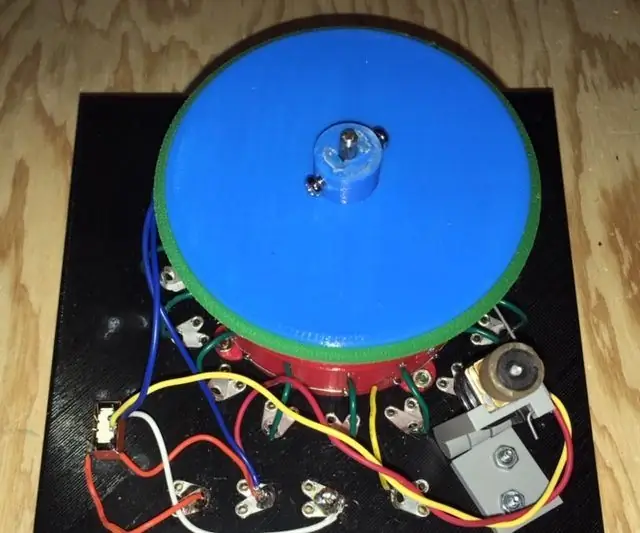
Inhaltsverzeichnis:
- Lieferungen
- Schritt 1: Drucken Sie die Teile
- Schritt 2: Bereiten Sie das Eingabe-Ausgabe-Panel vor
- Schritt 3: Bereiten Sie das Drehschalter-Schwungrad, den Drehknopf und den Rotor vor
- Schritt 4: Bereiten Sie den Rotary Switch Top vor
- Schritt 5: Bereiten Sie den Motor und die Motorhalterung vor
- Schritt 6: Bestücken Sie den Drehschalterkörper
- Schritt 7: Befestigen Sie den RS-Körper am Dezimal-Eingabe-Ausgabe-Panel
- Schritt 8: Verdrahten Sie den Drehschalter auf dem Dezimal-Eingabe-Ausgabe-Panel
- Schritt 9: Befestigen Sie den Motor und die Motorhalterung
- Schritt 10: Installieren Sie den Rotary Switch Rotor
- Schritt 11: Befestigen Sie den Rotary Switch Top
- Schritt 12: Verbinden Sie das Magnetventil und die Motorhalterung
- Schritt 13: Verdrahten Sie den Motor, das Magnetventil und das Relais
- Schritt 14: Testen
- Schritt 15: Abschließende Gedanken
2025 Autor: John Day | [email protected]. Zuletzt bearbeitet: 2025-01-23 12:52
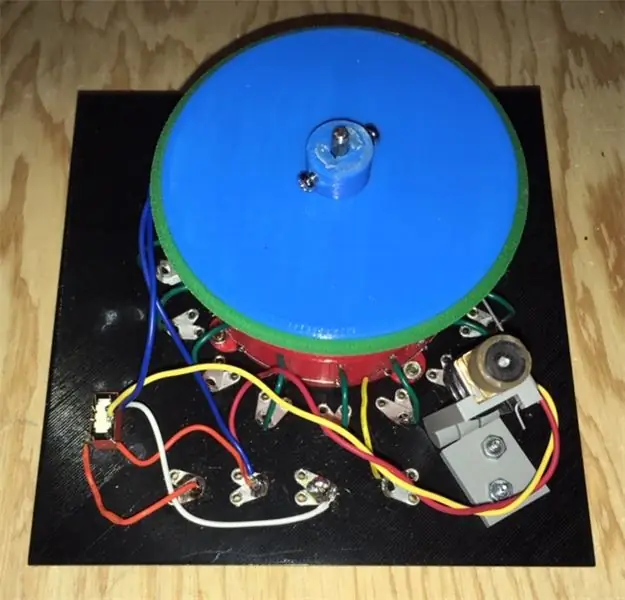
Dies ist der versprochene Nachfolger meines Minivac 601 Replica (Version 0.9) Instructable. Dies kam schneller als erwartet zusammen und ich bin mit dem Ergebnis ziemlich zufrieden. Das hier beschriebene Dezimal-Eingabe-Ausgabe-Panel ist ein Drop-In-Ersatz für die manuelle Version, die in der Version 0.9 Instructable beschrieben ist. Wie der Titel schon sagt, fügt es dem Drehschalter mit 16 Positionen die motorisierte Funktion hinzu. Dies geschieht wie beim Original Minivac 601 über eine Friktionsantriebsimplementierung. Hier ist ein Video des motorisierten Rotary Switch in Aktion:
Das neue Design beginnt mit einem robusteren Rotary Switch mit echten Lagern für einen viel reibungsloseren Betrieb. Eines der Probleme mit dem vorherigen Design war, dass die Toleranzen am Schalter selbst ziemlich locker waren. Infolgedessen benötigte der Motor zu viel Drehmoment, um den Schalter richtig zu drehen.
Darüber hinaus wird der Motor bei dem neuen Design auf Magnetspulenbasis nur eingeschaltet, wenn er aktiv ist. Bei Nichtgebrauch wird es vom Schalter abgenommen, was ein großartiges "Gefühl" bei der manuellen Betätigung des Schalters ermöglicht.
Lieferungen
Für dieses Instructable benötigen Sie zusätzlich zu den 3D-gedruckten Teilen Folgendes:
- 1 4 mm Urethan-Rundriemen - ca. 300 mm erforderlich (Amazon)
- 2 F684ZZ Doppelgeschirmte Flanschkugellager 4x9x4 mm (Amazon)
- 1 12V-Magnetventil Uxcell a14032200ux0084 (Amazon)
- 1 Yosoo Micro DC 12V Untersetzungsmotor (Amazon)
- 2 M3 x 10 mm Schrauben mit Muttern
- 8 M3 x 8 mm Schrauben mit Muttern
- 2 M3 x 6 mm Schrauben
- 4 M2 x 6 mm Schrauben
- 1 kleines Stück Gummischlauch mit einem Innendurchmesser von ca. 7 mm und einem Außendurchmesser von ca. 10 mm
- 1 Allzweck-12-V-DPDT-Signalrelais - Digi-Key Teilenummer 399-11029-5-ND
- 16 Reed-Schalter - Digi-Key Teilenummer 2010-1087-ND
- 19 Scheibenmagnete - 6 mm (Durchmesser) x 3 mm (Höhe)
- 1 85 mm Länge aus 4 mm Pianodraht
- 1 65 mm Länge aus 0,8 mm Pianodraht
Schritt 1: Drucken Sie die Teile
Druckauflösung: 0,2 mm
Füllung: 20%
Umfänge: 5 (Alle Löcher in den oberen Platten sollten sehr "robust" sein, um das Löten von Teilen zu unterstützen.)
