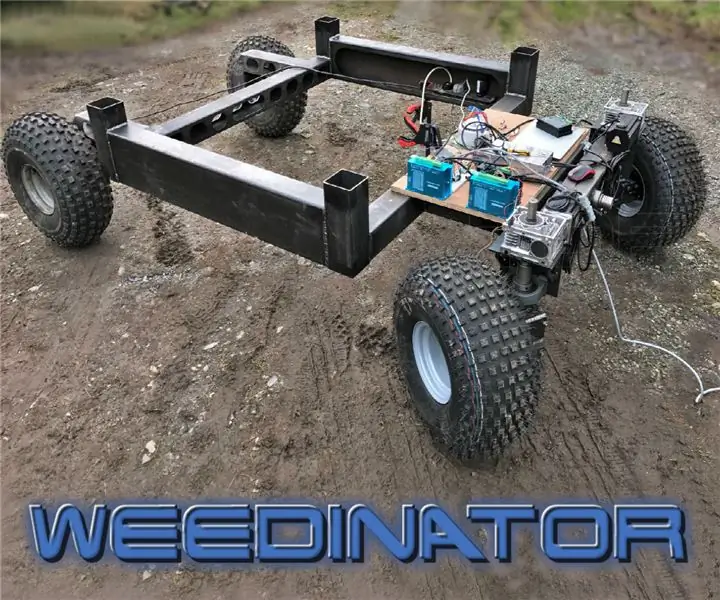
Inhaltsverzeichnis:
- Schritt 1: Werkzeuge und Komponenten
- Schritt 2: Verwenden der Oberflächenplatte
- Schritt 3: Aufbau der schwenkbaren Vorderachse
- Schritt 4: Aufbau der Hinterachsbaugruppe
- Schritt 5: Ovale Slots in 100 x 100 Boxen herstellen
- Schritt 6: Ausstecken der 200 X 100 Box
- Schritt 7: Fertiges Chassis
- Schritt 8: Nächste Schritte
2025 Autor: John Day | [email protected]. Zuletzt bearbeitet: 2025-01-23 12:52
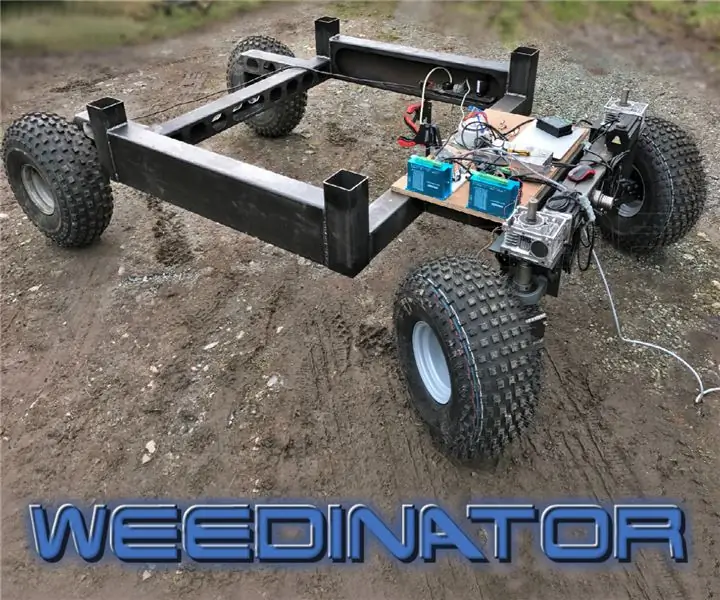
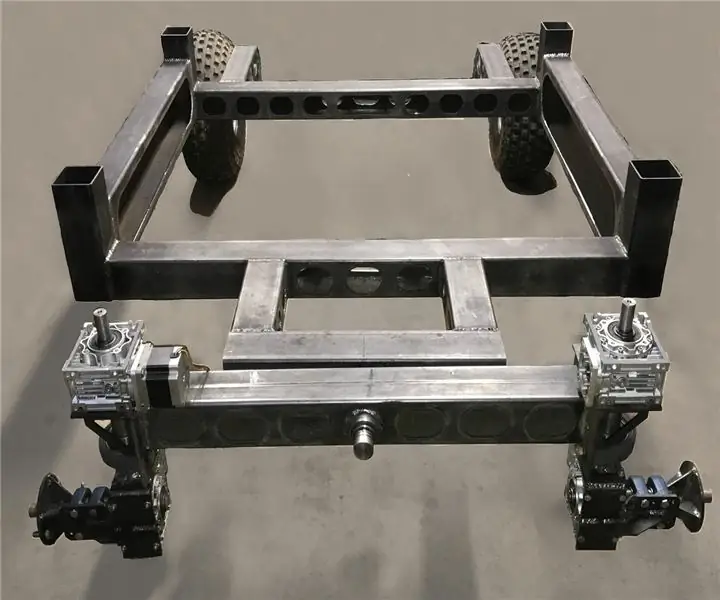
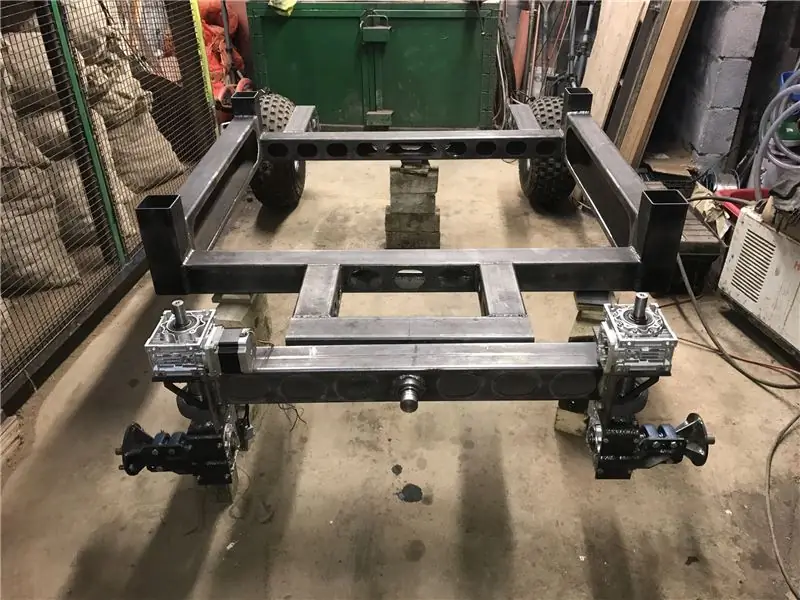
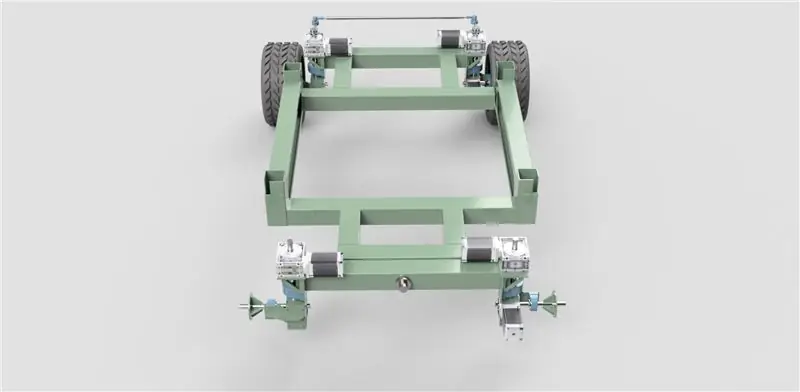
Der Winter ist die perfekte Zeit, um Maschinen zu bauen, insbesondere wenn es um Schweißen und Plasmaschneiden geht, da beide eine ordentliche Menge Wärme liefern. Wenn Sie sich fragen, was ein Plasmaschneider ist, lesen Sie weiter, um detaillierte Verfahren zu erhalten.
