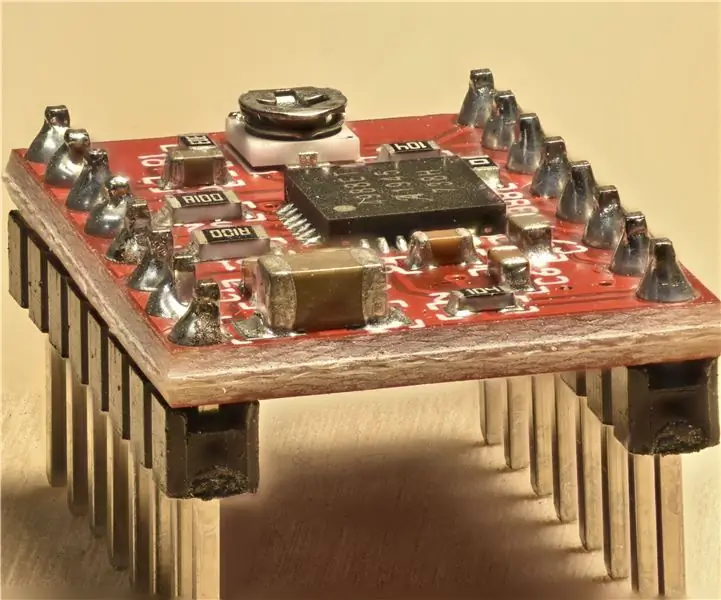
Inhaltsverzeichnis:
- Lieferungen
- Schritt 1: RAMPS und Arduino
- Schritt 2: Spannungsteiler
- Schritt 3: Tastatur
- Schritt 4: Kameraschnittstelle
- Schritt 5: Stepper-Verbindung
- Schritt 6: Endschalter
- Schritt 7: Strom- und Prüfstandstest
- Schritt 8: Schiene
- Schritt 9: Gehäuse
- Schritt 10: Betrieb
- Schritt 11: Erstellen Sie Notizen und Gedanken
2025 Autor: John Day | [email protected]. Zuletzt bearbeitet: 2025-06-01 06:08
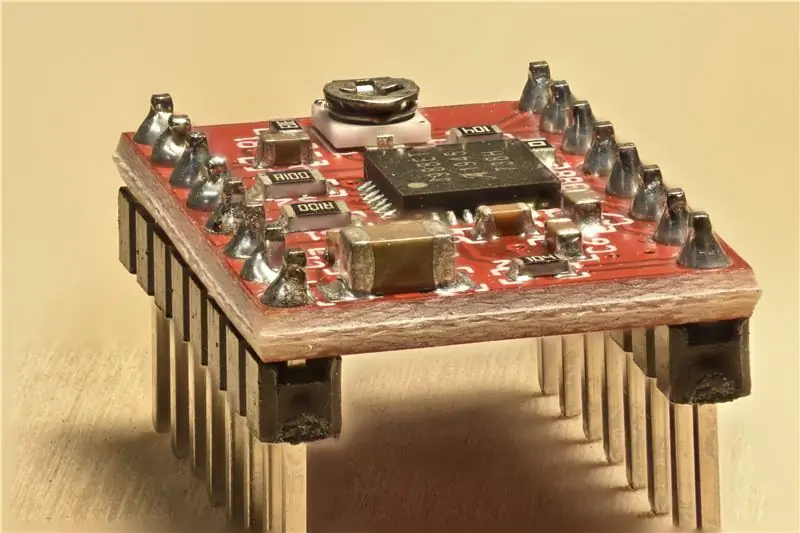
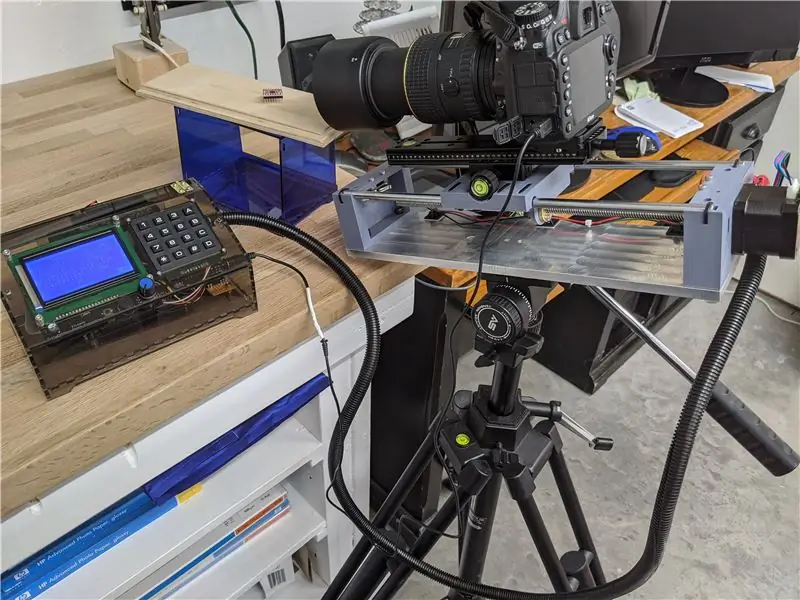
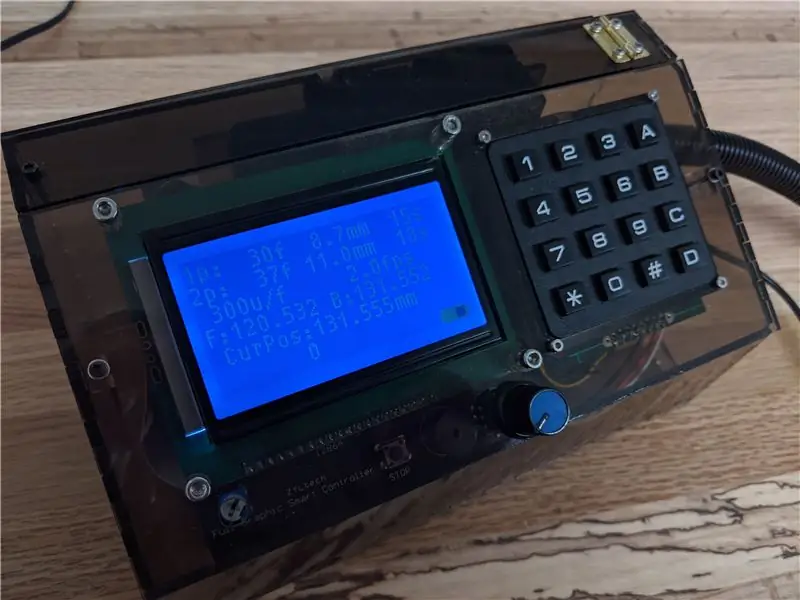
Wiederverwendete 3D-Druckerteile und die Arduino-basierte FastStacker-Software ermöglichen den einfachen und kostengünstigen Aufbau eines voll ausgestatteten Focus-Stacking-Rigs
Sergey Mashchenko (Pulsar124) hat großartige Arbeit bei der Entwicklung und Dokumentation einer DIY-Arduino-basierten Focus-Stacking-Schiene geleistet, wie in seinem Wiki (https://pulsar124.fandom.com/wiki/Fast_Stacker) beschrieben. Viele Leute haben sein Projekt aufgebaut und wie er in seinem Wiki feststellt, wurde sein Projekt in einschlägigen Foren breit diskutiert. Ich habe kürzlich selbst eine Version dieses Builds fertiggestellt, wie ich in einem Kommentar in seinem Wiki dokumentiere. Ich habe einen Controller um das Design von Pulsar124 herum mit einem Arduino, einer Tastatur, einem Stepper-Treiber und einem Nokia 5110 LCD-Display gebaut. Es wurde viel gelötet und das alte LCD war sehr problematisch. Die Foren zeigten, dass auch andere Probleme mit dem LCD hatten. Die Software des Projekts von Pulsar124 ist sehr schön. Es ist ausgereift und hat alle Funktionen und ich wollte es einfacher machen, ein System zu bauen, das es verwendet. Ich portierte seine Software so, dass sie auf einer 3D-Drucker-Steuerungsplattform läuft, die aus einem Arduino Mega, einem RAMPS 1.4-Schild und einem vollgrafischen Smart-Controller-LCD-Panel mit den dazugehörigen Kabeln besteht. Ich stelle dieser Software hier eine Anleitung zum Zusammenbauen der Staplersteuerung zur Verfügung, auf der sie läuft. Für die Schiene selbst habe ich, anstatt wie im Originalprojekt mit einer kommerziellen Velbon-Schiene zu beginnen, eine einfache 3D-Drucker-basierte Schiene entworfen, die ich auch hier dokumentiere. Ich übernehme keine Verantwortung für diesen Code oder Design, wenn jemand seine Kamera oder etwas anderes durcheinander bringt.
Lieferungen
Stapler-Controller
Die folgenden Teile werden sehr günstig zusammen als "3D-Drucker-Kit" oder "RAMPS-Kit" verkauft, Sie können sie jedoch einzeln kaufen oder aus einem unbenutzten 3D-Drucker aufsammeln.
- Arduino mega
- RAMPS 1.4
- 1 Stepper-Treiber (die Kits werden normalerweise mit mindestens 4 geliefert)
- Vollgrafik-Smart-Controller-LCD-Display mit Anschlussplatine und Flachbandkabeln. Wählen Sie beim Kauf eines mit einem integrierten Potentiometer zur Steuerung der Hintergrundbeleuchtung.
- Header-Jumper zum Konfigurieren des Stepper-Treibers
- Endschalter im repRap-Stil und zugehörige Kabel
Für die Steuerung zusätzlich erforderlich:
- 4x4 Schaltertastatur
-
Spannungsteiler Teile
- 150K Widerstand
- 390K Widerstand
- 0,1 uf Kondensator
- 2 einzelne Stiftleisten (optional)
-
Teile der Kameraschnittstellenrelaisplatine
- 2 Reed-Relais - 10 mA Spule, eingebaute Snubber-Dioden
- 1/8"-Phonobuchse
- 3-poliger 0,1"-Header
- 6-zelliger AA-Akku mit wiederaufladbaren NiMH-Akkus für batteriebetriebenen Betrieb
- Wandwarzenversorgung mit nominal 9 VDC für Wechselstrombetrieb
- Überbrückungsdrähte oder Drähte/Stifte/Steckerstiftgehäuse, um die Verbindung zwischen der Tastatur und den RAMPS-Stiftleisten herzustellen. 8-Pin zu 2 X 4-Pin-Anschluss erforderlich.
- Drähte oder Kabel zum Anschluss von Endschaltern an RAMPS-Stiftleiste. Ich habe die Kabel verwendet, die mit den Endschaltern im RAMPS-Kit geliefert wurden, und sie wie unten beschrieben verlängert.
