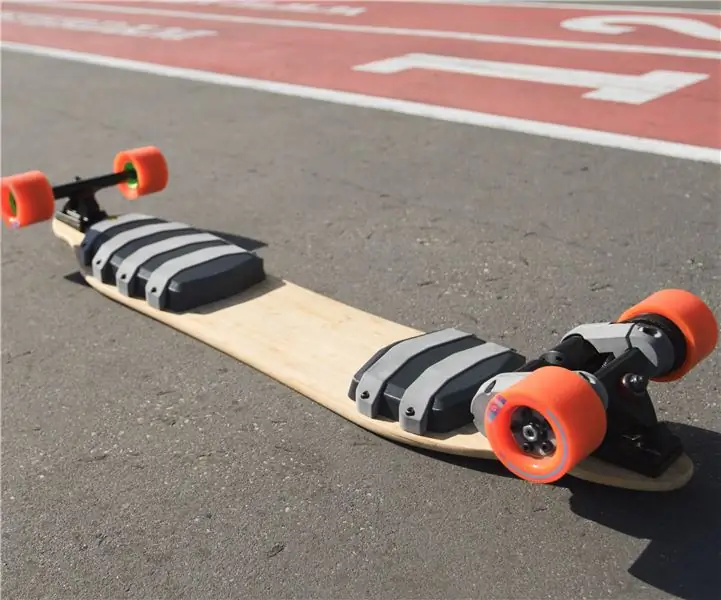
Inhaltsverzeichnis:
2025 Autor: John Day | [email protected]. Zuletzt bearbeitet: 2025-01-23 12:52
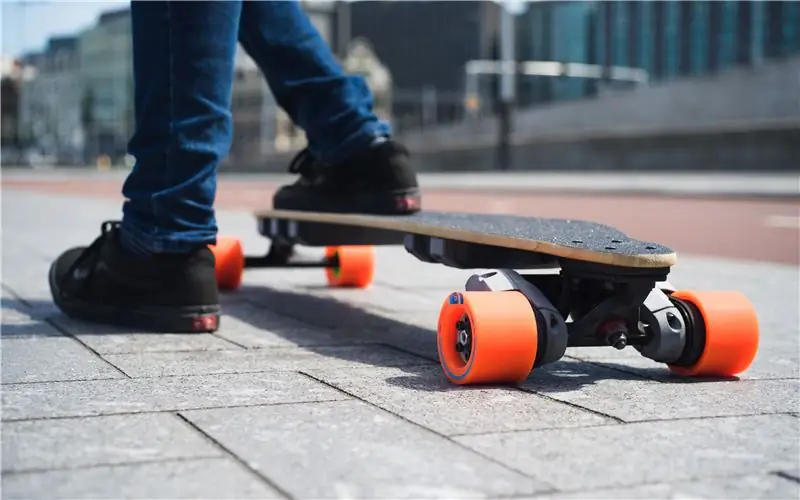
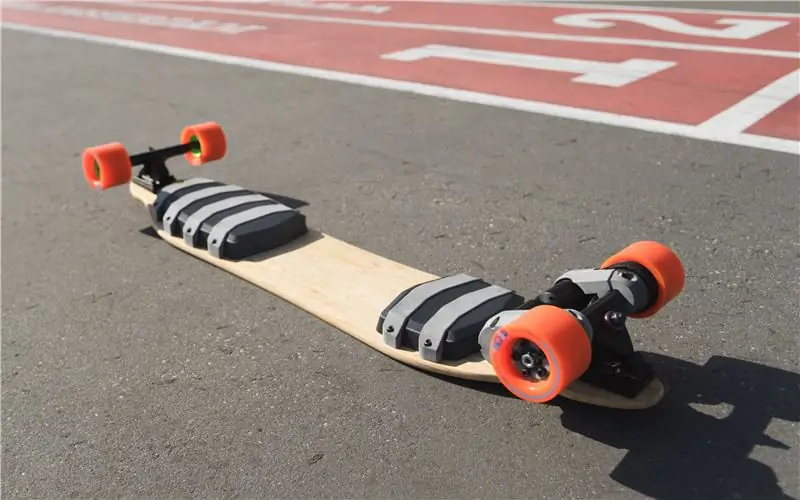
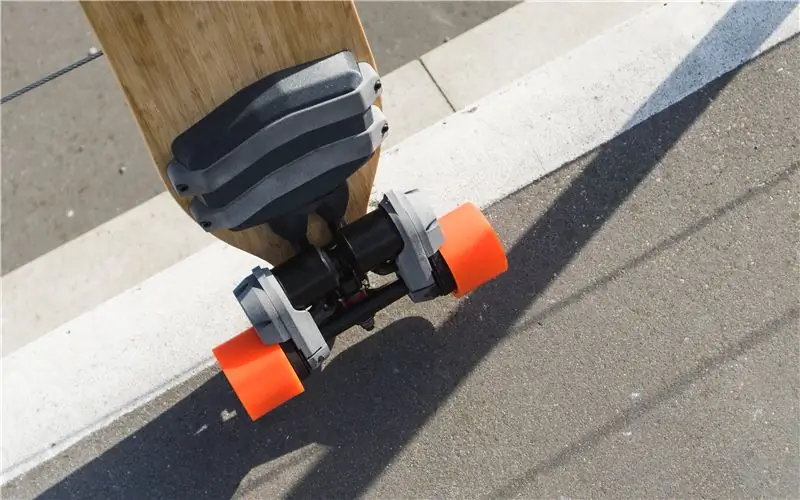
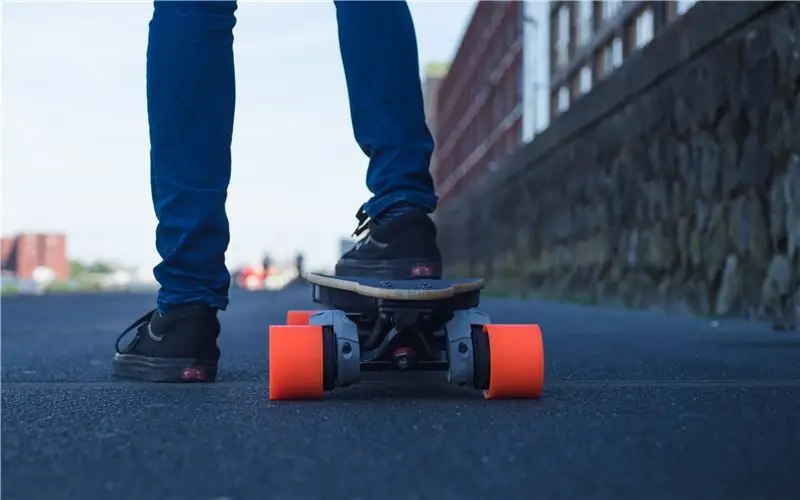
Dieses Instructable ist ein Überblick über den Build-Prozess für das Fusion E-Board, das ich während der Arbeit an 3D-Hubs entworfen und gebaut habe. Das Projekt wurde beauftragt, die neue HP Multi-Jet Fusion-Technologie von 3D Hubs zu bewerben und mehrere 3D-Drucktechnologien und deren effektive Kombination aufzuzeigen.
