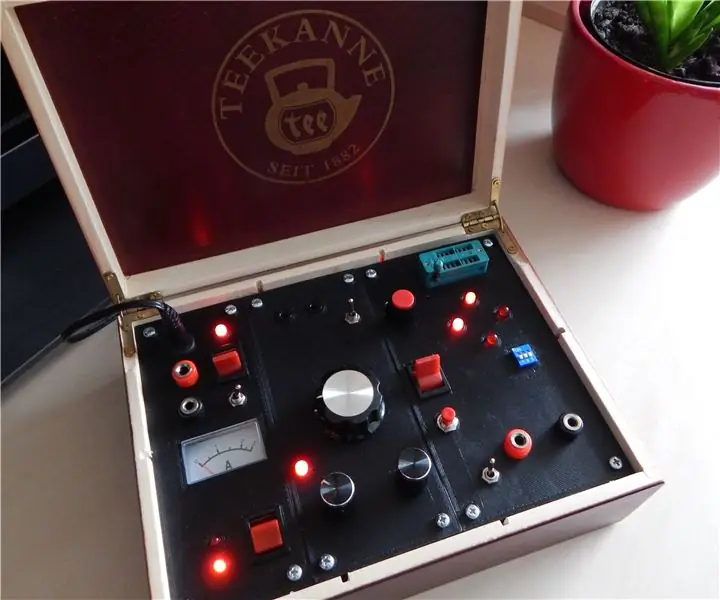
Inhaltsverzeichnis:
- Schritt 1: DC- und Stepper-Steuerungstheorie
- Schritt 2: Schaltplan
- Schritt 3: Schaltpläne
- Schritt 4: Notwendige Komponenten und Werkzeuge
- Schritt 5: Frontplattendesign
- Schritt 6: 3D-Druck und Sprühlackierung
- Schritt 7: Panelverkabelung
- Schritt 8: Panel-Board-Anschlüsse
- Schritt 9: PCB
- Schritt 10: Arduino
- Schritt 11: Montage und Prüfung
- Schritt 12: Outro
2025 Autor: John Day | [email protected]. Zuletzt bearbeitet: 2025-01-23 12:52

Vor ein paar Monaten gab mir ein Freund von mir ein paar ausrangierte Tintenstrahldrucker und Kopierer. Ich war daran interessiert, ihre Stromquelleneinheiten, Kabel, Sensoren und insbesondere Motoren zu ernten. Ich rettete, was ich konnte und wollte alle Teile testen, um sicherzustellen, dass sie funktionstüchtig sind. Einige Motoren wurden mit 12 V bewertet, einige mit 5 V, einige waren Schrittmotoren und andere waren Gleichstrommotoren. Wenn ich nur ein Gerät hätte, bei dem ich einfach den Motor anschließen, die Frequenz, das Tastverhältnis einstellen und eine Schrittmethode auswählen könnte, um es zu testen.
Ich beschloss, es ohne digitalen Signalprozessor oder Mikrocontroller zu bauen. Der bescheidene 555 oder tl741 als Oszillator, 4017 Zähler und viele Logikgatter für Schrittmotormodi. Am Anfang hatte ich viel Spaß beim Entwerfen der Schaltung, sowie beim Designen der Frontplatte für das Gerät. Ich habe eine anständige Teekiste aus Holz gefunden, in die ich alles hineinlegen kann. Ich habe die Schaltung in vier Teile unterteilt und angefangen, sie auf einem Steckbrett zu testen. Bald zeigten sich die ersten Anzeichen von Frustration. Es war eine Katastrophe. Viele Gates, viele ICs, Drähte. Es hat nicht richtig funktioniert und ich habe zwischen zwei Möglichkeiten überlegt: Ganz einfach machen - nur für Gleichstrommotoren, oder beiseite legen und manchmal später fertig machen … Ich habe mich für die zweite Option entschieden.
Schritt 1: DC- und Stepper-Steuerungstheorie
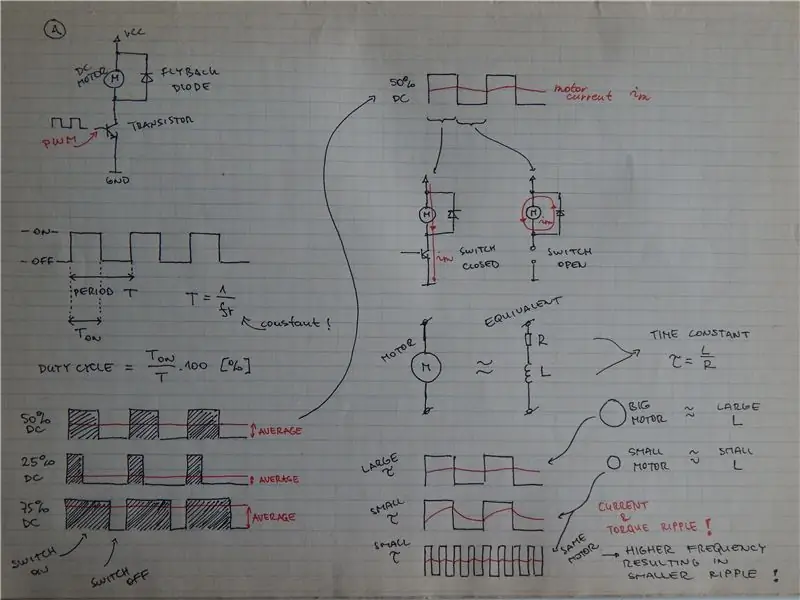
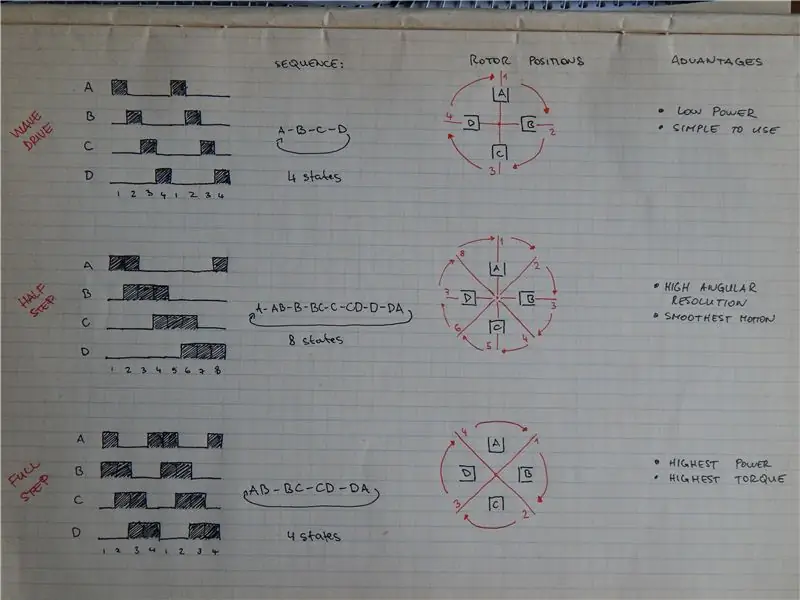
Gleichspannungs Motor
Die gebräuchlichste Art, einen Gleichstrommotor zu steuern, ist die sogenannte Pulsweitenmodulation (PWM). PWM wird auf einen bestimmten Schalter angewendet und schaltet den Motor ein und aus. Im Bild sehen Sie die angezeigte Schaltzeit und ihr Verhältnis zur Frequenz, auch die Schaltzeit ist angegeben. Die Einschaltdauer ist definiert als die Schaltzeit geteilt durch die Gesamtperiode. Wenn wir die Frequenz konstant halten, besteht die einzige Möglichkeit, das Tastverhältnis zu ändern, darin, die Einschaltzeit zu ändern. Durch die Erhöhung des Tastverhältnisses erhöht sich auch der Mittelwert der am Motor anliegenden Spannung. Aufgrund der höheren Spannung fließt ein höherer Strom durch den Gleichstrommotor und der Rotor dreht sich schneller.