Filament: AMZ3D PLA in Schwarz und Weiß für das Panel, jede Farbe(n) kann für die Innenteile verwendet werden
Hinweise: Alle Teile wurden in PLA ohne Stützen gedruckt. Die folgenden Teile sind für dieses Instructable erforderlich:
- 1 MV601 Dezimal-Eingabe-Ausgabe-Panel
- 1 MV601 Reibungsantriebsmotorrad
- 1 MV601 Motorhalterung
- 1 RS-Karosserie
- 1 RS Schwungrad
- 3 RS-Dichtung
- 1 RS-Knopf
- 1 RS-Rotor
- 1 RS-Oberseite
Schritt 2: Bereiten Sie das Eingabe-Ausgabe-Panel vor
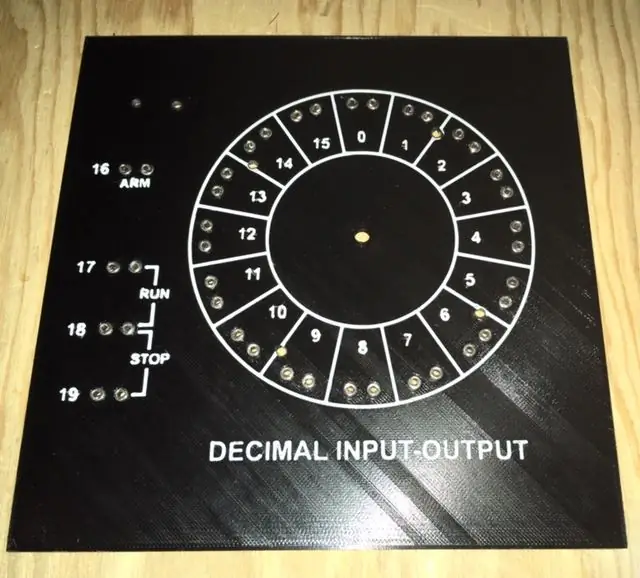
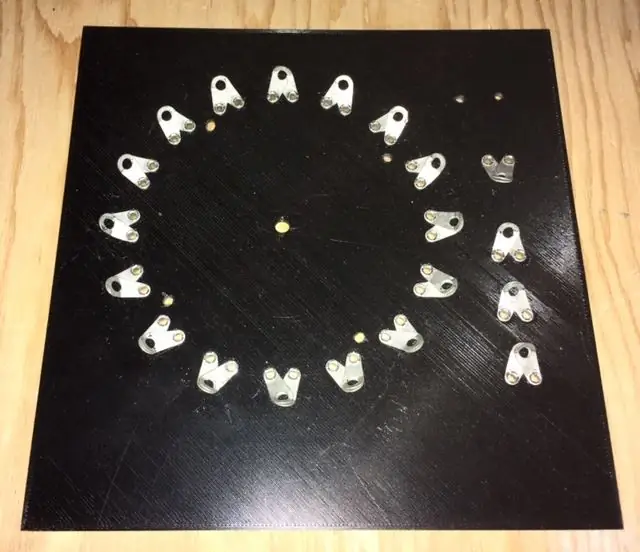
Befolgen Sie die Anweisungen aus Schritt 3 des Minivac 601 Replica (Version 0.9) Instructable, fügen Sie die Nieten und Lötösen zum Input-Output-Panel hinzu.
Zusätzlich ab Schritt 6:
Bereiten Sie die Lötösen vor, indem Sie jedes Paar von Lötösen auf dem Hauptpanel aufeinander zu drehen (mit dem Niet als Drehpunkt), bis die großen Löcher miteinander ausgerichtet sind. Biegen Sie die Enden der ausgerichteten Nasen vorsichtig einige Grad nach oben (dafür eignet sich eine kleine Spitzzange gut). Verwenden Sie die obigen Fotos, um die optimale Ausrichtung für jede Lasche zu bestimmen.
Schritt 3: Bereiten Sie das Drehschalter-Schwungrad, den Drehknopf und den Rotor vor
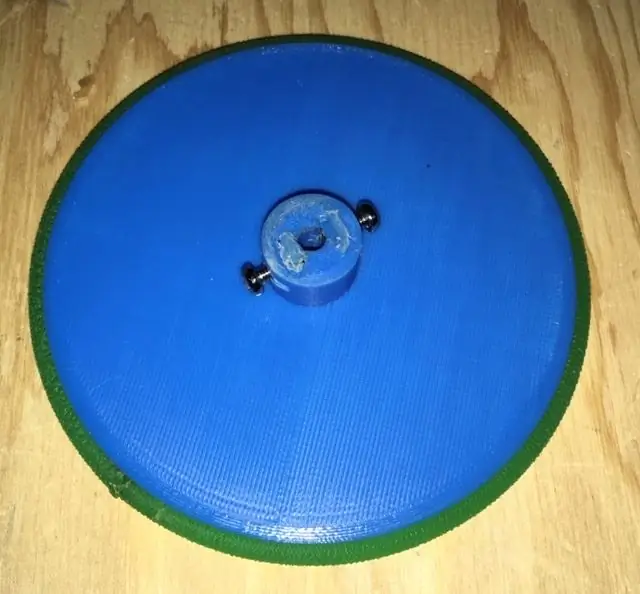
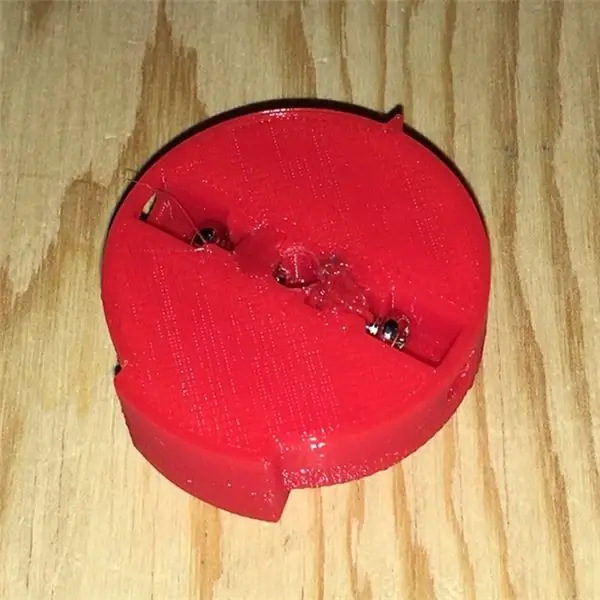
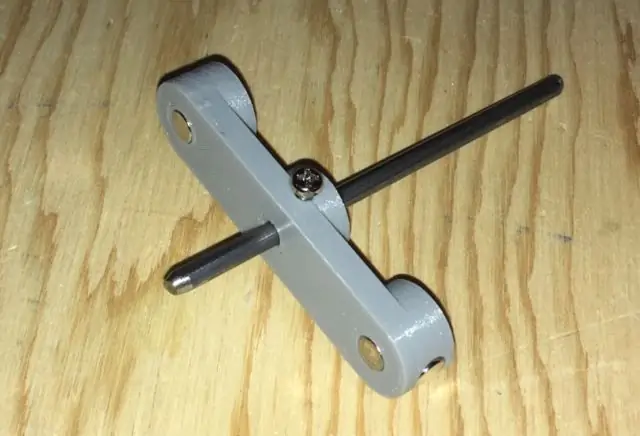
Drücken Sie sechs der M3-Muttern in die Schlitze oben am Schwungrad und Rotor und unten am Knopf. Schrauben Sie die M3 x 8 mm Schrauben von den Seiten in diese Muttern ein, bis sie gerade das Wellenloch erreichen, um als Stellschrauben zu dienen. An diesem Punkt benutzte ich einen 3D-Stift, um die Schlitze mit Filament zu füllen und die Muttern sicher zu halten. Das gleiche könntest du auch mit etwas Heißkleber erreichen.
