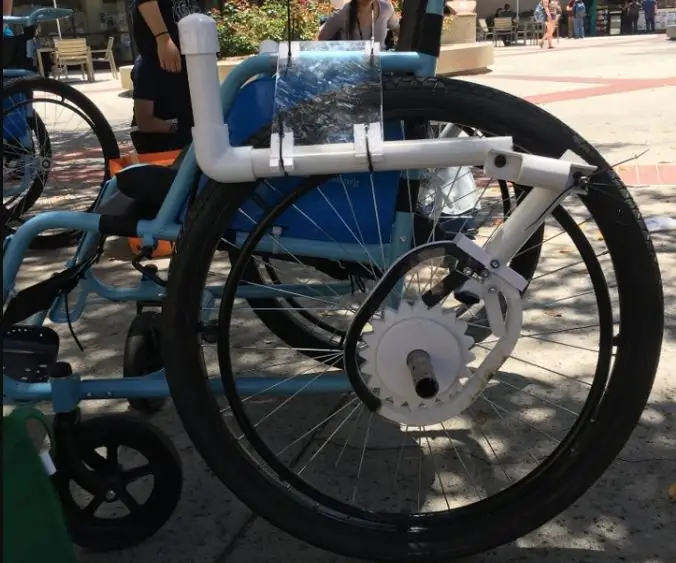
Inhaltsverzeichnis:
- Schritt 1: Erstellen Sie den äußeren Gehäusedeckel für den Körper auf SolidWorks
- Schritt 2: Erstellen Sie den Körper in SolidWorks
- Schritt 3: Erstellen Sie die Verbindung in SolidWorks
- Schritt 4: Erstellen Sie den Hebelarm/-griff auf SolidWorks
- Schritt 5: Erstellen Sie die Armlehne auf SolidWorks
- Schritt 6: Erstellen Sie das Zahnrad in SolidWorks
- Schritt 7: Sperrklinke in SolidWorks erstellen
- Schritt 8: Richtungsknopf auf SolidWorks erstellen
- Schritt 9: Erstellen Sie die Rohrhalterung
- Schritt 10: Beginnen Sie mit der Montage auf SolidWorks
- Schritt 11: Bestellen Sie Teile von McMaster-Carr
- Schritt 12: Teile aus dem Baumarkt beziehen
- Schritt 13: Herstellung der Teile
- Schritt 14: Setzen Sie alle Teile zusammen
- Schritt 15: Iteratives Testen
- Schritt 16: Beitragsseite
2025 Autor: John Day | [email protected]. Zuletzt bearbeitet: 2025-01-23 12:52
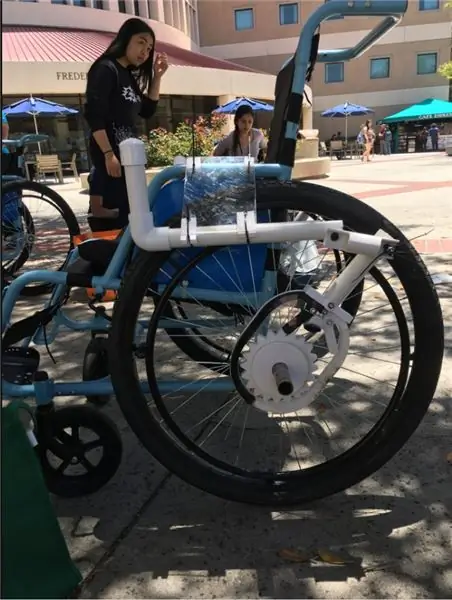
Der gewöhnliche Rollstuhl enthält viele Mängel für Personen mit einer Schwäche der oberen Extremitäten oder begrenzten Ressourcen. Unser Team wurde beauftragt, einen Rollstuhlhebelantrieb für die Rollstühle der Free Wheelchair Mission zu entwickeln, der es Benutzern ermöglicht, weiter auf ihren Stühlen zu gehen und Menschen mit einer Schwäche der oberen Extremitäten zu helfen, die Stühle zu benutzen. Der Rollstuhl-Hebelantrieb des Support Systems ist ein kostengünstiges Gerät, das den Bedarf an Schulterbewegungen erheblich verringert und Ermüdungserscheinungen durch horizontale Hebelantriebe anstelle von vertikalen entgegenwirkt, was für geschwächte Patienten und Patienten in ländlichen Gebieten geeignet wäre. Der typische vertikale Hebelarmantrieb konzentriert sich zu sehr auf die Muskeln in den Armen und Schultern, was bei Patienten mit einer Schwäche der oberen Extremität zu Komplikationen führen kann. Aus diesem Grund hat unser Team einen horizontalen Hebelantrieb entwickelt, der auf die Verwendung der Brustmuskulatur abzielt, um Menschen zu erleichtern, die ihre Schultermuskulatur nicht nutzen können.
Markt- und Wertversprechen
Um die Schulterschmerzen und -ermüdung zu bekämpfen, die mit dem Rollstuhlfahren bei Menschen insbesondere aus ländlichen Dörfern mit nicht asphaltierten Straßen verbunden sind, zielt unser Hebelantrieb darauf ab, das Problem zu lindern, indem er eine Vorwärts- / Rückwärtsbewegung anstelle einer Aufwärts- / Abwärtsbewegung verwendet eine verbesserte Armlehne für Komfort und Unterstützung. Da ländliche Dörfer und unbefestigte Straßen häufig sehr steinig und uneben sind, müsste der Patient noch mehr Kraft auf den Hebelarm aufwenden, um seinen Rollstuhl im Vergleich zu einem glatten Weg auf eine gewisse Distanz zu bewegen. Daher werden die Menschen mit Schwächen der oberen Extremität in ländlichen Gebieten noch stärker behindert, da sie mehr Bewegung und Kraft benötigen, um sich von Ort zu Ort zu bewegen, was zu Problemen führt, da sie ständig schwächer werden, da sie ihre Schultermuskulatur im Alltag weiter beanspruchen. So können sich Personen aus ländlichen Gebieten mit einer Schwäche der oberen Extremität durch den Einsatz eines horizontalen Hebelantriebs nicht nur frei bewegen, sondern auch die Belastung der Schultermuskulatur reduzieren, da sie stattdessen die Kraft in der Brust verwenden.
Kostenanalyse
Wir haben uns für PVC, Acryl und ABS entschieden. Es war ein Kompromiss aus Stärke und Kosten. Die drei Materialien sind relativ billiger, aber robust genug, um richtig zu funktionieren. Die geschätzten Kosten betragen etwa 170 US-Dollar. Wir hatten ursprünglich geplant, für die meisten Komponenten unseres Hebelantriebs wie das Außengehäuse und die Armgriffe Aluminium zu verwenden, da Aluminium billiger ist als Stahl. Nach Recherchen stellten wir jedoch fest, dass die Verwendung von dicken Blechen und Stangen aus Aluminium aufgrund der hohen Kosten für die Gewinnung erheblicher Metallmengen nicht ideal wäre. Stattdessen haben wir günstigere Alternativen gefunden, indem wir unterschiedliche Materialien für verschiedene Teile verwendet haben. Wir haben eine große Acrylplatte für das Außengehäuse verwendet und die Platte mit Laser in kleinere Teile geschnitten, was ungefähr 25 US-Dollar kostete. Im Vergleich dazu hätten große Aluminiumbleche über 70 US-Dollar gekostet. Außerdem haben wir uns für unsere Armgriffe auch für PVC-Rohre anstelle von Metallstangen entschieden, da PVC-Rohre nicht nur robust, sondern auch noch extrem günstig sind. Obwohl Aluminiumstangen stabiler gewesen wären, hätten wir für jede Seite des Rollstuhls etwa 30 US-Dollar ausgegeben. Im Gegensatz dazu kosteten die PVC-Rohre etwa 5 US-Dollar. Der Großteil unserer Kosten stammt aus dem ABS-3D-Druck. Da wir drei Teile unseres Systems gedruckt haben, dauerte die Gesamtzeit zum Drucken all dieser Teile insgesamt etwa 32 Stunden. Infolgedessen belief sich der Stundensatz für die Nutzung des 3D-Druckers auf 130 US-Dollar.
