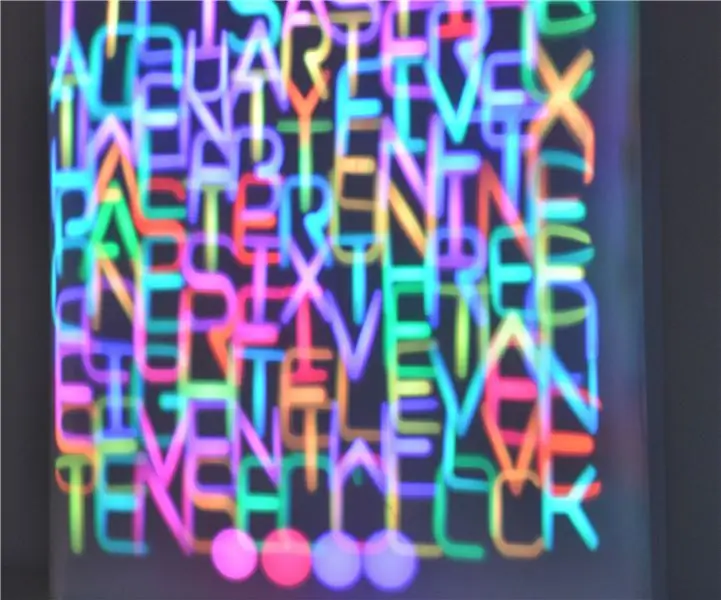
Inhaltsverzeichnis:
- Schritt 1: Design
- Schritt 2: Materialien sammeln
- Schritt 3: 3D-gedruckte Komponenten
- Schritt 4: Konstruieren des Rahmens
- Schritt 5: Zusammenbau der Briefkästen
- Schritt 6: Zusammenbau der Aktoren
- Schritt 7: Herstellung der Backplate
- Schritt 8: Komponenten an Backplate und Verkabelung anbringen
- Schritt 9: Anbringen der Rückplatte am Rahmen
- Schritt 10: Kalibrieren der Servos
- Schritt 11: Hochladen des Codes
- Schritt 12: Anbringen des Bildschirms
- Schritt 13: Anbringen der oberen und unteren Abdeckung
- Schritt 14: Fertige Uhr und Zusammenfassung
2025 Autor: John Day | [email protected]. Zuletzt bearbeitet: 2025-01-23 12:52
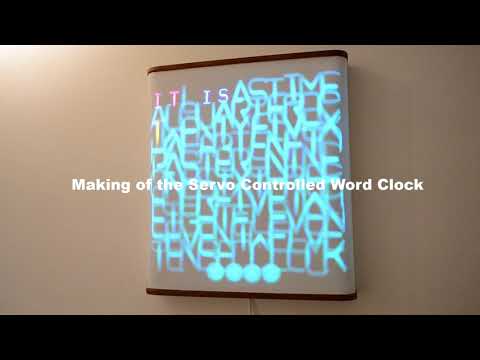
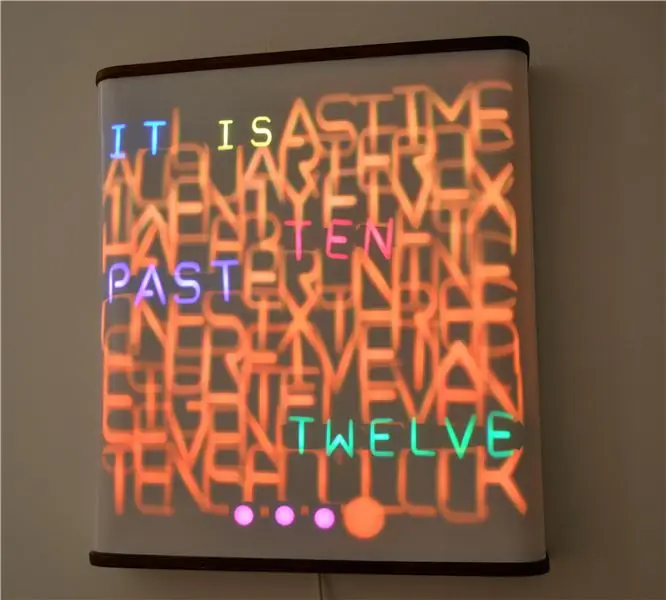
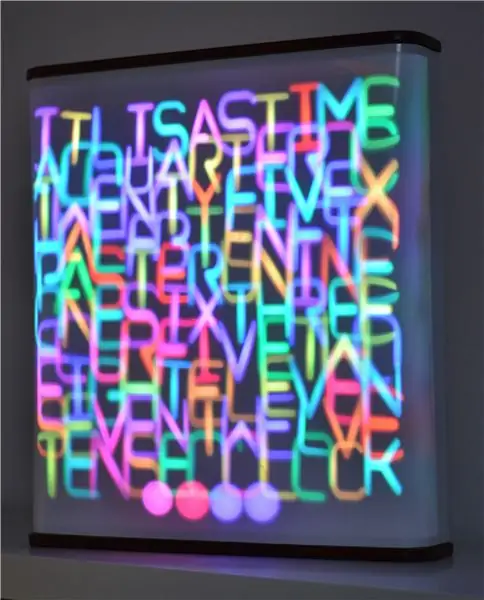
Fusion 360-Projekte »
Was hat 114 LEDs und läuft immer? Wie Sie vielleicht wissen, ist die Antwort eine Wordclock. Was hat 114 LEDs + 114 Servos und ist ständig in Bewegung? Die Antwort ist diese servogesteuerte Wordclock.
Für dieses Projekt habe ich mich mit einem Freund von mir zusammengetan, was sich aufgrund des großen Aufwands dieses Builds als ein Muss herausstellte. Außerdem ergänzten sich meine elektronischen und seine mechanischen Fähigkeiten recht gut. Die Idee zu dieser Adaption der beliebten Wordclock kam uns, als wir eine normale als Weihnachtsgeschenk bastelten. Dort ist uns aufgefallen, dass es auch möglich ist, die Buchstaben von der Rückseite auf ein weißes Blatt Papier zu projizieren. Zu dieser Zeit war dies nur eine Umgehungslösung, um unsere beschissene Handwerkskunst zu verbergen, da wir beim Anbringen eines Vinylaufklebers mit den Buchstaben auf der Rückseite einer Glasplatte eine Menge Blasen hatten. Wir haben dann festgestellt, dass man beim Biegen des Papierbogens interessante Effekte erzielen kann, da die Buchstaben ihre Größe ändern und unscharf werden. Dies hat uns auf die Idee gebracht, eine Wordclock zu entwickeln, bei der die Buchstaben von hinten auf eine Leinwand projiziert werden und sich hin und her bewegen lassen, um die Größe des projizierten Bildes zu ändern. Anfangs waren wir mit dem Bau dieses Projekts etwas zurückhaltend wegen des Kosten- und Arbeitsaufwands, den es kostet, wenn man jeden der 114 Buchstaben einzeln verschieben möchte. Also haben wir uns mit der Idee auseinandergesetzt, eine Version zu machen, bei der nur jedes Wort, das zur Anzeige der Zeit verwendet wird, hin und her verschoben werden kann. Nachdem wir jedoch gesehen hatten, dass der Epilog-Wettbewerb auf Instructables stand und nach epischen Projekten fragte, und nachdem wir relativ billige Servomotoren gefunden hatten, beschlossen wir, den ganzen Weg zu gehen und eine richtige Version zu machen, bei der jeder Buchstabe einzeln von einem Servo gesteuert wird.
ACHTUNG: Dies ist kein eintägiger Build!
Um Ihnen eine Vorstellung vom Aufwand dieses Projekts zu geben, betrachten Sie die folgenden Zahlen. Die fertige Uhr enthält
- 798 individuelle 3D-gedruckte Modelle (Gesamtdruckzeit ~ 200 Stunden)
- ~600 Schrauben + ~250 Muttern und Unterlegscheiben
- ~500 Drähte (Gesamtlänge ~ 50 m). Nicht mitgezählt die Drähte, die bereits an den Servos angeschlossen waren.
Schritt 1: Design
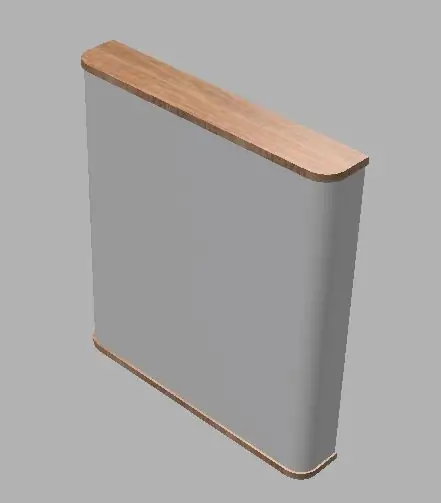
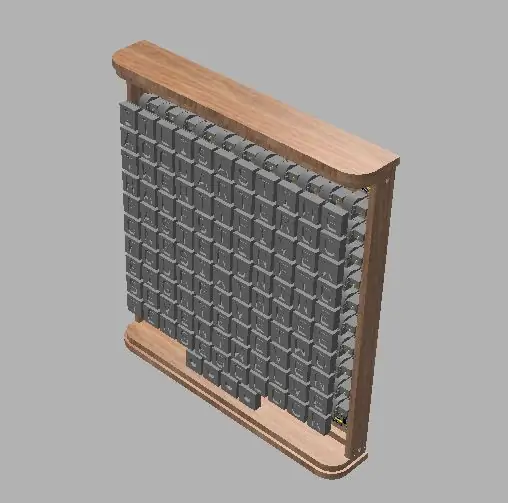
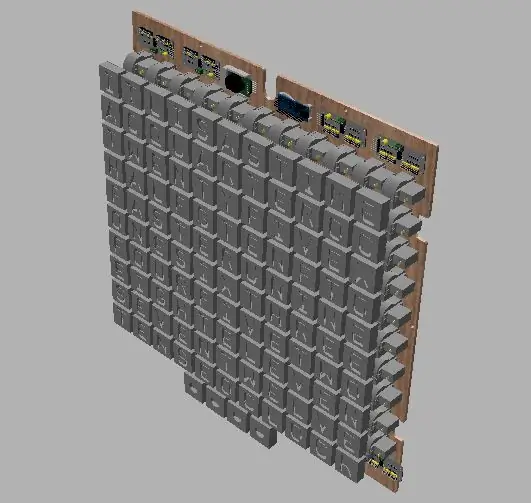
Die Uhr wurde mit Autodesk Fusion 360 und Inventor entwickelt. Wie Sie sehen, besteht die Uhr aus 114 Briefkästen, die von Linearantrieben bewegt werden, die wiederum von Servomotoren angetrieben werden. Jeder Briefkasten enthält eine LED, die den Brief auf die Rückseite eines Bildschirms aus weißer PVC-Folie projiziert. Alle Komponenten sind in einem Holzrahmen untergebracht.
