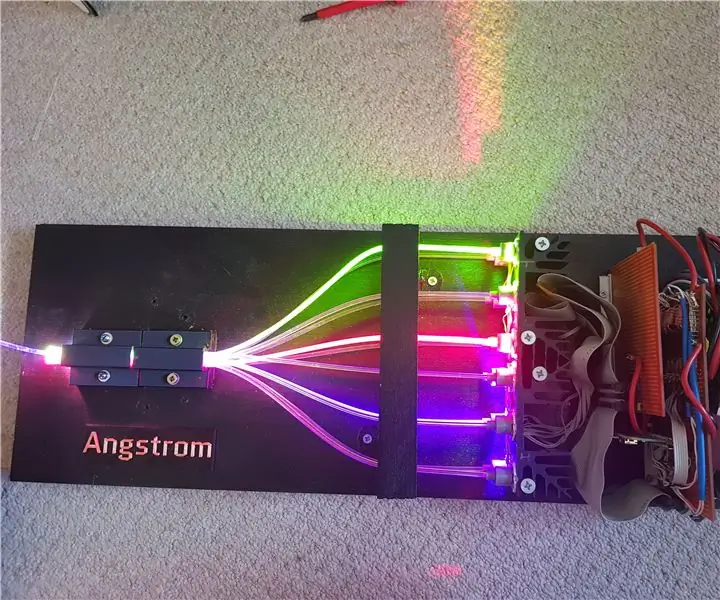
Inhaltsverzeichnis:
- Schritt 1: Erforderliche Teile - Baseboard, Stromversorgung, Controller und LED-Baugruppe
- Schritt 2: Erforderliche Teile: LEDs
- Schritt 3: Erforderliche Teile: LED-Steuerschaltung
- Schritt 4: Erforderliche Teile: Glasfaser und Combiner
- Schritt 5: Erforderliche Teile: 3D-gedruckte Teile
- Schritt 6: Zusammenbau der Hauptsteuerplatine
- Schritt 7: Die Leistungs-MOSFETs
- Schritt 8: LEDs und Kühlkörper
- Schritt 9: LED-Verkabelung
- Schritt 10: Testen der Controllerplatine
- Schritt 11: Glasfaserkopplung der LEDs
- Schritt 12: Konfigurieren des Raspberry Pi
- Schritt 13: Der Faserkombinierer
- Schritt 14: Die einzelne Faserausgangskopplerplatte
- Schritt 15: Mehr Leistung!. Mehr Wellenlängen
2025 Autor: John Day | [email protected]. Zuletzt bearbeitet: 2025-06-01 06:08
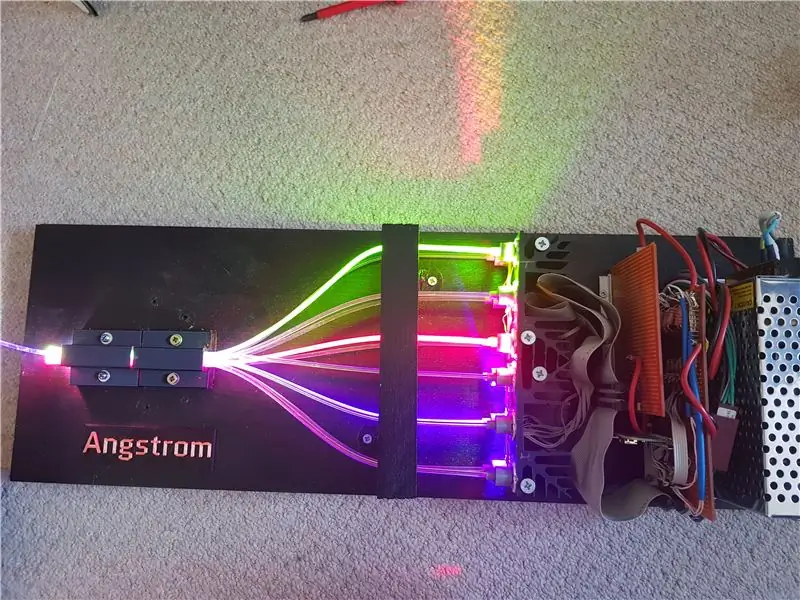
Angstrom ist eine abstimmbare 12-Kanal-LED-Lichtquelle, die für unter £100 gebaut werden kann. Es verfügt über 12 PWM-gesteuerte LED-Kanäle mit einer Spannweite von 390 nm bis 780 nm und bietet sowohl die Möglichkeit, mehrere Kanäle zu einem einzigen fasergekoppelten 6-mm-Ausgang zu mischen, als auch die Möglichkeit, einen oder alle Kanäle gleichzeitig auf einzelne 3-mm-Faserausgänge auszugeben.
Zu den Anwendungen gehören Mikroskopie, Forensik, Farbmetrik, Dokumentenscannen usw. Sie können das Spektrum verschiedener Lichtquellen wie Kompaktleuchtstofflampen (CFL) einfach simulieren.
Zusätzlich könnten die Lichtquellen für interessante theatralische Lichteffekte genutzt werden. Die Stromkanäle sind mehr als in der Lage, zusätzliche LEDs mit einer höheren Nennstromversorgung zu handhaben, und die mehreren Wellenlängen erzeugen einen schönen und einzigartigen mehrfarbigen Schatteneffekt, den normale weiße oder RGB-LED-Quellen nicht duplizieren können. Es ist ein ganzer Regenbogen in einer Box!.
Schritt 1: Erforderliche Teile - Baseboard, Stromversorgung, Controller und LED-Baugruppe
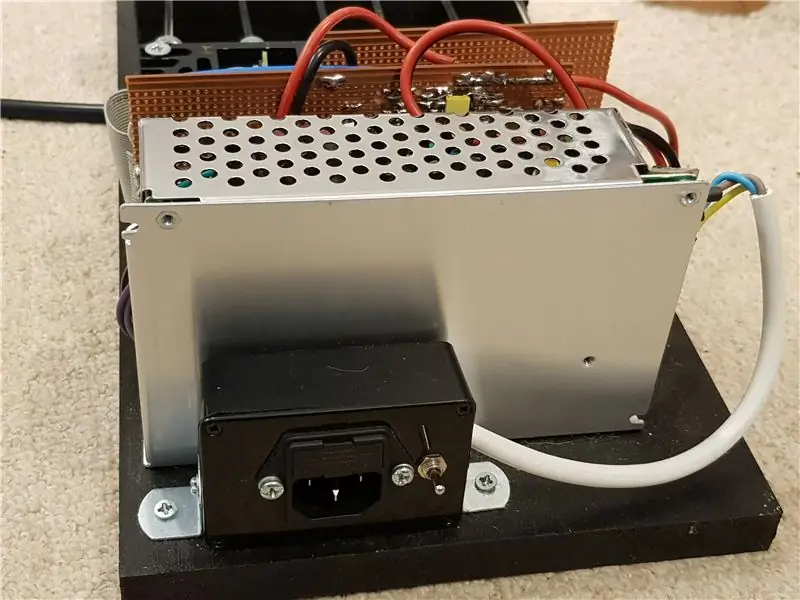
Sockelleiste: Das Gerät ist auf einem Holzsockel montiert, ca. 600 mm x 200 mm x 20 mm. Zusätzlich wird ein spannungsabbauender Holzblock 180 mm x 60 mm x 20 mm verwendet, um die Lichtwellenleiter auszurichten.
Ein 5V 60W Netzteil wird über einen abgesicherten Kaltgerätestecker mit 700mA Sicherung an das Stromnetz angeschlossen und als Hauptschalter wird ein kleiner Kippschalter mit einer Nennleistung von mindestens 1A 240V verwendet.
Die Hauptplatine besteht aus einer standardmäßigen phenolisch kupferplattierten Leiterplatte mit einem Rastermaß von 0,1 Zoll. Im Prototyp misst diese Platine ungefähr 130 mm x 100 mm. Der Prototyp wurde mit einer optionalen zweiten Platine von ca. 100 mm x 100 mm ausgestattet, die jedoch nur für zusätzliche Schaltungen wie Signalverarbeitungslogik für die Spektroskopie usw. dient und für die Basiseinheit nicht erforderlich ist.
Die Haupt-LED-Baugruppe besteht aus 12 3-W-Stern-LEDs mit jeweils einer anderen Wellenlänge. Diese werden im Abschnitt über die LED-Baugruppe weiter unten näher erläutert.
Die LEDs sind auf zwei Aluminium-Kühlkörpern montiert, die im Prototyp 85 mm x 50 mm x 35 mm tief waren.
Zur Steuerung wird ein Raspberry Pi Zero W verwendet. Es ist mit einem Header ausgestattet und wird in eine passende 40-polige Buchse auf der Hauptplatine gesteckt.