Material- und Prototypendesign
- PVC-Rohr ~ 2,16 $
- PVC-Sockelkappe ~ 1,66 $
- PVC 90-Grad-Ellbogen ~ 2,28 $
-Acrylblatt ~ 24,98 $
- ABS-Getriebe, ABS-Klinken, ABS-Knöpfe ~ 130 $
- Stahlschrauben ~ 6,92 $
- Gummibänder ~ 3,18 $
- E6000 Bastelkleber ~ $4.29
Schritt 1: Erstellen Sie den äußeren Gehäusedeckel für den Körper auf SolidWorks
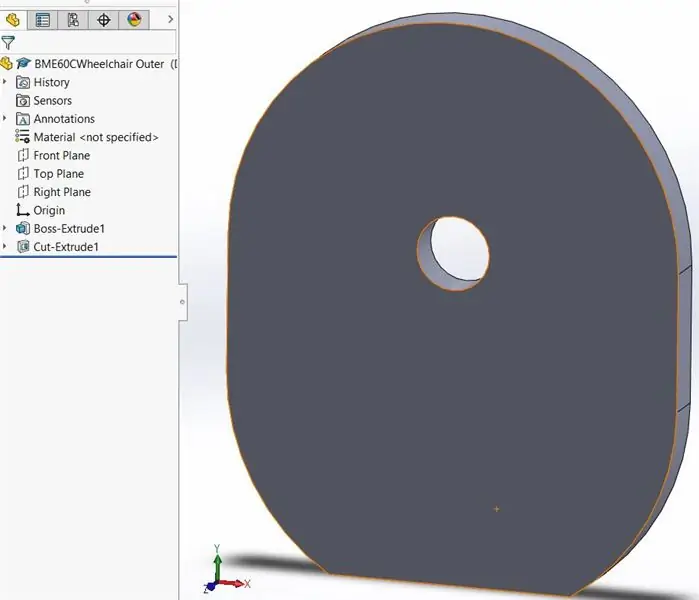
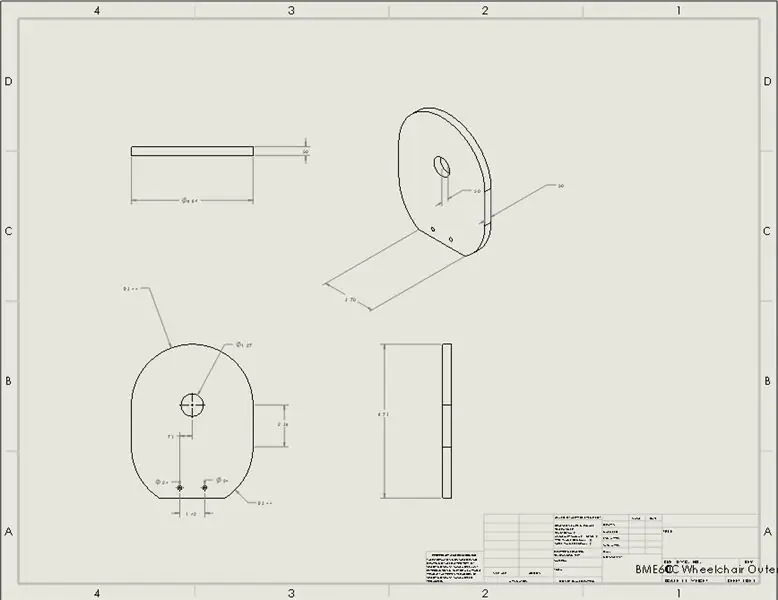
Stellen Sie vor dem Start des gesamten Projekts die Abmessungen mit MMGS ein.
Erstellen Sie mit der vorderen Ebene eine neue Skizze und zeichnen Sie am Ursprung einen Kreis mit einem Durchmesser von 175 mm. Skizzieren Sie dann zwei vertikale Linien an den Tangenten des Kreises, die beide 60 mm lang sind. Zeichnen Sie anschließend Tangentenbögen am Ende beider Linien und verbinden Sie sie mit einer horizontalen Linie. Trimmen Sie dann mit der Funktion "Objekte trimmen" die untere Hälfte des Kreises innerhalb der Region.
Sobald die Skizze fertig ist, extrudieren Sie die Skizze mit einer Blindextrusion von 12,70 mm. Sobald die Extrusion abgeschlossen ist, öffnen Sie eine neue Skizze und zeichnen Sie einen Kreis, der mit der Spitze der Tangentenlinien mit einem Durchmesser von 32,20 mm ausgerichtet ist, und schneiden Sie die Extrusion mit "durch alle" ein Loch.
Um die unteren beiden Kreise zu erstellen, öffnen Sie eine neue Skizze und zeichnen Sie zwei Kreise mit einem Durchmesser von 6 mm und machen Sie sie 15 mm vom Boden und 58,84 mm von der Mitte des Tangentenbogens entfernt. Sobald die Skizze fertig ist, verwenden Sie Cut Extrude mit "through all", um zwei Löcher zu machen.
Schritt 2: Erstellen Sie den Körper in SolidWorks
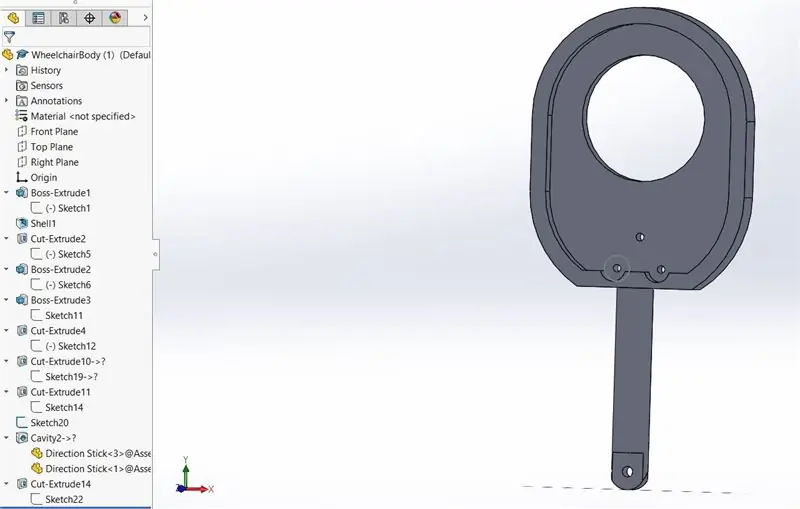
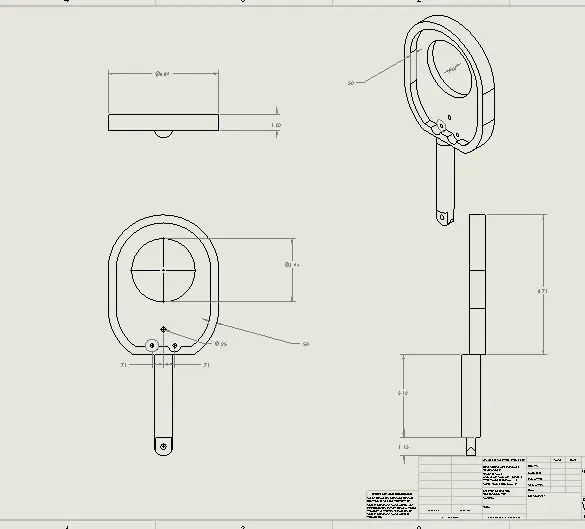
Um den Körper zu beginnen, wiederholen Sie die Skizze wie in Teil 1, um die Gesamtform des Körpers zu erstellen und ihn 25,40 mm zu extrudieren. Nachdem das Teil extrudiert wurde, verwenden Sie die Schalenoption auf einer der Flächen des Teils mit der Abmessung 12,70 mm.
Öffnen Sie anschließend eine neue Skizze und zeichnen Sie einen Kreis in der Mitte des Teils mit einem Durchmesser von 100 mm, der 133,84 mm von der Unterseite und 87,50 mm von den Seiten des Teils entfernt ist. Sobald die Skizze fertig ist, schneiden Sie die Extrusion erneut mit "through all", um ein Loch zu erstellen.
Um den Hebel zu erstellen, erstellen Sie eine neue Skizze auf der oberen Ebene und drehen Sie das Teil nach unten. Beginnen Sie mit der Skizze, indem Sie einen Kreis mit einem Durchmesser von 28,74 mm an der Basis des vorherigen Teils erstellen und diesen um 130 mm extrudieren.
Nachdem der Hebel erstellt wurde, erstellen Sie eine neue Skizze an der Basis des Hebels. Zeichnen Sie zwei horizontale Linien mit gleichem Abstand vom Ursprung, die 25,10 mm lang sind. Danach verbinden Sie die beiden Linien mit Tangentenbögen mit der Höhe von 14 mm. Sobald die Skizze fertig ist, extrudieren Sie die neue Skizze 30 mm blind.
Erstellen Sie mit dem neuesten extrudierten Teil eine neue Skizze auf der vorderen Ebene und skizzieren Sie einen Kreis, der 14,95 mm von der Oberseite und 12,55 mm von der Seite entfernt ist. Schneiden Sie dann die Extrusion durch alle, um ein Loch zu erstellen.
Skizzieren Sie mit dem Gesamtkörper zwei Löcher an der Unterseite des Körpers mit einem Durchmesser von 6 mm und einem Abstand von 36 mm voneinander, 15 mm von der Unterseite und 58,84 mm von der Oberseite der Tangentenbögen. Schneiden Sie anschließend die Extrusion durch alle, um zwei Löcher zu erstellen.
