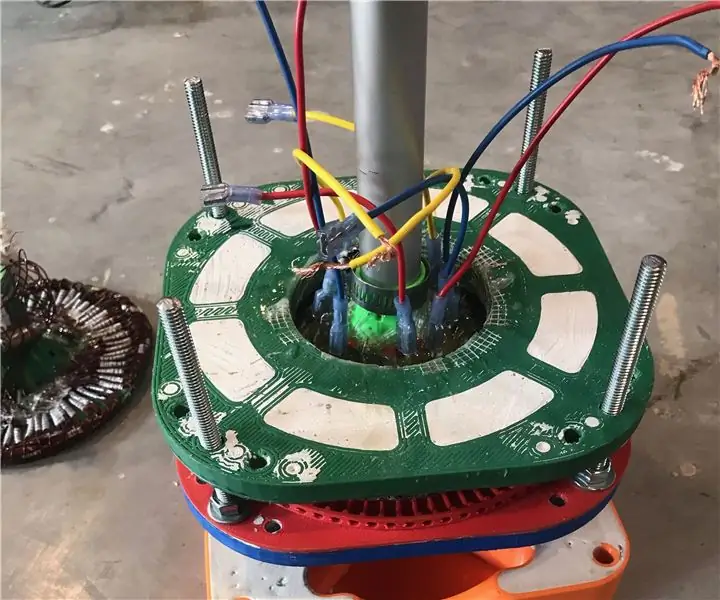
Inhaltsverzeichnis:
2025 Autor: John Day | [email protected]. Zuletzt bearbeitet: 2025-01-23 12:52
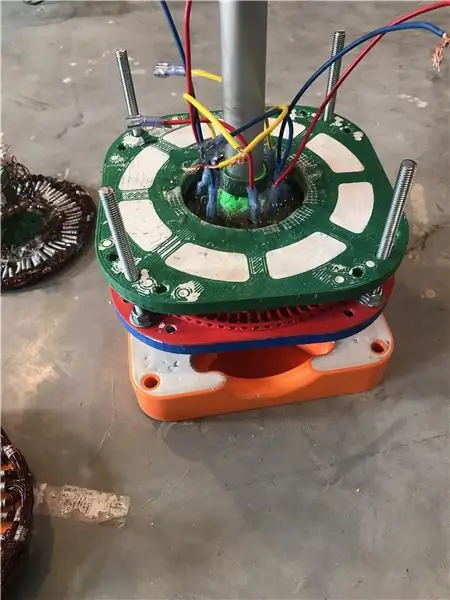
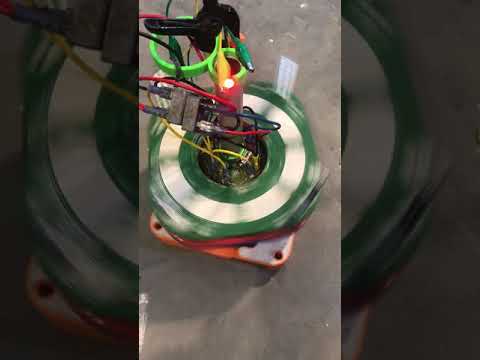
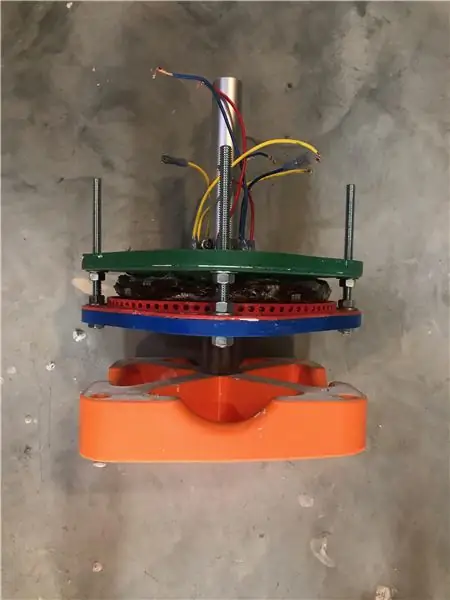
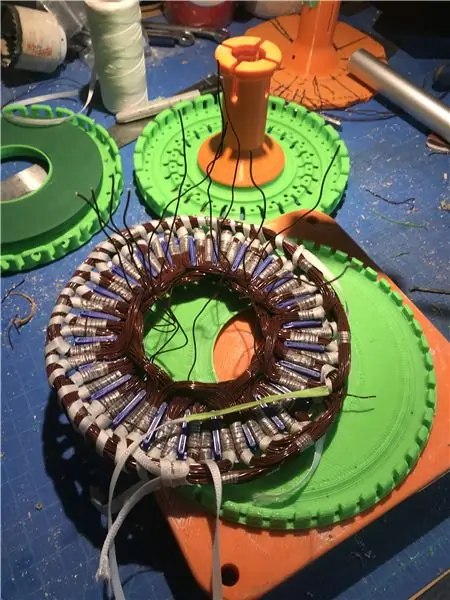
HALT!! LESEN SIE DIES ZUERST!!! Dies ist eine Aufzeichnung eines Projekts, das sich noch in der Entwicklung befindet. Bitte bieten Sie Unterstützung an.
Mein letztendliches Ziel ist, dass diese Art von Motor/Generator zu einem parametrisierten Open-Source-Design werden kann. Ein Benutzer sollte in der Lage sein, einige Parameter wie Drehmoment, Geschwindigkeit, Strom, Volt / U/min, gängige Magnetgrößen und möglicherweise verfügbarer Platz einzugeben, und eine Reihe von 3D-druckbaren.stl- und.dxf-Schnittdateien sollte generiert werden.
Was ich getan habe, ist eine Plattform zu schaffen, die ein simuliertes Design validieren kann, das dann von der Community zu einem optimaleren Gerät weiterentwickelt werden kann.
Dies ist zum Teil ein Grund, warum ich dies mit einem Dynamometer eingerichtet habe. Ein Dynamometer misst Drehmoment und Drehzahl, damit PS oder Watt gemessen werden können. In diesem Fall habe ich die Lichtmaschine mit einer durchgehenden, stationären Welle gebaut, die den Aufbau eines Dynamometersystems einfacher macht und so konfiguriert werden kann, dass sie von einem RC-Regler (hoffentlich) als Motor angetrieben und das Drehmoment gemessen wird am Ausgang, sowie Drehzahl, V und Ampere, wodurch der Motorwirkungsgrad bestimmt werden kann.