Aber welche Frequenz soll man wählen? Um diese Frage zu beantworten, schauen wir uns genauer an, was ein Gleichstrommotor eigentlich ist. Äquivalent kann es als RL-Filter beschrieben werden (wobei die Gegen-EMK nur für einen Moment vernachlässigt wird). Wird an den Motor eine Spannung angelegt (RL-Filter), steigt der Strom mit einer Zeitkonstanten tau gleich L / R an. Bei der PWM-Steuerung steigt bei geschlossenem Schalter der durch den Motor fließende Strom und verringert sich während der Zeit, in der der Schalter ausgeschaltet ist. An diesem Punkt hat der Strom die gleiche Richtung wie zuvor und fließt durch die Rücklaufdiode. Motoren mit höherer Leistung haben eine höhere Induktivität und damit eine höhere Zeitkonstante als kleinere Motoren. Ist die Frequenz beim Bestromen des Kleinmotors niedrig, nimmt der Strom während der Ausschaltzeit schnell ab, gefolgt von einem starken Anstieg während der Einschaltzeit. Diese Stromwelligkeit verursacht auch eine Welligkeit des Motordrehmoments. Das wollen wir nicht. Daher sollte bei der Versorgung kleinerer Motoren die PWM-Frequenz höher sein. Dieses Wissen werden wir in späteren Schritten beim Design verwenden.
Schrittmotor
Wenn wir einen unipolaren Schrittmotor steuern möchten, der in der Hobbyelektronik verwendet wird, haben wir die Wahl zwischen 3 grundlegenden Steueroptionen (Modi) - Wave Drive (WD), Half Step (HS) und Full Step (FS). Die Reihenfolge der einzelnen Modi und die Position des Rotors ist in der Abbildung angegeben (der Einfachheit halber habe ich einen Motor mit zwei Polpaaren angegeben). In diesem Fall bewirken Wave Drive und Full Step eine Drehung des Rotors um 90 Grad und können durch Wiederholen von 4 Zuständen erreicht werden. Im Half Step-Modus benötigen wir eine Sequenz von 8 Zuständen.
Die Wahl des Modus hängt von den Anforderungen des Systems ab - wenn wir ein großes Drehmoment benötigen, ist Full Step die beste Wahl, wenn ein niedrigeres Drehmoment ausreicht und wir unsere Schaltung möglicherweise aus der Batterie versorgen, wird der Wellenantriebsmodus bevorzugt. Bei Anwendungen, bei denen die höchste Winkelauflösung und die sanfteste Bewegung erreicht werden soll, ist der Half Drive-Modus die ideale Wahl. Das Drehmoment ist in diesem Modus etwa 30 % niedriger als im Full Drive-Modus.
Schritt 2: Schaltplan
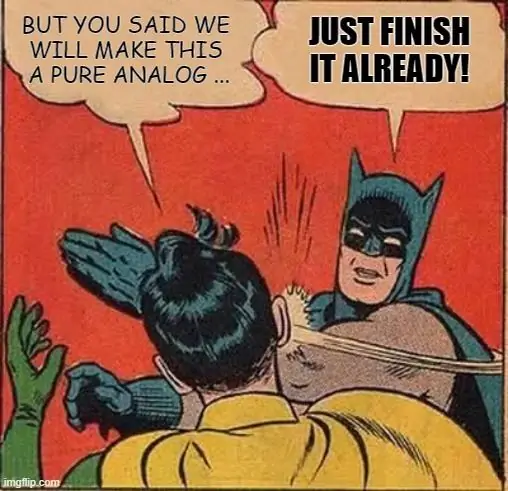
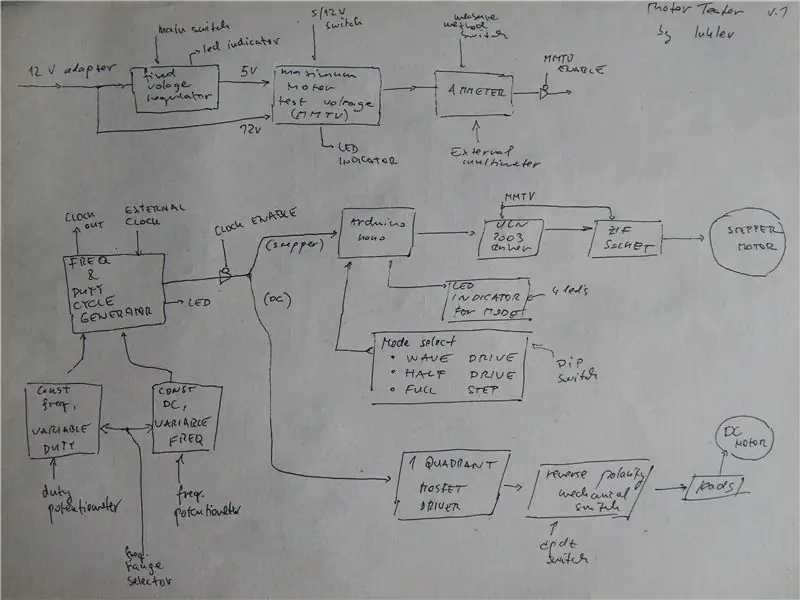
Dieses einfache Meme beschreibt treffend meinen Denkprozess während des Designs.
Der obere Teil des Diagramms beschreibt die Stromversorgung - ein 12-Volt-Adapter, der durch einen Linearregler auf 5 Volt reduziert wird. Ich wollte die maximale Prüfspannung des Motors (MMTV) wählen können - entweder 12 oder 5 Volt. Das eingebaute Amperemeter umgeht die Steuerkreise und misst nur den Motorstrom. Praktisch wäre auch, mit einem Multimeter zwischen interner und externer Strommessung umschalten zu können.
Der Oszillator arbeitet in zwei Modi: Der erste ist eine konstante Frequenz und ein variabler Arbeitszyklus, und der zweite ist eine variable Frequenz. Beide Parameter können über Potentiometer eingestellt werden, und ein Drehschalter wird die Modi und Bereiche umschalten. Das System wird auch eine Umschaltung zwischen interner und externer Uhr über einen 3,5-mm-Klinkenanschluss enthalten. Auch die interne Uhr wird über eine 3,5-mm-Klinke mit dem Panel verbunden. Ein Schalter und eine Taste zum Aktivieren/Deaktivieren der Uhr. Der DC-Motortreiber wird ein Einquadranten-N-Kanal-Mosfet-Treiber sein. Die Richtungsänderung erfolgt über den mechanischen dpdt-Schalter. Motorkabel werden über Bananenbuchsen angeschlossen.
Die Schrittmotorsequenz wird von einem Arduino gesteuert, das auch 3 vom Dip-Schalter angegebene Steuermodi erkennt. Der Treiber des Schrittmotors wird uln2003 sein. Der Arduino steuert auch 4 LEDs, die die Animation der angetriebenen Motorwicklungen in diesen Modi darstellen. Der Schrittmotor wird über eine ZIF-Buchse mit dem Tester verbunden.
