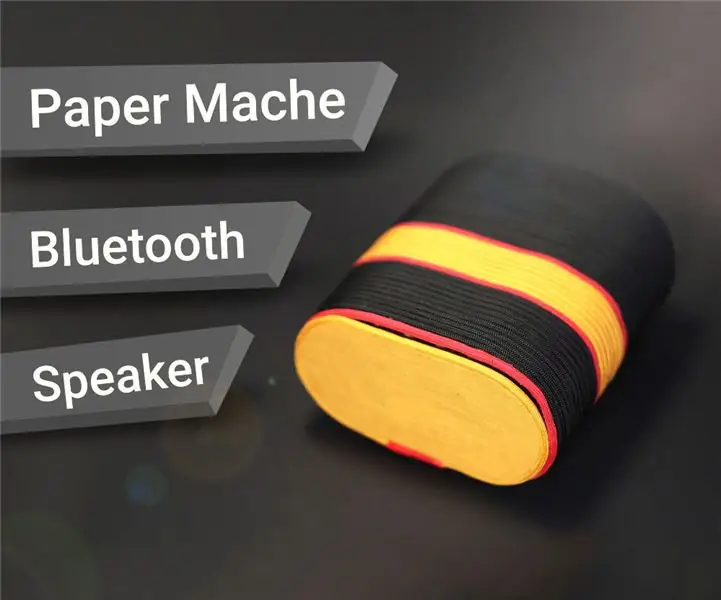
Inhaltsverzeichnis:
- Schritt 1: Design-, Material- und Werkzeugauswahl
- Schritt 2: Materialien
- Schritt 3: Werkzeuge
- Schritt 4: Elektronische Komponenten
- Schritt 5: Schablonen drucken
- Schritt 6: Schablonen auf Hartfaserplatten anwenden
- Schritt 7: Vorschneiden
- Schritt 8: Vorbereitung der Käppchensäge
- Schritt 9: Äußerer Schnitt
- Schritt 10: Gelenke schneiden
- Schritt 11: Inner Cut
- Schritt 12: Temporäre Montage und Messungen
- Schritt 13: Lautsprecher
- Schritt 14: Bluetooth-Audioboard
- Schritt 15: Stromkreis
- Schritt 16: Ladeschaltung
- Schritt 17: Testen
- Schritt 18: Rahmenmontage
- Schritt 19: Pappmaché-Shell
- Schritt 20: Rückwand
- Schritt 21: Paracord Wrap
- Schritt 22: Frontgrill
- Schritt 23: Fazit
2025 Autor: John Day | [email protected]. Zuletzt bearbeitet: 2025-06-01 06:08
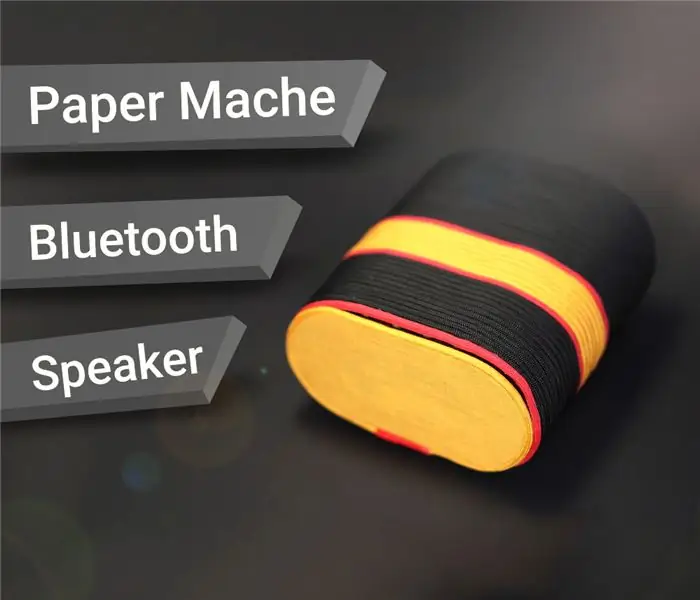
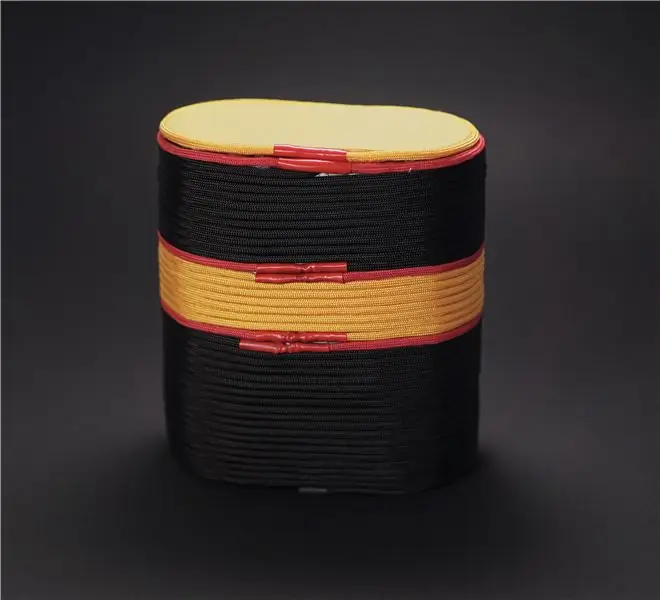
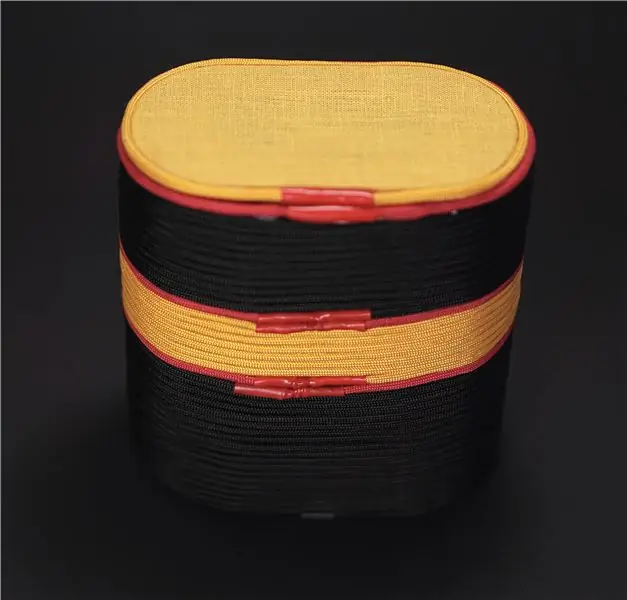
Woher kam diese Idee? Die meisten von uns haben mindestens ein Stück alte, nicht funktionierende Elektronik, die irgendwo im Haus oder Schuppen liegt. Vor kurzem habe ich einen alten, nicht funktionierenden Röhrenfernseher gefunden, die erste Entscheidung ist einfach, dieses Stück Geschichte einfach wegzuwerfen, aber warte… Es macht mir immer Spaß, Elektronik zu zerlegen und dieser alte Röhrenfernseher ist keine Ausnahme, er hat viele kleine unnötige und unbekannte Teile, aber ein Teil ist mir bekannt und das ist Lautsprecher. Die erste Entscheidung ist, diesen sehr nützlichen Teil zu speichern. Und nun hat dieser Lautsprecher einen neuen Platz für neues Leben gefunden.
Wie viel?
- Zeitaufwand für den eigentlichen Build: etwa eine Woche
- Wartezeit auf die Teile: wenige Wochen
- Kosten: 40 USD
Einige Speks
- Abmessungen (H:B:T): 8,5 cm x 14 cm x 16 cm
- Gewicht: 660g
- Leistung: 3W
- Ladespannung: 8,4-15V
- Arbeitsabstand: 8-10m (offener Raum)
Bitte beachten Sie! Englisch ist nicht meine Muttersprache. Wenn Sie Fehler oder irreführende Formulierungen finden, können Sie mich jederzeit über private Nachrichten oder den Kommentarbereich unten kontaktieren.
Schritt 1: Design-, Material- und Werkzeugauswahl
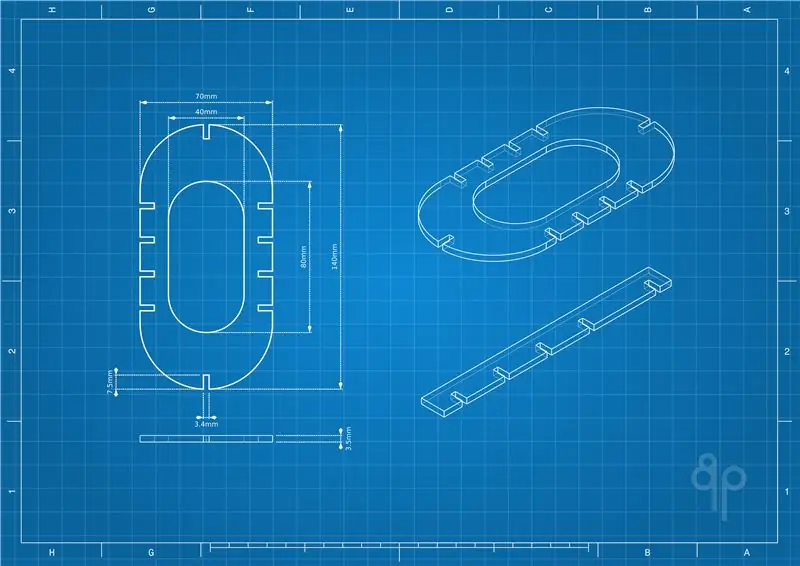
Es gibt keine Grenzen, wenn Sie so etwas wie einen Bluetooth-Lautsprecher bauen, aber wenn Sie Anforderungen stellen, treffen Sie auch auf viele Einschränkungen.
Design Hier gibt es nur wenige Einschränkungen, Volumen für die Hauptkomponenten und Volumen für die richtige Schallübertragung, auch das Gewicht ist sehr wichtig.
Materialien Der Hauptpunkt dieses Aufbaus ist Tragbarkeit und Kosten, Hartholz, Papier und Stoff sind erschwinglich und leicht. Außerdem benötigen Sie kein spezielles Werkzeug, um mit ihnen zu arbeiten.
Werkzeuge
Zweifellos sind CNC- und Laserschneider großartige Werkzeuge, aber es gibt ein kleines Problem, die Zugänglichkeit dieser Werkzeuge ist ziemlich eingeschränkt. Aus diesem Grund habe ich mich dafür entschieden, hauptsächlich Handwerkzeuge zu verwenden, da diese weit verbreitet sind. Wenn Sie jedoch Zugriff auf CNC- oder Laserschneider haben, überspringen Sie einfach viele Schritte und verwenden Sie sie.
Components TPA3110D2 Verstärker für den Einsatz in Fernsehern, Lautsprecher auch aus dem Fernseher, sieht aus wie ein perfektes Paar:)
Schritt 2: Materialien
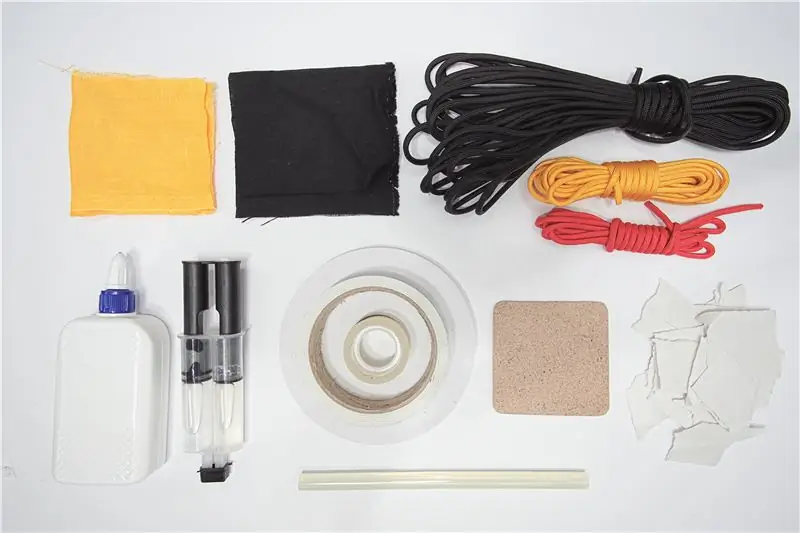
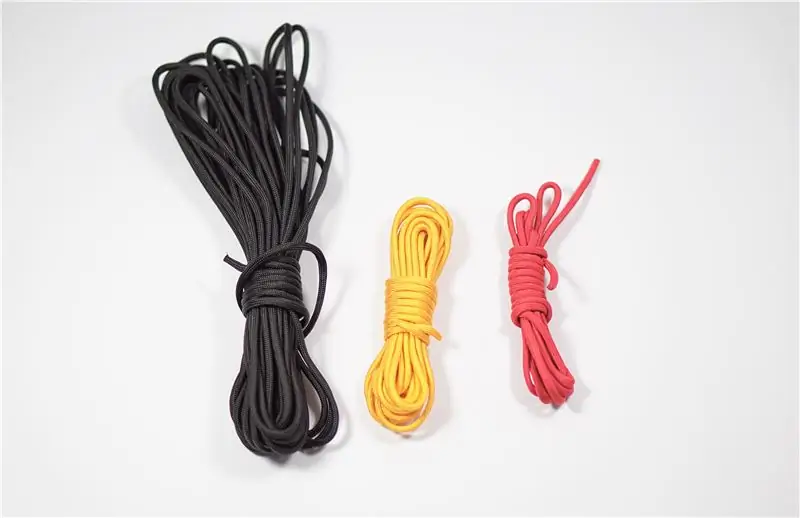
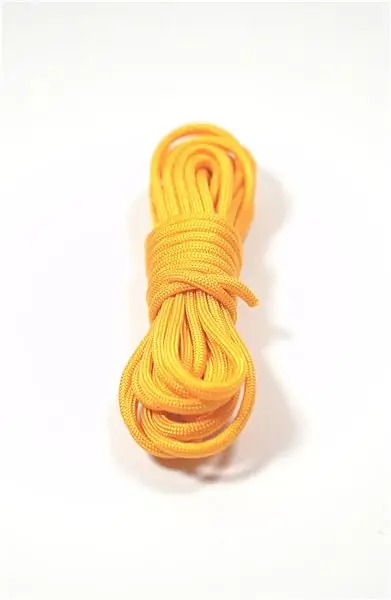
Hartfaserplatte (HDF) Dicke: 3,5 mm Größe: 40 cm x 40 cm
Epoxidkleber20 Gramm reichen aus.
Papier 25 Blatt A4 oder Letter Zeitung
Leinenstoff Stück ca. 30cm x 30cm
PVA Kleber (Holzleim) 250-300ml Flasche
Doppelseitige Haftklebebänder
- Klares 15mm Klebeband
- 20 cm x 10 mm doppelseitiges druckempfindliches Schaumklebeband
- 2m x 24mm doppelseitiges Schaumklebeband
Paracord (550er Schnur)
- Schwarz 4mm, 12m;
- Gelb 4 mm, 3 m;
- Rot 4mm, 1m.
Büropapier 4 Blatt „A4“oder „Letter“Büropapier mit einer Dichte von 80 g/m²
Lötdraht 5gr, 0,3 oder 0,4 mm Lötdraht, mit Flussmittelkern
Plastikfolie Plastikfolie für Lebensmittel
Schritt 3: Werkzeuge
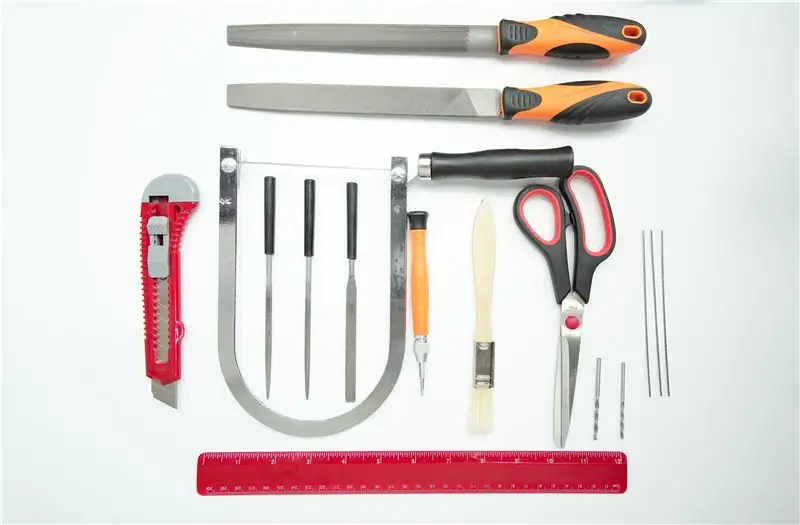
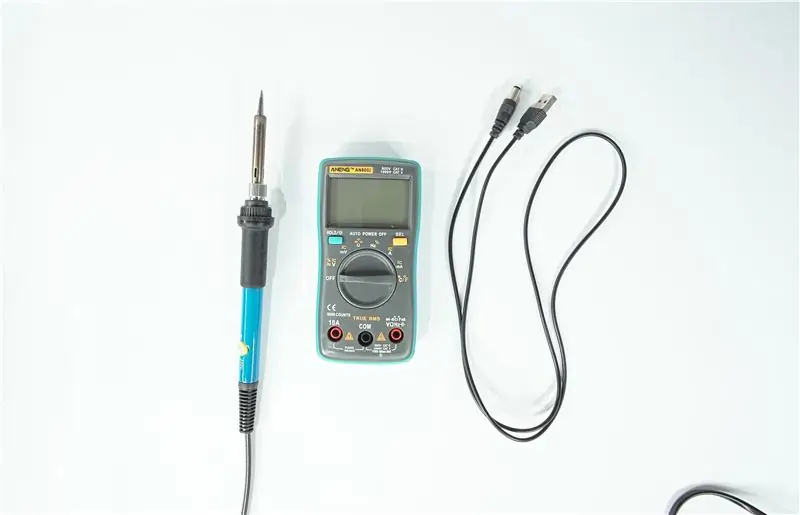
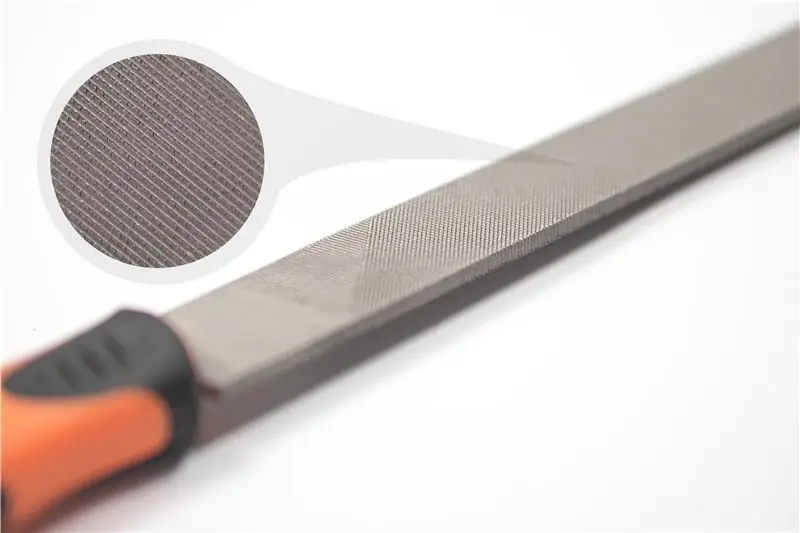
Dies ist eine vollständige Liste der Tools, die in diesem Projekt benötigt und verwendet werden. Viele Werkzeuge sind austauschbar, zum Beispiel ist es möglich, "Dreiquadratfeile" zu verwenden, die Einzel- und Kreuzschnittmuster enthält, ein Kunststofflineal als Blasenentferner usw.