Für meine Zwecke kann es von einem Motor mit variabler Drehzahl (Überschuss von Akku-Bohrschrauber, mit Untersetzungsgetriebe) angetrieben und der Wellendrehmomenteingang gemessen sowie V und Ampere ausgegeben werden, wodurch ein echter Wirkungsgrad und die erwarteten Turbinenlasten erzielt werden können simuliert werden.
In diesem Modus hoffe ich, einen RC-Regler mit regenerativem Bremsen und vielleicht einen Arduino zu verwenden, um die Last zu steuern, die mein VAWT trägt, um MPPT (Multi Power Point Tracking) zu erreichen.
MPPT wird sowohl in der Solar- als auch in der Windturbinensteuerung verwendet, aber bei Wind ist es etwas anders. Ein großes Problem bei der Windkraft ist, dass sich die aus dem Wind verfügbare Energie um den Würfel, also um das Achtfache, erhöht, wenn sich die Windgeschwindigkeit von 10 km/h auf 20 km/h verdoppelt. Wenn 10 W bei 10 km/h verfügbar wären, dann sind 80 W bei 20 km/h verfügbar. Es ist großartig, mehr Energie zu haben, aber die Leistung der Lichtmaschinen verdoppelt sich nur, wenn sich die Geschwindigkeit verdoppelt. Wenn Sie also die perfekte Lichtmaschine für 20 km/h Wind haben, kann ihre Last so stark sein, dass sie bei 10 km/h nicht einmal anspringt.
MPPT verwendet einen Hochleistungs-Halbleiterschalter, um eine Lichtmaschine sehr schnell zu trennen und dann wieder anzuschließen. Es ermöglicht Ihnen, einzustellen, wie viel Last eine Lichtmaschine trägt, und das Multi des MPPT bedeutet, dass Sie verschiedene Lasten für unterschiedliche Geschwindigkeiten einstellen können.
Dies ist sehr nützlich, da alle Arten von Turbinen ihre maximale Energie sammeln, wenn die Last an die verfügbare Energie oder Windgeschwindigkeit angepasst wird.
SO
Dies ist kein Rezept, obwohl ich glaube, dass es von dem kopiert werden könnte, was ich gepostet habe, und würde Ihnen gerne weitere Informationen zur Verfügung stellen, aber ich schlage vor, dass die beste Option darin besteht, mir Verbesserungen vorzuschlagen, bevor der Wettbewerb „Circuits and Sensors“endet, damit ich dieses instructable in Betracht ziehen, beantworten und vielleicht verbessern kann.
Ich werde weiterhin Informationen aktualisieren, überarbeiten und hinzufügen. Wenn es jetzt interessant ist, möchten Sie vielleicht noch einmal vorbeischauen, aber ich hoffe, dass ich einiges fertig habe, bevor der Sensors-Wettbewerb am 29./19. Juli endet.
Außerdem bin ich kein besonders soziales Biest, aber ich klopfe mir ab und zu gerne auf die Schulter, und das ist einer der Gründe, warum ich hier bin:-) Sag mir, wenn dir meine Arbeit gefällt und du sehen willst mehr Bitte:-)
Dieses Projekt entstand, weil ich eine kontrollierbare Last zum Testen meiner Turbinenkonstruktionen wollte und ich wollte, dass sie leicht reproduzierbar ist, damit andere sie auch verwenden können. Zu diesem Zweck beschränkte ich mich darauf, etwas zu entwerfen, das nur mit einem FDM-Drucker gebaut werden konnte, ohne dass andere Werkzeugmaschinen benötigt wurden. Es scheint nicht viele kommerzielle Produkte zu geben, die den Bedarf an einem Generator mit hohem Drehmoment und niedriger Drehzahl ohne Rastmomente decken, obwohl es einige aus China gibt. Im Allgemeinen gibt es nicht viel Nachfrage, weil Getriebe so billig und Strom so billig ist.
Was ich wollte, war etwas, das etwa 12 V bei 40-120 U/min und etwa 600-750 W bei 120-200 U/min produzierte. Ich wollte auch, dass es mit preiswerten 3-Phasen-PMA-Controllern aus der RC-Welt (ESC's Electronic Speed Controllers) kompatibel ist. Eine letzte Anforderung war, dass es sich um einen Außenläufer (Gehäuse oder Schale mit Magneten dreht, während Welle mit Stator stationär ist) mit einer Welle, die das Gehäuse vollständig durchdringt, und einem Stator, der an der Welle festklemmt.
Dieses instructable ist in Arbeit, und ich poste es, damit die Leute einen Blick auf den Prozess bekommen, nicht so sehr, weil ich denke, dass sie es kopieren sollten. Eine wichtige Sache, die ich ändern würde, ist, dass die von mir gebaute Drahtträgerplatte nicht annähernd stark genug ist, um die Magnetfelder um den Ring richtig zu kanalisieren, so dass ein Großteil des Magnetflusses, der in diesen Magneten bezahlt wird, nach hinten verschwendet wird. Wenn ich das Design überarbeite, was ich in Kürze tun werde, würde ich wahrscheinlich die magnetischen Trägerplatten als CNC-geschnittene Stahlplatten machen. Stahl wäre ziemlich billig, viel stärker und würde den größten Teil dieses Builds vereinfachen. Es war interessant, die FDM/Draht/Gips-Verbundwerkstoffe zu machen, wie ich sie hier gezeigt habe, und mit eisenhaltigem PLA wären die Dinge auch anders gewesen. Ich entschied jedoch, dass ich etwas haben wollte, das wirklich Bestand hatte, also Stahlplatten.
Ich habe gute Fortschritte bei dieser Version gemacht, die ich zum Testen dieses VAWT verwenden werde. Was die Niederspannungsleistung angeht, bin ich noch nicht ganz am Ziel. Ich denke, meine Leistung in Watt/Drehmoment ist im richtigen Bereich, ich werde sie im Laufe der Zeit aktualisieren, aber zu diesem Zeitpunkt hat das, was ich habe, eine gute Chance, die kontrollierbare Last zu sein, die ich brauche. Wenn es kurzgeschlossen ist, scheint es in der Lage zu sein, ziemlich viel Drehmomentwiderstand zu bieten, mehr als genug, um die Turbine zu testen. Ich muss nur eine kontrollierte Widerstandsbank aufbauen, und ich habe einen Freund, der mir dabei hilft.