Schritt 2: Erforderliche Teile: LEDs
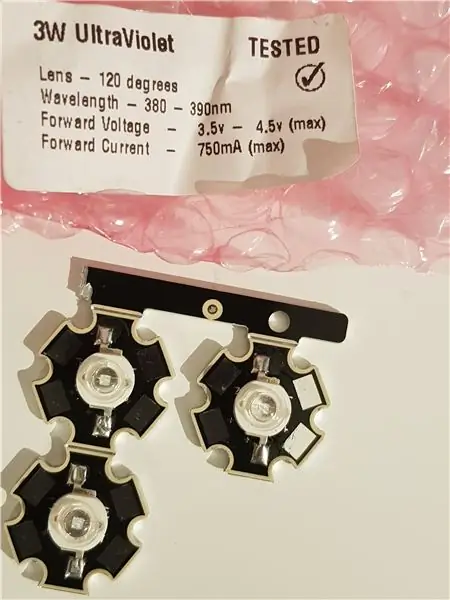
Die 12 LEDs haben die folgenden Mittenwellenlängen. Es handelt sich um 3W-Stern-LEDs mit einem 20-mm-Kühlkörpersockel.
390nm410nm 440nm460nm500nm520nm560nm580nm590nm630nm660nm780nm
Alle bis auf die 560-nm-Einheit wurden von FutureEden bezogen. Die 560-nm-Einheit wurde von eBay bezogen, da FutureEden kein Gerät hat, das diese Wellenlänge abdeckt. Beachten Sie, dass dieses Gerät aus China versendet wird, also planen Sie die Lieferzeit ein.
Die LEDs werden mit Akasa-Wärmeleitband am Kühlkörper befestigt. Schneiden Sie 20-mm-Quadrate und kleben Sie dann einfach eine Seite auf die LED und die andere auf den Kühlkörper. Befolgen Sie dabei die Anweisungen des Herstellers, welche Seite des Bandes zum LED-Kühlkörper führt.
Schritt 3: Erforderliche Teile: LED-Steuerschaltung
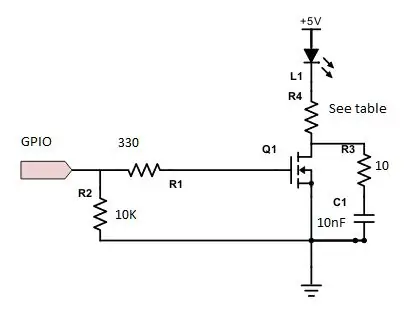
Jeder LED-Kanal wird von einem GPIO-Pin auf dem Raspberry Pi gesteuert. PWM wird verwendet, um die LED-Intensität zu steuern. Ein Leistungs-MOSFET (Infineon IPD060N03LG) treibt jede LED über einen 2-W-Leistungswiderstand an, um den LED-Strom zu begrenzen.
Die Werte von R4 für jedes Gerät und den gemessenen Strom sind unten aufgeführt. Der Widerstandswert ändert sich, weil der Spannungsabfall an den LEDs mit kürzerer Wellenlänge höher ist als bei LEDs mit längerer Wellenlänge. R4 ist ein 2W-Widerstand. Es wird während des Betriebs ziemlich warm. Achten Sie also darauf, die Widerstände frei von der Controllerplatine zu montieren und die Leitungen so lang zu halten, dass der Widerstandskörper mindestens 5 mm von der Platine entfernt ist.
Die Infineon-Geräte sind günstig bei eBay erhältlich und werden auch von Anbietern wie Mouser geführt. Sie haben eine Nennleistung von 30 V 50 A, was eine große Spanne ist, aber sie sind billig und einfach zu handhaben, da sie DPAK-Geräte sind und daher leicht von Hand löt werden können. Wenn Sie Geräte ersetzen möchten, stellen Sie sicher, dass Sie eines mit entsprechenden Stromreserven und einem Gate-Schwellenwert so auswählen, dass das Gerät bei 2-2,5 V vollständig eingeschaltet ist, da dies den vom Pi GPIO verfügbaren Logikpegeln (3,3 V max.) entspricht Stifte. Die Gate-/Source-Kapazität beträgt für diese Geräte 1700 pf und jeder Ersatz sollte ungefähr eine ähnliche Kapazität haben.
Das Snubber-Netzwerk über dem MOSFET (10nF Kondensator und 10 Ohm 1/4W Widerstand) dient zur Steuerung der Anstiegs- und Abfallzeiten. Ohne diese Komponenten und den 330-Ohm-Gate-Widerstand gab es Anzeichen für Nachschwingen und Überschwingen am Ausgang, was zu unerwünschten elektromagnetischen Störungen (EMI) hätte führen können.
Tabelle der Widerstandswerte für R4, den 2W-Leistungswiderstand
385nm 2,2 Ohm 560mA415nm 2,7 Ohm 520mA440nm 2,7 Ohm 550mA 460nm 2,7 Ohm 540mA 500nm 2,7 Ohm 590mA 525nm 3,3 Ohm 545mA 560nm 3,3 Ohm 550mA 590nm 630nm 3,9 Ohm 3,9 Ohm 610nm 5,60nm 3,9 Ohm 3,9Ohm 780nm 610nm 5,6
Schritt 4: Erforderliche Teile: Glasfaser und Combiner
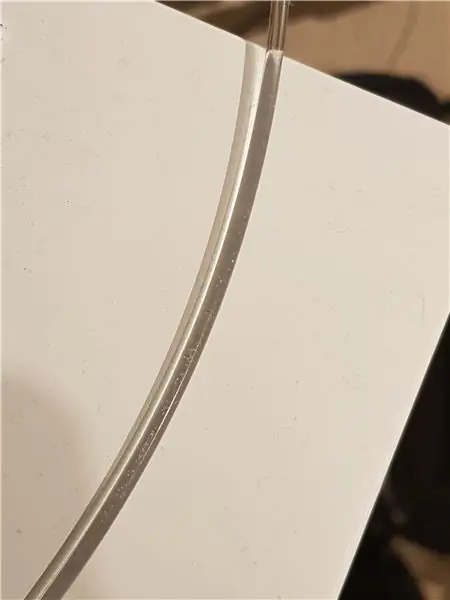
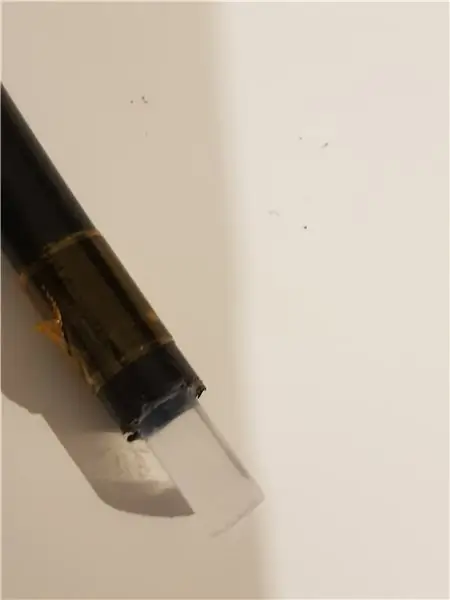
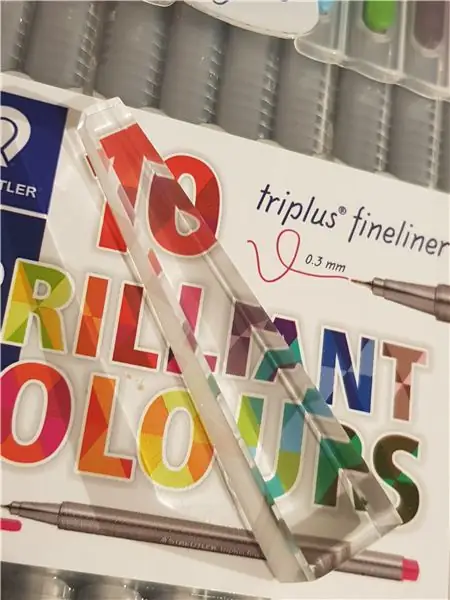
Die LEDs sind über 3mm Kunststofffaser an einen optischen Combiner gekoppelt. Dies ist von einer Reihe von Anbietern erhältlich, aber die billigeren Produkte können bei kurzen Wellenlängen eine übermäßige Dämpfung aufweisen. Ich kaufte einige Glasfasern bei eBay, die ausgezeichnet waren, aber einige billigere Glasfasern bei Amazon, die eine signifikante Dämpfung bei etwa 420 nm und darunter aufwiesen. Die Faser, die ich bei eBay gekauft habe, stammte aus dieser Quelle. 10 Meter sollten ausreichen. Sie benötigen nur 4 Meter, um die LEDs mit einer Länge von 12 x 300 mm zu koppeln, aber eine der Optionen beim Bau dieses Geräts besteht darin, auch einzelne Wellenlängen an eine 3 mm-Ausgangsfaser auszukoppeln, so dass es praktisch ist, zusätzliche für diese Option zu haben.
www.ebay.co.uk/itm/Glasfaserkabel-0-25-…
Die Ausgangsfaser ist eine flexible 6-mm-Faser, die von einem robusten Außenmantel aus Kunststoff umgeben ist. Es ist ab hier erhältlich. In den meisten Fällen wird wahrscheinlich eine Länge von 1 Meter ausreichen.
www.starscape.co.uk/optical-fibre.php
Der optische Kombinator ist ein sich verjüngender Kunststoff-Lichtleiter, der aus einem Stück 15 x 15 mm Vierkantstab hergestellt, auf ca. 73 mm geschnitten und abgeschliffen wird, so dass das Ausgangsende des Leiters 6 mm x 6 mm beträgt.
