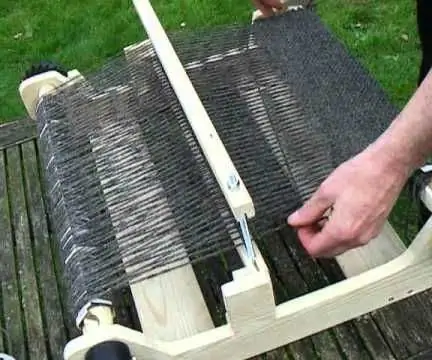
Inhaltsverzeichnis:
- Schritt 1: Upcycling einer Palette
- Schritt 2: Machen Sie einen Warp- und einen Stoff-Beam
- Schritt 3: Die Rahmenseite
- Schritt 4: Der Webkamm und das Ratchet-Gear
- Schritt 5: Montage des Rahmens
- Schritt 6: Montage des Webkamms
- Schritt 7: Heddle die Warp
- Schritt 8: Das Shuttle zum Weben
- Schritt 9: Stückliste und Quellen
2025 Autor: John Day | [email protected]. Zuletzt bearbeitet: 2025-01-23 12:52
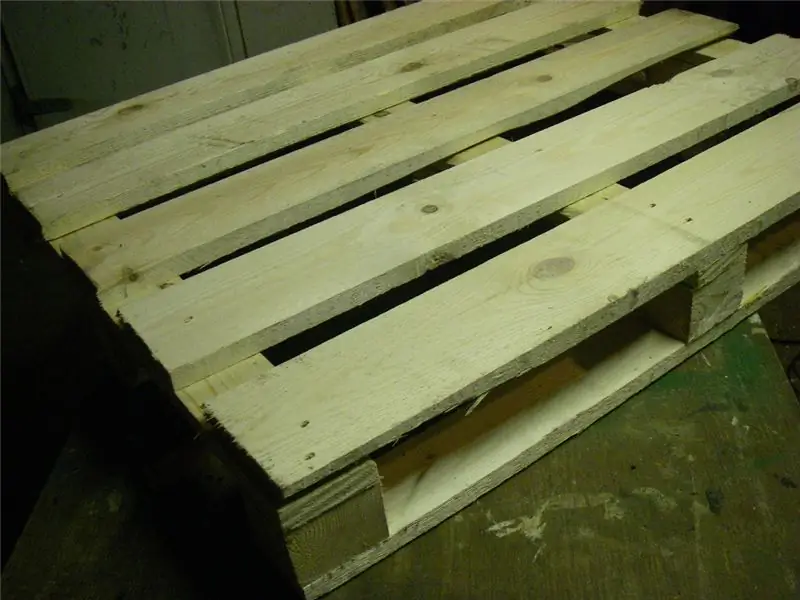
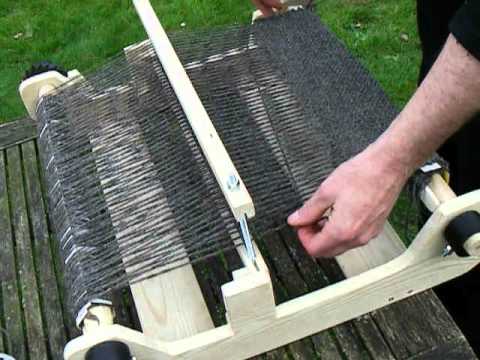
Dieses Projekt zeigt, wie man eine Palette upcycelt und aus ihren Holzbrettern einen Webstuhl herstellt, indem einige zusätzliche Teile (den Webkamm und die Ratschenräder) aus einem 3D-Drucker verwendet werden.
Durch die Verwendung zweier etwas widersprüchlicher Materialien wie Holz, das oft als "gutes" Material angesehen wird, weil es ein Naturstoff ist, und zweitens Kunststoff (ABS) als synthetisches Material, das oft als "böse" angesehen wird, wollte ich zeigen, dass gut oder Das Böse ist nie eine Eigenschaft eines Materials selbst, sondern lediglich, dass es davon abhängt, was die Menschen damit machen.
Wenn man es kreativ oder produktiv einsetzt (wie hier beim Weben), wo man es für die Ewigkeit immer wieder verwenden kann, dann ist sogar der Kunststoff in Ordnung. Aber es ist nicht in Ordnung, wenn wir es als Einweg-Verpackungsmaterial verwenden und es im Pazifik schwimmt und dort eine schwimmende Insel von einem Drittel der Größe Europas baut. Es geht also um unsere Verantwortung, wie wir mit den Dingen umgehen. Außerdem wollte ich mit diesem Projekt zeigen, wie wir Holzwerkstoffe aus alten Paletten wiederverwenden und upcyceln können und dass "Upcycling" noch besser ist als "Recycling" (zB. Verbrennen des Palettenholzes).
Aber das sind nur meine persönlichen Ambitionen, die mich zu diesem Projekt motiviert haben. Wenn Sie keine Palette zur Verfügung haben, können Sie auch normale Weichhölzer wie Fichte, Tanne oder Kiefer (oder sogar Hartholz) mit einer Dicke von 20 mm verwenden. Wenn nur 18 mm verfügbar sind, funktioniert es auch.