Eine Sache, die ich kurz ansprechen werde, ist, dass ich wie viele Leute jetzt einen 3D-Drucker (FDM mit PLA) seit einigen Jahren besitze, an dem ich 20-30 kg Freude hatte. Ich finde es jedoch oft frustrierend, da Teile jeder Größe/Stärke entweder teuer und sehr langsam zu drucken oder billig, schnell und dünn sind.
Ich weiß, wie viele Tausende dieser 3D-Drucker es gibt, die oft nichts tun, weil es zu lange dauert oder zu viel kostet, um nützliche Teile herzustellen. Ich habe eine interessante Lösung für stärkere schnellere Teile aus demselben Drucker und PLA entwickelt.
Ich nenne es eine "gegossene Struktur", bei der das gedruckte Objekt (bestehend aus einem oder mehreren gedruckten Teilen und manchmal Lagern und Wellen) mit Hohlräumen hergestellt wird, die mit einem aushärtenden flüssigen Füllstoff gefüllt werden sollen. Natürlich wären einige der offensichtlichen Optionen für eine gegossene Füllung etwas wie Epoxidharz, das mit kurzsträngigen geschnittenen Glasfasern beladen ist und für hochfeste und leichte Baugruppen verwendet werden könnte. Ich probiere auch einige kostengünstigere, umweltfreundlichere Ideen aus. Die andere Seite dieser "gegossenen Struktur"-Baugruppe besteht darin, dass der Hohlraum oder der Hohlraum, den Sie füllen möchten, hochfeste Elemente mit kleinem Durchmesser haben kann, die vorgespannt auf der gedruckten "Form / dem Stopfen" aufgereiht sind, was die resultierende Struktur ergibt ein Verbund aus Materialien und Struktur, Teil Stressed Skin (der PLA-Mantel), aber mit einem Kern mit hoher Druckfestigkeit, der auch Elemente mit hoher Zugfestigkeit enthält. Ich werde ein zweites instructable mit diesem tun, also werde ich hier darüber sprechen, nur um abzudecken, wie es zu diesem Build gehört.
Schritt 1: Materialliste und Prozess
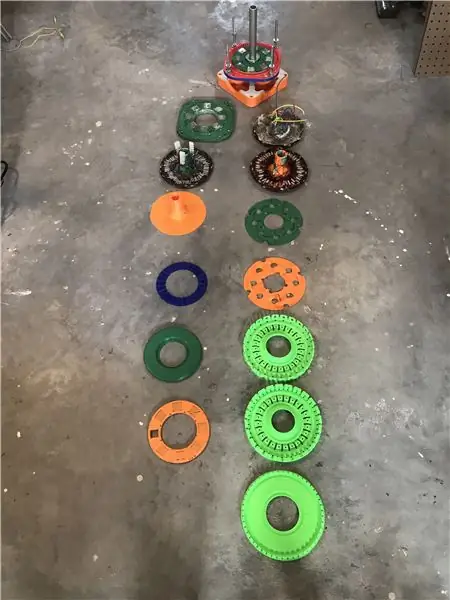
Die PMA besteht aus 3 Baugruppen, wobei jede Baugruppe eine Vielzahl von Teilen und Materialien enthält oder verwendet.
Von oben (Lagerseite) nach unten (Statorseite), 1. Lagerträger und oberes Lagerfeld
2. Stator
3. Unteres Magnetarray
1. Der Lagerträger und das obere Magnetarray
Dafür habe ich die oben aufgeführten 3D-gedruckten Teile verwendet
- 150mm8pol oberes Magazin und Lagerträger CV5.stl,
- Lagerseite Innenplatte
- Lagerseite Außenplatte
- 1" ID selbstausrichtendes Lager (wie in Standard-Lagerblöcken ++ Internet-Link hinzufügen),
- 25' aus 24g verzinktem Stahldraht
- 15 'von 10g verzinktem Stahldraht
- 2 Rollen grobe Stahlwolle
Optional können der schwere Stahldraht und die Stahlwolle durch Stahlträgerplatten ersetzt werden, Laser- / Wasserstrahlschnitt oder eine 3D-gedruckte magnetische Trägerplatte ist möglich (aber schwerer Stahldraht ist immer noch eine gute Idee, da er einer plastischen Verformung widersteht) Zeit). Ich habe versucht, eine Trägerplatte mit mit Eisenoxidpulver beladenem Epoxid zu gießen und hatte einigen Erfolg. Eine seitliche Verbesserung der Flusskopplung zwischen Magneten in der Anordnung durch Verwendung einer effektiveren Trägerplatte sollte die Spannung bei niedrigeren Drehzahlen erhöhen. Es ist auch gut zu bedenken, dass dies die Hauptstrukturkomponente ist und die Rückplatte die Kräfte von den Magneten auf die Abstützpfosten überträgt. Die magnetischen Kräfte, die die Platten aufeinander zu ziehen, können Hunderte von lbs betragen, und die Kräfte nehmen exponentiell (gewürfelt, in die dritte Potenz) zu, wenn sich die Platten nähern. Dies kann sehr gefährlich sein, und es ist Vorsicht geboten mit Werkzeugen und anderen Gegenständen, die von der montierten Platte oder deren Rückseite angezogen werden könnten!
Ich habe ungefähr 300ft 24g beschichteten Magnetdraht in den Wicklungen verwendet, auf die ich später ausführlich eingehen werde.