Viele Werkzeuge sollten in Ihren lokalen „Heimwerker“- oder „Baumarkt“-Geschäften erhältlich sein.
Kappsäge Kappsäge mit mindestens 20 cm Arbeitstiefe.
Ersatzsägeblätter Da es sich bei der Kappsäge um ein empfindliches Handwerkzeug handelt, das viele Ersatzsägeblätter benötigt, sollten 50 Stk. ausreichen.
Bohrer Wir brauchen nur wenige Löcher, jeder Bohrer sollte diese Aufgabe erfüllen.
Universalmesser Abbrechklinge (18 mm) oder Messer mit fester Klinge
Heißklebepistole
Satz von Dateien
- 8 Zoll, Single Cut Flachfeile;
- 8 Zoll, Cross Cut Rundfeile;
- 8-Zoll-Querschnitt-Flachdatei;
- Kleine Nadelfeilen eingestellt.
Lineal 30 cm Lineal
Multimeter Jedes Multimeter, das Spannungen anzeigen kann.
Lötkolben Dieses Projekt erfordert ein wenig Löten, jeder für dieses Projekt geeignete Lötkolben, nur eine Empfehlung, Lötspitze sollte etwa 1,6-2,4 mm breit sein.
Schraubstock 60mm Schraubstock wird ausreichen
Schraubendreher Flach für Potentiometer und Kreuz für M3-Schrauben.
Bohrer
- 3,2 mm Holzbohrer
- 7mm Holzbohrer
- 12mm Spatenbohrer
Schüssel 500ml Schüssel.
Malpinsel 15mm synthetischer Malpinsel
Laserdrucker
Schritt 4: Elektronische Komponenten
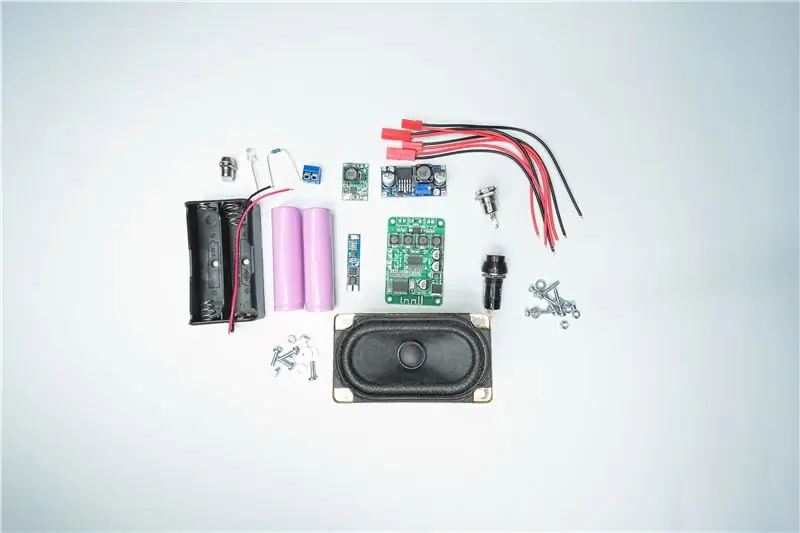
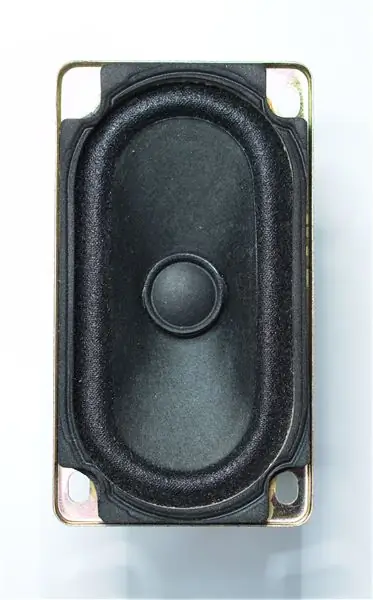
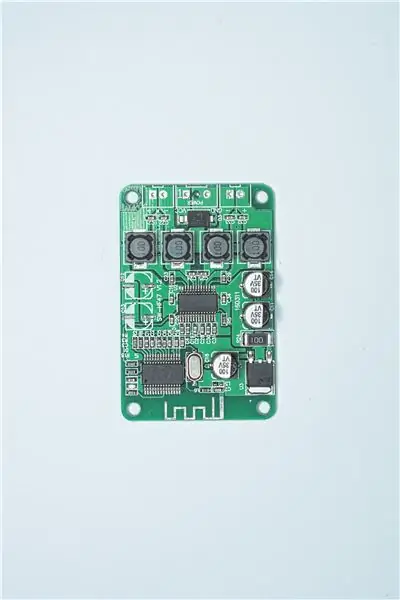
Lautsprecher 3 Watt, 8 Ohm, 4 Zoll Lautsprecher (90X50mm).
Bluetooth Audio Board TPA3110D2 basiertes Bluetooth Audio Board.
Akkus 2x 18650 Li-Pol Akkus
Akkuhalter 2S Akkuhalter für 18650 Li-Pol’s.
Spannungserhöhungsplatine DC-DC-Aufwärtswandler 3,2-35 V, 2 Ampere Spannungserhöhungsplatine.
Ladeplatine Da wir eine 2S-Konfiguration verwenden, erfüllt die TP5100-Ladeplatine unsere Bedürfnisse, dies ist keine perfekte Lösung, mehr dazu unten.
Batterieschutzplatine 2S Li-Ion BMS
Schrauben, Muttern und Unterlegscheiben
- 10x M3 oder M2.5, 20mm Schrauben;
- 10x M3 oder M2.5 Unterlegscheiben;
- 10x M3 oder M2,5 Muttern.
Magnete 4x (10 mm Durchmesser, 3 mm Höhe) Neodym-Magnete.
Drähte 5 Paar Drähte mit JST-Anschlüssen
Ladebuchse 5,5 x 2,1 mm DC Barrel-Buchse.
LED-Anzeigen Rot und Grün 5mm, 2V LEDs.
Halter für LED-Blinker 2x, 5mm Metall-LED-Halter mit Gewinde.
Selbstsichernder Druckknopf 2 Pin, 16mm.
Schrumpfschläuche
- 5 mm mind. 20 cm Schlauch für Paracord
- Set aus unterschiedlich großen Tuben
Schritt 5: Schablonen drucken
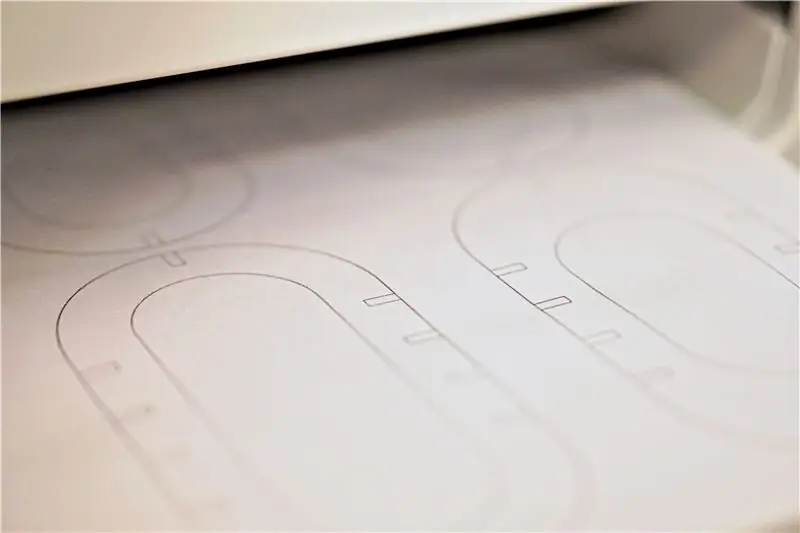
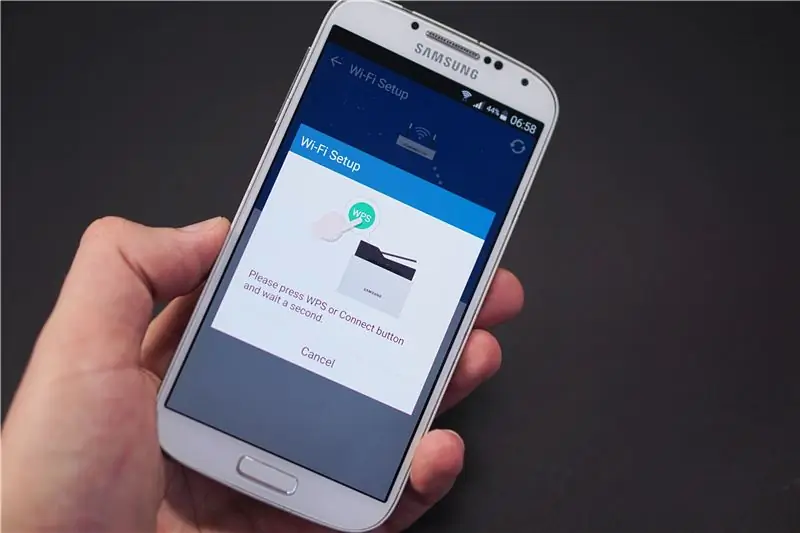
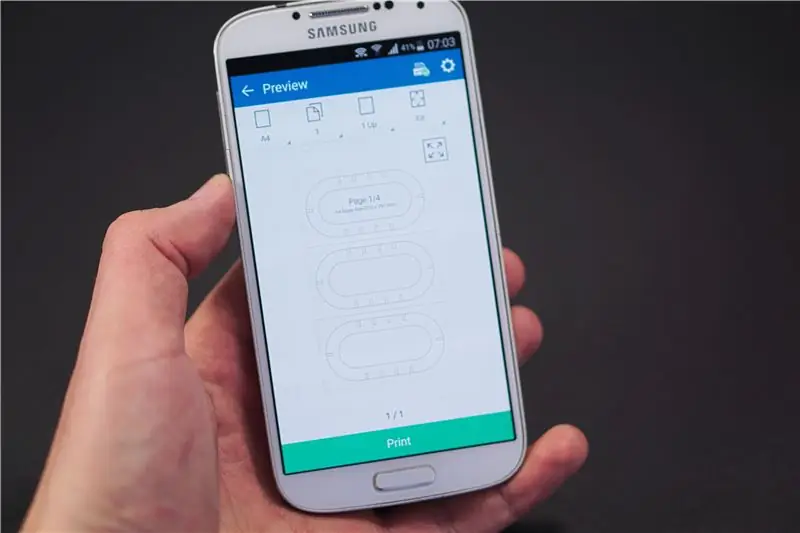
Es ist bereits ein komplettes Design, aber Sie können die Größe immer nach Ihren Wünschen korrigieren.
Zeichnungen zum Drucken angehängt für zwei Papierformate „Letter“und „A4“, Grund für diese Schablonengröße ist ein Seitenverhältnis von 1:1. Sie können einfach das gesamte Dokument ohne Änderungen drucken. Es ist möglich, mit einem kompatiblen Drucker direkt vom Telefon aus zu drucken.
Notiz! Einige Drucker unterstützen das Drucken ohne Ränder nicht und können Bilder skalieren, das passiert mir, keine große Sache, aber in einigen Fällen können Unterschiede erkennbar sein.
Schritt 6: Schablonen auf Hartfaserplatten anwenden
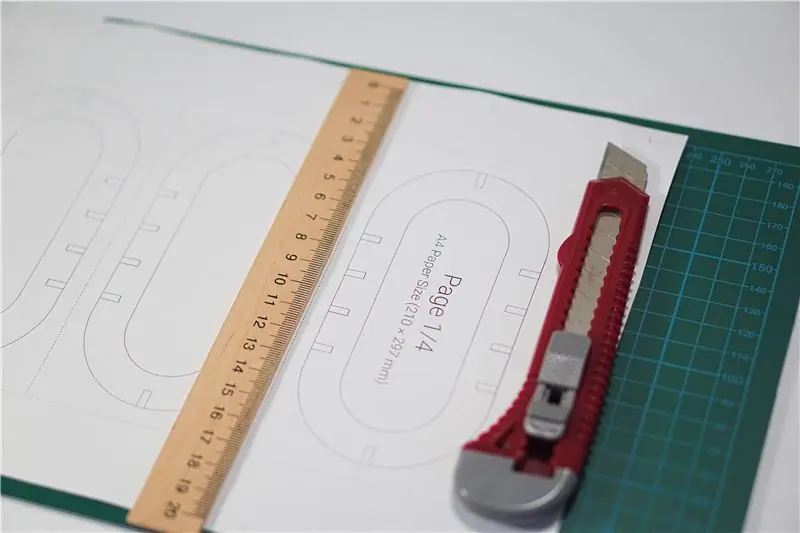
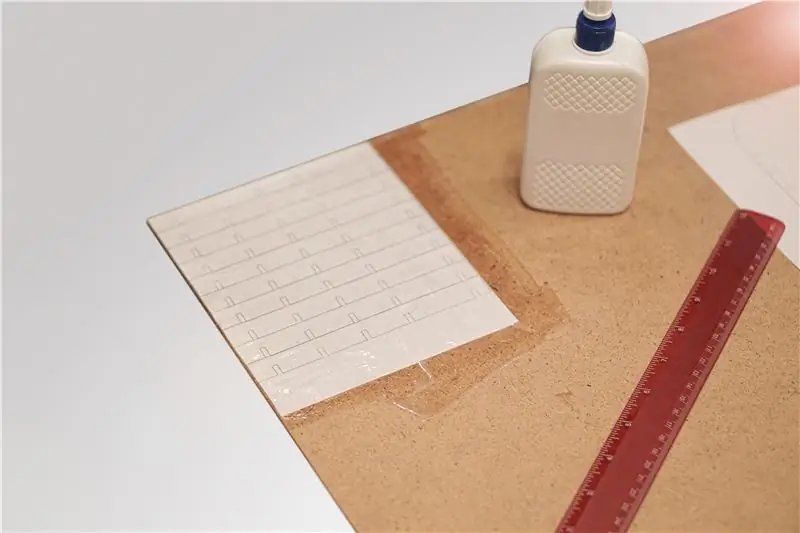
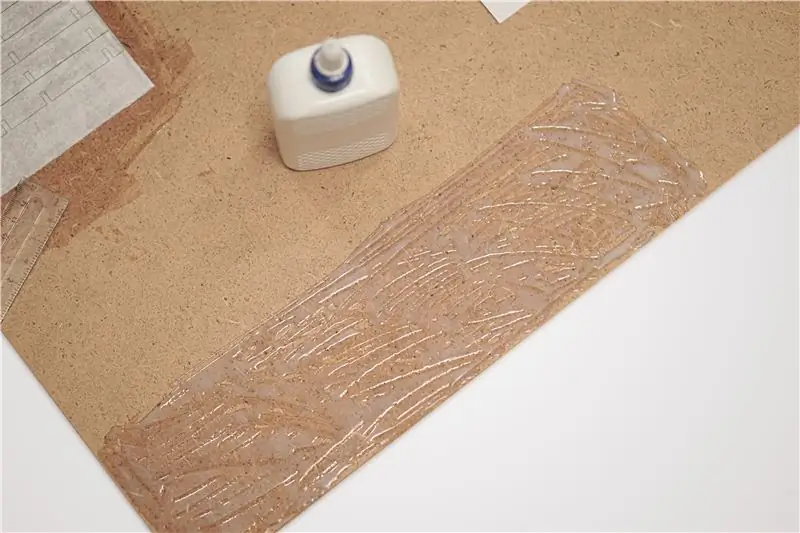
Es gibt viele verschiedene Methoden, um Druckbilder auf das Holz zu übertragen, für dieses Projekt können wir einfach Schablonen auf das Holz kleben, da alle Rahmenteile verdeckt werden.