Erstellen Sie unten am Teil eine neue Skizze. Machen Sie auf beiden Seiten gerade Linien mit 14,93 mm. Machen Sie eine horizontale Linie von 28,74 mm, um die beiden Linien zu verbinden. Zeichnen Sie einen Kreis mit einem Radius von 14,37 mm und richten Sie ihn bereits am Kreis in der Mitte aus. Schneiden Sie es zu einem Halbkreis. Schneiden Sie die Extrusion durch die gesamte rampenförmige Figur im unteren Teil des Teils, um eine abgerundete Kante zu hinterlassen.
*Erstellen Sie zur Vorbereitung der Kavität eine neue Skizze in der Rückwand. Zeichnen Sie einen Kreis mit einem Radius von 20,57 mm, der 15 mm vom unteren Rand und 58,84 mm vom seitlichen Tangentenbogen entfernt ist. Nachdem Sie alle Teile zusammengebaut haben, bearbeiten Sie das Teil innerhalb der Baugruppe und verwenden das Hohlraum-Feature, um die Halbkreise zu erstellen.
Erstellen Sie auf der vorderen Ebene eine neue Skizze. Zeichnen Sie in der Mitte einen Kreis mit einem Durchmesser von 6,35 mm zwischen dem großen Kreis und den beiden kleinen Kreisen unten. Machen Sie den Kreis 40,13 mm vom Boden entfernt und 33,70 mm vom Tangentenbogen an den Seiten entfernt. Schneiden Sie anschließend die Extrusion durch alle, um einen kleinen Kreis in der Mitte zu erstellen.
*Dieser Schritt wird später fortgesetzt, nachdem alle Teile zusammengebaut wurden.
Schritt 3: Erstellen Sie die Verbindung in SolidWorks
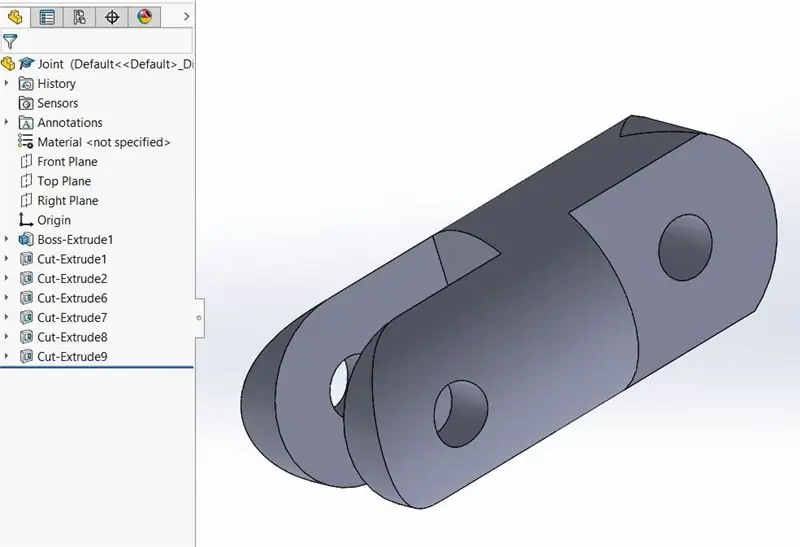
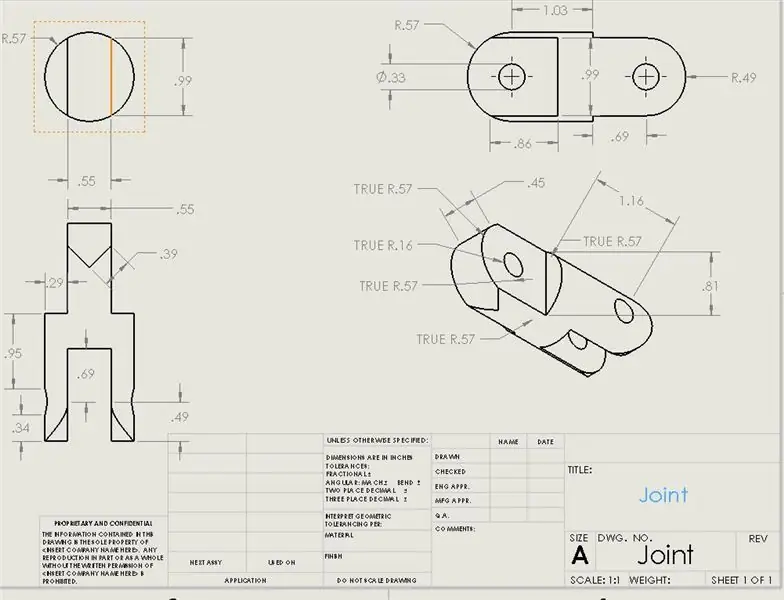
Um mit der Verbindung zu beginnen, erstellen Sie zunächst eine neue Skizze auf der Frontplatte und zeichnen Sie einen Kreis mit einem Durchmesser von 28,74 mm. Extrudieren Sie den gerade skizzierten Kreis mit 120 mm blind.
Drehen Sie dann das Teil und skizzieren Sie es auf der Rückseite. Zeichnen Sie zwei vertikale Linien mit einer Länge von 25,10 mm und 7,37 mm vom Rand des Kreises entfernt. und schneiden Sie das Extrudieren mit "blind" und einer Tiefe von 30 mm für beide Bereiche.
Als nächstes skizzieren Sie von der rechten Ebene aus einen Kreis in der Region, die wir gerade geschnitten haben. Der Durchmesser sollte 8,38 mm betragen mit einem Abstand von 12,55 mm von der Oberkante und 14,95 mm von der Seitenkante. Machen Sie einen Blindschnitt von 30 mm.
Machen Sie auf der rechten Ebene auf beiden Seiten gerade Linien mit einer Länge von 15,05 mm. Machen Sie eine vertikale Linie von 28,74 mm, um die beiden Linien zu verbinden. Zeichnen Sie einen Kreis mit einem Radius von 14,37 mm und richten Sie ihn bereits am Kreis in der Mitte aus. Schneiden Sie es zu einem Halbkreis. Schneiden Sie die Extrusion durch die gesamte rampenförmige Figur im unteren Teil des Teils, um eine abgerundete Kante zu hinterlassen.
Skizzieren Sie anschließend von der Rückwand aus gesehen zwei vertikale Linien mit einer Länge von 25,10 mm und 7 mm von der Mitte. Machen Sie einen Blindschnitt mit einer Tiefe von 35 mm.
Skizzieren Sie auf der rechten Ebene einen Kreis auf dem rechten Teil, wobei die Mitte 17,24 mm von der linken Kante des Teils entfernt ist. Blindschnitt durch alles extrudieren, um einen Kreis zu erstellen
Wiederholen Sie auf der rechten Ebene die rampenförmige Figur auf der linken Seite des Teils.
Schritt 4: Erstellen Sie den Hebelarm/-griff auf SolidWorks
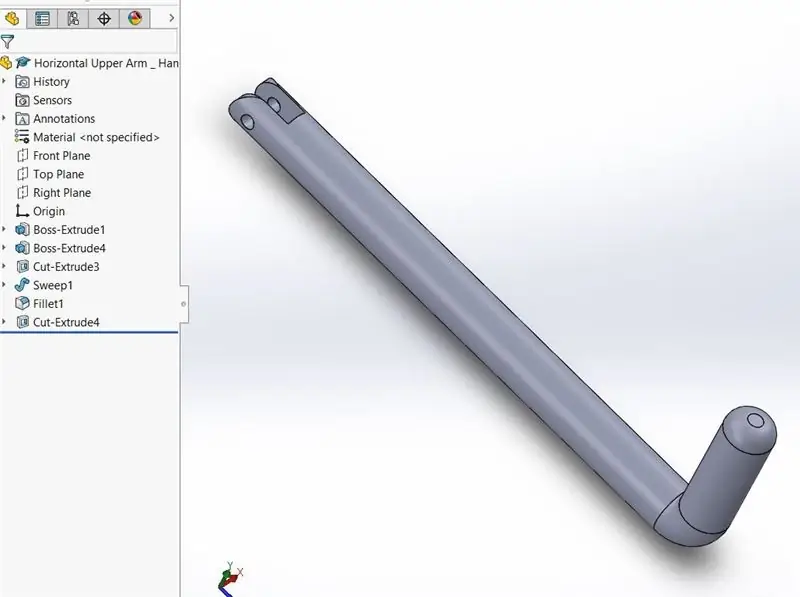
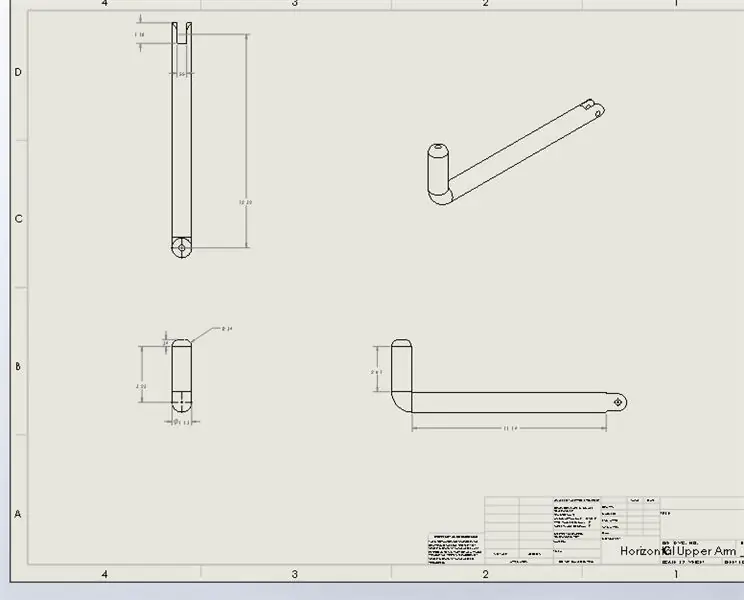
Skizzieren Sie auf der vorderen Ebene einen Kreis mit einem Durchmesser von 28,75 mm im Ursprung. Boss extrudiert es 275 mm.
