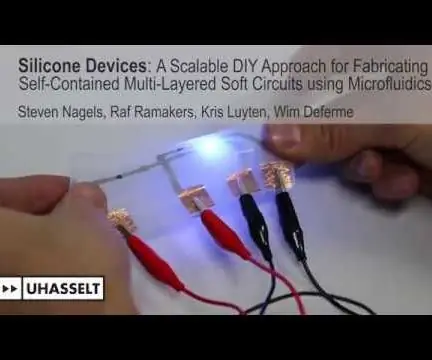
Inhaltsverzeichnis:
- Schritt 1: Lasercut-Start- und Transferplatten
- Schritt 2: Startplatte für Komponenten vorbereiten
- Schritt 3: Transferplatte für die selektive Adhäsion vorbereiten
- Schritt 4: Komponentenplatzierung
- Schritt 5: Primer-Auftrag
- Schritt 6: Cast / Blade Coat Silikon
- Schritt 7: Transferplatte ankleben
- Schritt 8: Startplatte entfernen
- Schritt 9: Schablonenmaske für die oberste leitfähige Schicht
- Schritt 10: Obere leitfähige Schicht
- Schritt 11: Prime Component Bottoms
- Schritt 12: Cast / Blade Coat Silikon
- Schritt 13: Schablonenmaske für die untere leitfähige Schicht
- Schritt 14: VIAs von oben nach unten
- Schritt 15: Untere leitfähige Schicht
- Schritt 16: Cast / Blade Coat Silikon
- Schritt 17: Kontaktpads
- Schritt 18: Probe frei schneiden
- Schritt 19: Bewundern Sie
2025 Autor: John Day | [email protected]. Zuletzt bearbeitet: 2025-01-23 12:52
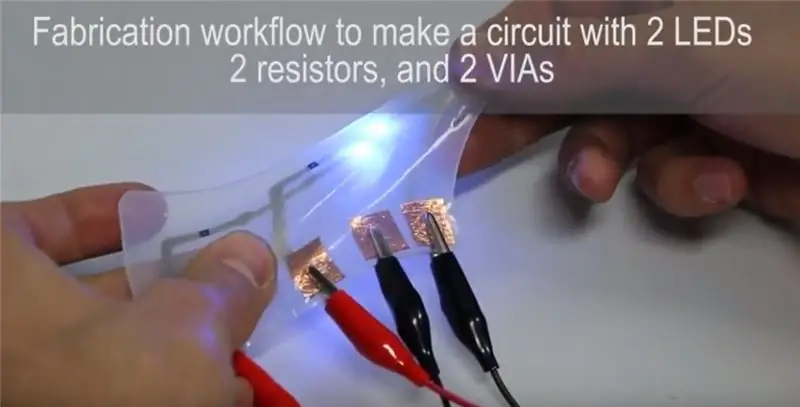

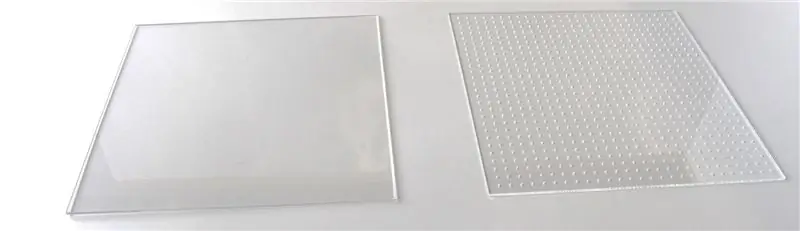
Silikongeräte bieten die frühen Vorteile weicher und dehnbarer Elektronik durch einen herstellerfreundlichen Ansatz. Indem Sie diesem Instructable folgen, lernen Sie die grundlegenden Fähigkeiten, die zum Erstellen Ihrer eigenen vollintegrierten weichen elektronischen Schaltungen erforderlich sind. Denken Sie an Baymax! Er ist eine hervorragende Zukunftsvision eines weichen Roboters, die nur durch die Entwicklung weicher elektronischer Schaltungen Realität werden kann.
"Halt Noagels hoch… Was genau meinst du mit diesem Hokuspokus über 'weiche elektronische Schaltkreise'?"
Kurz gesagt, dehnbare Elektronik verspricht, die Art und Weise, wie wir von unseren Geräten umgeben sind und mit ihnen zu interagieren, zu naturalisieren. Sie sind buchstäblich weiche und „dehnbare“elektronische Schaltkreise, die neue Möglichkeiten in der Mensch-Computer-Interaktion eröffnen und eine Schlüsseltechnologie für Soft Robotics sind.
Silicone Devices stellen einen einzigartigen Herstellungsansatz dar, der Technologie in die Maker-Community einbringt, die früher in wissenschaftlichen Forschungsgruppen ansässig war. Natürlich ist der von Silicone Devices demonstrierte Herstellungsprozess nicht der einzige Weg zu dehnbarer und weicher Elektronik und auch kein völlig neuer. Wissenschaft arbeitet in inkrementellen Schritten. Einer unserer Schritte ist es, die Technologie einfach zu implementieren und Maker auf der ganzen Welt zu erreichen. (Das bedeutet Sie. Genau hier, jetzt!) Durch unseren Herstellungsansatz können Sie Ihre eigenen weichen Schaltkreise erstellen. Silicone Devices unterstützt die Integration von Mikrocontrollern, I/O-Komponenten und einer Stromquelle, die alle in einem eigenständigen Gerät kombiniert sind.
Diese Arbeit entstand durch die Zusammenarbeit von Raf Ramakers, Kris Luyten, Wim Deferme und Steven Nagels (das bin ich) an der Hasselt University, Belgien. Die in diesem instructable vorgestellte Technik wird am führenden Ort der Mensch-Computer-Interaktion veröffentlicht: Human Factors in Computing Systems (CHI 2018). Dieses instructable zielt darauf ab, unsere Forschungsergebnisse über die akademische Gemeinschaft hinaus zu kommunizieren. Wenn Sie möchten, können Sie hier ausführlichere Informationen lesen: Hier ist die Projektseite von Silicone Devices, die vollständige wissenschaftliche Veröffentlichung finden Sie hier und einen allgemeineren Hintergrund zur Herstellung von verbindungsbasierter dehnbarer Elektronik finden Sie hier.
Aber - um sicherzustellen, dass Sie nicht TL;DR machen - kommen wir zur Sache!
Was wirst du brauchen:
- Zugang zu einem CO2-Laserschneider von Fablab oder Makerspace (Referenz: ein 60W Trotec Speedy 100R)
- Airbrush (bevorzugt) oder Sprühflasche (zugänglichere Alternative)
- Acryl/PMMA/Plexiglasplatten (genug, um 2 Quadrate von 280x280mm zu schneiden) wir haben 3mm dick verwendet, alles ab 1,5mm sollte funktionieren
- Schwarzer Vinylaufkleber (ausreichend, um 4 Quadrate von ca. 260x260mm zu schneiden) (wir haben MacTac 8900 Pro Mattschwarz verwendet)
- Trennspray (Voss Chemie Trennspray, Smooth-on Ease Release)
- Flüssigmetall: Galinstan (am besten 10 g bereithalten, je nachdem, wie verschwenderisch Sie sind, können Sie jede Menge über 5 g verwenden)
- 2 Stück 3ml Einwegpipette um Galinstan aus seinem Behälter auf die Schablone zu nehmen
- Feiner Pinsel, wie aus diesem Set
- Weicher Gummiroller (auch Gummibrayer genannt, wie dieser)
- Silikonprimer (Bison Silicone Primer getestet, 3M AP596 Haftvermittler könnte auch funktionieren)
- Eine Tube billiges Silikondichtmittel + Spender (Dichtungspistole)
- Schnellhärtendes 2-Komponenten-Silikon auf Platinbasis (Siliconesandmore getestet, DragonSkin 10 Alternative) Bei Verwendung der mitgelieferten Designdateien sollten Sie 150 g nicht überschreiten. Die meisten Kits werden jedoch in Mengen von 1 kg verkauft.