Schneiden Sie eine Länge des 4 mm Urethan-Rundriemens nur wenige mm kürzer als der Umfang des Schwungrads. Erhitze die Enden der Schnur mit einer Kerze, bis sie gerade schmelzen, und verbinde dann die beiden Enden schnell miteinander. Halte die verbundenen Enden etwa 30-60 Sekunden lang zusammen, während der Kunststoff abkühlt, und versuche, sie so ausgerichtet wie möglich zu halten. Dazu gibt es viele gute YouTube-Videos. Dehnen Sie Ihren neuen Gummi-"O-Ring" über das Schwungrad in die Nut um den Rand herum, wie im Bild oben.
Setzen Sie zwei Scheibenmagnete in die Unterseite des RS Rotors ein. Es ist sehr wichtig, dass die Polarität der Magnete, die sich auf der Unterseite der RS-Rotorscheibe befinden, der Polarität der im RS-Gehäuse befestigten Magneten entgegengesetzt ist. Mit anderen Worten, sie sollten anziehen! Setzen Sie auch einen Scheibenmagneten in das Loch an der Seite des Rotors ein. Verwenden Sie bei Bedarf ein wenig Klebstoff, um diese Magnete zu befestigen.
Schieben Sie einen 85 mm langen 4 mm Pianodraht in die Welle des Rotors. Lassen Sie etwa 18 mm aus der Unterseite des Rotors herausragen, wie oben abgebildet. Ziehen Sie die Stellschrauben an der Welle fest. Nicht überdrehen.
Schritt 4: Bereiten Sie den Rotary Switch Top vor
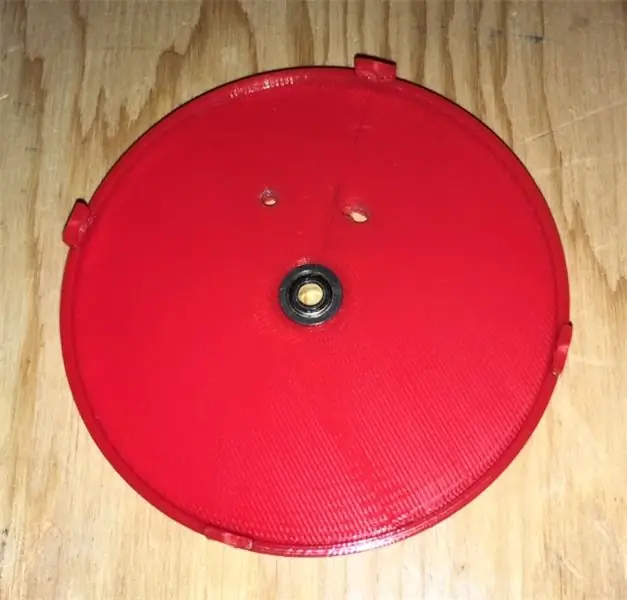
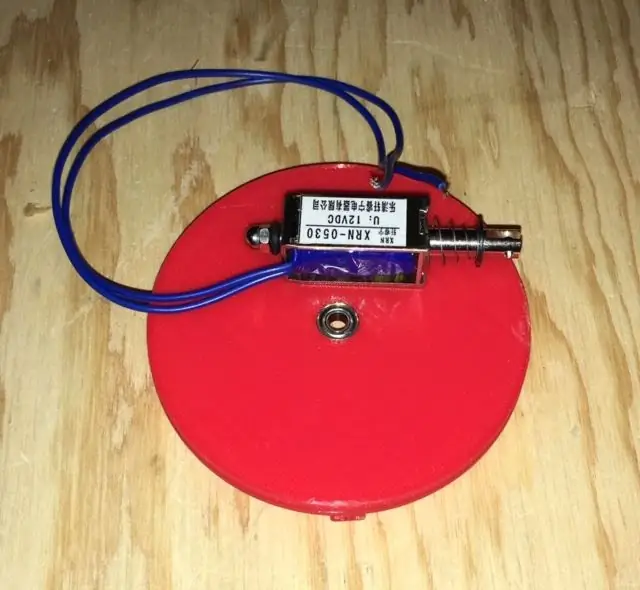
Drücken Sie von der Innenseite des Rotary Switch Top eines der Flanschkugellager in das mittlere Loch. Bei ordnungsgemäßer Installation sollte es innen und außen bündig mit der RS-Karosserie abschließen.