Gehen Sie als nächstes zur Rückwand und skizzieren Sie zwei vertikale Linien mit einer Länge von 25,10 mm mit einem Abstand von 7 mm von der Mitte. Extrudieren Sie die beiden Linien so, dass in der Mitte eine Lücke mit einem Extrusionsmaß von 35 mm vorhanden ist.
Skizzieren Sie auf dem gerade extrudierten Teil einen Kreis mit einem Durchmesser von 8,40 mm mit einem Abstand von 17,76 mm von der Kreismitte zum Rand und 12,56 mm von der Unterseite des Teils. Schneiden Sie die Extrusion durch alle, um ein Loch zu erstellen.
Erstellen Sie auf der rechten Ebene eine kurze Linie mit der Länge von 9,24 mm, die mit der ganz linken Seite des Teils verbunden ist. Zeichnen Sie einen Bogen mit einem Radius von 30 mm. Zeichnen Sie dann eine vertikale Linie, die das andere Ende des Bogens mit der Länge von 76,39 mm verbindet. Nachdem die Skizze fertig ist, fegen Sie die Skizze.
Danach filetieren Sie die Oberseite des Teils, das wir gerade 10 mm gefegt haben.
Machen Sie schließlich auf der rechten Ebene auf beiden Seiten des Teils mit dem von uns erstellten Loch gerade horizontale Linien, die 17,78 mm lang sind. Machen Sie eine vertikale Linie von 25,10 mm, um die beiden Linien zu verbinden. Zeichnen Sie einen Kreis mit einem Radius von 12,56 mm und richten Sie ihn bereits am Kreis in der Mitte aus. Schneiden Sie es zu einem Halbkreis. Schneiden Sie die Extrusion durch die gesamte rampenförmige Figur im unteren Teil des Teils, um eine abgerundete Kante zu hinterlassen.
Schritt 5: Erstellen Sie die Armlehne auf SolidWorks
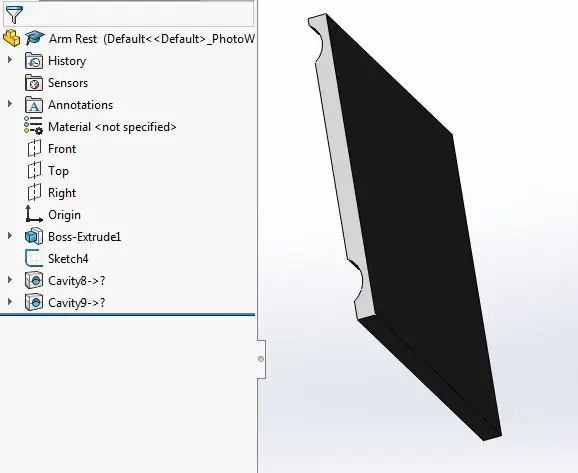
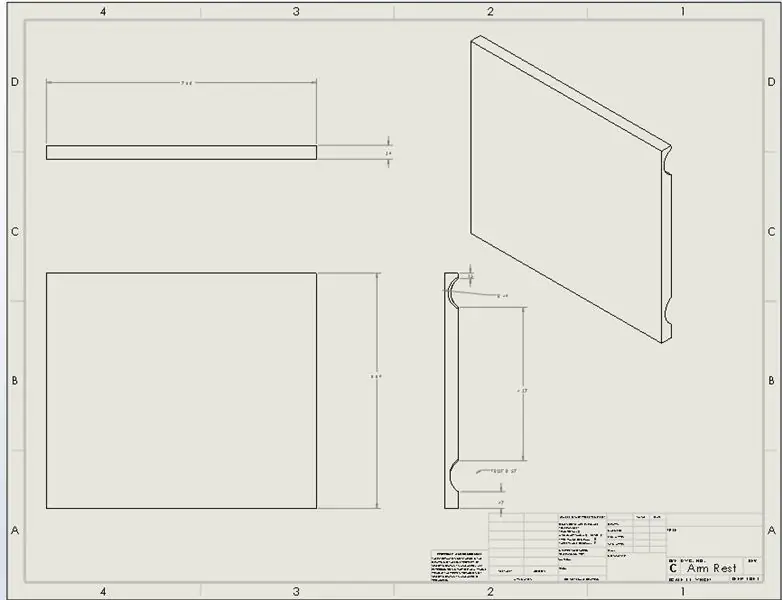
Skizzieren Sie auf der vorderen Ebene ein Rechteck mit einer Höhe von 170 mm und einer Länge von 195 mm und stellen Sie ein Blindprofil von 10 mm her.
*Verwenden Sie nach der Montage das Hohlraum-Feature, um die Vertiefungen auf dem rechteckigen Prisma zu erstellen
Schritt 6: Erstellen Sie das Zahnrad in SolidWorks
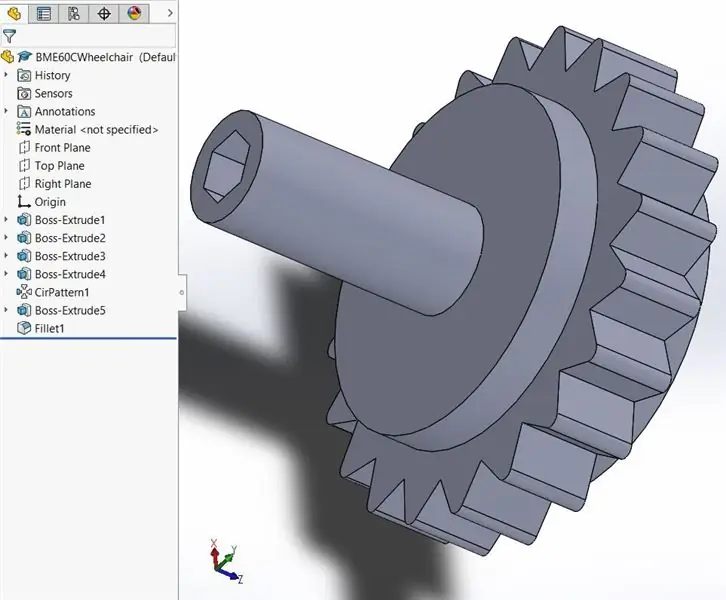
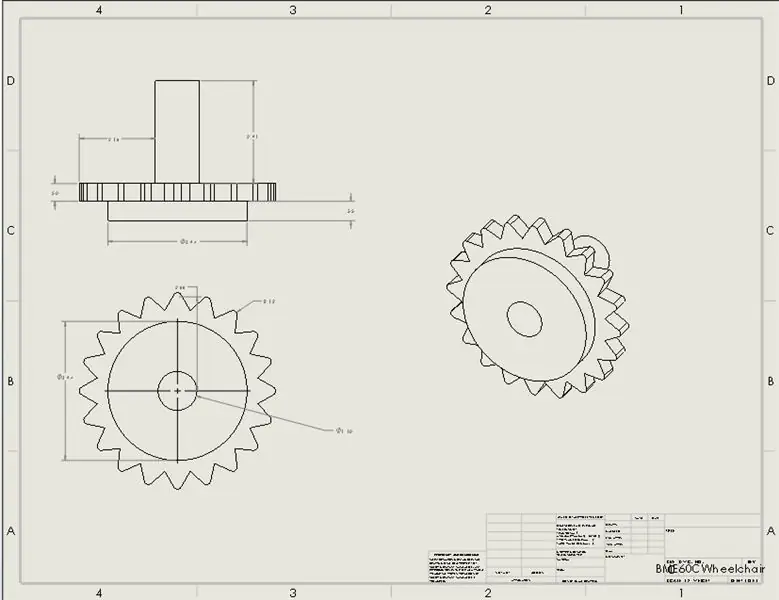
Um mit dem Zahnrad zu beginnen, erstellen Sie eine neue Skizze auf der vorderen Ebene und zeichnen Sie zwei Kreise vom gleichen Punkt mit den Durchmessern 25,40 mm und 31,75 mm. Anschließend mit einer Blindextrusion bei 30 mm Vorsprung extrudieren.