Schritt 2: Herstellung der Magnetplatten
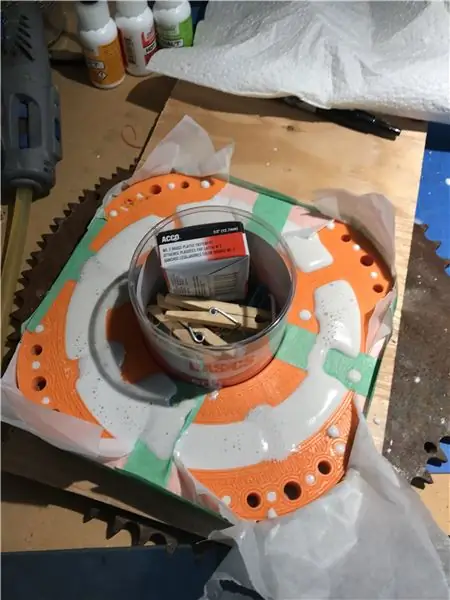
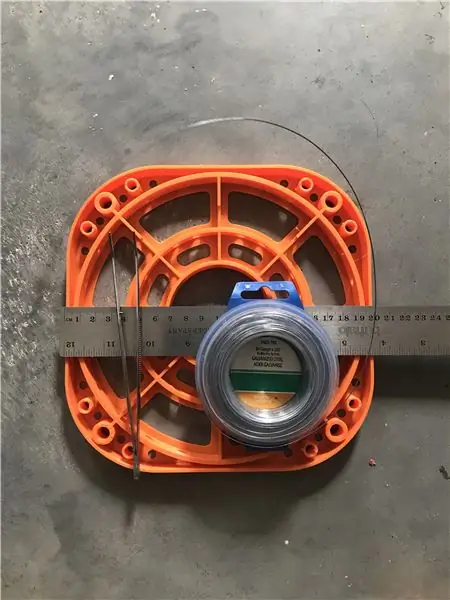
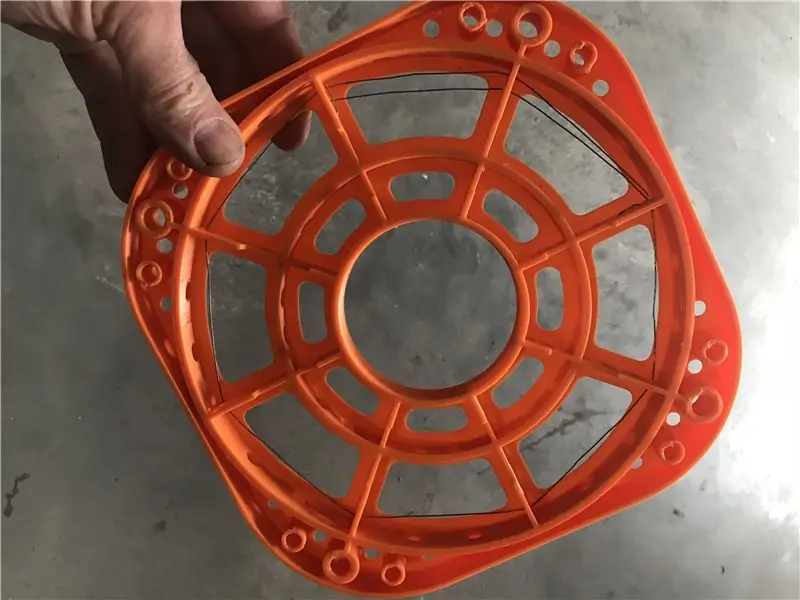
In diesem Axialflussgenerator verwende ich zwei Magnetarrays, eine auf jeder Seite der Statorspulen, um das Cogging zu minimieren und die Leistung zu maximieren. Dies bedeutet, dass kein Magnetkern benötigt wird, um das Magnetfeld durch die Kupferwicklungen zu ziehen, wie dies bei den meisten Motor-/Alt-Geometrien der Fall ist. Es gibt einige Axialflussdesigns, die Ferriskerne verwenden, und ich werde in Zukunft möglicherweise einige Experimente auf diese Weise versuchen. Ich würde gerne 3D-druckbares eisenbeladenes Material ausprobieren.
In diesem Fall habe ich ein 8-poliges Magnetarray in einem etwa 150 mm großen Kreis mit 1 "x 1" x 0,25" Seltenerdmagneten gewählt. Diese Größe sollte sicherstellen, dass alle Teile auf ein 210 mm x 210 mm Druckbett passen. Im Allgemeinen habe ich diese Lichtmaschine zuerst dimensioniert, indem ich verstanden habe, dass je größer der Durchmesser, desto besser in Volt pro U/min, also so groß gemacht wurde, dass sie bequem in mein Druckbett passt. Zu Ihrer Information, es gibt mehr als einen Grund, warum größer besser ist: mehr Platz für Magnete, je weiter die Magnete von der Mitte entfernt sind, desto schneller bewegen sie sich und es gibt auch mehr Platz für Kupfer! All diese Dinge können sich schnell summieren! Ich bin jedoch zu dem Schluss gekommen, dass in dieser Größenklasse ein konventioneller Flusssystem könnte ein besserer Eigenbau sein. Kleine Rotoren haben nicht viel Platz und die Dinge können ziemlich eng werden, besonders wenn Sie eine durchgehende Welle machen, wie ich es in diesem Design getan habe. Auch wenn Ihr Magnet (radiale Länge) klein im Verhältnis zu Ihrem Rotordurchmesser ist, wie in diesem (ungefähr 6 "Durchmesser zu 1" Magnet), dann ist der Windi ng wird etwas seltsam, da der innere Wickelkopf nur etwa die Hälfte der Länge des äußeren beträgt.
Zurück zur Anweisung! Die Art und Weise, wie ich die Magnetplatten dieser Lichtmaschine zusammengebaut habe, besteht darin, zuerst die Magnetplatte (grün) auf den roten Flansch / die Rückplatte zu kleben. Dann legte ich die Magnetplatte auf ein paar dünne Schichten Sperrholz (ca. 0,75 dicke) und legte beide auf eine schwere Stahlplatte, damit die Magnete die Baugruppe festklemmen können. Dann wickelte ich Stahldraht auf die Rückseite der Magnetplatten. Das lief nicht ganz so, wie ich es mir erhofft hatte. Das starke Magnetfeld zog den Draht zur Mitte der Magnete, und es gelang mir nicht, jede Drahtreihe so zu biegen, dass sie perfekt an die nächste Stelle passte, ohne die erste Wicklung zu drängeln. Ich hatte gehofft, dass ich den Draht einfach aufspulen könnte und der magnetische Fluss ihn festhalten würde. Als nächstes versuchte ich, Drahtringe zu schneiden, und das war besser, aber immer noch weit von dem entfernt, was ich wollte Ich habe gehofft, eine schöne, konsistente Trägerplatte aus Draht zu erhalten. Komplexere Möglichkeiten sind möglich und könnten zukünftige Experimente wert sein. Ich habe auch versucht, im Magnetfeld verdichtete Stahlwolle als Trägerplatte oder Flussmittel zu verwenden Rückweg Dies schien zu funktionieren, aber die tatsächliche Eisendichte schien nicht sehr hoch zu sein, also habe ich Ich würde seine Wirksamkeit nicht testen, zum Teil, weil ich der Meinung war, dass die Drahtstruktur für die mechanischen Belastungen der Magnetplatten wichtig ist. Die Stahlwolle kann auch eine zukünftige Untersuchung wert sein, aber wasserstrahlgeschnittene Stahlplatten sind wahrscheinlich die nächste Option, die ich versuchen werde.