Schritt 1: Upcycling einer Palette
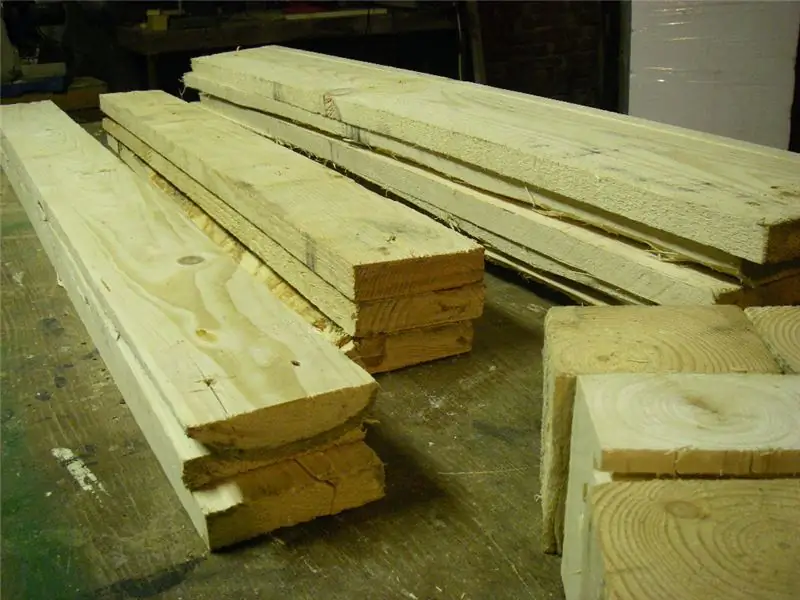
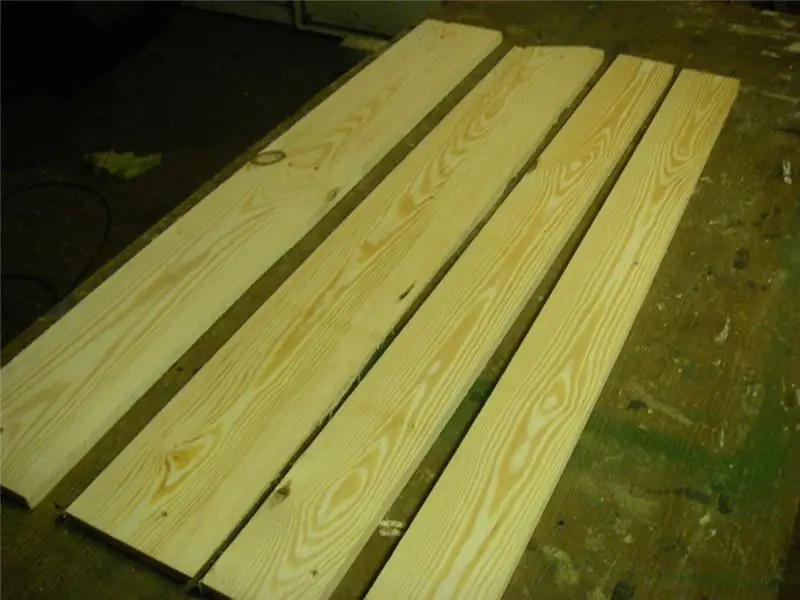
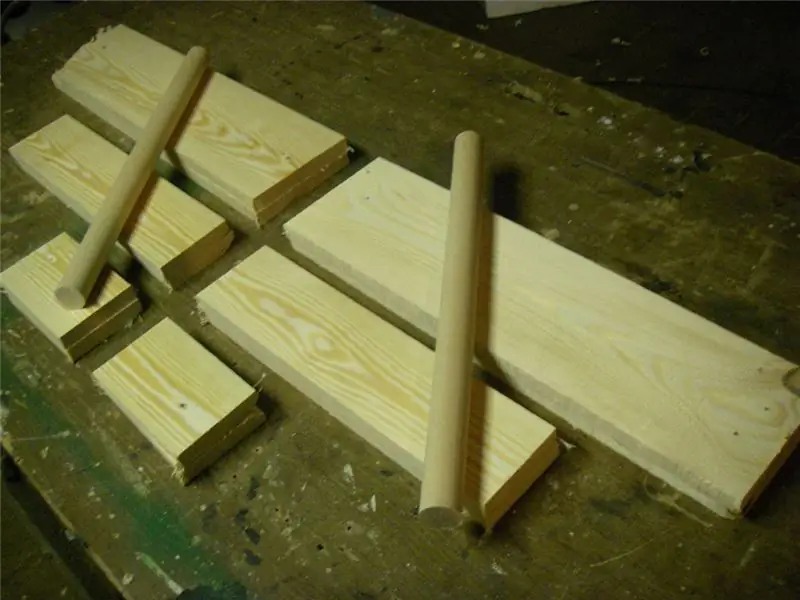
Jede Palette mit Abmessungen, die dem standardisierten "Euro-Paletten"-Format entsprechen, sollte geeignet sein. Hier verwende ich eine Palette, die kein Standardformat hat, aber die wichtigsten Punkte erfüllt, wie zum Beispiel bis zu 14,5 cm breite Dielen mit einer Dicke von 22 mm, die uns 20 mm gehobelt ergeben.
Zuerst müssen Sie die Palette mit Hilfe einer Brechstange (oder zwei) zerlegen. Entfernen Sie mit Hammer und Zange alle Nägel von den Holzbrettern. Anschließend sollten die Dielen auf eine Dicke von 20 mm gehobelt werden. Dies kann durch eine Abrichtmaschine oder manuell durch einen Zimmermannshobel erfolgen. Wenn Ihnen keines dieser Werkzeuge zur Verfügung steht, können Sie natürlich auch im Baumarkt entsprechende Dielen (2cm dick, 15cm breit, 60cm lang) kaufen. Aber der Upcycling-Prozess gehört zum Spaß dazu;)
Schneiden Sie die Dielen entsprechend den Plänen in Schritt 3 auf Länge und Breite zu. Auf dem Bild sind auch zwei Holzrundstäbe aus Buchenholz zu sehen, die ich ursprünglich gekauft habe. Aber dann habe ich mich später entschieden, jedes einzelne Holzteil aus der Palette zu fertigen und die abgerundeten Stäbe durch zwei weitere achteckige Stäbe ersetzt, die ich aus zwei miteinander verleimten Holzstreifen gemacht habe. Das achteckige Profil ist noch besser für das Weben.
Schritt 2: Machen Sie einen Warp- und einen Stoff-Beam
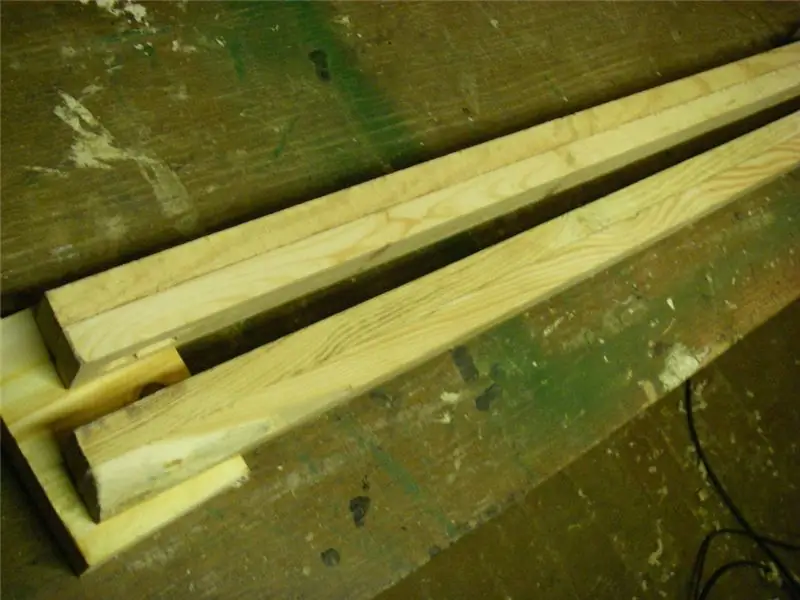
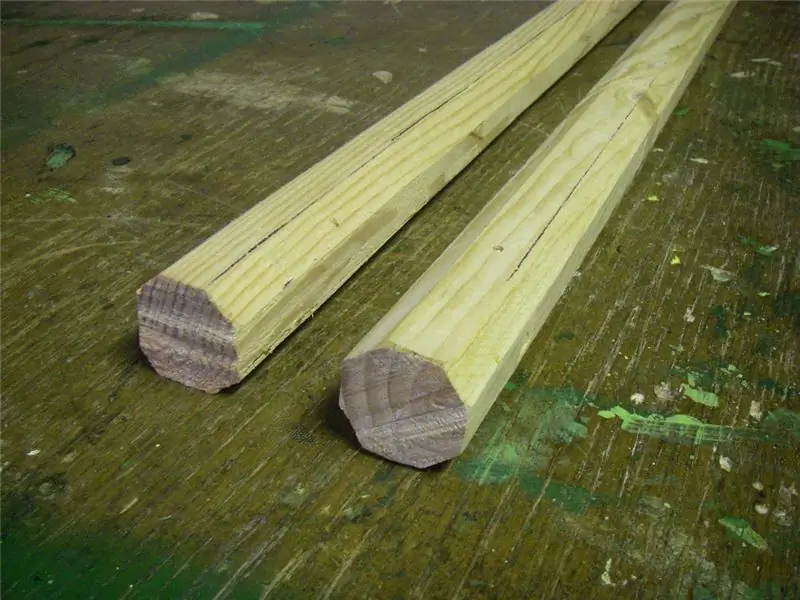
Kleben Sie zwei kleine Bretter von 710 mm Länge, 40 mm Breite und 20 mm Dicke zusammen. Sie erhalten ein Vierkantprofil mit 40x40mm. Schneiden Sie diese auf einer Tischkreissäge auf 35 x 35 mm zu.