Schritt 2: Materialien sammeln
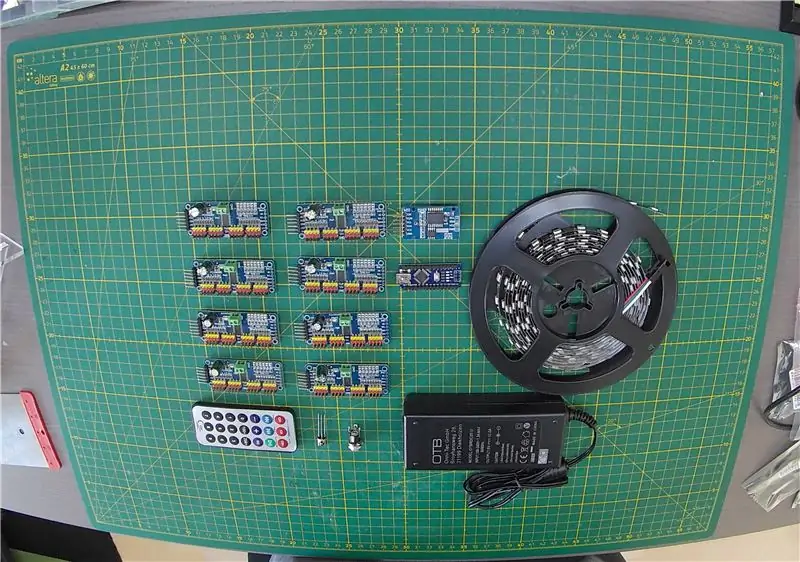
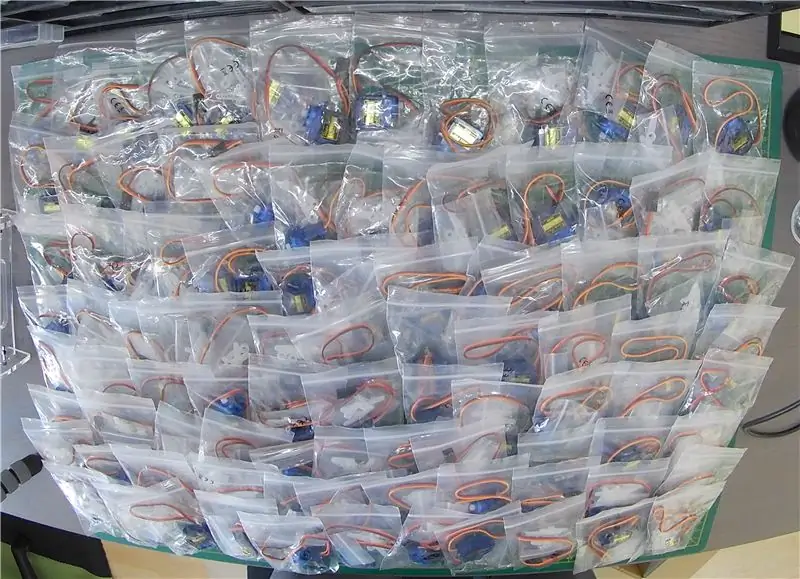
Elektronische Bauteile
114x SG90 Mikro-Servomotoren (ebay.de)
Obwohl die Servos mit dem Namen der beliebten Marke "Tower Pro" gekennzeichnet waren, handelt es sich sicherlich um billigere Imitationen. Da der Preis des Knockoffs jedoch etwa 1 EUR im Vergleich zu 3 EUR für das Original beträgt, macht dies das gesamte Projekt viel erschwinglicher. Anscheinend ziehen die Knockoffs auch weniger Strom (das bedeutet natürlich auch weniger Drehmoment), was es einfacher machte, eine geeignete Stromversorgung für das gesamte Projekt zu finden.
- 5 m WS2812B LED-Streifen, 60 LEDs/m (ebay.de)
- 8x 16 Ch PWM Servotreiber PCA9685 (ebay.de)
- DS3231 RTC-Modul (ebay.de)
- Arduino-Nano (ebay.de)
- VS1838B IR-Empfänger + Fernbedienung (ebay.de)
- 5 V, 10 A Netzteil (ebay.de)
- 20x 15 cm Servoverlängerungskabel (ebay.de)
- Kabel DC-Buchse auf blanken Draht (conrad.de)
- 300-500 Ohm Widerstand
- 1000 µF Kondensator (> 5 V)
Materialien für Rahmen
-
Holzlatten
- 2 Stück 40 x 10 x 497 mm
- 2 Stück 12 x 12 x 461 mm
- 2 Stück 12 x 12 x 20 mm
-
Multiplex
- 2 Stück 12 x 77 x 481 mm
- 2 Stück 12 x 84 x 489 mm
- weiße PVC-Folie (700 x 1000 x 0,3 mm) (modulor.de)
- 500 x 500 mm HDF-Platte, 3 mm dick
Schrauben, Kabel usw
- 228x M2 Schrauben, 8 mm lang + Unterlegscheiben + Sechskantmuttern
- 228x Blechschrauben M2.2, 6,5 mm lang
- verschiedene Holzschrauben
- 50 m, 0,22 mm2 (24 AWG) Kabel
Darüber hinaus erforderte dieses Projekt umfangreiche 3D-Druck- und Lötarbeiten. Die Rückenplatte wurde mittels Laserschneiden hergestellt. Der Rahmen wurde mit einer Kreissäge, Stichsäge und Bohrer gebaut. Wie bei jedem anständigen Projekt haben wir auch viel Heißkleber verwendet, auch etwas Epoxid- und Plastikkleber.
Die Gesamtkosten für dieses Projekt beliefen sich auf ca. 350 EUR.
Schritt 3: 3D-gedruckte Komponenten
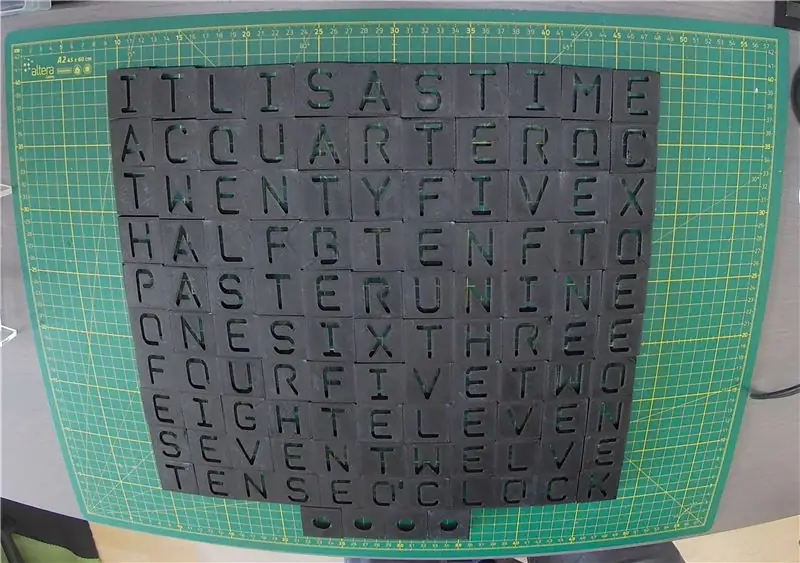
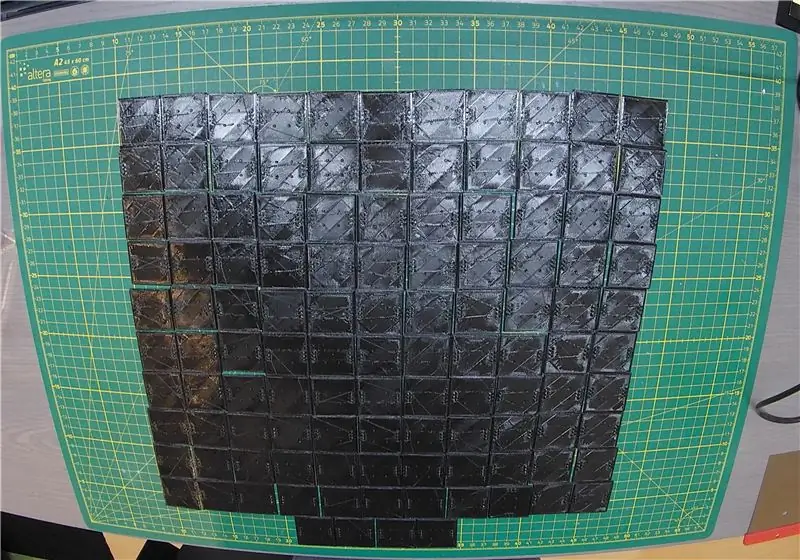
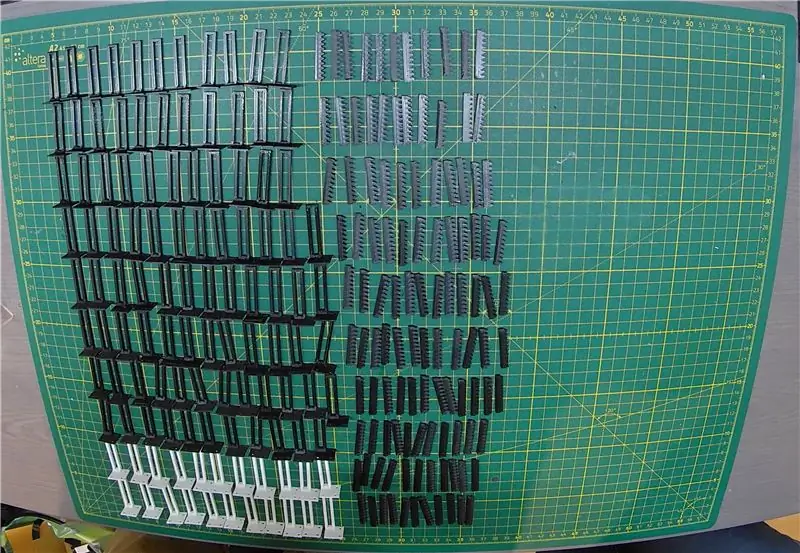
Briefkästen
Jeder Briefkasten besteht aus einer 3D-gedruckten Abdeckung, die als Schattenmaske fungiert, und einer Grundplatte, auf der eine LED angebracht wird. Die Grundplatte enthält vier Passstifte zum Ausrichten auf dem Aktor und sechs Löcher zum Durchführen der LED-Kabel. Insgesamt sind das 228 Modelle, die alle aus schwarzem PLA (Formfutura EasyFill PLA) mit 0,4 mm Schichthöhe gedruckt wurden. Die Gesamtdruckzeit auf meinem Anycubic Kossel Linear Plus betrug etwa 23 Stunden für die Briefumschläge und 10 Stunden für die Grundplatten. Alle stl-Dateien finden Sie in der angehängten Zip-Datei.