Wenn Sie den Fortschritt des Weedinator verfolgt haben, zeigte Stufe eins den Antriebs- / Lenk- / Federungsmechanismus und seitdem habe ich das Federungssystem für eine einfachere Version meines International 454-Traktors abgeschafft. Bei diesem System bleiben die Hinterräder am Chassis fixiert, während die Vorderräder auf einer einzigen Achse schwenken. Dieses System bietet sich an, wenn die Lenkung mit einer Spurstange verbunden ist, mit der das Spiel im Getriebe beseitigt und Kräfte ausgeglichen werden können, die durch Beschleunigung, Reibung oder Bremsen an den Rädern selbst entstehen.
Funktioniert die Lenkung bei angetriebenen/gebremsten Rädern? Ich denke, es wird auf das Drehmomentverhältnis der jeweiligen Systeme ankommen, dass die Lenkung ausreichend kraftvoll sein muss, um die Übertragungskräfte zu bewältigen. Klingt kompliziert? Ergebnisse werden erzielt, wenn der Weedinator Anfang 2018 aus der Werkstatt gerollt und getestet wird.
Schritt 1: Werkzeuge und Komponenten
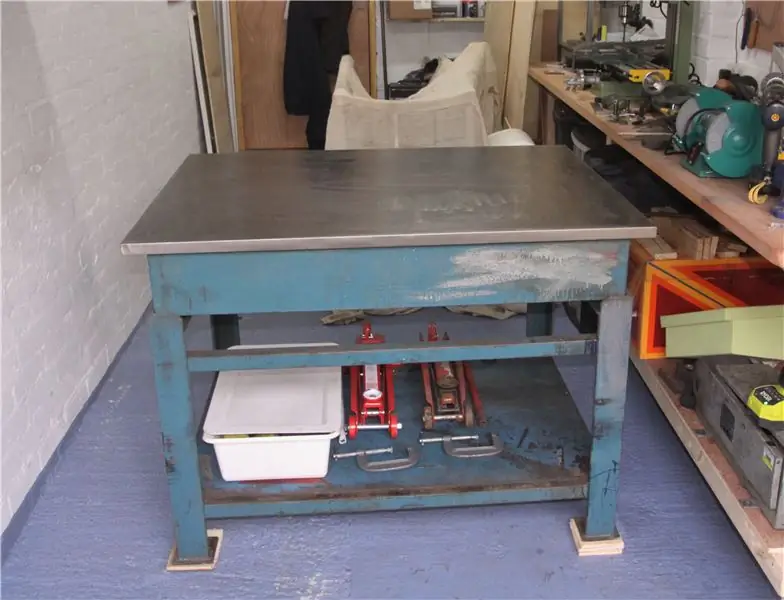
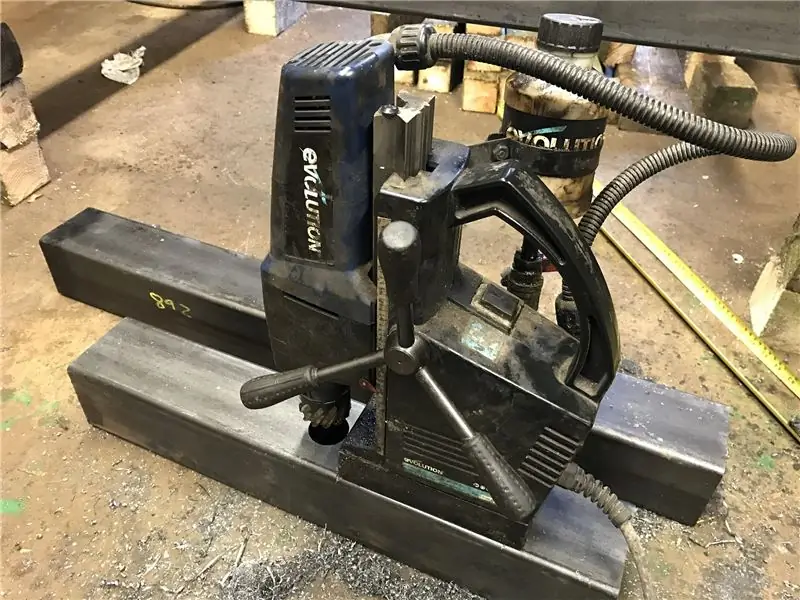
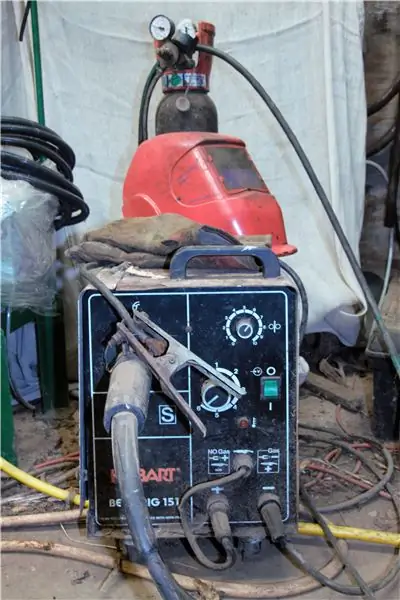
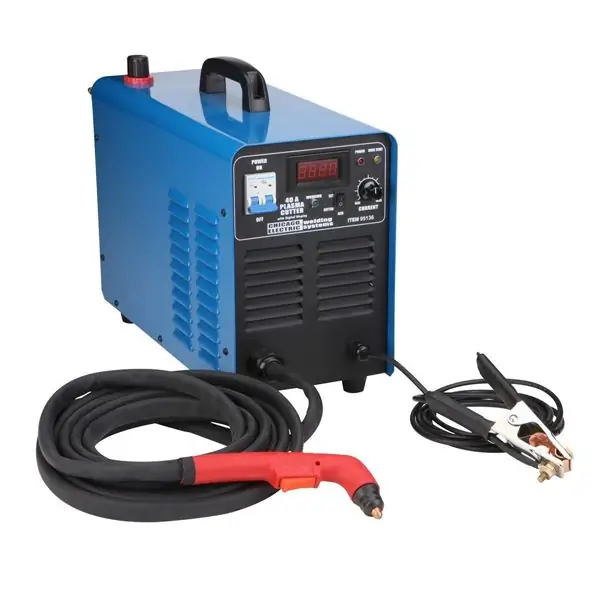
- Nivelliertisch / Richtplatte
- MIG-Schweißer
- Plasma Schneider
- Klemmen
- Halbrunde grobe 12" Feile
- 100 x 100 x 4 mm Kastenprofil
- 200 x 100 x 5 mm Kastenprofil
- Magnet-Räumbohrmaschine
- 40mm Räumbohrer
- 60mm Räumbohrer
