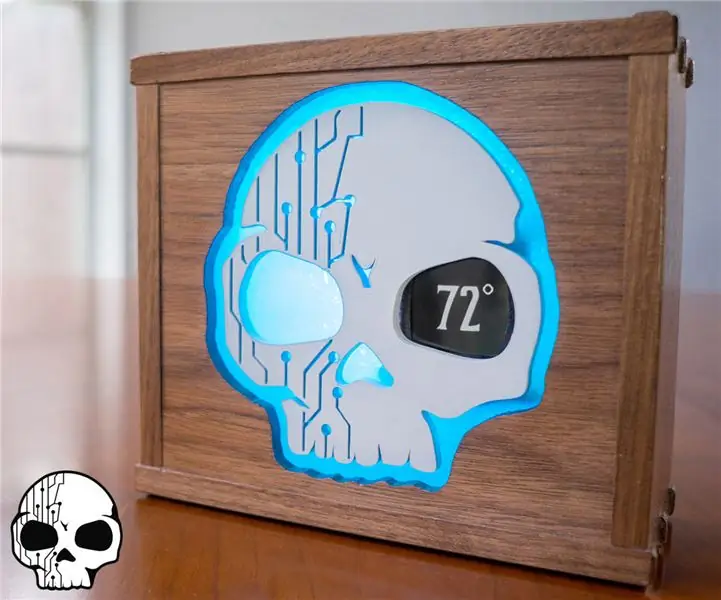
Inhaltsverzeichnis:
2025 Autor: John Day | [email protected]. Zuletzt bearbeitet: 2025-01-23 12:52
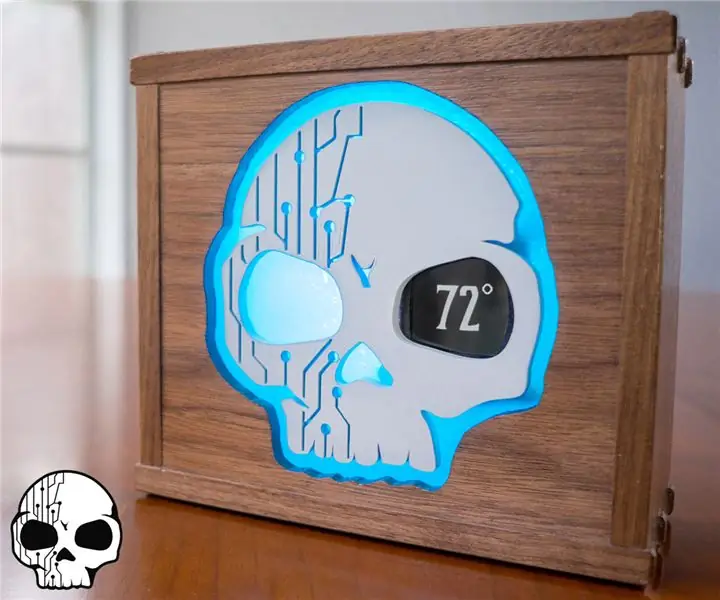
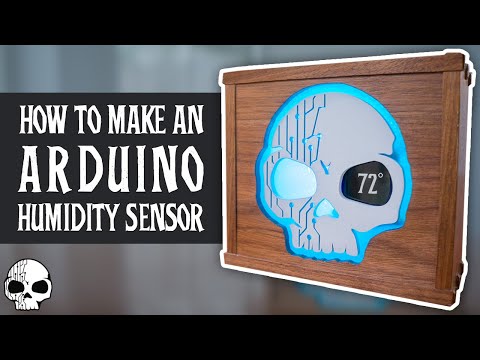
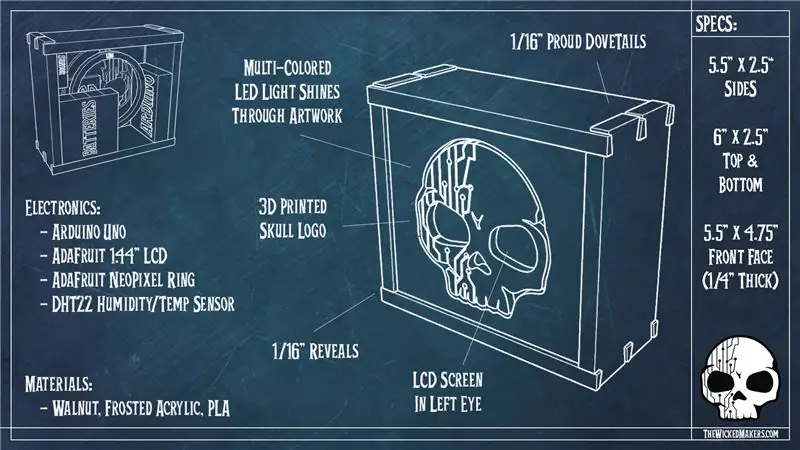
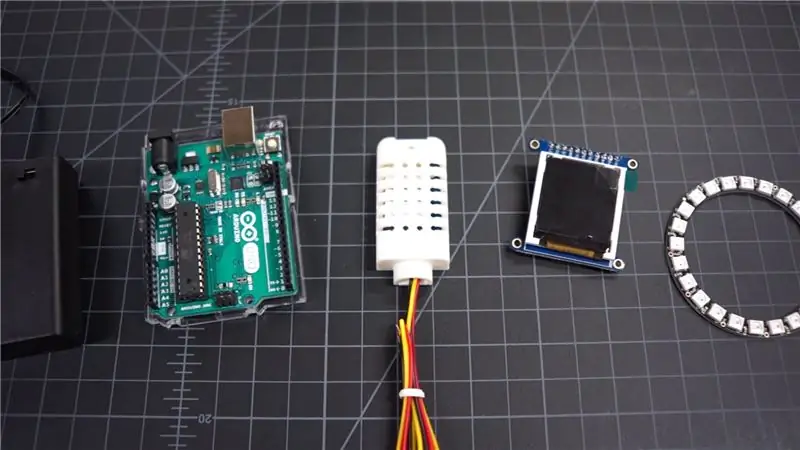
Wir leben in Zentral-Texas und die meiste Zeit des Jahres schwankt die Luftfeuchtigkeit in unserem Geschäft massiv. Als Holzarbeiter kann dies bei bestimmten Projekten schwierig sein, daher haben wir einen Arduino-betriebenen "Shop-Sensor" gebaut, um uns eine optisch ansprechende Möglichkeit zu geben, zu sehen, wie sich die Luftfeuchtigkeit ändert! Es besteht aus Walnussholz und hat eine Schwalbenschwanzverbindung. Wenn sich die Luftfeuchtigkeit ändert, verschiebt sich die Farbe der Beleuchtung über das Farbspektrum. Es hat auch einen LCD-Bildschirm in einem der Augen, der die Temperatur im Raum anzeigt.