Ich habe ein elektrisch motorisiertes Longboard entworfen und gebaut, das für kurze bis mittelschwere Fahrten verwendet oder mit öffentlichen Verkehrsmitteln kombiniert werden kann, um eine viel größere Reichweite zu bieten. Er hat eine hohe Endgeschwindigkeit, ist sehr wendig und lässt sich bei Nichtgebrauch leicht tragen.
Schritt 1: Designprozess
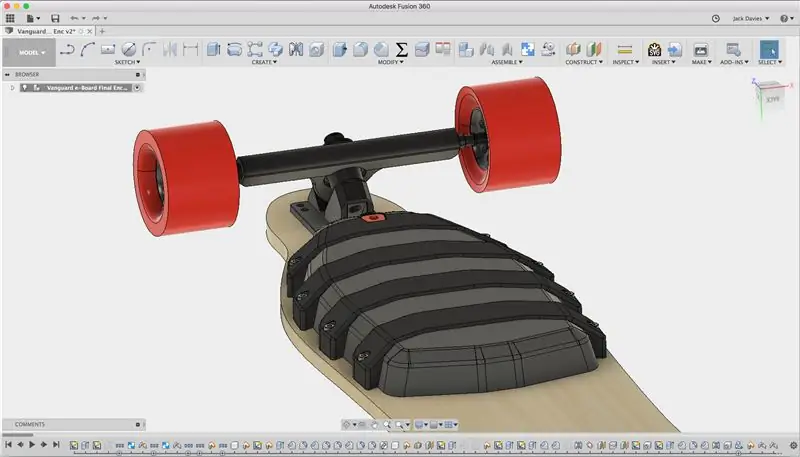
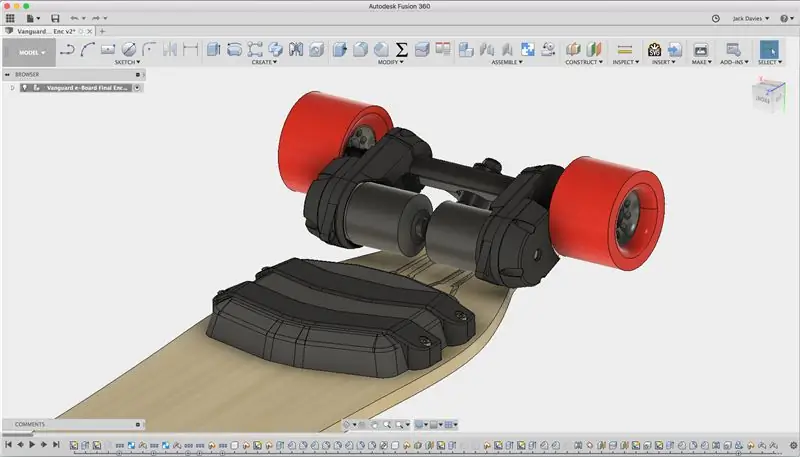
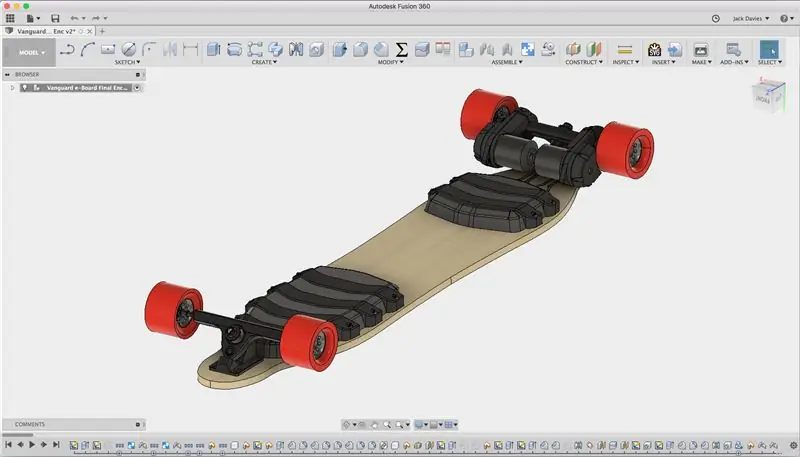
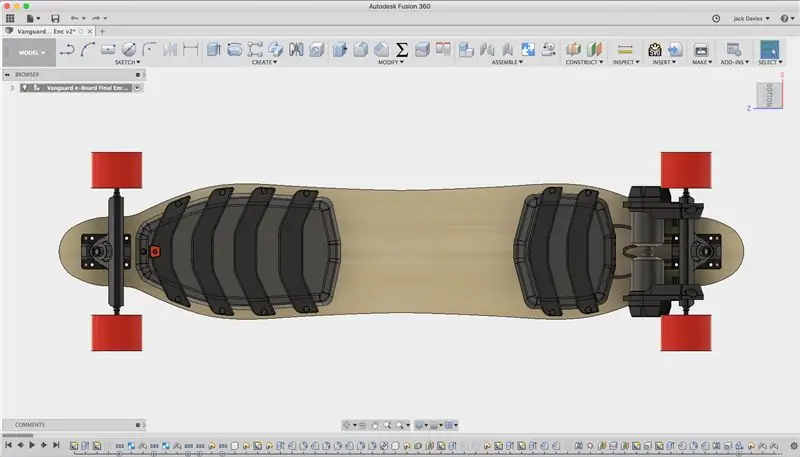
Ich begann das Projekt, indem ich die wichtigsten Standardkomponenten des Longboards identifizierte; LKW, Deck und Räder. Diese waren von der Stange, also habe ich diese als Ausgangspunkt des Designs verwendet. In der ersten Phase wurde der Antriebsstrang entwickelt, der die Motorhalterungen, das Getriebe-Setup und einige Modifikationen an den Trucks umfasste. Die Größe und Position der Motorhalterungen bestimmt die Größe und Position der Gehäuse, daher war es wichtig, dass dies zuerst abgeschlossen wurde. Ich berechnete die gewünschten Höchstgeschwindigkeits- und Drehmomentanforderungen, die es mir dann ermöglichten, die Motoren und den Akku für das Board auszuwählen. Außerdem wurde das Übersetzungsverhältnis berechnet und die Riemenscheibengrößen sowie die Antriebsriemenlänge ausgewählt. Dadurch konnte ich die richtige Größe der Motorhalterungen ermitteln, die einen gut gespannten Riemen gewährleisteten.