An der Außenseite befestigen Sie das 12V-Magnetventil mit zwei M3 x 6 mm Schrauben, den vorgesehenen Löchern und den Gewindelöchern im Magnetventil selbst am Rotary Switch Top. Siehe das Bild oben.
Schritt 5: Bereiten Sie den Motor und die Motorhalterung vor
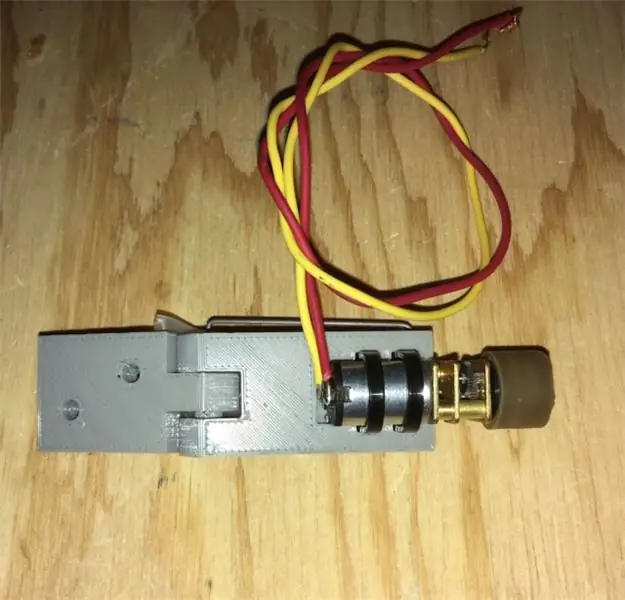
Schieben Sie das Reibungsantriebsmotorrad auf die Welle des 12-V-Untersetzungsmotors. Es sollte eng anliegen. Schneiden Sie nach dem Anbringen einen 9 mm langen Gummischlauch der passenden Größe zu und spannen Sie ihn über das soeben hinzugefügte Motorrad. Dies sollte für viel Traktion sorgen.
Löten Sie einige Drähte auf die Leitungen an der Unterseite des Motors. Seien Sie vorsichtig, diese sind ziemlich empfindlich.
Befestigen Sie den Motor mit ein paar kleinen Kabelbindern an der Motorhalterung in dem dafür vorgesehenen Schlitz wie im Bild oben.
Schritt 6: Bestücken Sie den Drehschalterkörper
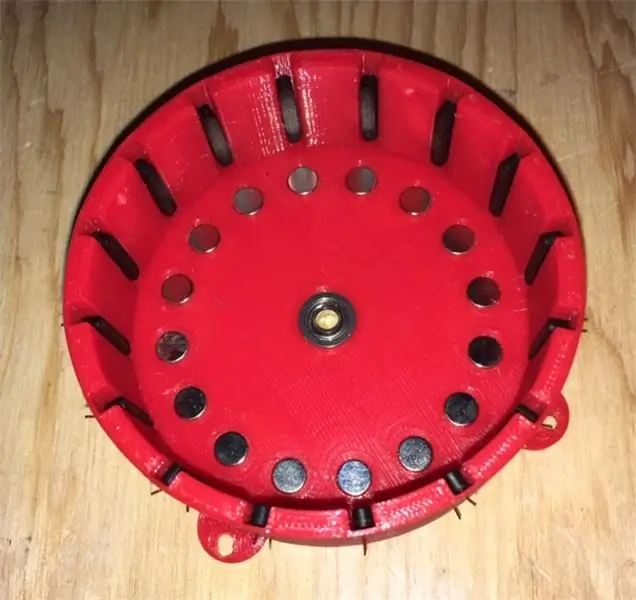
Schieben Sie zuerst das andere Flanschkugellager von innen in das Mittelloch des RS-Körpers. Bei ordnungsgemäßer Installation sollte es innen und außen bündig mit der RS-Karosserie abschließen. Mine passte gut und brauchte keinen Kleber, um an Ort und Stelle zu bleiben.
Setzen Sie die sechzehn Reedschalter in die Schlitze um den RS-Körper ein. Die Stifte für die Schalter sollten leicht von der Innenseite zur Außenseite des Gehäuses durch die Löcher passen und können von außen vorsichtig gebogen werden, um den Schalter in Position zu halten.
Setzen Sie sechzehn Scheibenmagnete in den RS Body ein. Achten Sie darauf, dass die Polarität aller sechzehn Magnete gleich ist. Sie können sie mit etwas Kleber festhalten, wenn sie nicht selbst genug greifen. Sie sollten beim Einsetzen bündig mit dem Innenboden des RS-Körpers abschließen.
Schritt 7: Befestigen Sie den RS-Körper am Dezimal-Eingabe-Ausgabe-Panel
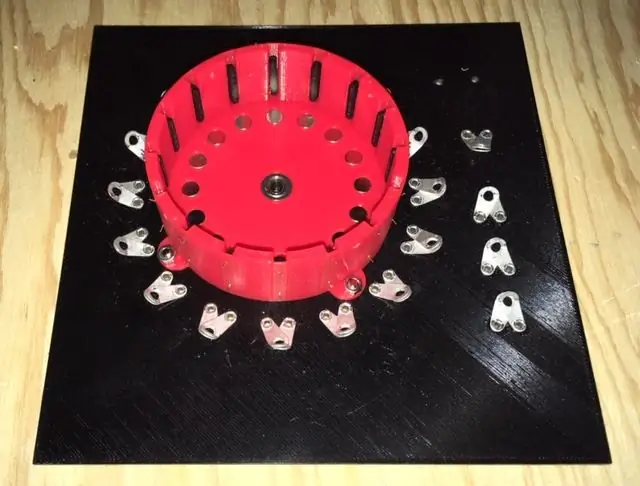
Befestigen Sie das RS-Gehäuse mit vier M3 x 8 mm-Schrauben und Muttern an der Rückseite des Input-Output-Panels, wie in der Abbildung oben gezeigt.