Eine unserer Lieblingsbeschäftigungen ist die Kombination von feiner Holzbearbeitung mit Technologie und dies war ein wirklich lustiges Projekt, bei dem wir genau das gemacht haben.
Dieses Projekt hat etwas Holzbearbeitung, etwas Elektronik und etwas 3D-Druck.
Warum spielt Feuchtigkeit bei der Holzbearbeitung eine Rolle?
Die einfache Antwort ist, dass Holz auf Veränderungen des Feuchtigkeitsgehalts der Luft reagiert, indem es sich ausdehnt und zusammenzieht. Selbst nach dem vollständigen Trocknen und sogar mit dem Finish "bewegt sich" fast alles Holz weiter. Dies kann Gelenke auseinanderziehen, Schubladen nicht passen und andere unangenehme Dinge. Um mehr über dieses Phänomen zu erfahren, empfehlen wir eine Google-Suche!
VERWENDETE KOMPONENTEN:
- Arduino Uno
- Adafruit Neopixel-Ring
- Adafruit 1,44" LCD-Bildschirm
- DHT22 Feuchtigkeitssensor
- 4x AA-Batteriepack
- Mini-SD-Karte
BENUTZTES WERKZEUG:
- 3D Drucker
- Router
- Allzweckmesser
- Datei
- Klemmen
- Lötkolben
- Lot
- Heißklebepistole
- Maßband
- Bleistift
- Meißel
- Markierungslehre
- Hobel (nicht erforderlich)
- Jointer (nicht erforderlich)
- Bandsäge (nicht erforderlich)
- Tischkreissäge (nicht erforderlich)
- Drehwerkzeug / Dremel (nicht erforderlich)
- Bohrmaschine (nicht erforderlich)
MATERIALIEN:
- Walnuss (Holzetui)
- Frostic Acryl (Lichtdiffusor)
- PLA (3D gedrucktes Totenkopf-Logo)
- Holzkleber
- Sekundenkleber
- Heißkleber
- Blaues Malerband
- Doppelseitiges Klebeband
- Schellack
Schritt 1: Der Fall: das Holz
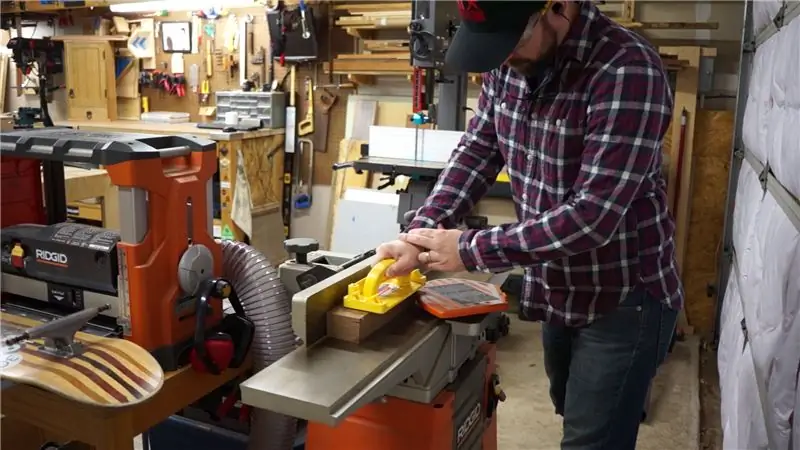
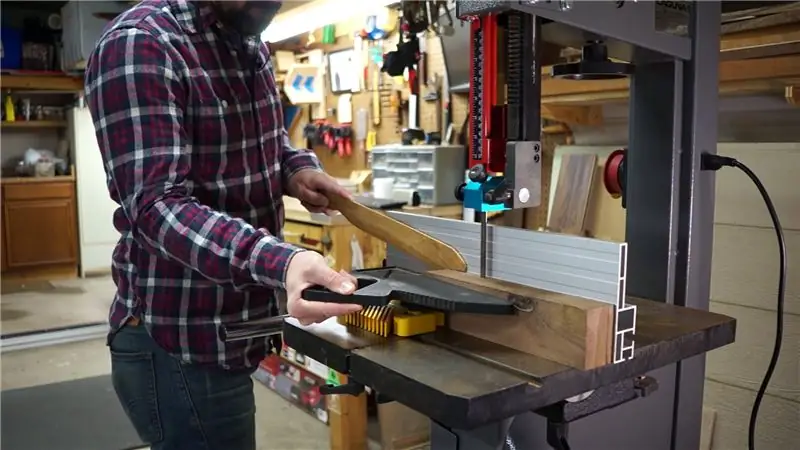
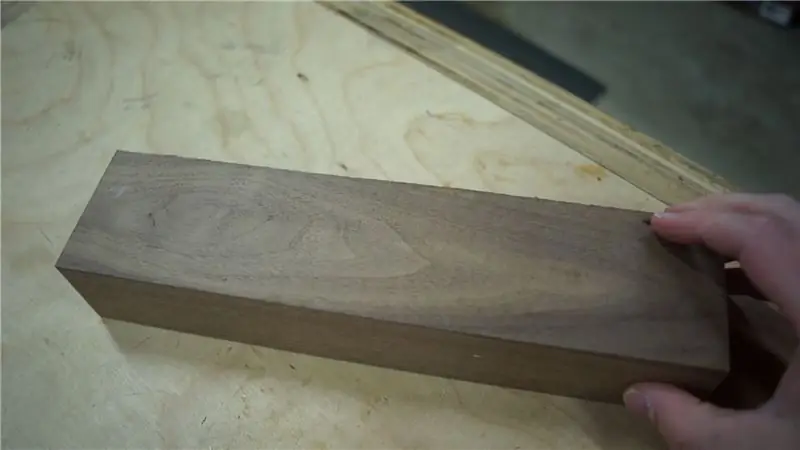
Um das Gehäuse zu bauen, haben wir Walnussholz verwendet, das dunkelbraun / graues Hartholz ist. Warum Walnuss? Es ist einfach, damit zu arbeiten, wir hatten einige und es sieht im Allgemeinen großartig aus … was es zu einer großartigen Wahl für diese Aufgabe macht! Müssen Sie Walnuss verwenden? Nein! Dafür können Sie jede Holzart verwenden.
