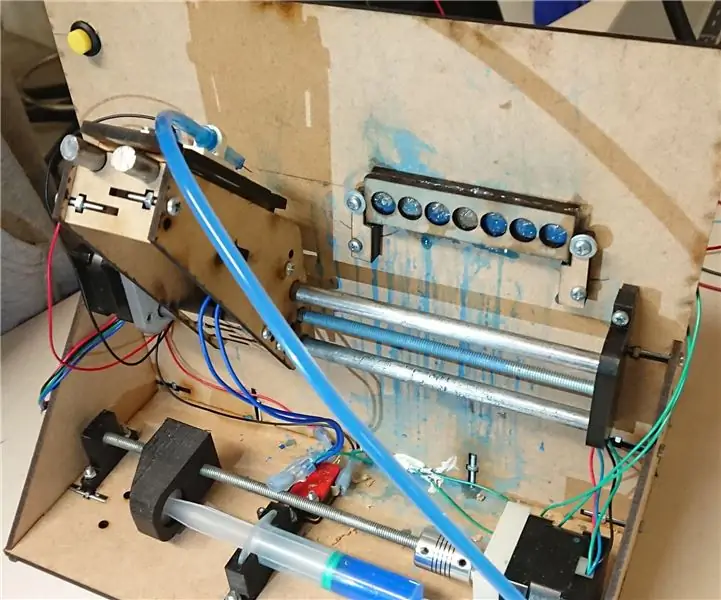
Inhaltsverzeichnis:
2025 Autor: John Day | [email protected]. Zuletzt bearbeitet: 2025-01-23 12:52
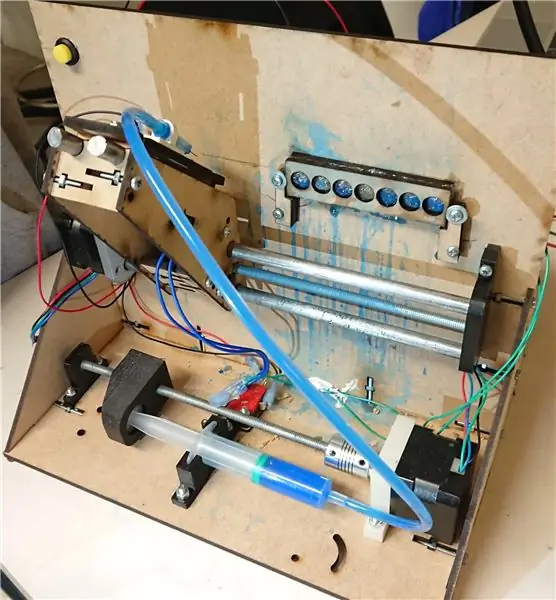
Im Rahmen unseres Masterstudiengangs "Mechatronik 1 - MECA-Y403" an der ULB wurden wir gebeten, einen Roboter mit einer bestimmten Funktion zu entwerfen und eine Website zu erstellen, die das Design des Roboters zusammenfasst, beginnend mit der Materialauswahl, der Modellierung, die Realisierung und der Code, der das ganze System zum Laufen bringt. Die gesamte Gruppe entschied sich einstimmig für die Realisierung des Roboters „Bubble Wrap Painter“.
Der "Bubble Wrap Painter" ist ein Gerät, das Farbe in einige Blasen der Luftpolsterfolie von einer vom Computer gelieferten Spannungssteuerung spritzen kann. Zunächst musste der Roboter in der Lage sein, die Flüssigkeit in einer 2D-Ebene einzuspritzen, um eine Punktzeichnung zu erzeugen. Aus wirtschaftlichen und praktischen Gründen hat sich die Gruppe jedoch zurückgezogen, um Farbe auf einer 1D-Trajektorie zu spritzen. Der Roboter funktioniert wie folgt: Über ein Schneckensystem wird der Kolben einer zunächst mit Farbe gefüllten Spritze gedrückt. Die Spritze ist mit einem flexiblen Polypropylenschlauch verbunden, über den die Farbe zu einer am mobilen Modul befestigten Metallspitze geleitet werden kann. Dieses Modul ist in der Lage, entlang einer horizontalen Achse zu gleiten, wiederum mittels eines Schneckensystems. Die Spitze hingegen ist an einem linearen Elektromagneten befestigt, der ebenfalls am mobilen Modul befestigt ist. Der Elektromagnet wird verwendet, um die auf einer vertikalen Platte befestigte Luftpolsterfolie anzustechen. Sobald die Blase durchstochen ist, wird die Farbe hineingespritzt und so weiter.