Schritt 8: Verdrahten Sie den Drehschalter auf dem Dezimal-Eingabe-Ausgabe-Panel
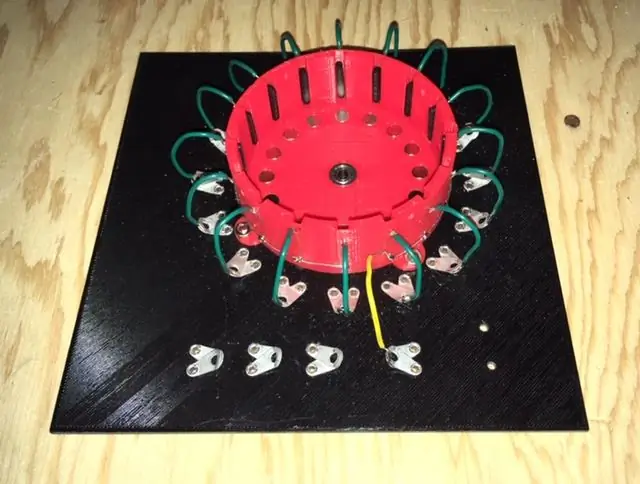
Draht in den Rotary Switch. Entfernen Sie zuerst genügend Isolierung von einem 22 AWG-Vollkerndraht, so dass das blanke Kupfer vollständig um den Drehschalterkörper gewickelt ist und mindestens 3 Zoll isolierter Draht übrig bleibt. Löten Sie den blanken Draht vorsichtig an die unteren Leitungen aller 16 Reedschalter, die sie miteinander verbinden. Sie sollten in der Position beginnen und enden, die der gelbe Draht im Bild oben zeigt, damit der Draht an der ARM-Lötfahne des Panels befestigt werden kann.
Bei kurzen Längen von 22 AWG-Draht verbinden Sie die obere Leitung von jedem Reed-Schalter mit der entsprechenden Lötfahne (grüne Drähte oben). Diese Verbindungen erfordern ein wenig Fingerspitzengefühl, um den Kunststoff nicht zu schmelzen.
Schritt 9: Befestigen Sie den Motor und die Motorhalterung
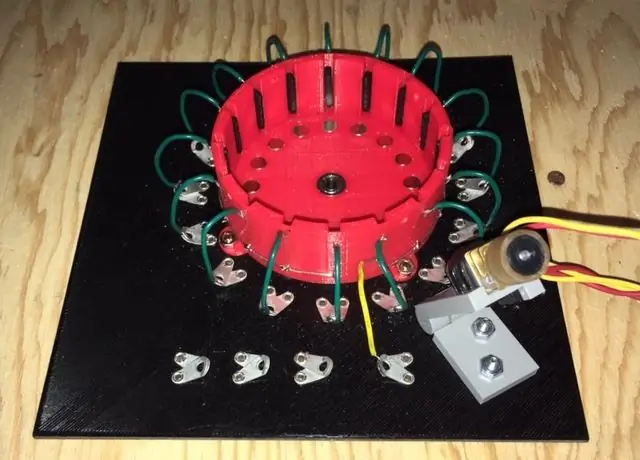
Befestigen Sie den Motor und die Motorbaugruppe mit den beiden M3 x 10 mm Schrauben und Muttern an der Rückseite des Digital Input-Output Panels. Verwenden Sie das obige Bild als Leitfaden.
Schritt 10: Installieren Sie den Rotary Switch Rotor
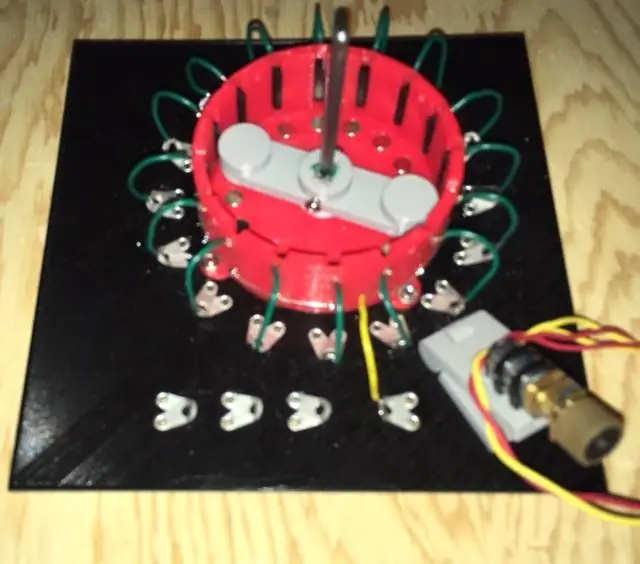
Fügen Sie drei Drehschalterdichtungen auf der Welle an der Unterseite des Rotors hinzu. Dadurch wird der richtige Abstand zwischen den Magneten am Gehäuse und am Rotor sichergestellt. Schieben Sie den Rotor und die Welle in das Lager an der Unterseite des Rotary Switch Gehäuses.
Schritt 11: Befestigen Sie den Rotary Switch Top
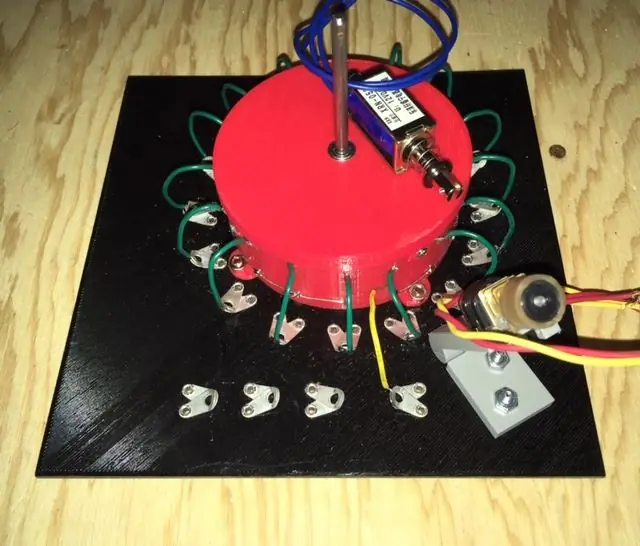
Schieben Sie das Rotary Switch Top auf die Welle und befestigen Sie es mit vier M2 Schrauben am Rotary Switch Gehäuse. Stellen Sie sicher, dass das Magnetventil mit der Motorhalterung ausgerichtet ist.