Dazu benötigen Sie PVA-Kleber. Dünne Leimlinie in Schablonengröße auf die Fläche auftragen, Kleber mit Kunststofflineal glatt streichen. Sie sollten eine dünne Leimschicht auftragen, sie kann uneben sein, der Hauptpunkt ist, dass die Fläche vollständig mit Leim bedeckt ist. Da PVA-Kleber sehr langsam trocknet, können wir die Schablone ganz einfach an die richtige Stelle verschieben, aber versuchen Sie nicht, die Schablonen nach 15-20 Minuten zu verschieben. Wenn alle Schablonen fertig sind, lassen Sie sie mindestens 10 Stunden trocknen (dies ist für ideale Trocknungsbedingungen), empfohlene Trocknungszeit 24 Stunden.
Notiz! PVA Glue ist wasserbasiert, d.h. Inkjet-gedruckte Linien können sich beim Kleben auflösen. Es ist besser, einen Laserdrucker zu verwenden oder, falls dies nicht möglich ist, eine sehr dünne Klebstoffschicht aufzutragen.
Schritt 7: Vorschneiden
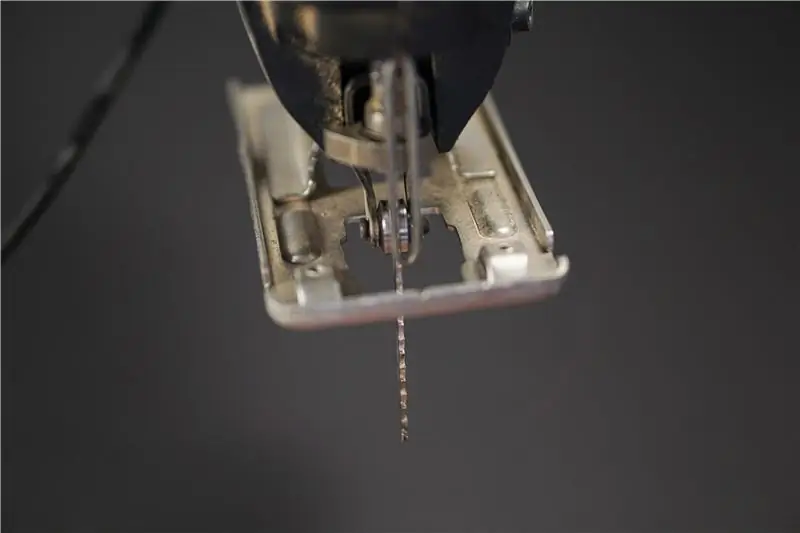
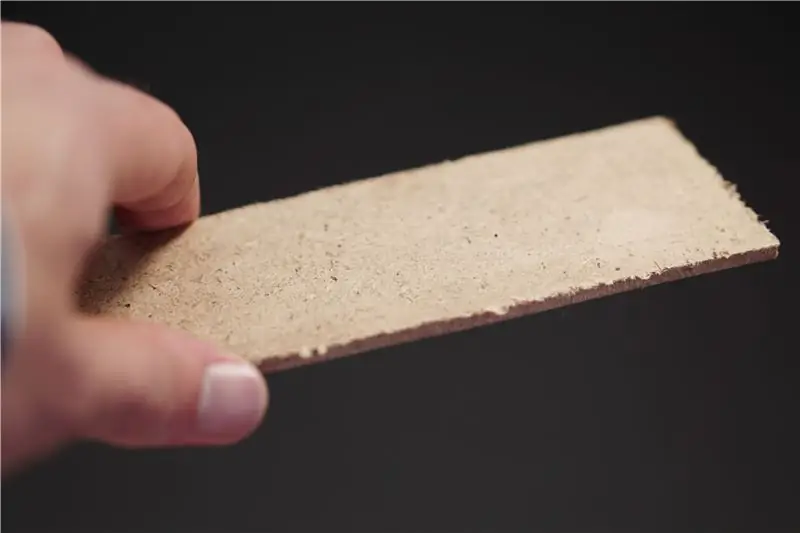
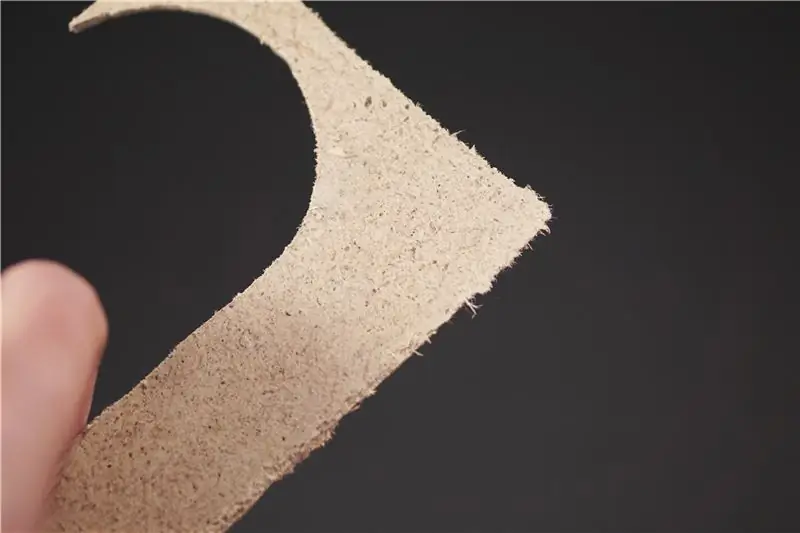
Dieser Schritt hat seinen Grund. Da die Kappsäge eine begrenzte Arbeitstiefe hat, ist es ziemlich unbequem, auch nur die Hälfte ihres Potenzials zu nutzen.
Dazu können wir Jig Saw verwenden, das spart viel Zeit, wenn Sie keine haben, können Sie „Hack Saw“verwenden, trotzdem spart es viel Zeit.
Schritt 8: Vorbereitung der Käppchensäge
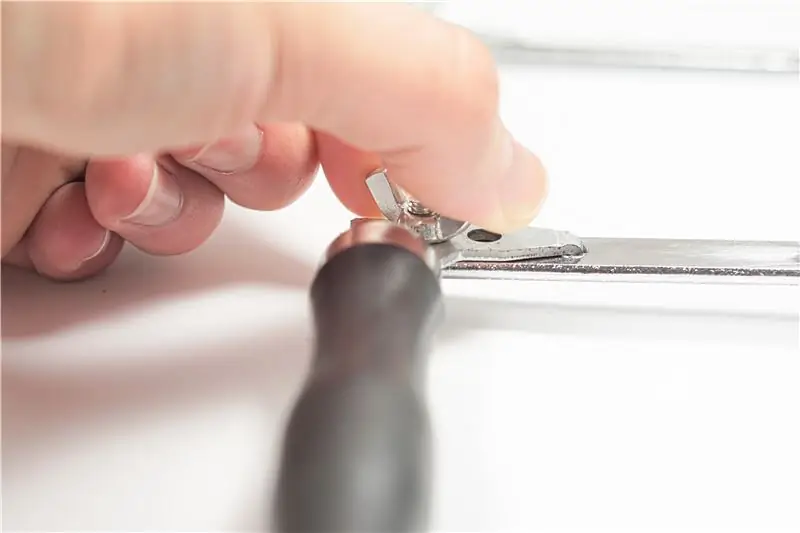
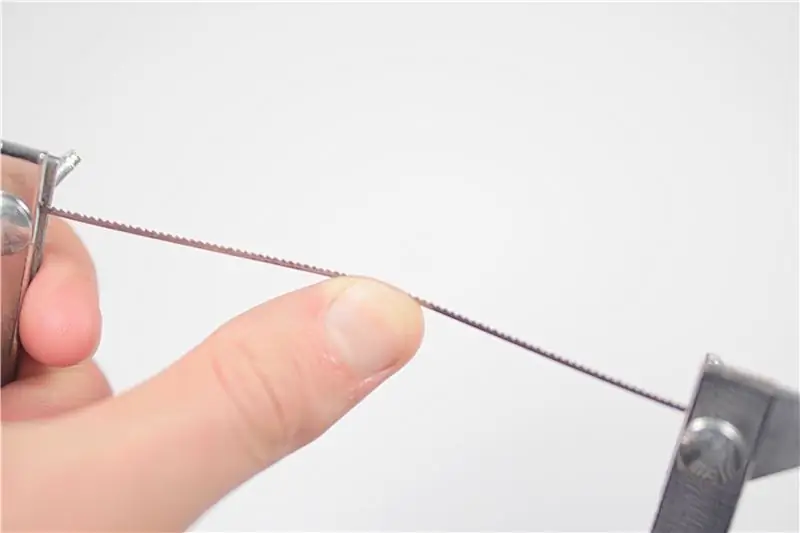
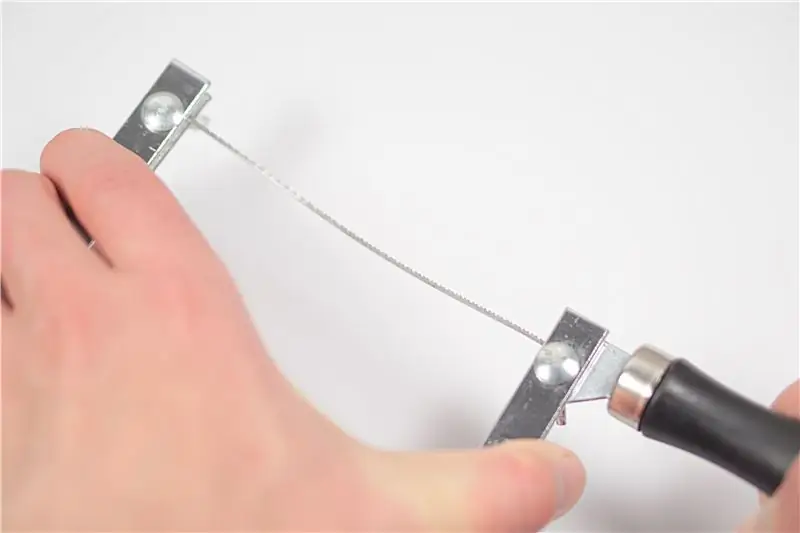
Während der Arbeit an diesem Projekt habe ich festgestellt, dass die Kappsäge recht einfach zu bedienen ist, aber erst nach vielen Stunden damit.
Es gibt einige Tipps, die den Prozess viel einfacher machen:
- Sägeblatt beim Drücken einsetzen;
- Die maximale Spannung des Sägeblatts erleichtert den Schneidvorgang erheblich und schneidet glatter;
- Beeilen Sie sich nicht;
- Machen Sie nach 15 Minuten Arbeit eine Pause, besonders für die Augen.
Schritt 9: Äußerer Schnitt
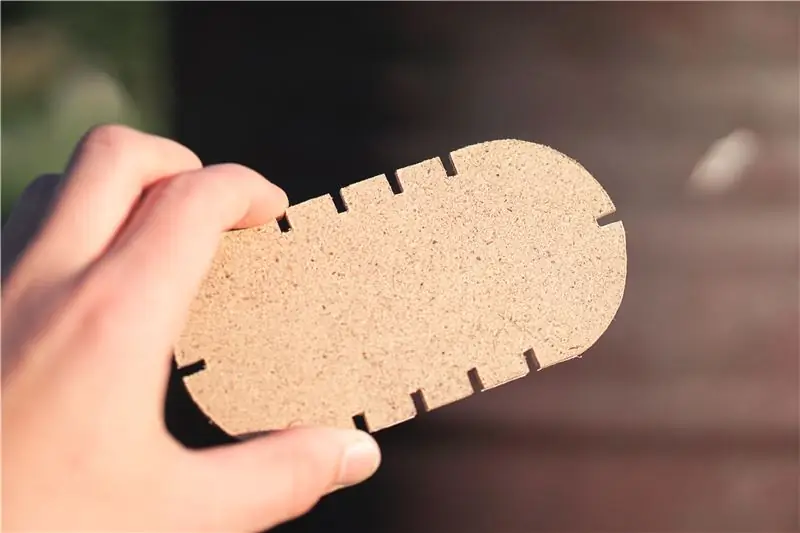
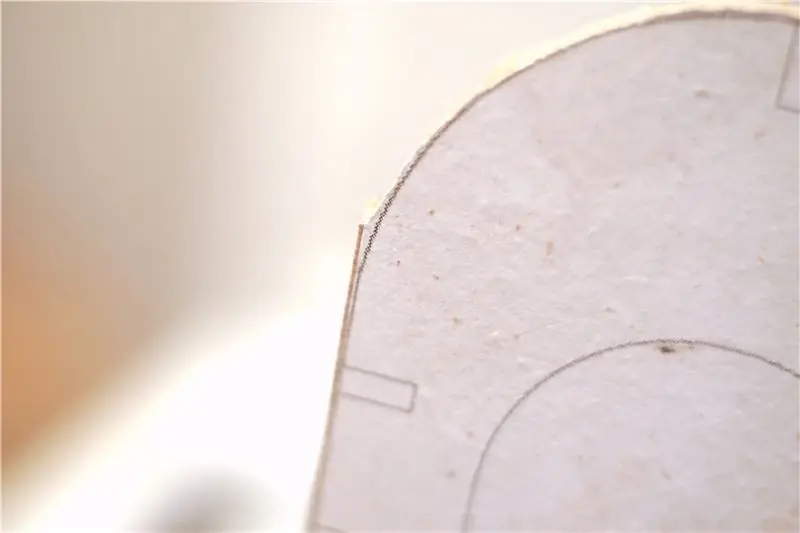
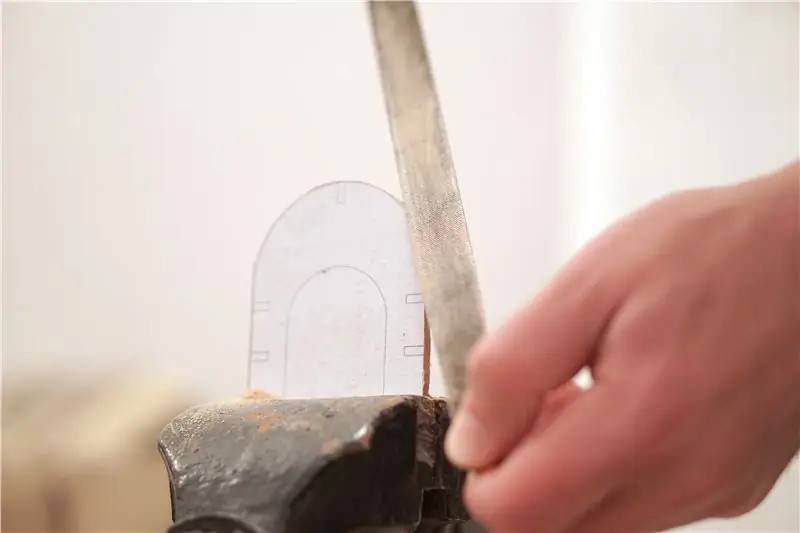
Wenn wir nun unsere RAW-Stücke haben, können wir mit der Hauptschnitte beginnen, indem wir der Schablone folgen.
Dieser Schritt erfordert viel Zeit, beeilen Sie sich nicht und versuchen Sie, die Schnitte so glatt wie möglich zu machen. Haben Sie keine Angst, wenn etwas schief geht, kleine Fehler können später leicht nachpoliert werden.