Der nächste Schritt bestand darin, die Gehäuse für Batterie und Geschwindigkeitsregler (ESC) zu entwerfen. Das ausgewählte Deck besteht hauptsächlich aus Bambus, ist also ziemlich flexibel und biegt sich im Wesentlichen in der Mitte. Dies hat den Vorteil des Fahrkomforts, da es die Unebenheiten der Straße absorbiert und nicht auf den Fahrer überträgt. Dies bedeutet jedoch auch, dass ein geteiltes Gehäuse benötigt wird, um die Batterie und die Elektronik unterzubringen, da ein Gehäuse in voller Länge nicht in der Lage wäre, sich mit der Platine zu biegen und während des Betriebs Kontakt mit dem Boden hätte. Die elektronischen Drehzahlregler (ESC) wurden aufgrund elektrischer Einschränkungen am nächsten an den Motoren platziert. Da die Motoren über die Drehgestelle angebaut werden, ändert sich die Position während der Drehung, so dass das Gehäuse so konstruiert werden musste, dass die Motoren frei sind.
Das Batteriesystem wurde am anderen Ende des Decks platziert und beherbergte die Elektronik für die Stromversorgung. Dazu gehörten der Akkupack, bestehend aus 20 Lithium-Ionen 18650 Zellen, das Batteriemanagementsystem, Ein-/Ausschalter und Ladebuchse.
Ich habe Autodesk Fusion360 für den gesamten Konstruktionsprozess verwendet. Mit dieser Software konnte ich schnell Komponenten innerhalb der Hauptbaugruppe modellieren, was die Entwicklungszeit erheblich beschleunigte. Ich habe auch die Simulationsfunktionen in Fusion360 verwendet, um sicherzustellen, dass die Teile stark genug sind, insbesondere die Motorhalterungen. Dadurch konnte ich die Größe der Halterungen tatsächlich reduzieren, da ich die Festigkeits- und Durchbiegungsanforderungen überprüfen und Material entfernen konnte, während gleichzeitig ein angemessener Sicherheitsfaktor beibehalten wurde. Nach Abschluss des Konstruktionsprozesses war es sehr einfach, die Einzelteile für den 3D-Druck zu exportieren.
Schritt 2: Antrieb
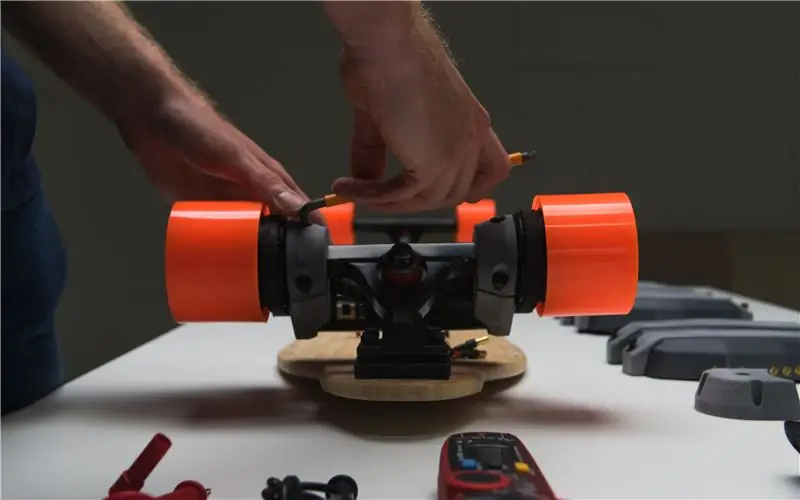
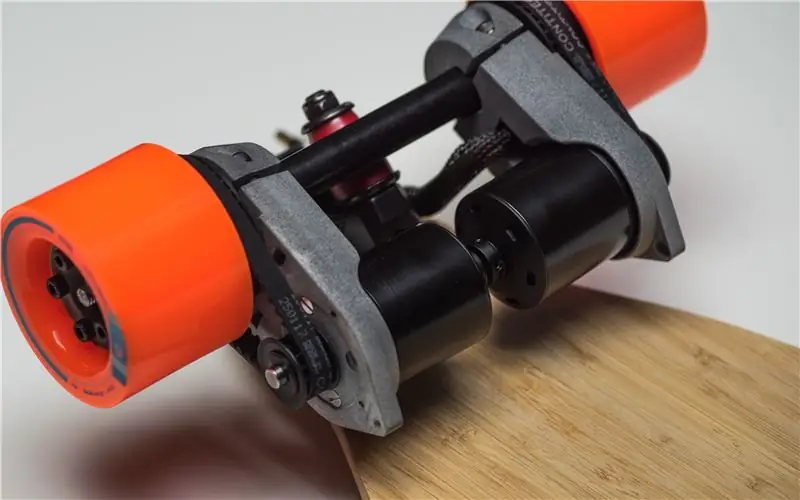
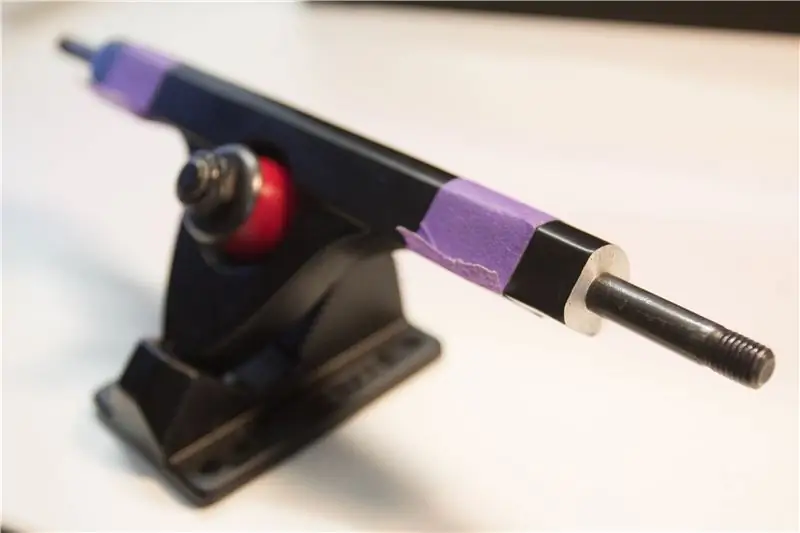
Ich habe zuerst den Bau des Antriebsstrangs abgeschlossen, um einen angemessenen Abstand für das Elektronikgehäuse zu gewährleisten. Ich habe Calibre Trucks ausgewählt, da sie ein quadratisches Profil haben, das sich perfekt zum Festklemmen der Motorhalterungen eignet. Die Achse war jedoch etwas zu kurz, um die beiden Motoren auf demselben LKW verwenden zu können, daher musste ich diese verlängern, damit die Räder passen.