Schritt 12: Verbinden Sie das Magnetventil und die Motorhalterung
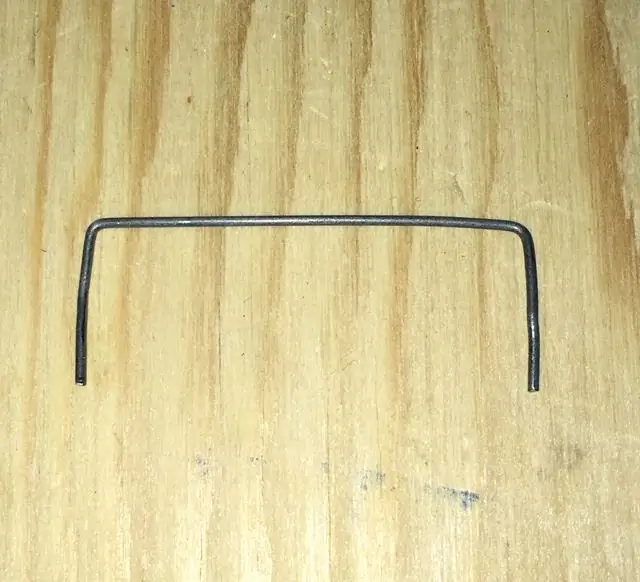
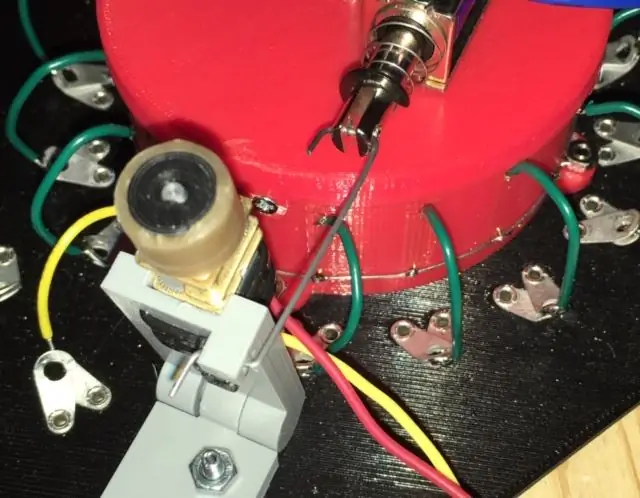
Verwenden Sie ein Stück 0,8 mm Pianodraht, um das Solenoid und die Motorhalterung zu verbinden. Wie im ersten Bild oben gezeigt, sollte der Draht an der langen Seite 35 mm und an den kürzeren Seiten etwa 15 mm betragen. Biegen Sie nach der Installation die kurzen Enden der Drähte, um zu verhindern, dass sie vom Magnetventil und der Motorhalterung rutschen. Siehe das zweite Bild.
Schritt 13: Verdrahten Sie den Motor, das Magnetventil und das Relais
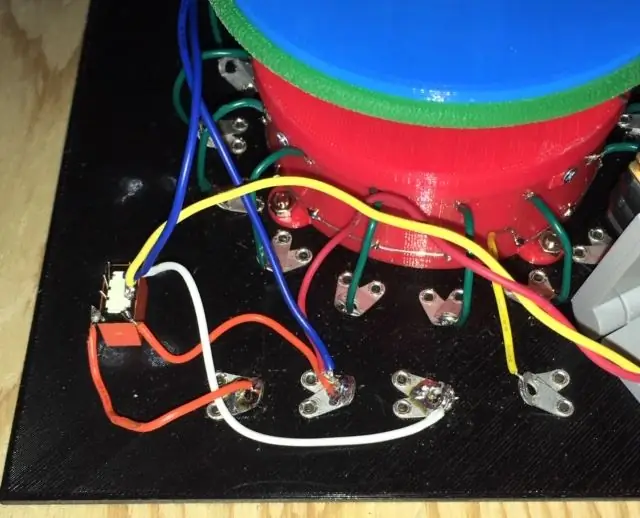
Verdrahten Sie den Motor, das Solenoid und das Relais wie im Bild oben. Die Magnetkabel (blau) sind parallel zum Motor (rot und gelb) verdrahtet. Ich habe den Motor und das Magnetventil einfach "tot abgehört" durch den Öffner des Relais (gelb, blau auf der einen Seite weiß auf der anderen Seite zu den RUN-Nieten (17)), dann die Relaisspule mit den STOP-Nieten (19) verdrahtet auf dem Dezimal-Eingabe-Ausgabe-Feld (orange). Motor, Magnetspule und Relaisspule (rot, blau, orange) haben alle ein gemeinsames Kabel, das mit den mit 18 gekennzeichneten gemeinsamen Nieten verbunden ist.
Schritt 14: Testen
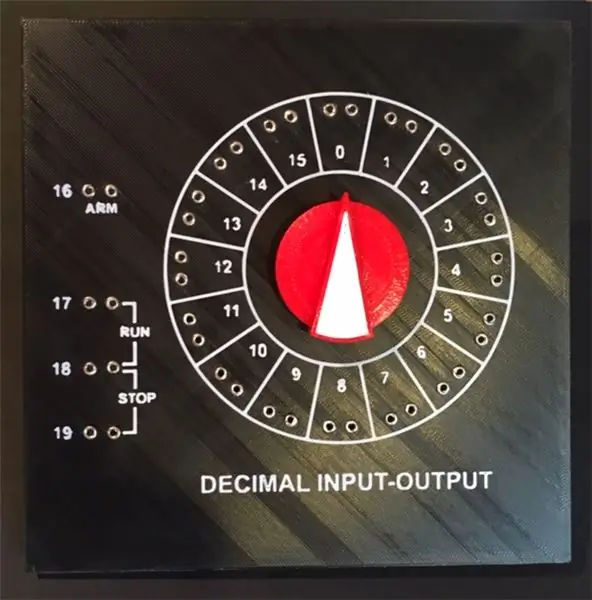
Bevor Sie den Rotary Switch Knob anbringen können, müssen Sie sicherstellen, dass der Zeiger des Drehknopfes auf den Rotary Switch Rotor Magneten ausgerichtet ist. Ich tat dies, indem ich mein Multimeter an den ARM und die 0-Punkte auf dem Panel anschloss und den Rotor drehte, bis der Stromkreis geschlossen war. Schieben Sie den Rotary Switch Knob auf die 18-mm-Welle, bis er bündig mit der Dezimal-Ein-Ausgabe-Platte abschließt und ziehen Sie die Stellschrauben so fest, dass der Knopf auf 0 zeigt.