Als nächstes nahm ich das orange 3D-gedruckte Teil und wob Draht durch und um es herum, entlang der Richtungen der höchsten Belastung, Schraube an Schraube und Schraube an jeder Ecke ein paar Mal zur Mitte. Ich habe es auch um die Schraubenlöcher gewickelt, in denen die gesamte Gewindestange als Hebepfosten verläuft, um den Abstand zwischen den Platten zu halten und einstellbar zu machen.
Nachdem ich überzeugt war, dass die Magnetplatte und der Flansch gut genug waren und die orangefarbene Trägerplatte zufriedenstellend mit Verstärkungsdraht eingefädelt war, verband ich die beiden mit Klebstoff. Es ist Vorsicht geboten, da diese Klebeverbindung wasserdicht oder dicht sein muss. Ich hatte die ersten beiden Male Undichtigkeiten, und es ist ein Durcheinander, verschwendet viel Gips und ist mehr Stress, als Sie brauchen. Ich würde empfehlen, etwas Blaukleber oder anderen Kaugummi wie nicht permanenten Klebstoff bei sich zu haben, um Lecks schnell zu flicken. Sobald die Teile verbunden sind, füllen Sie das Verstärkungsmaterial Ihrer Wahl. Ich habe einen harten Gips verwendet, der mit PVA-Kleber modifiziert wurde. Der Gips soll eine Kompression von 10.000 psi erreichen, aber nicht viel Spannung (also der Draht). Ich würde gerne Epoxy mit gehacktem Glas und Cabosil oder Beton und Beimischungen ausprobieren.
Eine praktische Sache an dem Pflaster ist, dass Sie, wenn es einmal tritt, ziemlich viel Zeit haben, wo es hart, aber zerbrechlich ist und Lecks oder Kleckse leicht abgekratzt oder abgeschlagen werden können.
In dieser Ausführung gibt es zwei Magnetplatten. Einer hat ein Lager, eine Standard 1 Stehlager-Selbstausrichtungseinheit. Ich habe meins schon früh in die Magnetanordnung gedrückt. Für die Anwendung, für die ich es entworfen habe, wird ein zweites Lager in der Turbine über der Lichtmaschine angeordnet, also nur das eine Pendellager verwendet. Das war am Ende etwas mühsam. Diese Teile könnten auch mit jeder Magnetplatte mit einem Lager zusammengebaut werden, wenn die Ausgangsdrähte vom Stator intern durch die montierte Welle geführt würden ermöglichen die Montage von gegenläufigen Propellern an einer gemeinsamen, nicht rotierenden Welle/Rohr.
Schritt 3: Erstellen des Stators

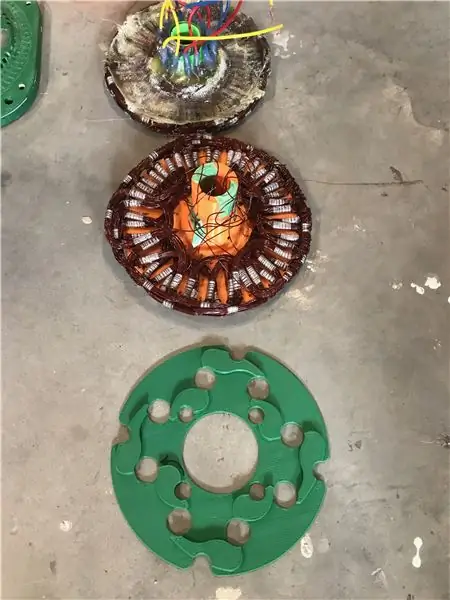
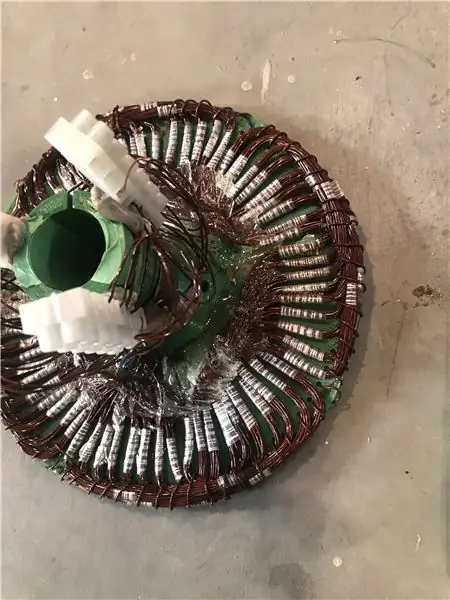
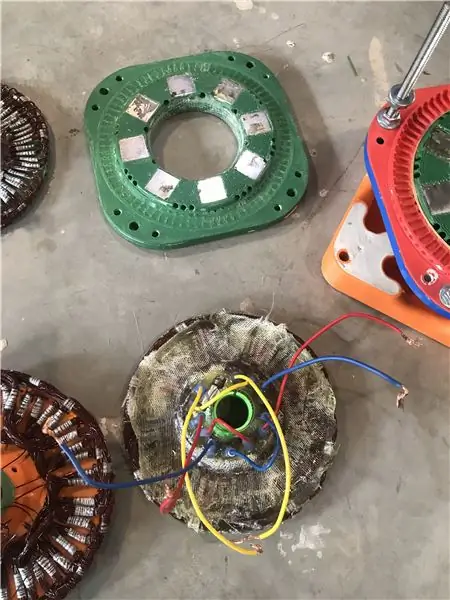
In Übereinstimmung mit meinem Thema, zu erklären, was ich getan habe und warum es damals wie eine gute Idee erschien, wird der Stator etwas mehr Platz benötigen.