- 3 Mischbecher (>100ml) und Rührstäbe (6" ist am bequemsten)
- Waage mit einer Genauigkeit von 0,1 oder 0,001 Gramm (diese tragbaren machen den Trick)
- Höhe rekonfigurierbarer Blade Coater oder lasergeschnittene DIY-Version in den Höhen 1 mm, 1,5 mm und 2 mm (TODO, super kurz separat anweisbar)
- 2 Low-Profile-LEDs der Größe 1206 (Digikey, Farnell)
- 2 100-Ohm-Widerstände der Größe 2010 (Digikey, Farnell)
- Kupfer- oder Aluminiumband. Folie ist noch besser (wenn Klebeband abgewaschen werden muss)
- Feine Pinzette
- ein X-acto-Messer
-
Scotch Magic-Band
Dieses Tutorial geht ziemlich ins Detail! Bitte lassen Sie sich nicht von der Anzahl der Schritte oder langen Beschreibungen abschrecken. Da wir unser System mit Silikon abdichten, werden Fehler, die sich in der Testphase zeigen, schwer zu beheben sein. Sie müssen daher jeden Schritt sorgfältig lesen und von Anfang an richtig machen. Der gesamte Vorgang sollte nicht länger als 2 Stunden dauern, wenn Sie alle Werkzeuge ständig zur Verfügung haben und Gießsilikon mit einer Aushärtezeit von 15 Minuten verwenden.
Dieses Tutorial verwendet ein sehr einfaches Design eines Silikongeräts, bestehend aus 4 Kontaktpads, 2 LEDs und 2 VIAs als laufendes Beispiel. Das Endergebnis ist oben auf dem Foto und Video zu sehen. Obwohl dieses Design ziemlich einfach ist, unterstützt unser DIY-Fertigungsansatz viele Arten von SMD-Komponenten und eine beliebige Anzahl von Schichten. Daher skaliert unser Ansatz auf dehnbare Schaltungen beliebiger Komplexität, wie die Beispieldesigns in dem am Anfang dieser Anleitung verlinkten Youtube-Video zeigen.
Alle Designdateien (als.zip gebündelt) hier. Praktische Zusammenstellung von einzelnen PDF-Anleitungen hier.
Schritt 1: Lasercut-Start- und Transferplatten
Als ersten Schritt müssen Sie einige starre Trägerplatten laserschneiden, um daran zu arbeiten.
Warum brauchst du 2 Teller? Nun, nachdem wir auf der glatten Startplatte eine Bauteilschicht erzeugt haben, kleben wir die Silikonfolie mit den Bauteilen innen auf die Transferplatte, drehen den Stapel um, nehmen die glatte Startplatte ab und legen dabei die Bauteile von ihrer Rückseite frei. Die Transferplatte hat winzige Löcher, damit Luft entweichen kann, wenn in Schritt 7 eine nasse Silikonschicht aufgetragen wird.
Anforderungen an die Trägerplatten:
•Muss für die richtige Ausrichtung im Übertragungsschritt gleich groß sein
•Größe: 280x280mm
•Material: klares Acryl (PMMA oder Plexiglas)
•Startplatte links oben markieren, Transferplatte rechts oben
Schritt 2: Startplatte für Komponenten vorbereiten
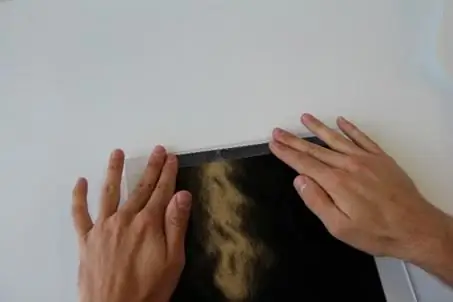
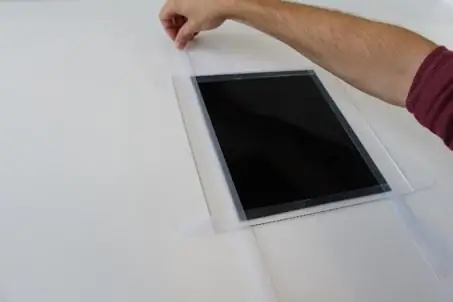
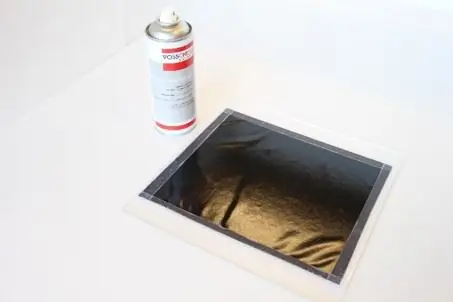
In diesem Schritt beginnen wir mit dem Aufbau unserer Strecke auf der glatten Startplatte. Später wollen wir diese Platte aber wieder entfernen. Daher sollten Sie zunächst einen dünnen Film Trennspray über die gesamte Startplattenoberfläche sprühen. Anschließend nimmst du einen schwarzen Vinylaufkleber mit den Maßen einige Zentimeter unter denen deiner Startplatte. Ziehen Sie dann das Aufkleberpapier ab und legen Sie den Aufkleber flach auf und in die Mitte der Startplatte; klebrige Seite nach oben. Sichern Sie den Aufkleber mit Klebeband (achten Sie darauf, dass Sie nicht zu stark am Klebeband ziehen, da dies zu Falten in Ihrer Aufkleberoberfläche führt). Mit einer weiteren Schicht Formtrennspray auf der klebrigen Oberfläche abschließen. Halten Sie die Düse etwa 20 cm über der Oberfläche und sprühen Sie eine glatte, durchgehende Schicht. Tipp: Zweimal und im überlappenden Raster sprühen!
Vorbereitung der Startplatte:
• Aufkleber zuschneiden (ca. 2 cm kleiner als die Plattenmaße)
• Durch Reiben mit Baumwolltuch oder Papiertuch statische Aufladung auf Aufkleber und Platte aufbringen, dadurch liegt es gleichmäßiger auf
• Sprühstartplatte lösen (zweimal und rasterförmig)
•Klebebandaufkleber auf der Startplatte, Klebeseite nach oben
•Bestückungsmarkierungen mit Laserschneider einritzen (P = 6-7) NICHT DURCHSCHNEIDEN
• Sprühklebefolie freigeben (zweimal und in einem Rastermuster)
Schritt 3: Transferplatte für die selektive Adhäsion vorbereiten
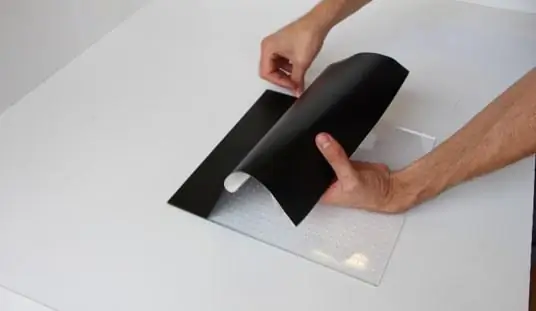
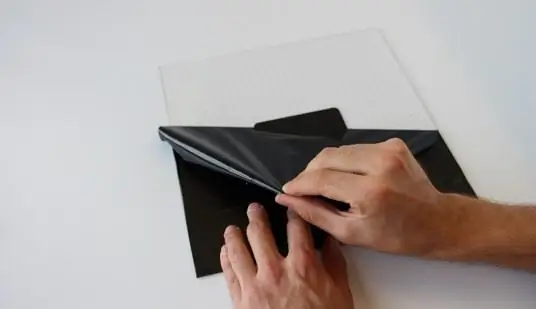
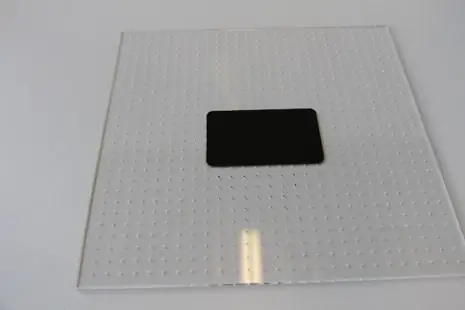
Um eine korrekte Ausrichtung bei allen Schritten nach Schritt 7 zu gewährleisten, lassen wir unser Silikon an Stellen außerhalb der Kontur unserer weichen Schaltung eine starke Verbindung mit der Transferplatte herstellen. Diese starke Verbindung wird durch Vorbehandlung der Transferplatte mit Bison Silicone Primer erreicht. Am Ende des Bauprozesses möchten Sie Ihre weiche Schaltung leicht von der Bauplatte trennen und somit nicht mit ihr verbunden haben. Daher müssen wir den Bereich, der von unserem weichen Schaltkreis eingenommen wird, frei von Grundierungsmaterial halten. Dies tun wir, indem wir diesen Bereich während des Aufsprühens der Grundierung mit einem zugeschnittenen Aufkleber abdecken. Diese Maske wird erhalten, indem ein Aufkleber (normalerweise, klebende Seite nach unten) auf die gesamte Oberfläche der Transferplatte geklebt und anschließend die Schaltungskontur + 5 mm Randform aus dem Aufkleber lasergeschnitten wird. Überschüssiges Aufklebermaterial wird entfernt.