- 6 x 617082RS Dünnschliff-Rillenkugellager 40x50x6mm (61708-2RS-EU)
- Achsschenkel für 4" 12mm Rad PCD …. 2 of
- Wasserwaage
Schritt 2: Verwenden der Oberflächenplatte
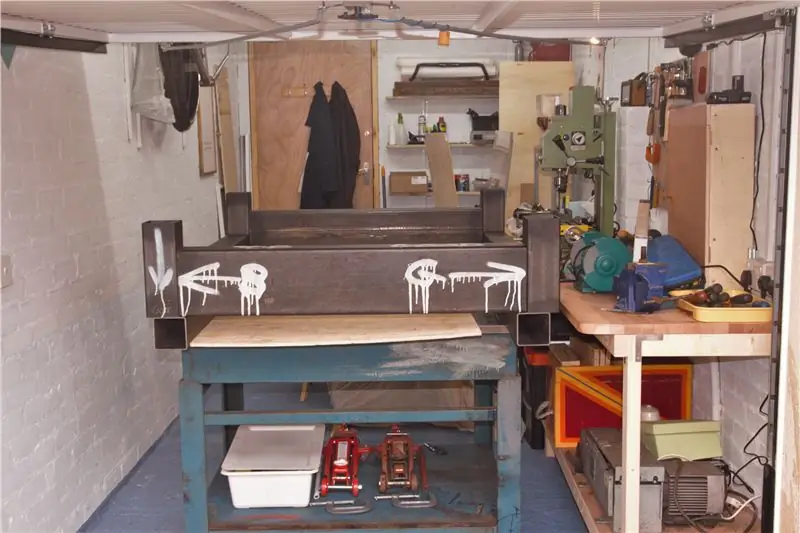
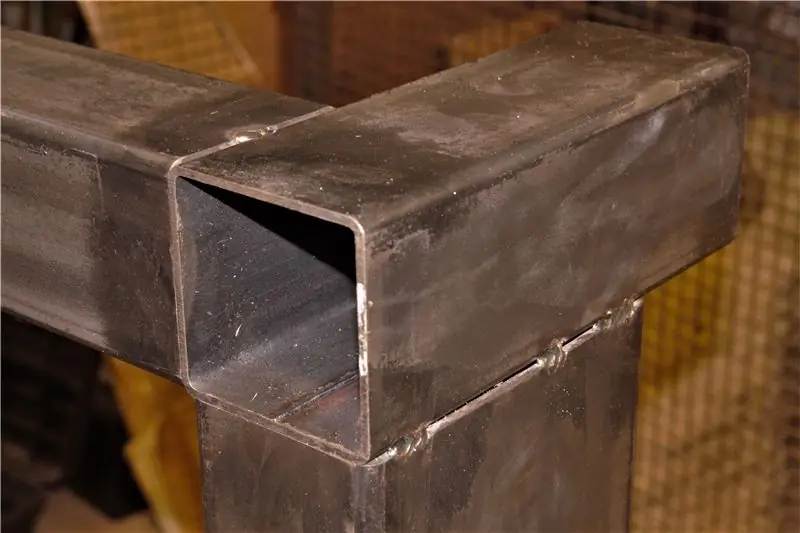
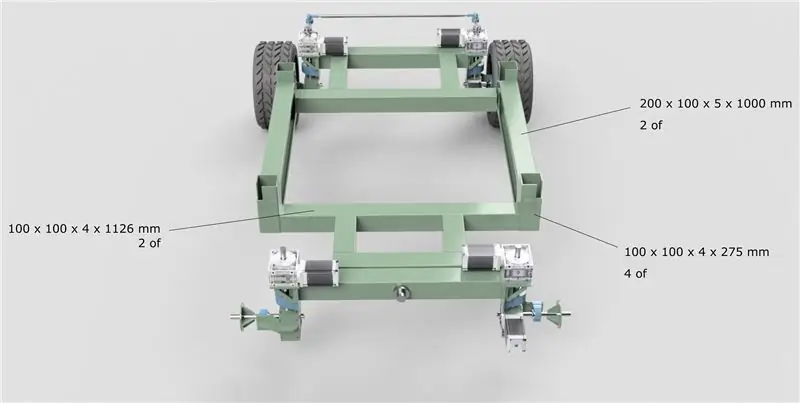
Der zentrale Teil des Chassis, der auch die CNC-Maschine sein wird, ist auf einer extrem ebenen Planplatte ausgelegt, damit die Kastenprofile so genau wie möglich positioniert werden können und die CNC-Komponenten schön und reibungslos laufen. Die Teile werden auf dem Tisch verschweißt, wobei darauf geachtet wird, dass keine heißen Spritzer auf den Tisch selbst gelangen, die ihn ruinieren würden.
Das Kastenprofil selbst muss mit einer Genauigkeit von etwa 0,2 mm geschnitten werden und ich habe den besten Stahllieferanten an meinem Standort mit einer Säge ausgewählt, die einen automatischen Vorschub verwendet, um eine Genauigkeit von 0,1 mm zu erreichen. Andere Stahllieferanten schneiden auf +- 5 mm, was nutzlos ist!
Die Abschnitte werden auf Rechtwinkligkeit zueinander überprüft und sorgfältig in diagonalen Sequenzen aneinander geheftet, um Verzerrungen zu vermeiden.
In diesem Stadium scheint die Konstruktion sehr schwer und sehr überdimensioniert zu sein, aber in den späteren Phasen wird der Plasmaschneider verwendet, um so viel Masse wie möglich aus der Struktur zu entfernen.