Sie sollten jetzt in der Lage sein, das neue und verbesserte motorisierte Drehschalterfeld mit sechzehn Positionen in den Rahmen des Minivac 601 einzubauen. Wenn Sie 12 V an die RUN-Anschlüsse des Panels anlegen, sollte sich der Drehschalter in eine Richtung drehen. Vertauschen Sie die Polarität der Stromkabel und der Drehschalter sollte sich in die entgegengesetzte Richtung drehen.
Während Sie den Motor mit Strom versorgen, sollte der Motor stoppen, wenn Sie die STOP-Leitungen mit Strom versorgen. Siehe Experimente 12, 13 und 14 im Handbuch mit dem Titel "Buch 1 - Kennenlernen des Minivac 601" für weitere Details.
HINWEIS: Diese Methode zum Anhalten unterscheidet sich geringfügig von der "Kurzschluss"-Methode, die im ursprünglichen Minivac 601 verwendet wurde. Der STOPP hier muss ein richtiger Stromkreis sein und nicht nur ein "Draht", der von den Nieten 18 bis 19 verläuft.
Schritt 15: Abschließende Gedanken
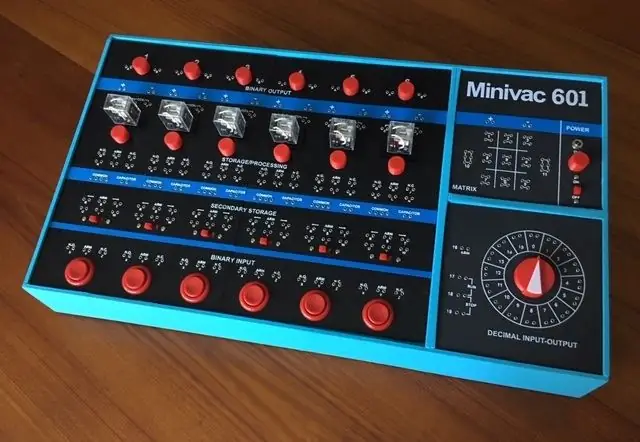
Ich bin verschiedene Wege gegangen, als ich versuchte zu entscheiden, wie man den Rotary Switch am besten "motorisiert".
Mein erstes (fehlgeschlagenes) Design beinhaltete einen Gleichstrommotor, der über Riemenscheiben mit dem Rotary Switch verbunden war. Tatsächlich wurde das Schwungrad von diesem Instructable von diesem Design neu bestimmt.
In einem Plan überlegte ich, einen Arduino und einen Motorcontroller mit einem Gleichstrom- oder Schrittmotor zu verwenden. Die Ironie, einen Mikroprozessor zu verwenden, der um viele Größenordnungen leistungsfähiger ist als das Gerät, das ich zu replizieren versuchte, war mir nicht entgangen.
Ein weiteres Verfahren umfasste einen Gleichstrommotor mit hohem Drehmoment und langsamer Geschwindigkeit mit einem Getriebe und einem Kupplungsmechanismus auf Solenoidbasis.
Letztendlich bin ich wirklich froh, dass ich eine Lösung gefunden habe, die nicht nur einfacher als alle oben genannten ist, sondern auch mehr dem Design des ursprünglichen Minivac 601 entspricht.
Empfohlen:
7-Segment-Uhr Version 2: 4 Schritte
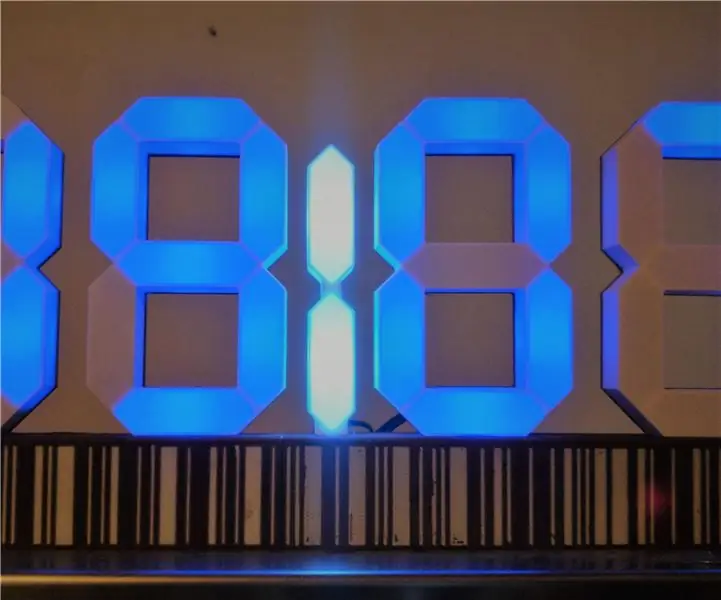
