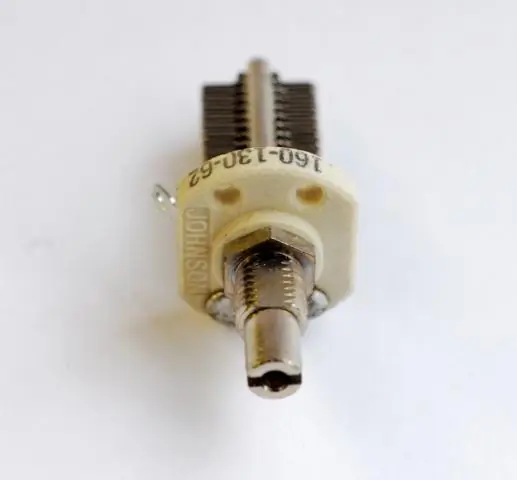
Inhaltsverzeichnis:
- Schritt 1: Markieren des Zentrums für Pilotlöcher
- Schritt 2: Zeichnen Sie einige Kreise
- Schritt 3: Markierungslinien für die Statorplatten
- Schritt 4: Schneiden
- Schritt 5: Markieren der Löcher für den Stator
- Schritt 6: Markieren des inneren Kreises
- Schritt 7: Schneiden des Bogens
- Schritt 8: Bohren
- Schritt 9: Drehen mit einem Bohrer
- Schritt 10: Formen der Statorplatten
- Schritt 11: Von diesem zu dem
- Schritt 12: Machen Sie Ihre eigenen Unterlegscheiben
- Schritt 13: Fertigstellen Ihrer Unterlegscheiben
- Schritt 14: Rotor- und Statorbaugruppe
- Schritt 15: Das Gehäuse
- Schritt 16: Der Isolator
- Schritt 17: Plastikglaskappen
- Schritt 18: Fertig
2025 Autor: John Day | [email protected]. Zuletzt bearbeitet: 2025-01-23 12:53
Ich baute ein Kristallset für meinen Sohn, aber es kam zum Stillstand. Als ich herausfand, dass ich keinen variablen Kondensator in meinem Müllhaufen habe. Einen aus einem alten Radio zu holen, war keine Option. Da die meisten neuen Radios analoges Tuning verwenden. Und die mit Luft-Wechselkondensatoren sind sehr selten und sind Sammlerstücke. Ich habe einmal einen Artikel über den Bau eines Luft-Wechselkondensators gelesen. Also beschloss ich, mein eigenes aus Aluminiumblechresten und Dingen zu bauen, die leicht im Haus zu finden sind. Wenn Sie einen Bohrer, eine Schere, eine Feile und etwas Schleifpapier haben. Diesen kannst du ganz einfach bauen. Es erfordert nicht viel Geschick.:-) Ich habe meine aus Aluminiumblechen mit einer Dicke von 1,5 und 2 mm hergestellt. Das Gehäuse ist aus einem Aluminium-Kühlkörper, ich schaffe es auch, 3 Stück Schrauben mit ein paar Muttern aus meiner Trödelkiste zu holen. Die Plastikbuchse, die auch als Isolator fungiert, besteht aus einem Plastikstift und einigen Plastikdeckeln. Ich habe auch meine eigenen Unterlegscheiben / Abstandshalter aus dem 2 mm dicken Aluminiumblech hergestellt. Die Kontakte des Rotors, der auch als Spanner fungiert. Waren von einem kaputten Waschmaschinen-Timer. Sie können mit der Anzahl der Platten und der Größe der Op-Abstände experimentieren, indem Sie weitere Platten und Unterlegscheiben im Rotor und Stator hinzufügen.
Schritt 1: Markieren des Zentrums für Pilotlöcher
In diesem Schritt führen wir die Messungen durch. Legen Sie das Aluminiumblech flach auf Ihre Werkbank. Zeichnen Sie von einem Ende ein Quadrat mit den Maßen 5 x 5 cm. Verwenden Sie einen scharfen Gegenstand wie einen Nagel oder eine Feile. Holen Sie sich die Mitte und schlagen Sie mit einem kleinen Nagel ein Loch hinein. Stanzen Sie alle 5 Zentimeter ein Loch entlang der geraden Linie, wie auf dem Foto gezeigt.