Schritt 3: Aufbau der schwenkbaren Vorderachse
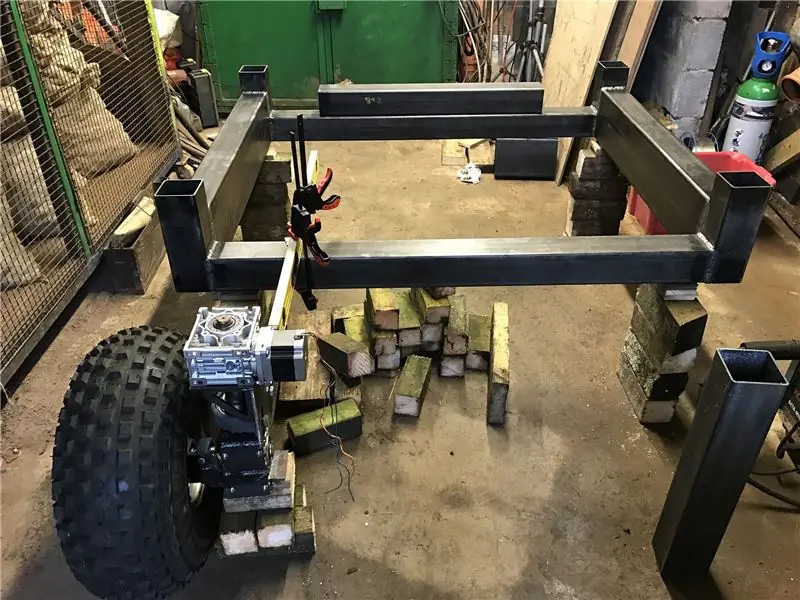
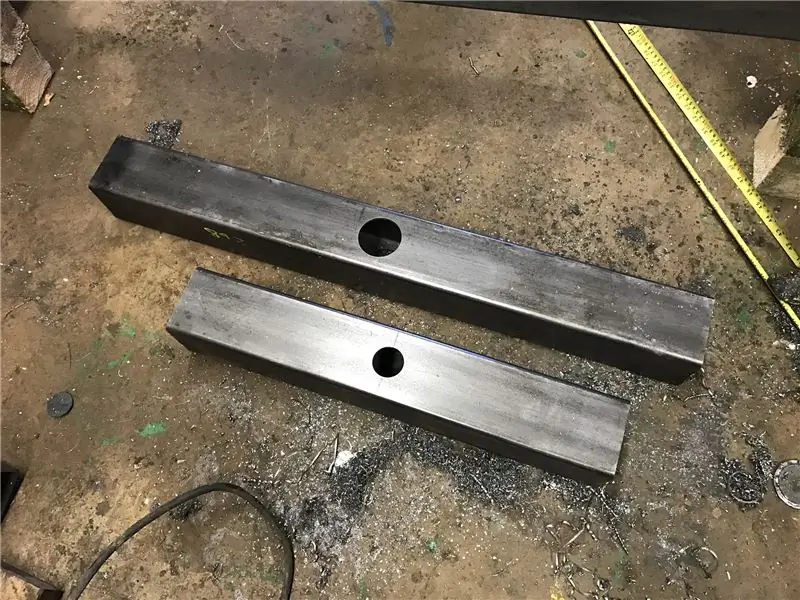
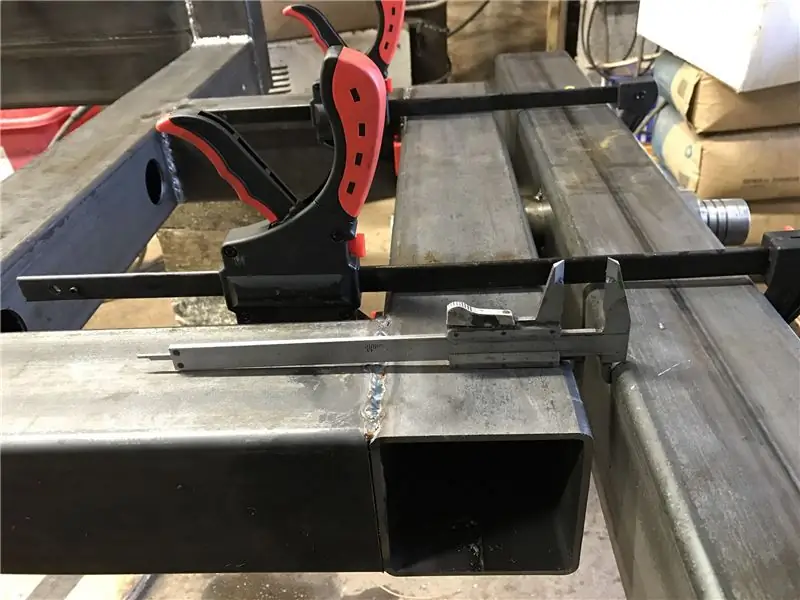
Die vorderen Antriebseinheiten werden relativ zum Hauptchassis positioniert und mit Holzklötzen ausgeglichen. Damit kann die Vorderachse vermessen werden. Dann wird auf jeder Seite mit einem Räumbohrer ein Loch mit einem Durchmesser von 60 mm in der Mitte gebohrt. Die 600 mm lange Box hat einen Bohrdurchmesser von 40 mm.
Der kleine 100 x 100 Kastenunterrahmen wird auf das Hauptchassis geschweißt, um es so eben und quadratisch wie möglich zu machen, und das Aufhängerohr wird in die 60 mm Löcher eingesetzt und geschweißt.
Die flachen 50 mm Lager werden in das Rohr eingesetzt und die Welle wird sorgfältig positioniert und eingeschweißt.
Das 970 mm Achslagerprofil wird dann der Reihe nach an jede der Antriebseinheiten geschweißt.