Beachten Sie auch hier, dass einige Acrylsorten bei kurzen Wellenlängen eine übermäßige Dämpfung aufweisen können. Leider ist es schwer zu bestimmen, was Sie bekommen werden, aber Rute aus dieser Quelle hat gut funktioniert
www.ebay.co.uk/itm/SQUARE-CLEAR-ACRYLIC-RO…
Der Stab dieser Quelle hatte jedoch eine übermäßige Dämpfung und war für 390 nm UV-Licht fast vollständig undurchlässig.
www.ebay.co.uk/itm/Acrylic-Clear-Solid-Squ…
Schritt 5: Erforderliche Teile: 3D-gedruckte Teile
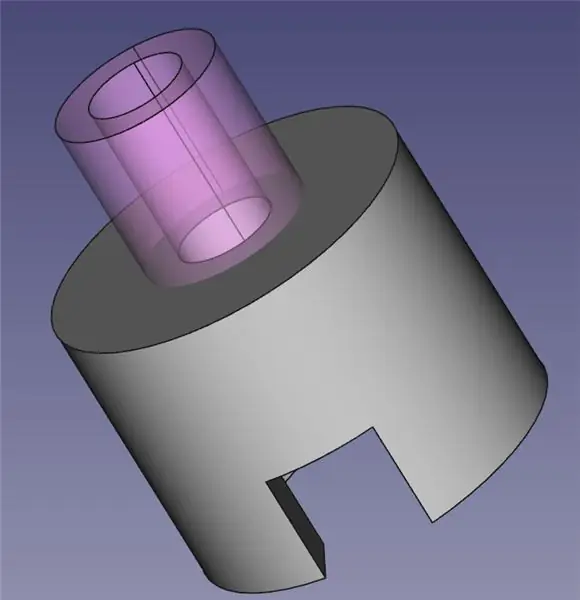
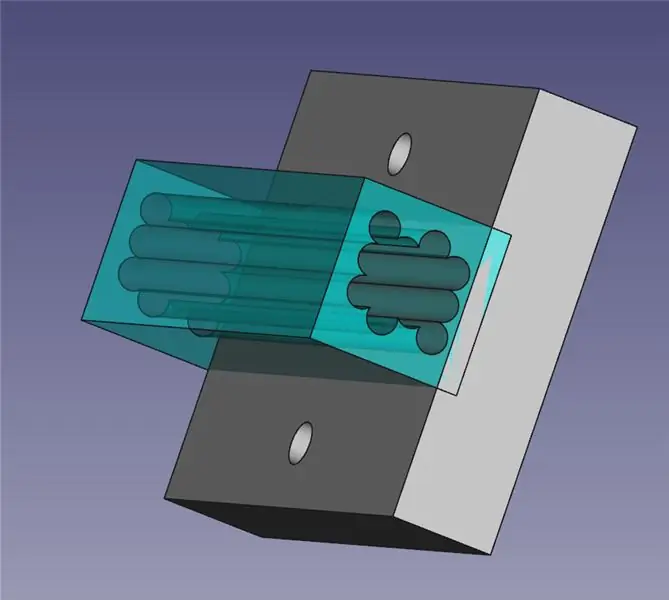
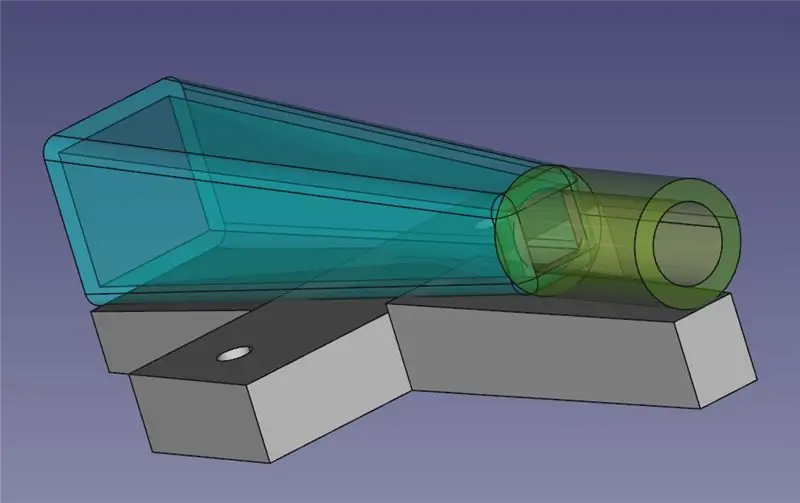
Einige Teile sind 3D gedruckt. Sie sind
Die LED-Faseradapter
Die Fasermontageplatte
Der (optionale) Glasfaser-Ausgangsadapter (für einzelne Ausgänge). Dies ist nur die neu bedruckte Fasermontageplatte.
Die Optokoppler-Montageplatte
Alle Teile sind in Standard-PLA gedruckt, mit Ausnahme der Faseradapter. Ich empfehle PETG für diese, da PLA zu sehr weich wird; Die LEDs werden ziemlich warm.
Alle STLs für diese Teile sind in den angehängten Dateien für das Projekt enthalten. Sehen Sie sich den Schritt zum Konfigurieren des Raspberry Pi für die ZIP-Datei an, die alle Projektressourcen enthält.
Drucken Sie die Faseradapter für die LEDs mit 100 % Füllung. Die anderen können mit 20% Füllung bedruckt werden.
Alle Teile wurden mit einer Schichthöhe von 0,15 mm unter Verwendung einer Standard-Düse von 0,4 mm mit 60 mm/s auf einem Creality Ender 3 und auch einem Biqu Magician gedruckt. Jeder kostengünstige 3D-Drucker sollte die Arbeit erledigen.
Die Teile sollten alle vertikal mit den Löchern nach oben gedruckt werden - dies gibt die beste Präzision. Sie können Stützen für sie überspringen; dadurch sieht die Hauptkupplungs-Montageplatte an der Hinterkante etwas zerlumpt aus, aber das ist nur kosmetisch; ein Hauch von Schleifpapier wird es aufräumen.
Wichtig: Drucken Sie die Fasermontageplatte (und die optionale zweite Kopie davon für den einzelnen Faserausgangsadapter) im Maßstab 1,05, d. h. 5 % vergrößert. Dadurch wird sichergestellt, dass die Löcher für die Faser genügend Freiraum haben.
Schritt 6: Zusammenbau der Hauptsteuerplatine
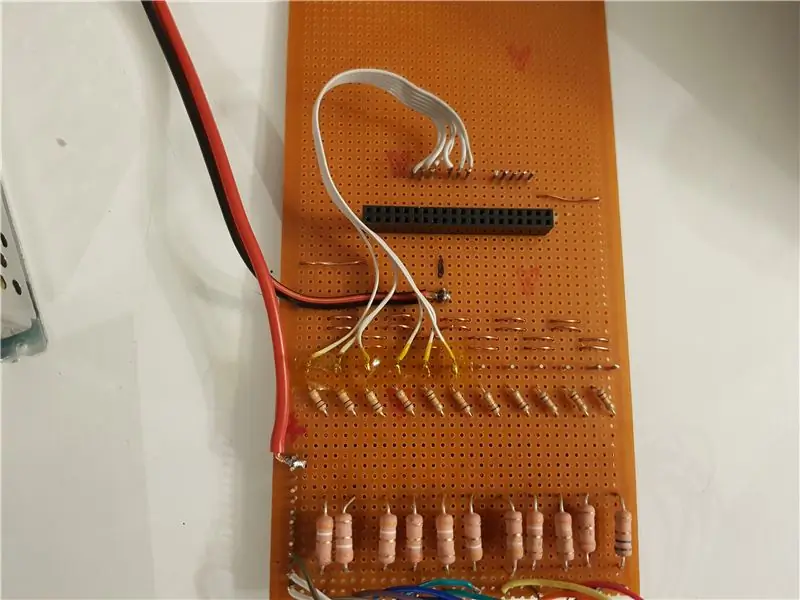
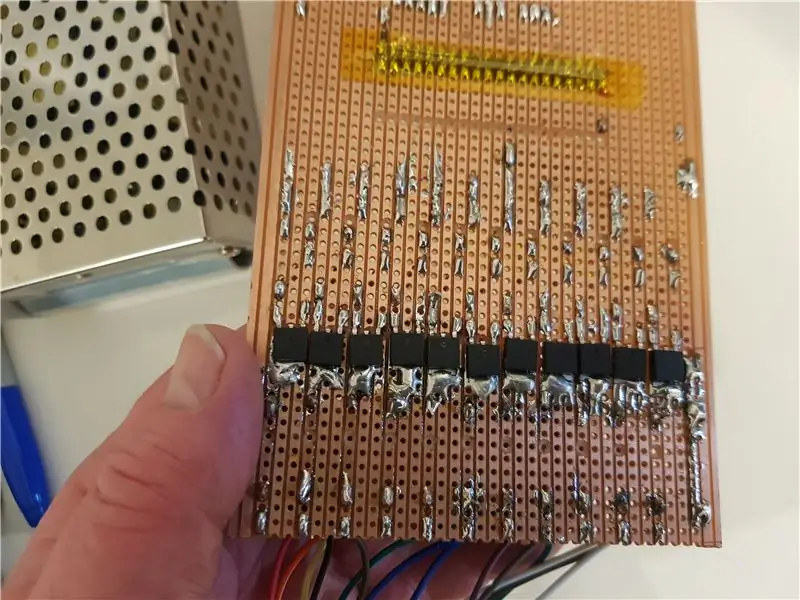
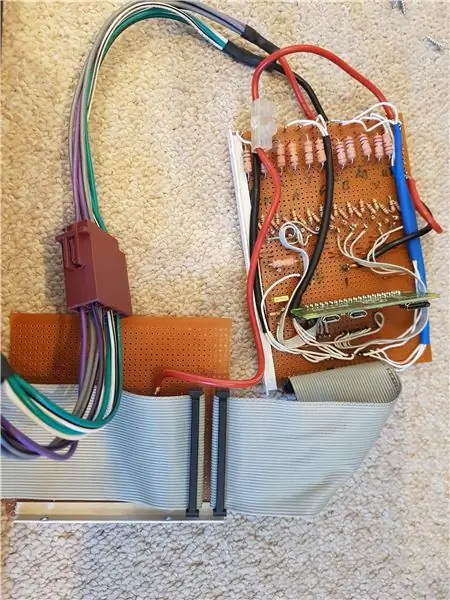
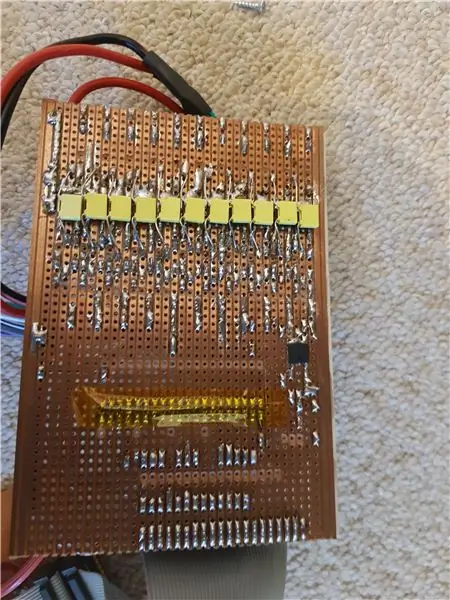
Die Controller-Platine wird aus Standard-Kupfer-Stripboard (manchmal auch als Veroboard bekannt) hergestellt. Ich füge kein detailliertes Layout bei, da das Board-Design, das ich am Ende hatte, etwas unordentlich wurde, weil ich Komponenten wie das Snubber-Netzwerk hinzufügen musste, die ich ursprünglich nicht geplant hatte. Auf der Oberseite der Platine, oben teilweise aufgebaut, befinden sich die Leistungswiderstände und die Buchse für den Raspberry Pi. Ich habe einen rechtwinkligen Header für den Pi verwendet, damit er im rechten Winkel zur Hauptplatine sitzt, aber wenn Sie einen normalen geraden Header verwenden, sitzt er stattdessen einfach parallel zur Platine. Auf diese Weise nimmt es etwas mehr Platz ein, also planen Sie entsprechend.