Anschließend die Kanten mit einem Handhobel so entfernen, dass ein achteckiges Profil entsteht.
Anschließend die letzten 10 cm jedes Stabendes mit dem Planer oder einer Schleifmaschine auf einen Durchmesser von 35 mm runden.
Alternativ können Sie auch einen zylindrischen Holzschaft mit 35mm Durchmesser und 710 mm Länge verwenden.
Schritt 3: Die Rahmenseite
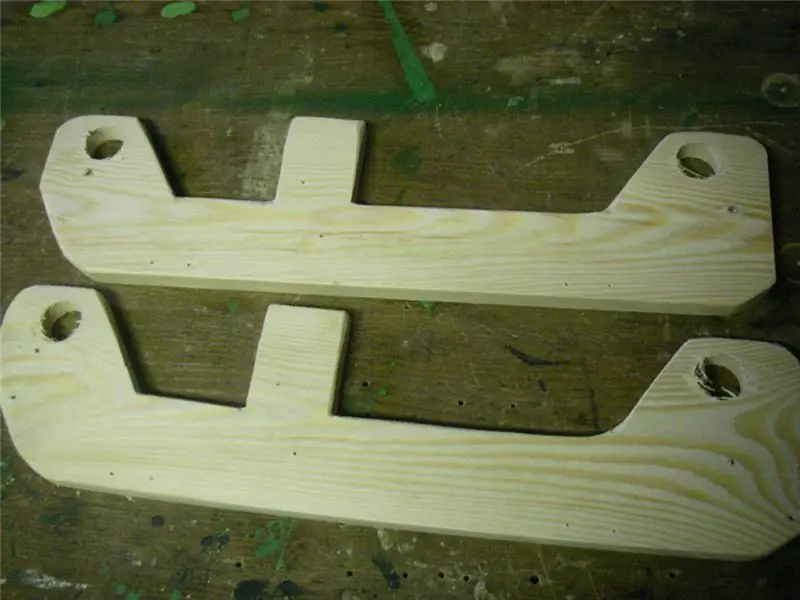
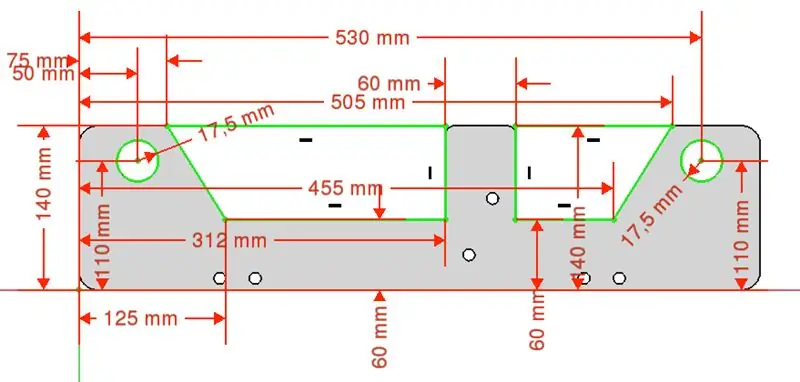
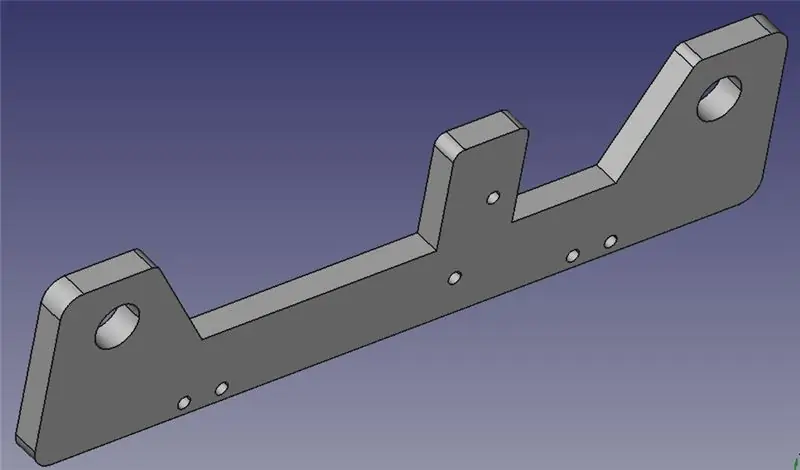
Die Rahmenseite ist aus einer 20 mm Diele mit 58x14cm gefertigt und hat laut Plan einige Bohrlöcher. Dieser Teil ist auch als fcstd-Datei (FreeCAD) verfügbar.
Der Kammhalter ist ein kleines Stück 118x60mm und lässt sich leicht aus den Dielen herausschneiden. Es wird an der Rahmenseite montiert und hat die Auf- und Abbewegungen in seinen Lückengrößen codiert.