Ich erreichte dies, indem ich einen Teil des Aluminium-LKW-Aufhängungskörpers kürzte und mehr von der Stahlachse freilegte. Dann schneide ich den größten Teil der Achse ab und lasse etwa 10 mm übrig, die ich dann mit einem M8-Stempel einfädeln könnte.
Dann könnte eine Kupplung aufgeschraubt und eine weitere Gewindeachse hinzugefügt werden, wodurch die Achse effektiv verlängert wird. Ich habe Loctite 648 Befestigungsmittel verwendet, um die Kupplung und die neue Achse dauerhaft zu sichern, um sicherzustellen, dass sie sich während des Gebrauchs nicht lösen. Dadurch passten die beiden Motoren auf den LKW und bot viel Freiraum für die Räder.
Der Antriebsstrang wurde hauptsächlich mit der HP Multi-Jet Fusion-Technologie gedruckt, um Steifigkeit und Festigkeit bei hohen Beschleunigungs- und Bremsvorgängen zu gewährleisten, bei denen die größten Kräfte übertragen würden.
Eine spezielle Riemenscheibe wurde entwickelt, um in die Hinterräder einzurasten, die dann mit einem HTD 5M-Riemen mit der Motorriemenscheibe verbunden wurde. Eine 3D-gedruckte Abdeckung wurde hinzugefügt, um die Riemenscheibenbaugruppe zu schützen.
Schritt 3: Rippengehäuse
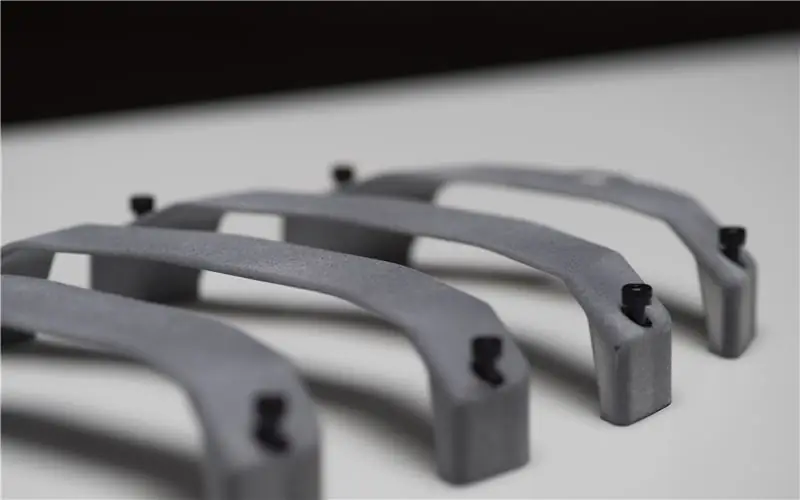
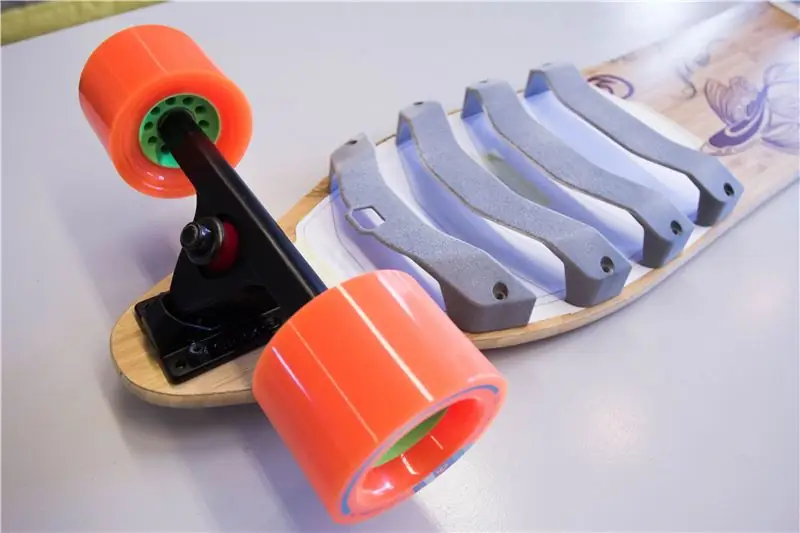
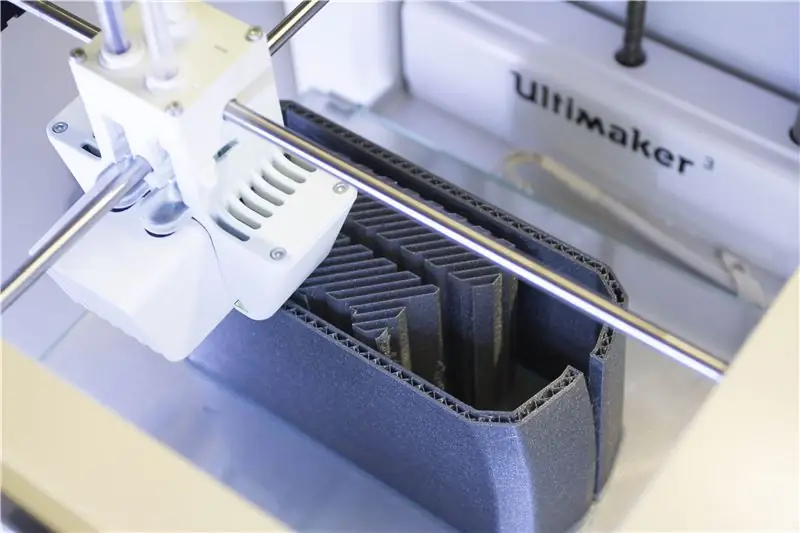
Eine der wichtigsten Designentscheidungen, die ich getroffen habe, war die Trennung der Gehäuse, was zu einem sauberen Aussehen führte und es dem flexiblen Deck ermöglichte, ohne zusätzliche Steifigkeit der Gehäuse zu funktionieren. Ich wollte die funktionalen Aspekte der HP Multi Jet Fusion-Technologie vermitteln, also entschied ich mich, den Hauptkörper der Gehäuse mit FDM zu drucken, was die Kosten senkte, und verwendete dann die HP-Teile, um sie zu stützen und an das Deck zu klemmen. Dies sorgte für eine interessante Ästhetik und war gleichzeitig sehr funktional.