Aktuatoren
Das Antriebsdesign wurde vom Linear Servo Extender von Roger Rabbit übernommen, was sehr hilfreich war. Da die Teile fest zusammenpassen, sollten sie auf einem anständigen 3D-Drucker gedruckt werden. Eine kleine Schichthöhe ist nicht so wichtig (0,2 mm ist gut) als ein kleiner Düsendurchmesser (wir empfehlen 0,4 mm). Die Teile sollten in der gezeigten Ausrichtung gedruckt werden. Jeder Aktuator besteht aus 5 Einzelteilen, da wir 114 Aktuatoren benötigt haben, sind das insgesamt 570 Teile (!). Um diese zu drucken, haben wir die kombinierte Leistung mehrerer professioneller 3D-Drucker (Ultimaker S2+, Ultimaker S5, Lulzbot TAZ6, Sindoh 3D Wox DP200) genutzt. Trotzdem hatten wir viele fehlgeschlagene Drucke auf den Teilen und ich habe ein paar Bilder zu Ihrer Unterhaltung eingefügt. Die Gesamtdruckzeit betrug ca. 150 Stunden (!). Auch hier sind die stl-Dateien in der angehängten Zip-Datei zu finden.
Schritt 4: Konstruieren des Rahmens
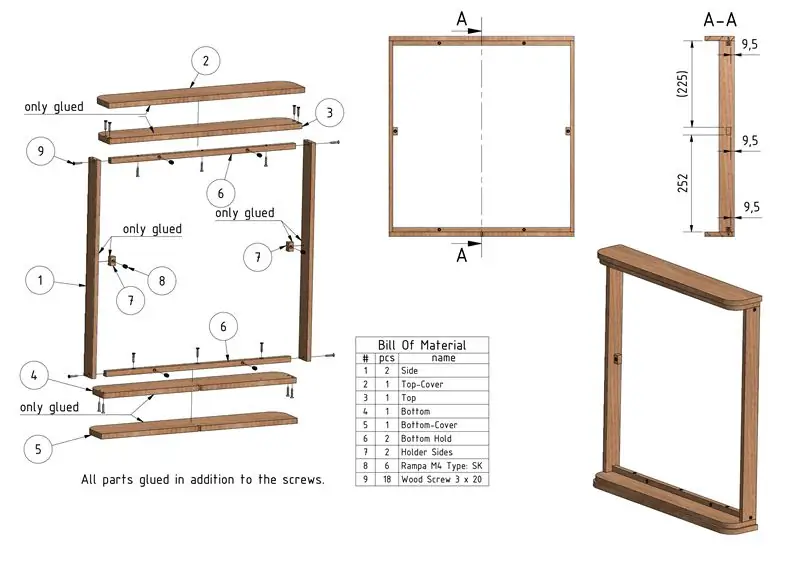
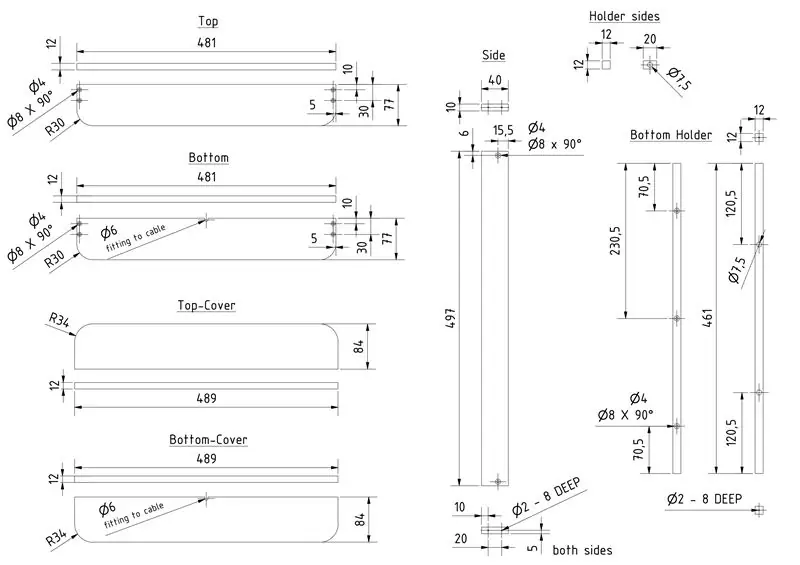

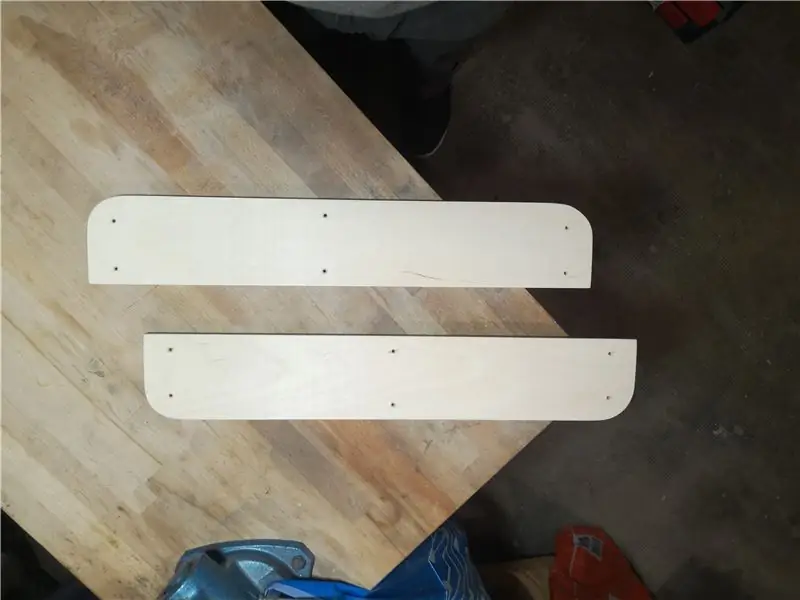
Der Rahmen wurde aus Holzlatten und Multiplexplatten gefertigt. Die Teile wurden mit einer Kreissäge und einer Stichsäge geschnitten und dann mit Holzleim und Holzschrauben aneinander befestigt. Die obere und untere Abdeckung wurden ebenfalls gebeizt, um ihr ein schöneres Aussehen zu verleihen. Eine detaillierte Beschreibung der Teile mit allen Abmessungen finden Sie in den beigefügten Zeichnungen.