Schritt 4: Der Webkamm und das Ratchet-Gear
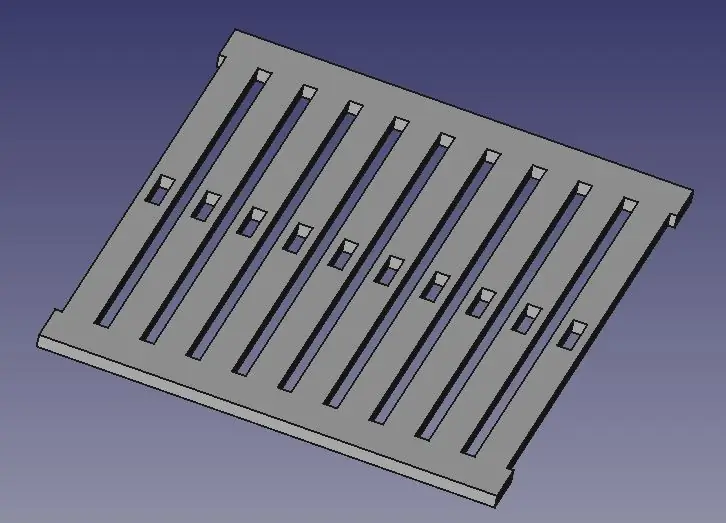
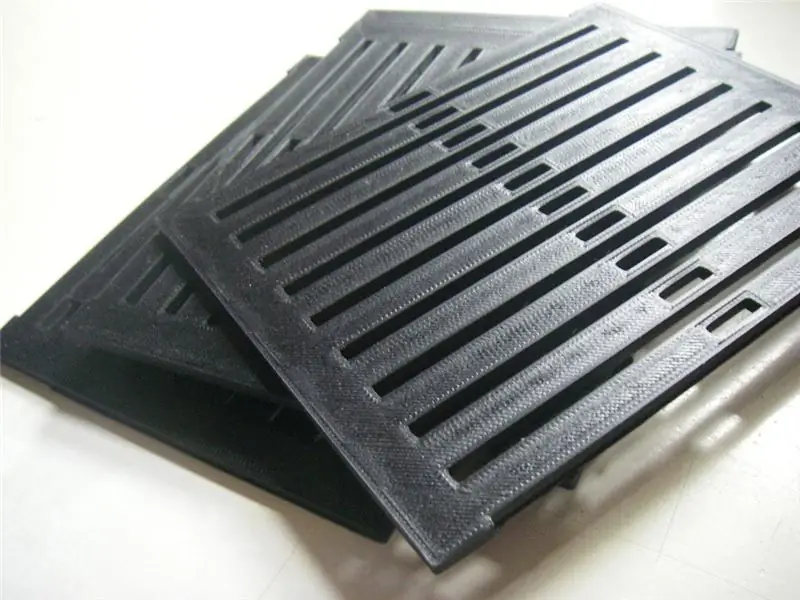
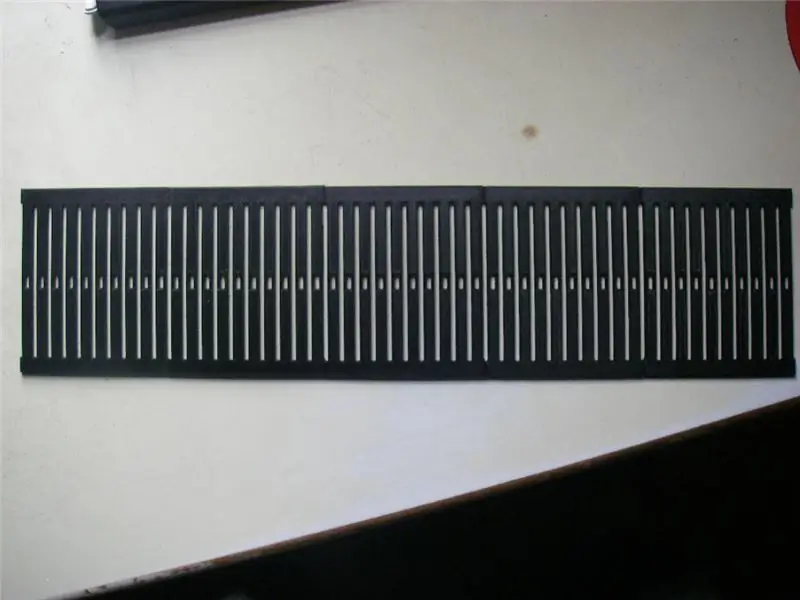
Der Webkamm und das Ratchet-Gear sowie die Endringe werden aus einem 3D-Drucker hergestellt. Ich war zu faul, diese Teile aus Holz zu fertigen;) Das ABS-Material ist stabil und stark genug für diese Webaufgabe. Sie finden die benötigten Konstruktionsdateien als.stl-Dateien zum Drucken und als.fcstd FreeCAD-Dateien im Quellpaket.
Schritt 5: Montage des Rahmens
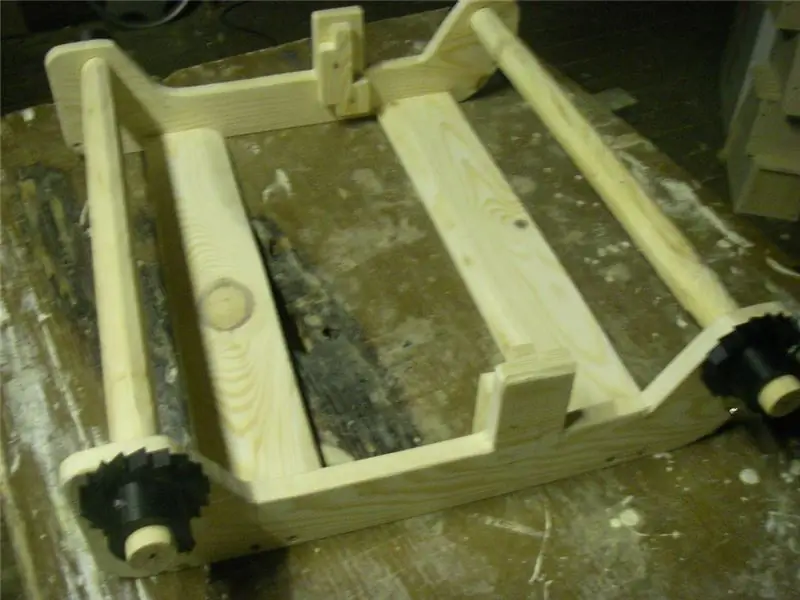
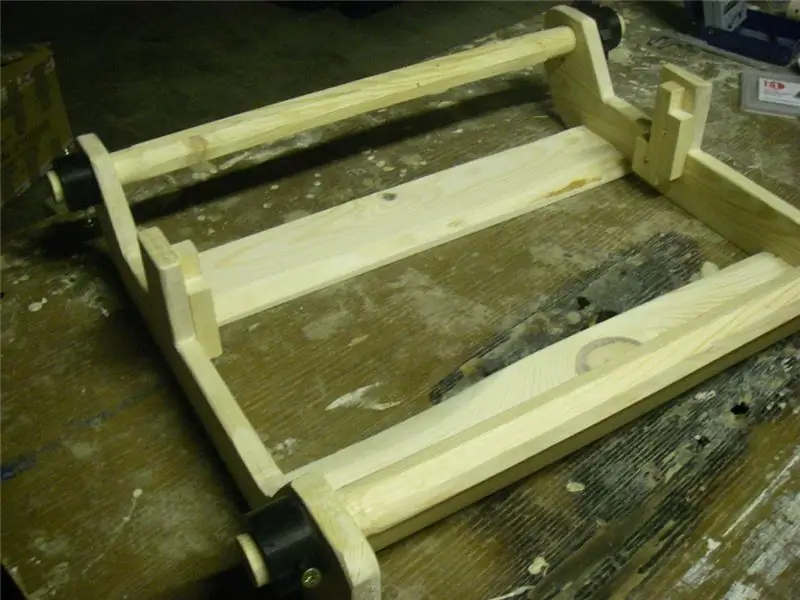
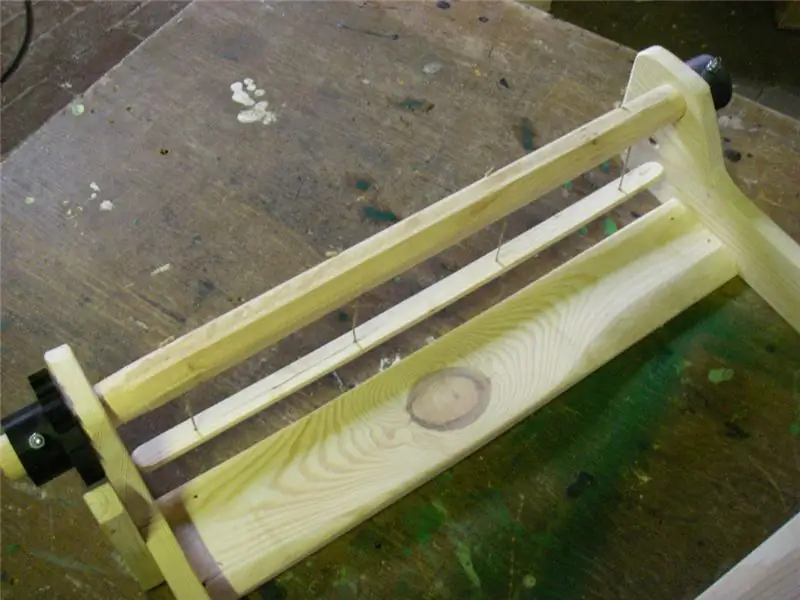
Beginnen Sie mit der Montage des Kammhalters an den Rahmenseiten mit zwei 35-mm-Holzschrauben. Legen Sie dann die beiden Querverbindungsteile zwischen die Seiten und stecken Sie die Kettbaum- und die Tuchbaumwellen in die Löcher. Verbinden Sie die Seitenteile mit zwei 60mm Holzschrauben auf jeder Seite mit den Querverbindungen.