Schritt 4: Aufbau der Hinterachsbaugruppe
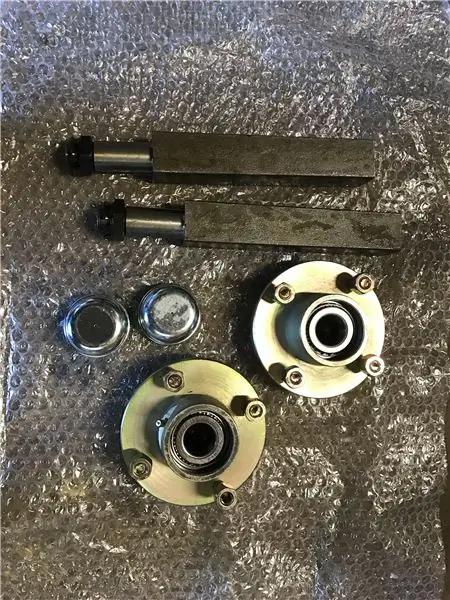
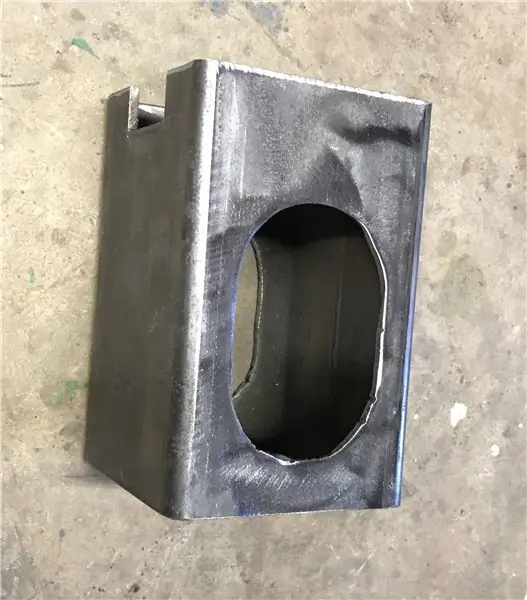
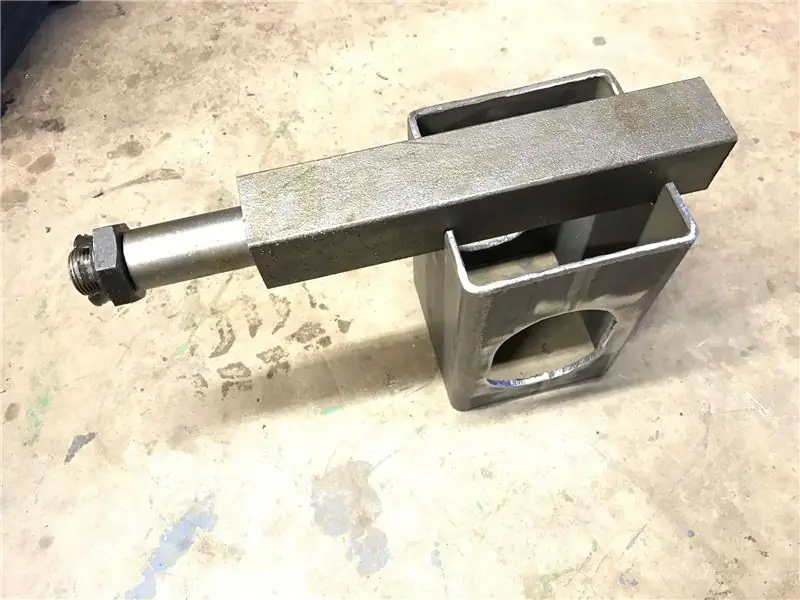
Die Hinterachse ist eine temporäre Befestigung, um das Testen der Hauptantriebseinheiten vorn zu ermöglichen. Die Abmessungen der verwendeten 100 x 100 mm Kastenprofile ergeben sich durch Einstellen der restlichen Fahrgestellebene und Durchmessen.
Schritt 5: Ovale Slots in 100 x 100 Boxen herstellen
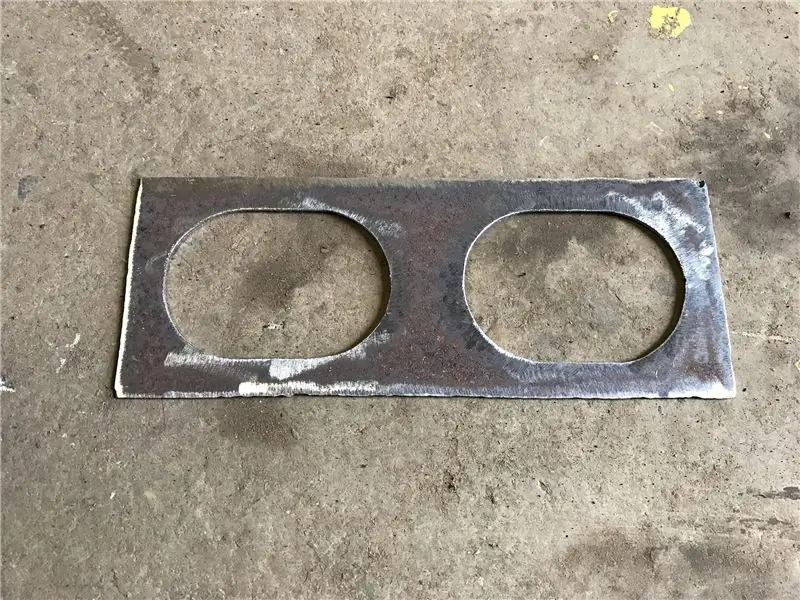
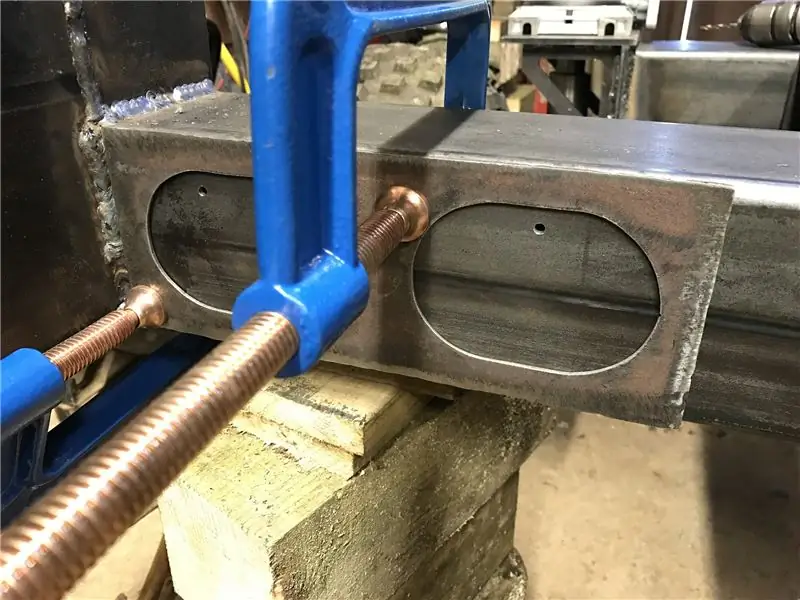
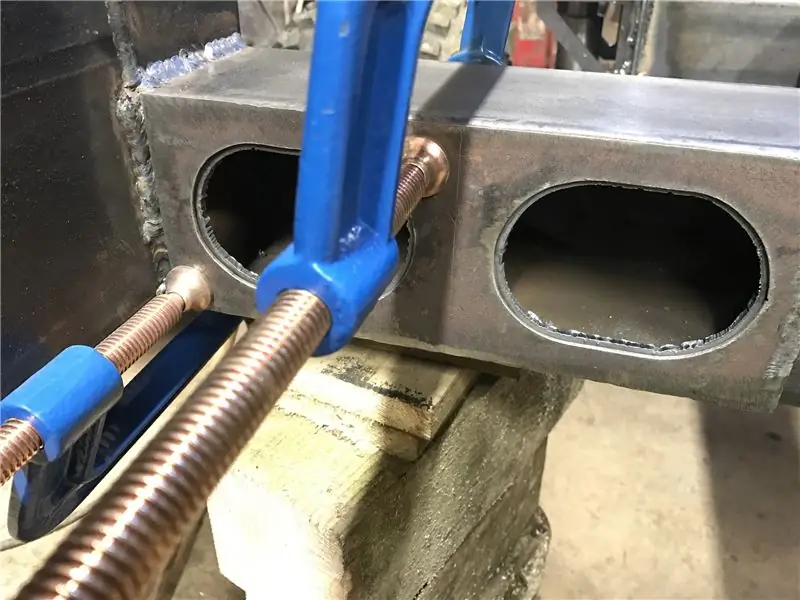
Die im Chassis verwendeten Kastenprofile sind viel zu schwer und müssen daher mit dem Plasmaschneider entlastet werden.