Veropins wurden verwendet, um Drähte mit der Platine zu verbinden. Zum Schneiden von Gleisen ist ein kleiner Spiralbohrer sinnvoll. Verwenden Sie für den Pi-Sockel ein scharfes Cuttermesser, um die Spuren zu schneiden, da Sie kein Ersatzloch zwischen den beiden Sätzen von Sockelstiften haben.
Beachten Sie die Doppelreihe von 1 mm Kupferdraht. Dies dient dazu, einen niederohmigen Pfad für die fast 7 Ampere Strom bereitzustellen, die die LEDs bei voller Leistung verbrauchen. Diese Drähte gehen zu den Source-Anschlüssen der Leistungs-MOSFETs und von dort zu Masse.
Es gibt nur ein kleines 5V-Kabel auf dieser Platine, das den Pi mit Strom versorgt. Dies liegt daran, dass die 5V-Hauptstromversorgung zu den Anoden der LEDs geht, die in meinem Prototyp über ein Standard-PC-IDE-Festplattenkabel auf einer zweiten Platine angeschlossen sind. Sie müssen dies jedoch nicht tun und können sie einfach direkt an eine Buchse auf der ersten Platine anschließen. In diesem Fall führen Sie einen doppelten Satz Kupferdrähte entlang der Anodenseite, um den Strom auf der +5V-Seite zu handhaben. Im Prototyp befanden sich diese Drähte auf der zweiten Platine.
Schritt 7: Die Leistungs-MOSFETs
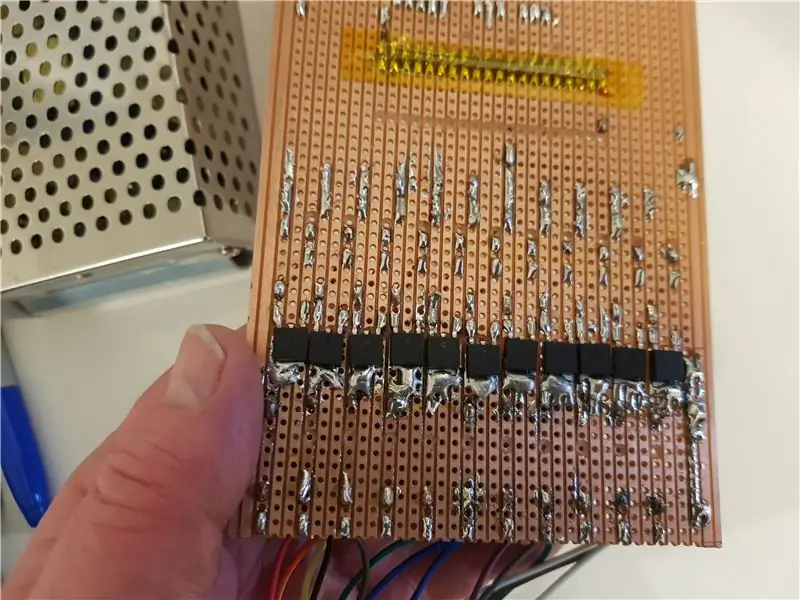
Die MOSFETs wurden auf der Kupferseite der Platine montiert. Da es sich um DPAK-Geräte handelt, muss die Lasche direkt auf die Platine gelötet werden. Verwenden Sie dazu eine entsprechend große Spitze des Lötkolbens und verzinnen Sie die Lasche schnell leicht. Verzinnen Sie die Kupferschienen, wo Sie das Gerät anbringen werden. Legen Sie es auf die Platine und erhitzen Sie den Tab wieder. Das Lot wird schmelzen und das Gerät wird befestigt. Versuchen Sie dies relativ schnell, um das Gerät nicht zu überhitzen. es verträgt mehrere Sekunden Hitze, also keine Panik. Sobald die Lasche (Drain) gelötet ist, können Sie die Gate- und Source-Leitungen an die Platine löten. Vergessen Sie nicht, zuerst die Spuren für die Gate- und Source-Leitungen zu schneiden, damit sie nicht mit der Drain-Lasche kurzgeschlossen werden!. Sie können auf dem Bild nicht sehen, aber die Schnitte befinden sich unter den Kabeln zum Gehäuse des Geräts.
Leser mit Adleraugen werden nur 11 MOSFETs bemerken. Dies liegt daran, dass der 12. später hinzugefügt wurde, als ich die 560-nm-LEDs bekam. Es passt aufgrund der Breite nicht auf das Board, wurde also woanders platziert.
Schritt 8: LEDs und Kühlkörper
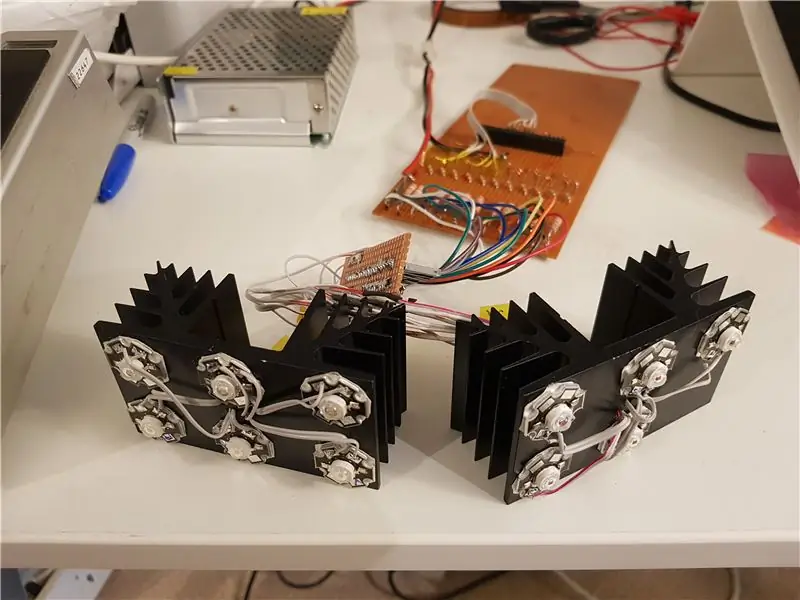
Hier ist eine Nahaufnahme der LEDs und Kühlkörper. Die Verkabelung der Controllerplatine stammte aus einer früheren Version des Prototyps, bevor ich auf die Verwendung eines IDE-Kabels umgestellt habe, um die LEDs mit dem Controller zu verbinden.