Schritt 10: Gelenke schneiden
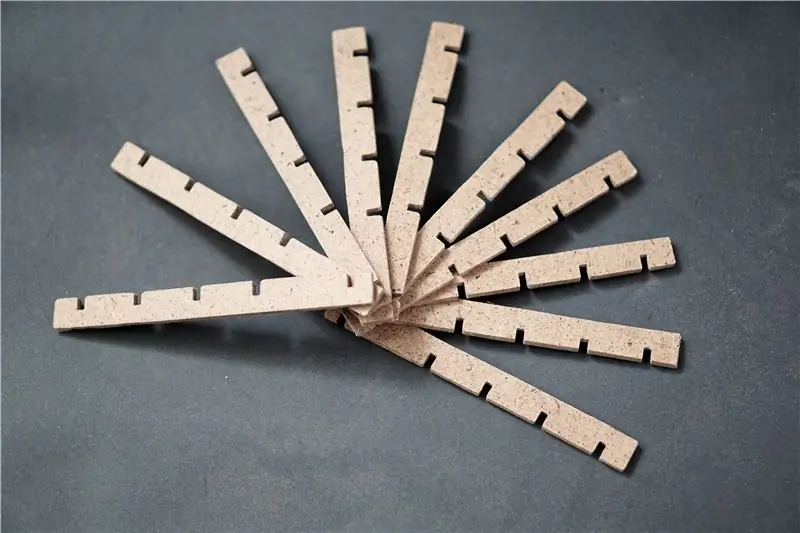
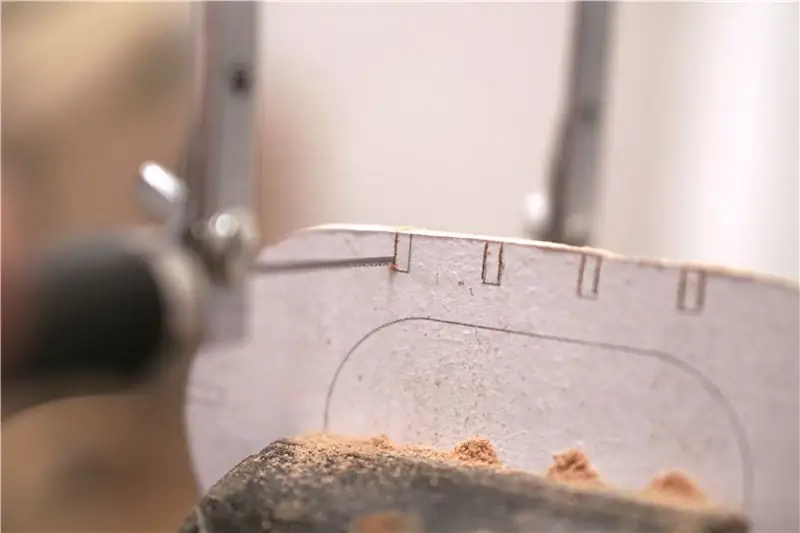
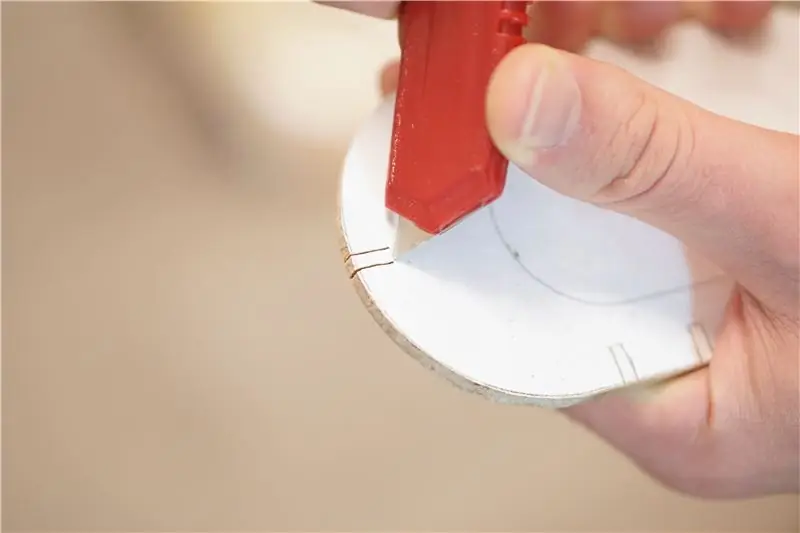
Es gibt keinen Grund, enge Verbindungen herzustellen, es ist besser, die Verbindungen nach der Kappsäge mit Nadelfeilen zu polieren.
Insgesamt gibt es mehr als 80 Verbindungspunkte, es dauert ungefähr 4 Stunden, um alle zu beenden.
Vertikale Linien
Zuerst sollten wir vertikale Linien schneiden, dies ist der einfachste Teil, Sie können diesen Vorgang zuerst für alle Teile durchführen, dies ist effizienter.
Horizontale Linien
Wenn alle Teile fertig sind, nehmen Sie ein Cuttermesser und schneiden Sie horizontale Linien von beiden Seiten leicht vor, danach können wir kleine Stücke leicht brechen und ziehen. Machen Sie sich keine Sorgen über das Abplatzen der Oberfläche, das ist in Ordnung.
Fertigstellung
Da diese Methode alles andere als perfekt ist, sollten die Fugen poliert werden. Dazu benötigen wir eine kleine Flachfeile und eine Vierkantnadelfeile. Mit einer Flachfeile können wir vertikale Seiten glätten, die Unterseite kann mit einer Vierkantnadel poliert werden.
Spitze! Um zu verhindern, dass HDF abplatzt, können wir einfach alle scharfen Winkel glätten.
Notiz! Dieser Schritt sollte durchgeführt werden, bevor Innenschnitte vorgenommen werden, der Grund dafür ist die strukturelle Steifigkeit, nachdem das Innenteil entfernt wurde, ist es schwer, das Teil richtig im Schraubstock zu befestigen und das Strukturteil wird schwächer.
Schritt 11: Inner Cut
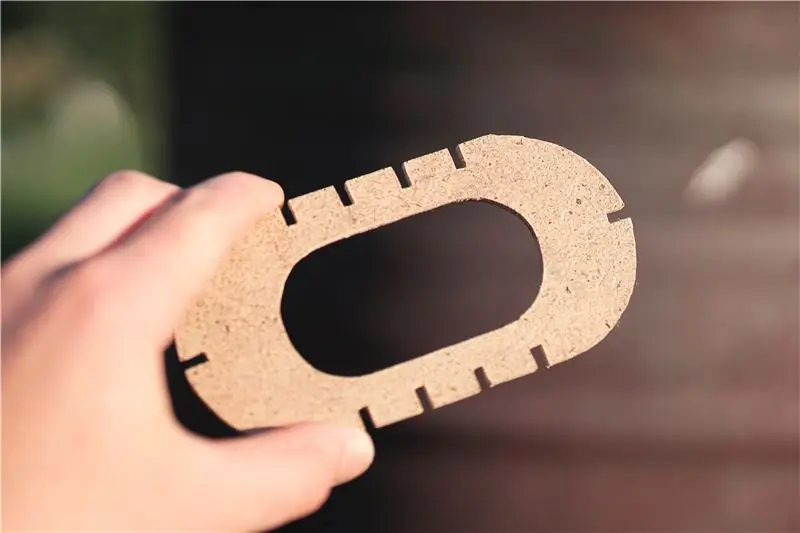
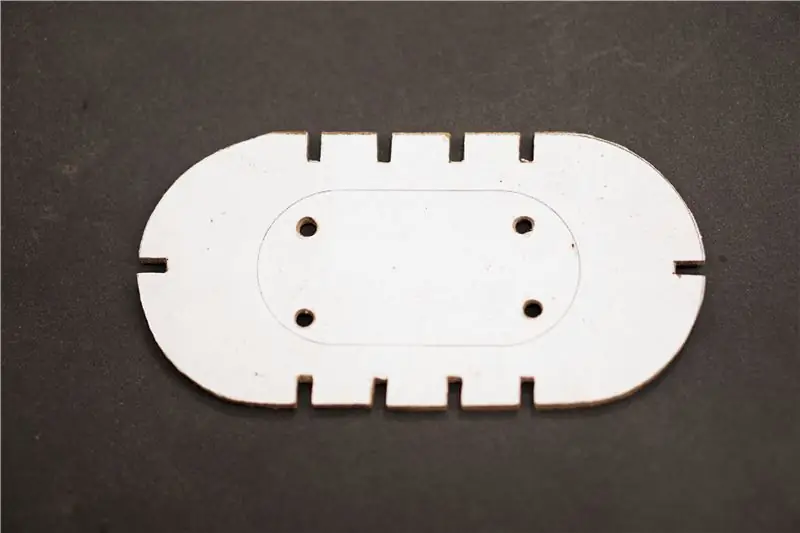
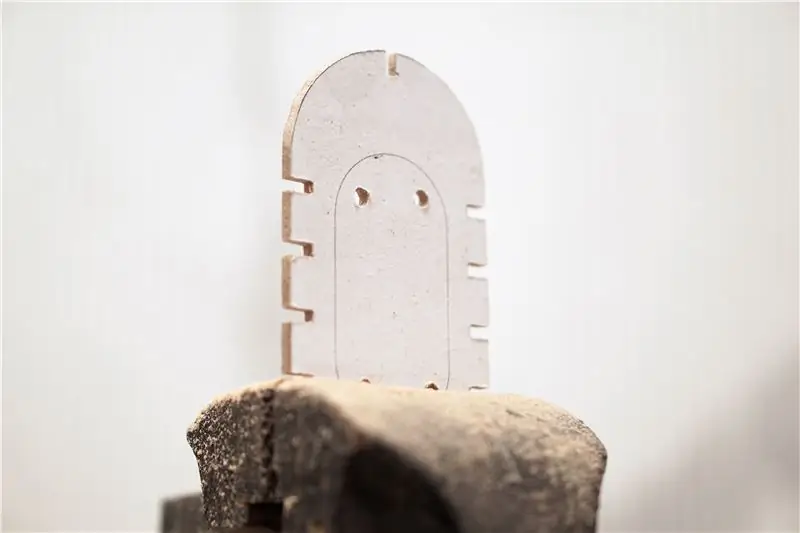
Dieser Schritt sollte viel einfacher gehen, da wir bereits nach dem Außenschneiden eine Fähigkeit haben, der Hauptpunkt ist, das Teil jedes Mal bequem zu platzieren, wenn Sie schwierige Stellen erreichen.
Pilotlöcher
Dafür können wir einen Spatenbohrer verwenden und von beiden Seiten mindestens zwei große Löcher bohren, aber ich bevorzuge es, kleine Löcher zu machen, es sind keine 4 Löcher erforderlich, aber manchmal muss man zwischen den Schnitten eine Pause machen oder die Hand wechseln, zusätzliche Löcher machen Prozess viel einfacher, Sie müssen die Kappsäge nicht am Startpunkt bewegen oder das Sägeblatt vollständig entfernen, erreichen Sie einfach den nächsten Punkt und Sie können Ihre Arbeit verlassen;)
Coping Sägeblattplatzierung
Dies ist ganz einfach, einfach eine Seite des Sägeblatts abschrauben, Sägeblatt in das Loch einführen, dann wieder spannsäge, danach Teil im Schraubstock befestigen und fertig, Sie können einen Schnitt machen.
Fertigstellung
Nachdem das Innenteil ausgeschnitten ist, nehmen Sie eine "Halbrundfeile" und glätten Sie die raue Oberfläche.
Spitze! Versuchen Sie, das Innenteil in einem Stück zu schneiden, dies ermöglicht es, den gesamten Rahmen im Schraubstock zu fixieren, auch dies reduziert das Wackeln und erleichtert den Schneidvorgang erheblich.
Schritt 12: Temporäre Montage und Messungen
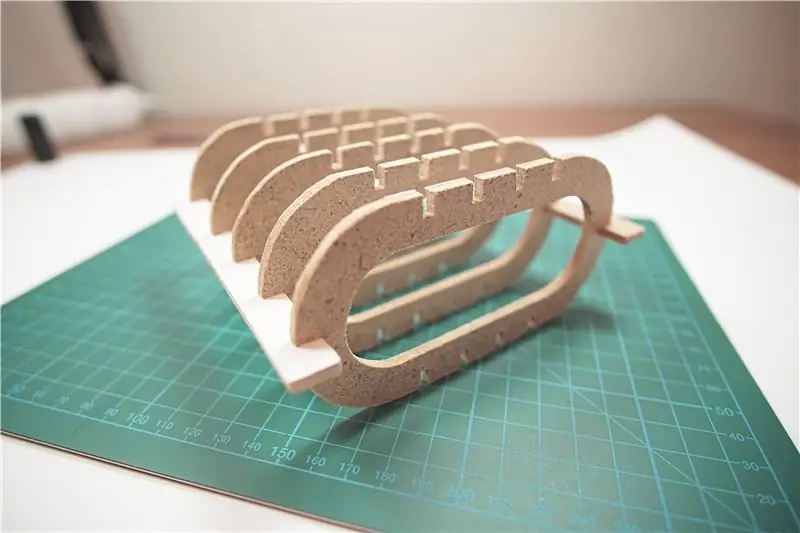
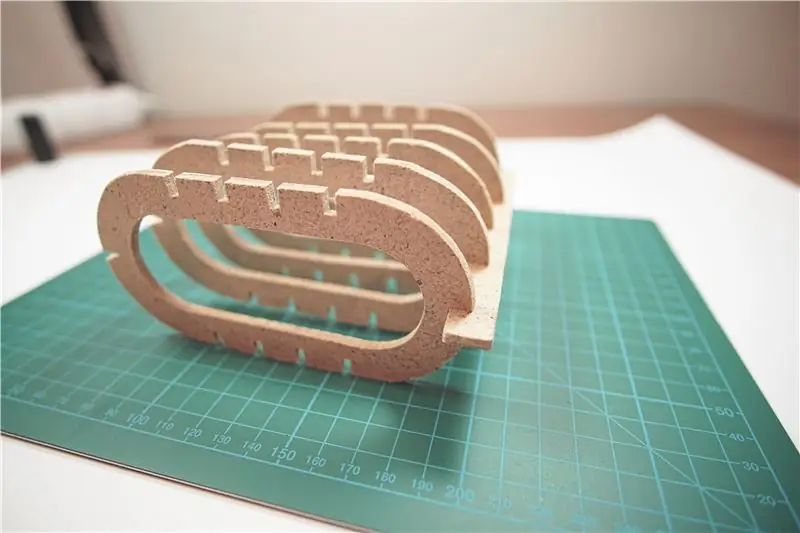
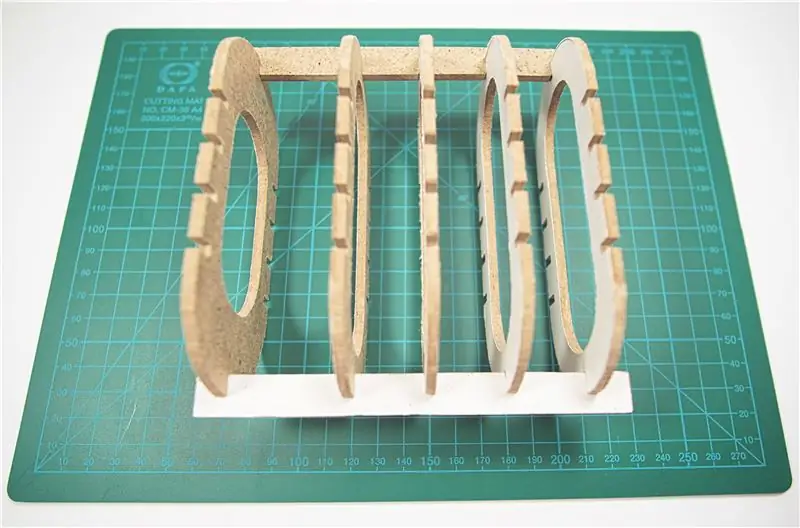
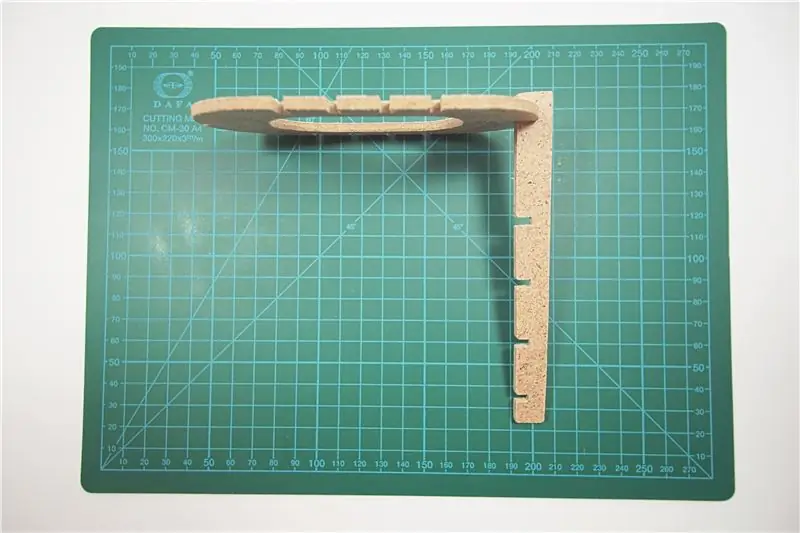
In diesem Stadium können wir unser Skelett sorgfältig zusammenbauen, wie auf den Bildern gezeigt, und wir können auch die notwendigen Messungen für unsere Innenteile vornehmen.
Dieser Bluetooth-Lautsprecher ist wartungsfähig, zumindest einige Teile, dies bedeutet, dass wir genug Kabel lassen sollten, um sicherzustellen, dass:
- Rückwand lässt sich leicht herausziehen, während (Ladeanschluss, LED und Ein-/Aus-Schalter) angebracht sind;
- Batteriemodul und Bluetooth-Audioplatine sollten aus der Hülle herauskommen, ohne sie vom Lautsprecher zu trennen.
Bluetooth-Audioboard, Step-Up-Konverter und Batterien in diesem Bauhalter wird auf der Montageplatte montiert, das Ladeboard auf der Rückplatte, es wird an der Halterung befestigt, alle Markierungspunkte und Messungen für diese Teile sollten auf dieser Bühne durchgeführt werden.