Schritt 5: Zusammenbau der Briefkästen
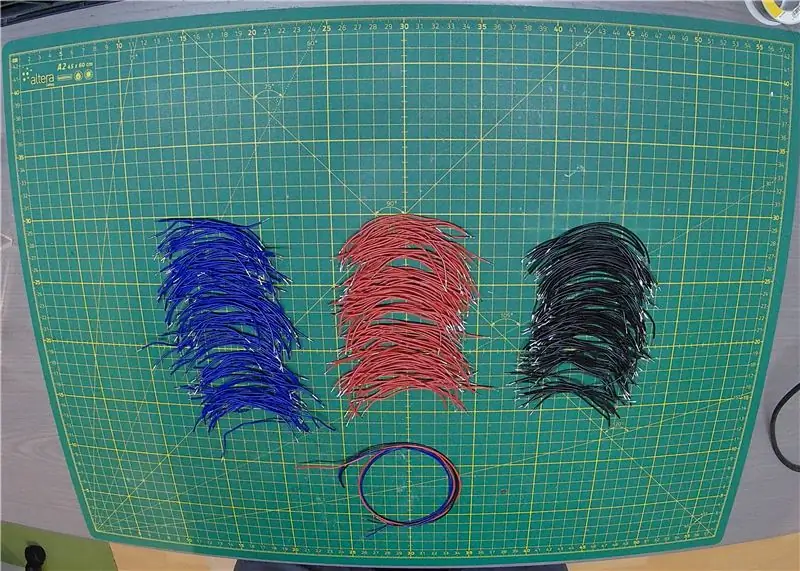
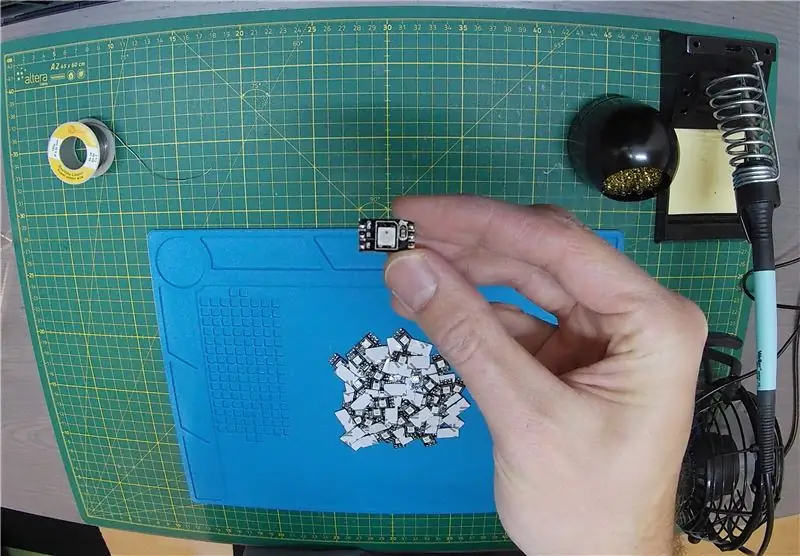
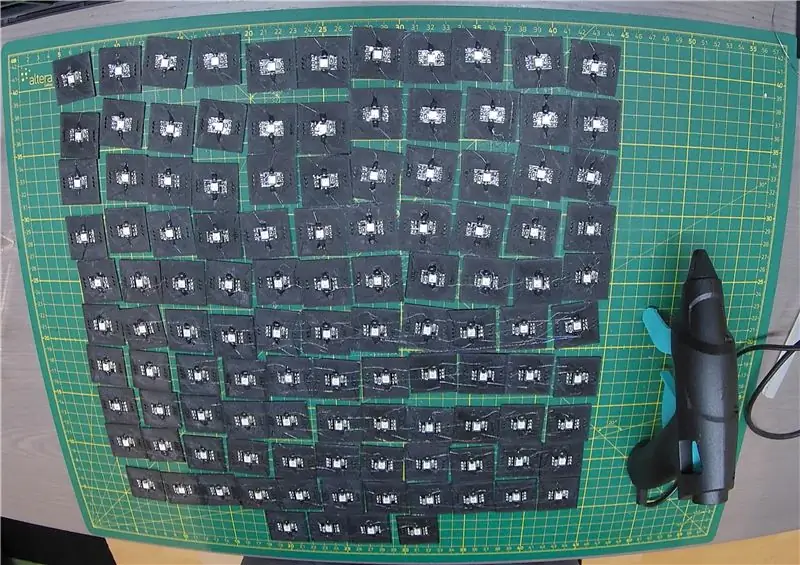
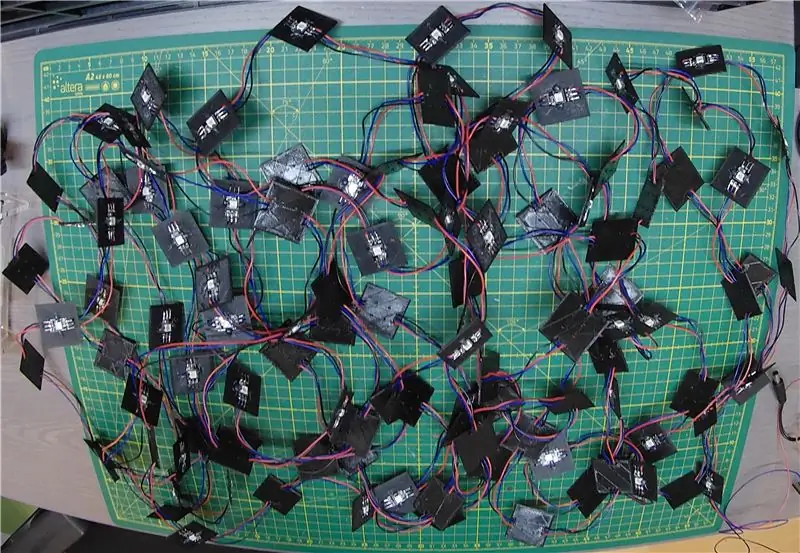
Der Zusammenbau der Briefkästen war viel Arbeit und hat sehr lange gedauert, vor allem das Löten. Dies liegt daran, dass jeder Schritt, den Sie machen, 114 Mal wiederholt werden muss.
- Schneiden Sie 114 einzelne Stücke aus dem LED-Streifen
- Alle LED-Pads verzinnen
- Befestigen Sie jede LED an der 3D-gedruckten Rückplatte eines Briefkastens. Die LED sollte zentriert sein. Wir haben es auch mit Heißkleber befestigt.
- Als nächstes haben wir 3x114 = 442 Drähte vorbereitet, d.h. abgelängt, die Enden abisoliert und verzinnt. Die Länge jedes Drahtes betrug jeweils 10 cm, mit Ausnahme der Drähte, die den letzten Buchstaben mit den Punkten verbinden, die länger sein müssen (~25 cm). Auch die mit dem ersten Buchstaben verbundenen Drähte, die mit dem Arduino und der Stromversorgung verbunden werden, sollten länger sein.
- Diasy-Chain-LEDs mit Drähten. Die Drähte werden durch die Löcher in der 3D-gedruckten Rückplatte jedes Briefkastens geführt.
- Die Frontabdeckung des Briefkastens wurde mit Kleber befestigt
- Teile des Lineargestells für den Aktuator müssen zusammengeklebt werden
- Linearregal wird mit Kleber an der Rückseite des Briefkastens befestigt
Schritt 6: Zusammenbau der Aktoren
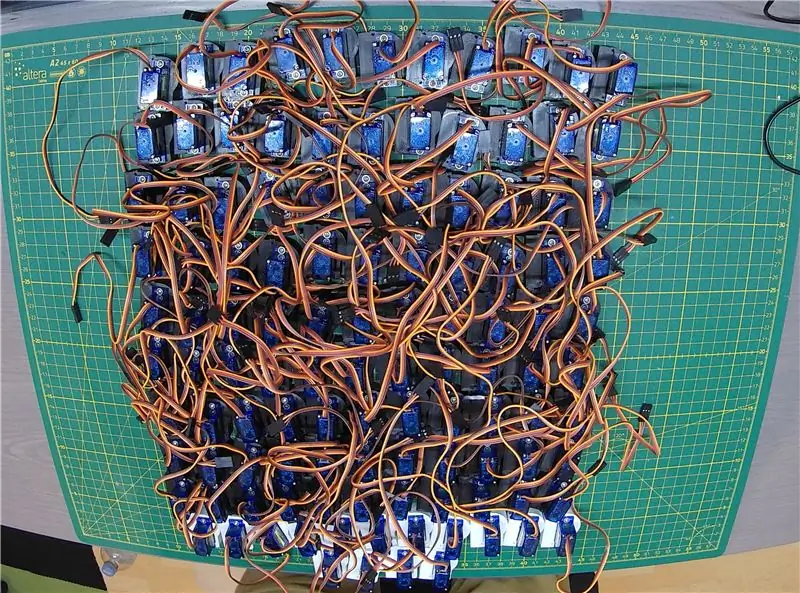
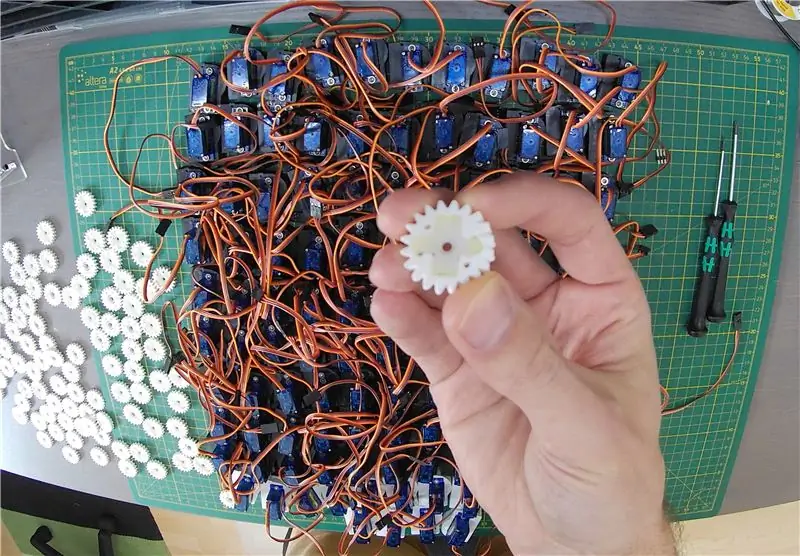
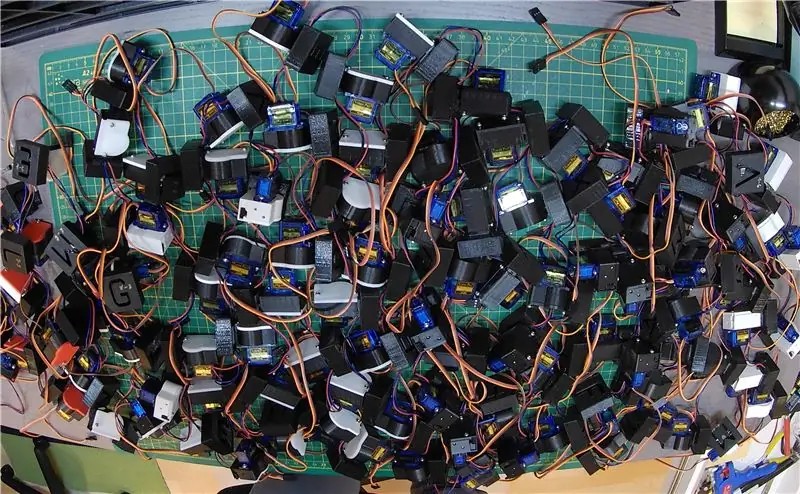
Auch hier war die Montage der Aktuatoren ein sehr mühsames Verfahren, das lange Zeit in Anspruch nahm.