In einem PMA sind die Wicklungen im Allgemeinen stationär, während sich die Magnetbaugruppen drehen. Dies ist nicht immer der Fall, aber fast immer. In einer axialen Flussanordnung wird mit dem Verständnis der grundlegenden "Rechte-Hand-Regel" davon ausgegangen, dass bei jedem Leiter, der auf ein rotierendes Magnetfeld trifft, Strom und Spannung zwischen den Enden des Drahtes erzeugt werden, wobei die Höhe des Nutzstroms proportional ist in Richtung des Feldes. Bewegt sich das Feld parallel zum Draht (zB im Kreis um die Drehachse), wird kein Nutzstrom erzeugt, aber erhebliche Wirbelströme, die der Bewegung der Magnete Widerstand leisten. Wenn der Draht senkrecht verläuft, wird die höchste Spannungs- und Stromabgabe erreicht.
Eine weitere Verallgemeinerung ist, dass der Raum innerhalb des Stators, durch den der magnetische Fluss während der Rotation fließt, für eine maximale Wattleistung mit so viel Kupfer wie möglich gefüllt sein sollte, alles radial verlegt. Dies ist ein Problem bei Axialflusssystemen mit kleinem Durchmesser, da in diesem Fall die für Kupfer verfügbare Fläche nahe der Welle ein Bruchteil der Fläche am Außenrand ist. Es ist möglich, im innersten Bereich, auf den das Magnetfeld trifft, 100% Kupfer zu erhalten, aber innerhalb dieser Geometrie erhält man vielleicht nur 50% am äußeren Rand. Dies ist einer der stärksten Gründe, sich von zu kleinen Axialflussdesigns fernzuhalten.
Wie ich bereits sagte, geht es bei diesem instructable nicht darum, wie ich es wieder tun würde, sondern darum, in einige Richtungen zu zeigen, die vielversprechend erscheinen, und einige der Schlaglöcher zu zeigen, die auf diesem Weg erreicht werden können.
Beim Entwerfen des Stators wollte ich ihn in Bezug auf die Voltabgabe pro U / min so flexibel wie möglich machen, und ich wollte, dass er dreiphasig ist. Für maximale Effizienz durch Minimierung der erzeugten Wirbelströme sollte jedes "Bein" (jede Seite einer Spule sollte als "Bein" betrachtet werden) jeweils nur auf einen Magneten treffen. Wenn Magnete nahe beieinander sind oder sich berühren, wie dies bei vielen Hochleistungs-RC-Motoren der Fall ist, werden während der Zeit, in der das "Bein" die Magnetflussumkehr durchläuft, erhebliche Wirbelströme entwickelt. Bei Motoranwendungen spielt dies keine so große Rolle, da die Spule von der Steuerung mit Strom versorgt wird, wenn sie sich an den richtigen Stellen befindet.
Ich habe das Magnetarray unter Berücksichtigung dieser Konzepte dimensioniert. Die acht Magnete in der Anordnung haben jeweils einen Durchmesser von 1 Zoll und der Abstand zwischen ihnen beträgt 1/2 Zoll. Dies bedeutet, dass ein Magnetsegment 1,5" lang ist und Platz für 3 x 1/2" "Beine" bietet. Jedes "Bein" ist eine Phase, so dass zu jedem Zeitpunkt ein Bein einen neutralen Fluss sieht, während die anderen beiden einen ansteigenden Fluss und einen abnehmenden Fluss sehen. Perfekter 3-Phasen-Ausgang, obwohl durch die Verwendung von quadratischen (oder tortenförmigen) Magneten dem Sternpunkt so viel Raum gegeben wird (um Wirbelströme zu minimieren), der Fluss fast früh seinen Höhepunkt erreicht, hoch bleibt und dann schnell auf Null abfällt. Diese Art der Ausgabe wird meiner Meinung nach trapezförmig genannt und kann für einige Controller, die ich verstehe, schwierig sein. 1-Zoll-Rundmagnete im selben Gerät würden eher eine echte Sinuswelle ergeben.
Im Allgemeinen wurden diese selbstgebauten Generatoren mit "Spulen", donutförmigen Drahtbündeln, gebaut, wobei jede Seite des Donuts ein "Bein" ist und eine Anzahl von Spulen in Reihe oder parallel miteinander verbunden werden kann. Die Donuts sind kreisförmig angeordnet, wobei ihre Mitten mit der Mitte des Magnetpfads ausgerichtet sind. Dies funktioniert, aber es gibt einige Probleme. Ein Problem besteht darin, dass, da die Leiter nicht radial sind, ein Großteil des Leiters nicht im 90-Grad-Winkel zum Magnetfeld verläuft, sodass Wirbelströme erzeugt werden, die als Wärme in der Spule und als Drehwiderstand in der Magnetanordnung auftreten. Ein weiteres Problem ist, dass die Leiter nicht radial sind und sich nicht so gut zusammenfügen. Die Leistung ist direkt proportional zu der Drahtmenge, die Sie in diesen Raum passen können, so dass die Leistung durch nicht radiale "Beine" reduziert wird. Während es möglich wäre und manchmal in kommerziellen Designs gemacht wird, erfordert das Wickeln einer Spule mit radialen "Beinen, die oben und unten verbunden sind, 2x so viel Endwicklung wie eine Serpentinenwicklung, bei der die Oberseite eines Beins mit der Oberseite des" verbunden ist nächsten passenden Bein, und dann wird die Unterseite dieses Beins mit dem nächsten passenden Bein verbunden und so weiter und weiter.
Der andere große Faktor bei Axialflussgeneratoren dieser Art (rotierende Magnete über und unter dem Stator) ist der Spalt zwischen den Platten. Dies ist eine Würfelgesetz-Beziehung, da Sie den Abstand zwischen den Platten um 1/2 verringern, erhöht sich die magnetische Flussdichte um das 8-fache. Je dünner Sie Ihren Stator machen können, desto besser!