Schritt 2: Zeichnen Sie einige Kreise
Hier werden wir Kreise auf das Blatt zeichnen. Wir können Kreise perfekt mit einem Zirkel zeichnen. Wenn Sie keinen Zirkel haben. Sie können improvisieren, indem Sie zwei kleine Nägel auf ein kleines Stück Holz schlagen. Setzen Sie einen Nagel in das Loch ein, das Sie auf dem Blatt gemacht haben, und drehen Sie ihn. Es ist wichtig, dass sich die Kreise nicht überlappen. Damit wir beim späteren Ausschneiden genügend Platz haben. Sie können beliebig viele Kreise machen, wenn Sie genügend Aluminiumblech haben. Es ist besser, einen Ersatz zu haben, wenn Sie einen falschen Schnitt gemacht haben. Dann wiederholen Sie den gleichen Vorgang, wenn Sie mitten in Ihrem Projekt keine Teile mehr haben.
Schritt 3: Markierungslinien für die Statorplatten
Zeichnen Sie mit einem Tri-Quadrat eine Linie von der Kante des Blattes bis zur Mitte des Bogens. (Derjenige, auf den ein Stift auf dem Foto zeigt) Dies ist wichtig, da jedes Teil eine einheitliche Größe haben muss. Und dies dient auch als Leitfaden, wenn wir sie ausschneiden.
Schritt 4: Schneiden
Mit einer großen Schere und einem starken Griff. Sie können alle Teile leicht ausschneiden. Und dann jedes Stück mit einem Gummihammer flachdrücken. Sie können auch einen Hammer verwenden. Aber sei sehr sanft.
Schritt 5: Markieren der Löcher für den Stator
Holen Sie sich ein Stück und ziehen Sie eine Linie von der Mitte. Gehe in die linke Ecke. Holen Sie sich die Mittellinie (von der Ecke zum Bogen) und stanzen Sie ein Loch hinein. Markieren Sie dieses Stück als Muster. Legen Sie es auf ein anderes Stück. Und bohre ein Loch in das zweite Stück darunter. Verwenden Sie das Loch im ersten Teil als Schablone. Drehen Sie das Muster um und stanzen Sie das zweite Loch. Wir tun dies, weil wir alle Rotor- und Statorplatten nacheinander bohren. Ich empfehle nicht, alle Teile zu stapeln und sie alle auf einmal zu bohren. Der Bohrer neigt immer zum Verbiegen. Oder Sie können, wenn Sie eine Bohrmaschine haben
Schritt 6: Markieren des inneren Kreises
Improvisieren Sie erneut einen Zirkel, um den inneren Kreis zu zeichnen. Schneiden Sie ihn mit einer Schere von beiden Enden bis zum Bogen des inneren Kreises. Passen Sie auf, dass Sie es nicht bis zur Mitte schneiden.:-) wenn alle Stücke geschnitten sind. Drücken Sie sie wieder mit einem Gummihammer flach.
Schritt 7: Schneiden des Bogens
Hier werden wir den Bogen schneiden, der noch den Rotor und die Statorplatten verbindet. Sie können es immer mit einer Schere schneiden. Aber es ist einfacher und schneller, wenn Sie einen gebogenen Meißel verwenden. (derjenige, den Holzschnitzer verwenden) Ich habe einen, aber ich möchte ihn nicht ruinieren.:-) Also habe ich einen aus einer kleinen Pfeife gemacht. Schärfen Sie es an einem Ende mit einer Feile. Und die Hälfte davon entfernt. Damit es wie ein gebogener Meißel ist. Lassen Sie sich beim Schneiden nicht verwirren. Der Rotor muss das Teil mit einem Loch darin haben. (Hier sind die Ersatzteile praktisch:-)
Schritt 8: Bohren
Jetzt haben wir unseren Rotor und Stator. Es ist Zeit, die Löcher größer zu machen. Mit Hilfe eines Bohrers. Finden Sie Schrauben (3Stk.) mit Muttern (ich habe 12 Stück Muttern verwendet, weil ich den Kopf jeder Schraube entfernt habe, damit ich meine Varicap an beiden Enden öffnen kann.) Ich habe eine 4mm verwendet. Bohrer. Finden Sie Schrauben, die perfekt in die Löcher passen, speziell für den Rotor
Schritt 9: Drehen mit einem Bohrer