Merken Sie sich:
• Aufkleber zuschneiden (ca. Plattenmaße)
• Aufkleber anbringen, ohne Luftblasen einzuführen
•Design sollte gespiegelt sein (Platte wird mit der Vorderseite nach unten gelegt)
•Grundierungsmaske (Plattenumrisse + 5mm Rand) mit Laserschneider (8-9W) ausschneiden
• Entfernen Sie den Aufkleber selektiv, um das darunter liegende Plexi freizulegen. Lassen Sie die Aufkleberteile, die den Leiterplattenbereich bedecken.
Schritt 4: Komponentenplatzierung
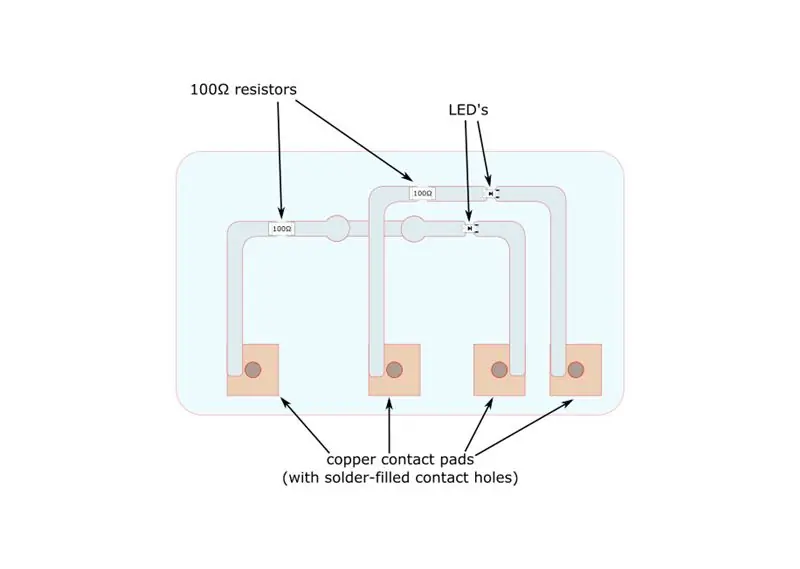
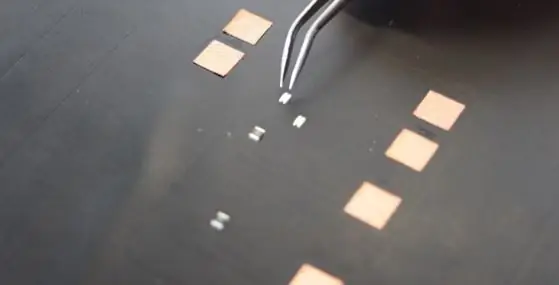
Etwas kontraintuitiv ist es, mit den Komponenten vor Leiterbahnen zu beginnen. Platzieren Sie beide Widerstände und LEDs wie in der Abbildung hier gezeigt.
Warum platzieren wir Komponenten an erster Stelle? Wir brauchen unsere Komponenten, die gut mit dem Silikonmaterial um sie herum vernetzt sind. Auf der Oberseite und an den Seiten ist dies einfach zu bewerkstelligen. Auf der Unterseite wollen wir unser Silikon jedoch überall mit dem Bauteil verbinden, außer an den Stellen, die von Leiterbahnen kontaktiert werden. Eine Möglichkeit, dies zu erreichen, besteht in der Folge: a) Einbetten und Binden der Oberseite der Komponenten in eine Silikonfolie, b) Umdrehen des Stapels, um die Kontaktpads der einzelnen Komponenten freizulegen, c) Anbringen von Leiterbahnen und erst danach d) Binden den verbleibenden freiliegenden unteren Oberflächenbereich der Komponente mit einer zweiten Schicht aus Gießsilikon. Diese Schritte a) b) c) und d) werden weiter unten in der Tabelle besprochen.
Allgemeine Richtlinien für diesen Schritt:
•Bauteile gemäß Schaltungsdesign auf Startplatte platzieren. Die Komponente fest durch die aufgesprühte Trennschicht in die Klebeschicht des Aufklebers drücken. Auf diese Weise bleibt es an Ort und Stelle.
•Komponenten sollten SMD sein. Vorzugsweise Größe 2010 oder größer. Der Abstand auf den benachbarten Pins eines ICs darf nicht unter 0,8 mm liegen. TQFN-Pakete sind die untere Grenze.
•Jede platzierte Komponente sollte ihre Kontaktflächen in einer Ebene mit der Klebeschicht des Aufklebers haben
Schritt 5: Primer-Auftrag
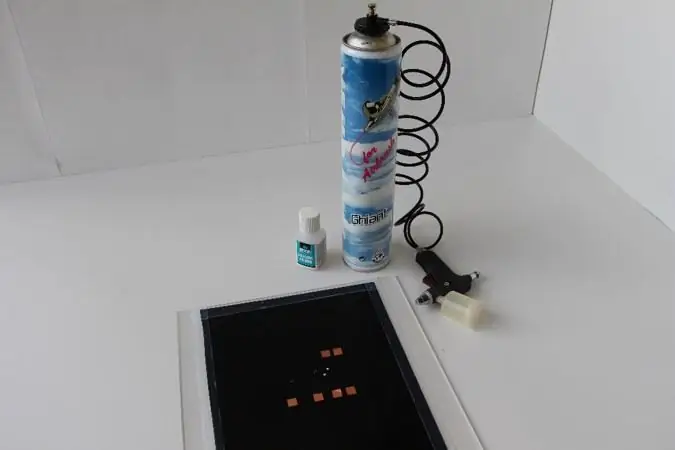
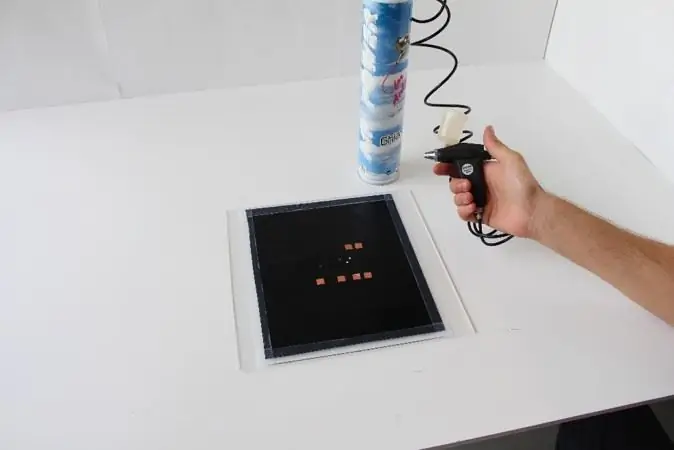
Das Auftragen des Primers ist ein entscheidender Schritt, der nicht weggelassen werden darf. Ohne eine gute Haftung zwischen der Komponente und dem umgebenden Silikon würde eine Belastung zu einem lockeren Sitz des Silikons um jede Komponente führen. Dieser lockere Sitz würde es dann ermöglichen, dass flüssiges Metall über die Kontaktpads fließt und somit Kurzschlüsse einführt. Eine dünne, gleichmäßige Schicht Bison Silicone Primer sollte alle exponierten Teile des flach auf dem Aufkleber liegenden Bauteils vollständig bedecken.