- Kabel zum Verbinden des Steppers mit dem RAMPS-Header. Ich habe ein 59" Stepperkabel von Amazon verwendet.
-
Manuelles Kameraverschluss-Steuerkabel, das mit Ihrem Kameratyp funktioniert - finden Sie bei ebay oder Amazon für ein paar Dollar. Schneiden Sie die Handtastereinheit ab und entsorgen Sie sie, und bewahren Sie das Kabel und den Stecker für Ihre Kamera auf.
Fokusschiene
- 3D-gedruckte Teile mit mitgelieferten STL-Dateien - Motorende, Gegenende und Schlitten.
- NEMA 17 Schrittmotor mit 300 mm T8 Gewindespindel abgebildet oder Ihre Längenpräferenz. Wenn die Leitspindel nicht integriert ist, verwenden Sie die Kupplung, um den Stepper mit der Leitspindel zu verbinden
- Messingmutter für Leitspindel - spielfrei oder federbelastet
- 4 LM8U-Lager
- 2 8-mm-Stahlstangen 340 mm lang oder passend zu Ihrer Leitspindel
- Grundplatte 100 mm x 355 mm (oder entsprechende Länge) Ich habe ein Stück 4 "x 14" Aluminiumschaft mit gereinigter Oberfläche verwendet. Viele andere Basisoptionen sind möglich.
- Schrauben zum Befestigen der Endstücke an der Basis - ich habe 1/4-20 "verwendet
- Muttern/Schrauben zur Befestigung von Endschaltern - 4-40 oder 3mm
- Endschalter im RepRap-Stil. Die RAMPS-Kits werden oft mit 3 oder 4 davon geliefert. Es können auch Standard-Mikroschalter verwendet werden, wobei die Lochbilder an den Endstücken beide akzeptieren.
-
Folgendes wird in der Reihenfolge von oben nach unten, beginnend bei der Kamera, verwendet, um Ihre Kamera am Schienenschlitten zu montieren
- 50mm Universal-Schnellschuhplatte mit 1/4 Schraube, passend für Arca-Swiss Standard (Montage an Kamera)
- 200mm Nodal Slide Fokussierschienenplatte mit Schnellspanner für Arca-Montierung (nimmt die Platte oben auf)
- 50mm Arca Swiss Klemme, Schnellwechsel-Plattenklemme, passend für Arca-Style-Platte (montiert die Gleitknotenplatte am Schlitten)
- Kabelbinder, 4"
Schritt 1: RAMPS und Arduino
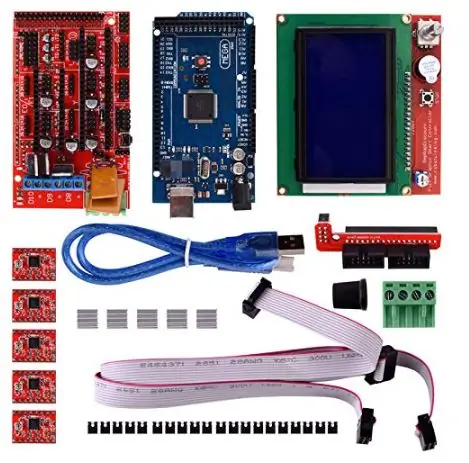
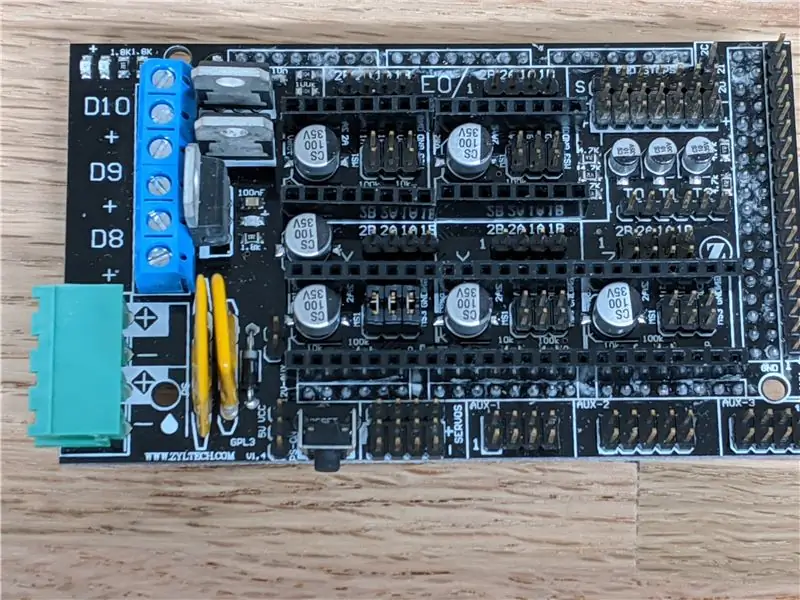
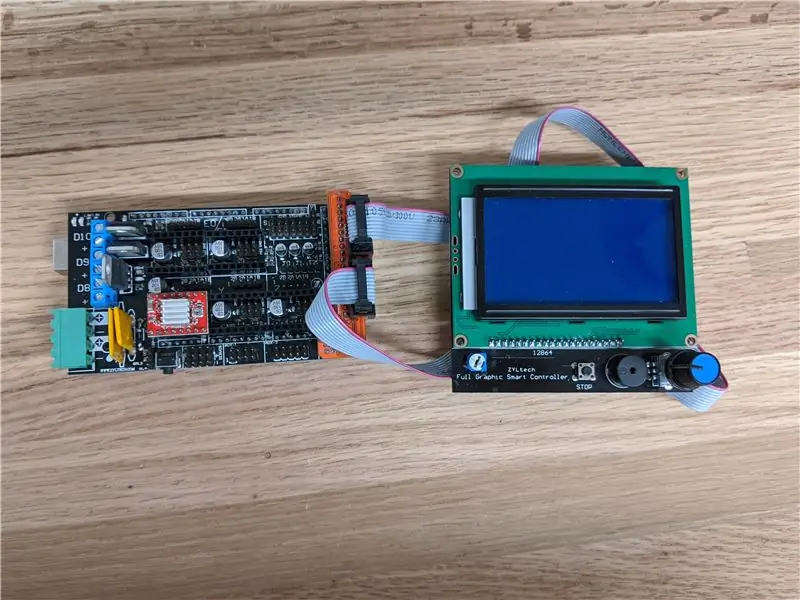
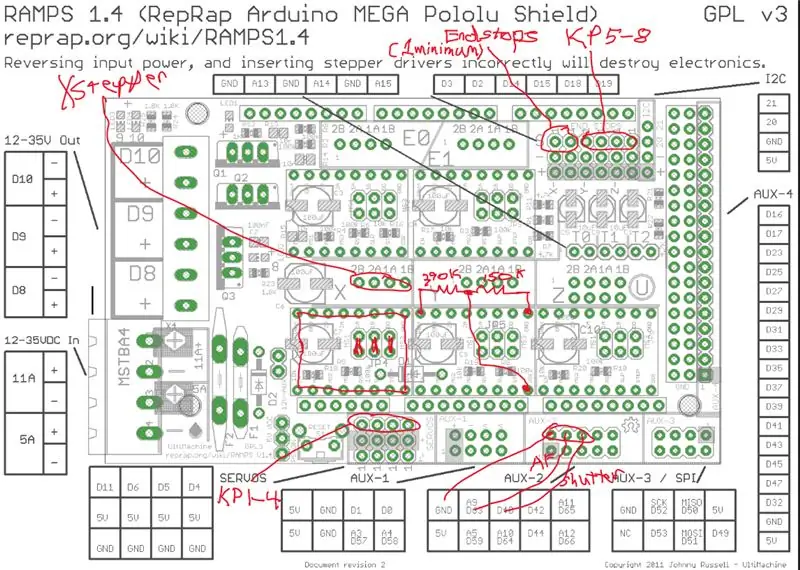
Das Bild zeigt eines der typischen RAMPS-Kits.
Die Software für diesen Build ist hier:
Installieren Sie die FastStacker-Software auf dem Mega-Board. Bevor Sie die Faststacker-Software kompilieren und auf das Board hochladen, verwenden Sie den Arduino IDE-Bibliotheksmanager, um die u8g2lib-Grafikbibliothek in Ihrer Arduino-Umgebung zu installieren. Wenn Sie eine andere Schiene, Endschalter usw. verwenden, finden Sie im Original-Build-Wiki Hinweise zur Anpassung.
Installieren Sie alle drei Jumper in der X-Schrittmotortreiberstelle des RAMPS wie im Bild gezeigt und installieren Sie dann einen Schrittmotortreiber an dieser Stelle. Dies ist für einen 16-Mikroschritt-Betrieb konfiguriert. Stecken Sie das RAMPS-Schild in den Arduino Mega. Verbinden Sie das Grafik-LCD mit der mit dem LCD gelieferten Schnittstellenkarte und den Flachbandkabeln mit dem RAMPS und achten Sie dabei auf die Etiketten an den Anschlüssen an jedem Ende. Beachten Sie, dass dieses LCD keine programmgesteuerte Steuerung der Hintergrundbeleuchtung unterstützt, so dass die Funktion im Software-Port abgetastet wird.
In den folgenden Schritten werden mehrere Verbindungen zum RAMPS-Board hergestellt, indem in verschiedene Header gesteckt wird. Das Diagramm der RAMPS-Platine fasst diese Verbindungen als Referenz mit weiteren Details in späteren Schritten zusammen.