Sobald die Extrusion abgeschlossen ist, erstellen Sie eine weitere Skizze auf der vorderen Ebene und zeichnen Sie einen weiteren Kreis mit einem Durchmesser von 31,75 mm und extrudieren Sie 20 mm.
Skizzieren Sie als nächstes auf der vorderen Ebene einen Kreis mit einem Durchmesser von 100 mm und extrudieren Sie ihn 12,70 mm.
Zeichnen Sie auf die Oberseite des gerade extrudierten Teils ein gleichseitiges Dreieck mit einer Seitenlänge von 30 mm. Extrudieren Sie das Dreieck 12,70 mm.
Verwenden Sie nach Abschluss der Extrusion das kreisförmige Muster-Feature, um 20 gleichmäßige Dreiecke um das Teil herum zu erhalten. Verrunden Sie dann alle Kanten der Dreiecke.
Skizzieren Sie auf der vorderen Ebene einen weiteren Kreis mit einem Durchmesser von 100 mm und extrudieren Sie ihn 13,97 mm.
Um das Loch in der Mitte des Zahnrads zu erstellen, skizzieren Sie einen Kreis auf der Rückwand mit dem Durchmesser 27,94 mm und schneiden Sie die Extrusion bis zur Oberfläche.
Schritt 7: Sperrklinke in SolidWorks erstellen
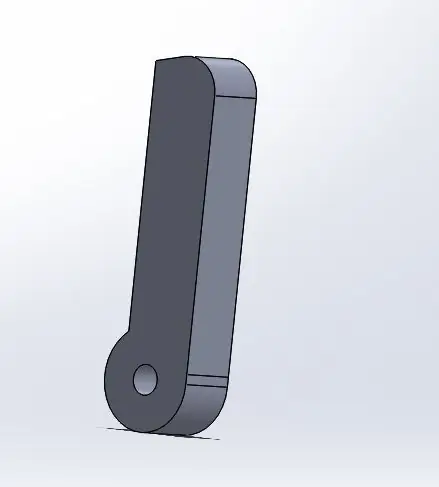
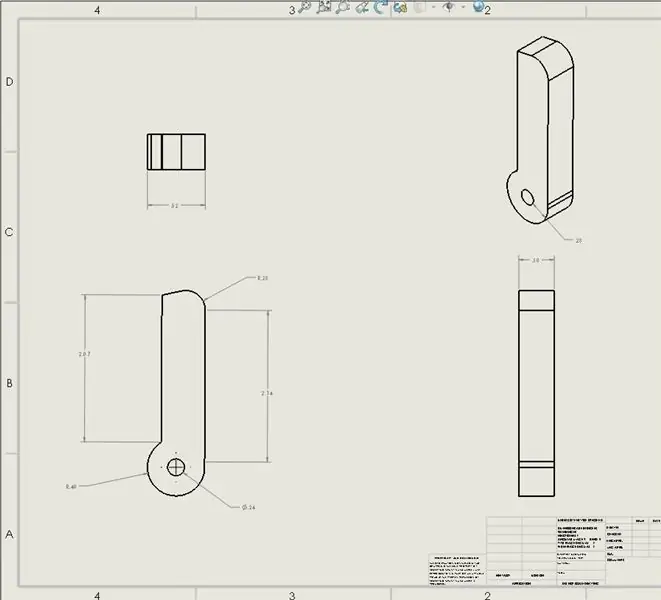
Zeichnen Sie auf der vorderen Ebene eine vertikale Linie mit einer Länge von 2,07 Zoll. Zeichnen Sie anschließend einen Bogen mit einem Radius von 0,40 Zoll, der mit dem unteren Ende der vertikalen Linie verbunden ist. Zeichnen Sie außerdem eine horizontale Linie, die mit der oberen Kante der vertikalen Linie verbunden ist. Klicken Sie mit intelligenten Bemaßungen auf die obere Kante und dann auf die vertikale Linie, und legen Sie den Winkel auf 78,00 Grad fest.
Nachdem der Winkel eingestellt wurde, zeichnen Sie eine weitere vertikale Linie, die mit der schrägen Linie mit einer Länge von 2,14 Zoll verbunden ist. Verrunden Sie dann die Kante dieser Linie mit der horizontalen Linie mit einem Radius von 0,28 Zoll.
Sobald die Skizze fertig ist, extrudieren Sie mit einer Blindextrusion 0,5 Zoll. Um das Loch in der Mitte zu erstellen, skizzieren Sie einen Kreis mit einem Radius von 0,12 Zoll in der Mitte des Teils und verwenden Sie die Schnittextrusion durch alles.
Schritt 8: Richtungsknopf auf SolidWorks erstellen
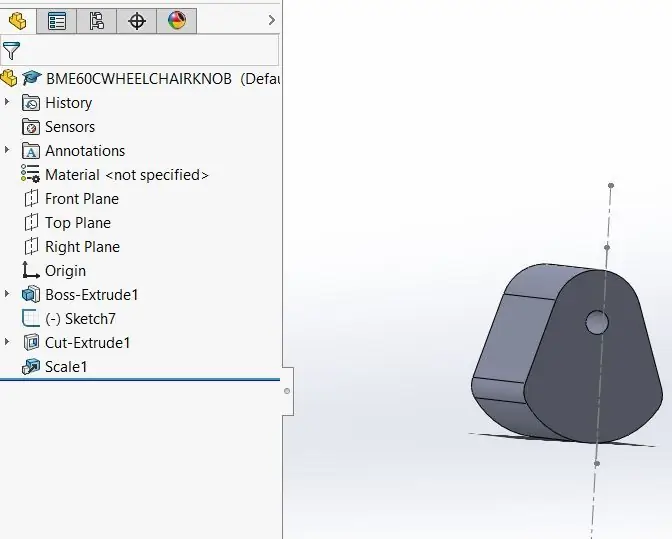
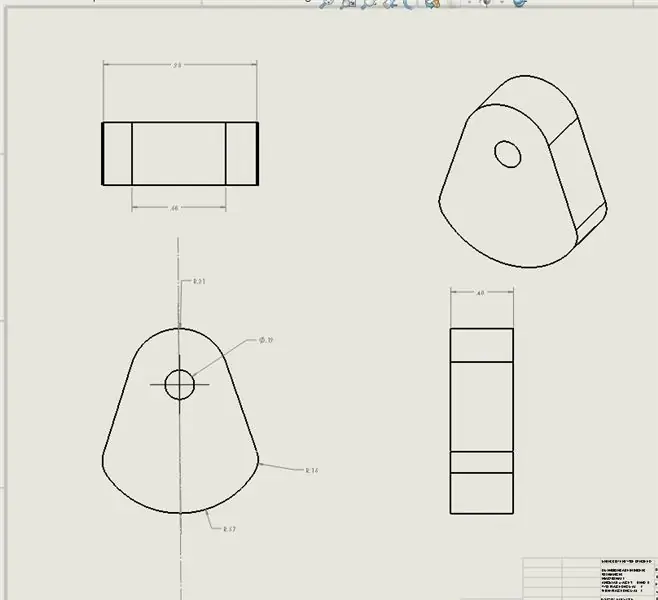
Skizzieren Sie auf der vorderen Ebene eine vertikale Mittellinie. Skizzieren Sie dann oben auf der Mittellinie einen Bogen mit einem Radius von 10 mm. Zeichnen Sie dann auf beiden Seiten schräge Linien mit einer Länge von 18,26 mm. Zeichnen Sie dann auf beiden Seiten einen Bogen mit einem Radius von 5 mm. Um beide Seiten zu verbinden, zeichnen Sie einen weiteren Bogen mit einem Radius von 18 mm. Extrudieren Sie die Skizze mit Blindextrusion 12,70 mm.
Um ein Loch zu erstellen, skizzieren Sie einen Kreis mit einem Durchmesser von 5,90 mm, dessen Mittelpunkt 8 mm vom Ursprung entfernt ist. Verwenden Sie geschnittenes Extrudieren bis zur Oberfläche.
Skalieren Sie das Teil um den Schwerpunkt mit einem Skalierungsfaktor von 0,8 mm.