Die mit FDM bedruckten Gehäuse wurden in zwei Hälften geteilt, um den Druck zu erleichtern, da Trägermaterial von der Außenfläche entfernt werden konnte. Die Trennlinie wurde sorgfältig positioniert, um sicherzustellen, dass sie beim Anklemmen an die Platine vom HP-Teil verdeckt wird. Löcher für die Motoranschlüsse wurden hinzugefügt und vergoldete Rundstecker wurden angeklebt
Gewindeeinsätze wurden in das Bambusdeck eingebettet, um die Gehäuse an der Diele zu befestigen, und wurden bündig mit der Brettoberfläche geschliffen, um sicherzustellen, dass zwischen Deck und Gehäuse kein Spalt vorhanden war.
Schritt 4: Elektronik
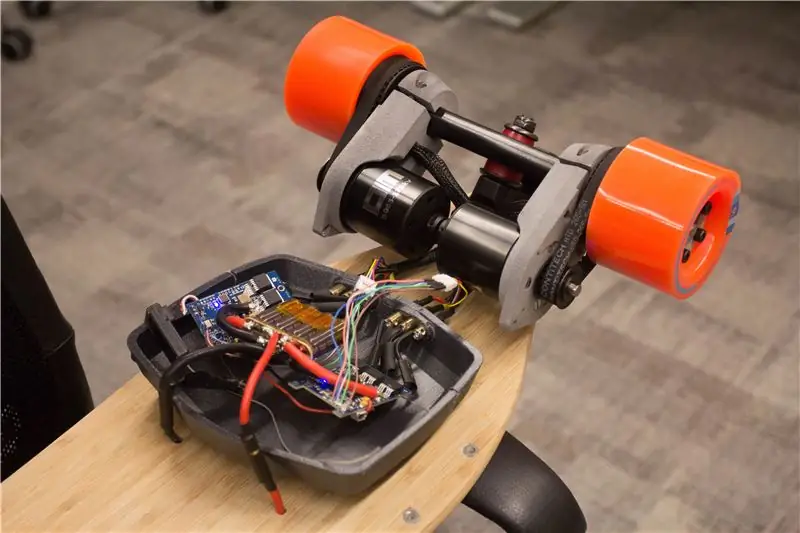
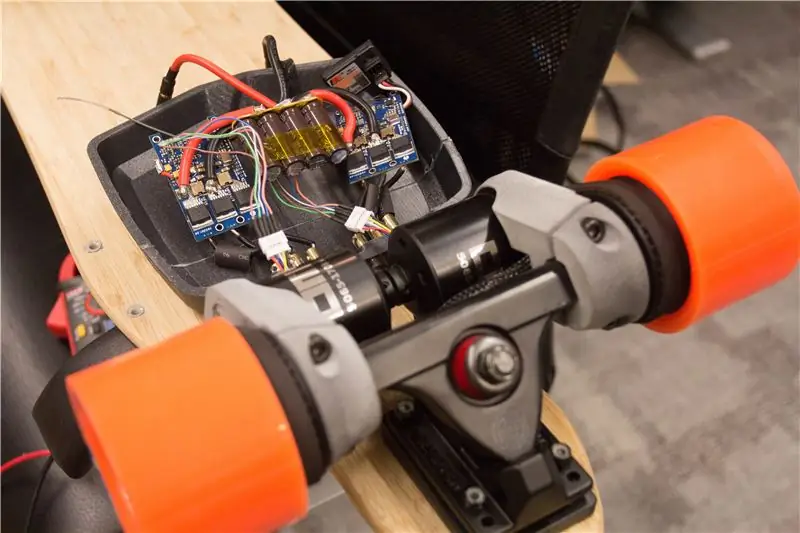
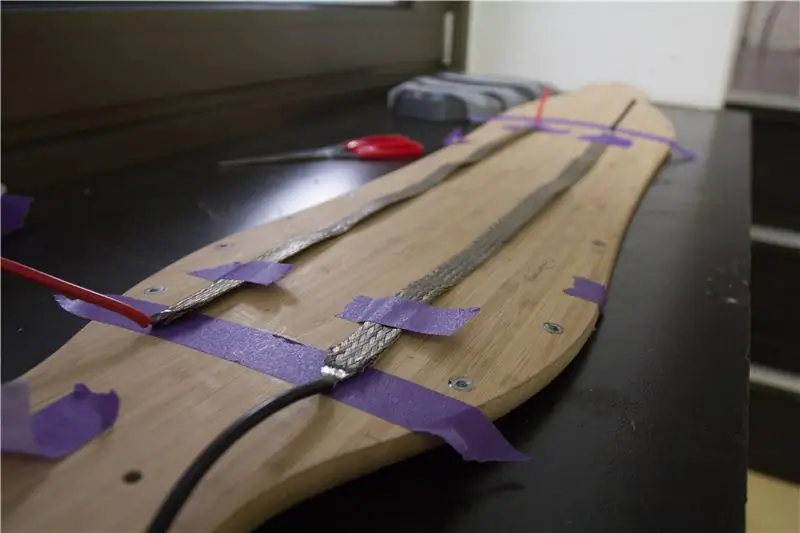
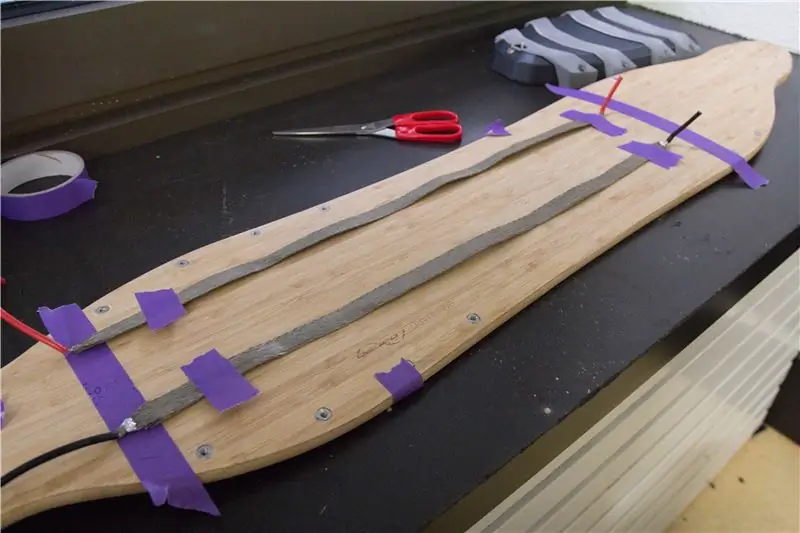
Die Elektronik wurde sorgfältig ausgewählt, um sicherzustellen, dass das Board leistungsstark, aber auch intuitiv zu bedienen ist. Diese Platine könnte potenziell gefährlich sein, wenn Fehlfunktionen auftreten, daher ist die Zuverlässigkeit ein sehr wichtiger Faktor.
Der Akku besteht aus 20 einzelnen 18650 Lithium-Ionen-Zellen, die zu einem 42-V-Paket punktgeschweißt sind. 2 Zellen werden parallel und 10 in Reihe geschweißt; Die Zellen, die ich verwendet habe, waren Sony VTC6. Ich habe einen Punktschweißer verwendet, um die Nickellaschen zu schweißen, um die Packung zu bilden, da das Löten zu viel Hitze erzeugt, die die Zelle beschädigen kann.