Anschließend die Sperrräder und die Klemmringe auf die Wellenenden schieben und mit einer M6x70 Zylinderschraube und zwei Muttern fixieren. Binden Sie nun den Stringstick (zum Verbinden der Kettfäden) wie im obigen Foto an den Stoffbaum.
Schritt 6: Montage des Webkamms
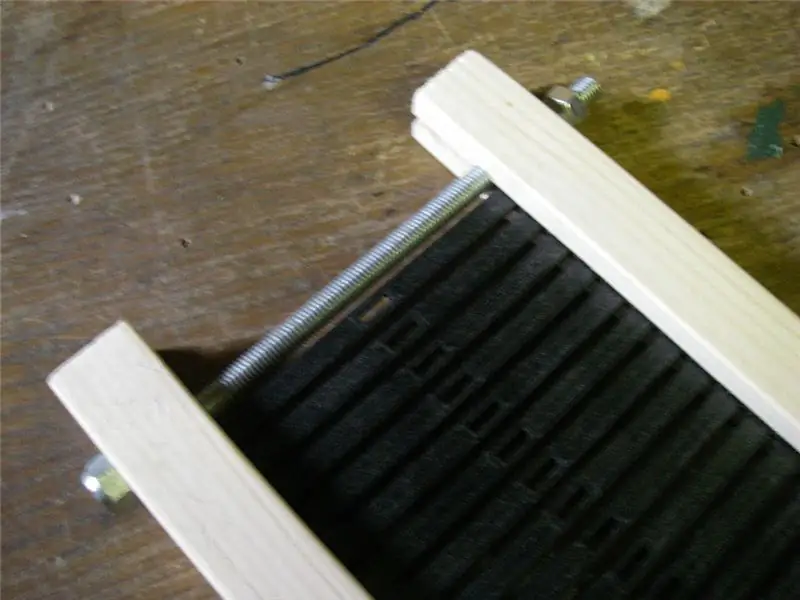
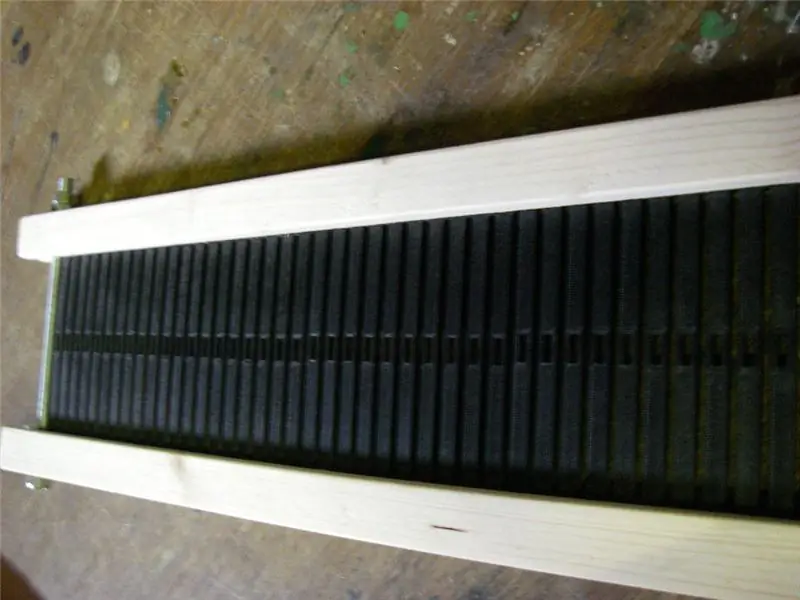
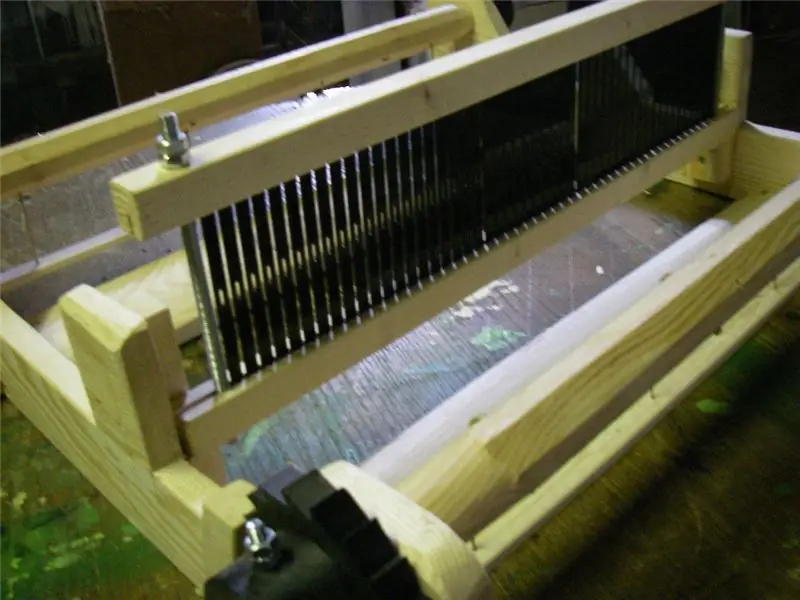
Halten Sie zum Zusammenbauen des Kamms die beiden Schlitzbalken parallel, aber mit Blick auf den Schlitz zueinander. Setzen Sie dann die 4 3D-gedruckten Kammmodule in den Schlitz ein, so dass sie einen homogenen Kamm von ca. 400mm Länge bilden.