Schritt 2: Spannungsteiler
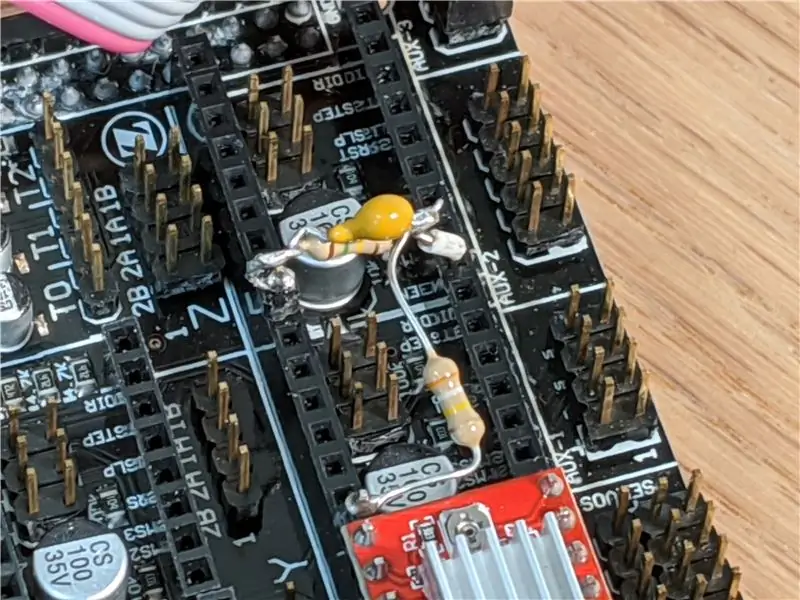
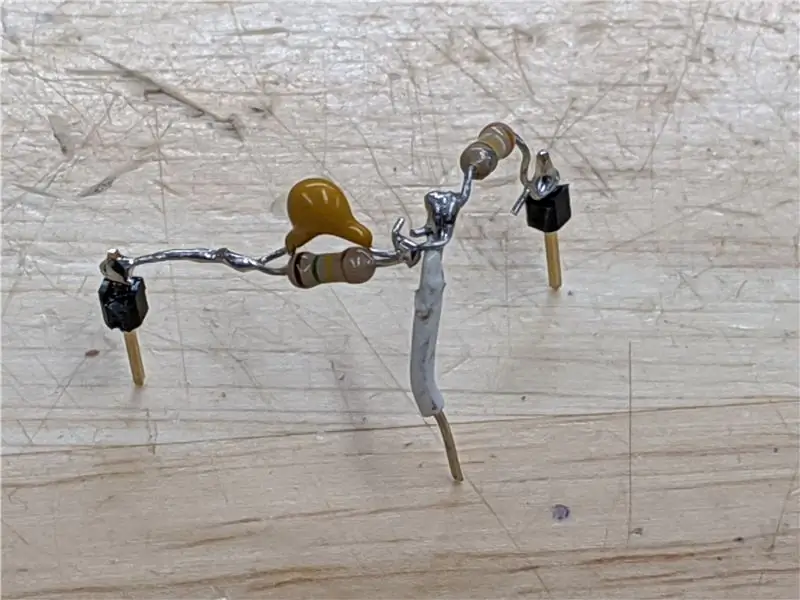
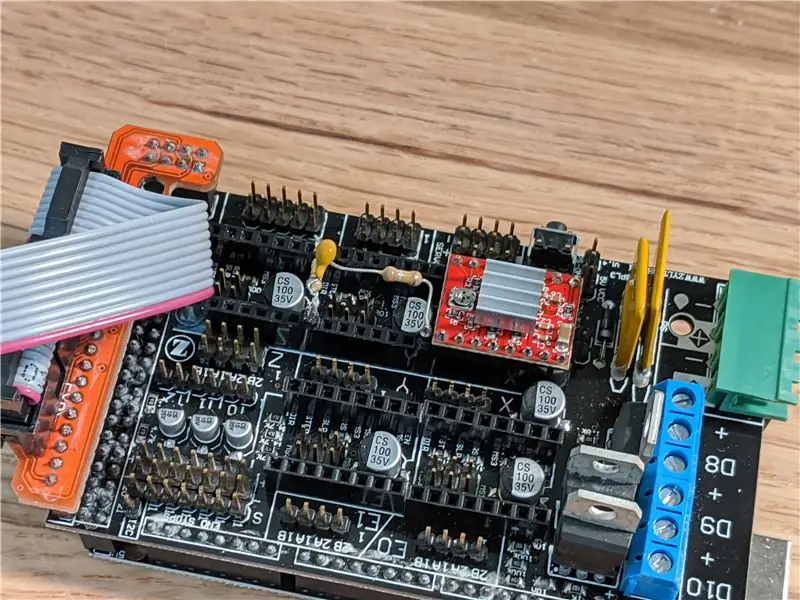
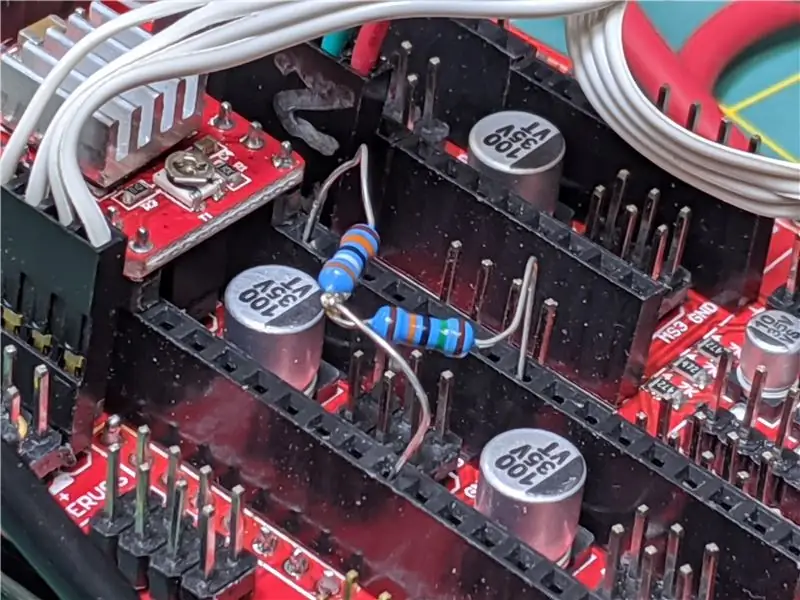
Die Staplersteuerung umfasst Funktionen zum Überwachen der Batteriespannung (oder was auch immer die Eingangsstromquelle ist). Ein Spannungsteiler wird gemäß dem ursprünglichen Design aus 2 Widerständen und einem 0,1uf Rauschunterdrückungskondensator gebildet. In diesem Build wird der Spannungsteiler in Pins des ansonsten unbenutzten y-Stepper-Headers gesteckt. Für die Messungen wird die interne 2,56V Spannungsreferenz des mega verwendet.
Die beiden Teilungswiderstände werden in der ursprünglichen Projektdokumentation und im Code als R3 und R4 bezeichnet und wir setzen das hier fort. Angenommen, R3 ist direkt mit "+" der Batterie verbunden (Y-Header-Pin 16) und R4 ist mit Masse verbunden (Y-Header-Pin 9), das Teilerverhältnis ist R4 / (R3 + R4). Dieser Build geht von einem Nenneingang aus Spannungsbereich von 6,9V bis 9V. Bei Batteriebetrieb werden 6 AA NiMH-Akkus verwendet. Beim Betrieb mit Wechselstrom verwendet es eine 9-V-Nennwandwarze. Wir werden 9,2 V auf 2,56 V mit diesen Widerständen skalieren: R4 = 150 K, R3 = 390 K.
Bauen Sie den Spannungsteiler wie gezeigt auf. Die Pins sind nicht unbedingt erforderlich, Sie können die Widerstandskabel direkt in den Header stecken. Die Anschlüsse an den Widerständen, die ich hatte, schienen jedoch klein zu sein und ich hatte Angst, dass sie nicht zuverlässig eingesteckt bleiben könnten, also fügte ich die Pins hinzu. Ich bin mir nicht sicher, ob der Kondensator wirklich benötigt wird - er scheint ohne eine einzige Lötverbindung in Ordnung zu sein, wie im Bild der minimalistischen Version des Teilers gezeigt.
Stecken Sie den Teiler in den Y-Stepper-Header der RAMPS wie folgt und wie im Bild gezeigt:
Pin 16 (Vcc) - freie Leitung des 390K-Widerstands.
Pin 9 (Gnd) - freie Leitung des 150K Widerstands
Pin 8 (Y-Stepper-Aktivierung, Arduino A7) - Abgriff des Spannungsteilers
Schritt 3: Tastatur
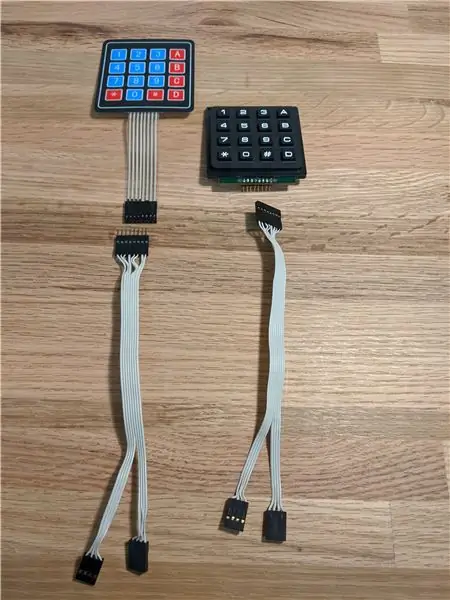
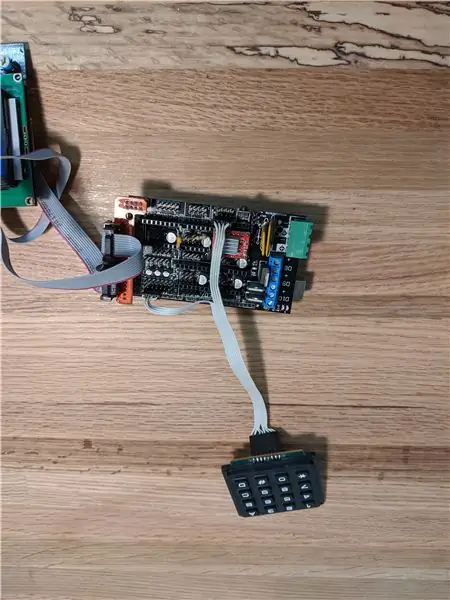
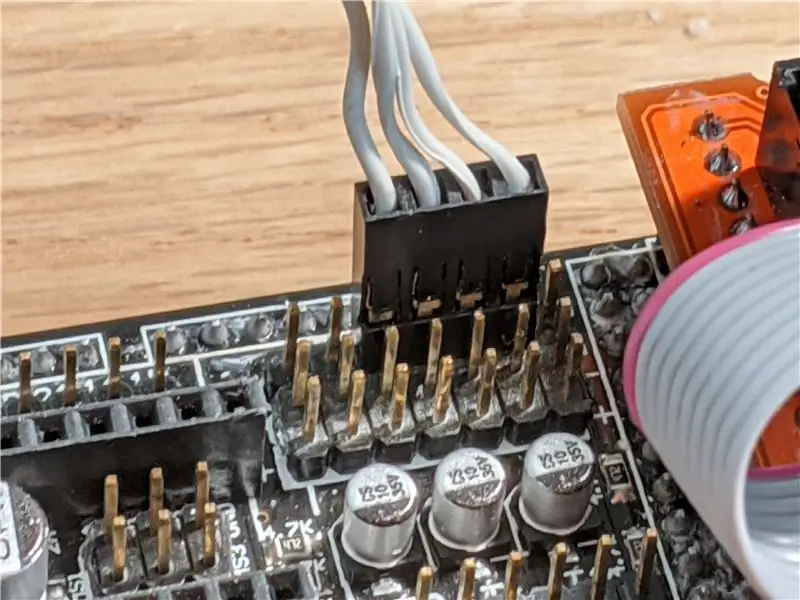
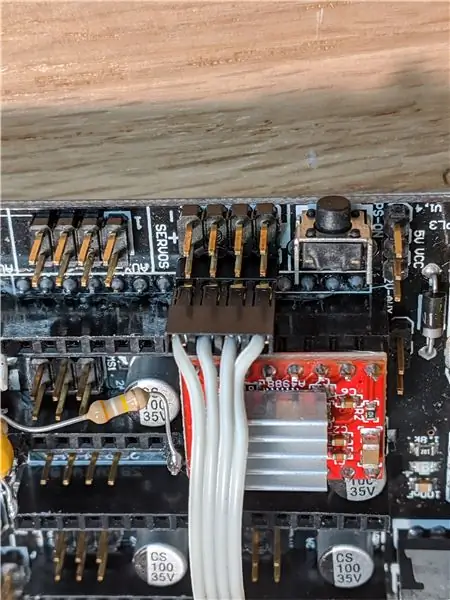
Es werden 2 Arten von allgemein verfügbaren Tastaturen angezeigt. Die Datei stacker.h enthält Tastenzuordnungen für beide, wobei die Schwarz/Weiß-Einheit standardmäßig aktiviert ist. Entkommentieren Sie stattdessen die andere Zuordnung, wenn Sie einen der roten/blauen Membrantypen verwenden. Schlagen Sie in der Originaldokumentation des Projekts nach, wenn Ihre davon abweicht.