Zu Ihrer Überlegung:
•Verwenden Sie Bison Silicone Primer und Airbrush (Sealey Tools AB931)
•Komponenten auf der Startplatte aus jedem Winkel dünn einsprühen
• Trocknen lassen und sofort mit Schritt 6 für eine optimale Vernetzung fortfahren
Schritt 6: Cast / Blade Coat Silikon
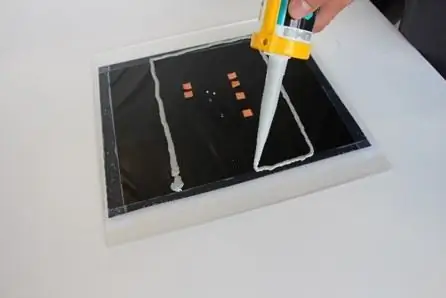
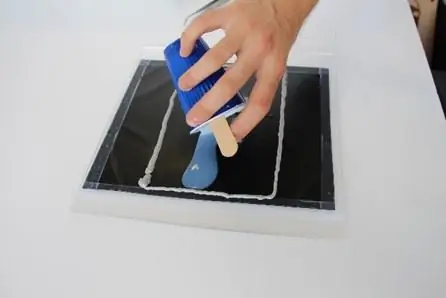
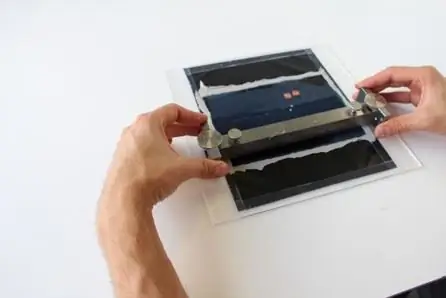
Als nächstes: Silikon um und über unsere Komponenten gießen! Die Dicke dieser Schicht muss etwa 300 Mikrometer höher sein als die Dicke Ihres dicksten Bauteils. Für die eingangs genannten Komponenten bedeutet dies 1mm. Um diese erforderliche Dicke zu erreichen, verwenden wir einen Flutbalken, den wir in genau dieser Höhe über die Oberfläche streichen. (Für Neugierige: Fachjargon dafür ist Klingenbeschichtung).
Gießsilikon allein ist nicht viskos. Ich würde die Form nicht halten, nachdem ich ihm eine bestimmte Höhe gegeben habe. Dazu wird eine Art „Schwimmbad“aus zähflüssigerem Acrylmastix (Silikondichtmasse) aufgetragen. Diese Versiegelung wollen wir nicht in unser Muster schmieren: Deshalb werden wir zweimal und von der Mitte nach außen beschichten.
Aufzählung:
• Legen Sie das Acrylkitt-Kit um den erforderlichen Umfang der Silikonfolie herum
•Mix 2 Komponenten Shore 15 Härte Platin Polyadditionssilikon
• Gießen Sie in Mastix-„Pool“, beginnend in der Mitte und auf alle Komponenten
•Klinge beschichtet eine Silikonschicht mit einer Höhe von 300um > höchste Komponente
•Warten Sie, bis das Silikon aushärtet
Schritt 7: Transferplatte ankleben
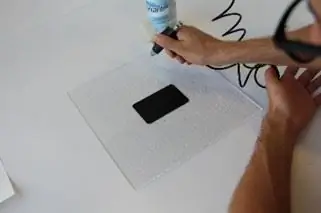
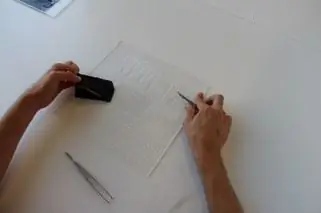
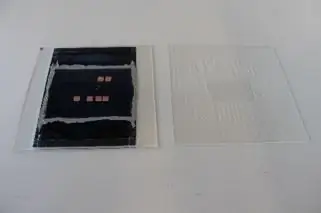
Hey, ihr macht bisher einen tollen Job! Normalerweise lächelt Ihnen an dieser Stelle eine mit Silikonen gefüllte Folie zu. Bauteile sollten komplett mit Silikon ummantelt sein und mit ihren unteren Kontakten flach auf der Plexiglas-Trägerplatte mit einem dazwischen liegenden Vinyl-Aufkleber aufliegen. Lassen Sie uns nun diesen Stapel umdrehen und diese Kontakte freilegen!
*Hier Fehlausrichtungswarnung einfügen*
Was wir an dieser Stelle haben, ist ein Bogen mit Bauteilen, die nach einem digitalen Design genau platziert (Sie haben eine genaue Arbeit gemacht, oder?) an der oberen linken Ecke Ihrer Trägerplatte ausgerichtet sind. Wir müssen nun eine zweite Platte darauf legen, die Silikonplatte darauf kleben, den Stapel umdrehen und die erste Trägerplatte entfernen - alles ohne diese Eckausrichtung zu verlieren! Sie werden sehen, das ist einfacher als es klingt. Stellen Sie sicher, dass Sie einen guten Schraubstock oder eine gerade Ecke haben, gegen die Sie die Platten ausrichten können.
Zuerst müssen wir unsere zweite Trägerplatte (die mit den Luftlöchern) besprühen, auf der Sie bereits einen Vinylaufkleber platziert und zu einer Grundierungsmaske in Form geschnitten haben. Sprühen Sie in einem gleichmäßigen, durchgehenden Muster. Anschließend den Primermaskenaufkleber entfernen.
Nehmen Sie nun Ihre Platte mit der bauteilgefüllten Platte. Richten Sie seine obere linke Ecke an Ihrem Schraubstock oder geraden Ecke aus. Als nächstes mischen Sie etwas mehr Silikon (ca. 50 ml reichen aus). Gießen Sie es auf die Silikonplatte und verteilen Sie es zu einer mehr oder weniger gleichmäßigen Schicht. Als nächstes nehmen wir die zweite Trägerplatte (mit Luftlöchern), die wir gerade grundiert haben. Seine rechte Ecke war ein paar Schritte zurück markiert. Legen Sie es mit der besprühten Seite nach unten auf die erste Platte und mit der markierten Ecke ebenfalls nach unten in Ausrichtung mit der oberen linken Markierung auf der Startplatte. Nach unten drücken, Luftblasen herausdrücken und die Platten dazwischen immer wieder ausrichten. Das Herausdrücken von mehr Silikon durch die Löcher sorgt für weniger Luftblasen und eine bessere Verbindung. Zufälligerweise bedeutet dies aber auch für Sie mehr Schwierigkeiten beim weiteren Verschieben der Platten in die Ausrichtung. Also erst ausrichten, dann Luft auspressen.
Warten Sie abschließend, bis das Silikon ausgehärtet ist.
Eine Shortlist-Übersicht:
•Transferplatte mit Primer besprühen. Grundierungsmaske entfernen
•Mix 2 Komponenten Shore 15 Härte Platin Polyadditionssilikon
•Auf das nun ausgehärtete silikonhaltige Bauteil eine gleichmäßige Schicht auftragen, ca. 1mm dick
•Transferplatte, grundierte Seite nach unten
•Mit Startplatte ausrichten
• Druck ausüben, Luft herausdrücken
•Ausrichtung doppelt prüfen
•Warten Sie, bis das Silikon aushärtet
Schritt 8: Startplatte entfernen
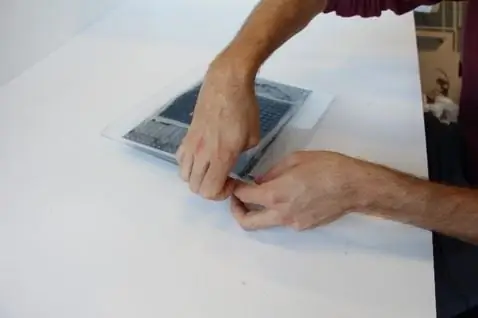
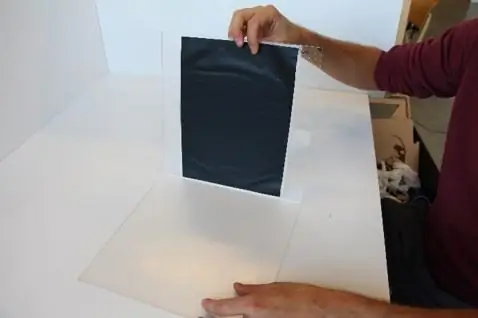
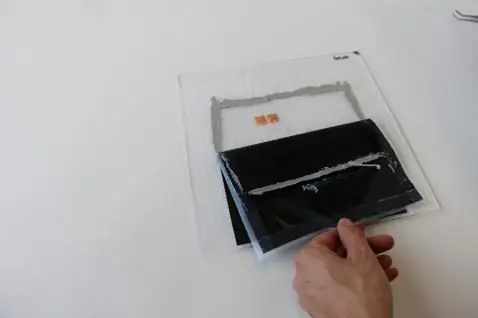
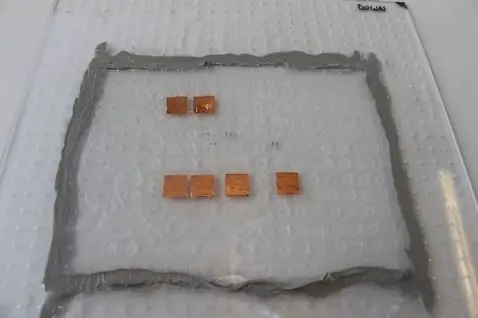
Der entscheidende Teil ist vorbei. Lassen Sie uns nun bis zu dem Moment arbeiten, in dem wir Ihre Ausrichtungsfähigkeiten überprüfen können!