Der Fräsprozess für die Walnuss bestand zuerst darin, sie auf der Abrichtmaschine zu glätten und zu begradigen, einige kleinere 3/8 dicke Stücke auf der Bandsäge nachzusägen und sie dann mit dem Dickenhobel auf die endgültige Dicke zu hobeln.
Sie haben keine eigenen Fräswerkzeuge? Kein Problem! Sie können Holz kaufen, das bereits die gewünschte Dicke hat, und diesen ersten Teil überspringen
Mit der Walnuss flach, gerade und auf unsere endgültige Dicke gefräst, haben wir sie auf der Tischsäge auf die endgültige Breite gerissen und dann auf die endgültige Länge geschnitten.
Das Ergebnis dieses Prozesses waren vier Teile, die alle perfekt flach, gerade und genau die Größe hatten, die wir wollten. Da wir Schwalbenschwänze schneiden, wird es später viel einfacher sein, perfekt dimensionierte Stücke zu haben. Wenn die Teile nicht die gleiche Größe haben oder nicht quadratisch sind, passen die Schwalbenschwänze nicht gut zusammen.
Schritt 2: Der Fall: die Schwalbenschwänze
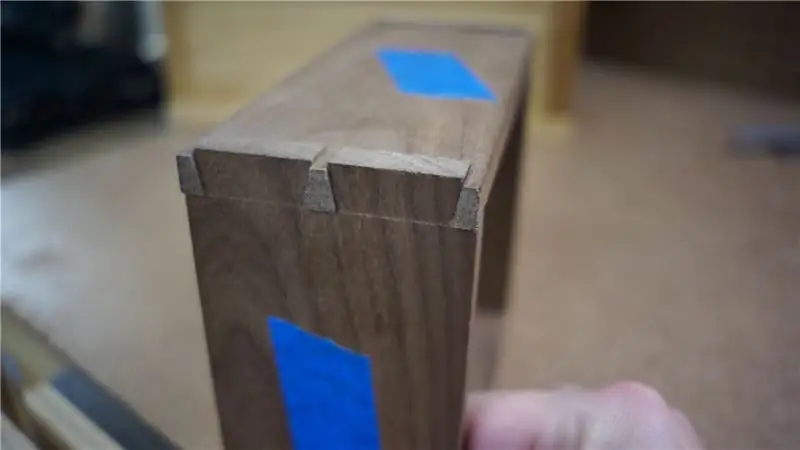
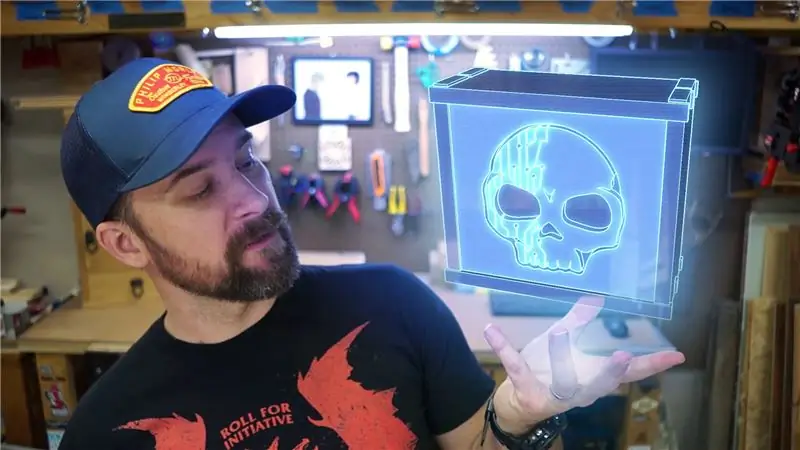
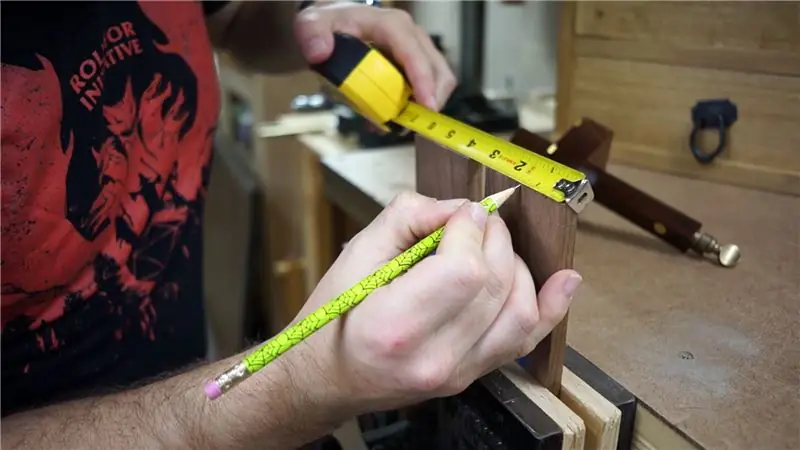
Wie in den Bildern und im Video gezeigt, ist ein Schwalbenschwanz eine Verbindung, bei der zwei Teile durch einen schwalbenschwanzförmigen Zapfen, bekannt als "Schwanz", der in eine Nut zwischen zwei "Stiften" passt, zusammengefügt werden. Es ist ein herausfordernder und unterhaltsamer Joint. Außerdem sehen sie FANTASTISCH aus.