Schritt 1: Teile- und Werkzeugbeschreibung
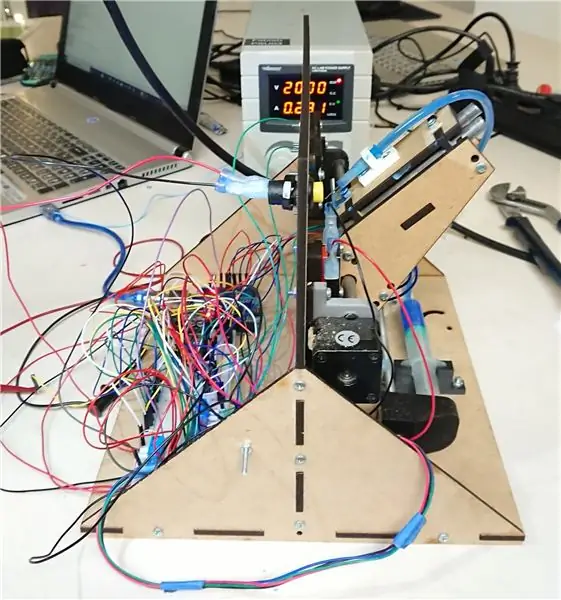
KAUFEN
2 Strahlkupplungen 5mm bis 6mm
1 Spritze mit 10 ml (7,5 cm lang)
1 Rohr aus flexiblem Polypropylen mit einem Durchmesser von 4 mm
1 Nadel mit seiner Sicherheitskappe
Gouache mit Wasser verdünnt
2 Gewindestangen: Durchmesser 6mm und 18,5cm lang
2 glatte Stäbe mit 8 mm Durchmesser und 21 cm Länge
2 glatte Stäbe mit 8 mm Durchmesser und 10 cm Länge
Luftpolsterfolie
ELEKTRONIK
1 Steckbrett
1 Arduino
1 Schrittmotor
1 Schrittmotor RS PRO Hybrid, Permanentmagnet-Schrittmotor 1,8°, 0,22 Nm, 2,8 V, 1,33 A, 4 Drähte
2 Mikroschalter V-156-1C25
1 Elektromagnet ZYE1-0530
Energieversorgung
2 Bananenstecker
45 Überbrückungsdrähte
6 leitfähige Kabel
Diode 1N4007
Transistor IRF5402
3 Widerstände 4, 7 kOhm
2 DRV8825-Treiber
1 Druckknopfschalter
SCHRAUBEN, MUTTERN UND BEFESTIGUNGEN
42 Schrauben M3 16 mm lang
4 Schraube M3 10 mm lang
4 Schrauben M4 16 mm lang
2 Schrauben M2, 5 16 mm lang
52 entsprechende Nüsse
2 Unterlegscheiben aus Stahl M3
GEBRAUCHTE WERKZEUGE
Laser-Schneide-Maschine
3D-Drucker (Ultimaker 2 oder Prusa)
Schraubenzieher
Schritt 2: CAD-Dateien
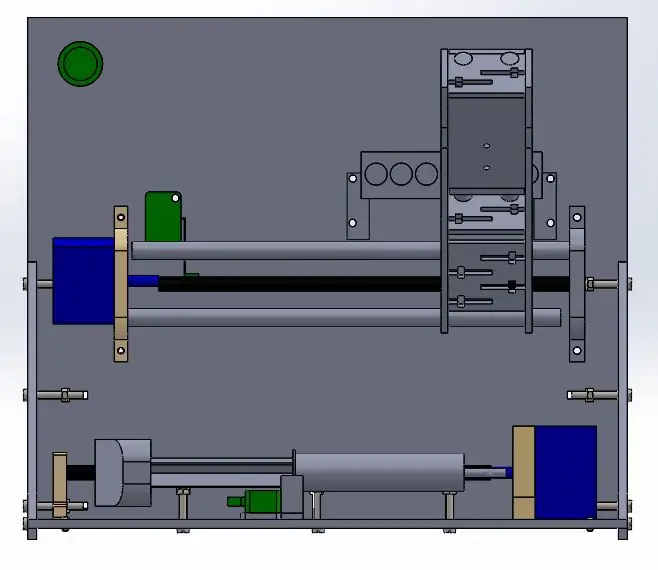
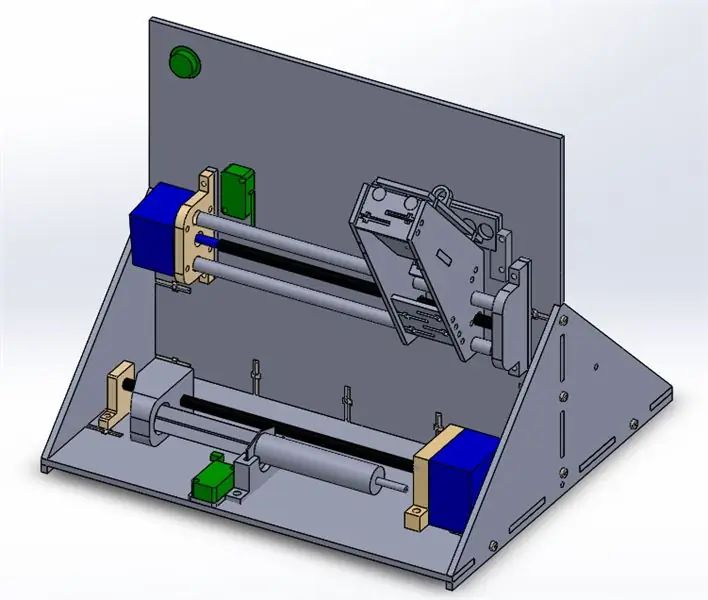
LASERSCHNEIDEN mit einer Dicke von 3 mm