Eine Schablone wird aus 2 mm Stahl hergestellt und an das Kastenprofil geklemmt, wo immer ein Loch benötigt wird. Bevor das Schneiden beginnt, wird ein kleines Loch in den zu entfernenden Stahlbohrer gebohrt, der es ermöglicht, die Schneidflamme zu entzünden, ohne dass durch massiven Stahl gesprengt werden muss, was die Düse sehr schnell zerstört. Die Plasmaflamme funktioniert viel besser, indem sie seitlich in Stahl schneidet.
Für einen sauberen Schnitt, der am Bohrloch beginnt, ist viel Übung erforderlich. Die Taschenlampe wird sehr fest gehalten und langsam nach hinten gegen die Seite der Schablone gezogen. Schieben Sie die Taschenlampe niemals nach vorne oder zur Seite! Manchmal muss die Schablone mit einer Feile repariert werden, um eine glatte Oberfläche zu gewährleisten.
Wenn es gut gemacht ist, mit einer Düse in gutem Zustand, sollte das zu entfernende Metall einfach herausfallen und alle Linien sollten sauber und sauber sein, sonst ist eine Menge sehr mühsamer Arbeit erforderlich, um alles zu reinigen. Die entstandene Schlacke wird einfach mit einem Hammer abgeschlagen und die finale Oberfläche mit einer groben Halbrundfeile gefeilt. Schleifen sollte nicht notwendig sein!
Schritt 6: Ausstecken der 200 X 100 Box
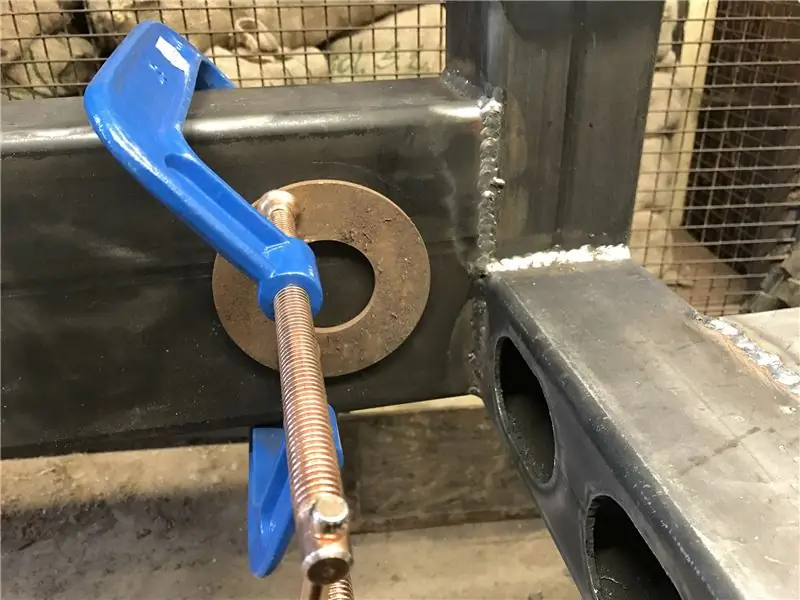
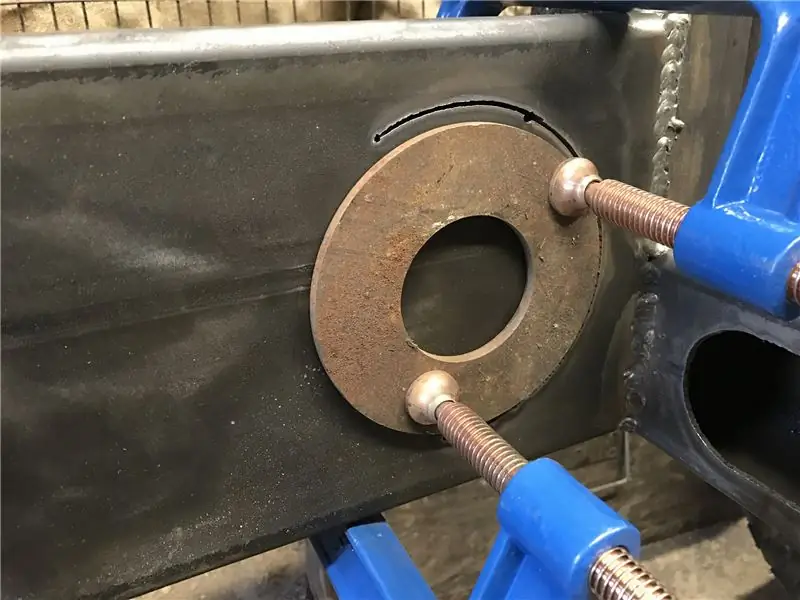
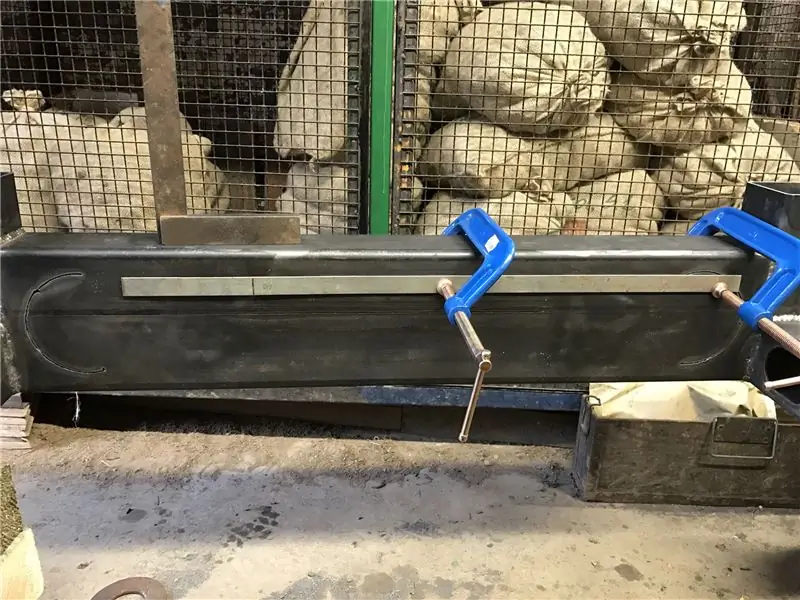
Die 200 x 100 Box ist unglaublich schwer, wird aber für eine einfache Verarbeitung auf der Oberflächenplatte benötigt. Es ist viel einfacher, unnötiges Material mit dem Plasmaschneider zu entfernen, als komplizierte Strukturen aufzubauen. Am Ende haben wir einen Rahmen mit einem attraktiven „Luftfahrt“-Design.