Schritt 9: Erstellen Sie die Rohrhalterung
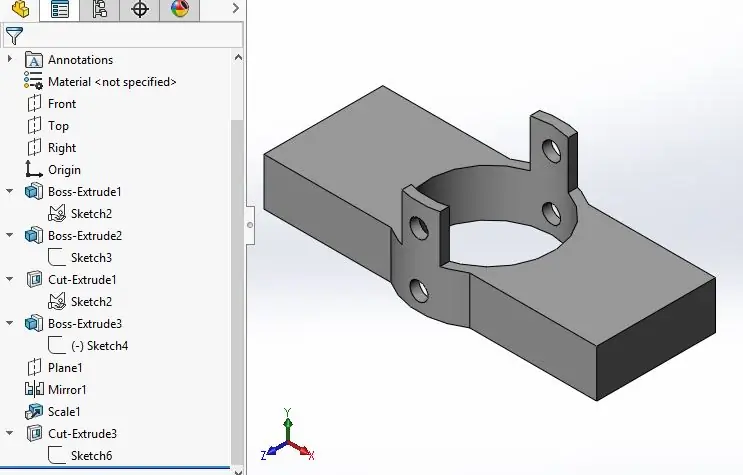
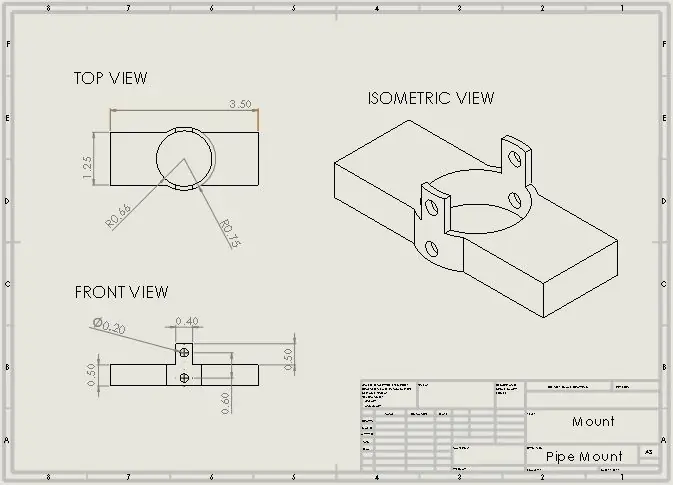
Um die Rohrhalterung zu erstellen, die den Hebelarm am Getriebekörper befestigt, beginnen Sie mit einer Skizze von zwei Kreisen. Der Innenkreis sollte den Durchmesser des PVC-Rohrs haben, damit er leicht herumgleiten kann, daher sollte er 1,3125 Zoll betragen. Der äußere Kreis sollte etwa 1,5 Zoll groß sein. Stellen Sie sicher, dass die beiden Kreise konzentrisch sind, und extrudieren Sie den Teil zwischen den beiden Kreisen um 0,5 Zoll. Skizzieren Sie dann ein Rechteck, das der Unterseite des Außengehäuses des Zahnrads entspricht. Dies wäre ein Rechteck von 3,5 Zoll mal 1,25 Zoll. Zentrieren Sie dieses Rechteck um den Kreis, indem Sie die lange Kante des Rechtecks auf einen Abstand von 1,75 Zoll von der Mitte des Kreises und die kurze Kante des Rechtecks auf 0,63 Zoll von der Mitte des Kreises einstellen. Extrudieren Sie das Rechteck um 0,5 Zoll. Da einige Teile des Rechtecks innerhalb des inneren Kreises liegen, schneiden Sie den inneren Kreis aus, um ihn zu löschen. Skizzieren Sie als Nächstes von der oberen Ebene des Teils eine Mittellinie vom Kreis zum äußeren Teil der extrudierten Kante. Skizzieren Sie von diesem Mittelpunkt auf der extrudierten Kante ein Rechteck, das 0,2 Zoll zu beiden Seiten reicht. Extrudieren Sie dieses kleine Rechteck um 0,5 Zoll. Erstellen Sie eine nach vorne gerichtete Referenzebene durch die Mitte des Teils und verwenden Sie die Spiegelfunktion, um ein identisches extrudiertes Rechteck auf der anderen Seite des Kreises zu erstellen.
Beim 3D-Drucken von Teilen ist es immer eine gute Idee, alles leicht zu skalieren, um Störungen beim Platzieren des Teils auf der Baugruppe zu vermeiden. In diesem Fall wurde das gesamte Teil um 1,05 hochskaliert. Skizzieren Sie schließlich zwei Kreise mit einem Durchmesser von 1/4 Zoll, die sich auf der Vorderseite der Mitte des Teils befinden, mit einem auf dem kleinen Rechteck und einem auf der Seite des Kreises. Stellen Sie sicher, dass die beiden Kreise vertikal miteinander verbunden sind, und schneiden Sie sie dann durch das gesamte Teil, sodass insgesamt vier Kreise ausgeschnitten werden. Dies wären Löcher, für die die Schrauben platziert werden können, um das PVC mit dem Hauptkörper des Getriebegehäuses zu verbinden.
Schritt 10: Beginnen Sie mit der Montage auf SolidWorks
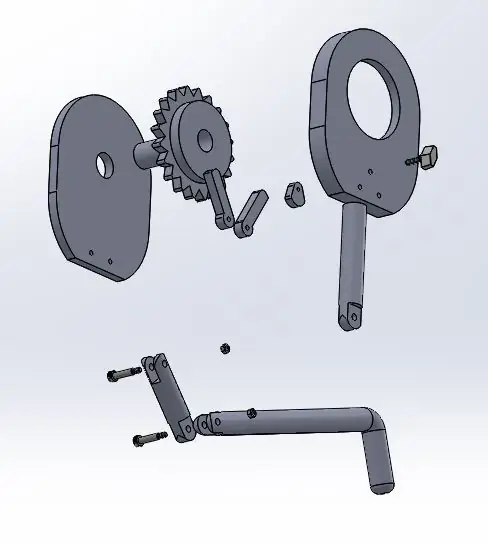
Fügen Sie zunächst alle Teile, die in den vorherigen Schritten erstellt wurden, zusammen mit dem handelsüblichen Außenknauf, Schrauben und Muttern ein, wodurch der Rollstuhlkörper zum Basisbauteil wird.
Beginnen Sie mit der Paarung des Körpers und des Zahnrads, indem Sie auf die Kante des Zahnrads und die Kante des Körpers klicken und eine konzentrische Verbindung verwenden. Klicken Sie dann auf die Fläche des Zahnrads und des Körpers, um eine übereinstimmende Verknüpfung zu erstellen.
Verbinden Sie dann den Körper und den Richtungsknopf, indem Sie auf die Fläche des Richtungsknopfs und des Körpers klicken, um eine deckungsgleiche Verknüpfung herzustellen.
Verbinden Sie nun den Außenknauf und den Rollstuhlkörper, indem Sie sowohl auf die Fläche des Außenknaufs als auch auf den Körper klicken, um eine deckungsgleiche Verbindung zu erzeugen.
Erstellen Sie eine konzentrische Verknüpfung, indem Sie auf die Fläche des Körpers und die Fläche des äußeren Knopfs klicken.
Stellen Sie dann eine konzentrische Verknüpfung her, indem Sie auf die Fläche des Richtungsknopfs und die Kante des Körpers klicken.
Klicken Sie nun auf die Flächen des Körpers und der Sperrklinke, um eine übereinstimmende Verknüpfung zu erstellen, und wiederholen Sie den Vorgang für die andere Sperrklinke.
Erstellen Sie eine Tangentenverknüpfung, indem Sie auf die Fläche des Richtungsknopfs und der Sperrklinke klicken und wiederholen Sie den Vorgang für die andere Sperrklinke.
Erstellen Sie als Nächstes eine deckungsgleiche Verknüpfung, indem Sie auf die Fläche des Körpers und des äußeren Gehäuses klicken, und stellen Sie eine konzentrische Verknüpfung her, indem Sie auf die Fläche des Körpers und die Kante des äußeren Gehäuses klicken. Dann machen Sie das Gesicht des Körpers und das Gesicht des äußeren Gehäuses parallel.
Erstellen Sie einen Grenzwinkel mit einem Höchstwert von 78 Grad und einem Mindestwert von 35 Grad für die Vorderseite des Körpers und die Vorderseite der Sperrklinke und wiederholen Sie den Vorgang für die andere Sperrklinke
Verbinden Sie anschließend das Gelenk und den Körper, indem Sie auf die Fläche beider klicken, um eine konzentrische Verknüpfung zu erstellen. Erstellen Sie dann eine zentrierte Breitenverknüpfung für beide Flächen der Verbindung und des Körpers.
Erstellen Sie dann eine konzentrische Verknüpfung für die Kante des Hebelarms und die Kante des Gelenks. Erstellen Sie eine weitere zentrierte Breitenverknüpfung für beide Flächen des Gelenks und des Hebelarms.
Stellen Sie eine weitere konzentrische Verbindung für die Fläche des Gelenks und die Schraube her. Erstellen Sie dann eine Tangentenverknüpfung, indem Sie auf die Fläche der Verbindung und die Fläche der Schraube klicken.