Schritt 3: Schaltpläne
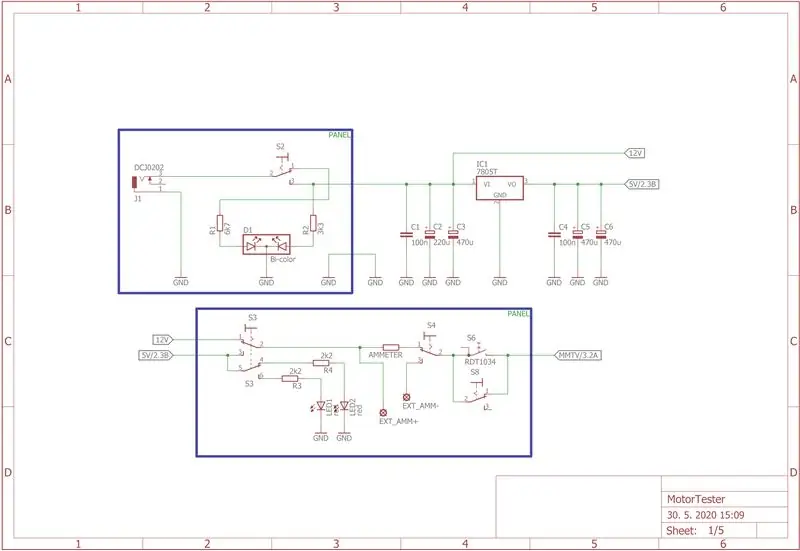
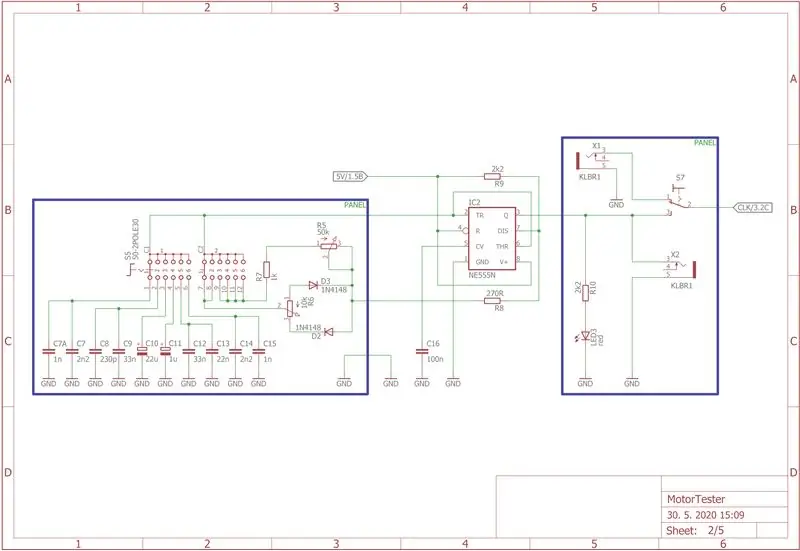
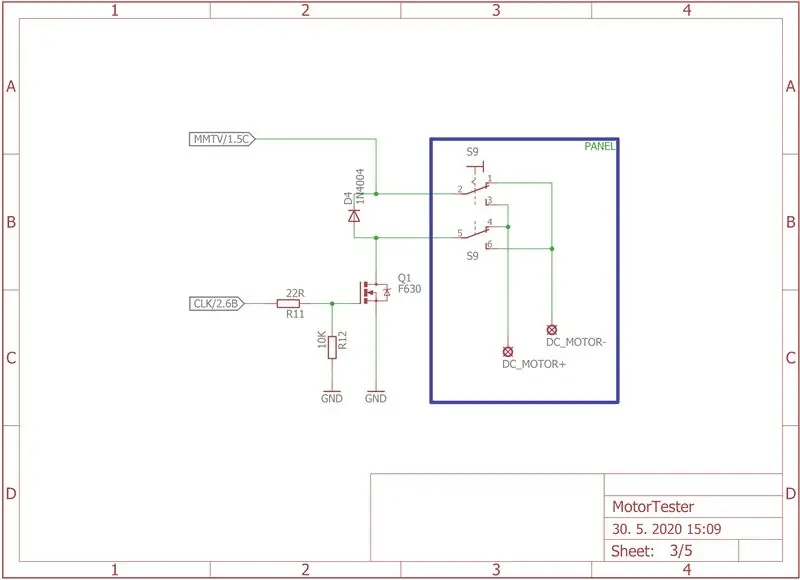
Die Schaltpläne sind in fünf Teile gegliedert. Die in blauen Kästchen eingerahmten Schaltkreise stellen die Komponenten dar, die sich auf dem Panel befinden werden.
- Energieversorgung
- Oszillator
- DC-Treiber
- Arduino Stepper-Treiber
- Logic Gates Stepper-Treiber
Blatt-Nr. 5 ist der Grund, warum ich dieses Projekt liegen ließ. Diese Schaltungen bilden Sequenzen für die zuvor erwähnten Steuermodi - WD, HS und FS. Dieser Teil wird in Blatt Nr. vollständig durch Arduino ersetzt. 4. Vollständige Eagle-Schaltpläne sind ebenfalls beigefügt.
Schritt 4: Notwendige Komponenten und Werkzeuge

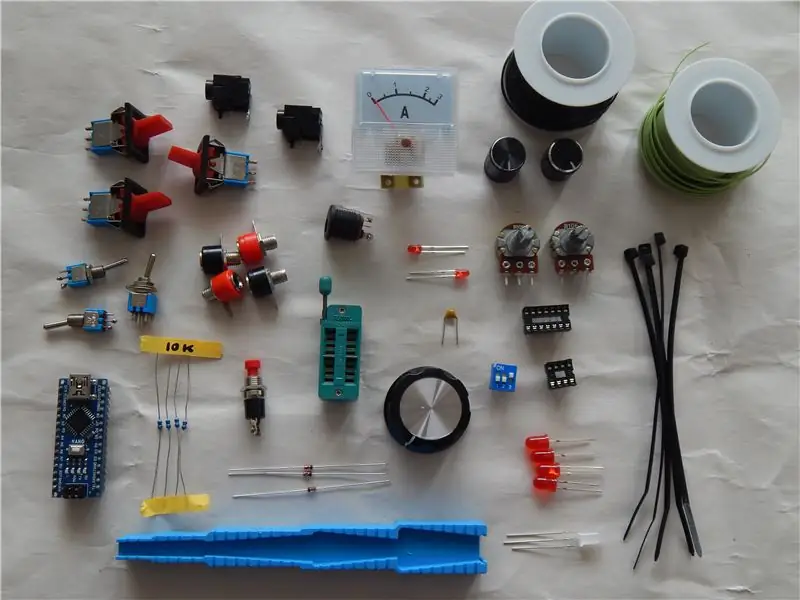
Notwendige Komponenten und Werkzeuge:
- Multimeter
- Bremssattel
- Kartonschneider
- Marker
- Pinzette
- Feine Zange
- Schneidezange
- Abisolierzange
- Lötkolben
- Lot
- Kolophonium
- Drähte (24 AWG)
- 4x SPDT-Schalter
- 2x dpdt-Schalter
- 4x Bananenbuchse
- Druckknopf
- ZIF-Buchse
- 2x 3,5 mm Klinke
- DC-Anschluss
- Arduino Nano
- 3-poliger DIP-Schalter
- 2x 3 mm LED
- 5x 5 mm LED
- Zweifarbige LED
- Potentiometerknöpfe
- DIP-Buchsen
- Universal-Leiterplatte
- Dupont-Anschlüsse
- Kabelbinder aus Kunststoff
Und
- Potentiometer
- Widerstände
- Kondensatoren
mit Ihren gewählten Werten, entsprechend den Frequenzbereichen und der Helligkeit der LEDs.