-Stützplatten
-Unterstützung zum Anheben des Schalters
-bewegliche Unterstützung für die Nadel
-Blasenhalter
-4 Verstärkungsunterstützung
3D DRUCKEN
-Unterstützung für den Motor
-unterstützen Sie die Gewindestange
-Spritzenpumpe
-Unterstützung für die Nadel
-Unterstützung für die Spritze
Schritt 3: Montage
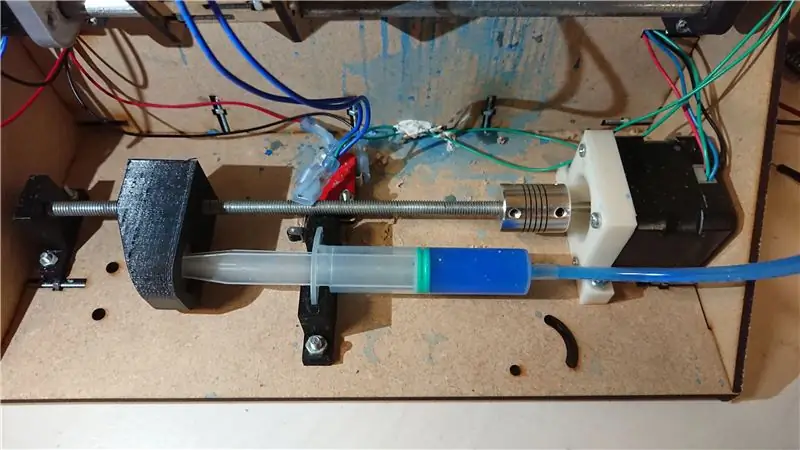
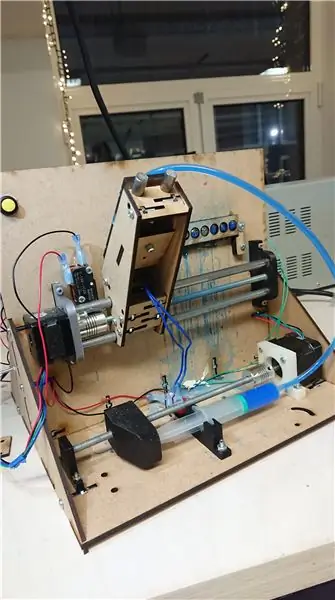
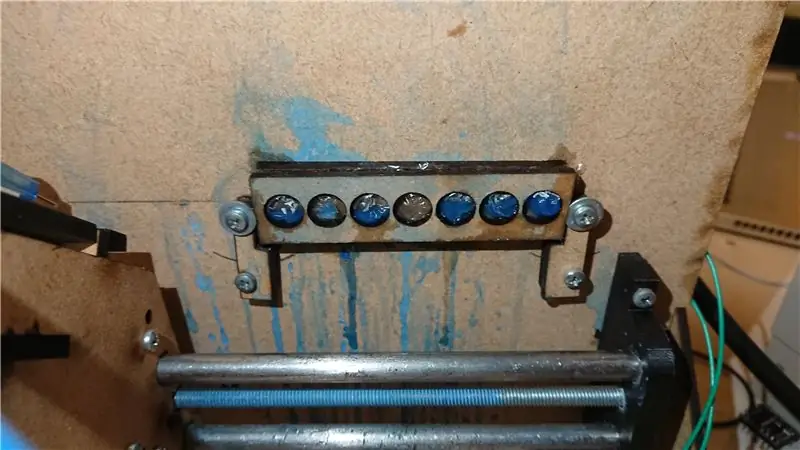
Zunächst haben wir einen Holzsockel entworfen, der aus 3 verschiedenen Elementen besteht: einer Bodenplatte, einer vertikalen Platte und einer dreieckigen Platte, die alles zusammenhält.
Sie können auf dem Bild sehen, dass die verschiedenen Platten sich wiederholende T-förmige Muster haben. Diese Muster werden verwendet, um die Baugruppe zu fixieren und ermöglichen, dass die Basis robust ist. Die beiden Schalter sind am Kolben und am Mobilmodul angebracht. Dies ermöglicht es, jeweils einen Hinweis auf die maximale Ausdehnung des Kolbens und einen Hinweis auf die äußerste rechte Position des mobilen Moduls zu geben.