7 Segment Clock Version 2: Hallo! Nach einer Anfrage des Instructables-Benutzers bezüglich der Verfügbarkeit des 12-Stunden-Formats nutzte ich den Vorteil, wesentliche Änderungen am ursprünglichen Projekt vorzunehmen. Während der Verwendung der Version 1 hatte ich das Bedürfnis, eine eigenständige Version zu erstellen. also habe ich es möglich gemacht
Selbst gemachter Kampfroboter Version 2: 6 Schritte
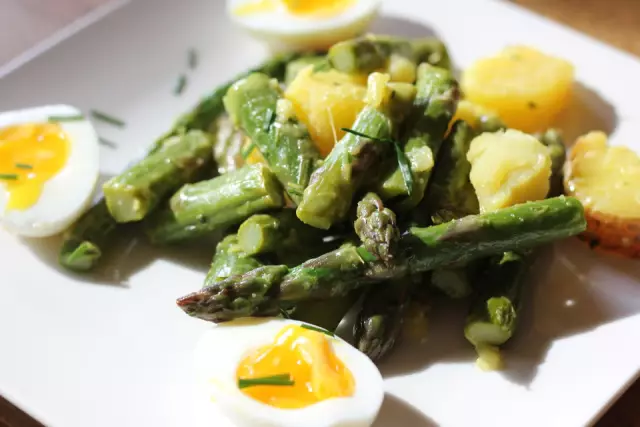
Homemade Combat Robot Version 2: Also… Dies ist meine zweite Version meines Ameisengewichts-Kampfroboters! Ich möchte Ihnen "Sidewinder" vorstellen. Für dieses Projekt habe ich 3D-gedruckte Teile (von mir entworfen) und einige elektronische Kleinteile verwendet, die ich für unter 100 US-Dollar gekauft habe. Ich habe ein CAD verwendet, also
Handwasch-Timer; Sauberere Version: 6 Schritte
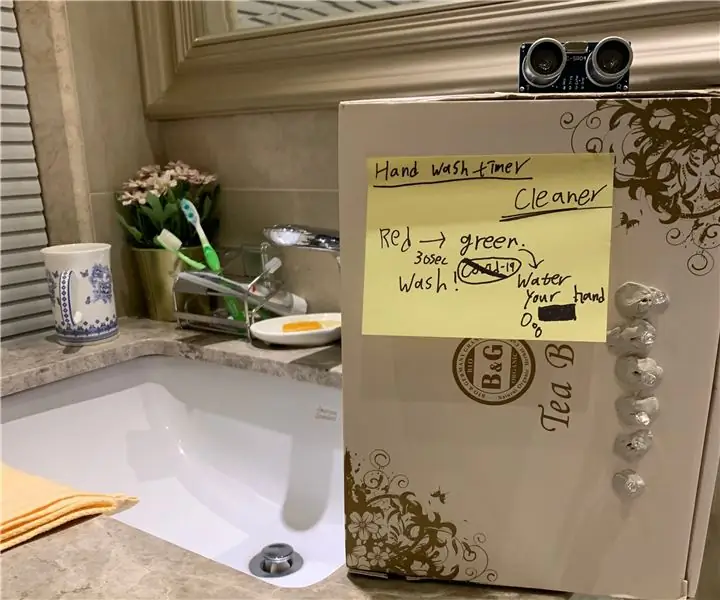
Handwasch-Timer; Cleaner Version: Nicht nur das Corona-Virus muss verhindert werden, sondern alle Krankheiten. Nach Angaben der Zentren für Krankheit und Prävention gibt es 2,8 Millionen Infektionen und 35000 Todesfälle durch Bakterien und Pilze. Dies zeigt, dass die Menschen ihre Hände waschen sollten
D4E1 Kamerahilfe für Linkshänder. Erweiterte Version.: 7 Schritte
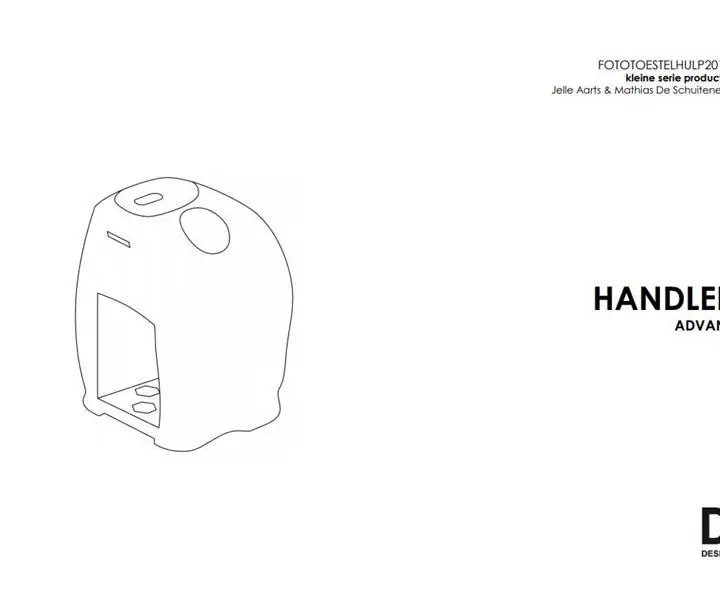
D4E1 Kamerahilfe für Linkshänder. Fortgeschrittene Version.: Annelies Rollez, Cesar Vandevelde und Justin Couturon entwarfen 2012 einen linken Kameragriff für Barts (Grimonprez) Digitalkamera. Wir haben das Design überprüft und parametrisiert, damit es in einem flexiblen Produktionsprozess hergestellt werden kann. Auf diese Weise die linke Ca
"Deaktivieren" oder Entfernen des Mikrofons im FireTV-Controller Version 2: 3 Schritte
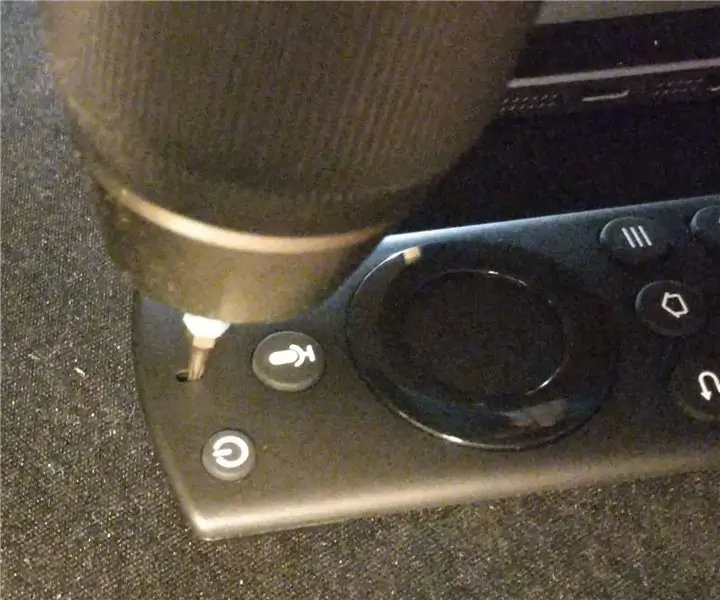
"Deaktivieren" oder Entfernen des Mikrofons im FireTV-Controller Version 2: Da es keine eindeutige Lösung gibt, das Mikrofon im FireTV-Controller durch Softwareeinstellungen zu deaktivieren, besteht die einzige andere Möglichkeit darin, das Mikrofon physisch zu entfernen. Für die erste Version des FireTV Controller kann eine andere Lösung helfen, tha