Schritt 5: Frontplattendesign
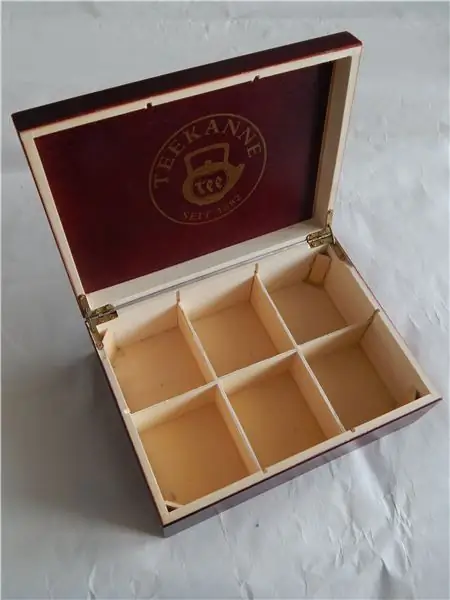
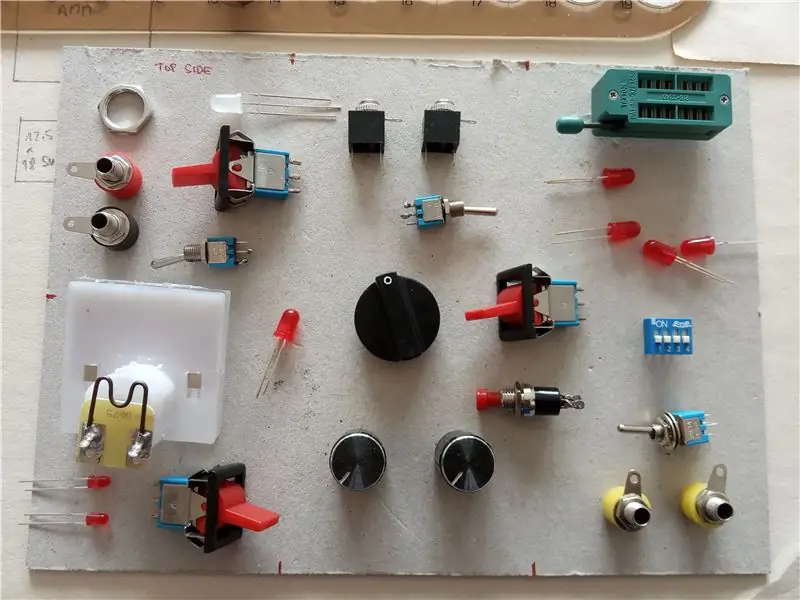
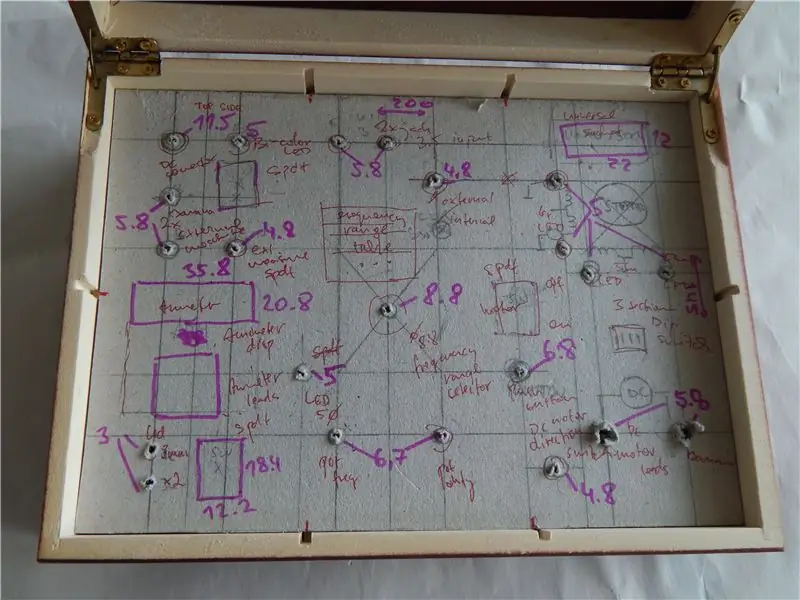
Der Tester wurde in eine alte hölzerne Teekiste gelegt. Zuerst habe ich die Innenmaße gemessen und dann aus Hartkarton ein Rechteck ausgeschnitten, das als Vorlage für die Platzierung von Bauteilen diente. Als ich mit der Platzierung der Teile zufrieden war, habe ich jede Position erneut gemessen und in Fusion360 ein Panel-Design erstellt. Ich habe das Panel zur Vereinfachung des 3D-Drucks in 3 kleinere Teile unterteilt. Ich habe auch einen L-förmigen Halter entworfen, um die Paneele an den Innenseiten der Box zu befestigen.
Schritt 6: 3D-Druck und Sprühlackierung
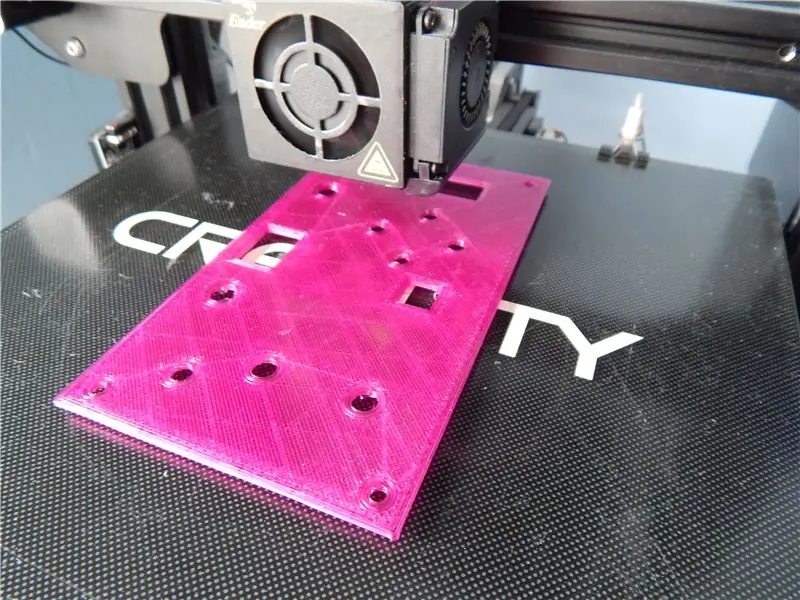
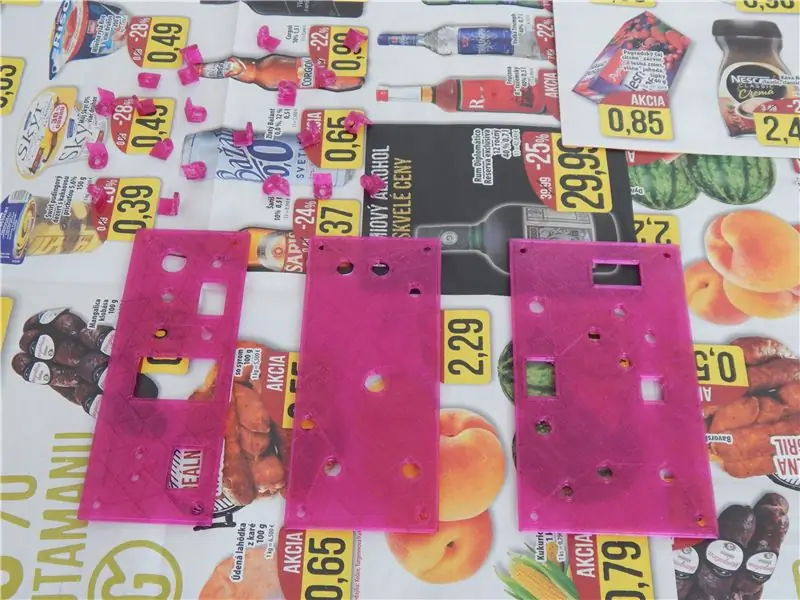
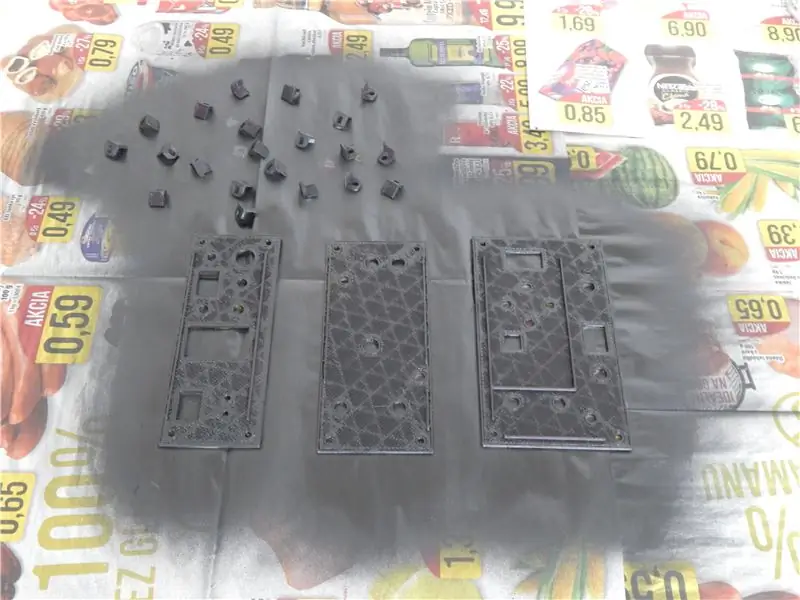
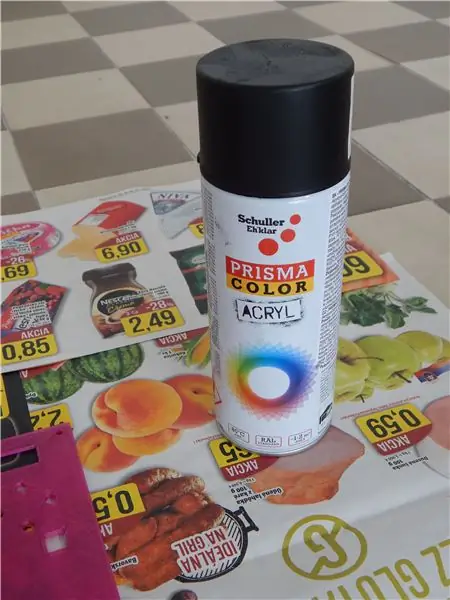
Die Platten wurden mit einem Ender-3 Drucker bedruckt, aus dem Restmaterial, das ich zu Hause hatte. Es war ein transparentes rosa Petg. Nach dem Druck habe ich die Platten und Halter mit mattschwarzer Acrylfarbe besprüht. Für eine vollständige Abdeckung habe ich 3 Schichten aufgetragen, sie einige Stunden zum Trocknen und Lüften für etwa einen halben Tag draußen gelegt. Seien Sie vorsichtig, Lackdämpfe können schädlich sein. Verwenden Sie sie immer nur in einem belüfteten Raum.