Wie bereits erwähnt, werden die LEDs mit Quadraten aus Akasa-Thermoband befestigt. Dies hat den Vorteil, dass bei Ausfall einer LED diese einfach mit einem scharfen Messer entfernt werden kann, um das Band zu durchschneiden.
Solange der Kühlkörper ausreichend groß ist, steht der Montage aller LEDs auf einem einzigen Kühlkörper nichts im Wege. Bei den gezeigten Kühlkörpern erreicht die Kühlkörpertemperatur bei voller Leistung 50 Grad C und daher sind diese Kühlkörper wahrscheinlich etwas kleiner als optimal. Im Nachhinein wäre es wahrscheinlich auch eine gute Idee gewesen, drei der längerwelligen LEDs auf jeden Kühlkörper zu setzen, anstatt alle sechs der kürzerwelligen Emitter auf einen und die längerwelligen Emitter auf den anderen zu setzen. Dies liegt daran, dass die kurzwelligen Emitter bei einem gegebenen Durchlassstrom aufgrund ihres höheren Durchlassspannungsabfalls mehr Leistung verbrauchen und daher wärmer werden.
Sie können natürlich eine Lüfterkühlung hinzufügen. Wenn Sie die LED-Baugruppe vollständig einschließen möchten, ist dies ratsam.
Schritt 9: LED-Verkabelung
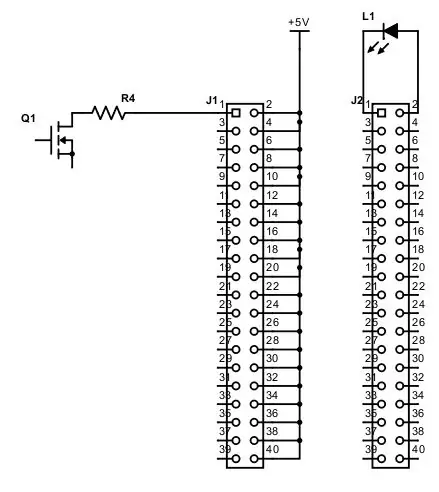
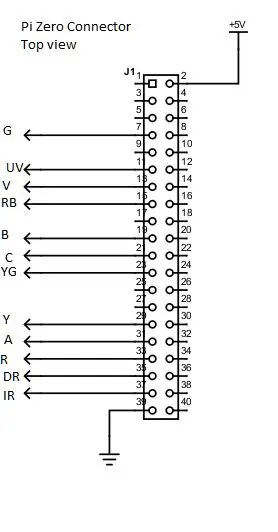
Die LEDs werden über ein standardmäßiges 40-Pin-IDE-Kabel mit dem Controller-Board verbunden. Es werden nicht alle Kabelpaare verwendet, sodass Raum für Erweiterungen bleibt.
Die obigen Schaltpläne zeigen die Verdrahtung des IDE-Anschlusses und auch die Verdrahtung zum Raspberry Pi selbst.
Die LEDs sind durch ihre Farben gekennzeichnet (UV = Ultraviolett, V = Violett, RB = Königsblau, B = Blau, C = Cyan, G = Grün, YG = Gelbgrün, Y = Gelb, A = Amber, R = Hell rot, DR = tiefrot, IR = infrarot), dh nach aufsteigender Wellenlänge.
Hinweis: Vergessen Sie nicht, dass auf der +5V-Anschlussseite der Kabelbuchse 2 x 1 mm dicke Drähte parallel auf dem Stripboard verlaufen, um einen Hochstrompfad zu gewährleisten. In ähnlicher Weise sollten die geerdeten Source-Anschlüsse zu den MOSFETs ähnliche Drähte haben, um den Hochstrompfad zur Erde bereitzustellen.
Schritt 10: Testen der Controllerplatine
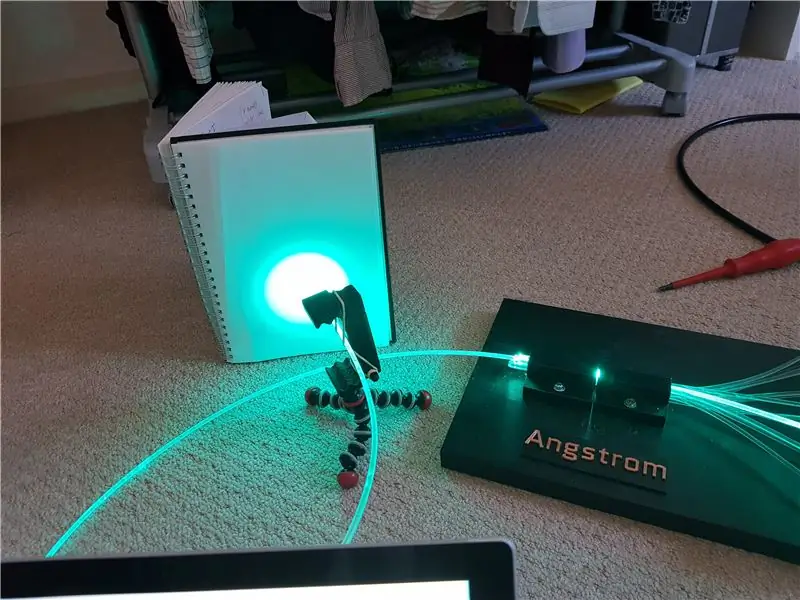
Ohne den Raspberry Pi in das Board zu stecken, können Sie testen, ob Ihre LED-Treiber richtig funktionieren, indem Sie die GPIO-Pins über ein Clipkabel an die +5V-Schiene anschließen. Die entsprechende LED sollte leuchten.
Verbinden Sie die GPIO-Pins niemals mit +5V, wenn der Pi eingesteckt ist. Sie beschädigen das Gerät, es läuft intern mit 3,3V.
Sobald Sie sicher sind, dass die Leistungstreiber und LEDs ordnungsgemäß funktionieren, können Sie mit dem nächsten Schritt fortfahren, der Konfiguration des Raspberry Pi.
Schauen Sie bei voller Leistung der LEDs nicht direkt in das Ende der Lichtwellenleiter. Sie sind extrem hell.
Schritt 11: Glasfaserkopplung der LEDs
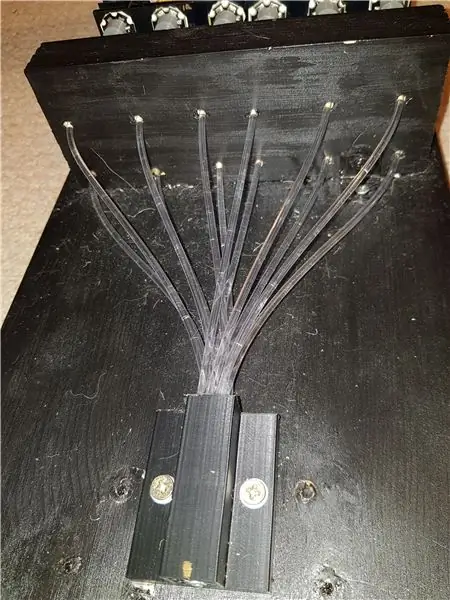
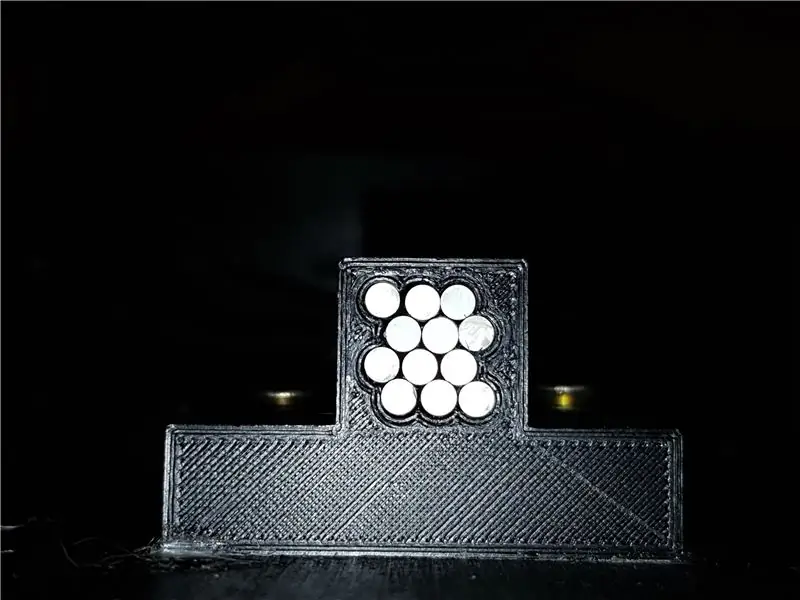
Jede LED wird über einen 3mm Lichtwellenleiter angekoppelt. Der 3D-gedruckte Faseradapter passt genau über die LED-Baugruppe und führt die Faser. Der Zugentlastungsblock wird ca. 65 mm vor den LED-Kühlkörpern montiert.
Dies bietet genügend Platz, um die Finger hineinzustecken und die Faseradapter auf die LEDs zu schieben und dann die Faser zu montieren.
Bohren Sie 4 mm Löcher durch den Zugentlastungsblock entlang der LEDs.