Skizzieren Sie auf der rechten Ebene zwei Achsenlinien für die zukünftige Paarungsreferenz, wobei die erste Linie dort ist, wo der Körper auf das Gelenk trifft, und die zweite, wo das Gelenk auf den Hebelarm trifft.
Erstellen Sie als Nächstes eine konzentrische Verknüpfung, indem Sie auf die Fläche des Hebelarms und die zweite Schraube klicken. Erstellen Sie nach der Verknüpfung eine weitere tangentiale Verknüpfung mit beiden Flächen beider Komponenten.
Verbinden Sie mit der zuvor gezeichneten ersten Achse die Kante der ersten Mutter und die Achse, um eine konzentrische Verbindung zu erstellen.
Verwenden Sie eine übereinstimmende Verbindung für die Stirnseite der ersten Schraube und der ersten Mutter und wiederholen Sie den Vorgang für die zweite Schraube und Mutter.
Machen Sie eine konzentrische Verbindung mit der Kante der zweiten Mutter und der zweiten Achse.
Erstellen Sie eine weitere konzentrische Verknüpfung mit der Fläche des Körpers und der Außenfläche der ersten Schraube. Machen Sie außerdem für diese Teile eine zufällige Verknüpfung.
Stellen Sie eine konzentrische Verbindung für die Fläche der Sperrklinke und die Außenfläche der dritten Schraube her.
Erstellen Sie eine deckungsgleiche Verknüpfung mit der Fläche des Körpers und der Außenfläche der dritten Schraube.
Erstellen Sie als Nächstes eine weitere konzentrische Verknüpfung, indem Sie auf die Fläche des Außengehäuses und die Außenfläche der dritten Schraube klicken und sie zur Deckung bringen.
Bilden Sie eine konzentrische Verknüpfung, indem Sie auf die Vorderseite des Körpers und die Vorderseite der Sperrklinke klicken und sie zur Deckung bringen. Wiederholen Sie dies für die andere Sperrklinke.
Stellen Sie eine konzentrische Verknüpfung her, indem Sie auf die Fläche des Richtungsknopfs und des äußeren Knopfs klicken.
Verbinden Sie schließlich die Fläche des Körpers und die Kante des Richtungsknopfs, um eine konzentrische Verknüpfung zu erstellen.
Schritt 11: Bestellen Sie Teile von McMaster-Carr
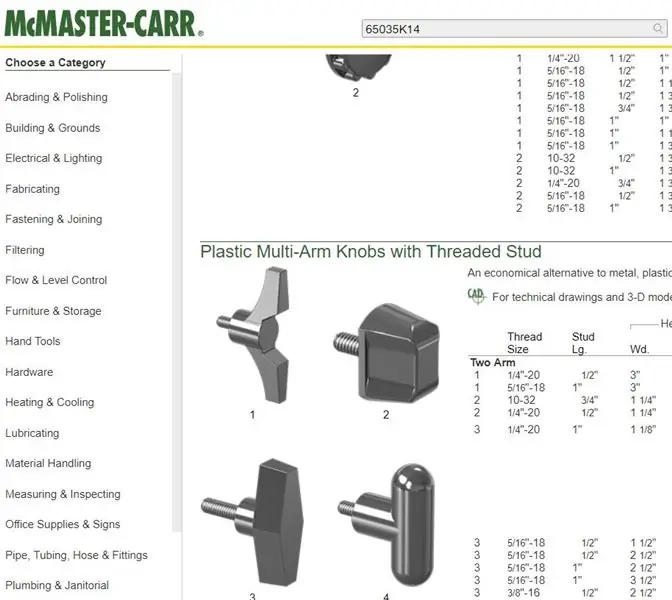
Bestellen Sie bei McMaster-Carr den zweiarmigen Kunststoffknauf (Außenknauf), die Bundschraube aus legiertem Stahl, die Sechskantmuttern aus Stahl und die Kabelbinder. Die Artikelnummern lauten 65035K14, 92981A205, 90592A016 bzw. 70215K61.
Schritt 12: Teile aus dem Baumarkt beziehen
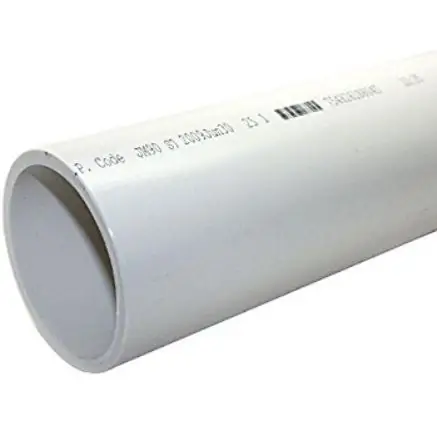
Besorgen Sie sich in einem lokalen Baumarkt Folgendes:
-18 "x 24" x.220" Acrylglasplatte
- Klarer Kleber (E6000 Kleber)
- 1 PVC-Steckkappe (2)
- 1 x 10' PVC-Rohr mit glattem Ende
- 1 PVC-90-Grad-Winkel (2)
Schritt 13: Herstellung der Teile
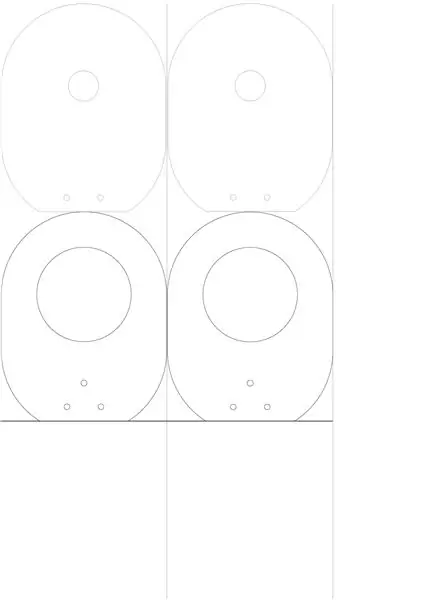
3D-gedruckte Teile: Bereiten Sie die SolidWorks-Teile vor und konvertieren Sie sie in STL-Dateien. Von dort aus legen Sie die Teile in die Makerware-Software und legen die zu druckenden Teile (Karosserieschale, Zahnräder, Montageteil, Sperrklinken, Richtungsknopf, Armlehneneinkerbungen*) aus. Wenn die Teile nicht auf das Bett des Druckers passen, warten Sie mit dem erneuten Drucken. Achten Sie beim Drucken darauf, Stützen und Flöße hinzuzufügen, um zu verhindern, dass die Drucke fehlschlagen.
Lasergeschnittene Teile: Mit dem 18" x 24" Acryl können die Vorder- und Rückplatten des Außengehäuses des Körpers hergestellt werden. Dazu nehmen Sie die Vorderseite beider Platten in SolidWorks und speichern sie beide als DWG-Datei. Diese können dann in die Laserschneidsoftware (in diesem Fall Epilog) hochgeladen werden, in der ihre Ausrichtung wie im Bild gezeigt eingestellt werden kann. Jeweils zwei werden aus dem Acryl ausgeschnitten und aus dem restlichen Material werden zwei Rechtecke geschnitten. Die Rechtecke dienen als Armlehnen.
Handgeschnittene Teile: Nehmen Sie die Rohre und schneiden Sie sie in die verschiedenen Längen (zwei 4,5 Zoll für den Griff, zwei von 4,5 Zoll für das Gelenk, zwei von 6,5 Zoll für den Hebel und zwei von 13,25 Zoll für den Arm). Von dort aus schneiden Sie die 13,25-Zoll-Armstücke an einem Ende (30 oder 35 mm) in der Mitte der anderen Seite des Rohres und bohren ein 1/4 Loch 15 mm von den Kanten des Rohres. Schneiden und bohren Sie zwei der 4,5-Zoll-Verbindungsstücke auf die gleiche Weise, aber auf beiden Seiten des gemeinsamen PVC-Rohrs. Machen Sie dasselbe (schneiden und bohren) Sie auf der einen Seite des Hebelarms, 6,5-Zoll-Rohr.
*Einrückungen der Armlehne oder die gesamte Armlehne aus dem vorherigen Schritt können verwendet werden.