Außerdem werden die Schrittmotoren mit vier Schrauben an einem mit einem 3D-Drucker erstellten Träger befestigt. An dieser Halterung ermöglichen zwei senkrechte Löcher die Befestigung an der vertikalen Platte. Die mit den beiden Drehachsen der Motoren verbundenen Gewindestangen sowie die vier glatten Stangen werden von zusätzlichen Stützen gehalten, die sich am Antipoden der Motoren befinden. Darüber hinaus werden Verbinder verwendet, um die Gewindestange an der Drehachse der Schrittmotoren zu fixieren.
Die Spritze wird zusätzlich mit einer Halterung fixiert, die auf die horizontale Platte geschraubt wird. Sein Stößel lässt sich durch ein Trapezstück drücken, das beim Drehen entlang der Gewindestange läuft. Dieses Teil hat in seinem Inneren ein Loch, das mit einer Mutter versehen ist. Diese Mutter ermöglicht die Bewegung des trapezförmigen Teils.
Der Schlauch wird durch einfaches Einstecken in das Ende der Spritze mit der Spritze verbunden. Das andere Ende des Rohres wird in den Ring eines kleinen weißen PLA-Stücks gesteckt. Die ursprünglich zur Spritze gehörende Metallspitze wurde ebenfalls auf das Ende des Röhrchens aufgeschnappt. Wir haben die Spritzenkappe an der Nadel angebracht, um den Durchmesser des weißen Stücks besser auszufüllen. Die Kappe hat am Ende ein Loch, damit die Nadelspitze hindurchpassen kann. Dieses kleine weiße Teil wird mit zwei Schrauben an der Gleitplatte des Mobilmoduls angeschraubt.
