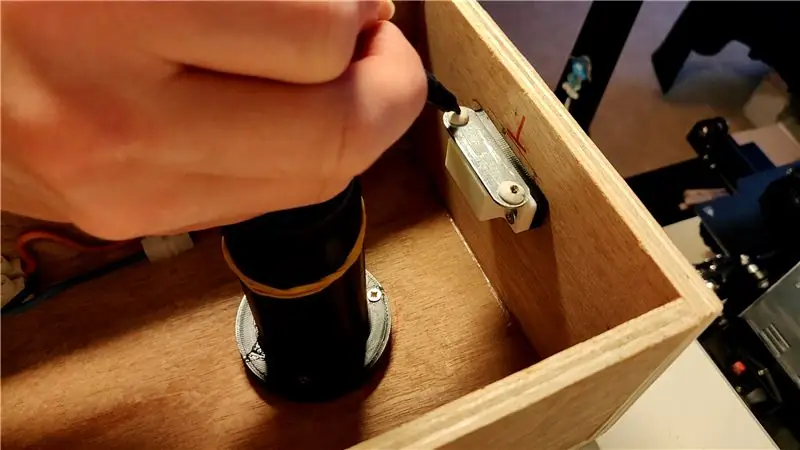
Dieser Schritt ist völlig optional, da die Frontplattenführungen die Frontplatte allein durch Reibung ausreichend halten. Ich beschloss, die Schnapper nur als Sicherheitsmerkmal mit einzubeziehen, damit sich die Frontplatte nicht löst, ohne dass ich sie lösen wollte
Ich lag viele Nächte wach und überlegte, was die beste Methode wäre, die Frontplatte der Schachtel dort zu halten, wo sie hingehörte. Am Ende kam ich auf die Verwendung von magnetischen Türschließern. Ich bezweifle, dass dies der offizielle Begriff für diese raffinierten Geräte ist, aber Sie werden sie sofort erkennen. Die Magnetschnapper werden am häufigsten verwendet, um Schranktüren geschlossen zu halten, ohne ein Schloss zu verwenden.
Das Magnetteil habe ich an der Außenschale des Applausmeters befestigt (oben, unten, linkes oder rechtes Panel). Dies geschah mit Hilfe von benutzerdefinierten 3D-gedruckten Abstandshaltern und Schrauben (yadda yadda yadda, lange Schrauben, dünnes Holz, Sie kennen die Geschichte jetzt ☺)
Die Metallplatten wurden mit dem Holz der Führungen verschraubt. Dies war auch das erste Mal, dass das Holz tatsächlich dick genug war, um keine Zwischenräume zu verwenden (yay). Ich hatte jedoch einige Probleme mit der Bestimmung der Position der Metallplatten. Ich habe eine Lösung gefunden:
- Befestigen Sie das magnetische Teil an der Box
- Platzieren Sie die Metallplatte auf dem Magneten in der perfekten Position
- auf die Löcher in der Platte eine kleine Kugel "Pritt-Buddy" (eine Art Kaugummi-Kleber zum Anbringen von Postern an Wänden ohne Reißnägel, normaler Kaugummi würde wahrscheinlich auch funktionieren)
- mit einem Alkoholmarker einen Punkt auf dem Pritt-Buddy-Ball an der Stelle machen, wo die Löcher sind
- Deckel schließen und dabei etwas Markertinte auf das Holz übertragen
- Hebe den Deckel an und tadaa! Du hast eine kleine Markierung gemacht, wo deine Schrauben hingehen sollen
- Entfernen Sie die Buddies und die Platte und schrauben Sie sie in die richtige Position, zuerst versuchen
- Schritt 8: Gewinn
Ich habe vier Magnetschnapper in die Box gelegt: einen unten, einen oben, einen mittig links, einen mittig rechts.
Die von mir gewählten Schnapper hatten eine Haltekraft von 6kg. Mit vier davon boten sie genug Kraft, um die gesamte Box allein an der Frontplatte fast hochzuheben.
Schritt 8: Was ich anders machen würde
Während ich dieses Applaus-Meter erstellt habe, habe ich oft meine Vergangenheit verflucht, weil ich dumme Entscheidungen getroffen habe. Ich werde hier die wichtigsten Lektionen auflisten, die ich gelernt habe:
-
VERWENDEN SIE DICKERES SPERRHOLZ. Im Ernst, es ist möglich, eine Box aus 8 mm Sperrholz herzustellen, aber es stellt viele Herausforderungen dar und erfordert einige Kompromisse.
- Erstens ist das Pilotbohren aller Löcher für die Schrauben eine Herausforderung, da es keine Toleranz für falsch abgewinkelte Bohrer gibt.
- Zweitens waren die Schrauben, die ich hatte, 16 mm (habe ich das schon einmal erwähnt?). Dies zwang mich, beim Einschrauben in das Holz einige Abstandshalter zu machen, um zu verhindern, dass die Schrauben auf der anderen Seite herausragen, aber gleichzeitig bedeutete dies, dass die Schrauben nicht tief genug eindrangen, um genug Zugkraft zu bekommen, um einige Komponenten festzuhalten.
- ….
- einfach dickeres Holz verwenden