Schritt 13: Lautsprecher
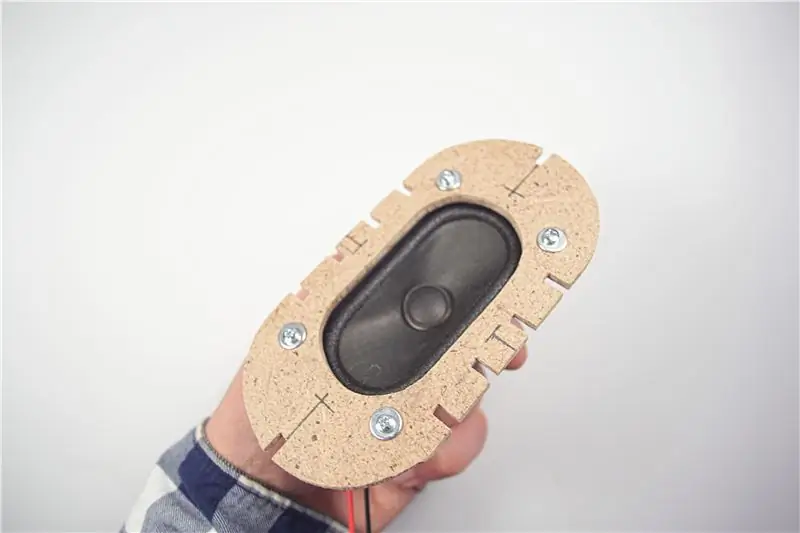
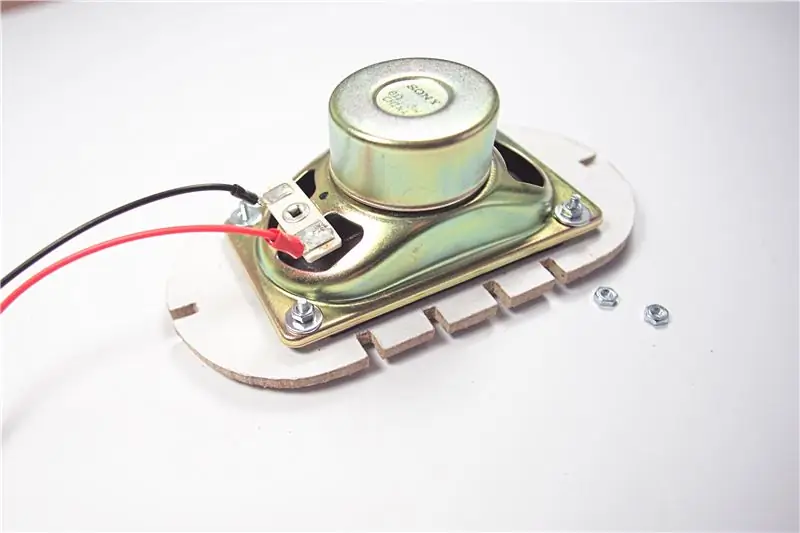
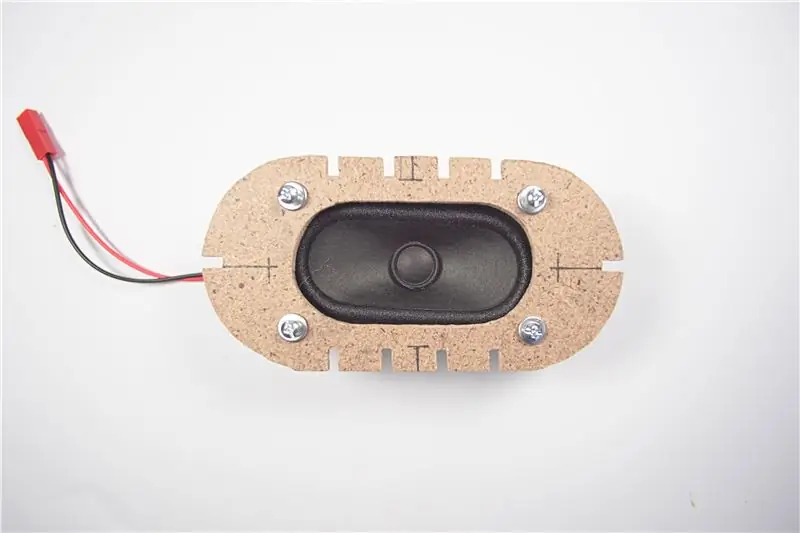
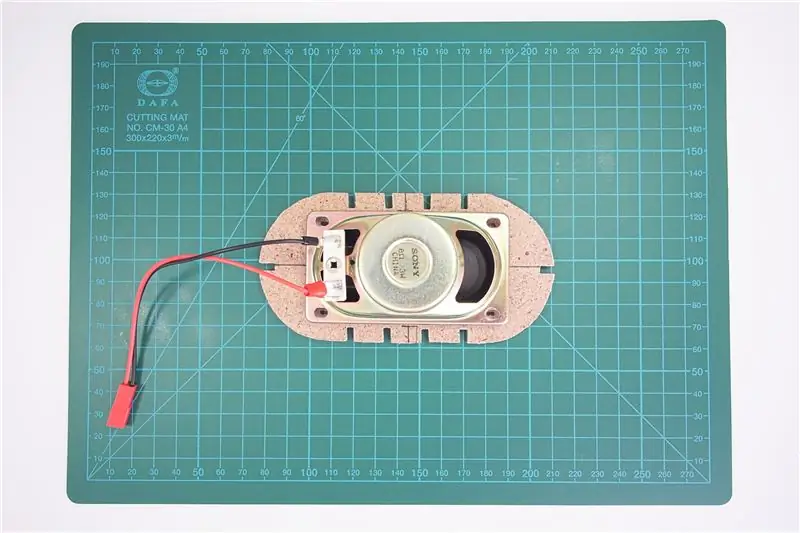
Jetzt können wir den Lautsprecher an der Frontplatte befestigen. Es gibt keine Löcher auf der Schablone, aber in diesem Schritt werden wir sie machen.
Richtige PlatzierungDer einfachste Weg, den Lautsprecher richtig zu platzieren, ist: Plattenhöhe minus Lautsprecherhöhe und durch zwei teilen. Wir sollten die gleiche Markierung von oben und unten in der Mitte der Platte machen, das gleiche Verfahren für die Breite. Mit diesen Markierungen als Richtlinie können wir den Lautsprecher nun genau in der Mitte platzieren und ihn vorübergehend mit Heißkleber befestigen.
Loch bohren und befestigen
Lautsprecher hat M4-Löcher, aber in meinem Laden vor Ort hatten sie nur M2,5, weil sie häufiger verwendet werden, das ist keine große Sache. Da Hartholz immer noch leicht zu brechen und M2,5 Schrauben sehr klein sind, benötigen wir zusätzlich 4 Unterlegscheiben.
Schritt 14: Bluetooth-Audioboard
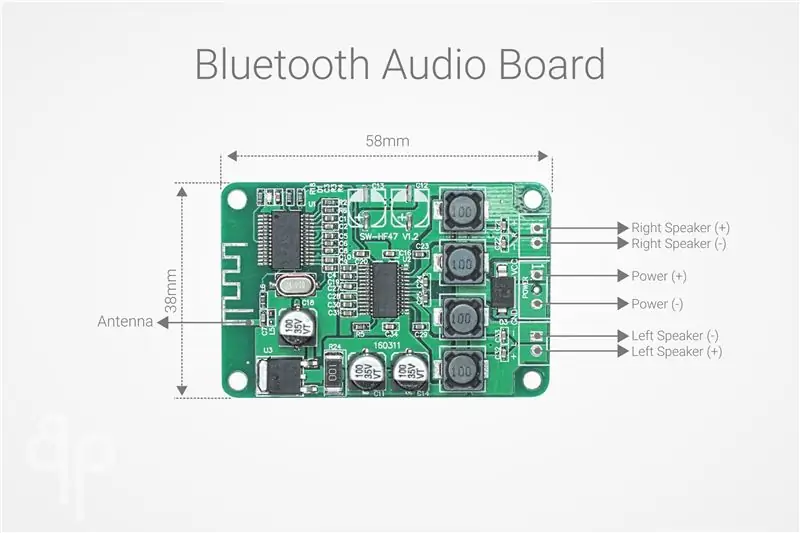
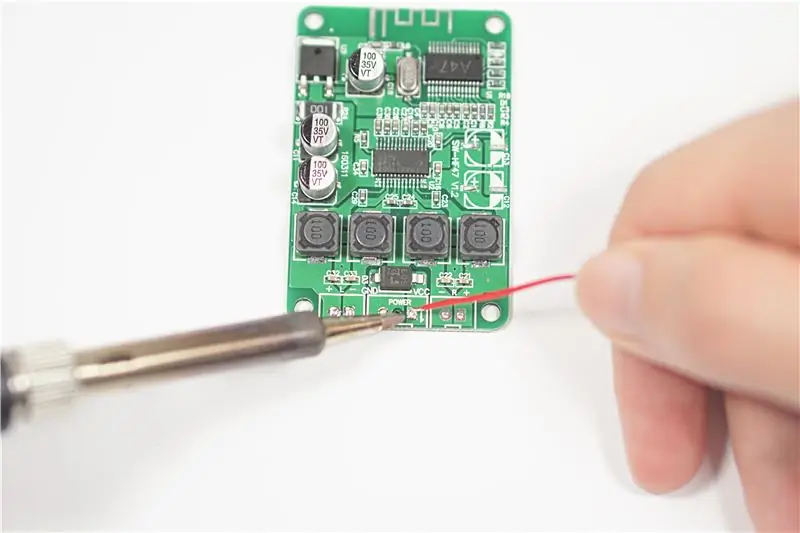
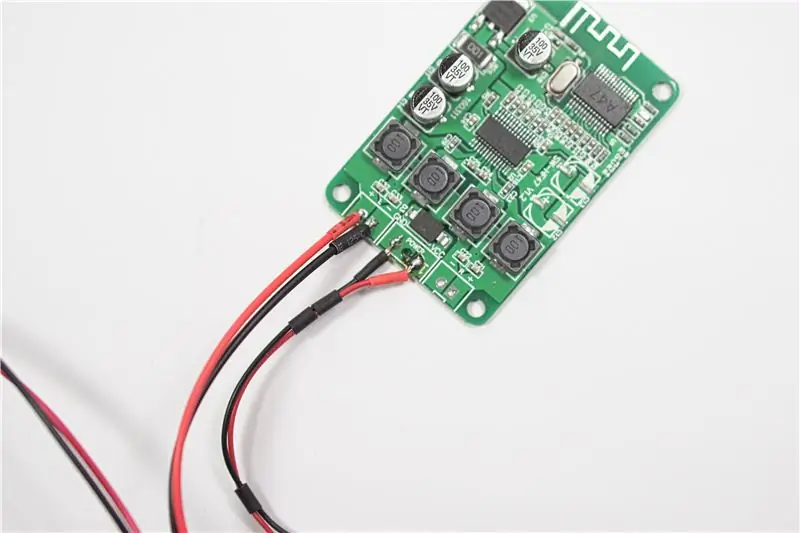
Laut TPA3110D2 Datenblatt kann dieser Class-D-Verstärker bis zu 15W pro Kanal liefern, das ist eine Menge Leistung, insbesondere für 3W-Lautsprecher, kein Zweifel, dass dieser Lautsprecher viel mehr halten kann, nur die Frage, wie lange.
Der Hauptnachteil dieses Boards ist kein Bluetooth-Chip. Dieses Bluetooth-Modul ist nicht schlecht, aber Stahl, CSR-basierter Barde ist viel besser.
Mein Bluetooth-Audioboard ist beschädigt angekommen, 2 Kondensatoren sind ausgefallen, aber für mich ist das nicht das Problem, da dieses Projekt nur einen Kanal benötigt.
Es gibt nicht viele Vorbereitungen für das Mainboard, einfaches Löten von Lautsprecherkabeln und Stromkabeln. In meinem Fall sind das Kabel mit JST-Anschlüssen.
Spitze! Ein weiteres kleines Detail, das hinzugefügt werden kann, sind winzige Kühlkörper aus dem Raspberry Pi Kit.
Schritt 15: Stromkreis
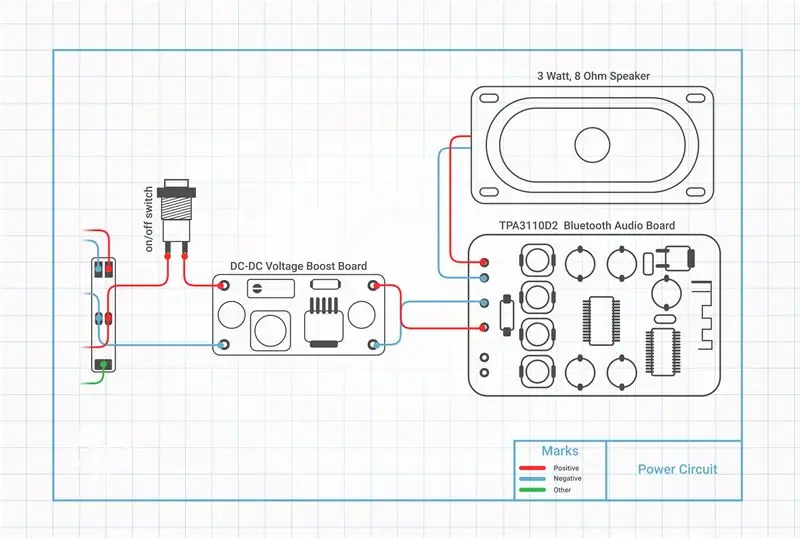
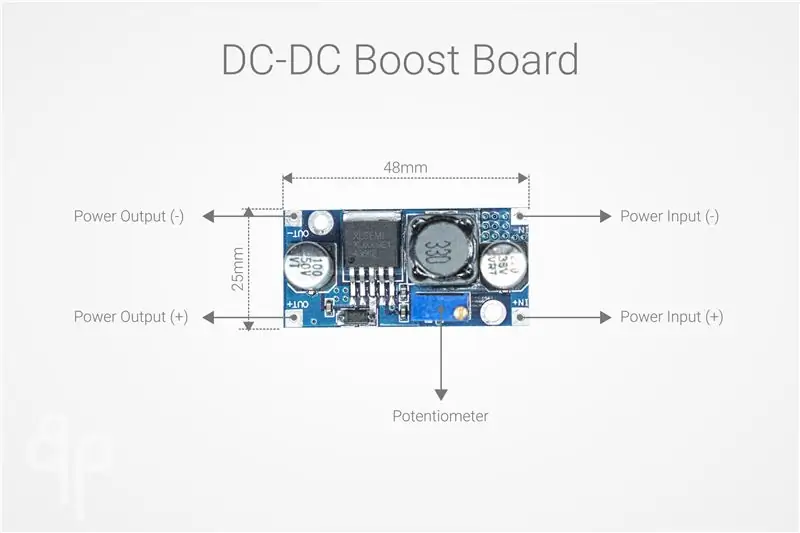

Wie bereits erwähnt, kann der TPA3110D2-Verstärker bis zu 15 Watt pro Kanal liefern, diese Leistung kann unseren Lautsprecher in Sekundenschnelle beschädigen.
Deshalb sieht die 2S-Konfiguration vernünftig aus. Bei maximaler Ladung können Li-Ion-Akkus eine Ausgangsspannung von bis zu 4,2 Volt 2S = 8,4 liefern, die minimal erforderliche Spannung für Verstärker beträgt 8 Volt, klingt zumindest vorerst gut. Die Spannung der Lithium-Ionen-Batterie kann jedoch auf 3 Volt absinken, was viel niedriger ist als das erforderliche Minimum.
Ich habe festgestellt, dass das Bluetooth-Board selbst bei Verwendung von 3 Watt-Lautsprechern nur bei maximaler Spannung einen klaren Klang liefert. Um dieses Problem zu lösen, benötigen wir einen Aufwärtsspannungswandler. Schließen Sie den Aufwärtswandler nahtlos an die Stromquelle an (in unserem Fall voll aufgeladene 2S Li-Ion-Baugruppe, mehr dazu im nächsten Schritt) und enden Sie dann mit dem Multimeter. Auf der Boost-Platine finden wir ein kleines Potentiometer, drehen Sie es allmählich im Uhrzeigersinn, bis das Multimeter eine Spannung von etwa 12-16 Volt anzeigt, und das ist alles.
Bei 16 Volt können wir ungefähr 0,55 Ampere erreichen, laut Verstärkerdatenblatt sollten wir 8 Watt Leistung erhalten. Ich habe viele verschiedene Spannungsvoreinstellungen ausprobiert und trotzdem ist der Ton bei niedriger Spannung nicht sehr gut, bei hoher Spannung ist der Ton akzeptabel, aber man kann nicht bei maximaler Lautstärke hören, es gibt keinen goldenen Punkt. Wenn Sie den Grund dafür kennen, hinterlassen Sie bitte einen Kommentar oder senden Sie mir eine Direktnachricht.