Sie müssen dafür keine Schwalbenschwänze verwenden…aber…fordern Sie sich selbst heraus…versuchen Sie es
Wir begannen damit, die Größe und Position unserer Pins und Tails auf den Boards auszumessen. Wir verwenden dann eine Lehre auf der Tischkreissäge, um unsere Schnitte zu machen.
(Die von uns verwendete Schablone stammt aus dem Fine Woodworking Magazine und ist wirklich einfach herzustellen. Auf YouTube gibt es ein fantastisches Video, das Ihnen zeigt, wie man es macht. Sie finden es, indem Sie auf YouTube nach "Tischsägen-Schwalbenschwänze" suchen.)
Bei der ersten Vorrichtung ist das Tischsägeblatt um etwa 10 Grad abgewinkelt, um die Schwänze zu schneiden, und dann hat die zweite Vorrichtung das Sägeblatt auf 90 Grad zurückgedreht, aber das Werkstück im gleichen Winkel wie zuvor angewinkelt und den Abfall entfernt. Dafür verwenden wir ein Flat-Top-Rip-Blatt und wenn wir es richtig machen, sollte dieses direkt von der Tischkreissäge passen…..
Nun… das taten sie nicht.:)
Wir mussten einige Anpassungen mit einem Meißel vornehmen und einige Schrottstücke geschickt einsetzen, um die Probleme zu verbergen, aber am Ende waren sie großartig.
Sie können mehr Details zu diesem Teil im Video in Schritt 1 sehen
Schritt 3: Der Fall: Montage
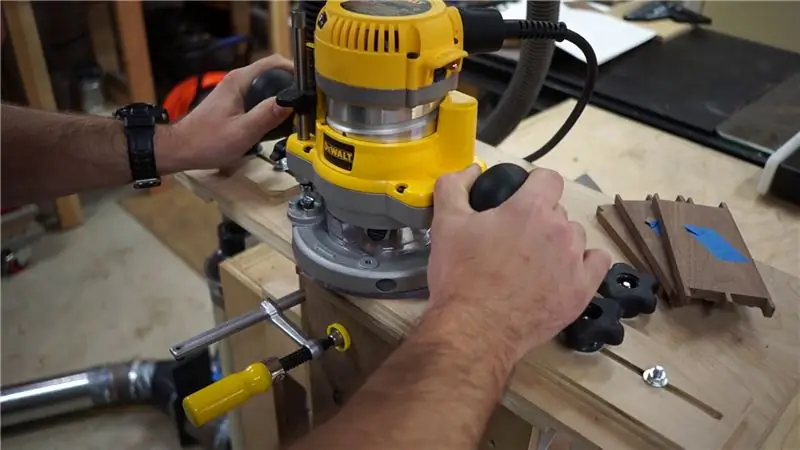
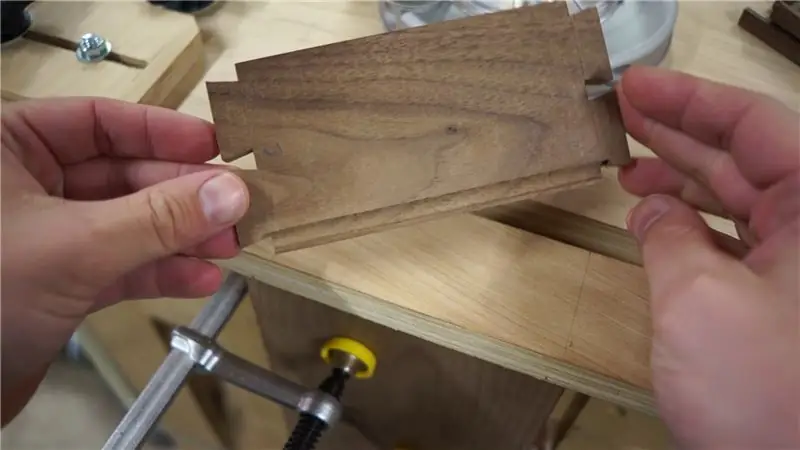
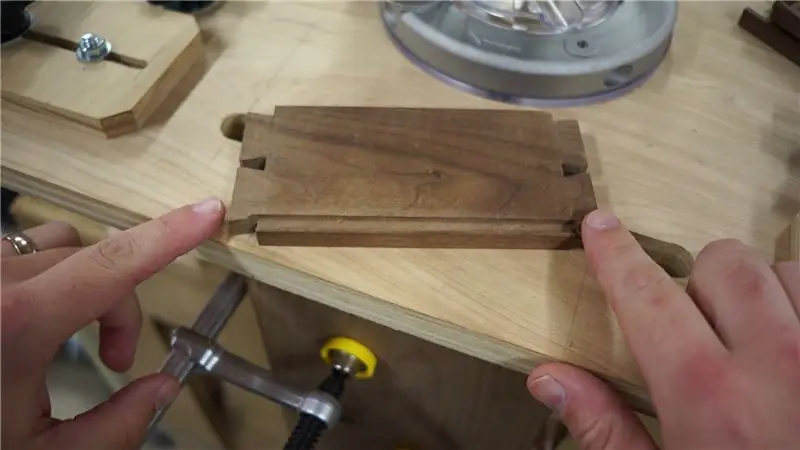
Das Gehäuse hat eine offene Rückseite und die Vorderseite sitzt schön in einer 1/8" tiefen "gestoppten" Rille. Um die Rille zu schneiden, haben wir einen Router verwendet.