Der Strom aus dem Batteriegehäuse wurde mit einem flachen geflochtenen Kabel, das direkt unter dem Griffband auf der Oberseite des Decks geführt wurde, auf die Geschwindigkeitsreglerbox übertragen. Dadurch konnten die Kabel „versteckt“werden und es war nicht mehr erforderlich, Kabel an der Unterseite zu verlegen, die hässlich ausgesehen hätten.
Da es sich um eine Dual-Motor-Platine handelt, sind zwei Drehzahlregler erforderlich, um jeden Motor unabhängig voneinander zu steuern. Ich habe den VESC-Geschwindigkeitsregler für diesen Build verwendet, einen Controller, der speziell für elektrische Skateboards entwickelt wurde, was ihn für diesen Einsatz sehr zuverlässig macht.
Die verwendeten Motoren sind 170kv 5065-Außenläufer, die jeweils 2200W produzieren können, was für dieses Board eine Menge Leistung ist. Mit dem aktuellen Getriebe-Setup beträgt die maximale Geschwindigkeit des Boards etwa 35 MPH und beschleunigt sehr schnell.
Der letzte Schritt bestand darin, eine Fernbedienung zu erstellen, um das Board zu steuern. Aufgrund der einfacheren Bedienung wurde ein drahtloses System bevorzugt. Es war jedoch wichtig, eine hohe Zuverlässigkeit der Übertragung zu gewährleisten, da ein Kommunikationsausfall ernsthafte Sicherheitsprobleme verursachen könnte, insbesondere bei hohen Geschwindigkeiten. Nachdem ich einige Funkübertragungsprotokolle getestet hatte, entschied ich, dass die 2,4-GHz-Funkfrequenz für dieses Projekt am zuverlässigsten wäre. Ich benutzte einen handelsüblichen RC-Autosender, reduzierte jedoch die Größe erheblich, indem ich die Elektronik in ein kleines Handgehäuse überführte, das 3D-gedruckt wurde.