In dieser Phase werden wir unsere Rotorplatten zu perfekten Bögen machen. Und um Grate und scharfe Kanten zu entfernen. Mit Hilfe eines Bohrers und einer groben Feile und etwas Sandpapier. Stapeln Sie alle Rotorplatten einander gegenüber und bilden Sie einen Kreis. (Wir tun dies, um Vibrationen zu vermeiden, wenn wir sie mit einem Bohrer drehen) Setzen Sie die Schraube ein und ziehen Sie die Mutter fest. Stecken Sie das Ende der Schraube in das Bohrfutter des Bohrers. Wie ein normaler Bohrer. Schalten Sie den Bohrer ein und verwenden Sie die Feile, um die Seiten der Rotorplatten zu glätten. Seien Sie sehr vorsichtig, stellen Sie den Bohrer auf niedrige Geschwindigkeit ein. Drücken Sie nicht lange auf den Bohrerschalter. (die Mutter kann sich lockern) Wenn dies passiert, kehren Sie die Richtung des Bohrers um. Mit feinem Sandpapier abschließen
Schritt 10: Formen der Statorplatten
Wir werden die Statorplatten in diesem Teil meines instructable formen. So wie wir es mit unseren Rotorplatten gemacht haben. Wir werden auch alle Statorplatten stapeln. Setzen Sie die Schrauben in jedes Loch ein und ziehen Sie die Muttern fest. Wenn Sie einen Schraubstock haben, umso besser. Wenn Sie das Foto klar sehen können. Die zu entfernenden Teile habe ich mit einem schwarzen Stift eingefärbt. Oder folgen Sie einfach dem Bogen und vermeiden Sie den Kopf der Schraube und der Mutter. Seien Sie geduldig, Sie können dies mit einer groben Feile tun. Denken Sie daran, dass Aluminium nicht so schwer zu bearbeiten ist.:-)
Schritt 11: Von diesem zu dem
Zu diesem Zeitpunkt müssen Ihre Stücke wie das dritte Stück auf diesem Foto aussehen. Gut erledigt. An dieser Stelle können Sie auch die Farbe entfernen. Wenn sie Farbe haben. Und überprüfen Sie noch einmal auf Kurven oder ob sie jemals schief sind.
Schritt 12: Machen Sie Ihre eigenen Unterlegscheiben
Stellen Sie Ihre eigenen Unterlegscheiben/Abstandshalter her. Von einer schwereren Spur oder vom gleichen Blatt. Sie benötigen jedoch 2 Stk. Von Unterlegscheiben/Abstandshaltern für jede Lücke. Ich empfehle, die gleiche Dicke wie die Stator- und Rotorplatten zu verwenden. Leichtere Dicke ist viel einfacher zu schneiden. Schneiden Sie einen Aluminiumstreifen von etwa 1 cm ab. weit. Bohren Sie Löcher mit dem gleichen Bohrer, den Sie für die Stator- und Rotorplatten verwendet haben. Schneiden Sie den Streifen in Quadrate. Stellen Sie sicher, dass sich das gebohrte Loch in der Mitte befindet. Setzen Sie die Schraube mit dem Kopf nach oben ein. Schneiden Sie dann die Ecken mit dem Kopf der Schraube als Führung ab, wie auf dem Foto zu sehen.
Schritt 13: Fertigstellen Ihrer Unterlegscheiben
Wie Sie es mit den Rotorplatten gemacht haben. Hämmern Sie sie vorsichtig, um sie flach zu machen. Stapeln Sie sie, setzen Sie die Schraube ein, ziehen Sie die Mutter fest. Und wieder mit einem Bohrer drehen und mit einer Feile glätten und mit einem feinen Sandpapier abschließen.
Schritt 14: Rotor- und Statorbaugruppe
Entfernen Sie den Kopf jeder Schraube. Setzen Sie eine Mutter auf ein Ende jeder Schraube. Drehen Sie die Nuss bis 5cm. der Schraube ragt aus der Mutter heraus. Holen Sie sich eine der Schrauben, setzen Sie sie auf eine Statorplatte, gefolgt von zwei Unterlegscheiben. Und wieder eine Statorplatte und zwei Unterlegscheiben. Wiederholen Sie diesen Schritt, bis Sie fertig sind. Lassen Sie genügend Platz für 2 Schrauben und zwei Unterlegscheiben und vergessen Sie nicht die Welle, auf der Sie einen Knopf platzieren können
Schritt 15: Das Gehäuse
Ich habe das Gehäuse aus einem Aluminiumkühlkörper hergestellt, der aus einem Fernsehgehäuse geborgen wurde. Es sind mehr oder weniger 2 mm. dick. Darauf legte ich Rotor und Stator. 1 mm Abstand lassen. Zwischen Rotor und Stator. Markieren Sie die 3 zu bohrenden Löcher mit den Rotor- und Statorlöchern als Schablone. Dann alle Löcher mit dem gleichen Bohrer gebohrt, der für die Rotor- und Statorplatte verwendet wurde. Dann habe ich es einfach in eine dreieckige Form geschnitten und alle Ecken abgerundet.