Jede Faserlänge ist ungefähr 250 mm lang. Da jede Faser jedoch einen anderen Weg nimmt, variiert die tatsächliche angepasste Länge. Der einfachste Weg, dies richtig zu machen, besteht darin, Faserlängen von 300 mm zu schneiden. Sie müssen dann die Faser begradigen, sonst wird es unmöglich sein, zu verwalten. Es ist wie ein 3 mm dicker Plexiglasstab und viel steifer, als Sie sich vorstellen.
Um die Faser zu begradigen, habe ich eine 300 mm lange (ca.) 4 mm OD Messingstange verwendet. Der Innendurchmesser des Stabes reicht aus, damit die Faser reibungslos in den Stab gleiten kann. Stellen Sie sicher, dass beide Enden der Rute glatt sind, damit Sie die Faser beim Ein- und Ausschieben nicht zerkratzen.
Schieben Sie die Faser so in die Stange, dass sie an einem Ende bündig ist und das andere etwas herausragt, oder ganz hinein, wenn die Stange länger als die Faser ist. Tauchen Sie den Stab dann für etwa 15 Sekunden in einen tiefen Topf mit kochendem Wasser. Entfernen Sie den Stab und positionieren Sie die Faser bei Bedarf so, dass das andere Ende bündig mit dem Stabende ist, und erhitzen Sie dann dieses Ende auf die gleiche Weise.
Sie sollten jetzt ein vollkommen gerades Stück Faser haben. Entfernen Sie, indem Sie ein weiteres Stück Faser durchschieben, bis Sie die begradigte Faser greifen und entfernen können.
Wenn Sie alle zwölf Faserstücke geglättet haben, schneiden Sie weitere zwölf Stücke von ca. 70 mm Länge ab. Diese werden verwendet, um die Fasern durch die Koppelplatte zu führen. Wenn die Konstruktion abgeschlossen ist, werden sie dann verwendet, um den einzelnen Faserauskoppler zu bestücken, damit sie nicht verschwendet werden.
Begradigen Sie diese geschnittenen Stücke auf die gleiche Weise. Montieren Sie sie dann an der Kupplungsplatte. Sie können sehen, wie sie auf dem Foto oben aussehen sollten. Die versetzte Anordnung soll die von den Fasern eingenommene Fläche minimieren (minimale kugelförmige Packungsdichte). Dies stellt sicher, dass der Faserkombinierer so effizient wie möglich arbeiten kann.
Nehmen Sie jedes Stück geschnittener Faser in voller Länge und schleifen Sie ein Ende flach, arbeiten Sie bis zu 800 und dann mit 1500er Schleifpapier. Anschließend mit Metall- oder Kunststoffpolitur polieren - ein kleines Drehwerkzeug mit Polierpad ist hier praktisch.
Entfernen Sie nun EINE geschnittene Faser und schieben Sie die Faser in voller Länge in die Kopplerplatte. Stecken Sie es dann wieder durch die Zugentlastung, so dass das polierte Ende über den LED-Faserkoppler die LED-Linsenfront berührt. Wiederholen Sie dies für jede Faser. Das Belassen der kurzen Faserstücke in den Löchern stellt sicher, dass jede lange Faser leicht an der richtigen Stelle platziert werden kann.
HINWEIS: Drücken Sie nicht zu stark auf die violetten und ultravioletten LEDs. Sie sind im Gegensatz zu den anderen LEDs, die mit Epoxidharz vergossen sind, mit einem weichen Polymermaterial gekapselt. Es ist leicht, die Linse zu verformen und die Bonddrähte zu brechen. Vertrauen Sie mir, ich habe das auf die harte Tour gelernt. Seien Sie also vorsichtig, wenn Sie die Fasern an diesen beiden LEDs anbringen.
Es spielt keine große Rolle, in welcher Reihenfolge Sie die Fasern durch den Koppler führen, aber versuchen Sie, die Fasern so zu schichten, dass sie sich nicht kreuzen. In meinem Design wurden die unteren sechs LEDs zu den untersten drei Löchern für die linken drei LEDs und dann zu den nächsten drei Löchern für die rechten drei LEDs und so weiter geleitet.
Wenn Sie alle Fasern durch den Koppler geführt haben, positionieren Sie ihn auf der Grundplatte und bohren Sie zwei Befestigungslöcher, dann schrauben Sie ihn fest.
Dann mit einem sehr scharfen Seitenschneider jedes Faserstück so nah wie möglich an der Kupplungsfläche abschneiden. Ziehen Sie dann jedes Stück heraus, schleifen und polieren Sie das abgeschnittene Ende und ersetzen Sie es, bevor Sie mit der nächsten Faser fortfahren.
Machen Sie sich keine Sorgen, wenn die Fasern nicht alle genau bündig mit der Kupplungsfläche abschließen. Es ist am besten, sich auf der Seite zu irren, wenn sie etwas zurückgesetzt sind, anstatt hervorzustehen, aber ein oder zwei Millimeter Unterschied spielen keine Rolle.
Schritt 12: Konfigurieren des Raspberry Pi
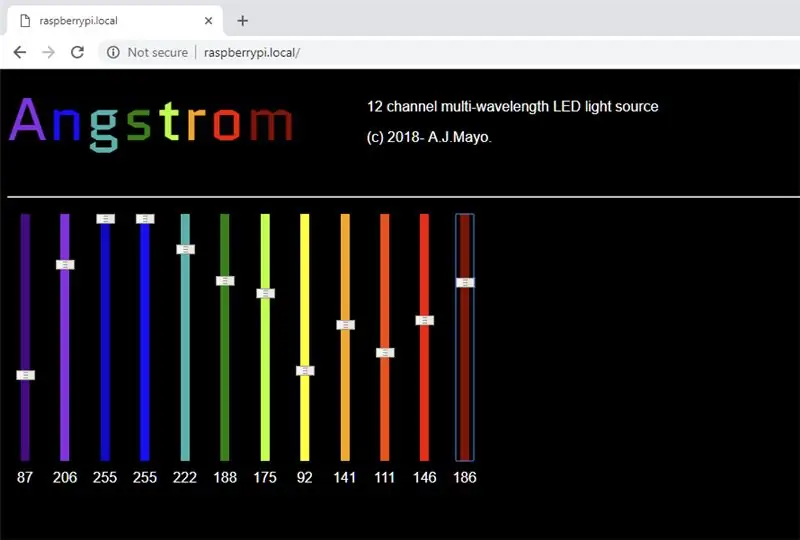
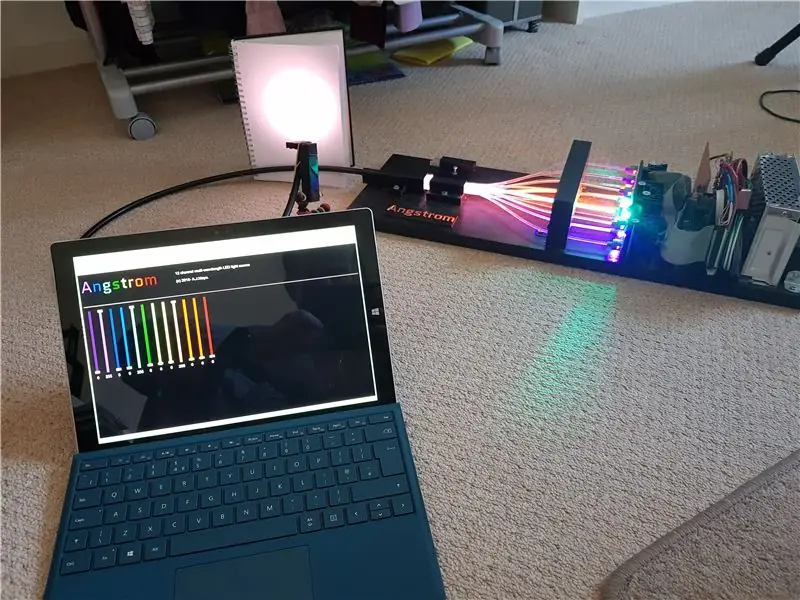
Der Konfigurationsprozess des Raspberry Pi ist im beigefügten rtf-Dokument dokumentiert, das Teil des Zip-Dateianhangs ist. Sie benötigen keine zusätzliche Hardware, um den Pi zu konfigurieren, außer einem freien USB-Port an einem PC zum Einstecken, einem geeigneten USB-Kabel und einem SD-Kartenleser zum Erstellen des MicroSD-Kartenimages. Sie benötigen außerdem eine MicroSD-Karte; 8G ist mehr als groß genug.
Wenn Sie den Pi konfiguriert und an die Hauptcontrollerplatine angeschlossen haben, sollte er als WLAN-Zugangspunkt angezeigt werden. Wenn Sie Ihren PC mit diesem AP verbinden und zu https://raspberrypi.local oder https://172.24.1.1 navigieren, sollten Sie die obige Seite sehen. Schieben Sie einfach die Schieberegler, um die Intensität und Wellenlänge des Lichts einzustellen, das Sie sehen möchten.
Beachten Sie, dass die Mindestintensität 2 beträgt; dies ist eine Besonderheit der Pi PWM-Bibliothek.
Das zweite Bild zeigt die Einheit, die das Spektrum einer CFL-Lampe emuliert, mit Emissionen bei ungefähr 420 nm, 490 nm und 590 nm (violett, türkis und bernsteinfarben), die den typischen drei Phosphorbeschichtungslampen entsprechen.