Das mobile Modul besteht aus einer Reihe von Holzteilen, die genauso befestigt sind wie die Platten, aus denen die Basis besteht. Das Modul bildet einen Kasten mit drei Löchern zur Aufnahme der beiden glatten Stangen und der Gewindestange. In dieser Box befinden sich zwei Muttern, mit denen das Modul bewegt werden kann. Die obere Platte des Moduls gleitet entlang zweier glatter Stangen. Dort im Inneren des Moduls hält eine feste Platte den Linear-Elektromagneten. Dadurch kann die Gleitplatte lineare Bewegungen hin und her ausführen.
Es gibt zwei Holzhalterungen, die es ermöglichen, zwei gelochte Zungen mit Unterlegscheiben, die durch die Schrauben blockiert werden, direkt an der vertikalen Platte zu befestigen. Diese beiden Laschen verkeilen einen Streifen Luftpolsterfolie in ihrer Mitte. Das Blasenpapier enthält hier sieben Blasen, die den 7 vom Computer codierten Bits entsprechen.
Auf der anderen Seite der vertikalen Platte befinden sich die Platine und das Arduino. Die Platine wird mit einem zunächst vorhandenen Klebesystem auf die horizontale Platte geklebt und das Arduino mit der Bodenplatte verschraubt. Darüber hinaus ist mit der Platine ein Widerstandsteiler verbunden, der mit dem Holzdreieck verschraubt ist. (BILD: Rückseite des Systems)
*Jede der zum System gehörenden Schrauben ist mit geeigneten Schrauben befestigt.
Schritt 4: Elektronik und Sensoren
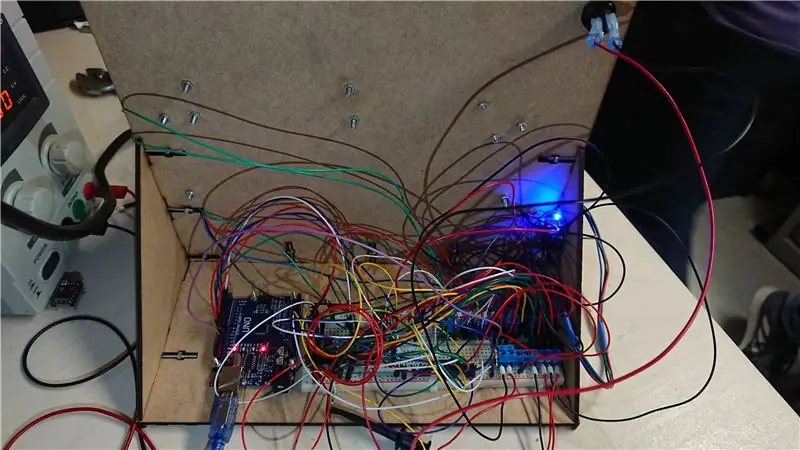
Wir müssen die Position des oberen Schrittmotors kennen, wenn der Luftpolsterfolienmaler gestartet wird, um die genaue Position der Blasen zu erreichen. Dies ist das Ziel des ersten Schalters. Jedes Mal, wenn das Gerät eine Linie zeichnet, dreht sich der Motor, bis der Schalter seinen Zustand ändert.