Schritt 16: Ladeschaltung
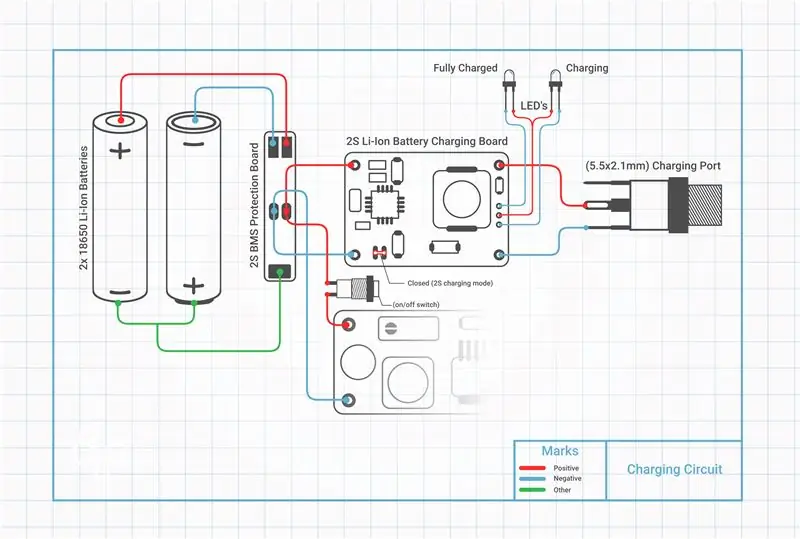
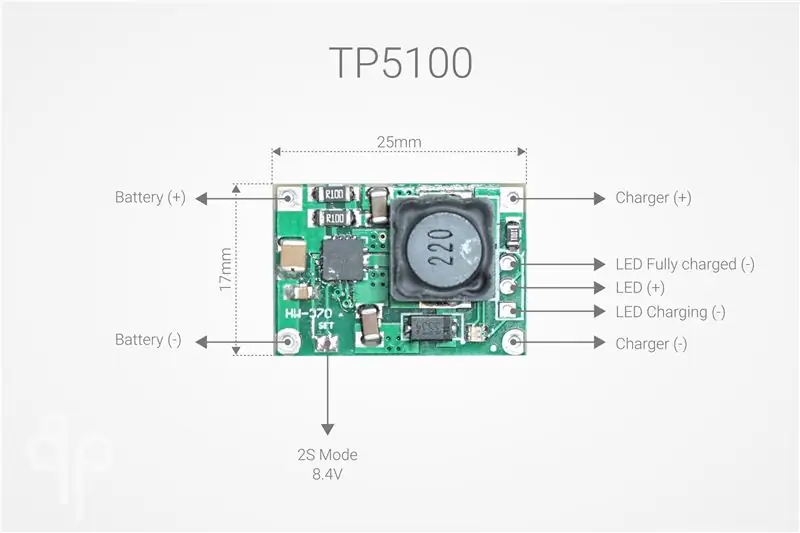
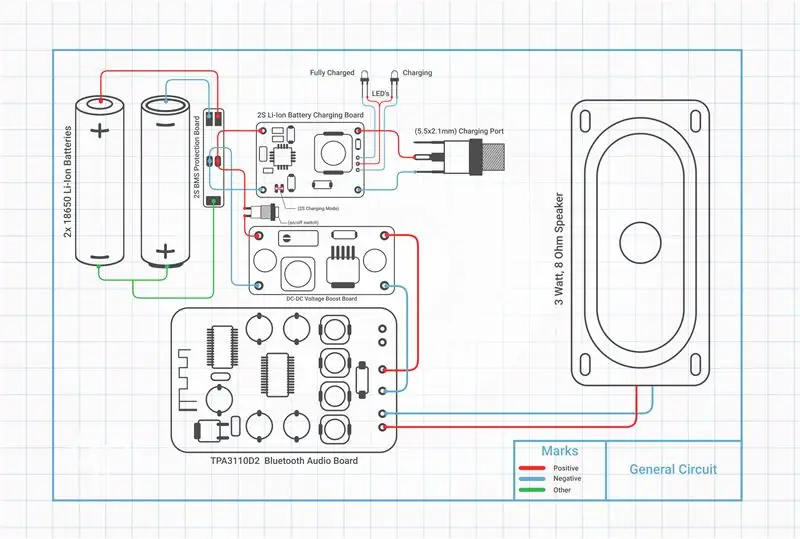
Die Ladeschaltung basiert auf dem TP5100-Chip, dieser Chip ist neu für mich, aber es gibt einige Gründe, warum dieses Modul in diesem Build verwendet wird:
- Breite Palette von Eingangsspannungen von 5 bis 15, dies bedeutet, dass wir sogar ein Router-Netzteil zum Laden oder sogar eine Autobatterie verwenden können, jedoch für eine Mindesteingangsspannung von 2S von 8,4 V:);
- Dedizierte Lötpunkte für Status-LED;
- 1S/2S Lademodi.
Es gibt auch einen Nachteil, dieses Modul kann zwei Li-Ionen-Akkus nacheinander laden, aber es gibt keine Überwachung für einzelne Zellen. Dies ist keine große Sache, wenn wir geschützte Batterien oder ähnliche Batterien mit gleicher Kapazität und Spannung verwenden, aber dies ist immer noch nicht sicher.
Diese Ladeplatine hat 7 Lötpunkte und einen Brückenpunkt:
- Ladeanschluss, Lötstellen;
- Lötpunkte für Status-LED;
- Lötpunkte für Akku, in unserem Fall 2S BMS (P+ und P-) Punkte.
Batterieschutz
Dafür verwende ich 2S BMS Protection Board basierend auf AO4406 Mosfet.
Diese Platine hat 5 Lötpunkte:
- (B+ und B-) Lötstellen für 2-x Li-Ion Akkus nacheinander;
- (BM) - Verbindung zwischen Batterien;
- (P+ und P-) - Lötpunkte für Last und TP5100 Ladeplatine. Schaltungen und Endmontage können Sie auf den Bildern sehen.
Notiz! Laden Sie zwei Li-Ion/Pol-Akkus mit unterschiedlichen Kapazitäten und Spannungen nacheinander auf, kann Akkus beschädigt werden.
Schritt 17: Testen
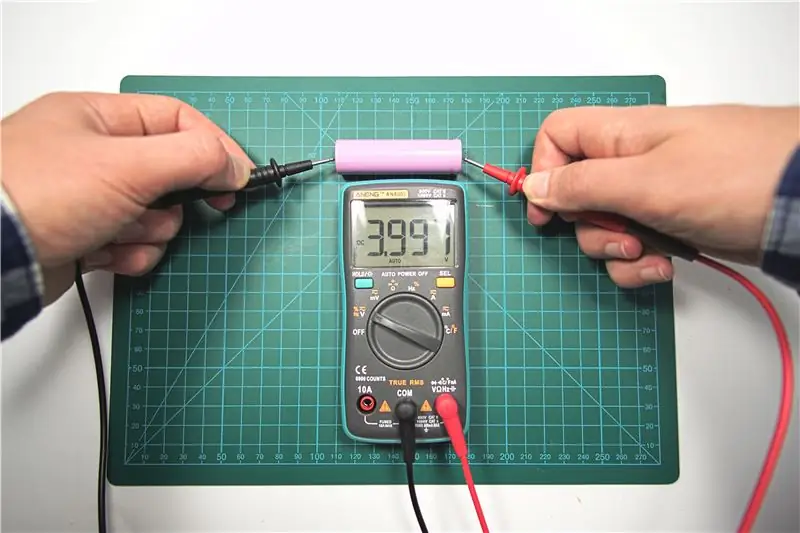
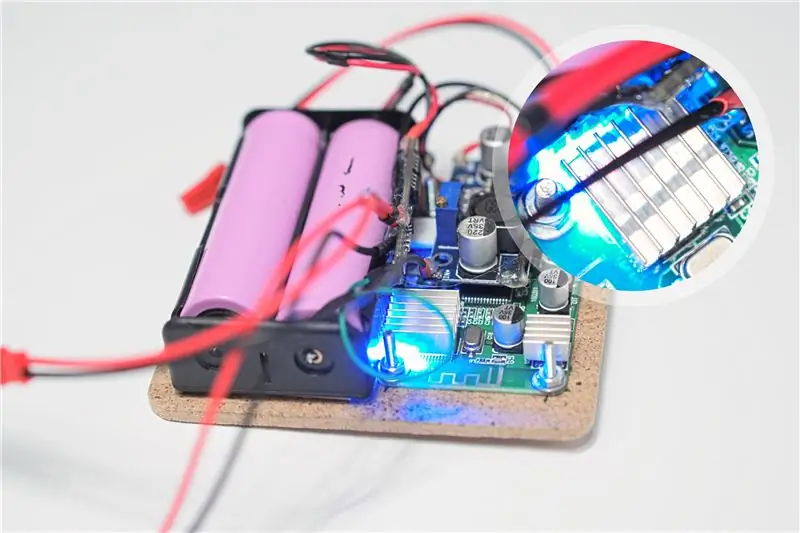
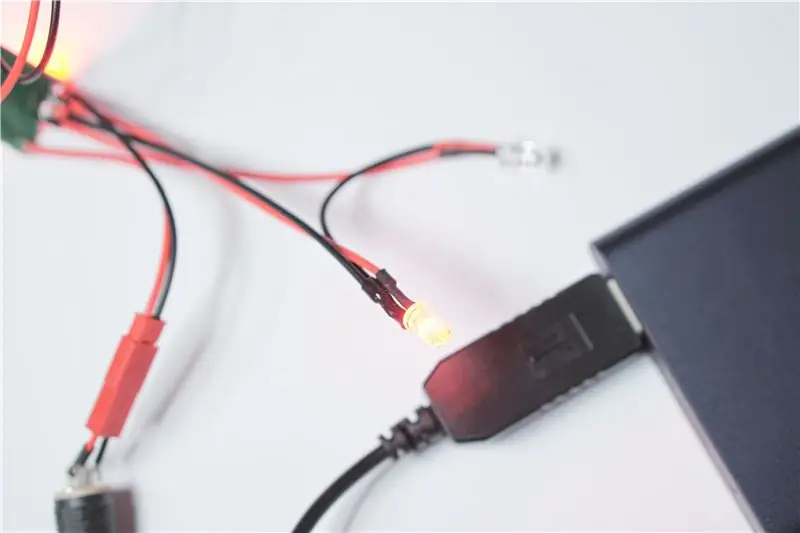
Vor Beginn der Endmontage sollte die gesamte Schaltung getestet werden.
- Status-LED, sollte die Ladestufen richtig anzeigen;
- Überladung - Messen Sie die Batteriespannung nacheinander nach der vollständigen Ladung;
- Überentladung - das dauert einige Zeit.
- Spielen Sie einige Lieder mit unterschiedlichen Lautstärken und Entfernungen vom Bluetooth-Lautsprecher ab;
- Überprüfen Sie die Temperatur des Verstärkers und der Bluetooth-Chips.
Schritt 18: Rahmenmontage
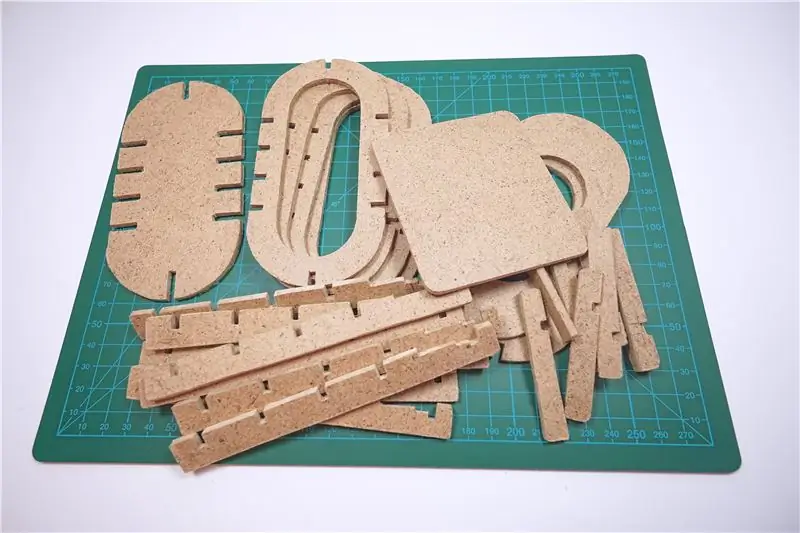
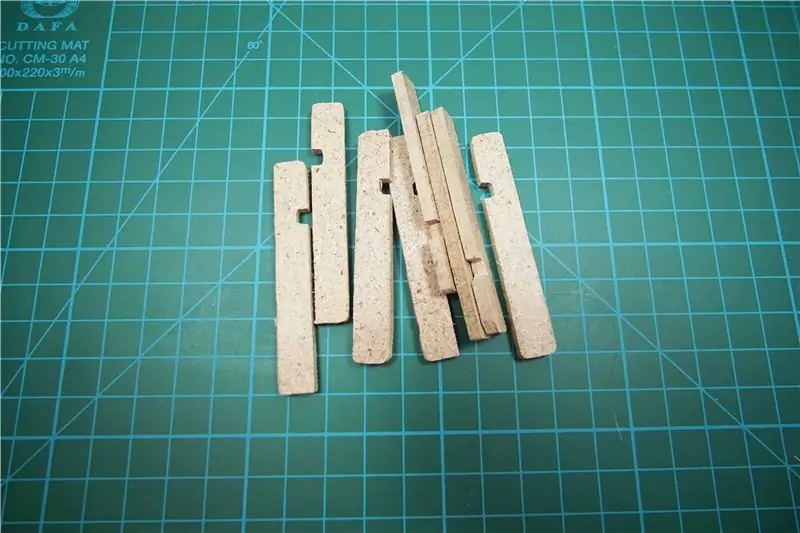
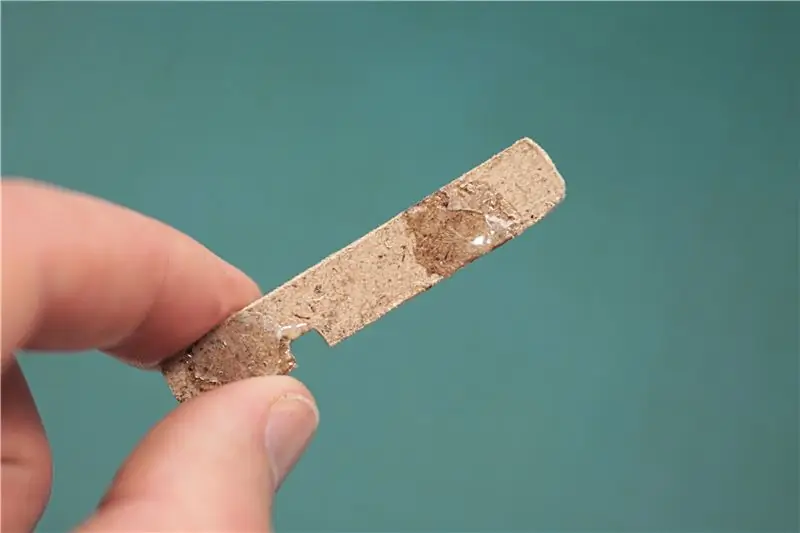
Nach dem Löten können wir mit der Montage des Rahmens beginnen.
- Stützstange seitlich einstecken, nur halb einführen, dadurch lassen sich andere Stützstangen viel einfacher platzieren, ohne andere Teile zu beschädigen.
- Nachdem die Seitenstützen halb installiert sind, können wir obere und untere Stützen einsetzen. Es gibt keine spezielle Installationsreihenfolge für die unteren Stützen, aber sie sollten auch auf dieser Stufe halb installiert werden.
- Bereiten Sie Epoxidkleber vor. Auf dieser Stufe benötigen wir ca. 3-4 cm Kleber. Mischen Sie zwei Verbindungen zusammen und rühren Sie sie mit einem Einweg-Kunststoff- oder Holzstab um.
- Tragen Sie zunächst ein wenig Epoxidkleber in die Verbindungsstelle auf und hämmern Sie sie dann nacheinander vorsichtig ein. Versuchen Sie jedoch zuerst, jedes Teil von Hand einzuführen kleiner Hammer.
- Wenn der Kleber getrocknet ist, setzen Sie alle Elektronikteile vorsichtig mit M2,5 Schrauben auf die Montageplatte.
- Legen Sie die Stützplatte ein und tragen Sie an den Stellen, an denen sie die Stützen berührt, etwas Heißkleber auf.
Schritt 19: Pappmaché-Shell
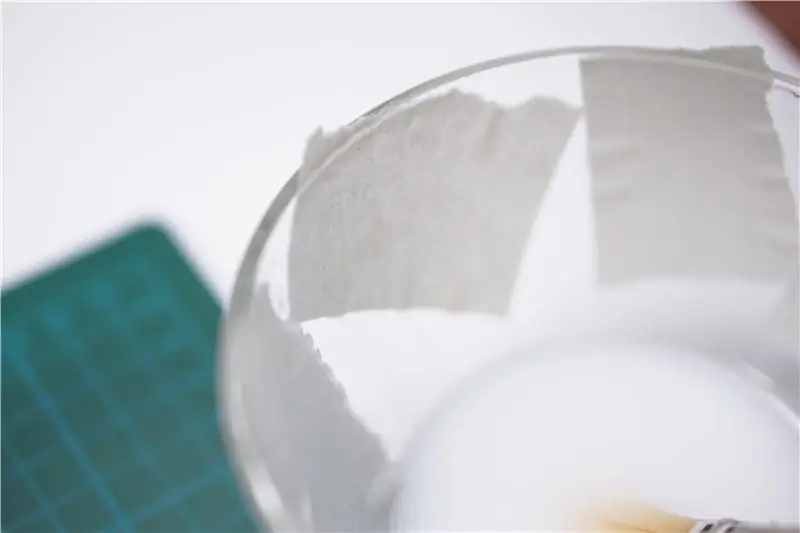
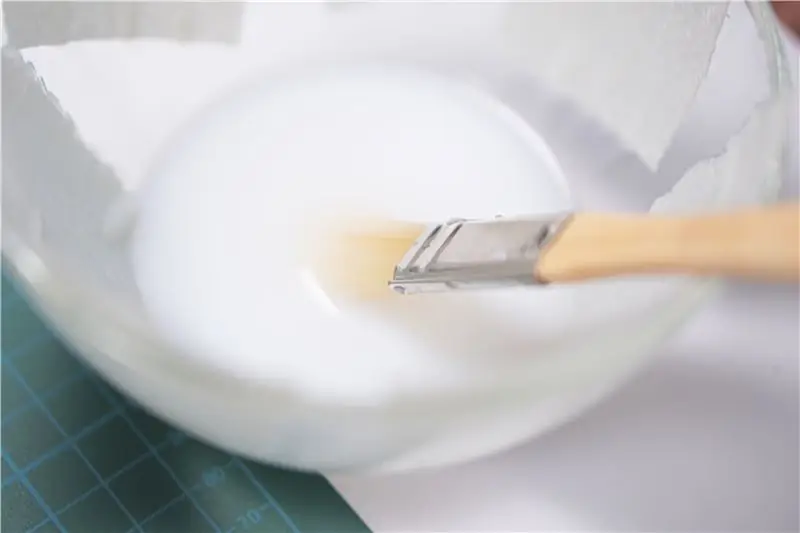
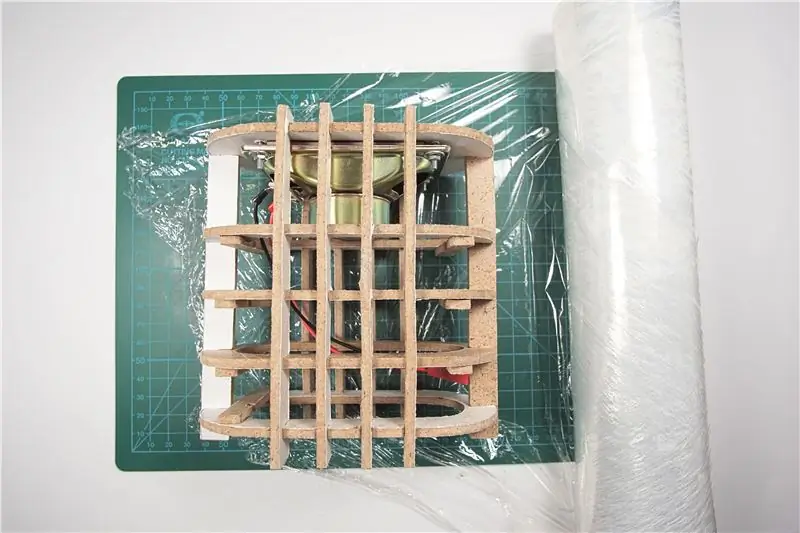
Dies ist, wo Projekt seinen Namen hat. Es gibt viele verschiedene Möglichkeiten, eine Muschel zu machen, aber die Pappmaché-Schale wurde sofort für diesen Bluetooth-Lautsprecher als die günstigste und einfachste ausgewählt.