Schritt 14: Setzen Sie alle Teile zusammen
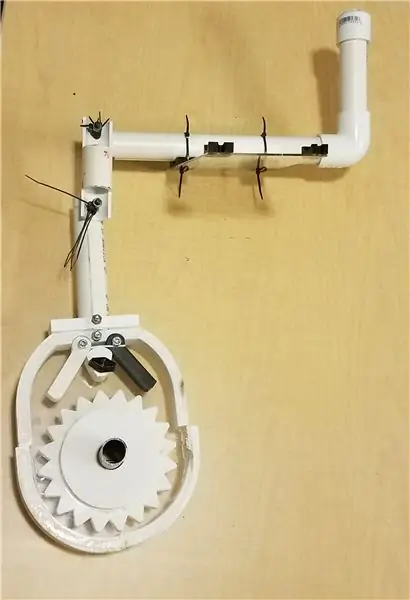
Aufbau des Körpers:
Nehmen Sie die lasergeschnittenen äußeren Körperteile und die 3D-gedruckten Schalenteile. Nehmen Sie eine Seite der Außenhülle und kleben Sie die Schalenteile entsprechend an die Kanten der Hülle. Nehmen Sie anschließend ein Gummiband und wickeln Sie es um die beiden Sperrklinken. Setzen Sie die Sperrklinken an ihren jeweiligen Stellen ein und verwenden Sie den Teilgewindebolzen und führen Sie ihn durch das Loch des Körpers und der Sperrklinken. Danach nehmen Sie den Richtungsknopf und den Kunststoffknopf. Stecken Sie den Plastikknopf durch das Außengehäuse und drehen Sie die beiden zusammen mit dem Außengehäuse dazwischen. Zum Schluss das Zahnrad in das entsprechende Loch stecken und den oberen Deckel des Außengehäuses auf das Zahnrad setzen und die Schale auf das obere Außengehäuse kleben. Lassen Sie es sitzen und trocknen. Denken Sie daran, auch die beiden Teilgewindebolzen mit den Sechskantmuttern zu sichern, nachdem Sie den oberen Deckel auf die Schale aufgesetzt und verklebt haben.
Nehmen Sie das 6,5-Zoll-Hebel-PVC-Rohr und kleben Sie es auf die Unterseite des Körpers. Von dort aus ruhen und trocknen lassen. Nehmen Sie das montierte Teil und schieben Sie es durch das Rohr, bis es flach auf der Unterseite des Körpers liegt. Nehmen Sie einen 1/4-Zoll-Bohrer und bohren Sie die Löcher in das Rohr und durch den Körper an den entsprechenden Stellen. Sichern Sie die Schrauben mit einer Sechskantmutter.
Zusammenbau der Armlehne:
Bei der Armlehne einfach die Einkerbungen auf die 4 Ecken der Armlehne setzen und kleben. Bohren Sie dann zwei Löcher (5/32'' Löcher) auf jeder Seite der Einkerbungen und legen Sie Kabelbinder durch sie. Die größeren Einkerbungen können dann mit dem 13-Zoll-PVC-Rohr des Hebelarms ausgerichtet und mit diesem verbunden werden. Die kleinere Einkerbung sollte vor dem Gebrauch ausgerichtet und später am Arm des Rollstuhls befestigt werden.
Zusammenbau des Hebelarms:
Setzen Sie die Kappe auf das 4,5-Zoll-Griffrohr und platzieren Sie das Winkelstück sicher auf der anderen Seite. Platzieren Sie mit der anderen Öffnung des Kniestücks das 13-Zoll-Armrohr und verbinden Sie es mit einer Schulterschraube mit einer Seite des Gelenks (4,5-Zoll-Rohr). Auf der anderen Seite des Gelenks eine weitere Schulterschraube nehmen und mit dem (6,5-Zoll-Rohr) Hebelarmstück verbinden. Nehmen Sie eine Sechskantmutter und sichern Sie die Schulterschraube. Da die Ansatzschrauben teilweise mit Gewinde versehen sind, können die Gelenke, in denen sie befestigt sind, dünn sein. Um die Verbindungen fester und sicherer zu machen, legen Sie etwa fünf Kabelbinder um jede Schulterschraube, um jede Verbindung festzuziehen.
Schritt 15: Iteratives Testen
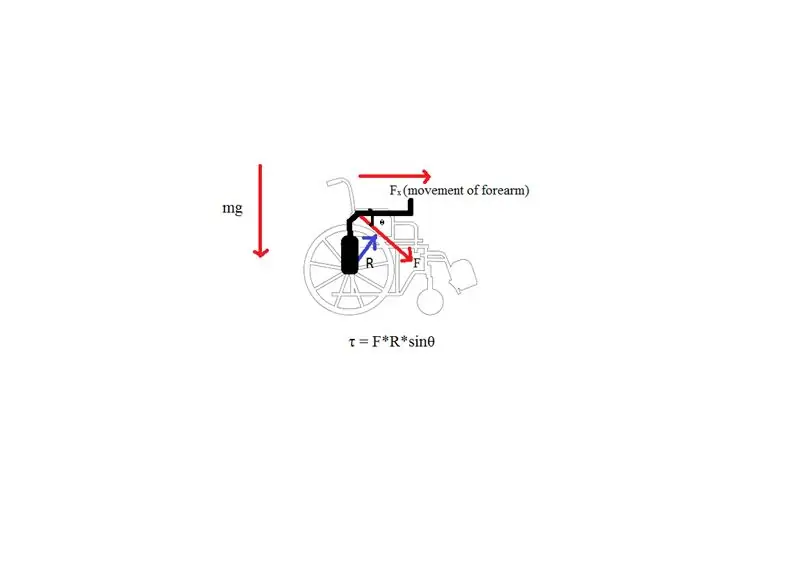
Stellen Sie zum Testen sicher, dass Sie Zugang zu einem der Rollstühle haben.
Befestigen Sie den Hebelarm am Rad. Stellen Sie sicher, dass die Teile dort passen, wo sie hin sollen, und stellen Sie sicher, dass bestimmte Teile parallel zu den entsprechenden Teilen des Rollstuhls sind, wie z. B. die Armlehne. Stellen Sie sicher, dass die in das Aluminiumrohr gebohrten Löcher und der Körper des Hebelarms ausgerichtet sind. Wenn die Teile unverhältnismäßig sind, gehen Sie zurück und nehmen Sie einige Maßänderungen vor.
Wenn alle Maße und Verhältnisse stimmen, lassen Sie einen Tester auf dem Rollstuhl sitzen und den Hebelarm benutzen. Wie auf dem Freikörperdiagramm gezeigt, drückt der Tester horizontal nach vorne, um eine diagonale Kraft zu erzeugen, die verwendet wird, um ein Drehmoment zu erzeugen und den Rollstuhl vorwärts zu bewegen. Analysieren Sie alle Probleme: Schwachheit der Verbindung, übermäßiger oder fehlender horizontaler Platz, Bruch von Teilen usw.
Probleme analysieren und neu gestalten.
In unserem Prototyp bewegte sich der Rollstuhl, aber in einem langsamen Tempo. Da das Karosserieteil nicht rechtzeitig fertig verklebt wurde, brach der Hebelarm bei unserem Testlauf. Außerdem war das Gelenk möglicherweise zu groß und locker, und es gab möglicherweise nicht genügend horizontalen Raum und Bewegung auf dem Hebelarm, was beides die pro Stoß ausgeübte Kraft einschränkte.
Schritt 16: Beitragsseite
Individuelle Beiträge für das Support-System
Projektleiterin: Sophia Ynami 12732132
- Die Projektleiterin Sophia Ynami war dafür verantwortlich, dass jedes Mitglied der Gruppe für seine jeweiligen Aufgaben verantwortlich war und alle Aufgaben fristgerecht erledigt wurden. Ich habe bei der Endmontage mitgeholfen sowie das Gerät vor dem Endlauf getestet und angepasst.
Hersteller: Yvonne Szeto 94326050
- Der Hersteller, Yvonne Szeto, war für die montagefertige Bereitstellung der verschiedenen Komponenten verantwortlich. Ich war dafür verantwortlich, die Rohmaterialien lasergeschnitten, gebohrt und verschiedene Teile im 3D-Drucker zu drucken. Ich habe auch die verschiedenen Komponenten zusammengebaut.
Materialingenieur: Willis Lao 15649487
- Der Materialingenieur Willis Lao war verantwortlich für die Entscheidung, welche Materialien für jede Komponente des Projekts verwendet werden sollten, und diese bei McMaster Carr/Home Depot zu bestellen/auszusuchen. Ich habe auch zu den Instructables beigetragen, indem ich die Einführung, die Kostenanalyse, den schrittweisen Prozess der Erstellung von Teilen und die Baugruppe geschrieben habe.
Tester: Matthew Maravilla 25352925
- Der Tester, Matthew Maravilla, war für die Überwachung und Analyse der iterativen Testmethode verantwortlich, einschließlich der Prüfung des Hebelarms und der Meldung von Maß- oder Teileänderungen, die angepasst werden müssen. Ich war auch für die Gliederung und die Mehrheit der Instructables verantwortlich.
Hauptdesigner: Anthony Cheuk 30511803
- Der leitende Designer, Anthony Cheuk, war verantwortlich für die Entwicklung eines machbaren Designs unter Berücksichtigung der verschiedenen Materialien, die verwendet werden konnten, und die Vorbereitung der Dateien und des Designs für die Herstellung (3D-Druck und Laserschneiden).