Schritt 16: Der Isolator
Suchen Sie nach etwas, das die Achse des Rotors von der Endplatte / dem Chassis isoliert. Wie zum Beispiel ein Gummischlauch aus einer Kraftstoffleitung eines Autos. Da ich kein Auto besitze. Ich habe nur einen Plastikstift für eine Buchse verwendet. Hinweis: Suchen Sie nach dem richtigen Stift, bevor Sie das obere Loch vergrößern. Bohren Sie nicht, bis Sie Ihre Buchse haben:-)
Schritt 17: Plastikglaskappen
Schneiden Sie zwei dreieckige Plastik aus den Glasdeckeln. Oder einen beliebigen Kunststoff Ihrer Wahl. Dieser Kunststoff isoliert den Rotorkontakt vom Aluminiumgehäuse. Ich habe meinen Kontakt nur vorübergehend geklebt. Ich werde es später mit einem Kupferstecker ändern. Diejenigen, die wie Unterlegscheiben aussehen, wie sie für die Masseverbindung verwendet werden.
Jetzt legen Sie einfach die beiden dreieckigen Kunststoffe auf beiden Seiten. Gefolgt von den beiden dreieckig geformten Aluminium und fertig. Denken Sie daran, wenn Sie zwei Statorplatten haben, müssen Sie drei Rotorplatten haben. 4/5, 5/6 usw. Ich hoffe, dass dieses instructable von großer Hilfe sein wird. Vielen Dank:-)
Schritt 18: Fertig
Hier ist der fertige variable Kondensator. Installiert auf einem Quarz-Kurzwellenempfänger.
Empfohlen:
Wie man aus einem alten Computer einen persönlichen Mini-Schreibtischventilator macht – passt in Ihre Tasche – wikiHow
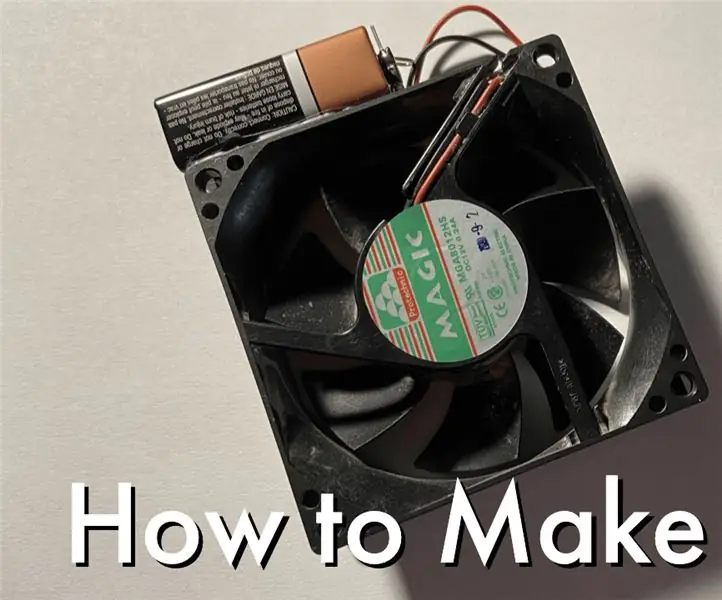