Schritt 7: Panelverkabelung
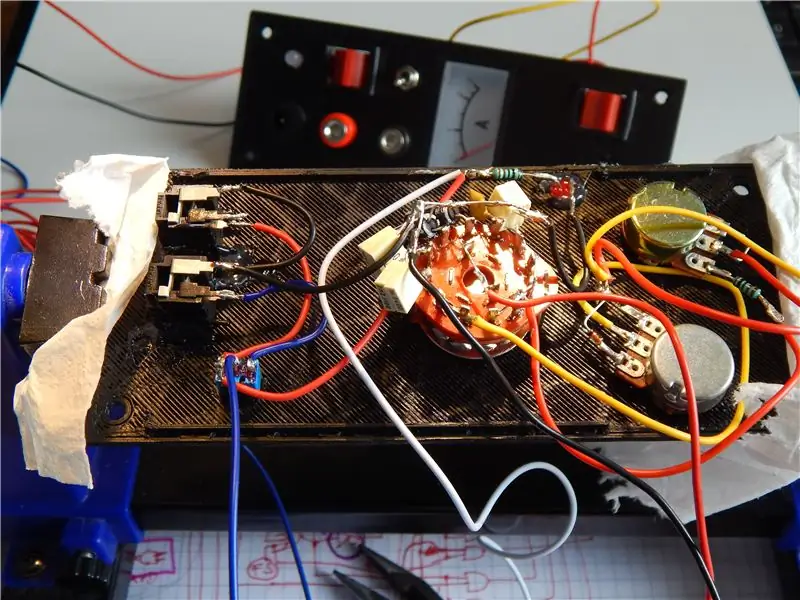
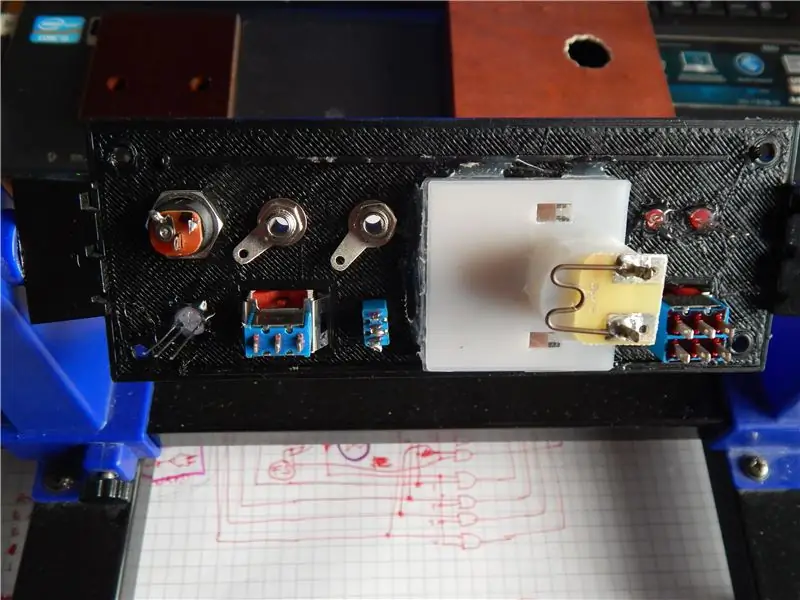
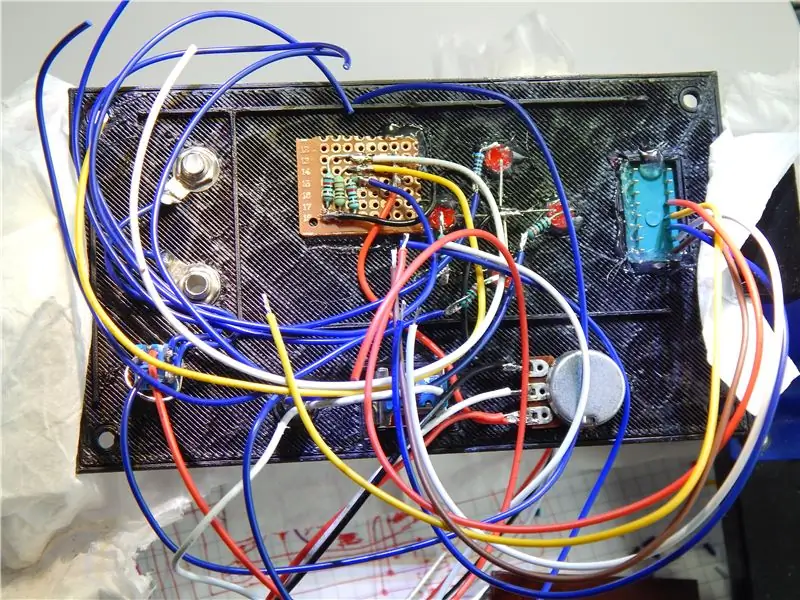
Persönlich mein Lieblingsteil, aber der zeitaufwendigste Teil (ich entschuldige mich im Voraus, dass ich die Schrumpfschläuche nicht verwendet habe, ich war in einer Zeitnot - sonst würde ich sie definitiv verwenden).
Verstellbare Halterungen helfen sehr bei der Montage und Handhabung von Paneelen. Es ist auch möglich, die sogenannte dritte Hand zu verwenden, aber ich bevorzuge den Halter. Die Griffe habe ich mit einem Textiltuch abgedeckt, damit die Platte bei der Arbeit nicht zerkratzt wird.
Ich habe alle Schalter und Potentiometer, LEDs und andere Anschlüsse in das Panel eingesetzt und verschraubt. Anschließend schätzte ich die Länge der Drähte, die die Komponenten auf dem Panel verbinden, und auch die, die zum Anschluss an die Leiterplatte verwendet werden. Diese sind in der Regel etwas länger und es ist gut, sie ein wenig zu verlängern.