Anstatt eine Vorlage zu erstellen, habe ich einige große Unterlegscheiben verwendet, die ungefähr die richtige Größe hatten. Es ist sehr befriedigend, die große "Zunge" aus Stahl mit schönen sauberen Schnitten zu entfernen, obwohl die Plasmadüse zu diesem Zeitpunkt anfing, sich zu verschlechtern.
Als ich an diesem Tag fertig war, hatte ich 17 kg Material abtransportiert.
Schritt 7: Fertiges Chassis
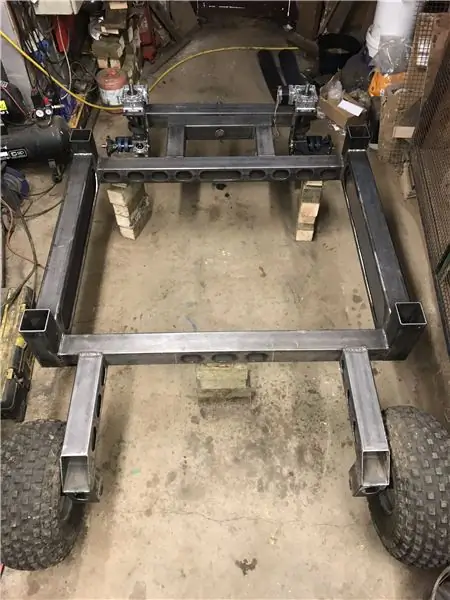
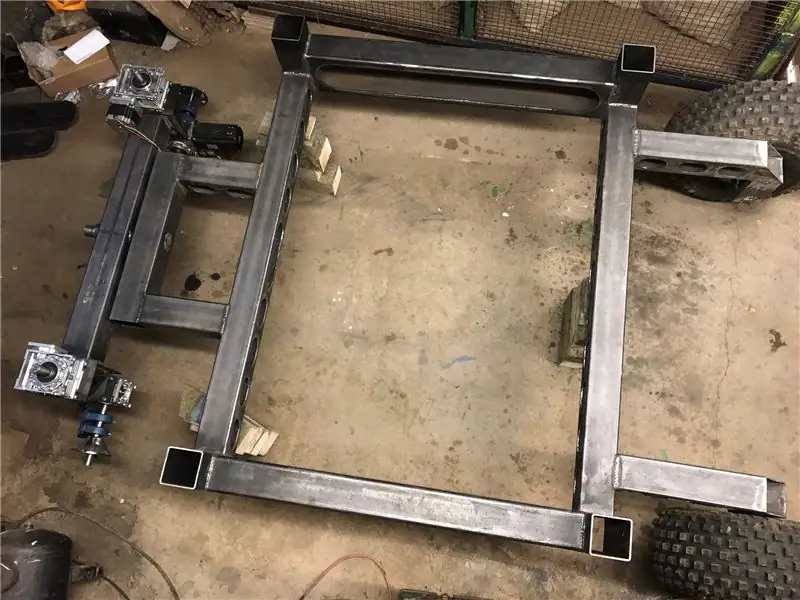
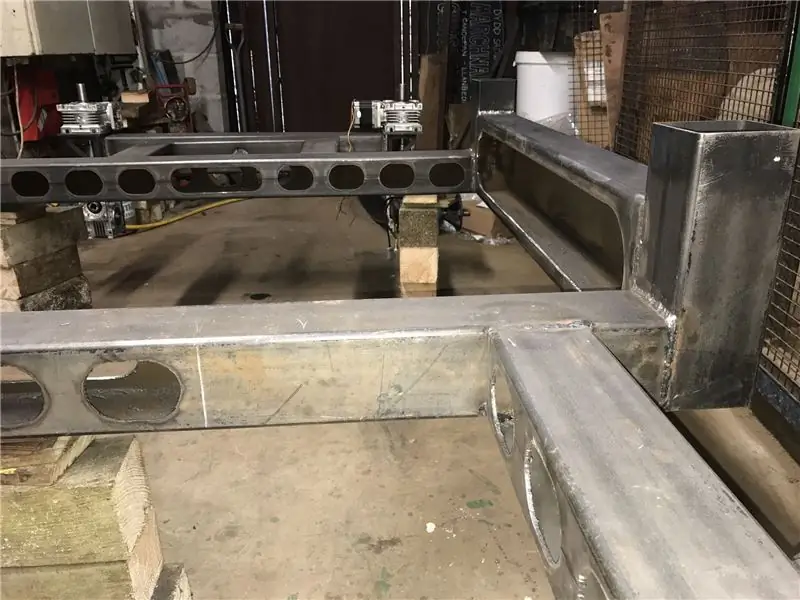
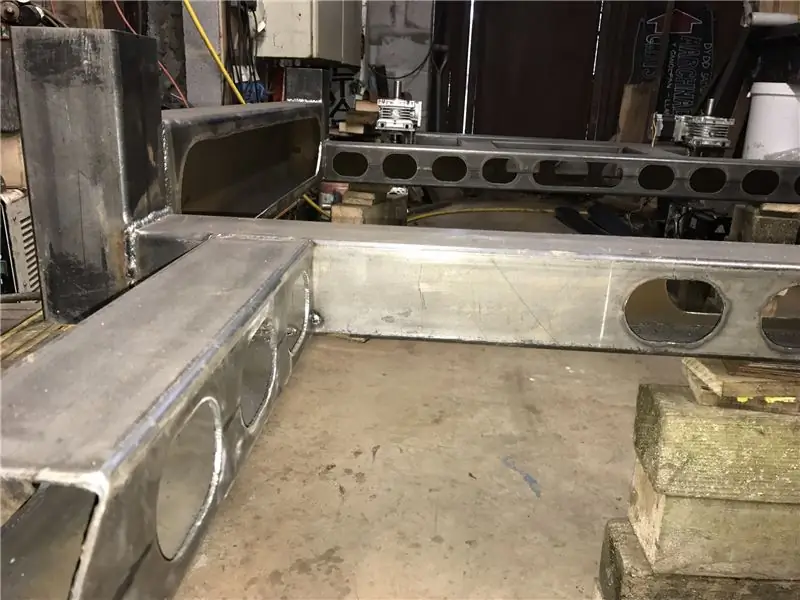
Das Chassis ist fertig und die Antriebs-/Lenkung kann getestet werden - wartet nur noch auf ein weiteres Paar Räder.