Wenn Sie Probleme damit haben, dass einige Tasten nicht funktionieren, aber keine vollständige Reihe oder Spalte, und Sie eine der Schwarz/Weiß-Einheiten verwenden, messen Sie den Widerstand der Reihen-Spalten-Verbindungen für alle Tasten. Die Tastaturen im Schwarz-Weiß-Stil verwenden eine Art gedruckter Kohlenstoffspuren auf der Platine im Inneren, die dazu führen, dass einige Reihen-Spalten-Verbindungen einen hohen Widerstand aufweisen, was dazu führt, dass einige Tasten nicht reagieren, wenn sie mit einigen Plattformen verwendet werden, z. B. Arduino Pro Mini.
Die Tastatur hat einen 8-poligen Stecker. 4 dieser Pins sind mit einem Header des RAMPS verbunden und die anderen 4 sind mit einem anderen Header verbunden. Ich habe 8-Pin-auf-Dual-4-Pin-Flachbandkabel für beide Tastaturtypen hergestellt, wie in den Bildern gezeigt. Sie sind bis auf das Geschlecht der Pins, die mit der Tastatur verbunden sind, gleich. Ich verwende Stiftgehäuse und crimpe an Stift- und Buchsenstiften zusammen mit Draht und einem Crimpwerkzeug, um die Kabel herzustellen, aber Überbrückungsdrähte oder andere vorgecrimpte Optionen können verwendet werden. Dieses Video von Pololu zeigt viele Produktoptionen, um diese Art von Kabeln zu bauen: https://www.pololu.com/category/39/cables-and-wir…. Jumperdrähte des gezeigten Typs sind eine einfache Option.
Verwenden Sie das Kabel, um die Tastatur wie folgt mit der RAMPS zu verbinden (die unten angegebene Pinnummerierung der Tastatur geht davon aus, dass sich Pin 1 bei Blick auf die Vorderseite der Tastatur links befindet, Pin 8 nach rechts):
Tastaturstifte 1-4 werden mit dem RAMPS Servos-Header verbunden, die Stifte sind in der Reihenfolge von links nach rechts aufgelistet, beginnend mit dem Stift, der der Reset-Taste am nächsten liegt. Dies verbindet sich wie folgt:
Tastatur 1- D11
Tastatur 2- D6
Tastatur 3- D5
Tastatur 4- D4
Tastaturstifte 5-8 werden mit dem RAMPS-Endstop-Header verbunden und wie folgt hergestellt:
Tastatur 5- Ymin- D14
Tastatur 6- Ymax- D15
Tastatur 7- Zmin - D18
Tastatur 8, Zmax- D19
Schritt 4: Kameraschnittstelle
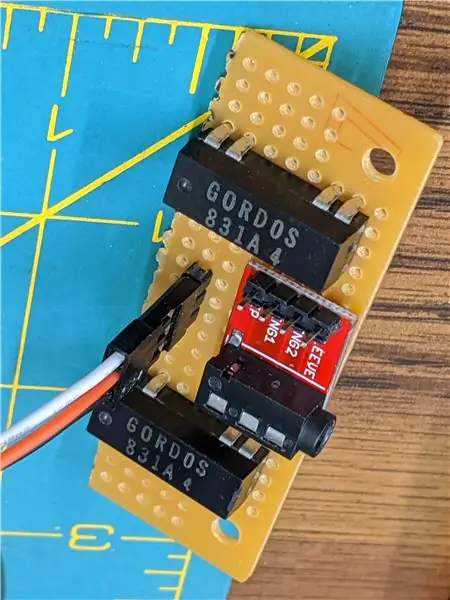
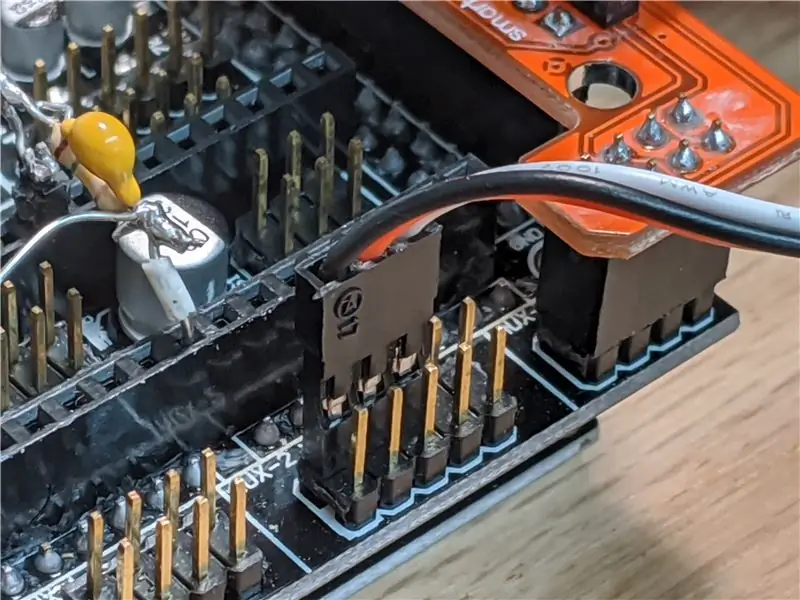
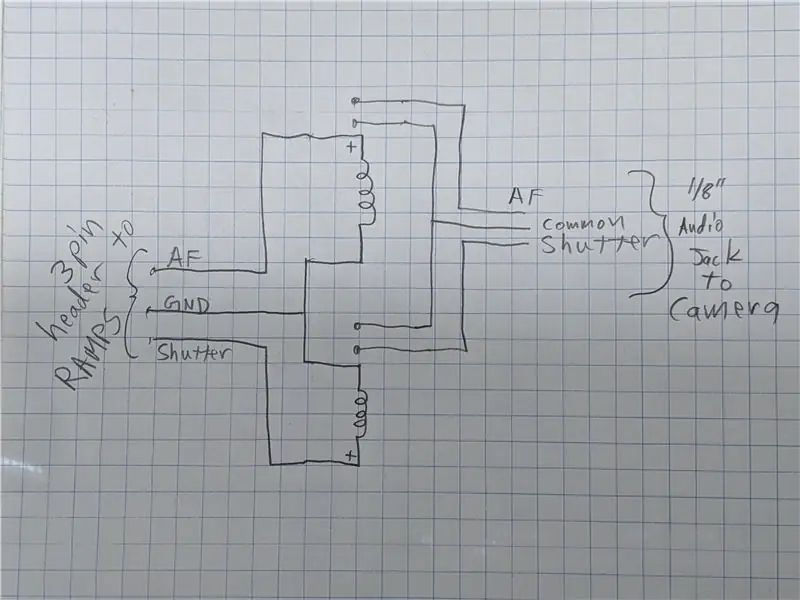
Eine kleine Platine mit 2 Reed-Relais, einem 3-Pin-Header und einer 1/8-Zoll-Audiobuchse dient als Schnittstelle zwischen der RAMPS und der Kamera. Ich schlage vor, Relais mit eingebauten Snubber-Dioden zu verwenden. Fügen Sie Ihre eigenen hinzu, wenn Sie dies nicht tun Wählen Sie eines aus, das zum Aktivieren nicht mehr als 10 mA benötigt (500-Ohm-Spule). Ich habe zufällig einige Gordos 831A-4-Relais, die ich verwendet habe, aber DigiKey hat zum Beispiel die Littlefuse #HE721A0510, Digi-Key-Teilenummer HE101-ND das sieht passend aus, der Schaltplan wird gezeigt.
Ein Kabel wird von der manuellen Verschlusssteuerung hergestellt, indem die Drucktastensteuerung abgeschnitten und geworfen wird, nachdem festgestellt wurde, welche Drähte AF, Verschluss und üblich sind. Dieses Kabel ist mit einem 1/8-Zoll-Audiostecker verbunden, der in die Buchse auf der Relaisplatine gesteckt wird.
Die Relaisplatine wird wie abgebildet mit einem kurzen 3-adrigen Servokabel an die RAMPS angeschlossen. Sie können ein Standard-Servokabel verwenden, Jumper verwenden oder Ihre eigenen herstellen. Die Kameraschnittstellen-Relaisplatine wird in den AUX-2-Header der RAMPS-Platine eingesteckt und stellt die folgenden Verbindungen her:
Aux 2, Pin 8- GND
Aux 2, Pin 7- AF- D63
Aux 2, Pin 6 - Verschluss- D40
Ich habe mit der Verwendung eines Relaismoduls für diese Funktion experimentiert, um den Bau einer Platine zu vermeiden, aber das allgemein verfügbare Modul, das ich ausprobiert habe, verbrauchte zu viel Strom von der 5-V-Schiene.