Nehmen Sie Ihr Plexi-Silikon-Aufkleber-Plexi-Sandwich, verwenden Sie ein Schneidemesser, um das Klebeband an den Kanten Ihres Vinyl-Aufklebers zu lösen. Die Plexiglas-Startplatte sollte sich jetzt leicht lösen. Wenn dies nicht der Fall ist, verwenden Sie einen flachen Gegenstand zwischen dem Aufkleber und Ihrem Teller oder zwischen beiden Tellern, um den Stapel aufzulockern. Achten Sie darauf, dass Sie Ihren Silikonstapel nicht von der zweiten Platte (mit Löchern) abreißen, da dies zu Fehlausrichtungen führt.
Wenn die Komponenten richtig platziert wurden - in Übereinstimmung mit dem Aufkleber - und der Silikonprozess sorgfältig genug durchgeführt wurde, um die Komponenten nicht zu verrutschen; Sie sollten jetzt Ihre Komponenten mit ihren Rückseiten schön freigelegt haben!
Verwenden Sie ein Multimeter, um den Wert jeder Komponente zu messen. (Widerstände messen Ohm, LEDs verwenden die Diodeneinstellung, um sie aufzuleuchten). Auf diese Weise können Sie elektrisch überprüfen, ob kein dünner Film aus Aufkleberkleber oder Gießsilikon die Kontaktpads bedeckt - mit bloßem Auge kaum sichtbar.
Zusamenfassend:
• Aufkleber auf einer Seite des Sandwiches aus Plexi-Silikon+Aufkleber-Plexi lösen
•Startplatte und Aufkleber von den in Silikon eingebetteten Komponenten abziehen
•Komponenten auf ungehinderte Freilegung leitender Pads prüfen
•Da wir den Stack gespiegelt haben, müssen alle weiteren Schritte mit gespiegelten Designebenen ausgeführt werden (alle Dateien in diesem Tutorial wurden bereits entsprechend vorbereitet, keine weiteren Anpassungen notwendig)
Schritt 9: Schablonenmaske für die oberste leitfähige Schicht
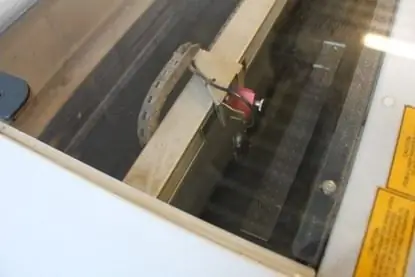
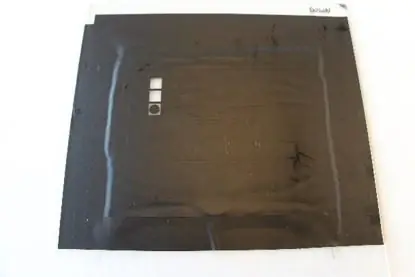
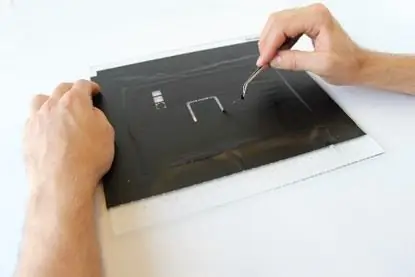
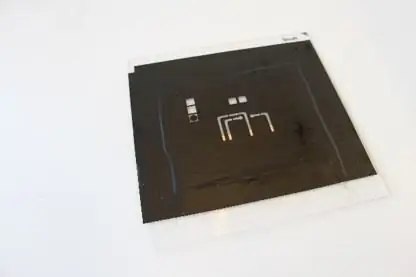
Ihr Moment der Wahrheit! Lassen Sie uns überprüfen, wie gut Sie in den vorherigen Schritten abgeschnitten haben.
Bringen Sie einen neuen Aufkleber an, um Ihre Silikonplatte vollständig mit freiliegenden Komponentenkontakten zu bedecken. Legen Sie die Platte in Ihren Laserschneider, während die Markierung in der oberen rechten Ecke zu sehen ist, und schneiden Sie die erste Schaltungsschicht durch den Aufkleber.
Wenn die Schablone, die wir als nächstes schneiden, gut mit Ihren Komponenten übereinstimmt, haben Sie alle vorherigen Schritte gut gemacht. Wenn sonst.. Naja, verdammt. Die Probleme beziehen sich höchstwahrscheinlich darauf, dass Ihr Aufkleber während des Auftragens von Silikon nicht flach aufliegt und/oder eine erhebliche Fehlausrichtung der zweiten Trägerplatte zur ersten Trägerplatte 2 Schritte zurück. Messen Sie, wie viele mm Sie abweichen, und Sie können dies durch die Designplatzierung in der Laserschneider-Software korrigieren.
Eine Zusammenfassung für Ihre Bequemlichkeit:
• Aufkleber zuschneiden (ca. Plattenmaße)
• Aufkleber anbringen, ohne Luftblasen einzuführen
• Laser kalibrieren, um den Aufkleber präzise zu durchschneiden (8-9W)
•Schneiden Sie die oberen Kupferleiterbahnen mit dem Laserschneider
• Aufkleber in Bereichen entfernen, die leitfähig gemacht werden müssen (Leiterbahnen, Pads)
Schritt 10: Obere leitfähige Schicht
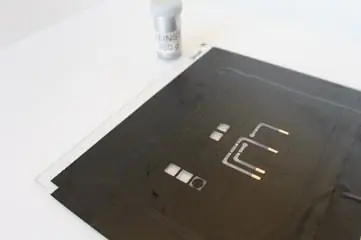
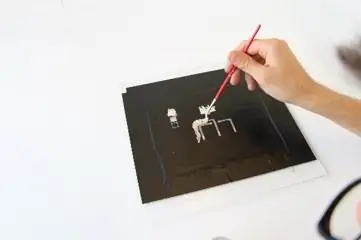
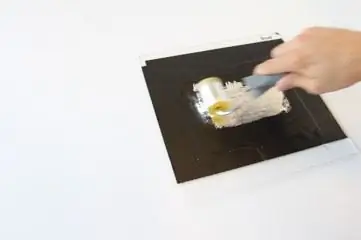
Wir werden in diesem Schritt mit dem flüssigen Metall arbeiten. Stellen Sie sicher, dass Ihr Arbeitsplatz vollständig abgedeckt ist (z. B. mit Zeitungspapier). Wenn Sie flüssiges Metall verschütten, wird es mühsam, es wieder zu reinigen. Es gibt kein echtes Lösungsmittel dafür und dringt auch nicht in Schwamm oder Papiertuch ein. Am besten arbeitest du richtig sauber und wirfst gleich danach die Zeitungen weg, die du vielleicht verschüttet hast. Tragen Sie am besten Handschuhe oder waschen Sie sich danach die Hände. Es wird Abstriche geben.
An dieser Stelle sollten Sie eine richtig definierte Schablone haben. Stellen Sie sicher, dass es an den Rändern gut am Silikon haftet. Wir wollen nicht, dass darunter flüssiges Metall durchfließt.
Nehmen Sie nun das flüssige Metall und einen feinen Pinsel. Tragen Sie das flüssige Metall in kurzen Ausstrichen auf die Schablonenöffnungen auf (Bilder als Referenz). Dies sollte eher ein Eintauchen als ein Verschmieren sein. Das flüssige Metall muss in engen Kontakt gebracht werden, damit es gut haften kann. Sobald Sie das Muster Ihrer Schablone abgedeckt haben, nehmen Sie die Rolle und rollen Sie das überschüssige flüssige Metall zur Seite. Dies kann mit einer kleinen Plastikpipette wiedergewonnen werden.