Es wird als "gestoppter" Groove bezeichnet, weil er nicht von einem Ende zum anderen geht. Es beginnt auf halbem Weg und endet kurz vor dem Rand. (Siehe Bilder.)
Wenn die Nut in diesem Fall bis zum Ende gegangen wäre, wäre sie durch die Schwalbenschwänze gestochen und Sie würden sie deutlich sehen. Da wir das nicht wollten, haben wir einen Stopped Groove verwendet.
Die Oberseite wurde aus etwa 1/4 dicker Walnuss hergestellt und auf die richtige Größe gerippt und quergeschnitten. Von dort aus haben wir unseren ersten Dry Fit gemacht und alles sah gut aus!
Schritt 4: Der Schädel
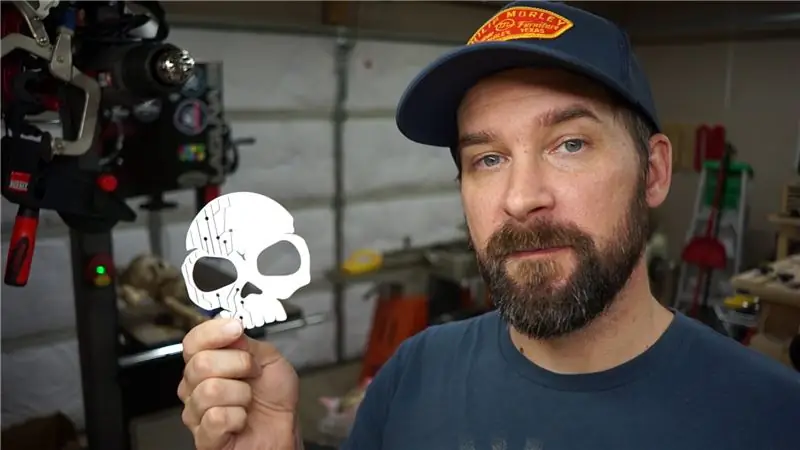
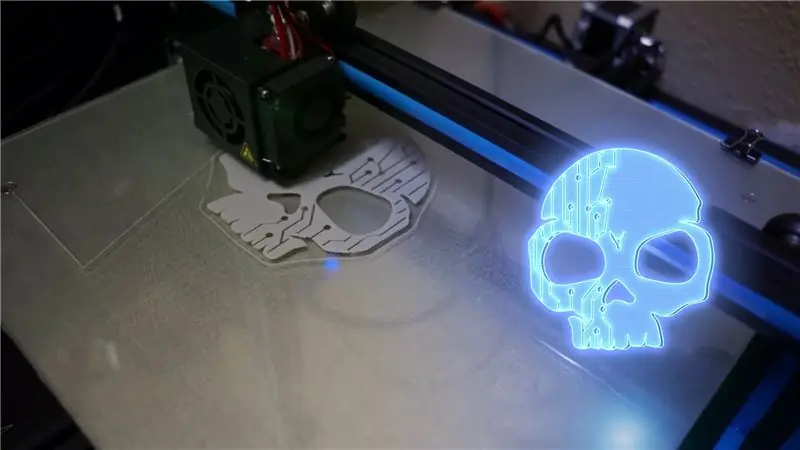
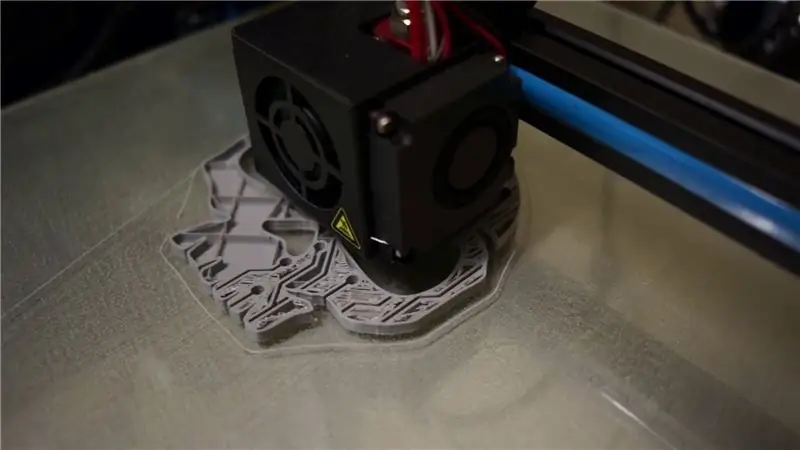
Die Idee für die Vorderseite des Gehäuses war, einen Ausschnitt in Form unseres Logos zu haben und das Licht von hinten durchscheinen zu lassen. Zuerst haben wir versucht, das Totenkopf-Logo aus einem Stück Holz zu fräsen, aber… es war eine Katastrophe. Also haben wir uns entschieden, den Schädel in 3D zu drucken und weiß zu malen, was großartig geworden ist!