- Befestigen Sie das Servo mit den mitgelieferten Schrauben am 3D-gedruckten Gehäuse
- Das runde Zahnrad wird mit dem mitgelieferten Kunststoffkreuz am Servo befestigt, aber zuerst muss das Kreuz in Form geschnitten und mit Epoxid am Zahnrad befestigt werden.
- Befestigen Sie das Getriebe mit der mitgelieferten Schraube am Servo
- Vor dem Einsetzen des Lineargestells wurde jedes Servo auf die gleiche Position genullt
- Linearregal mit Briefkasten einsetzen
- Einsetzen von zwei M2-Sechskantmuttern in das 3D-gedruckte Gehäuse, mit denen es später an der Backplate befestigt wird
- Gehäuse mit 3D-gedrucktem Deckel mit den M2.2 Blechschrauben verschließen
Am Ende hatten wir ein großes Durcheinander von diasy-verketteten Aktoren, wie im Bild oben gezeigt
Schritt 7: Herstellung der Backplate
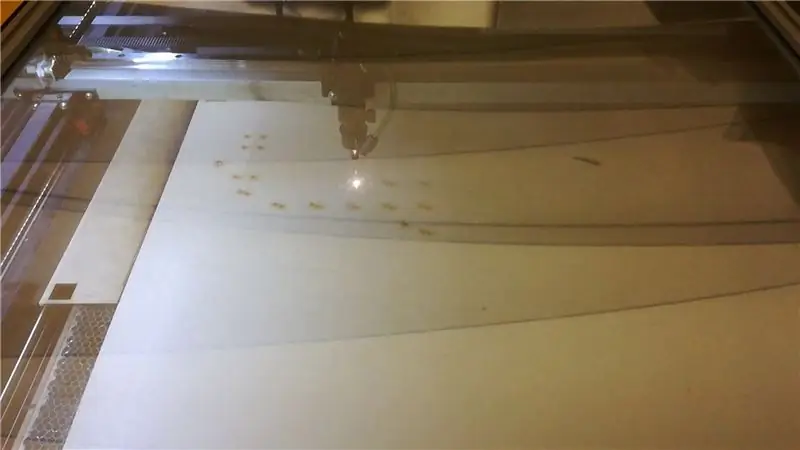
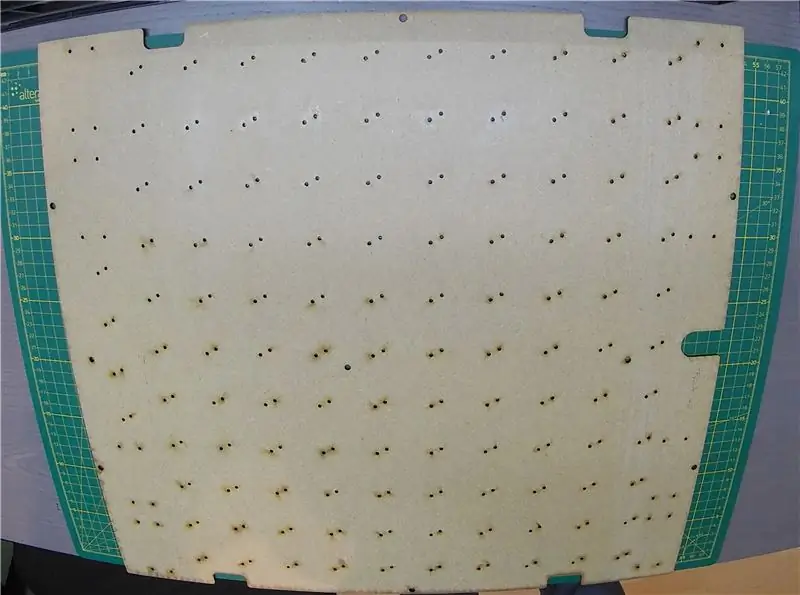
Die Rückplatte wurde mit einem CO2-Laserschneider aus unserem lokalen Herstellerbereich aus 3 mm dickem HDF-Holz lasergeschnitten. Zuerst versuchten wir es mit Sperrholz, aber es stellte sich als viel zu dünn heraus, um das Gewicht aller Komponenten zu tragen. Noch besser wäre in diesem Fall Aluminium gewesen, aber es ist natürlich teurer und lässt sich nicht mit einem CO2-Laser schneiden. Die dxf-Datei für die Backplate ist beigefügt.
Schritt 8: Komponenten an Backplate und Verkabelung anbringen
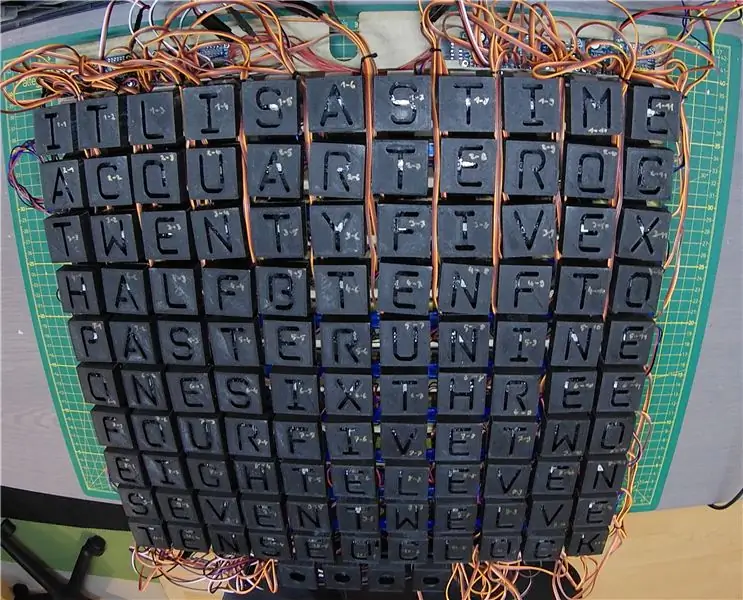
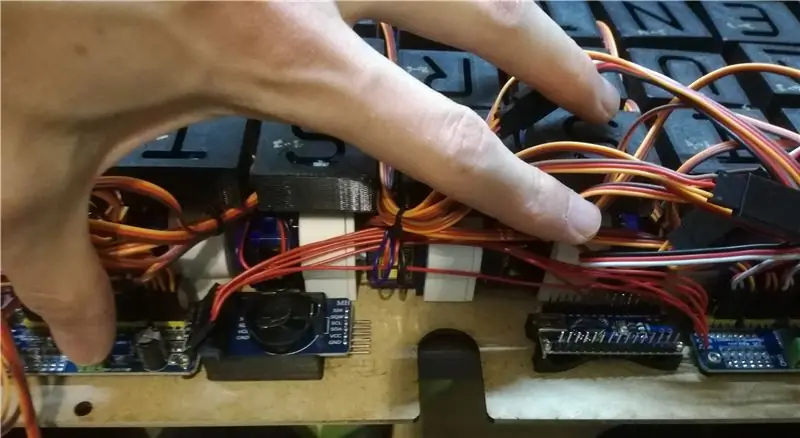
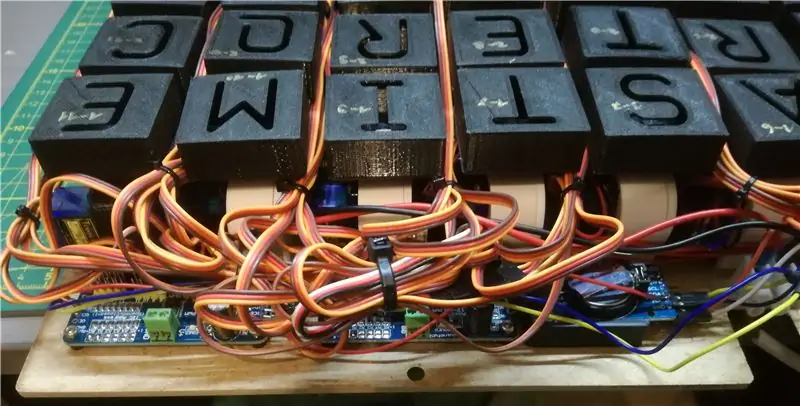
Zuerst sollten die PCA9685-Boards mit PCB-Abstandshaltern an der Backplate befestigt werden. Dann können das Arduino Nano- und RTC-Modul wie im Bild oben gezeigt platziert werden. Für die beiden letzteren haben wir 3D-gedruckte Halter verwendet, die mit Heißkleber befestigt wurden. Die Komponenten wurden wie im Schaltplan dargestellt angeschlossen. Beachten Sie, dass es am besten ist, jeden PCA9685 separat über den Klemmenblock mit Strom zu versorgen. Zuerst haben wir auch die V+- und GND-Anschlüsse verkettet und nur den Klemmenblock der ersten Platine angeschlossen (wie auf der adafruit-Seite vorgeschlagen), jedoch fließt in diesem Fall der gesamte Strom durch die erste Platine und wir haben den MOSFET verbrannt der Verpolungsschutzschaltung. Es liegt auch eine Tabelle bei, die die Verkabelung der Servos zeigt. Verlängerungskabel für die Servos wurden bei Bedarf verwendet. Beachten Sie, dass Sie jedem PCA9685 unterschiedliche I2C-Adressen zuweisen müssen, wie auf der adafruit-Seite erklärt.