Schritt 5: Stepper-Verbindung
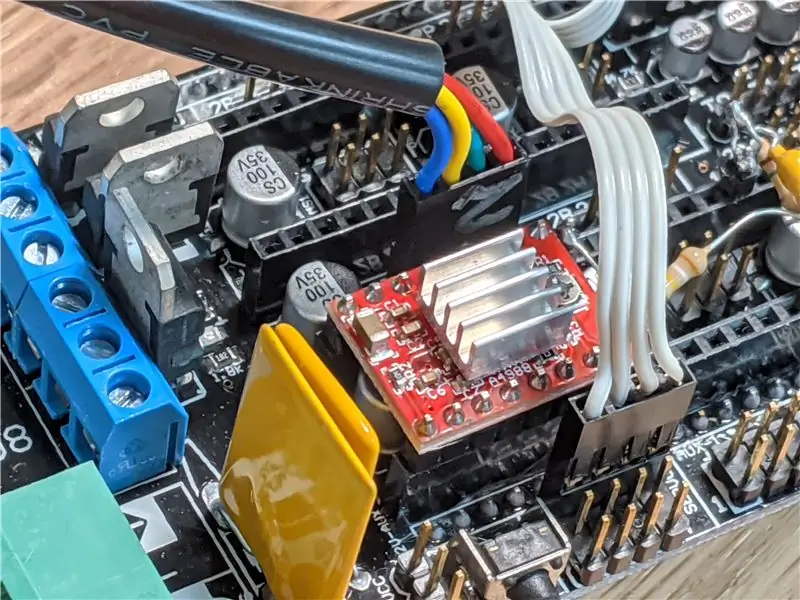
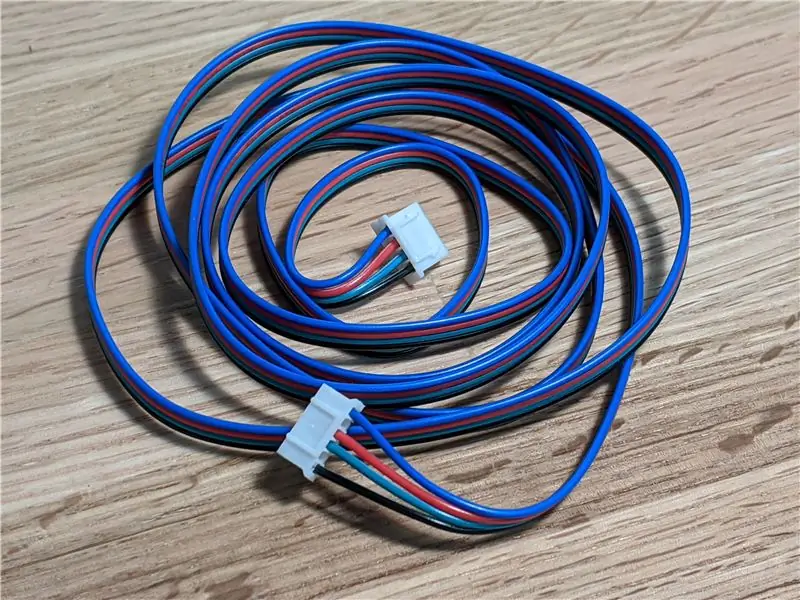
Stecken Sie das Stepper-Kabel in den X-Stepper-Header. Ich habe ein 59-Zoll-Stepper-Verlängerungskabel verwendet, wie im 2. Bild gezeigt. Wenn sich der Stepper in die falsche Richtung dreht, kehren Sie den Stepper-Stecker um, der in die RAMPS-Platine eingesteckt ist.
Schritt 6: Endschalter
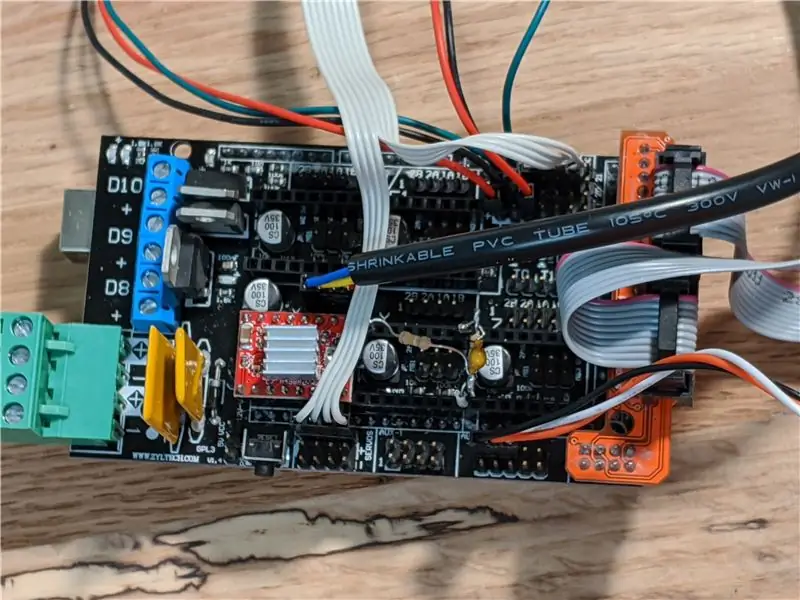
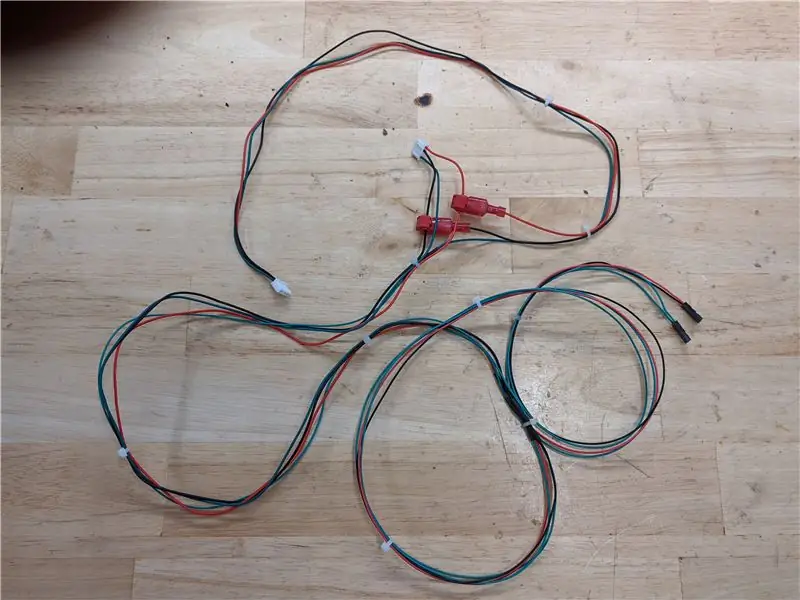
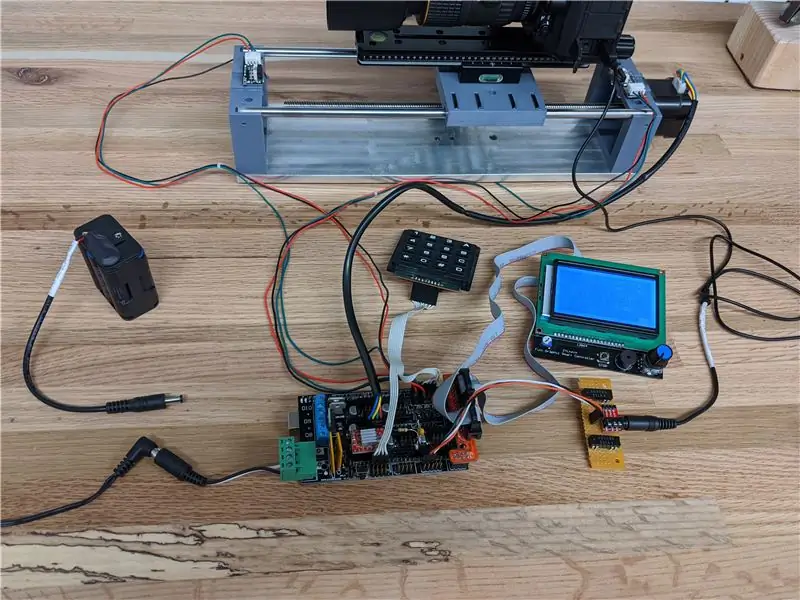
Die FastStacker-Software unterscheidet nicht zwischen den beiden Endstopps und kümmert sich nicht darum, welcher getroffen wurde. Die RAMPS-Stapler-Software ist so konfiguriert, dass sie direkt mit 2 Standard-repRap-Endschaltern und den dazugehörigen Kabeln arbeiten kann, die in die Xmin- und Xmax-Endstop-Stiftleistenpositionen des RAMPS eingesteckt werden. Das Bild zeigt, wo diese eingesteckt sind. In dieser Konfiguration wird jeder Endschalter auf der Schiene mit +5V, GND verbunden und für jeden Endschalter wird eine eigene Signalleitung verlegt. Die Software ODER verknüpft die beiden Eingänge miteinander. Dies ermöglicht eine einfache Plug-and-Play-Wiederverwendung der mit dem RAMPS-Kit gelieferten Kabel und ermöglicht das Aufleuchten der LED-Anzeigen auf den repRap-Endstop-Boards, wenn die Stopps ausgelöst werden. Die Signalleitungen der beiden repRap-Schalter können nicht miteinander verbunden werden, wenn die Platinen +5 empfangen, wenn dies der Fall ist, wird der eine ausgelöst und der andere nicht +5 mit GND kurzgeschlossen. Ich habe den gezeigten Kabelbaum aus den Originalkabeln hergestellt, ein einzelnes Strompaar an die Schalter gesendet, aber ihre einzelnen Signaldrähte beibehalten und alle Drähte verlängert. Dies verwendet immer noch 4 Drähte im Lauf zwischen Controller und Schiene.
Ein einfacherer Ansatz verwendet nur 2 Drähte - GND und entweder die Xmin- oder Xmax-Endstop-Header-Pins, die zu den beiden parallel verdrahteten normalerweise offenen Endstop-Schaltern geführt werden. Beim Auslösen eines Endschalters wird die Signalleitung auf Masse gezogen. Weniger Drähte, aber keine LED-Beleuchtung beim Auslösen eines Schalters.
Die Lochbilder an den Schienenendstücken unterstützen auch Mikroschalter in Standardgröße (nicht die Mini-Schalter wie auf den repRap-Boards). Verwenden Sie in diesem Fall die 2-Draht-Konfiguration.