Zusamenfassend:
•Stellen Sie sicher, dass Ihr Aufkleber gut an den Kanten der exponierten Bereiche haftet
•Reinigen Sie freiliegende Silikon- und Komponentenpads mit Isopropylalkohol
•Verwenden Sie einen Pinsel, um alle exponierten Stellen grob mit Galinstan. abzudecken
•Verwenden Sie die Walze, um das aufgetragene Galinstan zu einer gleichmäßigen Beschichtung zu machen
• Überschüssiges Galinstan in seinen Behälter zurückholen
•Entfernen Sie die Aufkleberschablone vorsichtig
•Wenn Galinstan beim Entfernen in Bereiche fließt, in denen es nicht sein sollte, war Ihre Beschichtung zu dick. Oberfläche reinigen und bei Schritt 9 neu starten.
Schritt 11: Prime Component Bottoms
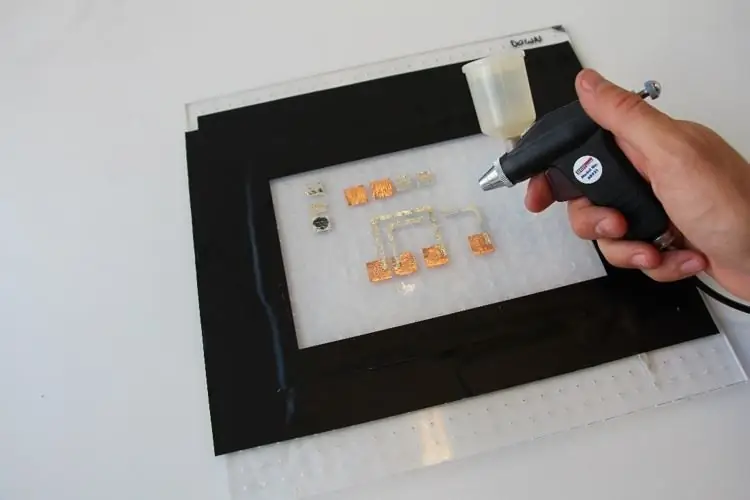
Dieser Schritt ist ziemlich selbsterklärend. Sie haben bereits zweimal Primer aufgetragen. Mach es einfach nochmal. Der Fokus liegt nicht auf der Silikonfolie, sondern auf den Bauteilunterseiten und speziell den Teilen, die nicht mit Flüssigmetall bedruckt sind. Lassen Sie die Grundierung trocknen und fahren Sie sofort mit Schritt 12 fort.
•Verwenden von Bison Silicone Primer und Airbrush (Sealey Tools AB931)
•Besprühen Sie freiliegende Bauteilunterseiten mit einer dünnen Schicht Primer
• Trocknen lassen und sofort mit Schritt 12 fortfahren
Schritt 12: Cast / Blade Coat Silikon
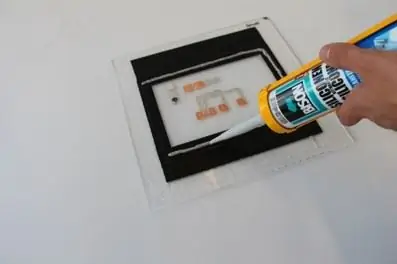
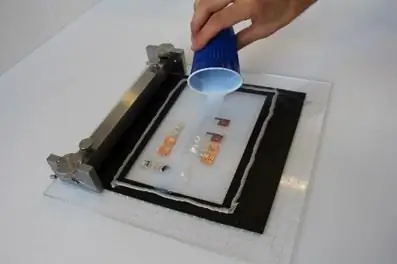
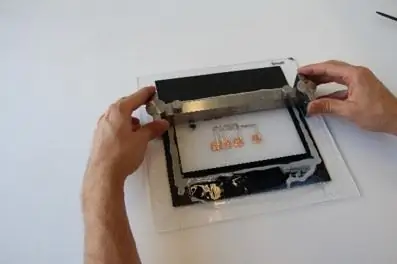
Dieser ist auch mehr von dem, den Sie zuvor gemacht haben. Am wichtigsten ist hier die Höhe, auf der Sie die Klinge beschichten. Die vorherige Schicht (Komponentenschicht) war 1 mm (empfohlene LED war 0,7 mm dick + 0,3 mm wie zuvor vorgeschlagen). Für jede Schaltungsschicht wird oben eine Höhe von 0,5 mm Silikon hinzugefügt, um genügend Spielraum für ungleichmäßige Beschichtungen mit Flüssigmetall zu lassen. Die Höhe, auf der Sie hier beschichten, wird daher 1 mm + 0,5 mm = 1,5 mm.
Detaillierte Schritte in Kürze:
• Legen Sie das Acrylkitt-Kit um den erforderlichen Umfang der Silikonfolie herum
•Mix 2 Komponenten Shore 15 Härte Platin Polyadditionssilikon
• Gießen Sie in Mastix-„Pool“, beginnend in der Mitte und auf alle Komponenten
•Klingenbeschichtung eine Silikonschicht mit einer Höhe von 0,5 mm > aktuelle Stapeldicke
•Warten Sie, bis das Silikon aushärtet
Schritt 13: Schablonenmaske für die untere leitfähige Schicht
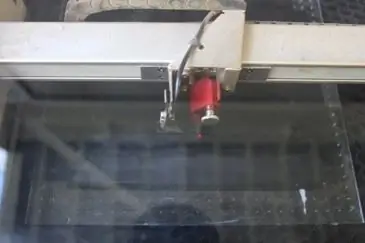
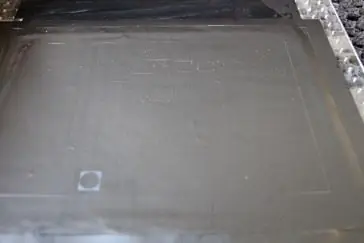
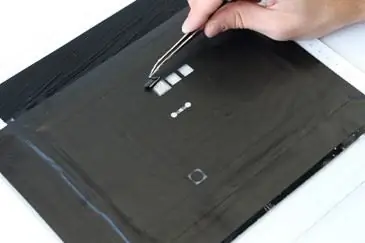
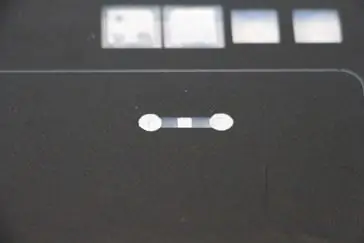
Und wir haben jetzt die einfachen Teile vollständig eingegeben! Was Sie hier finden, ist alles Wiederholung. Jede Schaltungsschicht, die Sie darüber anwenden, ist eine Wiederholung der Schritte, die für vorherige Schaltungsschichten ausgeführt wurden. Hier müssen Sie eine Schablonenmaske für die Schaltungsebene 2 erstellen.