Wir haben auch einen Umriss in 3D gedruckt, der etwas größer als der Schädel ist, haben ihn mit doppelseitigem Klebeband an der Vorderseite befestigt und dann mit einem scharfen Messer den Umriss in das Holz gezeichnet. Mit der scharfen und definierten „Messerlinie“haben wir dann mit der Oberfräse den Abfall in der Mitte weggeräumt. Wir haben ein gerades 1/16-Zoll-Router-Bit verwendet und sind unglaublich langsam, um bis zur Linie zu routen.
Für das letzte Detail haben wir eine kleine Handfeile verwendet und alle Werkzeugspuren oder fehlenden Stellen entfernt.
Von dort aus haben wir das Holzgehäuse verleimt und nach dem Trocknen des Leims die Schwalbenschwänze und Kanten des Gehäuses mit einem Meißel und einem Hobel abgeschrägt.
Schritt 5: Der Lichtdiffusor und das Schellack-Finish
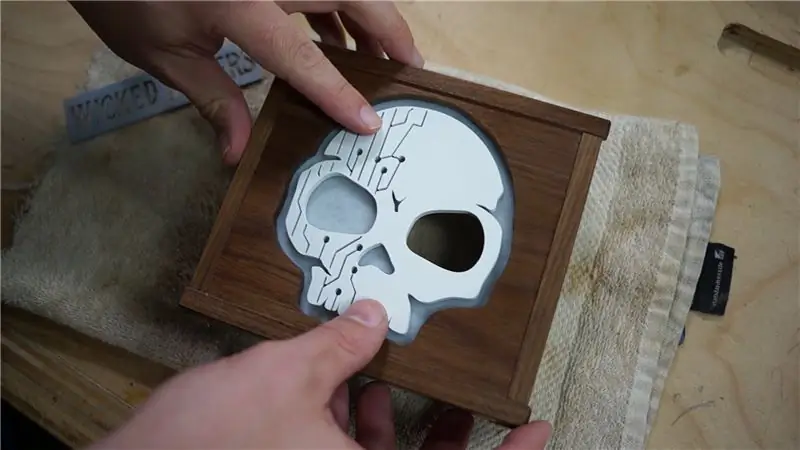
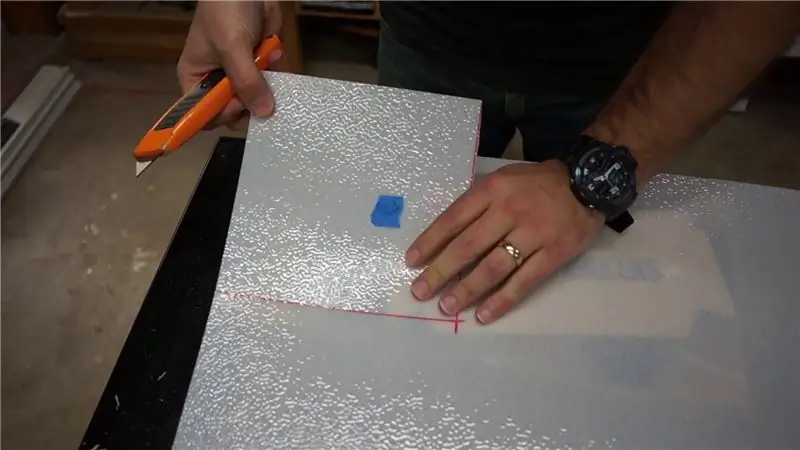
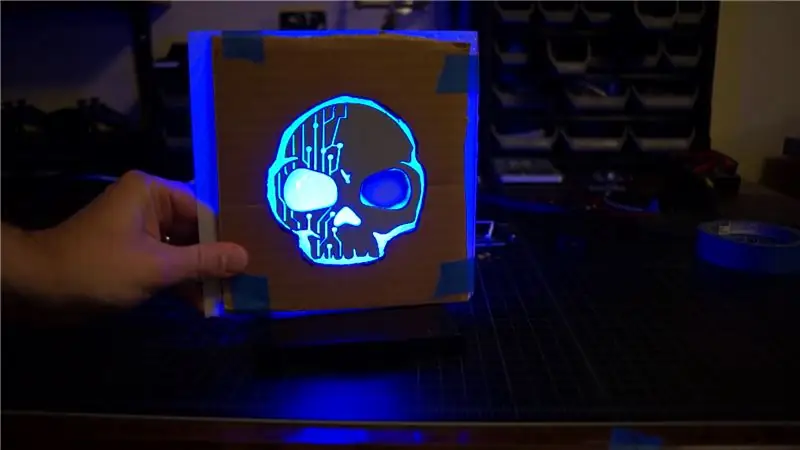
Hinter dem Schädel würde ein Stück mattweißes Plastik sein. Dies war hier, um das Licht dahinter zu "streuen", damit es sich besser ausbreitet und besser aussieht. Wir fanden ein kleines Stück Plastik im großen Kartonladen und schnitten ein Stück aus, das in unseren Koffer passt.
Wir haben zuerst einen Test gemacht, um sicherzustellen, dass es gut aussieht und alles großartig ist! Wir waren uns nicht 100% sicher, dass dieser Kunststoff das Licht richtig streuen würde, aber glücklicherweise tat er es.
Als nächstes benutzten wir etwas doppelseitiges Klebeband, um den 3D-Druck des Schädels vorübergehend an Ort und Stelle zu halten, damit wir die Positionierung des linken Auges erhalten konnten. Dies sollte durch einen LCD-Bildschirm ersetzt werden, also mussten wir den Kunststoff entfernen. Wir haben den zu entfernenden Bereich mit einem Marker markiert und dann den Abfall weggeräumt, indem wir das meiste davon auf der Bohrmaschine ausgebohrt und dann die Linie mit einer Schleiftrommel und einem Rotationswerkzeug gereinigt haben.