Die Aktuatoren wurden dann mit 228x M2-Schrauben an der Rückplatte befestigt. Die Arbeit war wieder sehr eintönig, aber als sie fertig war, nahm die Uhr bereits Gestalt an. Wir haben auch versucht, die Servokabel so gut wie möglich zu organisieren, aber am Ende war die Verkabelung immer noch sehr unordentlich.
Die Stromversorgung erfolgte, indem das Gleichstromkabel durch die Rückplatte geführt und an eine Klemmenleiste angeschlossen wurde.
Schritt 9: Anbringen der Rückplatte am Rahmen
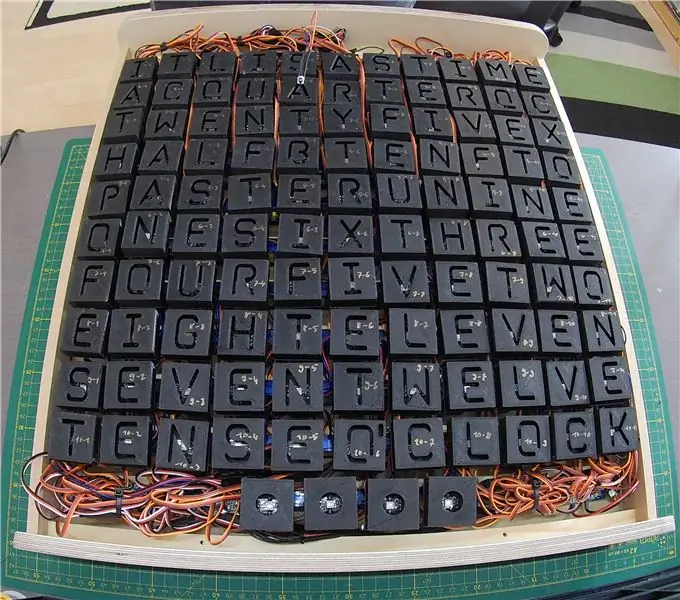
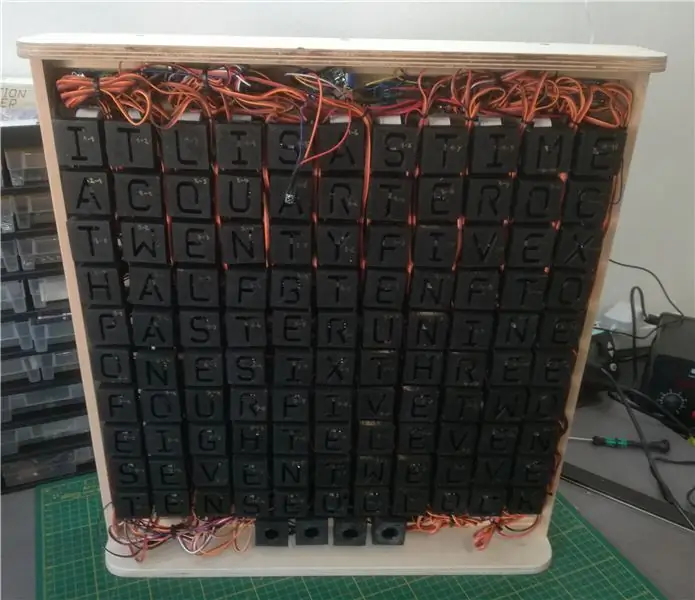
Nachdem alle Komponenten montiert und die Kabel organisiert waren, befestigten wir die Backplate mit 6x M4 Schrauben am Rahmen. Leider haben wir sehr wenig Platz für alle Kabel gelassen, so dass sie ein wenig eingequetscht werden mussten.
Schritt 10: Kalibrieren der Servos
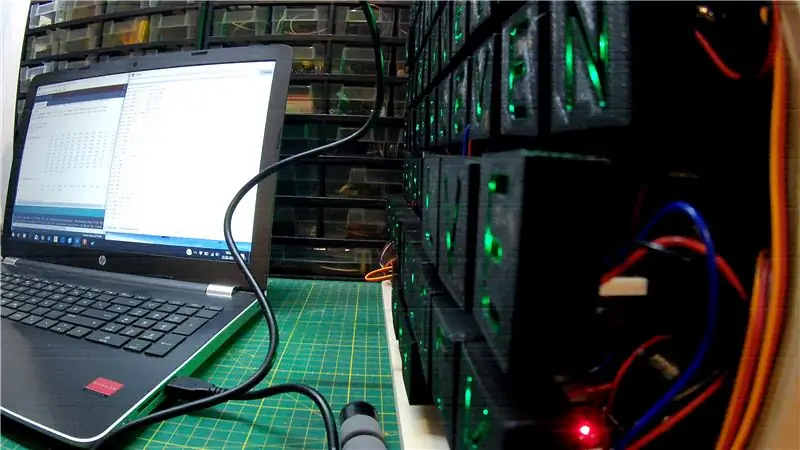
Da die Höhe aller Briefkästen nach der Montage leicht unterschiedlich war, haben wir den beiliegenden Code verwendet, um alle Servos so zu kalibrieren, dass die Briefkästen die gleiche minimale und maximale Position haben. Für die maximale Position haben wir versucht, den Letterbox so nah wie möglich am Bildschirm zu platzieren. Die kalibrierten Min/Max-Positionen für jedes Servo werden dann später in den Hauptcode eingetragen.
Schritt 11: Hochladen des Codes
Angehängt ist der Hauptcode für die Wordclock. Es gibt drei Arten von Effekten, um die Zeit anzuzeigen.
- Bewegen Sie alle Buchstaben schnell nach hinten (nacheinander) und leuchten Sie LEDs mit gleicher zufälliger Farbe auf. Bewegen Sie dann schnell nacheinander Buchstaben, die die Uhrzeit anzeigen, nach vorne und beleuchten Sie jedes Wort in einer zufälligen Farbe.
- Bewegen Sie alle Buchstaben schnell nach hinten (nacheinander) und leuchten Sie LEDs mit gleicher zufälliger Farbe auf. Bewegen Sie jedes Wort, das die Zeit anzeigt, langsam nach vorne (alle Buchstaben gleichzeitig) und verblassen Sie die Farbe von der Hintergrundfarbe auf einen zufälligen Wert.
- Bewegen Sie alle Buchstaben schnell an eine zufällige Position (nacheinander) und leuchten Sie LEDs mit verschiedenen zufälligen Farben auf. Bewegen Sie dann alle Buchstaben langsam nach hinten und verblassen Sie die Farbe. Weiter mit 1. oder 2.
Ich wollte auch einen Effekt implementieren, bei dem sich der Punkt, der die aktuelle Minute anzeigt, allmählich nach vorne bewegt und die Farbe verblasst, sodass er am Ende der Minute an der vorderen Position mit der richtigen Farbe steht. Leider habe ich es noch nicht zum Laufen gebracht, da der IR-Empfänger anscheinend nicht mehr reagiert.
Schritt 12: Anbringen des Bildschirms
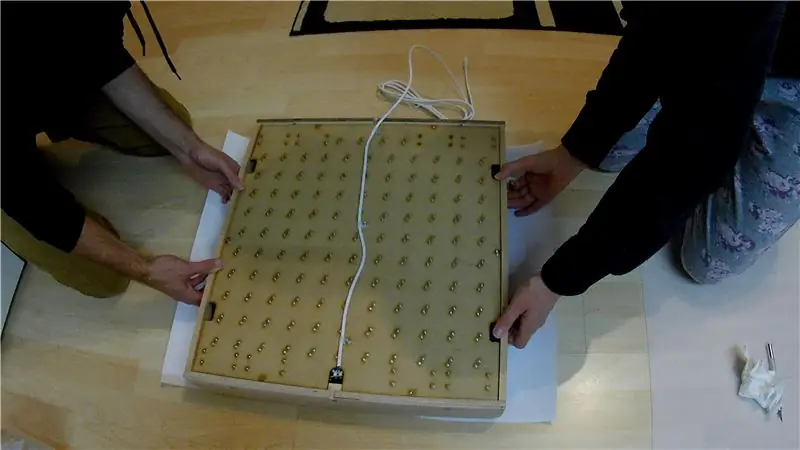
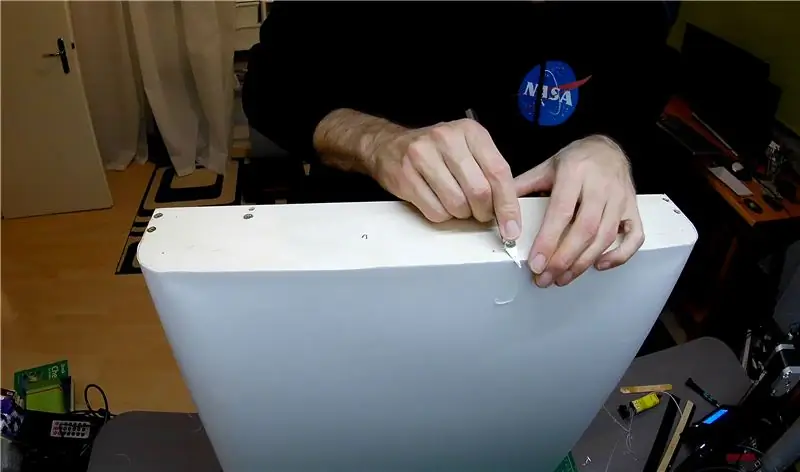
Zuerst wollten wir weißen Stoff als Sichtschutz verwenden. Das Problem war, dass sich der Stoff nach dem Anbringen am Rahmen in der Mitte nach unten beugte und wir am Ende eine Kissenverzerrung hatten. Wir haben uns dann entschieden, stattdessen eine dünne weiße PVC-Folie für den Bildschirm zu verwenden. Die Folie wird auch für die Herstellung von Lampenschirmen beworben, so dass sie eine vernünftige Transmission hat, aber nicht durchsichtig ist, so dass die schwarzen Briefkästen verborgen bleiben. In unserem ersten Versuch haben wir die Folie mit Epoxy befestigt, aber sie klebte nicht so gut, also wechselten wir zu Heißkleber. Seien Sie jedoch vorsichtig, wenn der Kleber zu heiß ist, kann er die Folie tatsächlich schmelzen. Überschüssige Folie wurde mit einem exakten Messer entfernt.