Schritt 13: Der Faserkombinierer
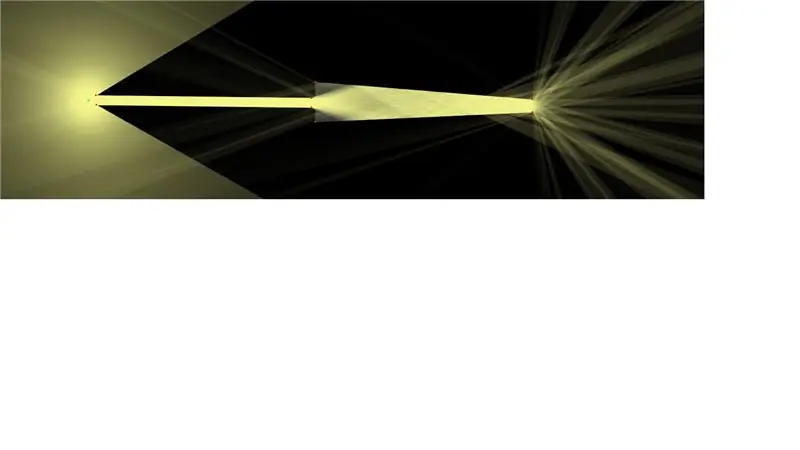
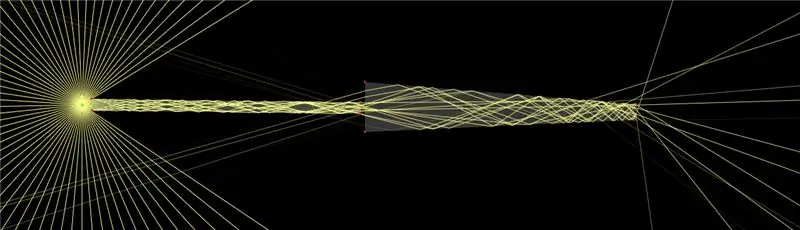
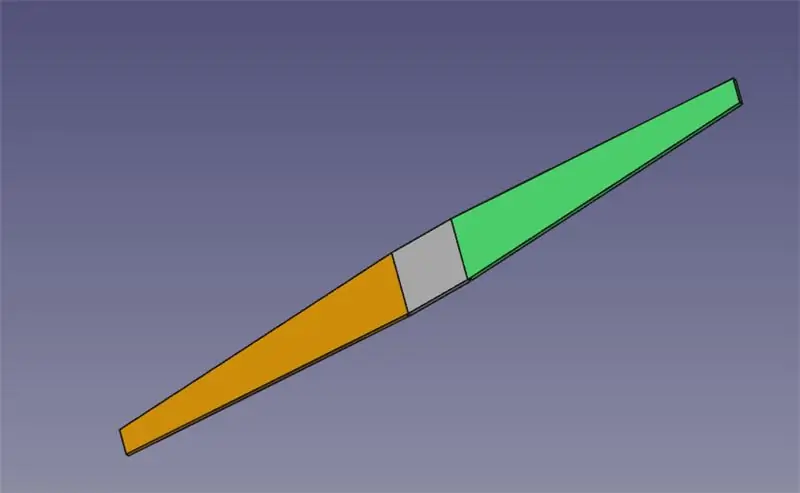
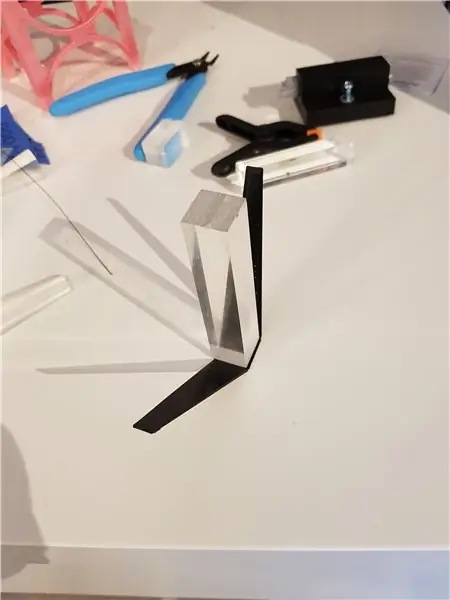
Der Fiber Beam Combiner besteht aus einem 15 x 15 mm quadratischen Acrylstab. Beachten Sie, dass einige Acrylkunststoffe im Spektrum ab 420 nm und darunter eine übermäßige Absorption aufweisen; Um dies zu überprüfen, bevor Sie beginnen, leuchten Sie die UV-LED durch den Stab und vergewissern Sie sich, dass sie den Strahl nicht übermäßig abschwächt (verwenden Sie ein weißes Blatt Papier, damit Sie das blaue Leuchten der optischen Aufheller im Papier sehen können).
Sie können die 3D-druckbare Schablone zum Abschleifen der Stange ausdrucken oder Ihre eigene aus einer geeigneten Plastikfolie konstruieren. Schneiden Sie den Stab auf ca. 73 mm und schleifen und polieren Sie beide Enden. Befestigen Sie dann die Schablone mit doppelseitigem Klebeband an zwei gegenüberliegenden Seiten der Stange. Schleifen Sie mit 40er Körnung, bis Sie sich innerhalb von 0,5 mm oder so von den Schablonenlinien befinden, und erhöhen Sie dann schrittweise auf 80, 160, 400, 800, 1500, 3000, 5000 und schließlich 7000er Körnung, um eine spitz zulaufende polierte Oberfläche zu erhalten. Entfernen Sie dann die Schablone und positionieren Sie sie neu, um die anderen beiden Seiten zu schleifen. Sie sollten jetzt eine sich verjüngende Pyramide haben, die für die Montage in der Faserkombinatorplatte geeignet ist. Das schmale Ende ist 6 mm x 6 mm groß, um dem Faserabzug zu entsprechen.
Hinweis: In meinem Fall habe ich nicht ganz auf 6 mm x 6 mm geschliffen, sodass der Combiner etwas aus der Montageplatte herausragt. Dies spielt keine Rolle, da die 6-mm-Faser eine Presspassung ist und an das schmale Ende des Combiners anstößt, wenn sie weit genug eingeschoben wird.
Entfernen Sie etwa 1 Zoll des Außenmantels von der 6-mm-Faser und achten Sie darauf, die Faser selbst nicht zu beschädigen. Wenn dann der Außenmantel der Faser nicht gut genug in die Kopplerplatte passt, wickeln Sie einfach ein Stück Klebeband darum. Es sollte sich dann einschieben lassen und mit der Combiner-Pyramide eng anliegen. Montieren Sie die gesamte Baugruppe in Übereinstimmung mit den Faserausgängen auf der Grundplatte.
Beachten Sie, dass Sie beim Kombinieren etwas Licht verlieren. Den Grund können Sie an den optischen Spuren oben erkennen, denn durch die Konzentration des Lichts nach unten vergrößert sich auch der Abstrahlwinkel und wir verlieren dabei etwas Licht. Für maximale Intensität bei einer einzigen Wellenlänge verwenden Sie die optionale Faserkopplerplatte, um eine oder mehrere LEDs direkt auf eine 3 mm-Faser zu übertragen.
Schritt 14: Die einzelne Faserausgangskopplerplatte
Dies ist nur ein zweiter Druck der Hauptfaserführung. Denken Sie auch hier daran, mit einer Skalierung von 105 % zu drucken, damit die Fasern durch die Löcher frei sind. Sie schrauben diese Platte einfach in einer Linie mit der Hauptfaserführung fest, schrauben die Combiner-Baugruppe ab und ersetzen sie durch diese Platte. Vergessen Sie nicht, es richtig herum zu montieren, die Löcher fluchten nur in eine Richtung!.
Legen Sie nun die 12 Stück Fasern, die Sie abgeschnitten haben, in die Löcher in der Platte. Um eine oder mehrere Wellenlängen aufzunehmen, entfernen Sie einfach ein Stück Faser und legen Sie eine längere Länge in das Loch. Wenn Sie möchten, können Sie alle 12 Wellenlängen gleichzeitig auswählen.
Schritt 15: Mehr Leistung!. Mehr Wellenlängen
Der Pi kann mehr Kanäle ansteuern, wenn Sie möchten. Die Verfügbarkeit von LEDs in anderen Wellenlängen dürfte jedoch eine Herausforderung darstellen. Sie können 365-nm-UV-LEDs günstig erhalten, aber das flexible 6-mm-Faserkabel beginnt bereits bei 390 nm stark zu absorbieren. Ich habe jedoch festgestellt, dass einzelne Fasern mit dieser Wellenlänge funktionieren. Wenn Sie also möchten, können Sie eine LED hinzufügen oder ersetzen, um eine kürzere UV-Wellenlänge zu erhalten.
Eine andere Möglichkeit besteht darin, die Helligkeit durch Verdoppelung der LEDs zu erhöhen. Sie könnten zum Beispiel einen 5 x 5 Faserkoppler (oder 4 x 6) entwerfen und drucken und 2 LEDs pro Kanal haben. Beachten Sie, dass Sie ein viel größeres Netzteil benötigen, da Sie fast 20 Ampere ziehen. Jede LED benötigt einen eigenen Vorwiderstand; nicht parallel die LEDs direkt. Die MOSFETs haben mehr als genug Kapazität, um zwei oder sogar mehrere LEDs pro Kanal anzusteuern.