Verbinden Sie die Balken mit je zwei Gewindestangen an jedem Ende, die Sie mit Hilfe von zwei M8-Muttern fixieren. Die radierten Stäbe dienen hier auch als Distanzhalter für die Schlitzbalken und bilden mit ihnen zusammen eine Art Rahmen.
Schritt 7: Heddle die Warp
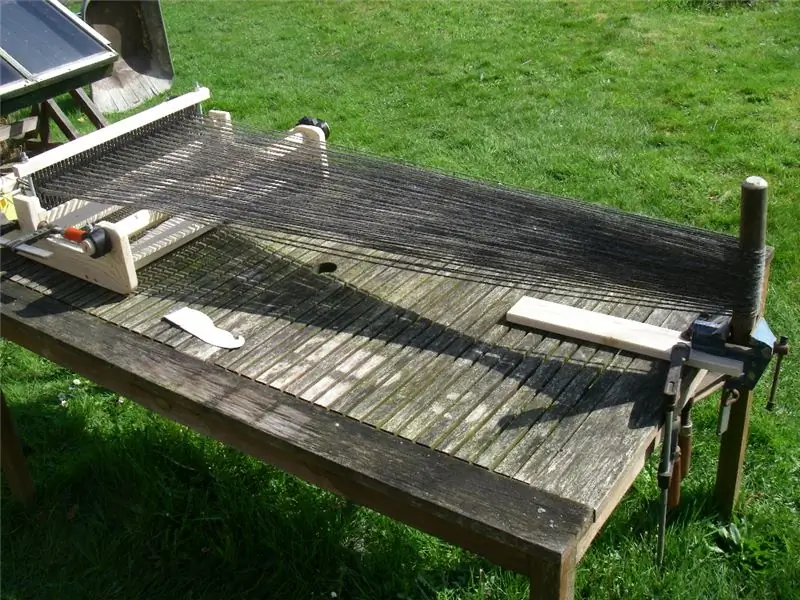
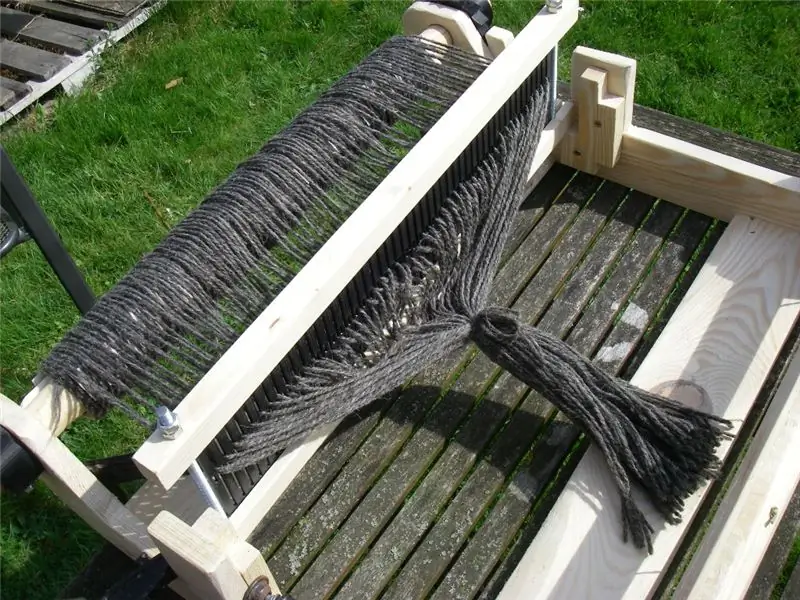
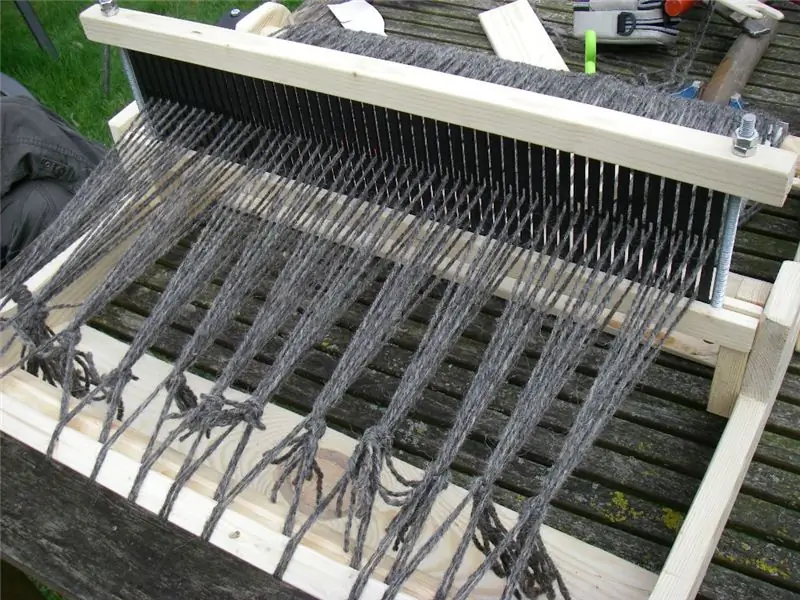
Als nächstes montieren Sie das OHLOOM mit einer Klemme an einem Tisch und hetzen die Kette.
Es ist wichtig zu beachten, dass die Länge der Kette viel länger sein kann als die Länge des Webstuhls, z. B. 2 oder 3 m. Denn das Garn auf der einen Seite und das frisch gewebte Tuch auf der anderen Seite lassen sich nach dem Lösen der Sperrklinke durch einfaches Drehen um die Kett- und die Stoffbaumkette wickeln. Dann müssen Sie etwas Spannung in die Kette bringen, bevor Sie sie wieder anbringen.