Beim Löten von Steckverbindern verwende ich fast immer flüssiges Lötflussmittel. Ich trage eine kleine Menge auf den Stift und dann auf und verbinde ihn mit dem Draht. Flussmittel entfernt oxidiertes Metall von den Oberflächen und erleichtert das Löten der Verbindung.
Schritt 8: Panel-Board-Anschlüsse
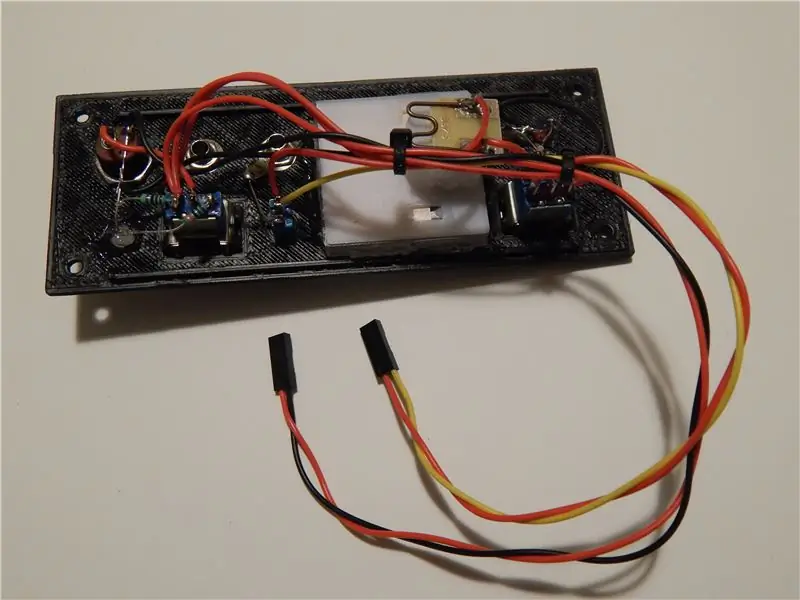
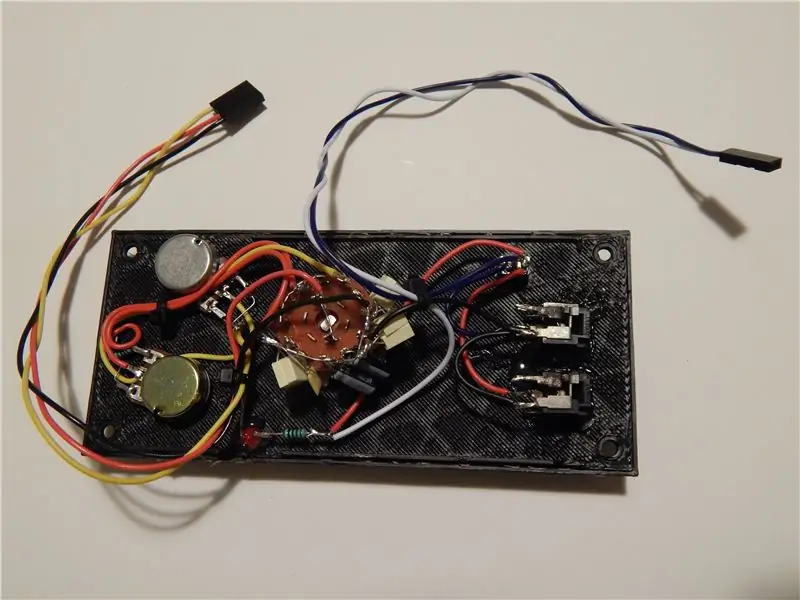
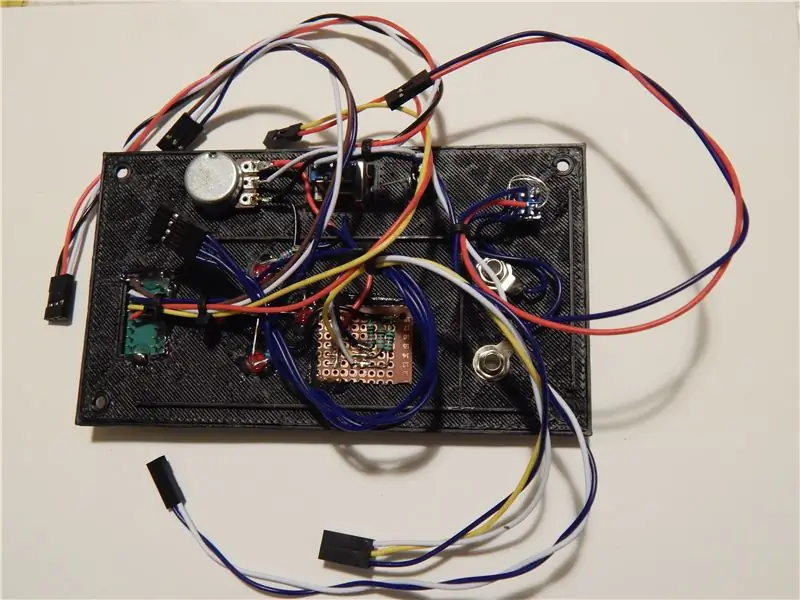
Um das Panel mit der Platine zu verbinden, habe ich Dupont-Steckverbinder verwendet. Sie sind weit verbreitet, günstig und vor allem klein genug, um bequem in die gewählte Box zu passen. Die Kabel sind nach dem Schema paarweise, Dreier- oder Viererkabel angeordnet. Sie sind farbcodiert, um sie leicht zu identifizieren und einfach anzuschließen. Gleichzeitig ist es für die Zukunft praktisch, sich nicht in einem einheitlichen Kabelgewirr zu verlieren. Abschließend werden sie mit Kunststoffkabelbindern mechanisch gesichert.