Schritt 13: Anbringen der oberen und unteren Abdeckung
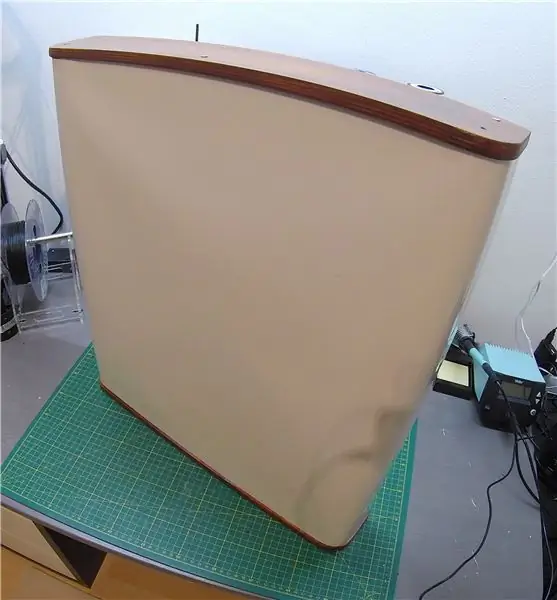
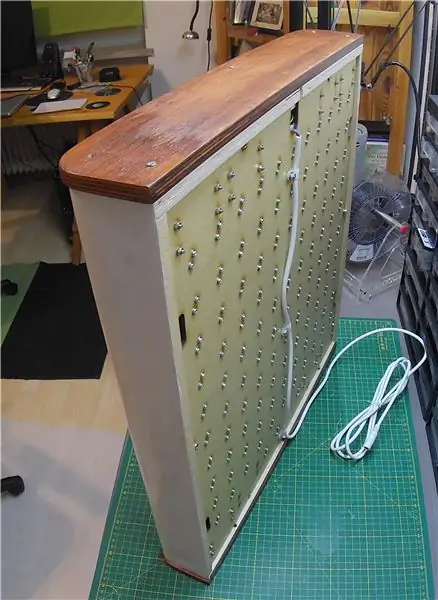
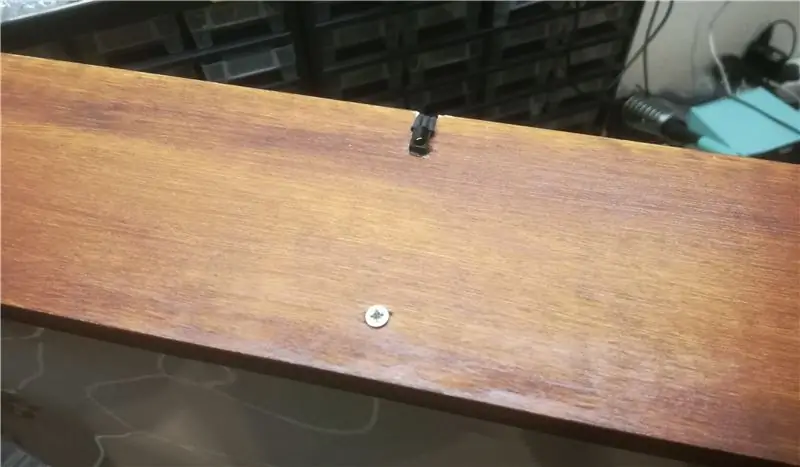
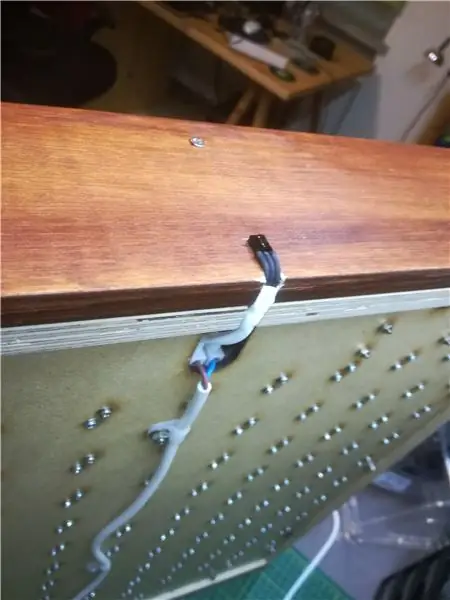
Schließlich wurden die gebeizten Holzabdeckungen oben und unten angebracht. Die dunkle Farbe bildet einen schönen Kontrast zum weißen Bildschirm. Der IR-Empfänger wurde durch das Loch in der Rückplatte geführt und mit Heißkleber an der oberen Abdeckung befestigt.
Schritt 14: Fertige Uhr und Zusammenfassung
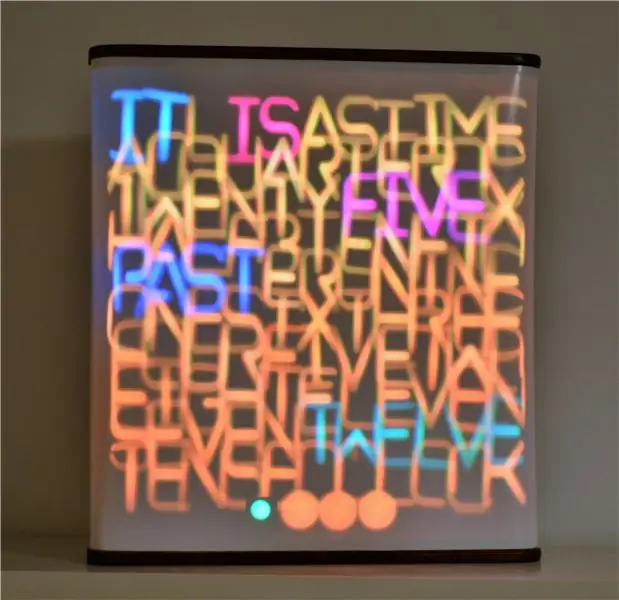
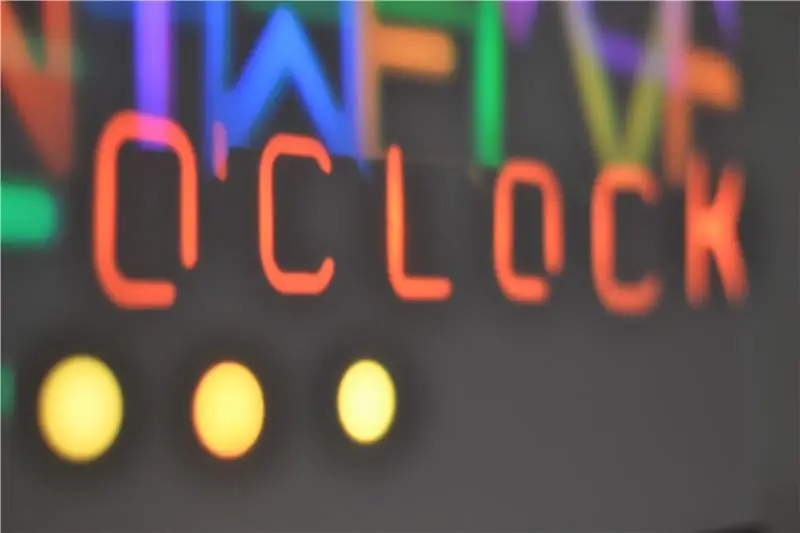
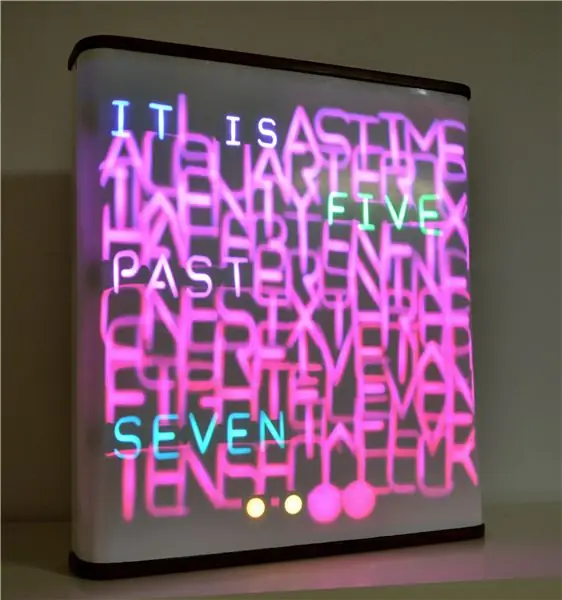
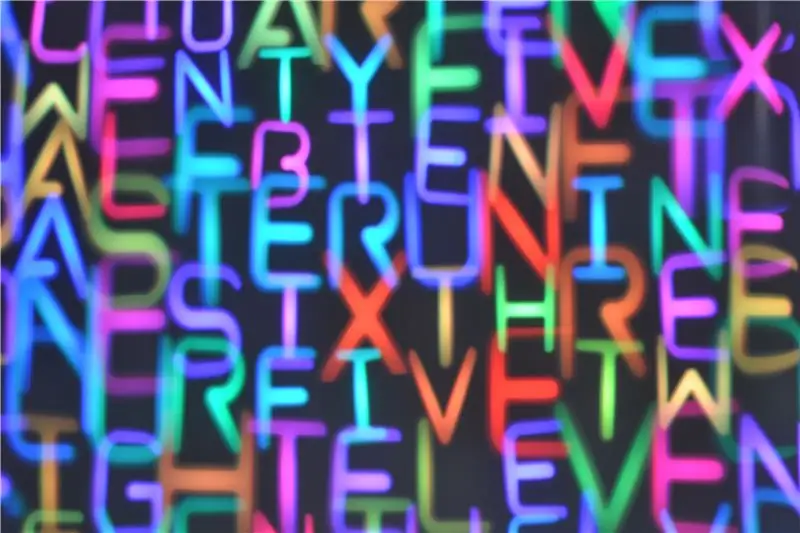
Nach zwei Monaten intensiver Arbeit war die Uhr endlich fertig und funktionierte. Insgesamt sind wir mit dem Ergebnis sehr zufrieden. Das Verschieben der Buchstaben hinter dem Bildschirm gepaart mit dem Ändern der Farben der LEDs erzeugt sehr cool aussehende Effekte. Am Ende passten die Buchstaben nicht perfekt und der Bildschirm war nicht 100% flach, aber dadurch sieht es fast noch schöner aus. Es gibt sicherlich Dinge, die verbessert werden können, aber ich glaube nicht, dass es aufgrund des enormen Aufwands dieses Builds eine Version 2.0 geben wird, es sei denn, wir lagern das nächste Mal die Produktion nach China aus.