Schritt 8: Das Shuttle zum Weben
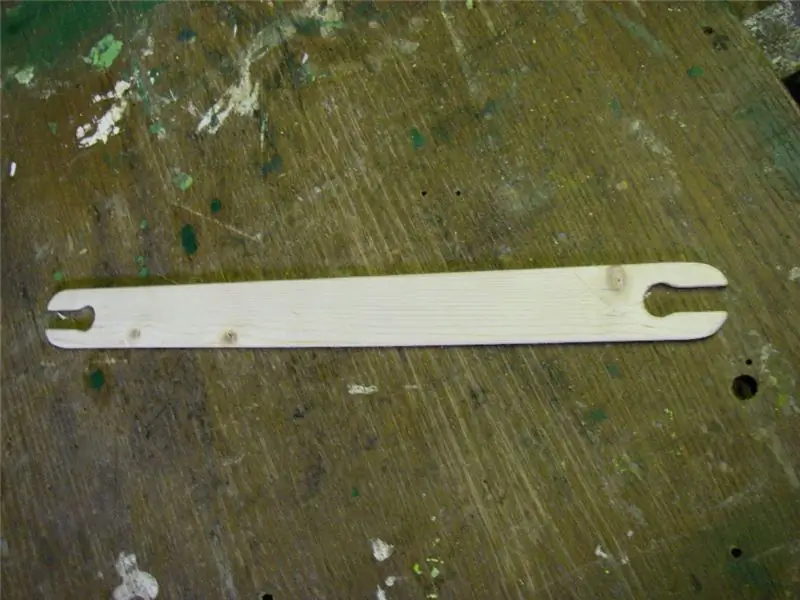
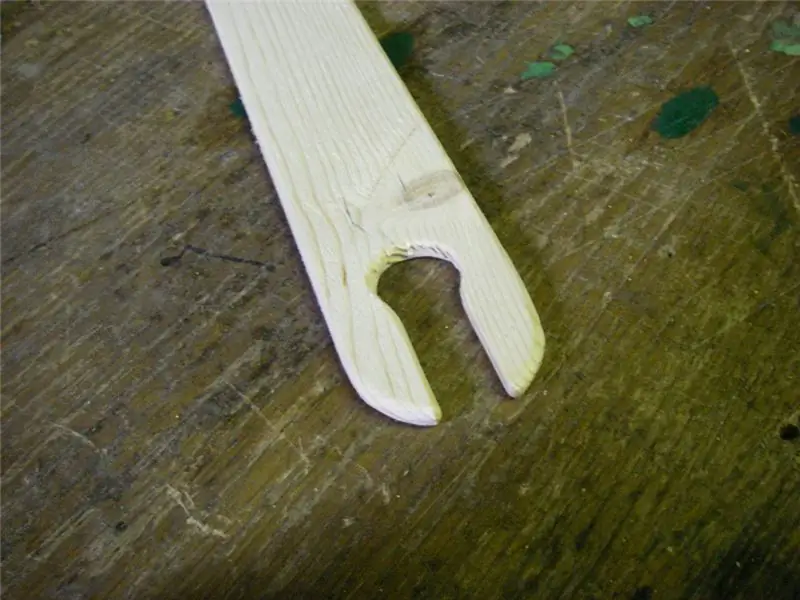
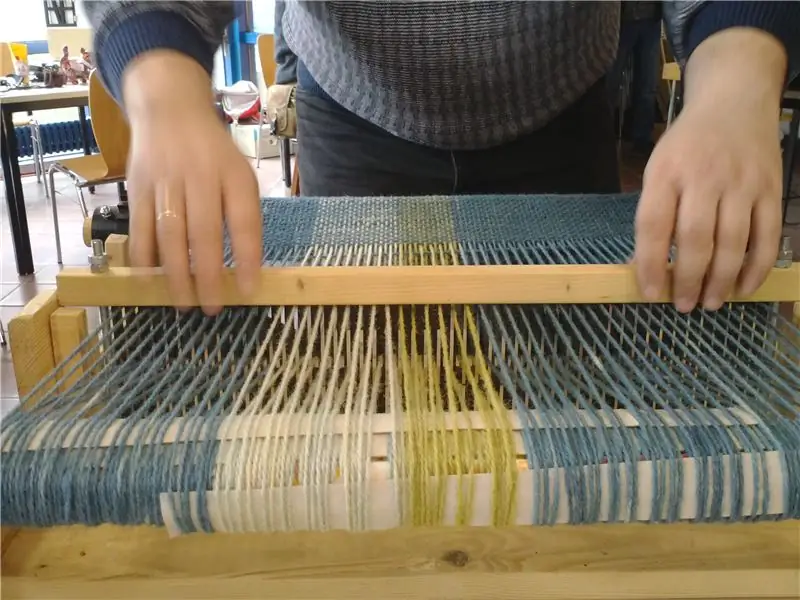
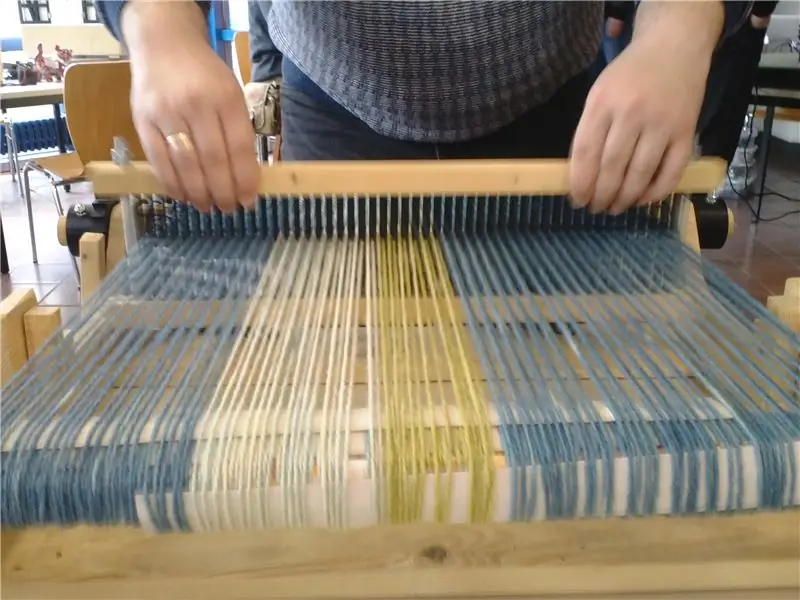
Bereiten Sie die Enden des Shuttles wie auf dem Foto oben vor. Es ist wichtig, die Kanten zu glätten, indem Sie sie mit einer Feile oder einem Schleifpapier abrunden. Scharfe Kanten könnten das Garn sonst beschädigen. Wickeln Sie dann etwas Garn auf das Schiffchen und beginnen Sie mit dem Weben.