Wie man aus einem alten Computer einen persönlichen Mini-Schreibtischventilator macht – passt in Ihre Tasche: Ich zeige Ihnen, wie Sie aus einem alten Computer einen persönlichen Mini-Schreibtischventilator machen. Ein Bonus ist, dass es sogar in Ihre Tasche passt. Dies ist ein sehr einfaches Projekt, daher ist nicht viel Erfahrung oder Fachwissen erforderlich. Fangen wir also an
Das Glück geht aus - Spiel: 7 Schritte
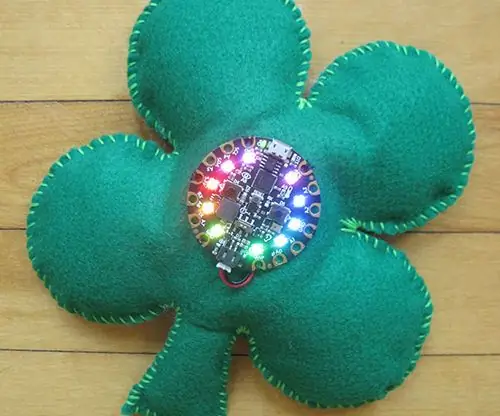
Luck's Running Out - Game: Dies ist ein Spiel der Geschwindigkeit und des Zufalls, ähnlich wie heiße Kartoffeln, das Klee wird herumgereicht, bis das Lied und die Animation zu Ende sind. Dieses Spiel macht am meisten Spaß, wenn es mit einer kurzen Aufgabe kombiniert wird, bevor Sie das Kleeblatt passieren. Ich bin kein technisch versierter Mensch
Uhrzeit und Datum aus dem Internet abrufen - Tutorial: 9 Schritte
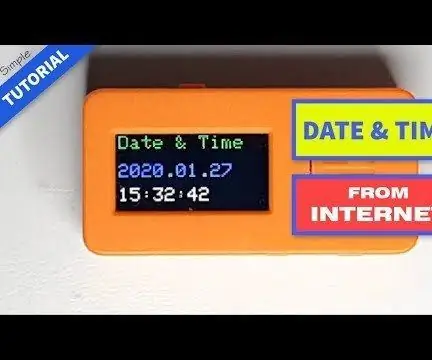
Abrufen von Uhrzeit und Datum aus dem Internet - Tutorial: In diesem Tutorial erfahren Sie, wie Sie mit M5Stack StickC und Visuino das Datum und die Uhrzeit vom NIST TIME-Server abrufen. Sehen Sie sich ein Demonstrationsvideo an
So tauschen Sie die CPU im Toshiba Satellite C55-A5300 aus – wikiHow
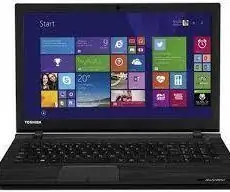
So tauschen Sie die CPU im Toshiba Satellite C55-A5300: So tauschen Sie die CPU im Toshiba Satellite C55-A5300
Wie poste ich auf Instagram vom Computer aus?: 9 Schritte
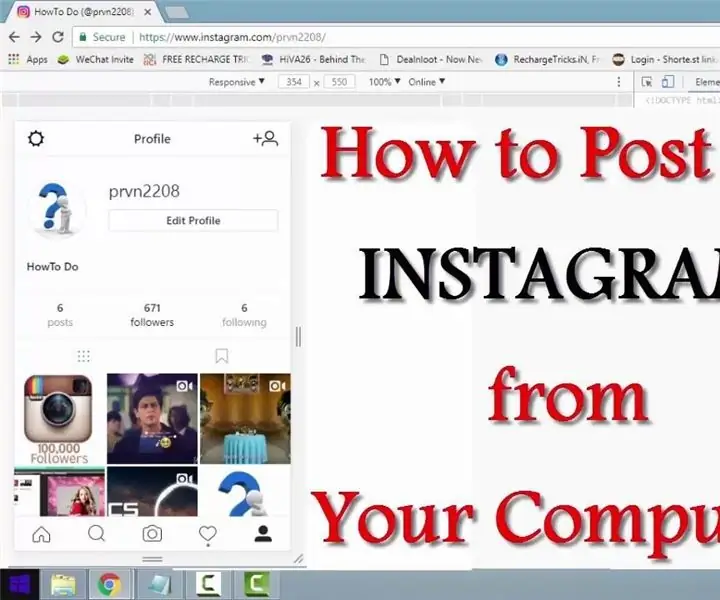
Wie poste ich auf Instagram vom Computer aus?: Instagram bekommt von Tag zu Tag mehr Aufmerksamkeit und ist jetzt eine der beliebtesten Social-Media-Plattformen der Welt. Menschen können mit Hilfe ihres Instagram-Kontos Bilder, Videos und Insta-Geschichten teilen. Mit regelmäßigen und interes