Sie können nicht wirklich LEDs mit höherer Leistung verwenden, da sie kein Licht aus einem kleinen Bereich wie die 3W-LEDs emittieren und Sie sie daher nicht effizient über Glasfaser koppeln können. Schlagen Sie „Etendue-Erhaltung“nach, um zu verstehen, warum dies so ist.
Der Lichtverlust durch den Combiner ist recht hoch. Dies ist leider eine Folge der Gesetze der Physik. Durch die Reduzierung des Strahlradius vergrößern wir auch seinen Divergenzwinkel und so entweicht etwas Licht, da Lichtleiter und Faser nur einen Akzeptanzwinkel von etwa 45 Grad haben. Beachten Sie, dass die Ausgangsleistung einzelner Faserausgänge deutlich höher ist als die des kombinierten Wellenlängenkopplers.
Empfohlen:
Video-Tutorials De Tecnologías Creativas 04: ¿Para Qué Servirá Un Potenciómetro Y Un Led?: 4 Schritte
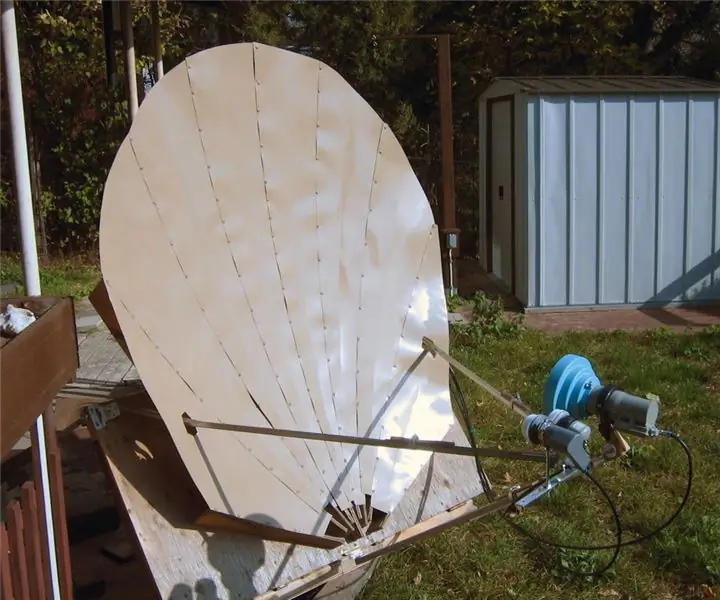
Video-Tutorials De Tecnologías Creativas 04: ¿Para Qué Servirá Un Potenciómetro Y Un Led?: En este Tutorial vamos a prender como modificar la intensid de la luz de un led con einer potenciómetro sobre una placa Arduino Uno. Este ejercicio lo realizaremos mediante simulación y para ello utilizaremos Tinkercad Circuits (utilizando una cuen
Arduino Ampel-Controller mit RBG Led - 4-Wege: 3 Schritte
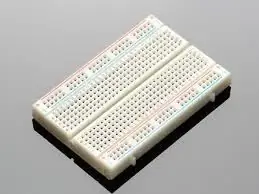
Arduino Ampel-Controller mit RBG Led | 4-Wege: In diesem Beitrag erfahren Sie, wie Sie einen Arduino-Ampelcontroller herstellen. Mit diesem Ampelsteuergerät wird der Verkehrsfluss gesteuert. Diese können in stark frequentierten Bereichen angewendet werden, um Verkehrsblockaden oder Unfälle zu vermeiden
Ein riesiges leuchtendes LED-Schild herstellen – wikiHow
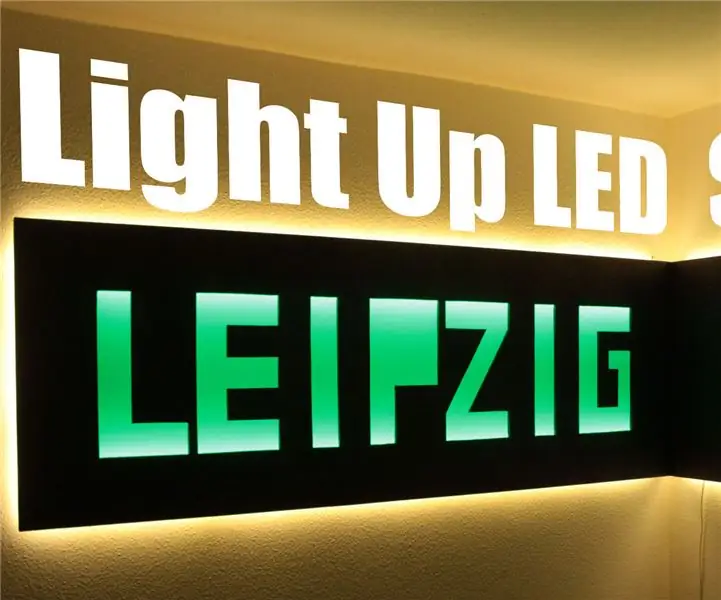
Wie man ein riesiges leuchtendes LED-Schild herstellt: In diesem Projekt zeige ich Ihnen, wie Sie ein riesiges Schild mit einem benutzerdefinierten Schriftzug bauen, der mit Hilfe von RGB-LEDs aufleuchten kann. Das Schild kann aber auch als primäre Lichtquelle in Ihrem Raum verwendet werden, indem warmweiße LED-Streifen verwendet werden. Lass uns st
Einfacher LED-Farbwechsel "Kerze": 5 Schritte (mit Bildern)
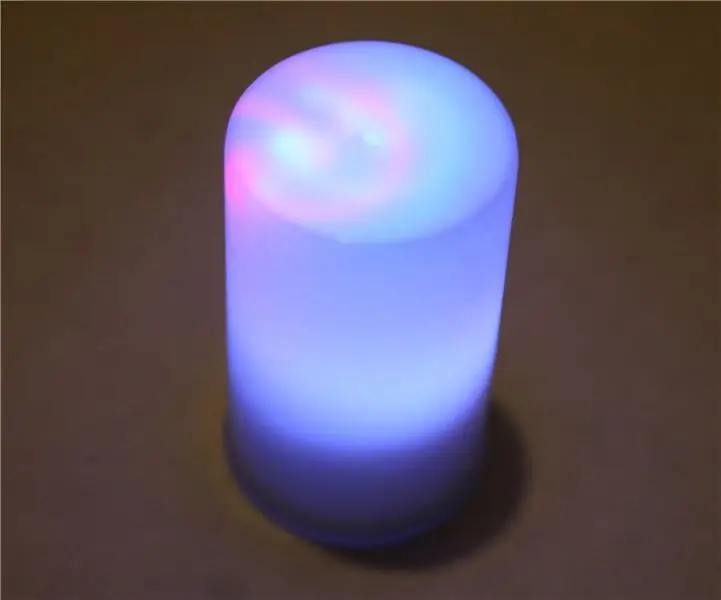
Einfacher LED-Farbwechsel "Kerze": Dies ist ein einfaches Farbwechsellicht, das sich hervorragend für Kinder und Erwachsene eignet. Sieht in einem schwach beleuchteten Raum wunderschön aus, ideal für die Feiertage und macht ein ziemlich cooles Nachtlicht
Wie erstelle ich einen LED-Würfel!: 3 Schritte
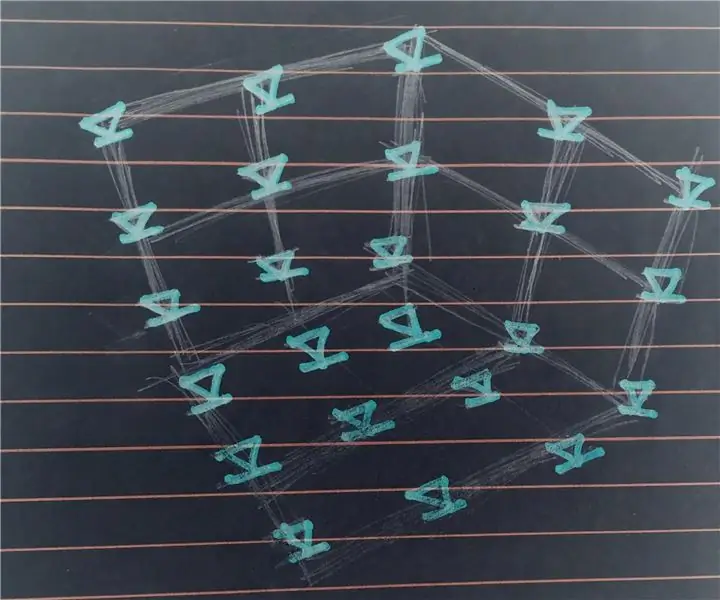
Wie man einen LED-Würfel herstellt!: Ein LED-Würfel kann ein großartiges Startprojekt für einen angehenden Elektronik-Bastler oder einen Studenten sein, der versucht, die Grundlagen der Schaltung zu erlernen. Durch den Bau eines ästhetisch ansprechenden Lichtwürfels lernen Sie die grundlegenden Schaltungsaufbauten kennen, vertraut