Ohne zu viel Ausarbeitung:
• Aufkleber zuschneiden (ca. Plattenmaße)
• Aufkleber anbringen, ohne Luftblasen einzuführen
•Untere Kupferleiterbahnen mit Laserschneider schneiden (W à Kalibrierung)
• Aufkleber in Bereichen entfernen, die leitfähig gemacht werden müssen (Leiterbahnen, Pads)
•Stellen Sie sicher, dass Ihr Aufkleber gut an den Kanten des exponierten Bereichs haftet
• Freiliegendes Silikon mit Isopropylalkohol reinigen
Schritt 14: VIAs von oben nach unten
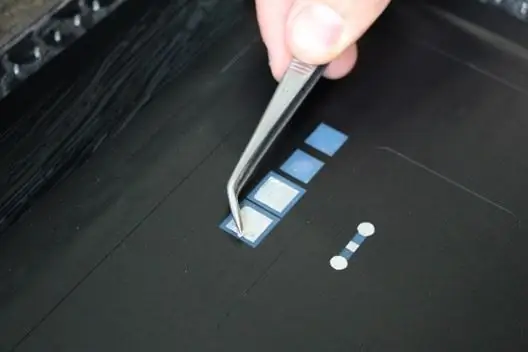
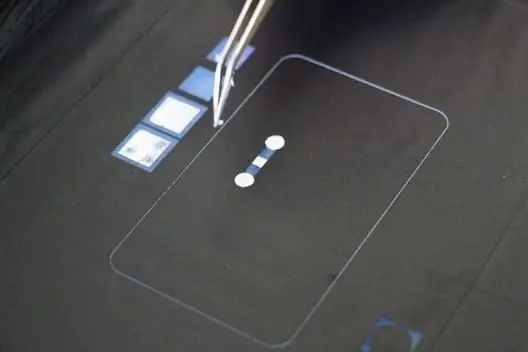
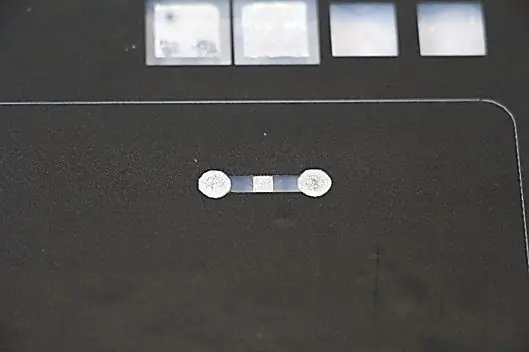
Die einzige Neuheit liegt an den Stellen, an denen wir eine Verbindung zwischen 2 aufeinanderfolgenden Schaltungsschichten benötigen. Im Fachjargon werden diese als Vertical Interconnect Access oder kurz VIA bezeichnet. Um eine Durchkontaktierung zu erstellen, müssen Sie eine Öffnung in das Silikon schneiden, die eine vorherige Schaltungsschicht bedeckt. Wenn Sie dann für die nächste Schaltungsschicht neues Flüssigmetall darauf drucken, fließt es in diese Öffnung und verbindet sich elektrisch.
Sie müssen zuerst den Laser kalibrieren (siehe: Kalibrierung), um die Silikondeckschicht auf der vorherigen Schaltungsschicht genau zu durchschneiden. Schneiden Sie dann einfach die VIA's gemäß der mitgelieferten Datei aus. Entfernen Sie jeden Ausschnitt der Silikondeckschicht mit einer Pinzette und fahren Sie mit dem nächsten Schritt fort: Drucken einer neuen Flüssigmetall-Schaltungsschicht darauf!
Erstellen von VIAs, eine kurze Version:
•Mit der Schablonenmaske der unteren leitfähigen Schicht
• Kalibrieren Sie den Laser, um präzise durch die Silikonschicht zu schneiden, um die obere leitfähige Schicht freizulegen (12-17 W)
• Schneiden Sie VIAs durch das gesamte Silikon, wo die obere und untere leitfähige Schicht miteinander verbunden werden müssen
• Entfernen Sie das ausgeschnittene Silikon, um die obere leitfähige Schicht freizulegen
Schritt 15: Untere leitfähige Schicht
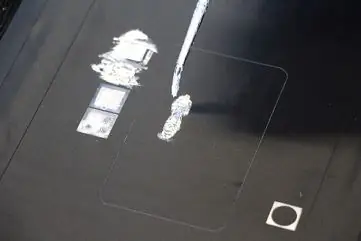
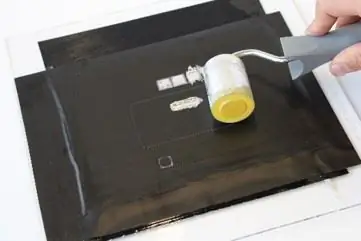
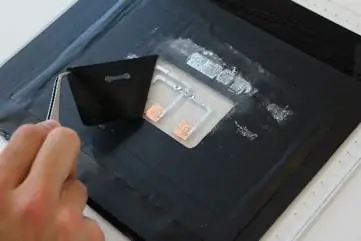
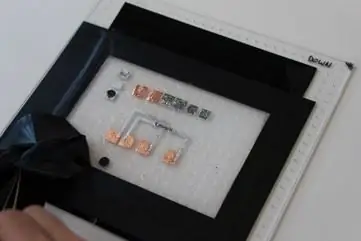
Stellen Sie auch hier sicher, dass Ihr Arbeitsraum abgedeckt ist, wenn Sie mit flüssigem Metall arbeiten. Dadurch wird es viel einfacher, mit Verschüttungen umzugehen.
Das Drucken dieser Schicht ist wieder eine Wiederholung früherer Bemühungen. Stellen Sie sicher, dass die Schablone an den Rändern gut am Silikon haftet. Wir wollen nicht, dass darunter flüssiges Metall durchfließt. Nochmals im Tauchverfahren flüssiges Metall mit einem feinen Pinsel auf die Schablonenöffnungen auftragen. Nehmen Sie die Walze und rollen Sie das überschüssige flüssige Metall zur Seite. Gewinnen Sie große Klumpen flüssigen Metalls mit einer Plastikpipette.
Eine andere TL;DR-Version:
•Verwenden Sie einen Pinsel, um alle exponierten Stellen grob mit Galinstan. abzudecken
•Verwenden Sie die Walze, um das aufgetragene Galinstan zu einer gleichmäßigen Beschichtung zu machen
•Entfernen Sie die Aufkleberschablone vorsichtig
•Wenn Galinstan beim Entfernen in Bereiche fließt, in denen es nicht sein sollte, war Ihre Beschichtung zu dick. Oberfläche reinigen und bei Schritt 13 neu starten.
•Verwenden Sie den Pinsel, um jedes VIA auszubessern und stellen Sie sicher, dass die oberen und unteren leitfähigen Schichten verbunden sind
Schritt 16: Cast / Blade Coat Silikon
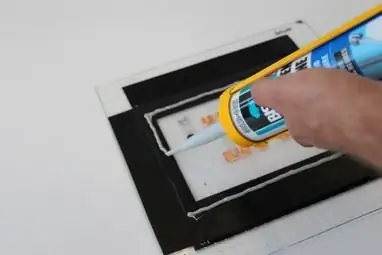
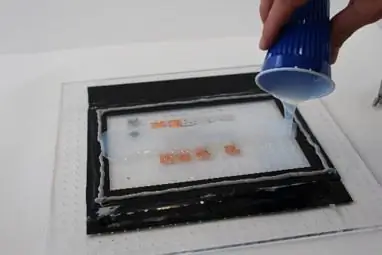
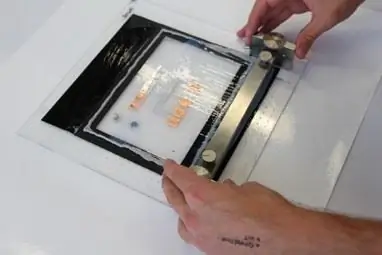
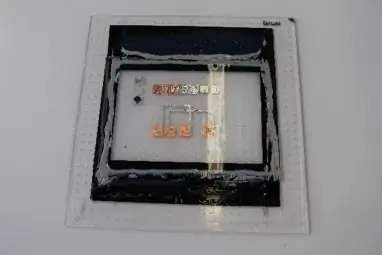
Sie können jetzt anfangen, sich zu freuen! Dies ist unsere letzte Schicht aus Gießsilikon, was bedeutet, dass Ihre weiche Schaltung fast fertig ist! Das haben Sie schon zweimal gemacht. Also halte ich es kurz und sage Ihnen, welche Höhe Sie für die Klingenbeschichtung anstreben sollten. Wir haben bereits eine 1 mm dicke Bauteilschicht und eine 0,5 mm dicke erste Schaltungsschicht. Diese Schaltungsschicht sollte ebenfalls 0,5 mm dick sein. Daher in diesem Schritt Klingenbeschichtung mit 2mm Gesamtdicke!