Vor diesem Hintergrund habe ich eine 4-lappige Wickelvorrichtung hergestellt, ein System zum Messen von etwa 50 Fuß Drahtlitzen eingerichtet und die Vorrichtung 6-mal gewickelt, um Drahtbündel mit einem Durchmesser von etwa 6 mm zu erzeugen. Diese passe ich auf den blauen Distanzring und binde sie durch die Löcher, so dass die Drahtenden hinten herauskamen. Dies war nicht einfach. Es wurde ein wenig geholfen, indem ich die Bündel sorgfältig zusammengeklebt hatte, damit sie nicht locker waren, und indem ich mir Zeit nahm und ein glattes Holzformwerkzeug verwendete, um die Drähte an Ort und Stelle zu drücken. Nachdem alle zusammengebunden waren, wurde der blaue Distanzring in die größte der hellgrünen Formwannen gelegt und mit Hilfe des dunkelgrünen Donutformwerkzeugs auf der anderen Seite der hellgrünen Wanne vorsichtig mit ein Schraubstock. Diese Formwanne hat eine Rille, in der die Bindedrahtwindungen sitzen. Dies erfordert Zeit und Geduld, während Sie vorsichtig etwa 1/5 Umdrehung drehen, drücken, drehen und weitermachen. Dadurch wird die Scheibe flach und dünn, während die Endwicklungen gestapelt werden können. Sie werden vielleicht feststellen, dass meine 4-lappige Wicklung gerade "Beine" hat, aber die inneren und äußeren Verbindungen sind nicht rund. Dies sollte ihnen das Stapeln erleichtern. Es hat nicht so gut geklappt. Wenn ich es noch einmal machen würde, würde ich die inneren und äußeren Endwicklungen kreisförmigen Bahnen folgen lassen.
Nachdem ich es flach und dünn gemacht und die Kanten nach unten gepackt hatte, wickelte ich ein flaches Band um die Kante, um es zu verdichten, und ein weiteres nach oben, unten und um jedes Bein und dann auch um das daneben. Danach können Sie die Bindedrähte entfernen und auf die kleinere Presswanne umsteigen, zurück zum Schraubstock gehen und ihn so dünn und flach wie möglich drücken. Sobald es flach ist, nehmen Sie es aus der Presswanne. Anstelle des aufwendigen Prozesses des sorgfältigen Wachsens und Beschichtens solcher Formen mit Trennmitteln verwende ich in der Regel nur ein paar Lagen Stretchfolie (aus der Küche). Legen Sie ein paar Schichten in den Boden der Form und legen Sie die Glasfaser auf die Stretchfolie. Als nächstes fügen Sie das Stator-Montagerohr hinzu, das auf die Oberseite der hellgrünen Formwanne passt, aber die Schicht aus Stretchfolie und Glasfaser dazwischen hat. Fügen Sie dann die Statorwicklung wieder ein, um sowohl die Stretchfolie als auch die Glasfaser nach unten zu drücken und das Statormontagerohr zu verriegeln. Dann zurück zum Schraubstock und wieder flach drücken. Sobald es gut in die Wanne passt, mit der Stretchfolie und Glasfaser dazwischen, wird Glasfasertuch hinzugefügt (mit einem Loch in der Mitte für das Statormontagerohr).
Jetzt ist es bereit, das Klebematerial zu gießen, üblicherweise werden Epoxid- oder Polyesterharz verwendet. Bevor dies geschieht, ist eine sorgfältige Vorbereitung wichtig, denn wenn Sie diesen Prozess einmal gestartet haben, können Sie nicht wirklich aufhören. Ich benutzte eine 3D-gedruckte Grundplatte, die ich zuvor gemacht hatte, mit einem 1 "Loch in der Mitte und einer flachen Platte darum herum. Ich benutzte ein 16" Stück 1" Aluminiumrohr, über das das Statorhalterungsrohr passen würde senkrecht zur flachen Platte gehalten. Die grüne Formwanne, die Statorwicklung und das Statormontagerohr wurden nach unten geschoben, um auf der flachen Platte zu sitzen. Vor dem Mischen von Epoxid bereitete ich zuerst 4 Stück Schrumpffolie vor und legte vorsichtig ein 5. Stück auf die dunkelgrüner Donut, damit er die minimalen Falten auf der Vorderseite gegen die Statorwicklung hat. Nachdem ich das Epoxid gemischt und auf das Glasfasertuch gegossen hatte, legte ich vorsichtig die Stretchfolie um das 1 "Rohr und platzierte das Grün darüber einen Ring bilden. Ich hatte auch ein paar alte Bremsscheiben vorbereitet, die etwas Gewicht gaben, und saß schön auf dem grünen Formring. Danach legte ich einen umgedrehten Topf auf die Bremsscheiben, und auf den Topf stapelte ich etwa 100 Pfund Zeug. Ich ließ dies 12 Stunden lang und es kam etwa 4-6 mm dick heraus.
Schritt 4: Testen und Sensoren
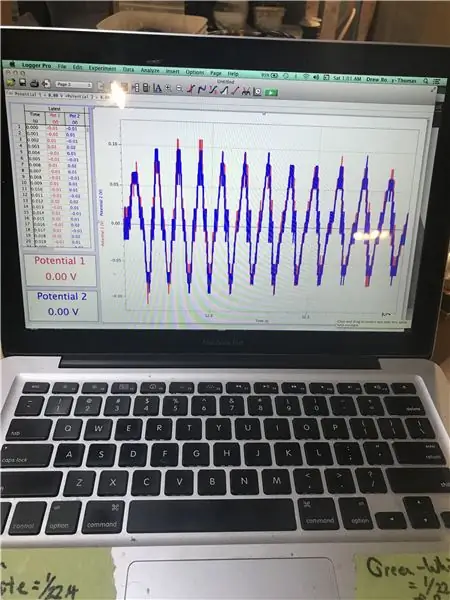
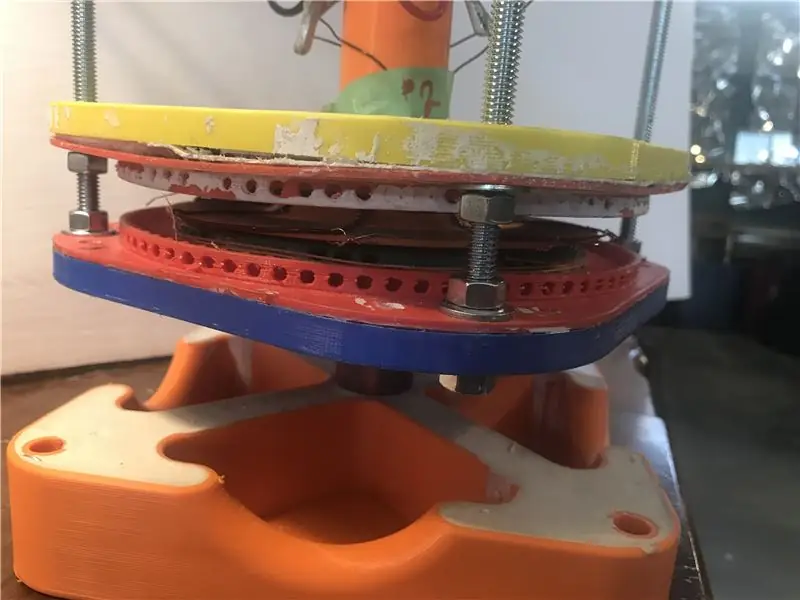
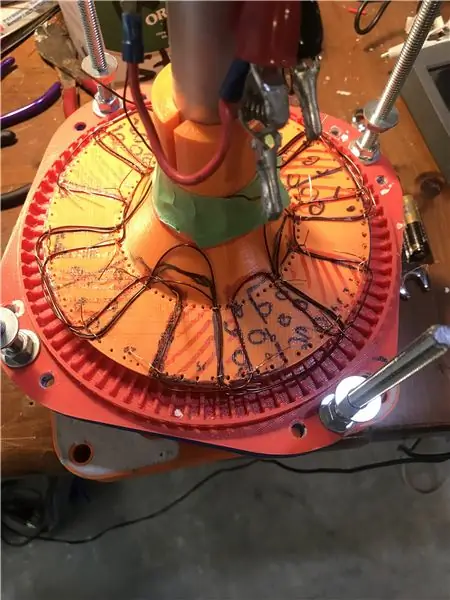