Schritt 8: Nächste Schritte
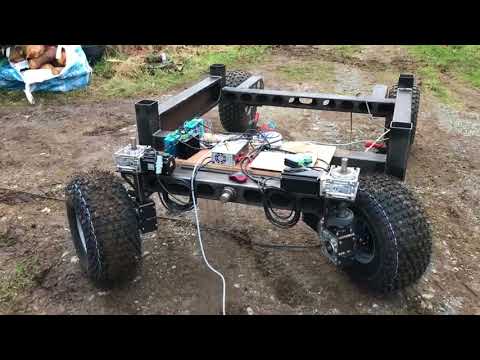
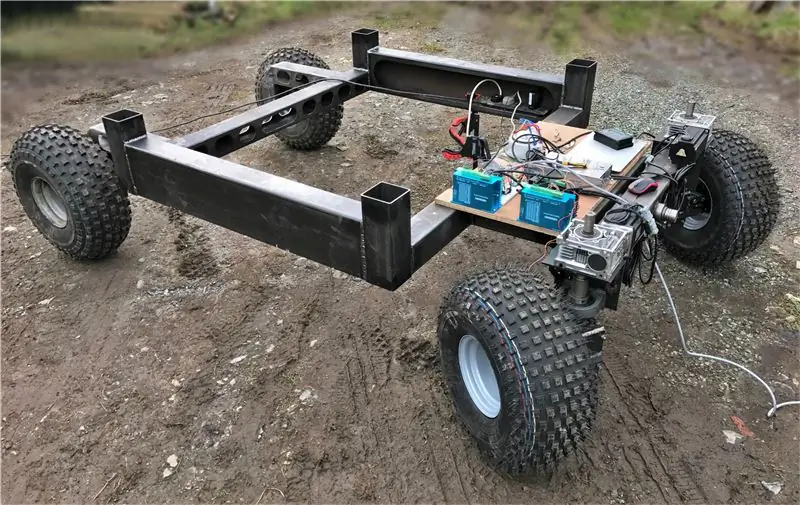
Zweiter im Metal Contest 2017
Empfohlen:
Einfaches BLE mit sehr geringem Stromverbrauch in Arduino Teil 2 - Temperatur- / Feuchtigkeitsmonitor - Rev 3: 7 Schritte
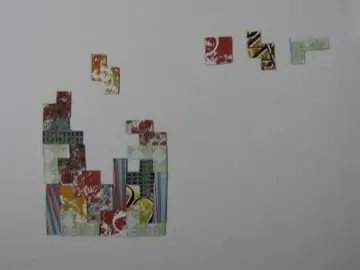
Easy Very Low Power BLE in Arduino Teil 2 – Temperatur-/Feuchtigkeitsmonitor – Rev 3: Update: 23. November 2020 – Erster Austausch von 2 x AAA-Batterien seit 15. Januar 2019 dh 22 Monate für 2x AAA AlkalineUpdate: 7. April 2019 – Rev 3 of lp_BLE_TempHumidity, fügt Datum/Uhrzeit-Plots hinzu, verwendet pfodApp V3.0.362+ und automatische Drosselung, wenn
Bewegungsaktivierte Cosplay Wings mit Circuit Playground Express - Teil 1: 7 Schritte (mit Bildern)
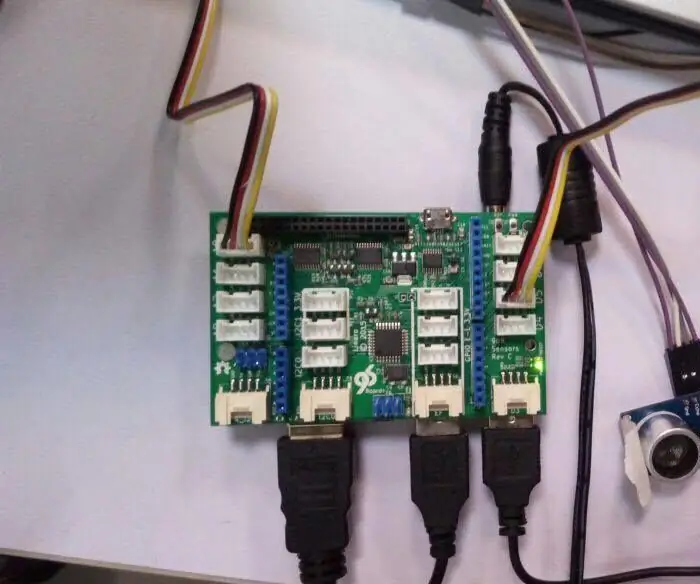
Bewegungsaktivierte Cosplay-Flügel mit Circuit Playground Express - Teil 1: Dies ist Teil 1 eines zweiteiligen Projekts, in dem ich Ihnen meinen Prozess zur Herstellung eines Paars automatisierter Feenflügel zeige. Der erste Teil des Projekts ist der Mechanik der Flügel, und der zweite Teil macht es tragbar und fügt die Flügel hinzu
RGB-Pixel-Weihnachtslichtshow Teil 1: 7 Schritte
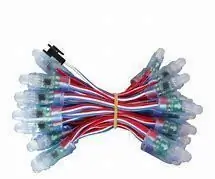
RGB-Pixel-Weihnachtslichtshow Teil 1: In dieser Anleitung zeige ich Ihnen, wie Sie eine RGB-Pixel-Lichtshow erstellen. Es gibt VIEL zu decken. Tatsächlich werde ich dies wahrscheinlich in etwa 3-5 verschiedene Anweisungen aufteilen. In diesem geht es um die Grundlagen. Sie haben viel zu lesen
Interessante Programmieranleitung für Designer - Bringen Sie Ihr Bild zum Laufen (Teil 2): 8 Schritte
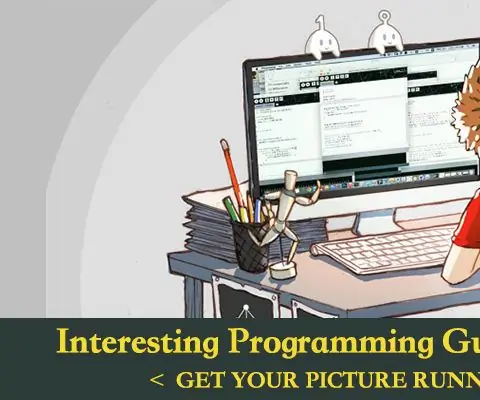
Interessante Programmieranleitung für Designer – Bringen Sie Ihr Bild zum Laufen (Teil 2): Mathematik scheint für die meisten von Ihnen nutzlos zu sein. Die in unserem täglichen Leben am häufigsten verwendete ist einfach Addieren, Subtrahieren, Multiplizieren und Dividieren. Es ist jedoch ganz anders, wenn Sie mit Programm erstellen können. Je mehr Sie wissen, desto mehr wundervolle Ergebnisse werden Sie erhalten
DIY RACING GAME SIMULATOR BUILD TEIL 1: 6 Schritte

DIY RACING GAME SIMULATOR BUILD TEIL 1: Hallo zusammen Willkommen, heute zeige ich euch, wie ich einen "Racing Game Simulator" mit Hilfe von Arduino UNO. YouTube-Kanal " abonnieren Sie unbedingt meinen Kanal A Builds(Hier klicken)" Dies ist der Build-Blog, So le