Überholspur:
• Legen Sie das Acrylkitt-Kit um den erforderlichen Umfang der Silikonfolie herum
•Mix 2 Komponenten Shore 15 Härte Platin Polyadditionssilikon
• Gießen Sie in Mastix-„Pool“, beginnend in der Mitte und auf alle Komponenten
•Klinge beschichten eine Silikonschicht mit einer Höhe von 500 um > aktuelle Stapeldicke
•Warten Sie, bis das Silikon aushärtet
Schritt 17: Kontaktpads
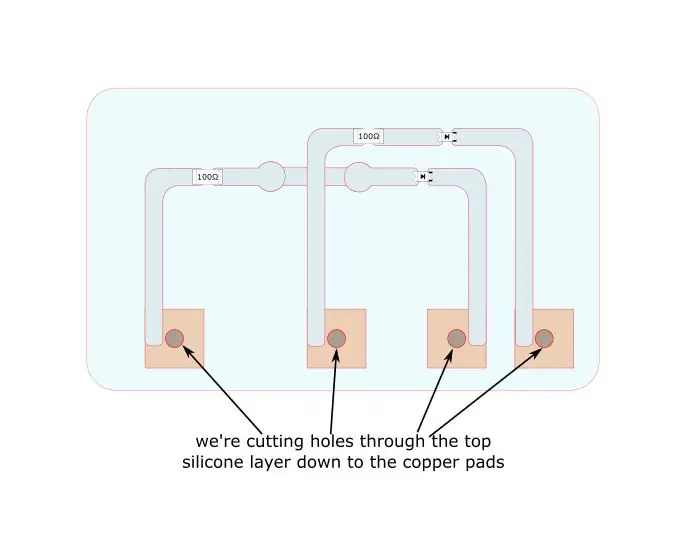
Während Silicone Devices Stromversorgung (Batterie) und Verarbeitung (Mikrocontroller) einbetten können, fügen wir der Einfachheit dieses Beispiels externe Anschlüsse hinzu, um die LEDs mit Strom zu versorgen. In diesem Schritt schneiden wir das Silikon bis zu den Kontakten durch, die wir innen eingebettet haben. Auch hier müssen Sie den Laser kalibrieren (siehe: Kalibrierung), um darunterliegende Schichten nicht zu beschädigen. Wenn Sie die Schnitte gemacht haben, reißen Sie die Silikonausschnitte mit einer Pinzette aus. Kratzen Sie dann überschüssige Silikonreste von Ihren Kontakten ab und reinigen Sie sie mit Wattestäbchen und tragen Sie für zusätzliche Zuverlässigkeit Lötzinn auf die Kontakte auf.
Kontaktpads, eine kurze Geschichte:
• Laser kalibrieren, um die Silikonschicht zu durchschneiden und Kupferbandkontakte freizulegen (20-30 W)
•Schaltkreiskontakte mit Laserschneider schneiden
• Silikon in Ausschnittbereichen entfernen
•Reinigen Sie freiliegende Kupferpads mit einem schnell trocknenden Lösungsmittel
•Lot auf freiliegende Pads auftragen, bis die Kontakte mit dem Silikon auf gleicher Höhe sind. Löten Sie weiter, während Sie überschüssiges Silikon von Ihren Kontakten abkratzen und Schmutz entfernen, bis Ihr Lötmittel am Pad haftet.
Schritt 18: Probe frei schneiden
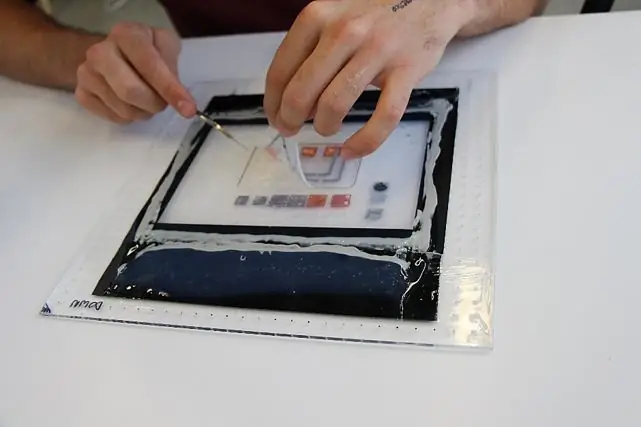
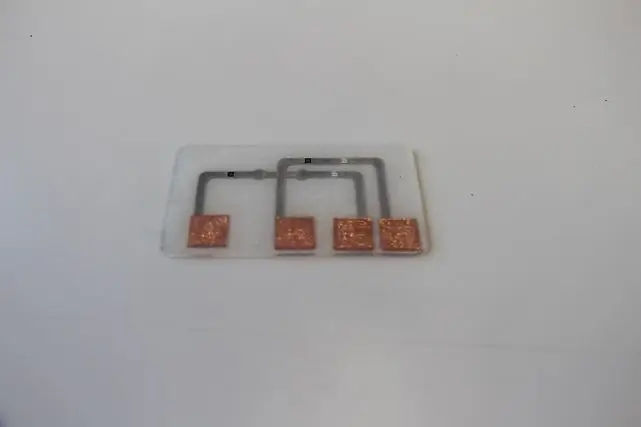
Es ist Zeit, Ihren Soft-Circuit von seiner Trägerplatte zu befreien! Da unsere Transferplatte unter unserer Weichschaltung nicht mit Primer beschichtet wurde, müssen wir nur die Seiten abschneiden und können sie abnehmen. Verwenden Sie zum Ausschneiden der Probe die hier beigefügte Schnittdatei. Wiederholen Sie die Schnitte mit zunehmender Leistung, bis die Probe frei wird. Der Z-Offset Ihres Lasers sollte -1 (die Hälfte der Stapelhöhe) betragen. Wenn der Probenausschnitt komplett durchbohrt ist, heben Sie eine Ecke von einer Seite an und schneiden Sie dann Ihren Soft-Circuit frei von allen darunter liegenden Befestigungen, die in der Trägerplatte Luftlöcher gebildet haben. Schauen Sie es sich gut an: Ihr erstes Silikongerät! Ein anschmiegsamer, dehnbarer und weicher Kreislauf!
Beispiel in Aufzählungszeichen freigeschnitten:
• Laser kalibrieren, um den kompletten Silikonstapel zu durchschneiden (40-60W)
•Probenumriss mit Laserschneider ausschneiden
•Heben Sie die Probe von der Platte, während Sie sie manuell von den Silikonansätzen freischneiden, die sich in den Luftlöchern der Transferplatte gebildet haben
Schritt 19: Bewundern Sie
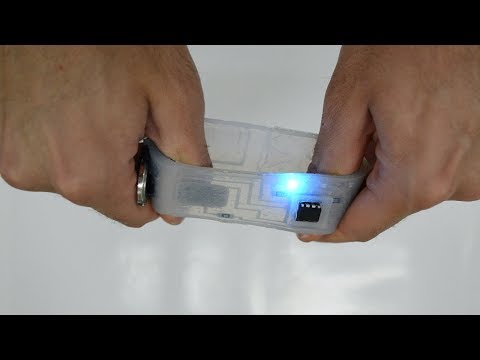
Schließen Sie nun Ihr Silikongerät an eine 5V-Stromversorgung an. Jeder Stecker-Widerstand-LED-Steckerpfad hat einen separaten Strombedarf. Sie können beide parallel schalten. Behalten Sie einfach die Polarität Ihrer LED im Auge und passen Sie Ihre Stromanschlüsse entsprechend an. Sobald Ihre Soft-Schaltung mit Strom versorgt wird, sollte die blaue LED aufleuchten.
Geben Sie Ihrer Schaltung eine Dehnung! Wenn Sie es richtig gemacht haben, sollten Sie leicht 50% Dehnung erreichen, ohne die Schaltung zu beschädigen. Hauptfehlerquelle werden Ihre Kontaktpads sein, da diese aus starren Folien bestehen, die bei hoher Belastung auseinanderreißen.
Die folgenden Adjektive passen zu Ihrem Silikongerät:
•Flexibel
•Weich/dehnbar
•Selbstheilung
•Durchscheinend
•Vollständig gekapselt
Anwendungsbereiche, die ich vorsehe: Biomonitoring-Patches (auf der Haut), Wearables, in Textilien eingebettete Silikongeräte, elektronische Schaltungen, die mechanische Gelenke überspannen, Antriebs- oder Sensorelektronik für weiche Roboter, …
Welche Anwendungen scheinen Ihrer Meinung nach für diese einzigartigen Arten von weichen Schaltkreisen geeignet zu sein? Lass es mich in den Kommentaren wissen! Ich kann es kaum erwarten zu sehen, was euch einfällt. Lassen Sie mich wissen, wenn Sie etwas Einzigartiges bauen. Wer weiß, vielleicht kann ich dir einen Rat geben!
Viel Glück beim Experimentieren, Danke schön, Noagel