Schritt 5: Fertiges Board & Promo-Video
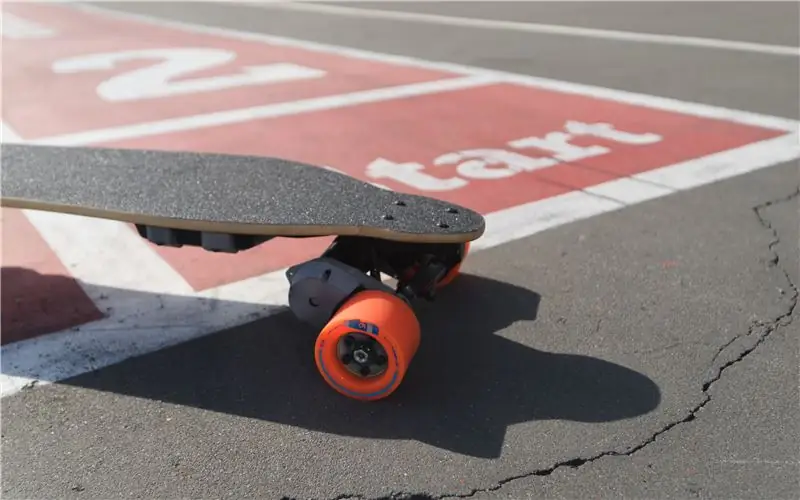
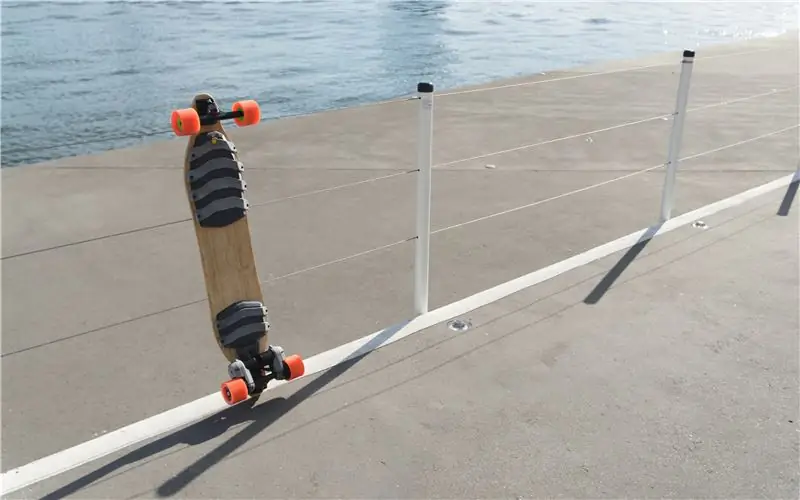
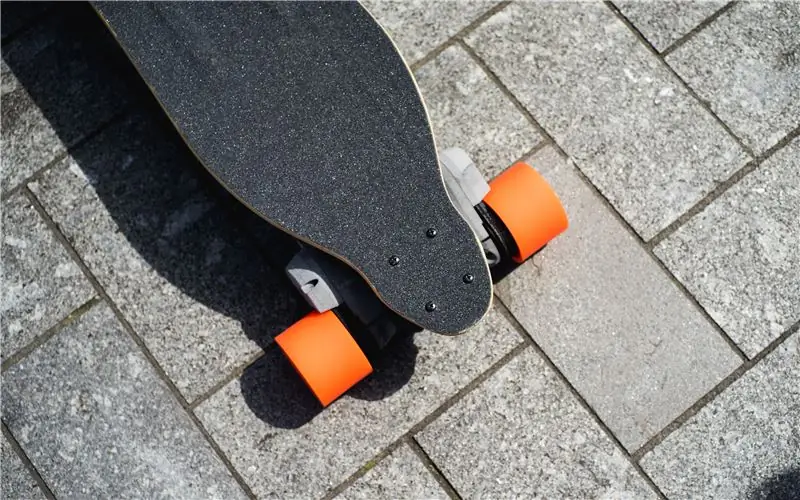
Das Projekt ist nun abgeschlossen! Wir haben ein ziemlich tolles Video des Boards in Aktion erstellt, Sie können es sich unten ansehen. Vielen Dank an 3D Hubs, die mir die Durchführung dieses Projekts ermöglicht haben - sehen Sie sich hier alle Ihre 3D-Druckanforderungen an! 3dhubs.com
Empfohlen:
DIY Circuit Activity Board mit Büroklammern - HERSTELLER - STEM: 3 Schritte (mit Bildern)
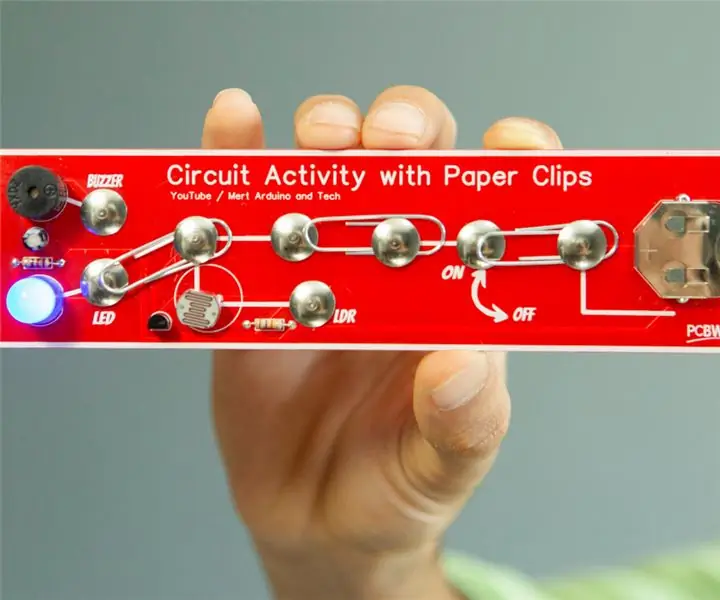
DIY Circuit Activity Board mit Büroklammern | HERSTELLER | STEM: Mit diesem Projekt können Sie den Weg des elektrischen Stroms ändern, um durch verschiedene Sensoren zu laufen. Mit diesem Design können Sie zwischen dem Aufleuchten einer blauen LED oder dem Aktivieren eines Summers wechseln. Sie haben auch die Wahl, einen lichtabhängigen Widerstand mit
Ein günstiges Attiny Arduino Board herstellen – wikiHow
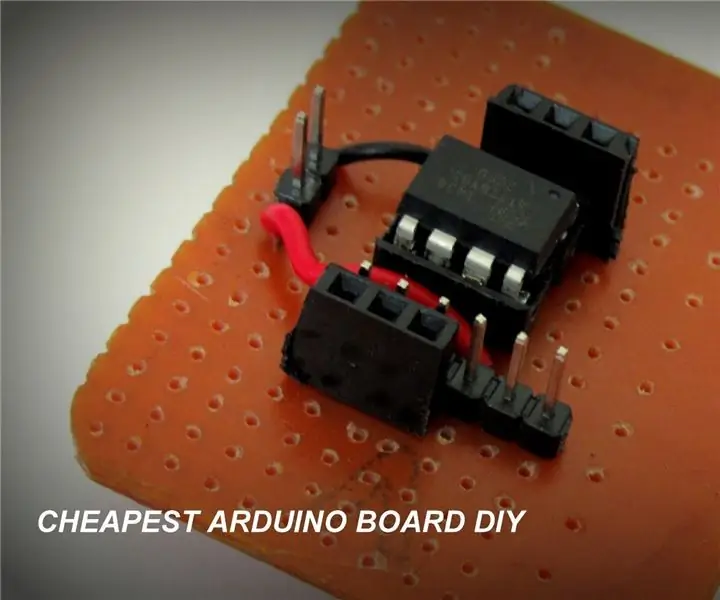
Wie man ein billiges Attiny Arduino Board herstellt: Nun, die meiste Zeit bekomme ich Probleme, wenn ich Arduino in einigen Projekten benötige, bei denen ich nur wenige I / O-Pins benötige 85/45Arduino-Tiny ist ein Open-Source-Set von ATtiny