Es gibt eine Reihe von messbaren Ein- und Ausgängen der Lichtmaschine, und es ist nicht einfach, sie alle gleichzeitig zu messen. Ich bin sehr glücklich, einige Tools von Vernier zu haben, die dies viel einfacher machen. Vernier stellt Produkte auf Bildungsniveau her, die nicht für den industriellen Einsatz zertifiziert sind, aber für Experimentatoren wie mich sehr hilfreich sind. Ich verwende einen Vernier-Datenlogger mit einer Vielzahl von Plug-and-Play-Sensoren. Bei diesem Projekt verwende ich Hall-basierte Strom- und Spannungssonden, um die Generatorleistung zu messen, einen optischen Sensor zur Angabe der Generatordrehzahl und eine Wägezelle zur Messung der Drehmomenteingabe. Alle diese Instrumente werden etwa 1000 Mal pro Sekunde abgetastet und auf meinem Laptop aufgezeichnet, wobei der Vernier-Logger als AD-Passthrough-Gerät verwendet wird. Auf meinem Laptop kann die zugehörige Software Echtzeitberechnungen basierend auf den Eingaben ausführen und Drehmoment- und Drehzahldaten kombinieren, um Echtzeit-Eingangswellenleistung in Watt und Echtzeit-Ausgangsdaten in elektrischen Watt zu liefern. Ich bin mit diesem Test noch nicht fertig, und Input von jemandem, der ein besseres Verständnis hat, wäre hilfreich.
Ein Problem, das ich habe, ist, dass diese Lichtmaschine wirklich ein Nebenprojekt ist, und deshalb möchte ich nicht zu viel Zeit damit verbringen. So wie es ist, denke ich, dass ich es für eine kontrollierbare Last für meine VAWT-Forschung verwenden kann, aber schließlich würde ich gerne mit Leuten zusammenarbeiten, um es zu verfeinern, damit es effizient zu meiner Turbine passt.
Als ich vor etwa 15 Jahren mit der VAWT-Forschung begann, wurde mir klar, dass das Testen von VAWTs und anderen Antriebsmaschinen komplexer ist, als die meisten Leute denken.
Ein Hauptproblem ist, dass die in einer sich bewegenden Flüssigkeit repräsentierte Energie exponentiell zu ihrer Bewegungsgeschwindigkeit ist. Dies bedeutet, dass sich die im Fluss enthaltene Energie um das 8-fache erhöht (sie wird verdreifacht), wenn Sie die Geschwindigkeit eines Flusses verdoppeln. Dies ist ein Problem, da Lichtmaschinen linearer sind und im Allgemeinen, wenn Sie die Drehzahl einer Lichtmaschine verdoppeln, Sie etwa das 2-fache an Watt erhalten.
Diese grundlegende Diskrepanz zwischen der Turbine (Energiesammelvorrichtung) und dem Wechselstromgenerator (Wellenleistung zu elektrischer Nutzleistung) macht es schwierig, einen Wechselstromgenerator für eine Windkraftanlage auszuwählen. Wenn Sie eine Lichtmaschine für Ihre Windkraftanlage auswählen, die die meiste Leistung aus 20 km/h Wind erzeugt, wird sie wahrscheinlich erst bei 20-25 km/h anfangen, sich zu drehen, da die Last auf die Turbine durch die Lichtmaschine zu hoch ist. Bei dieser Lichtmaschinenübereinstimmung nimmt die Turbine, sobald der Wind über 20 km liegt, nicht nur nur einen Bruchteil der im Wind mit höherer Geschwindigkeit verfügbaren Energie auf, sondern die Turbine kann überdrehen und beschädigt werden, da die von der Lichtmaschine bereitgestellte Last nicht hoch ist genug.
In den letzten zehn Jahren ist eine Lösung durch den Preisverfall der Steuerelektronik wirtschaftlicher geworden. Anstatt zu versuchen, einen Drehzahlbereich abzustimmen, berechnet der Konstrukteur die maximale Drehzahl, mit der das Gerät betrieben werden soll, und wählt einen Generator basierend auf der Energiemenge und der idealen Drehzahl für die Turbine bei dieser Drehzahl oder etwas darüber aus. Dieser Generator würde, wenn er an seine Last angeschlossen ist, normalerweise im niedrigen Drehzahlbereich zu viel Drehmoment liefern, und die überlastete Turbine wird nicht die gesamte Energie aufnehmen, die sie hätte, wenn sie richtig belastet wäre. Um die richtige Last zu erzeugen, wird eine Steuerung hinzugefügt, die die Lichtmaschine kurzzeitig von der elektrischen Last trennt, damit die Turbine auf die richtige Drehzahl hochfahren kann und die Lichtmaschine und die Last wieder verbunden werden. Dies wird MPPT (Multi Power Point Tracking) genannt. Die Steuerung ist so programmiert, dass, wenn sich die Turbinendrehzahl ändert (oder die Lichtmaschinenspannung ansteigt), die Lichtmaschine etwa tausend Mal pro Sekunde angeschlossen oder getrennt wird, um der für diese Drehzahl oder Spannung programmierten Last zu entsprechen.