Schritt 9: PCB
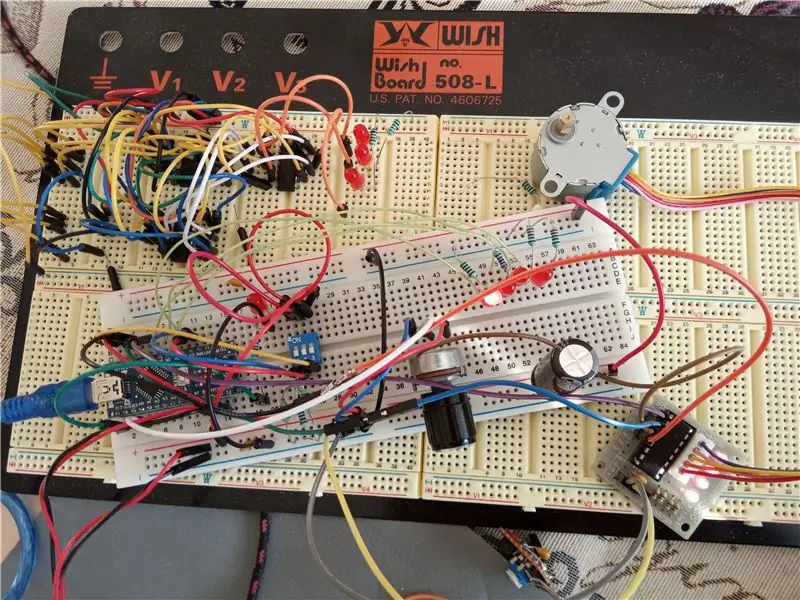
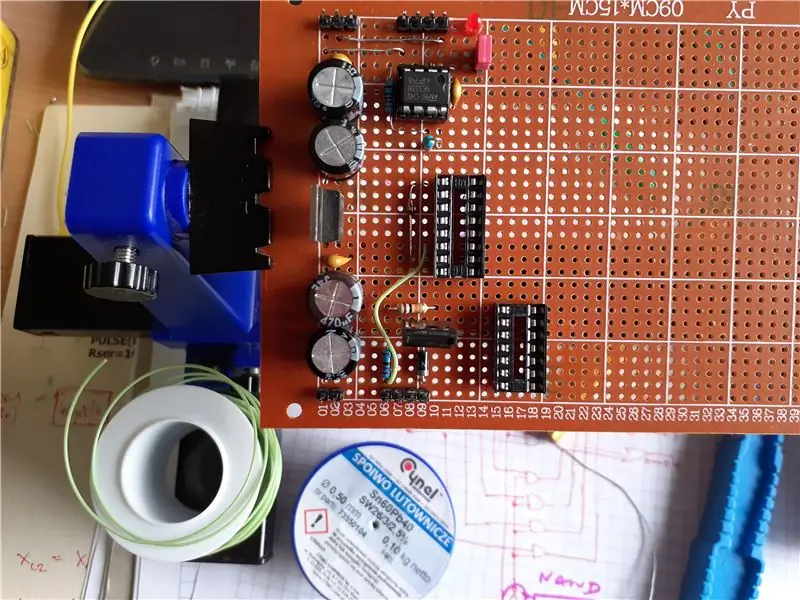
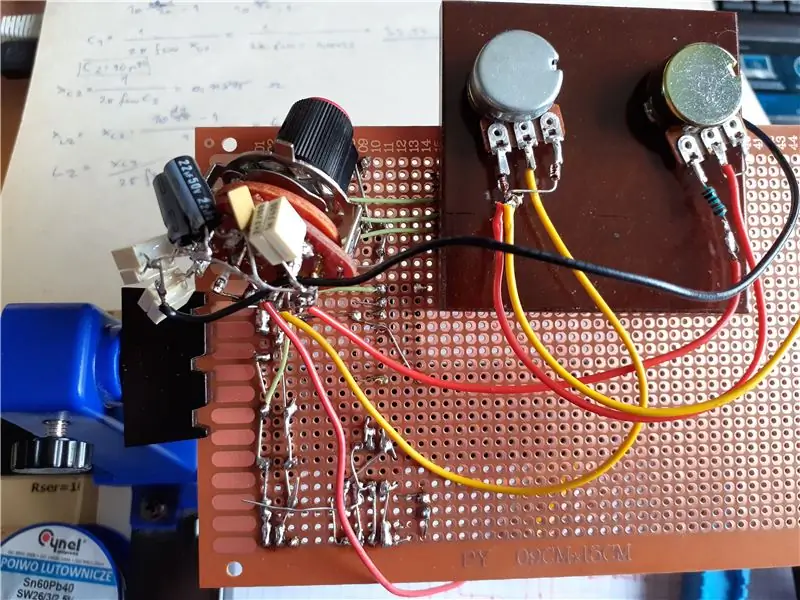
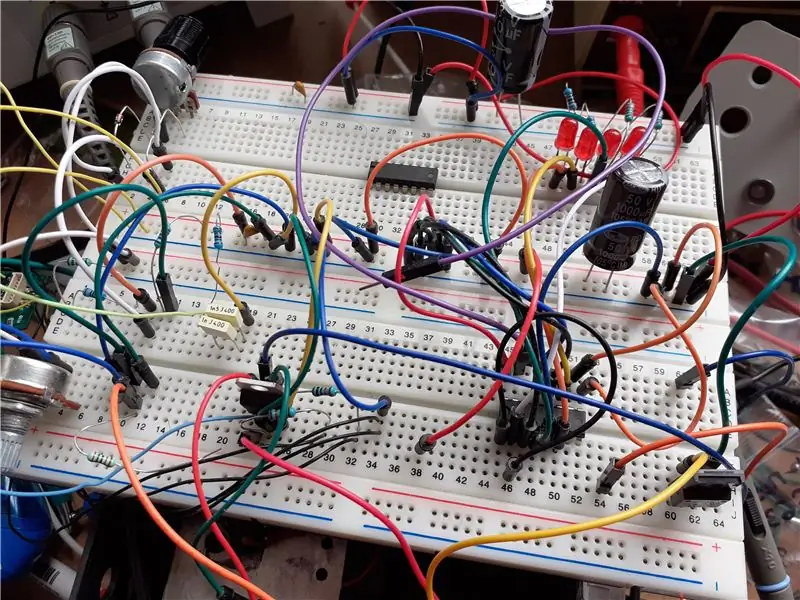
Da der Teil des Diagramms, der sich außerhalb des Panels befindet, nicht umfangreich ist, habe ich mich entschieden, eine Schaltung auf einer Universalplatine zu erstellen. Ich habe eine normale 9x15 cm Platine verwendet. Ich habe die Eingangskondensatoren zusammen mit dem Linearregler und dem Kühlkörper auf der linken Seite platziert. Anschließend habe ich Sockel für IC 555, 4017 Zähler und ULN2003 Treiber eingebaut. Der Sockel für den 4017-Zähler bleibt leer, da seine Funktion von arduino übernommen wird. Im unteren Teil befindet sich ein Treiber für den N-Kanal-Mosfet F630.
Schritt 10: Arduino
Die Verbindung des Systems mit arduino ist im Schaltplanblatt Nr. 4. Es wurde folgende Stiftanordnung verwendet:
- 3 digitale Eingänge für DIP-Schalter - D2, D3, D12
- 4 digitale Ausgänge für LED-Anzeigen - D4, D5, D6, D7
- 4 digitale Ausgänge für Stepper-Treiber - D8, D9, D10, D11
- Ein analoger Eingang für Potentiometer - A0
LED-Anzeigen, die die einzelnen Motorwicklungen darstellen, leuchten langsamer auf, als die Wicklungen tatsächlich mit Strom versorgt werden. Wenn die Blinkgeschwindigkeit der LEDs den Motorwicklungen entspräche, würden wir dies als kontinuierliches Leuchten aller sehen. Ich wollte eine klare einfache Darstellung und Unterschiede zwischen den einzelnen Modi erreichen. Daher werden die LED-Anzeigen unabhängig voneinander in Intervallen von 400 ms angesteuert.
Die Funktionen zur Steuerung des Schrittmotors wurden von Autor Cornelius in seinem Blog erstellt.