Vor dem Einkleben des mattierten Kunststoffs haben wir das Gehäuse mit Schellack veredelt. Wir haben 3 Schichten verwendet und dann mit Stahlwolle und Wachspaste poliert.
Wenn das Gehäuse innen und außen fertig ist, können wir Sekundenkleber verwenden, um den Kunststoff von innen zu befestigen.
Schritt 6: Die Elektronik
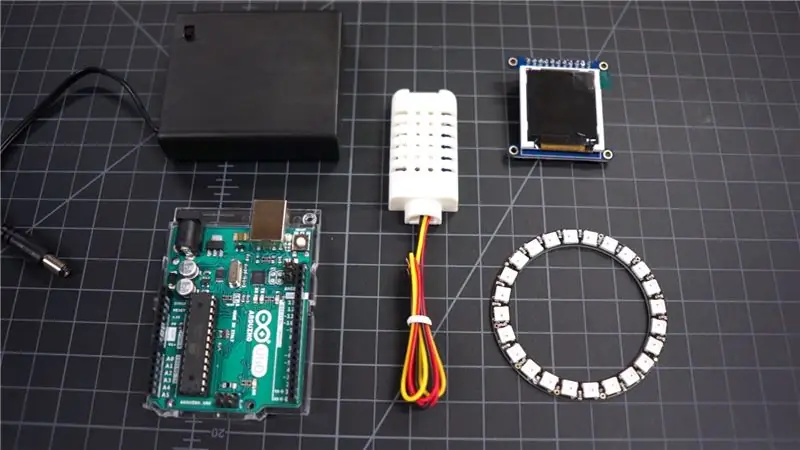
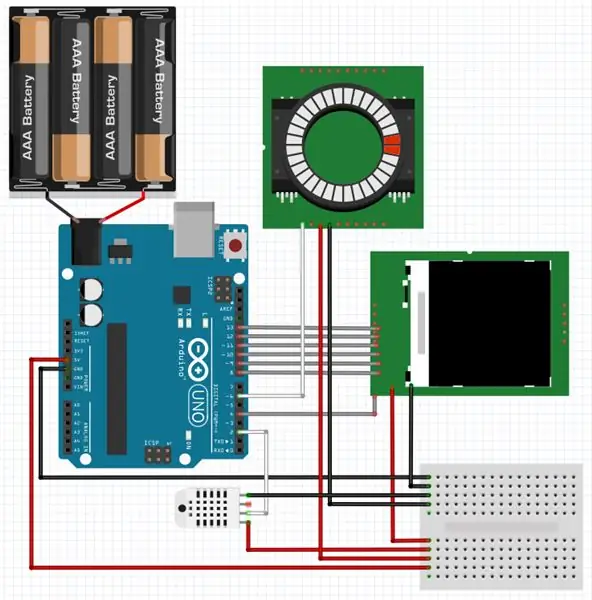
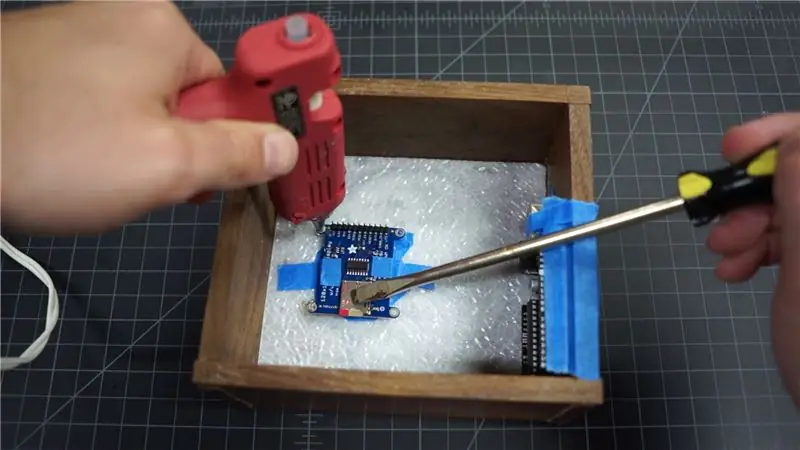
Die Komponenten, die wir installieren mussten, waren der Akku (4x AA), der Feuchtigkeits- und Temperatursensor, der LCD-Bildschirm, der Lichtring und natürlich das Arduino Uno. Wir haben viel Zeit damit verbracht, Prototypen zu erstellen, um zu sehen, wie das alles funktionieren würde, und sobald wir alles funktionierten, mussten wir herausfinden, wie alles in den Holzkoffer passt. Wir hatten einiges davon parallel gemacht, damit wir beim Bau des Gehäuses wussten, wie groß es ist.
Wir verwendeten blaues Klebeband, um die Position der Komponenten aufzurauen und sicherzustellen, dass sie passen würden, und verwendeten dann Heißkleber, um den LCD-Bildschirm und das Kunststoffgehäuse des Arduino an der Seite zu halten. Der Kunststoffkoffer/Halter ist hilfreich, da wir den Arduino bei Bedarf ein- und ausziehen können.
Der Neopixel-LED-Ring wurde auf den Akku geklebt, der Feuchtigkeitssensor wurde oben links auf das Holzgehäuse geklebt und dann wurde ein kleines Steckbrett auf die Unterseite des Holzgehäuses geklebt, das als Stromanschluss dienen sollte.