Wir brauchen einen weiteren Schalter, um zu wissen, wann der Stepper, der auf die Spritze drückt, das Ende des Kolbens erreicht hat. Der zweite Schalter wird verwendet, um das System zu stoppen, wenn die Spritze leer ist. Ein dritter optionaler Schalter kann das Lackieren fortsetzen, wenn die Spritze eingefüllt wurde. Diese Schalter verwenden niedrige Spannungen und können direkt vom Arduino versorgt werden. Die beiden Schrittmotoren und der Magnet benötigen mehr Leistung und werden von einem Stromgenerator mit 12V und 1A versorgt. Zwei DRV8825 Schrittmotortreiber wandeln die Signale vom Arduino in einen Strom für die Motoren um. Diese Treiber müssen kalibriert werden. Die Kalibrierung erfolgt, indem ein Stepper mit konstanter Geschwindigkeit rotiert und die Schraubendreherschraube eingestellt wird, bis das Drehmoment ausreicht, um die Nadel und die Stütze reibungslos zu bewegen. Das letzte Element ist der Elektromagnet. Ein Pull-Down-Widerstand wird verwendet, um den Mosfet zurückzusetzen, wenn kein Strom vom Arduino gesendet wird. Um die anderen Elektronikteile zu schützen, wird dem Elektromagneten auch eine Flyback-Diode hinzugefügt. Der Mosfet schaltet den Magneten zwischen High- und Low-Zuständen um.
Schritt 5: Python-Code
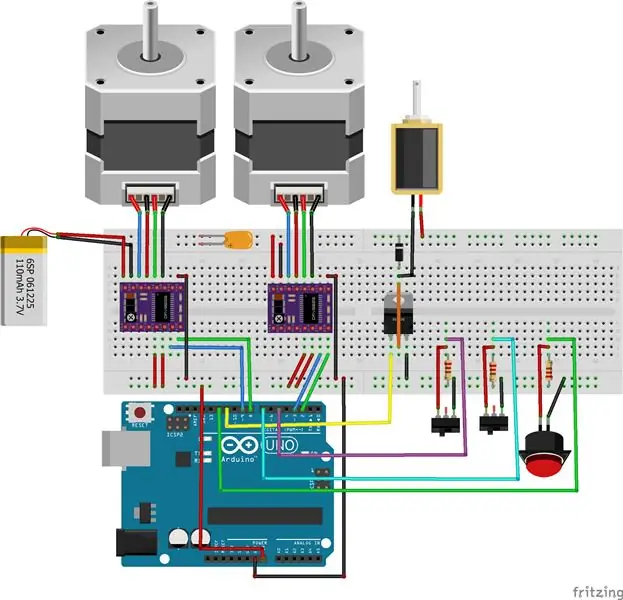
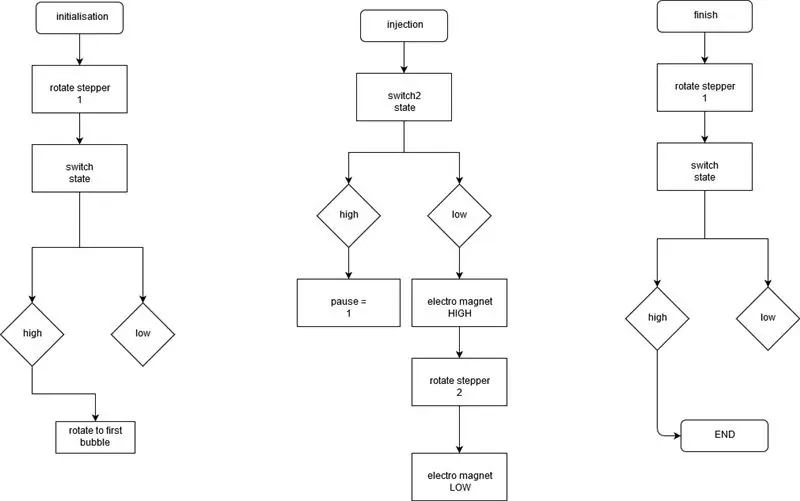
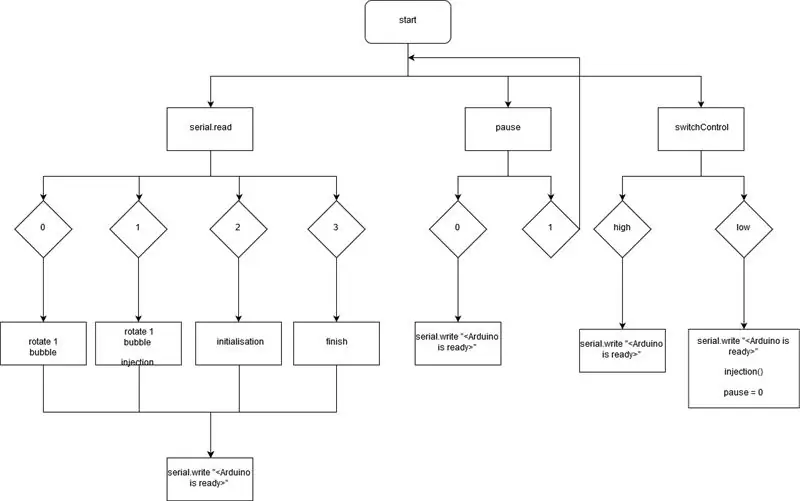
Für die Kommunikation zwischen Computer und Arduino mit Python haben wir uns auf die in diesem Forum bereitgestellten Codes gestützt:
Um den Schrittmotor zu steuern, war diese Seite sehr hilfreich: https://www.makerguides.com/drv8825-stepper-motor-driver-arduino-tutorial/ sehr hilfreich. Es gibt zwei Teile des Codes: Der erste ist ein Python-Code, der einen Buchstaben in den ASCII-Binärcode umwandelt und ihn nach und nach an das Arduino sendet, und der zweite ist ein Arduino-Code, der in die entsprechenden Blasen pikiert. Das folgende Flussdiagramm erklärt das Prinzip des Arduino-Codes:
Schritt 6: Video