Schritt 7: Strom- und Prüfstandstest
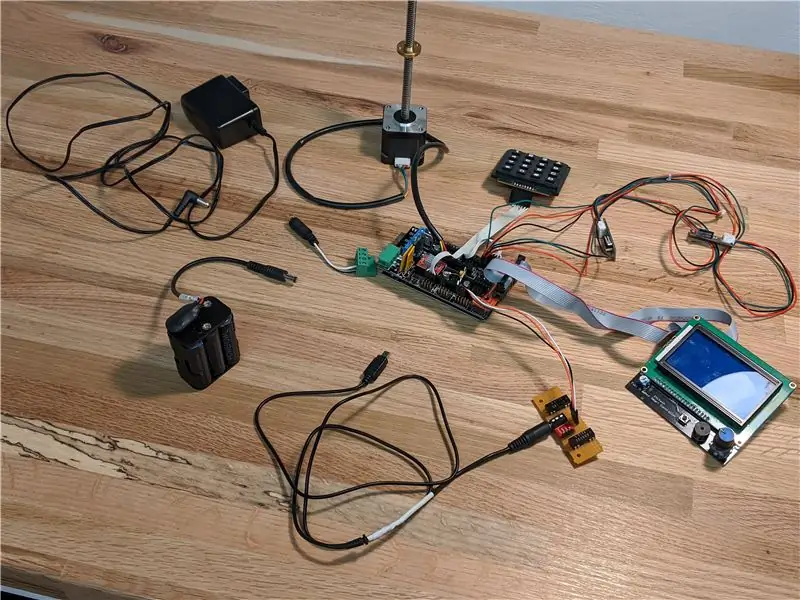
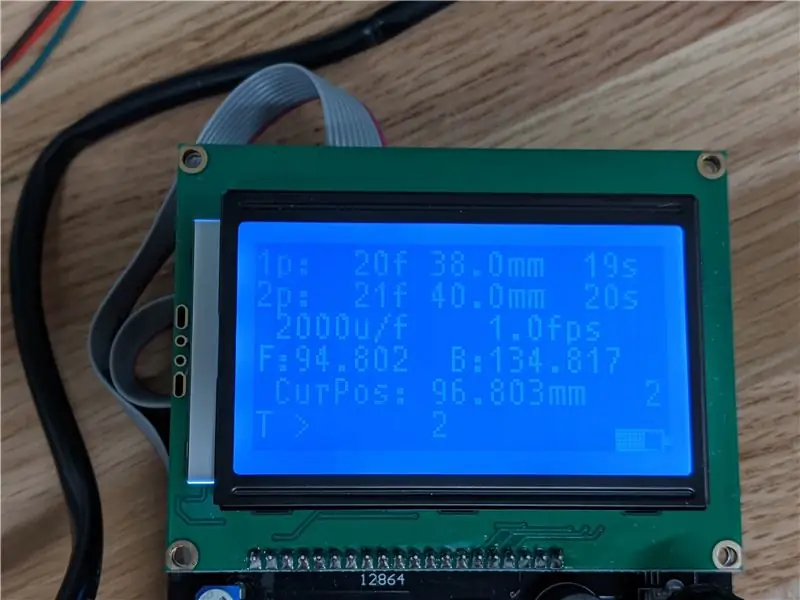
Legen Sie 7-9 V nominal an den Stromeingangsanschluss des RAMPS an. Beachten Sie im Bild, welche Klemmen am Stromanschluss verwendet werden. Dies ist der Niedrigleistungssatz der Vcc-Eingänge, nicht die Hochleistungseingänge, die die RAMPS-MOSFETS ansteuern. Das System sollte booten und Sie auffordern, eine beliebige Taste zu drücken, um die Kalibrierung zu starten. Wenn Sie dies tun, beginnt sich der Stepper zu drehen. Lassen Sie dies einige Sekunden lang tun und lösen Sie dann einen der Endschalter aus. Der Motor sollte umkehren. Lassen Sie es mehrere 10 Sekunden lang laufen und drücken Sie dann erneut auf einen Endschalter. Der Motor kehrt wieder um und bewegt sich in die seiner Meinung nach 4 mm Position. Führen Sie an dieser Stelle die Bedienung der verschiedenen Tasten auf der Tastatur anhand der Original-Projektdokumentation durch, um sicherzustellen, dass alle Tasten richtig gelesen werden. Beachten Sie, dass die Hintergrundbeleuchtungssteuerungsfunktion aus dem Originalprojekt auf diesem System nicht unterstützt wird - das LCD unterstützt sie nicht. Führen Sie einige Stapel aus und hören Sie auf das Klicken der Relais, die aktiviert werden, und wenn alles gut aussieht, überprüfen Sie die Schnittstelle zu Ihrer Kamera. Das sollte es für die Elektronik sein.
Schritt 8: Schiene
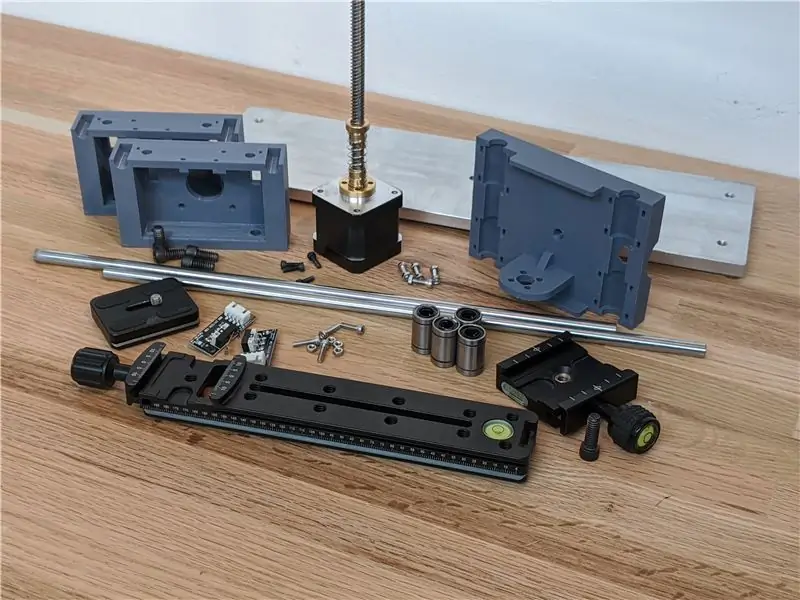
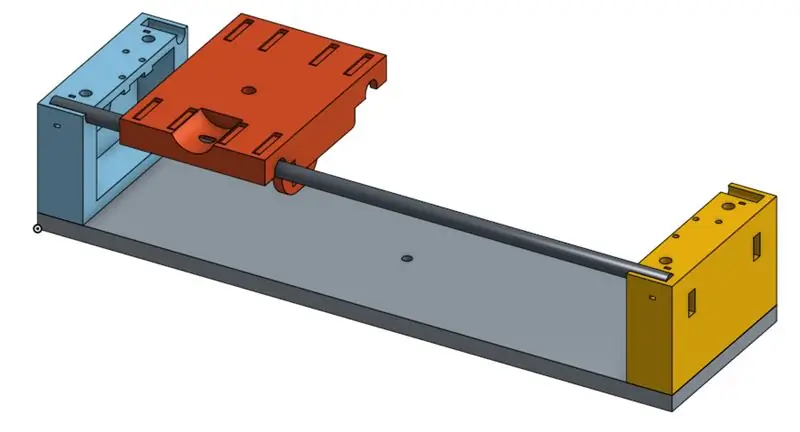
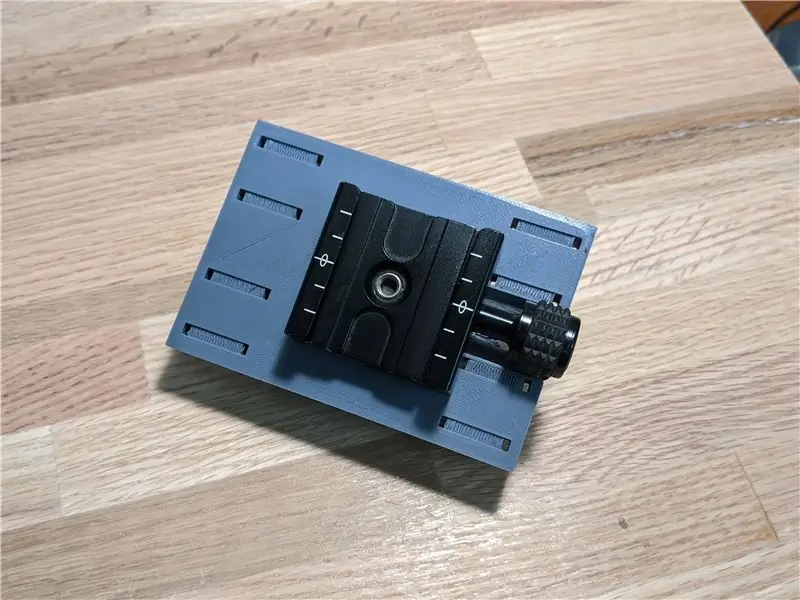
Die drei 3D-Drucke sind einfache Drucke und feine Schichten sind nicht erforderlich - ich habe 0,28 mm verwendet. Es passt zusammen wie auf den Bildern. Bitte beachten Sie, dass einige Bilder in diesem Instructable eine frühere Iteration des Schienendesigns zeigen, bevor ich die Endschalter von oben auf den Endstücken in die Innenseite der Endstücke bewegt habe. Der Schlitten nimmt entweder die spielfreie Mutter wie abgebildet oder die Standardmutter auf. Beginnen Sie am Motorende, befestigen Sie den Motor und den Endanschlag, fügen Sie die Schienen hinzu, schieben Sie dann den Schlitten auf und drehen Sie die Leitspindel von Hand, um sie auf die Mutter zu schrauben. Schieben Sie das entfernte Endstück auf die Schienen, fügen Sie die Kabelbinder hinzu, und die Montage ist weitgehend abgeschlossen, bis auf das Anschrauben an die von Ihnen gewählte Basis. Es gibt viele Möglichkeiten für eine Basis. Die von mir verwendete Aluminiumplatte ist stark und lässt sich leicht auf ein Stativ montieren. Aluminiumstrangpressen oder Holz sind andere Möglichkeiten.