Das einzige Löten, das wir machen mussten, waren die Strom-, Dateneingangs- und Massekabel am Neopixel-Ring. Wir haben auch eine Heißluftpistole und einige Schrumpfschläuche verwendet, um die Drähte zu verwalten und an Ort und Stelle zu halten. Nach dem Löten haben wir den Akku auf das Holzgehäuse geklebt, was dazu führte, dass der Lichtring genau zentriert und genau dort war, wo er sein musste, um das Licht richtig zu verteilen. (Wenn es zu nah am Kunststoff ist, breitet es sich nicht so weit aus, da Sie einen Teil der Wirkung verlieren.)
Der Akku hat einen kleinen Ein- / Ausschalter, mit dem wir die Stromversorgung für das Projekt umschalten, damit wir darauf zugreifen können. Der Rucksack öffnet sich auch nach hinten, sodass wir die Batterien bei Bedarf austauschen können.
Von dort waren alle Komponenten für die Endverdrahtung bereit.
Die Programmierung des Arduino war relativ einfach. Es prüft die Temperatur und zeigt sie auf dem Bildschirm an. Es überprüft auch die Luftfeuchtigkeit und passt die Farbe der LEDs an, je nachdem, wie feucht es ist. Am feuchtesten ist es, wenn es lila ist, was 95% + Luftfeuchtigkeit bedeutet. Es ist viel zu oft lila…aber das ist für Sie das Zentrum von Texas!
Schritt 7: Die Ergebnisse
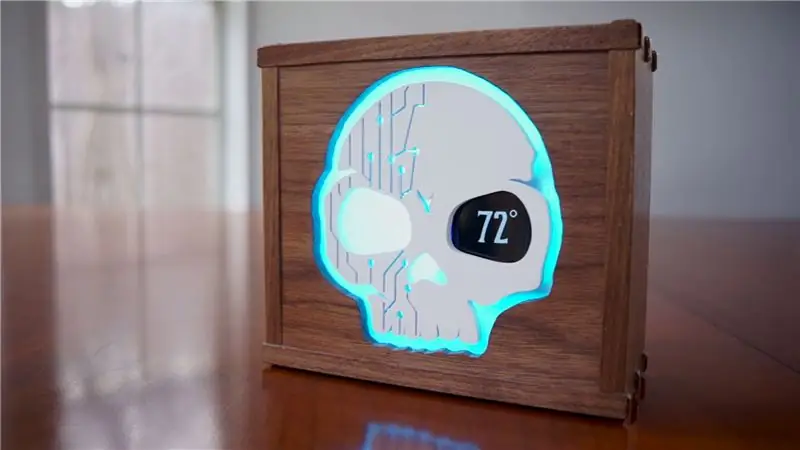
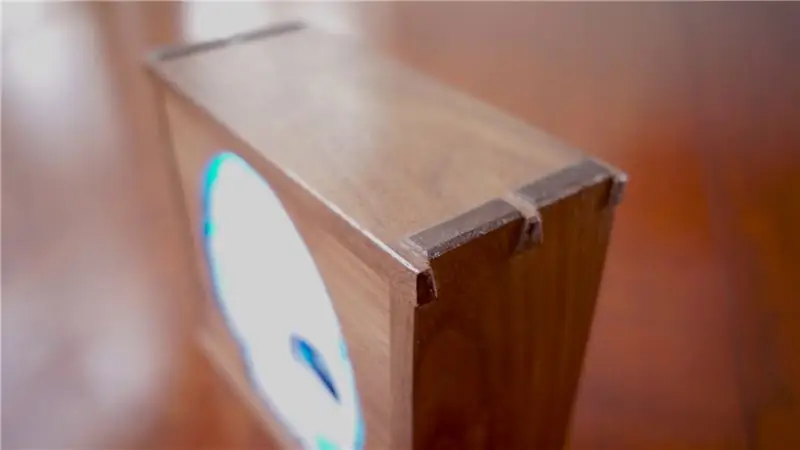
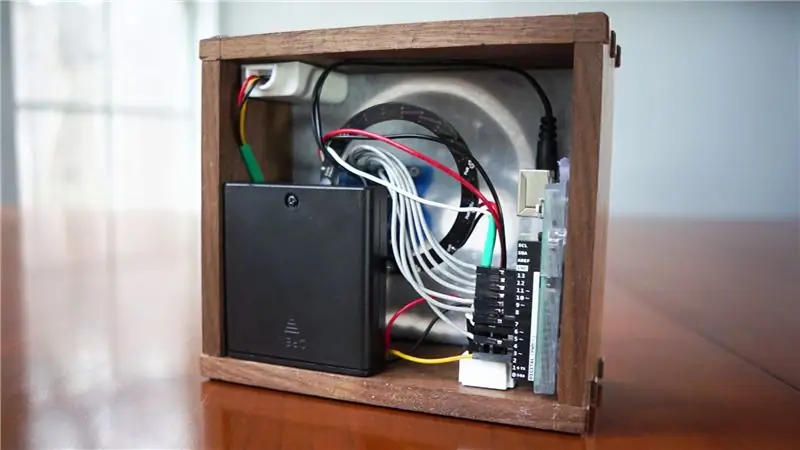
Wie Jaimie im Video erwähnt, hat dieses Projekt VIEL LÄNGER gedauert, als wir dachten, als wir es begannen. Aber es ist wirklich toll geworden. Es lebt jetzt in unserem Shop und lässt uns auf einen Blick wissen, wie feucht es im Shop ist.
Aus irgendeinem Grund LIEBEN wir es, feine Holzbearbeitung und Technologie zu mischen. Es macht einfach so viel Spaß.
Unser Favorit an diesem disziplinübergreifenden Projekt ist, dass es uns daran erinnert, dass wenn man Kreativität und Leidenschaft für die Herstellung großartiger Dinge kombiniert, es wirklich keine Grenzen gibt, was man erfinden und herstellen kann.
Jetzt … mach was!