Das Arbeitsprojekt!
Schritt 7: Verbesserungen
Das Projekt kann auf verschiedene Weise verbessert werden. Erstens kann die Anzahl der Blasen auf einer Linie leicht erhöht werden. Dies kann durch die Verwendung längerer Binärcodes erfolgen, indem beispielsweise zwei statt einem Buchstaben bei der Eingabe geschrieben werden. Der ASCII-Code wird dann zweimal länger.
Die wichtigste Verbesserung wäre, die Blasen nicht nur entlang der x-Achse, sondern auch entlang der y-Achse ausfüllen zu können. Die Blasenfüllung würde daher in 2D statt in 1D erfolgen. Am einfachsten geht das, indem man die Höhe des Luftpolsterpapiers variiert, anstatt den Motor zu heben und abzusenken. Dies würde bedeuten, dass die Kante des Blasenpapierhalters nicht an der Platte hängt, sondern an einer 3D-gedruckten Unterlage. Dieser Träger wäre mit einer Gewindestange verbunden, die selbst mit einem Schrittmotor verbunden ist.
Schritt 8: Aufgetretene Probleme
Das Hauptproblem, mit dem wir uns auseinandersetzen mussten, ist der Elektromagnet. Um einen unhandlichen und schweren dritten Motor zu vermeiden, schien der Elektromagnet der perfekte Kompromiss zu sein. Nach einigen Tests erwies sich die Steifigkeit immer wieder als zu gering. Also musste eine zweite Feder hinzugefügt werden. Außerdem kann er nur sehr leichte Lasten bewegen. Die Anordnung der verschiedenen Elemente musste überarbeitet werden.
Die Spritzenpumpe war auch ein Problem. Zunächst musste ein Teil modelliert werden, das an der Endlosstange eingehakt und gleichzeitig auf den Stößel gedrückt werden konnte. Zweitens war die Spannungsverteilung wichtig, um einen Bruch des Teils zu vermeiden. Außerdem sind die beiden Schrittmotoren nicht gleich: Sie haben nicht die gleichen Eigenschaften, was uns gezwungen hat, einen Spannungsteiler hinzuzufügen. Wir mussten Wasserfarbe (in unserem Fall verdünnte Gouache) verwenden, da eine zu dicke Farbe nicht in die Nadel eindringen würde und zu viel Druckverlust im Rohr verursachen würde.