Für Pappmaché benötigen wir nicht weniger als 250 ml PVA-Kleber, es gibt keine genaue Messung, da Sie Wände so dick machen können, wie Sie möchten, etwa zwei oder drei Dutzend Büropapier oder Zeitungen, Zeitungen viel besser, Sie können mehr darüber lesen das hier.
- Mischen Sie warmes Wasser mit Leim im Verhältnis 1:1 (auch 1:2 möglich);
- Papier zerkleinern, ca. 2x2 Zentimeter;
- Legen Sie zerrissene Papierstücke für etwa 10 Minuten in diese Mischung;
- Wickeln Sie den Rahmen in Plastikfolie ein;
- Decken Sie die Hälfte des Bluetooth-Lautsprecherrahmens mit Pappfolie ab, befestigen Sie ihn mit Kreppband oder Klebeband;
- Schicht für Schicht geschredderte Papierstücke auf die Kartonoberfläche auftragen, ca. 12 Schichten sollten ausreichen;
- Lassen Sie die Pappmaché-Schale etwa einen Tag lang trocknen. Dieser Vorgang hängt von den Bedingungen ab. Sie können die Schale nach 12 Stunden überprüfen. Wenn Sie Büropapier verwenden, die Trocknungszeit deutlich länger und die Struktur deutlich schwächer ist, empfehle ich daher nicht, es zu verwenden;
- Wiederholen Sie die gleichen Schritte für die Oberseite des Lautsprecherrahmens.
Jetzt haben wir zwei Stücke Pappmaché-Schale, die am Rahmen befestigt werden sollen, dafür verwenden wir wieder Epoxid oder Heißkleber.
- Karton aus der Schale entfernen;
- Kleber auf die Rahmenfugen auftragen;
- Befestigen Sie die Pappmaché-Schale mit Kreppband am Rahmen;
- Schwierig, aber immer noch möglich, versuchen Sie, im Inneren des Lautsprechers Klebstoff zwischen Gehäuse und Rahmen zu kleben;
- Klebstoff auf nicht abgedeckte Teile des Rahmens auftragen.
Schritt 20: Rückwand
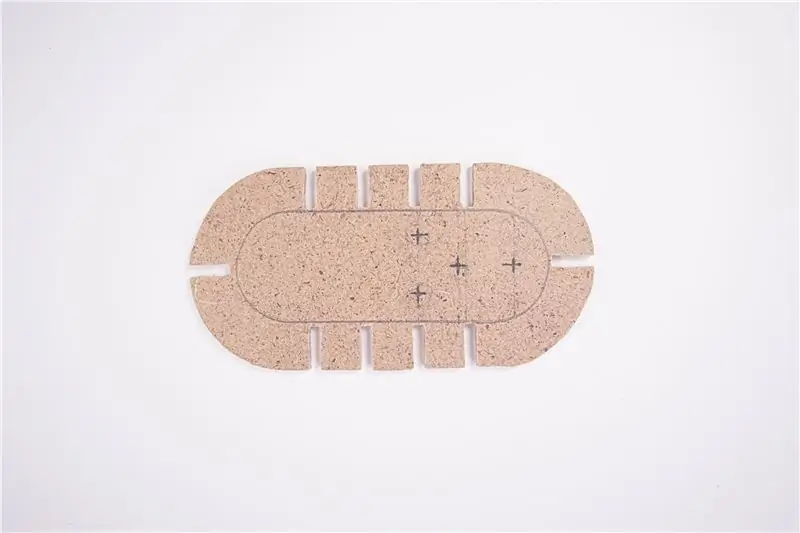
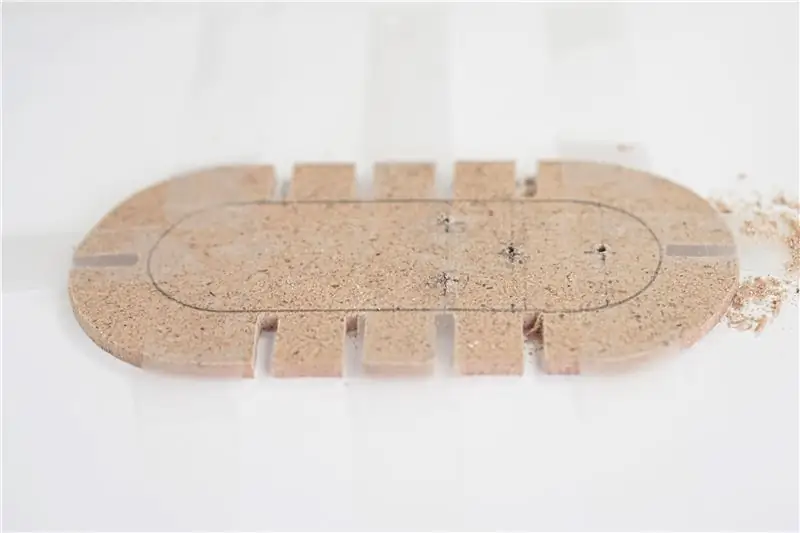
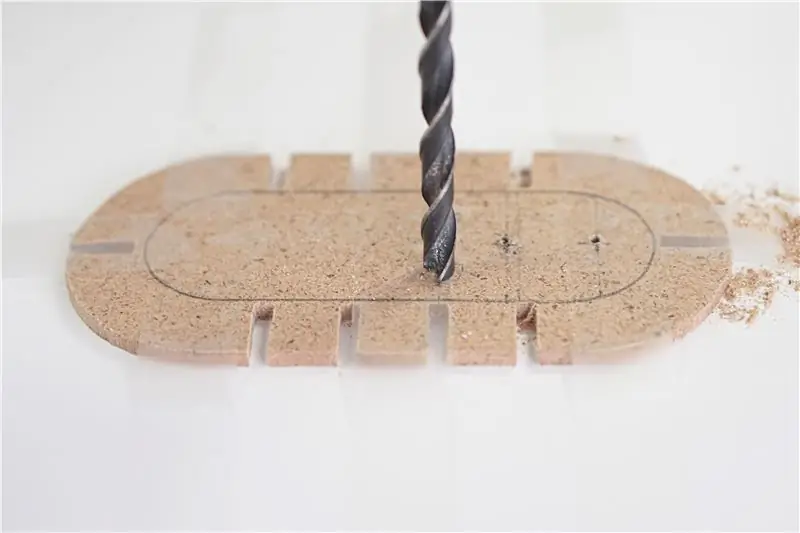
Um den gleichen Stil beizubehalten, entschied ich mich, Stoff mit fast der gleichen Struktur wie für den Frontgrill zu verwenden.
- Schneiden Sie ein Stück Stoff ab, das etwas größer als unsere Rückenplatte ist;
- Tragen Sie eine dünne Schicht Epoxidkleber auf die Rückwand auf;
- Legen Sie den Stoff auf die Rückenplatte und glätten Sie ihn vorsichtig mit einem Lineal.
- Wenn der Kleber getrocknet ist, schneiden Sie überschüssiges Material von der Unterseite ab und verwenden Sie die Rückplatte als Schablone. Es müssen keine Schnitte vorgenommen werden, da sie ausgeblendet werden;
- Fügen Sie Druckknopf, Ladeanschluss und LED-Anzeige hinzu, auch die Ladeplatine sollte an der Rückplatte montiert werden;
- Bringen Sie die Rückplatte am Hauptrahmen an und befestigen Sie sie mit Heißkleber.
Wenn die Rückplatte installiert ist, können wir Verbindungen verstecken, indem wir Paracord weiter wickeln, aber jetzt viel Heißkleber oder Epoxid verwenden.
Schritt 21: Paracord Wrap
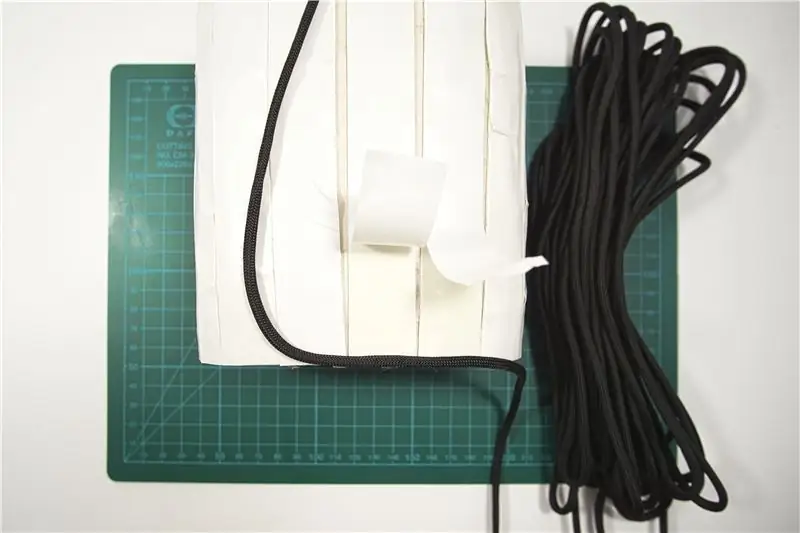
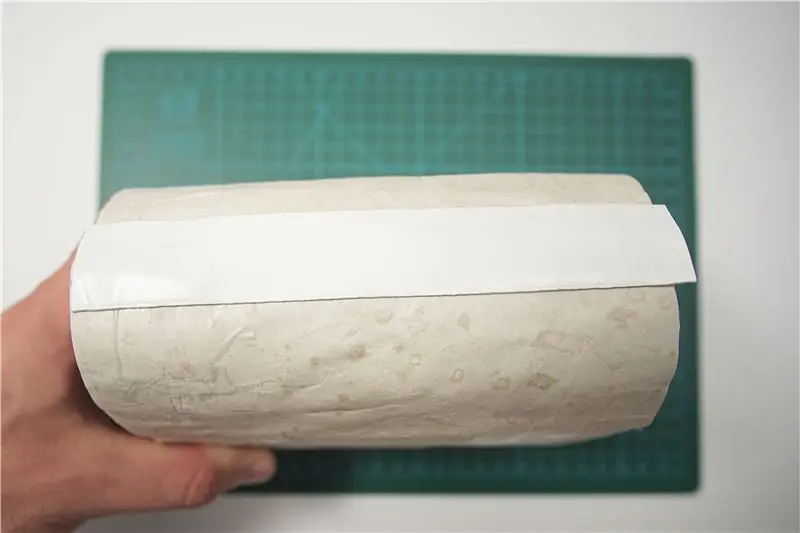
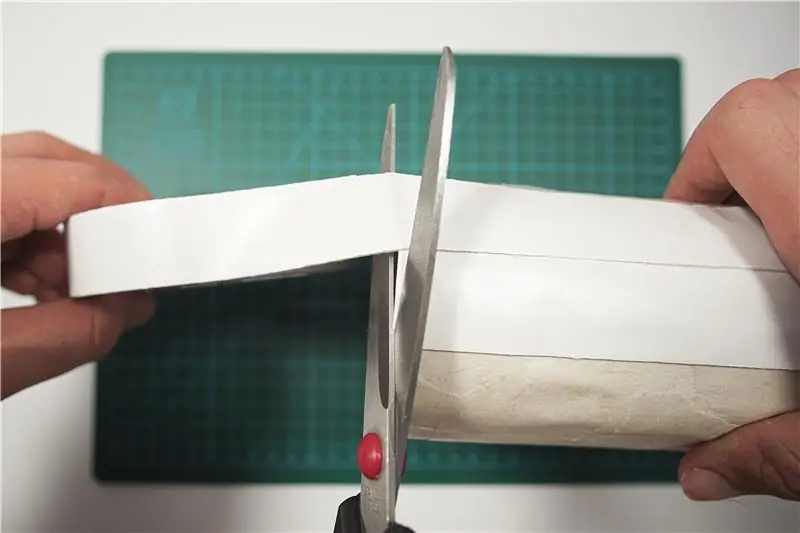
Unser Bluetooth-Lautsprecher ist bereit, einen „Anzug“zu tragen und attraktiver zu werden.
Paracord ist eine sehr verbreitete und nützliche Sache, aber was noch wichtiger ist, es hat eine sehr große Auswahl an Farben.
Es sind nur wenige Schritte erforderlich, um Ihren Bluetooth-Lautsprecher schön zu verpacken:
- Wickeln Sie die ganze Schale mit doppelseitigem Klebeband ein, ziehen Sie die Schutzschicht zu diesem Zeitpunkt nicht ab;
- Befestigen Sie ein Ende mit Heißkleber an der Unterseite, lassen Sie etwa 3 cm Schnur übrig, die wir später verwenden werden;
- Ziehen Sie eine kleine Menge der Schutzschicht von doppelseitigem Klebeband ab und beginnen Sie, den Lautsprecher aufzuwickeln. Versuchen Sie, jeden Wind so nah wie möglich an den vorherigen zu bringen.
- Wenn eine Hälfte des Bluetooth-Lautsprechers in Paracord eingewickelt ist, ist es an der Zeit, eine weitere Farbe hinzuzufügen:
- Schneiden Sie übermäßiges Paracord ab;
- Tragen Sie eine kleine Menge Epoxidkleber auf das Paracord-Ende auf;
- Ziehen Sie 3 mm Schrumpfschlauch am Paracord-Ende;
- Wiederholen Sie den vorherigen Schritt für zusätzliche Farbe;
- Wickeln Sie weiter und wiederholen Sie die obigen Schritte, wenn zusätzliche Farbe hinzugefügt wird.
Wenn Sie sich entschieden haben, nur eine Farbe zu verwenden, befestigen Sie einfach das Ende wie in Unterabsatz 2 dieses Schrittes beschrieben.