Schritt 9: Gehäuse
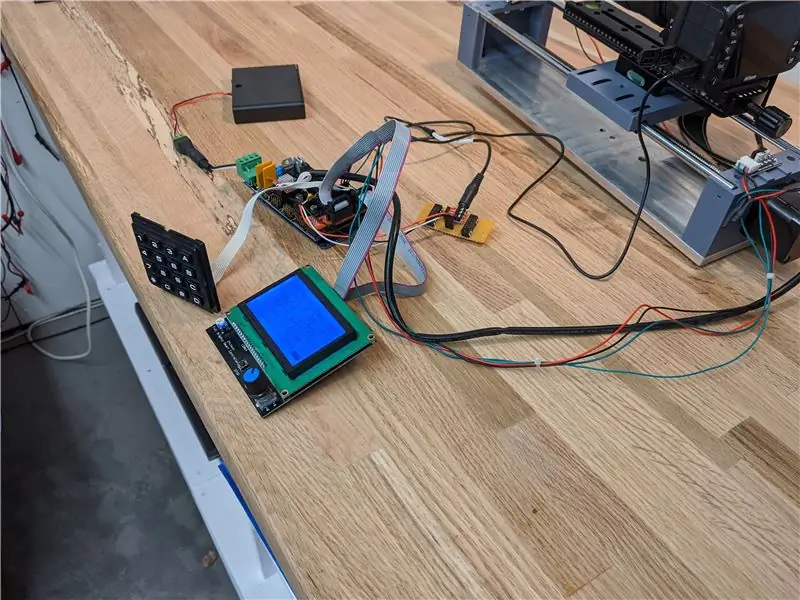
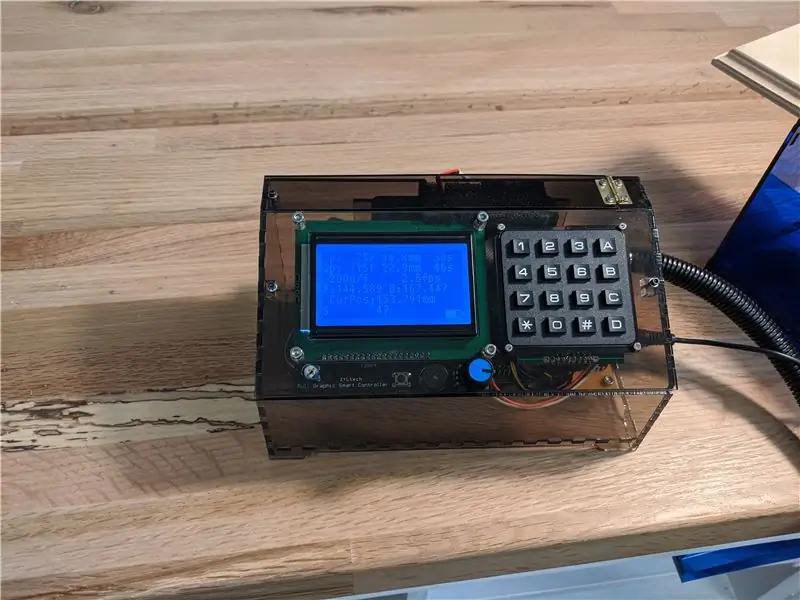
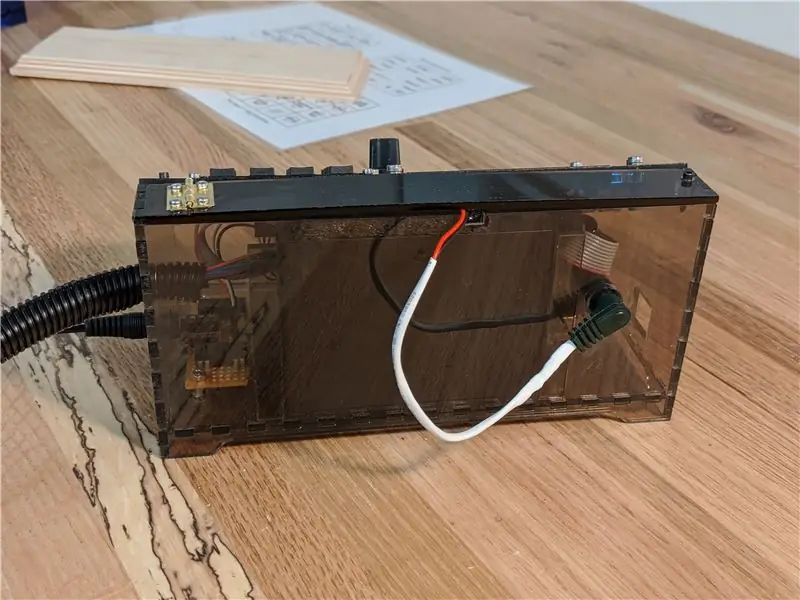
Es gibt viele Möglichkeiten, die im 1. Bild gezeigte Elektronik zu verpacken. Auf Thingiverse gibt es viele Designs für Boxen, die die RAMPS/Mega/LCD-Kombination enthalten, die ein Anfang für eine 3D-gedruckte Version sein könnten. Ich habe einen Laser verwendet, um eine Acrylbox im Konsolenstil aus dem in der beigefügten SVG-Datei angegebenen Design herzustellen. Die Box wurde mit Boxes.py erstellt und die Lochmuster in Lightburn hinzugefügt. Es ist für 2,8 mm Material vorgesehen. Ich entwarf die Box, um den Akku hinter der Elektronik zu halten, und führte sein Stromausgangskabel durch eine Kerbe auf der Rückseite. Ein aufklappbarer Deckel ermöglicht ein einfaches Entnehmen des Akkus. Die Stromeingangsbuchse für das System wird zu einem Loch auf der Rückseite der Box geführt, wo sie mit Sekundenkleber verklebt wird. Bei Batteriebetrieb wird das Batteriekabel wie abgebildet in die Buchse eingesteckt. Der Netzadapter wird bei Netzbetrieb in dieselbe Buchse eingesteckt. Der Akku kann geladen werden, ohne ihn aus der Box zu nehmen, wie in der Abbildung gezeigt.
Schritt 10: Betrieb
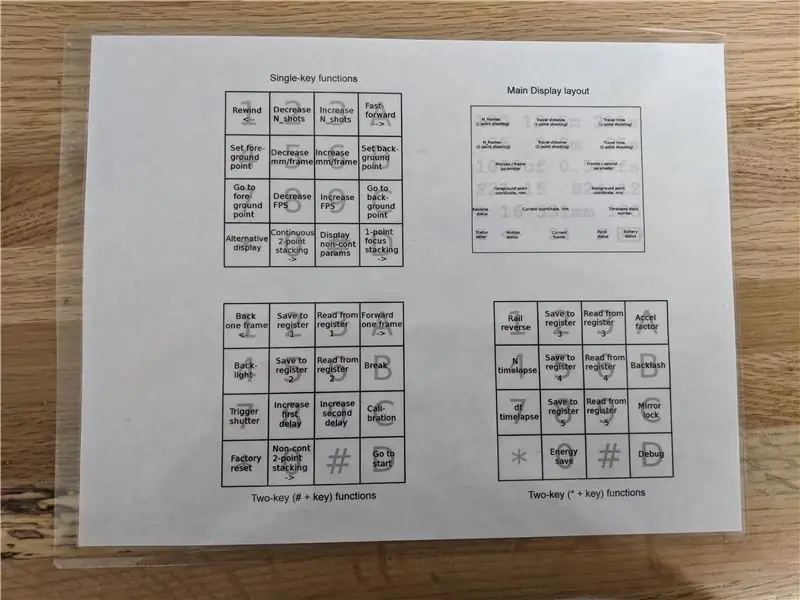
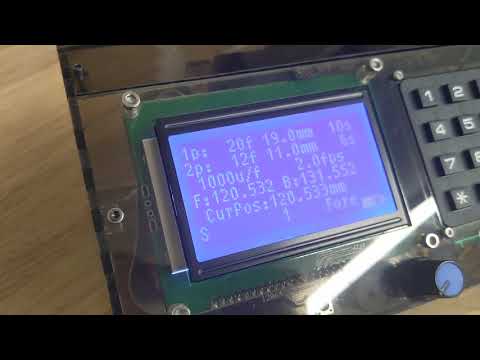
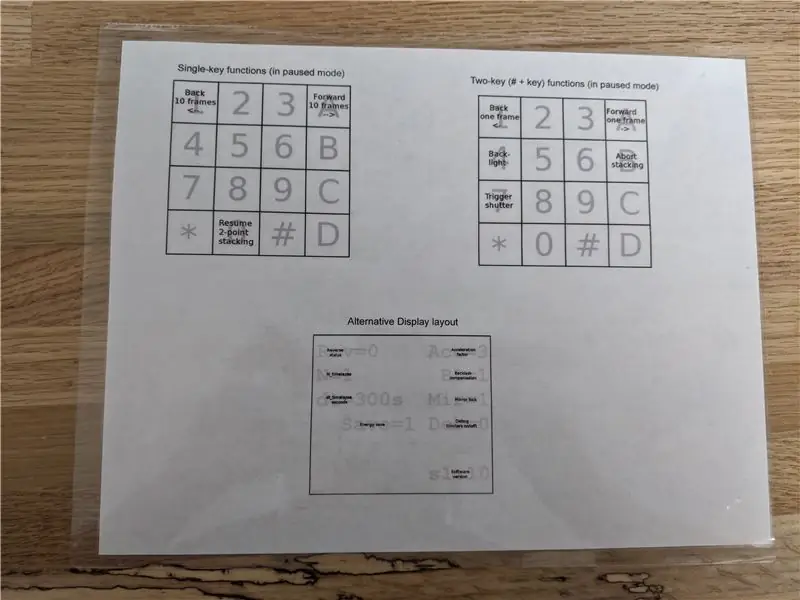
Hier verweise ich Sie zurück auf das ausgezeichnete Benutzerhandbuch von Pulsar124: https://pulsar124.fandom.com/wiki/User_guide. Ich habe wie gezeigt einen laminierten Spickzettel erstellt, der mir hilft, mich an Tastaturbefehle zu erinnern, bis ich mich damit vertraut gemacht habe. Wie bereits erwähnt, unterstützt das LCD keine Steuerung der Hintergrundbeleuchtung, daher funktioniert der Befehl #-4 nicht.
Sehen Sie sich das angehängte Video an, um eine sehr kurze Demo einiger grundlegender Operationen zu erhalten.