Ein elektrisches Longboard mit Telefonsteuerung bauen – wikiHow
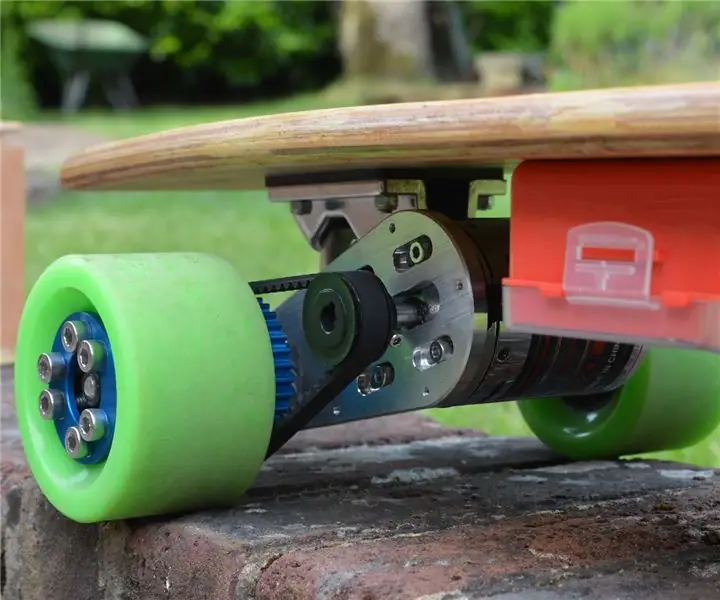
So bauen Sie ein elektrisches Longboard mit Telefonsteuerung: Elektrische Longboards sind der Hammer! TESTEN SIE DAS FOOTAGE IM OBENEN VIDEO, WIE MAN EIN ELEKTRISCHES LONGBOARD MIT BLUETOOTH STEUERT ERSTELLT mehr Speed aus dem Bo
So verwenden Sie das Webtool in Fusion 360: 5 Schritte
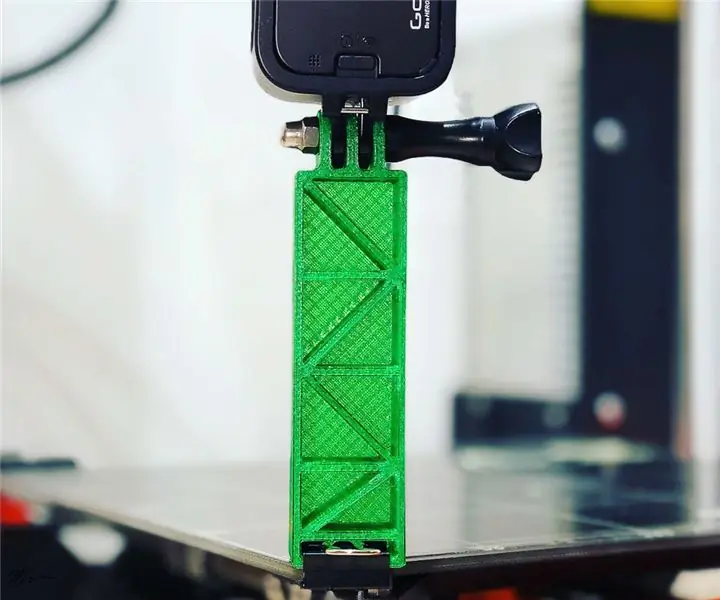
So verwenden Sie das Web-Tool in Fusion 360: Es ist eines dieser unterschätzten Tools, die Sie wahrscheinlich nicht verwenden, aber lesen Sie weiter und Sie werden sehen, warum Sie das Web-Tool in Fusion 360 nutzen müssen. Das Web-Tool bietet eine schnelle und super effiziente Möglichkeit, Kreuzstreben zu
Exportieren einer SVG-Datei in Fusion 360: 5 Schritte (mit Bildern)
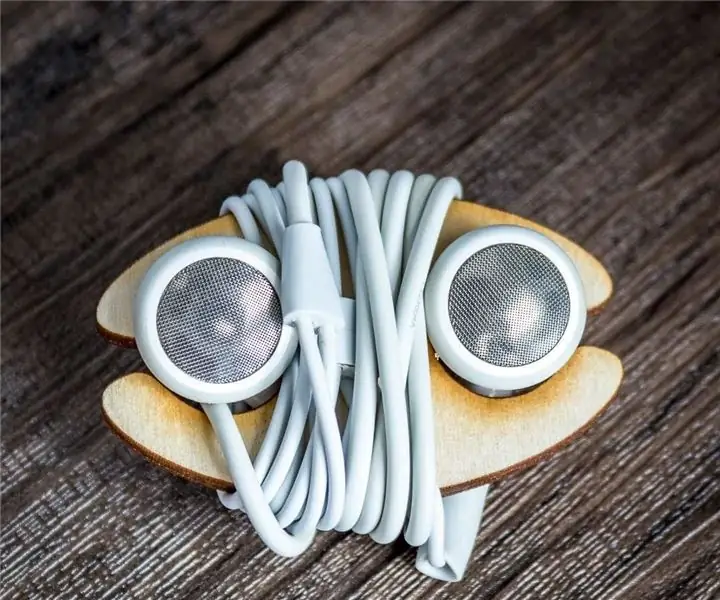
Exportieren einer SVG-Datei in Fusion 360: Ein Freund hat kürzlich einen neuen Laserschneider gekauft und mich gefragt, wie man mit Fusion 360 SVG-Dateien exportiert. Ich schlug vor, stattdessen einfach DXF-Dateien zu exportieren, aber es stellte sich heraus, dass die von ihm gekaufte Lasermarke nur SVG-Dateien akzeptiert. Das war das gleiche Problem wie ich