Schritt 22: Frontgrill
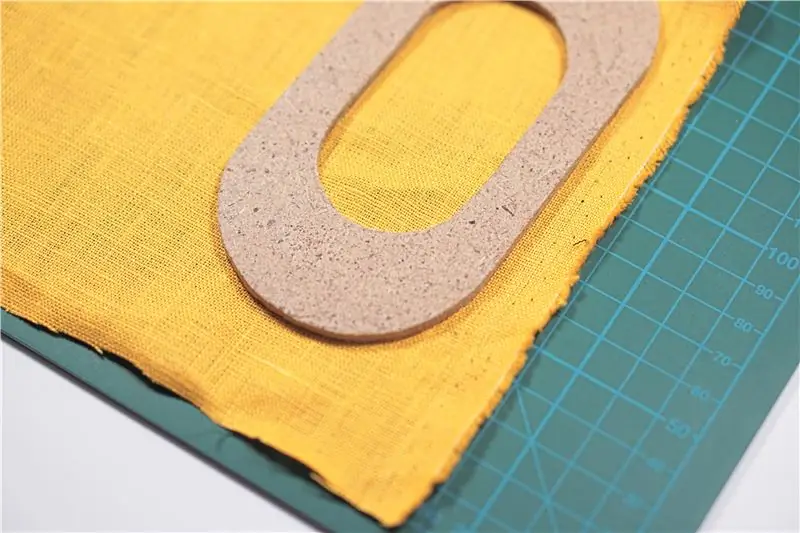
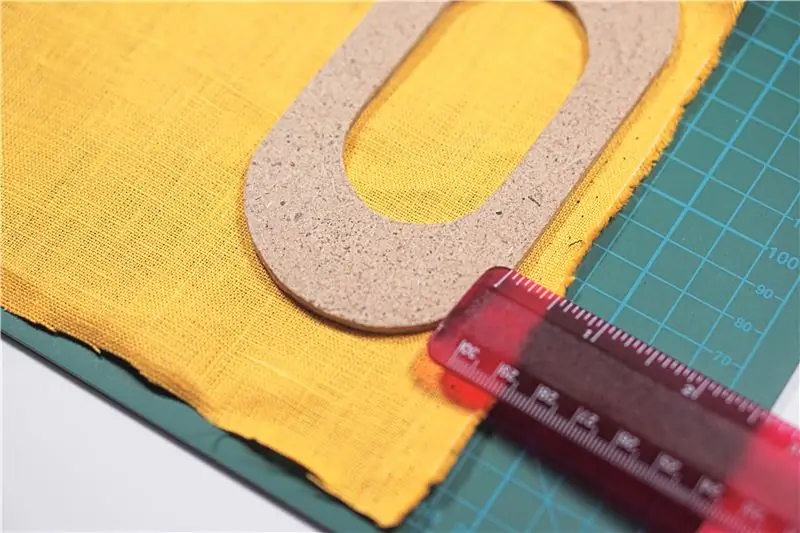
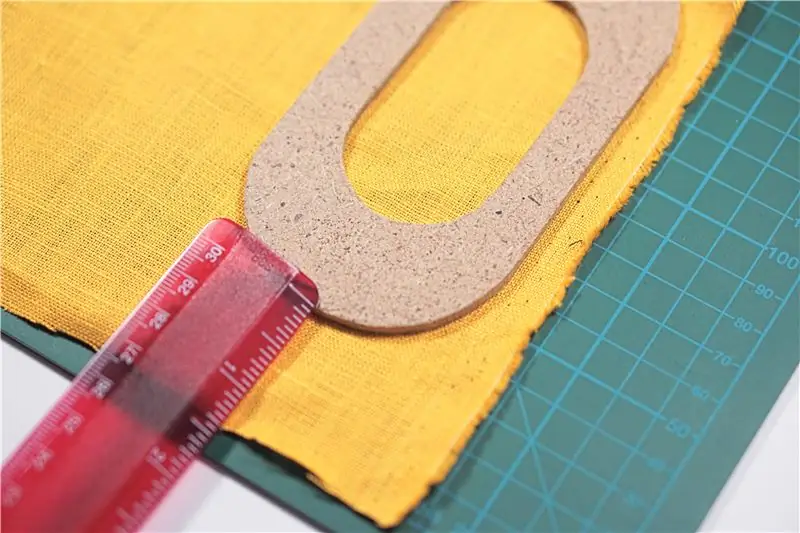
Der Verpackungsvorgang für den Frontgrill wird ein wenig anders sein als für die Rückwand, aber nicht sehr schwierig.
- Bereiten Sie den Stoff wie im vorherigen Schritt vor, aber lassen Sie jetzt genau überschüssigen Stoff: 15 mm von oben und unten und 40 mm von den Seiten;
- Schneiden Sie ein Stück vom dicken Stoff in Form Ihres Frontgrills ab und bohren Sie Löcher für Magnete;
- Kleben Sie Magnete auf das Bluetooth-Lautsprechergehäuse.
- Führungspunkte mit Korrekturflüssigkeit markieren;
- Befestigen Sie zwei weitere Magnete mit Epoxidharz an der Unterseite des Grills.
Das ist alles, jetzt können wir den Frontgrill mit Magneten montieren.
Schritt 23: Fazit
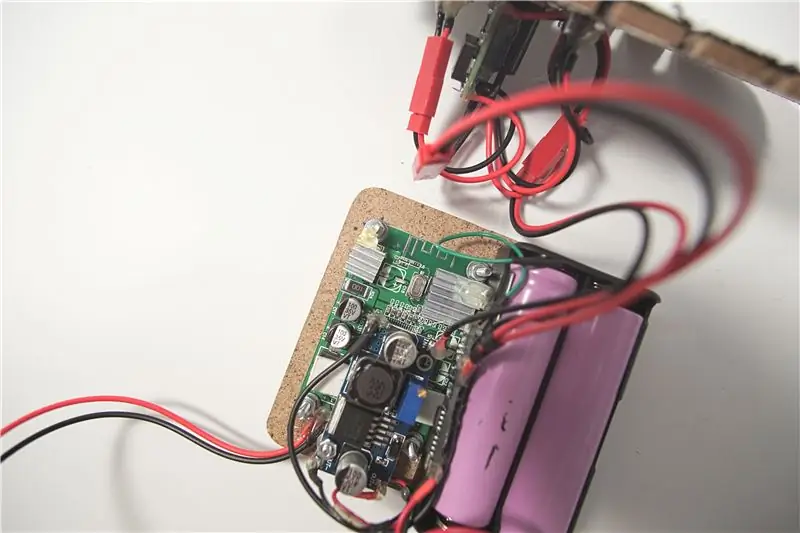
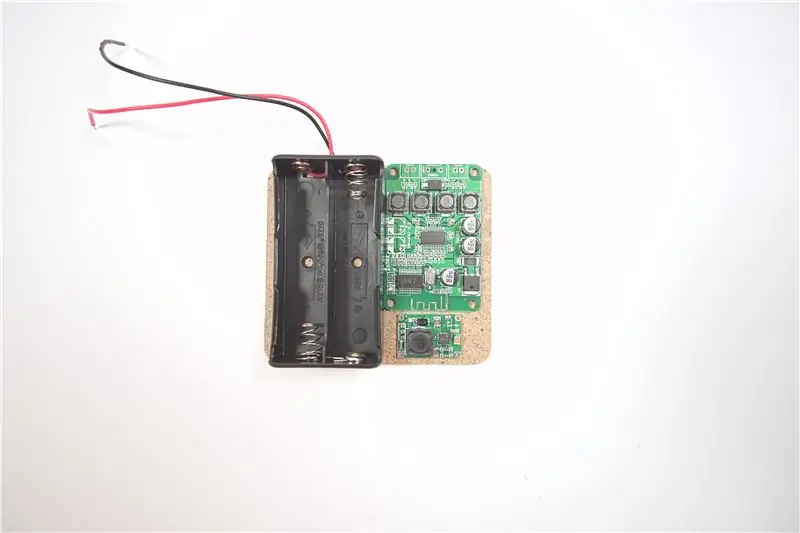
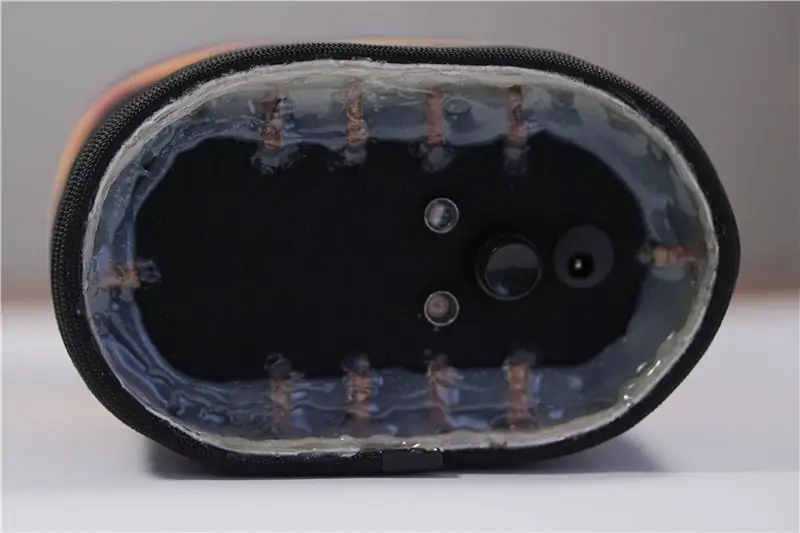
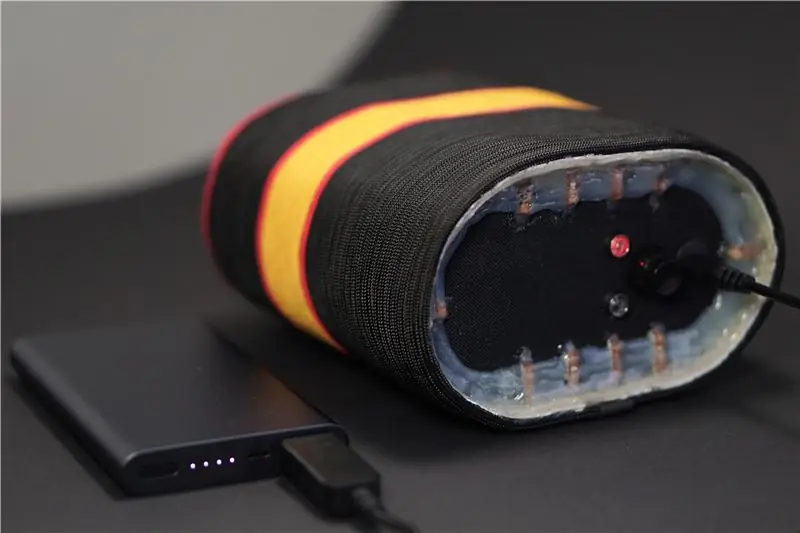
Bei diesem Projekt wurden viele Fehler, Änderungen und Verbesserungen vorgenommen.
Der Hauptfehler ist die Skalierung, und das ist meine Schuld, weil ich die Druckerskalierung vergessen habe und die Messung nach dem Drucken nicht überprüfe. Als mir dies klar wurde, ist bereits viel Arbeit geleistet und es gab keine Zeit, den gesamten Prozess noch einmal zu wiederholen, deshalb hat das Endprodukt einige Änderungen.
Hoffe es hat dir gefallen.
Empfohlen:
Ein Bluetooth-gesteuertes RC-Auto zu Hause bauen – wikiHow
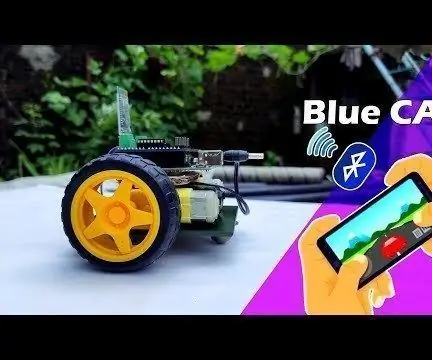
So bauen Sie ein Bluetooth-gesteuertes RC-Auto zu Hause: Erfahren Sie, wie Sie ein einfaches SmartPhone-gesteuertes Roboterauto mit Arduino und sehr einfachen elektronischen Komponenten bauen
LED Demon Eye mit Smartphone Bluetooth App einrichten: 5 Schritte
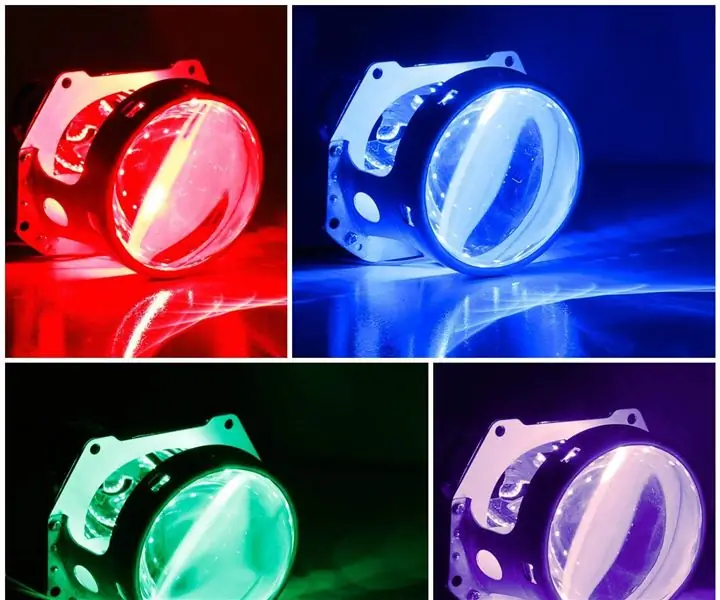
So richten Sie LED Demon Eye mit Bluetooth-App für Smartphones ein: In dieser Installationsanleitung erfahren Sie, wie Sie die App einrichten, die über Bluetooth eine Verbindung herstellt. Diese App ist sowohl im Apple Store als auch bei Google Play erhältlich und heißt "Happy Lighting"
DIY Multi-Room-WLAN + Bluetooth-Audiosystem - Hi-Fi: 7 Schritte
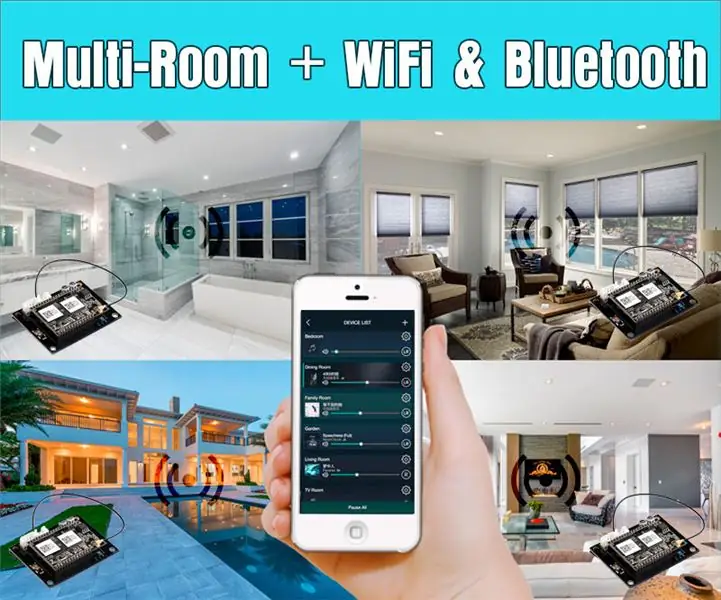
DIY Multi-Room-WLAN + Bluetooth-Audiosystem | Hi-Fi: Ich liebe Musik und ich weiß, dass du das auch tust. Aus diesem Grund bringe ich dir dieses Tutorial, das dich dazu führt, dein eigenes Wi-Fi + Bluetooth Hi-Fi-Audiosystem zu erstellen, damit du in der Lage bist, Genießen Sie Ihre Musik von Ihrem Telefon, PC, Tablet, persönlichen Assistenten
So richten Sie einen Bluetooth-Dongle auf einem Macbook Pro ein: 6 Schritte
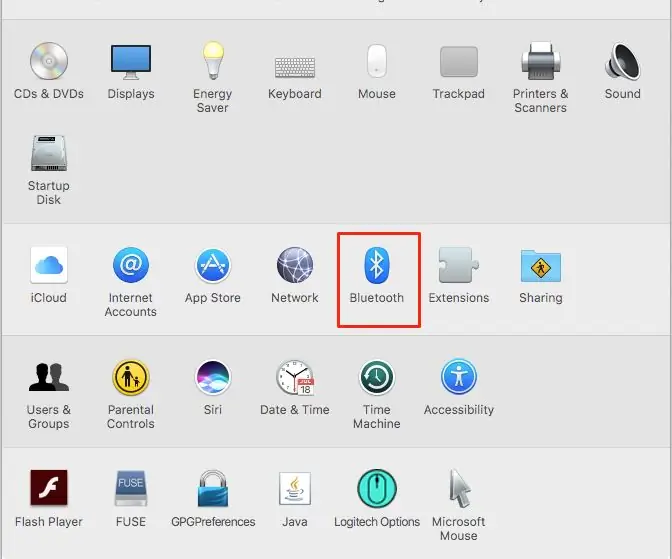
So richten Sie einen Bluetooth-Dongle auf einem Macbook Pro ein: Hintergrund: Nach langem Suchen und Durchstöbern veralteter Foren und Support-Threads (normalerweise gespickt mit abfälligen und wenig hilfreichen Kommentaren) habe ich es geschafft, einen Bluetooth-Dongle erfolgreich auf meinem Macbook einzurichten. Es scheint viele Leute zu geben
Domotik Bluetooth 3: 4 Schritte
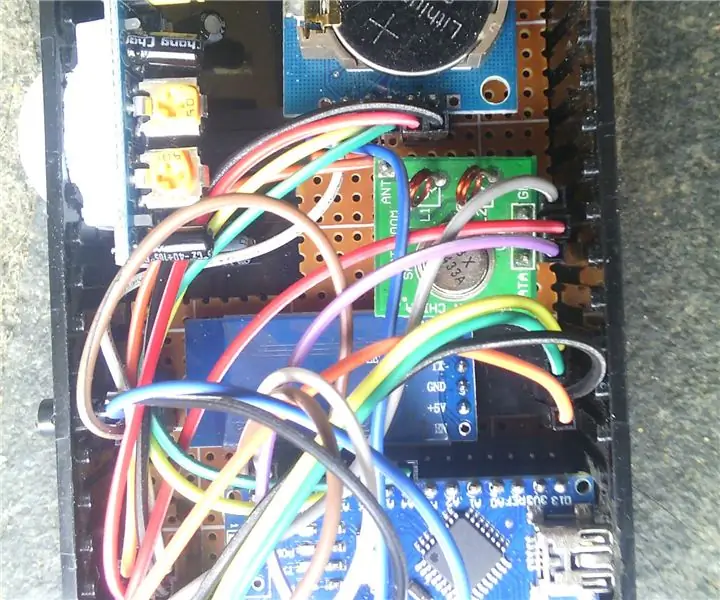
Domotique Bluetooth 3: L'idée du projet est une gestion de chauffage 3 pièces.Dans la pièce Principale, on place le capteur (Température, Présence) und dans le tableau électrique les relais.Le dialog entre le capteur et les relais se fait en RF433MHZLa Programmierung des P