Schritt 11: Montage und Prüfung
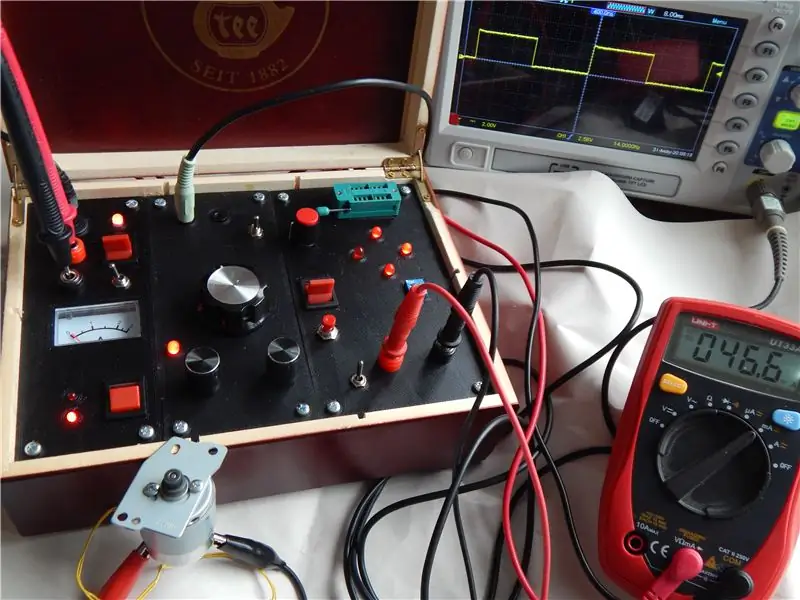
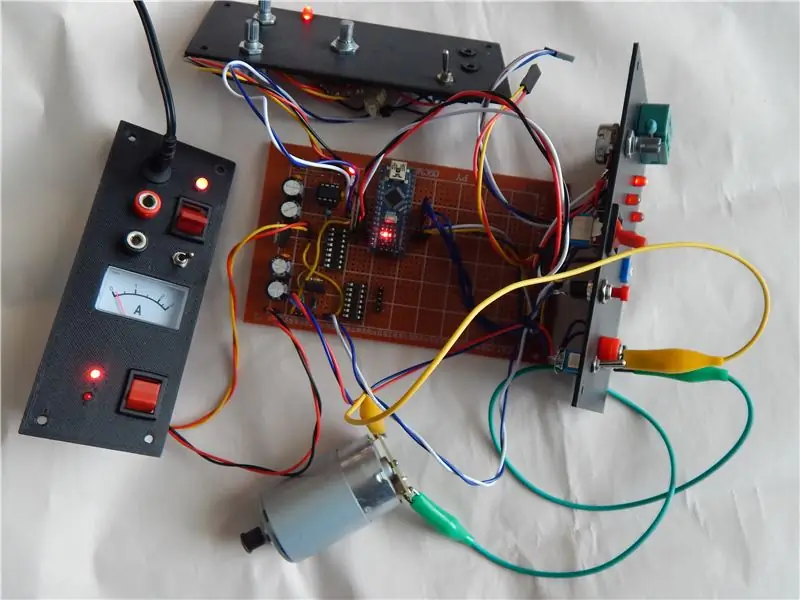
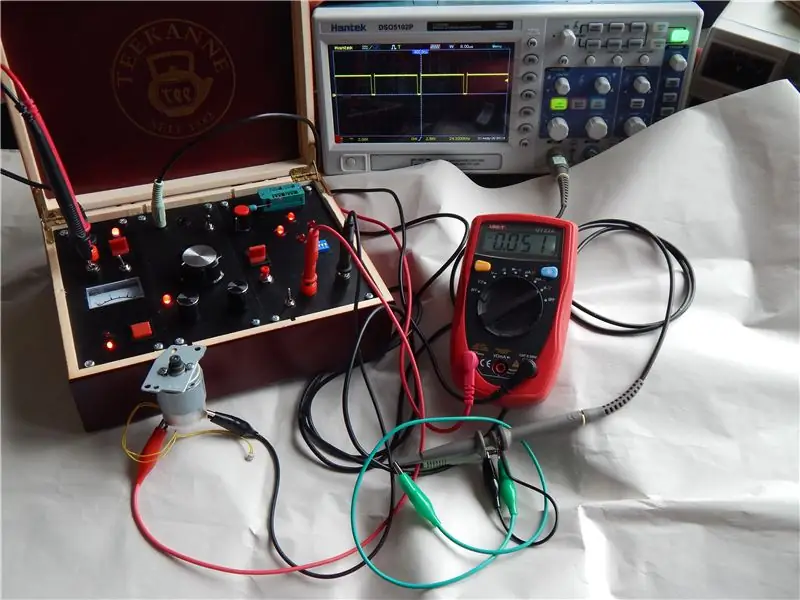
Schließlich habe ich alle Panels an die Platine angeschlossen und mit dem Testen des Testers begonnen. Ich habe den Oszillator und seine Bereiche mit einem Oszilloskop gemessen, sowie Frequenz- und Tastverhältnissteuerung. Ich hatte keine großen Probleme, die einzige Änderung, die ich vorgenommen habe, war, parallel zu den Eingangs-Elektrolytkondensatoren Keramikkondensatoren hinzuzufügen. Der zusätzliche Kondensator dämpft hochfrequente Störungen, die durch parasitäre Elemente des DC-Adapterkabels in das System eingebracht werden. Alle Testerfunktionen funktionieren wie gewünscht.
Schritt 12: Outro
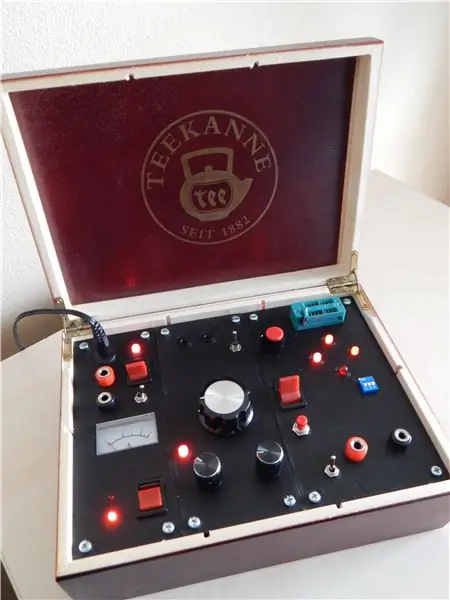
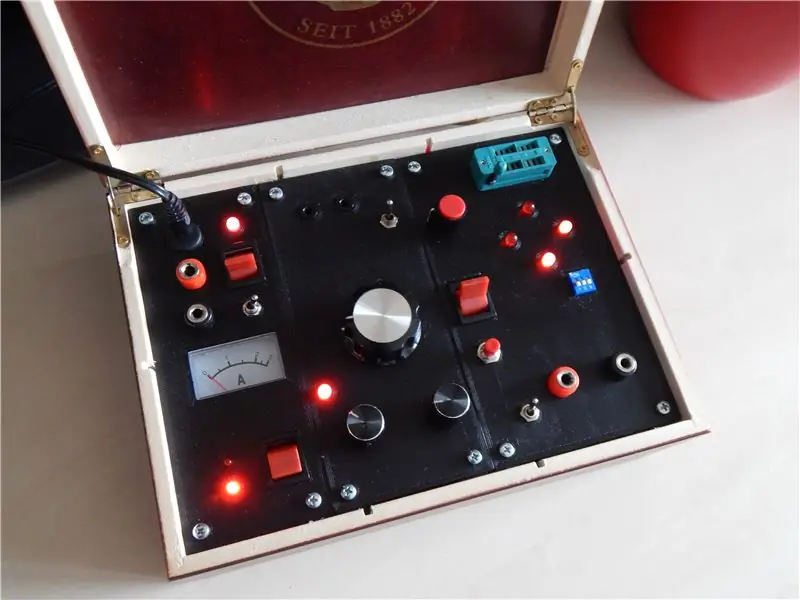
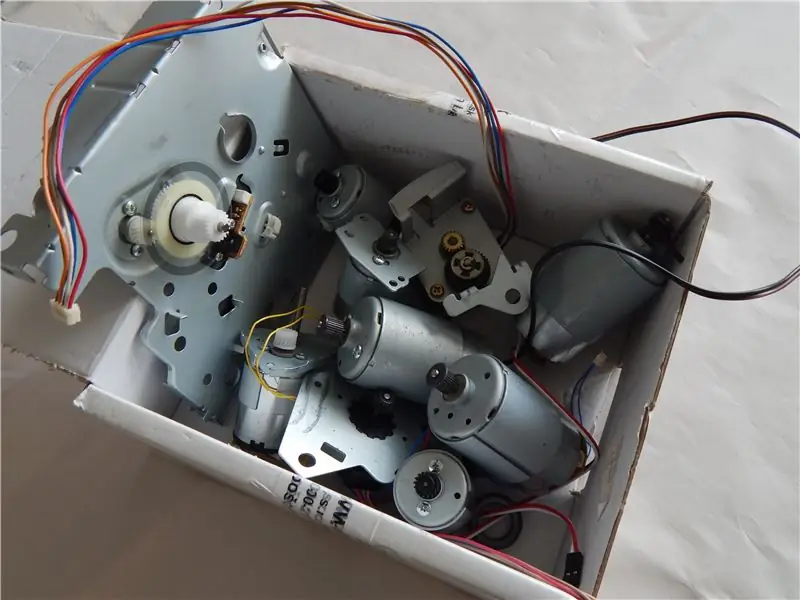
Jetzt kann ich endlich alle Motoren, die ich über die Jahre retten konnte, einfach testen.
Wenn Sie an Theorie, Schema oder irgendetwas über den Tester interessiert sind, zögern Sie nicht, mich zu kontaktieren.
Danke fürs Lesen und Ihre Zeit. Bleiben Sie gesund und sicher.