Schritt 11: Erstellen Sie Notizen und Gedanken
Die Portierung begann mit FastStacker V1.16. Dies liegt hauptsächlich daran, dass dies die Version ist, die ich für meinen Pro-Mini-basierten Build verwendet habe. Das lag daran, dass ich V1.17 nicht auf den Pro-Mini bringen konnte und ich mich nicht wirklich um die Teleskopsteuerungsfähigkeit von 1.17 kümmerte. Auf dem Mega benötigt diese Version, die ich 1.16a genannt habe, weniger als 20% des Speichers, also ist viel Platz für V1.17 und mehr. Der RAMPS-Port beinhaltete Pin-Mapping und den Ersatz des alten LCD-Treibers durch den u8g2lib-Grafiktreiber. Das größere LCD bot den Luxus zusätzlicher Zeichen, die ich für Labels, Nachrichten und Einheiten der vorhandenen Benutzeroberfläche verwendet habe, um sie für gelegentliche Benutzer etwas zugänglicher zu machen. Wie bereits erwähnt, unterstützt das LCD keine programmgesteuerte Hintergrundbeleuchtungssteuerung, so dass dieser Befehl ausgeblendet wird. Ich habe einige Änderungen im Spannungsüberwachungsbereich vorgenommen, indem ich die interne Spannungsreferenz verwendet und eine weitere kritische Grenzspannungskonstante hinzugefügt habe, die verwendet wird, um die niedrige Spannung zu überprüfen, bevor die Schiene abgeschaltet wird. Ich habe das Design auch darauf ausgerichtet, von 6 Zellen anstatt von 8 wie im ursprünglichen Build zu laufen. Die 6 Zellen sind energieeffizienter, benötigen weniger Platz und reduzieren die Belastung des 5-V-Reglers des Mega ohne Auswirkungen auf die körperliche Leistung. Ich habe den Piepser auf dem LCD verwendet, um einen kurzen Piepton zu geben, wenn eine der Fehlermeldungen angezeigt wird. Ich habe die Standardspielzahl bei 0,2 mm belassen, wie sie ursprünglich war, obwohl ich vermute, dass sie bei der Antispielmutter geringer ist, aber ich habe nicht versucht, sie zu messen. Wenn Sie die Spielkompensation deaktivieren und in einem steilen Winkel arbeiten, schalten Sie die Energiesparfunktion aus, damit Sie die Position sicher halten können. Eine Funktion, die ich mir in der Software gewünscht hätte, ist die Tastatursteuerung der Richtung der Spielkompensation (ohne die Betriebsrichtung des Schienenbetriebs mit dem Befehl *-1 umzukehren). Dies könnte dem ungenutzten Tastendruck für die Hintergrundbeleuchtung zugeordnet werden. Je nach Betriebsrichtung bin ich mir nicht sicher, ob die aktuelle Kompensationsrichtung immer richtig ist, d. h. dass Sie immer davon ausgehen können, dass der Schlitten sich vom Motor weg bewegt immer die Richtung ist, die nicht kompensiert werden muss. Ich denke, bei großen Stapeln spielt das keine Rolle. Der Code ist für 16 Mikroschritte konfiguriert. Es gab eine Konstante im Code, der verwendet wurde, um eine vernünftige Anzahl von Frames für 1pt-Stacks zu überprüfen, die ich in stacker.h als RAIL_LENGTH definiert und auf 180 gesetzt habe, was der ungefähre Verfahrbereich für diese Schiene ist. Ändern Sie, wenn Ihre Schiene anders ist.
Diese Plattform bietet neben dem Arbeitsspeicher noch weitere zusätzliche Funktionen, die dieser Build nicht nutzt. Die Grafikfähigkeiten des LCD könnten für mehr als das Zeichnen des Batterieladezustandsindikators verwendet werden. Der optische Encoder-Knopf ist verlockend und ich habe versucht, ihn in das Projekt zu integrieren. Ich fand einen guten Treiber, integrierte ihn in die Build- und Hauptschleife und versuchte, der Software vorzutäuschen, dass die Tasten "1" und "A" gedrückt wurden, wenn der Knopf gedreht wurde. Es funktionierte irgendwie, war aber ruckartig und bot keine nützliche Funktion, also zog ich es heraus. Auf der RAMPS-Platine befinden sich mehrere unbenutzte Steppertreiber, die zur Steuerung zusätzlicher Stepper verwendet werden könnten, wenn dies von Nutzen sein könnte.
Die 3D-Drucker-Controller wie RAMPS bieten großartige Ausgangspunkte für solche Builds und ich hoffe, dass noch ein paar Leute von der coolen Software von Pulsar124 profitieren können, die auf dieser einfach zu integrierenden Plattform gehostet wird.
Empfohlen:
PC-Build: 5 Schritte
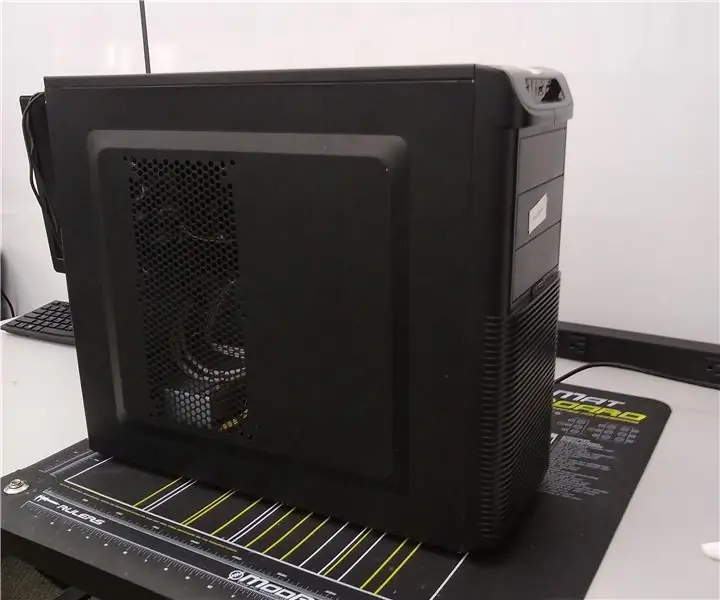
PC Build: Heute bauen Sie Ihren eigenen Computer. Die Komponenten, die Sie benötigen, sind: Motherboard RAM CPU Heat Sync Festplatte oder SSD Netzteil Gehäuselüfter GPUEs gibt viele Vorteile, einen eigenen Computer zu bauen, z
DIY RACING GAME SIMULATOR BUILD TEIL 1: 6 Schritte

DIY RACING GAME SIMULATOR BUILD TEIL 1: Hallo zusammen Willkommen, heute zeige ich euch, wie ich einen "Racing Game Simulator" mit Hilfe von Arduino UNO. YouTube-Kanal " abonnieren Sie unbedingt meinen Kanal A Builds(Hier klicken)" Dies ist der Build-Blog, So le
Computer-Build-Anleitung: 8 Schritte
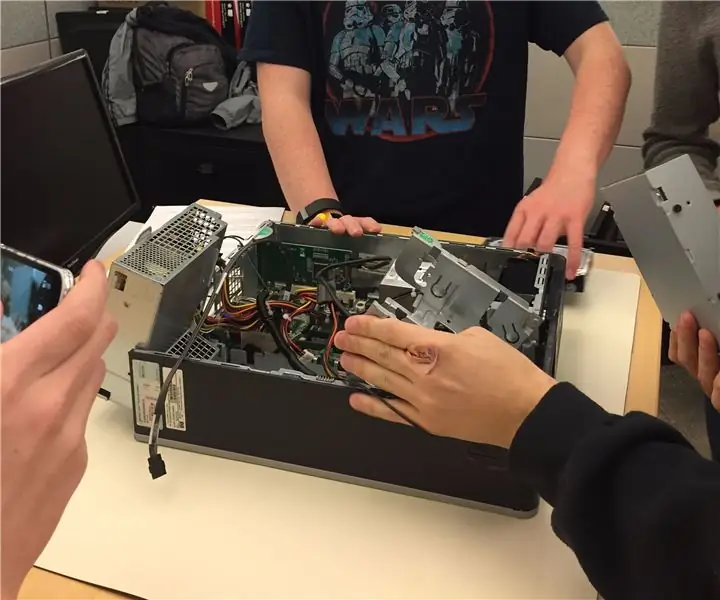
Computer Build Guide: Dies ist eine Anleitung zum Bau eines eigenen, benutzerdefinierten PCs. Obwohl einige denken, dass es einfach billiger und bequemer ist, einen vorgefertigten PC zu kaufen, würden die meisten Benutzer feststellen, dass es tatsächlich weniger teuer ist, ihn zusammenzustellen
IT-PC-Build: 9 Schritte
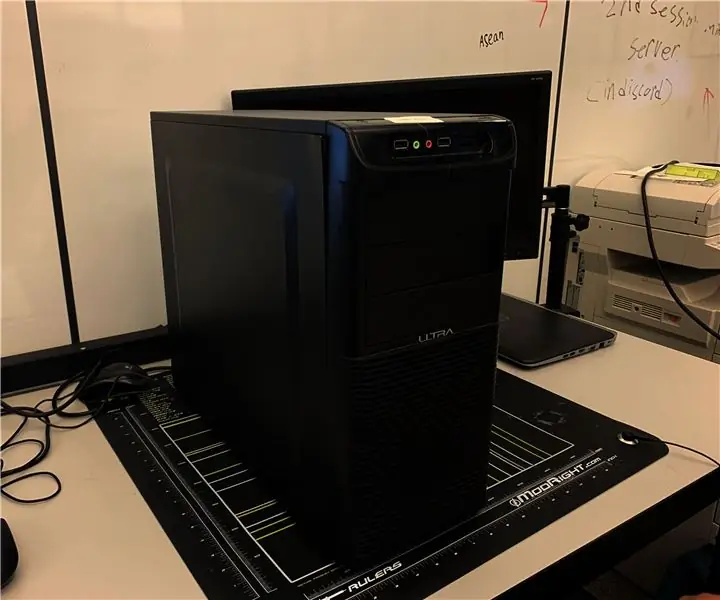
IT PC Build: Dies sind die einfachen Schritte zum Erstellen eines PCs. Dies sind die Materialien, die Sie benötigen…1. Motherboardi. CPUii. RAMiii. Kühlkörper und Wärmeleitpaste2. Stromversorgung3. Fall4. Ventilatoren5. Festplatte6. Kabel für Festplatte, Netzteil usw. 7. Antistatik
35 $ Wireless Follow Focus vom Kran 2 Schritte
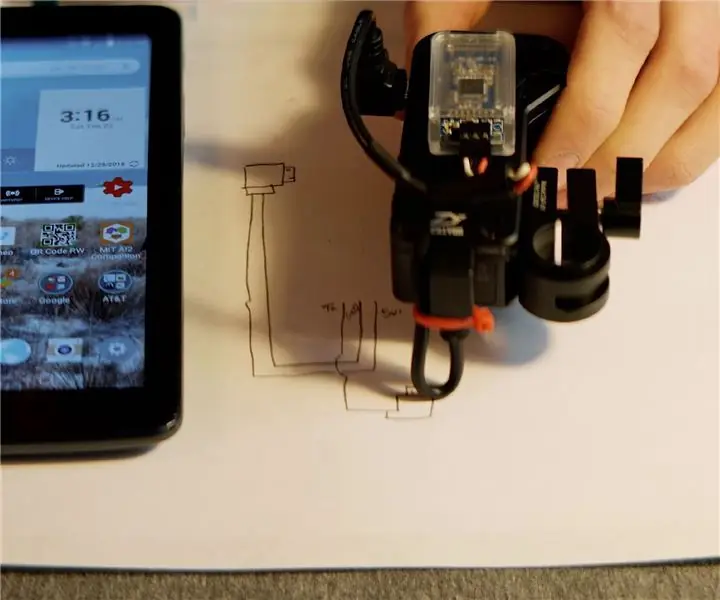
35 US-Dollar drahtloser Follow-Fokus vom Kran 2: Lassen Sie uns einen drahtlosen Follow-Fokus für 35 US-Dollar für Ihre Kamera erstellen. Dies kann hervorragend für Filmsets mit einem dedizierten Fokus-Puller verwendet werden und kann verwendet werden, um den Zoom oder den Fokus jeder Kamera drahtlos einzustellen