Schritt 9: Stückliste und Quellen
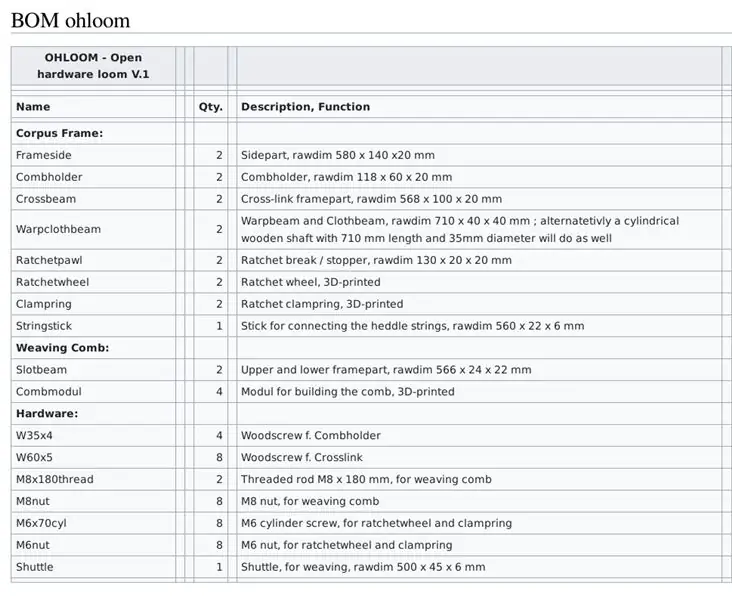
Eine OHLOOM-Projektseite in deutscher Sprache finden Sie unter:
wiki.opensourceecology.de/Open_Hardware-Wir…
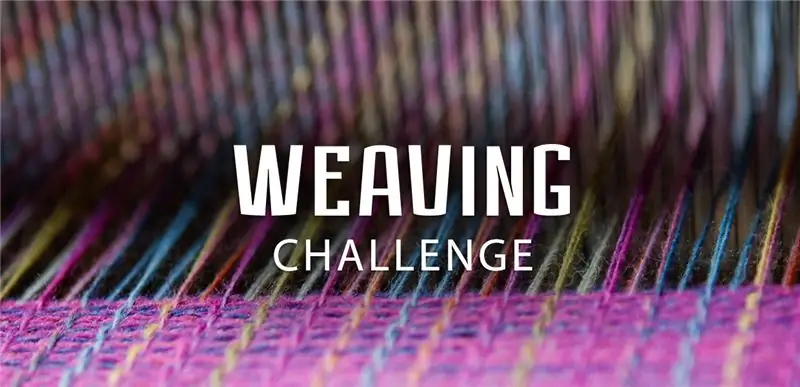
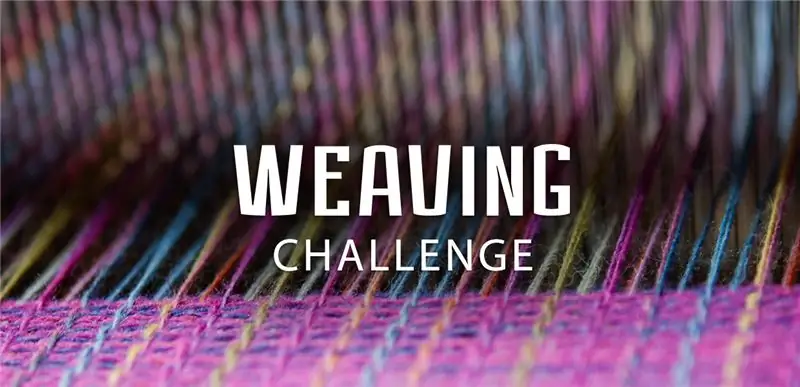
Zweiter Preis bei der Web-Challenge
Empfohlen:
So bauen Sie Ihr eigenes Anemometer mit Reed-Schaltern, Hall-Effekt-Sensor und einigen Schrott auf Nodemcu. - Teil 1 - Hardware: 8 Schritte (mit Bildern)
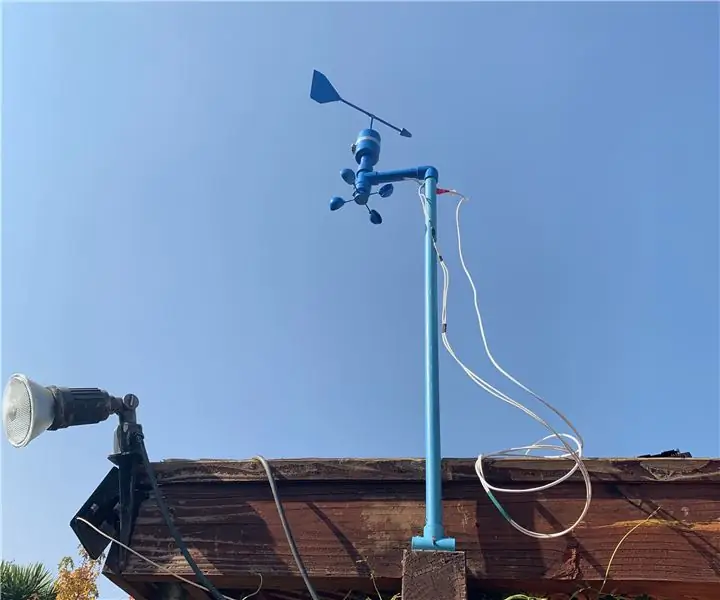
So bauen Sie Ihr eigenes Anemometer mit Reed-Schaltern, Hall-Effekt-Sensor und einigen Schrott auf Nodemcu. - Teil 1 - Hardware: EinführungSeit ich mit dem Studium von Arduino und der Maker-Kultur begonnen habe, habe ich gerne nützliche Geräte aus Schrott- und Schrottstücken wie Kronkorken, PVC-Stücken, Getränkedosen usw. gebaut. Ich liebe es, eine Sekunde zu geben Leben für jedes Stück oder jeden Kumpel
So verwenden Sie Tinkercad zum Testen und Implementieren Ihrer Hardware – wikiHow
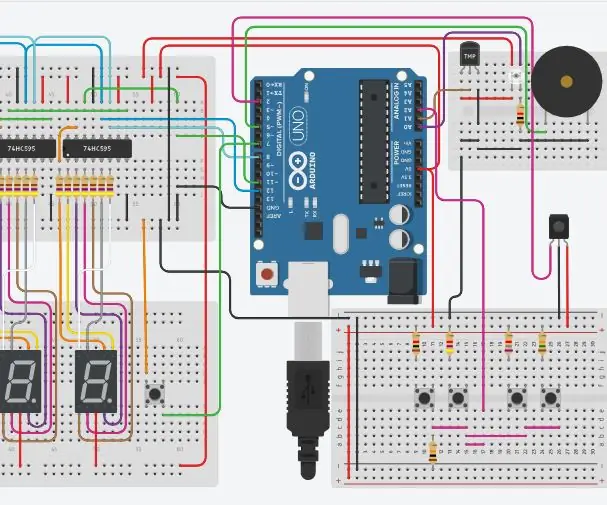
So verwenden Sie Tinkercad zum Testen und Implementieren Ihrer Hardware: Die Schaltungssimulation ist eine Technik, bei der Computersoftware das Verhalten einer elektronischen Schaltung oder eines Systems simuliert. Neue Designs können getestet, bewertet und diagnostiziert werden, ohne die Schaltung oder das System tatsächlich aufzubauen. Schaltungssimulation kann ein
Computer für RE-Systeme (Teil 1 von 2) (Hardware): 5 Schritte
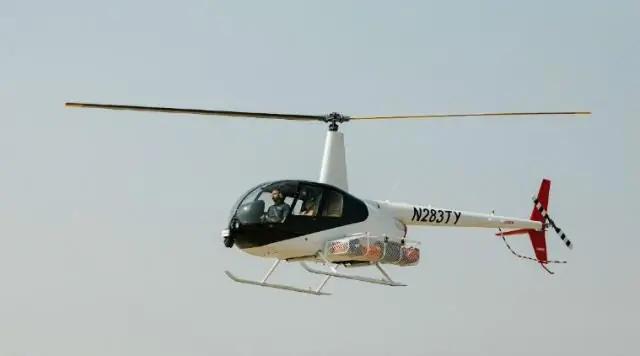
Computer für RE-Systeme (Teil 1 von 2) (Hardware): Hier zeige ich Ihnen, wie ich einen voll funktionsfähigen Mini-Desktop-Computer für kleine erneuerbare Energiesysteme hergestellt habe. Das RE-System, das ich verwenden möchte, wird hauptsächlich ein 12-Volt-System sein mit 6 oder 8 Golfcart-Batterien, und ich habe einen 700-Watt-Wechselrichter