Wenn Ihnen dieser Build gefällt und Sie es geschafft haben, ganz nach unten zu scrollen, stimmen Sie bitte im Epilog-Wettbewerb für uns ab.
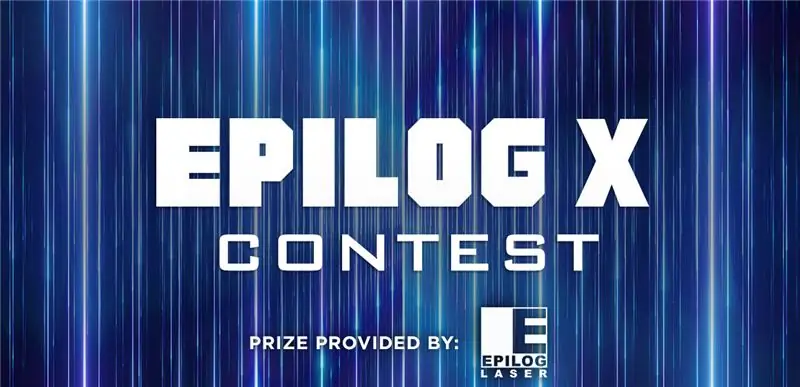
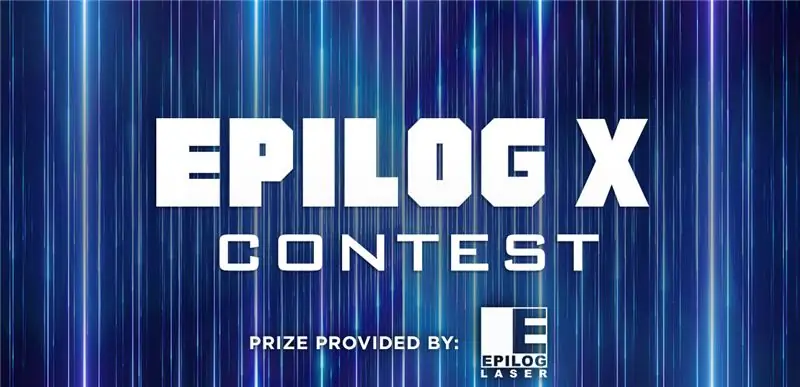
Erster Preis beim Epilog X-Wettbewerb
Empfohlen:
Löten von oberflächenmontierbaren Komponenten - Lötgrundlagen: 9 Schritte (mit Bildern)
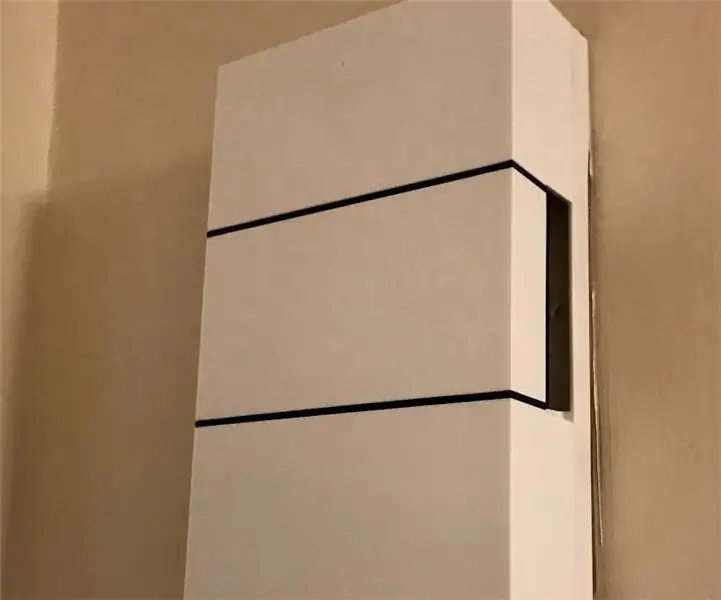
Löten von oberflächenmontierbaren Komponenten | Lötgrundlagen: Bisher habe ich in meiner Lötgrundlagen-Serie genug Grundlagen zum Löten besprochen, damit Sie mit dem Üben beginnen können. In diesem Instructable, was ich besprechen werde, ist etwas fortgeschrittener, aber es sind einige der Grundlagen zum Löten von Surface Mount Compo
Durchlöten von Komponenten - Lötgrundlagen: 8 Schritte (mit Bildern)
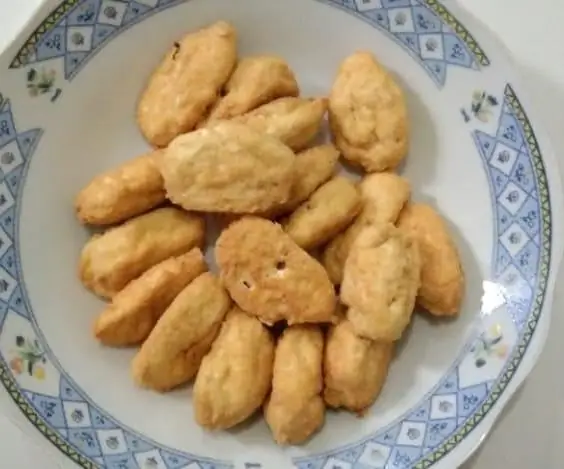
Löten von Durchgangslochkomponenten | Lötgrundlagen: In diesem Instructable werde ich einige Grundlagen zum Löten von Durchgangslochkomponenten auf Leiterplatten diskutieren. Ich gehe davon aus, dass Sie bereits die ersten 2 Instructables für meine Lötgrundlagen-Serie ausgecheckt haben. Wenn Sie nicht in meinem In
Anhängen von Google Kalender an Google Sites: 5 Schritte
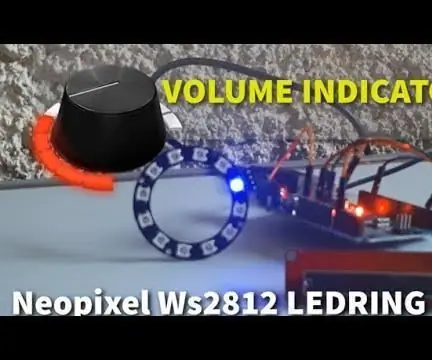
Anhängen von Google-Kalendern an Google Sites: Dies ist eine Anleitung, die Ihnen beibringt, wie Sie Google-Kalender erstellen, verwenden und bearbeiten und sie dann mithilfe der Freigabefunktionen an eine Google-Site anhängen. Dies kann für viele Menschen von Vorteil sein, da Google Sites verwendet werden kann, um i
MyPhotometrics - Gandalf: Leistungsmessgerät Zur Messung Von Lasern Im Sichtbaren Bereich Auf Basis Von "Sauron": 8 Schritte
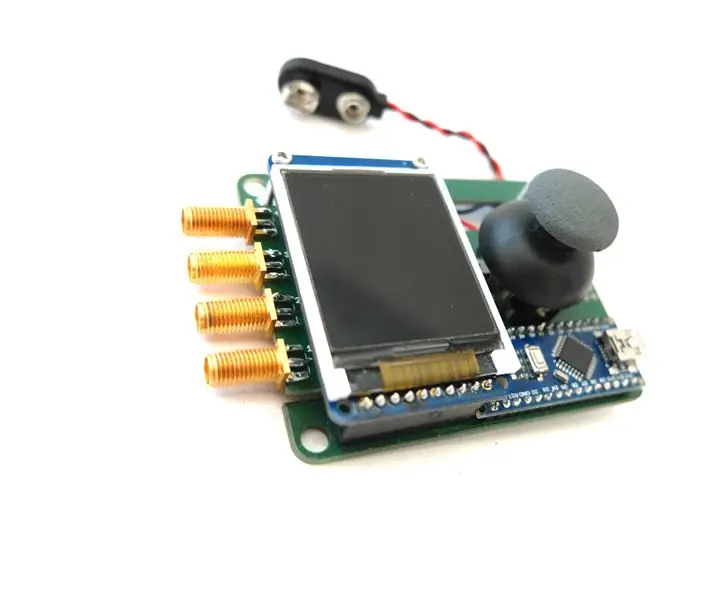
MyPhotometrics - Gandalf: Leistungsmessgerät Zur Messung Von Lasern Im Sichtbaren Bereich Auf Basis Von "Sauron": Dieses Werk ist lizenziert unter einer Creative Commons Namensnennung - Weitergabe unter gleichen Bedingungen 4.0 International Lizenz. Eine für Menschen lesbare Zusammenfassung dieser Lizenz findet sich hier.Was ist Gandalf?Gandalf ist eine Stand-A
Wir stellen vor: 'Deodorino' - das Infrarot-gesteuerte Arduino in einem leeren Deodorant-Stick. Klicken Sie auf das 1. Foto: 7 Schritte
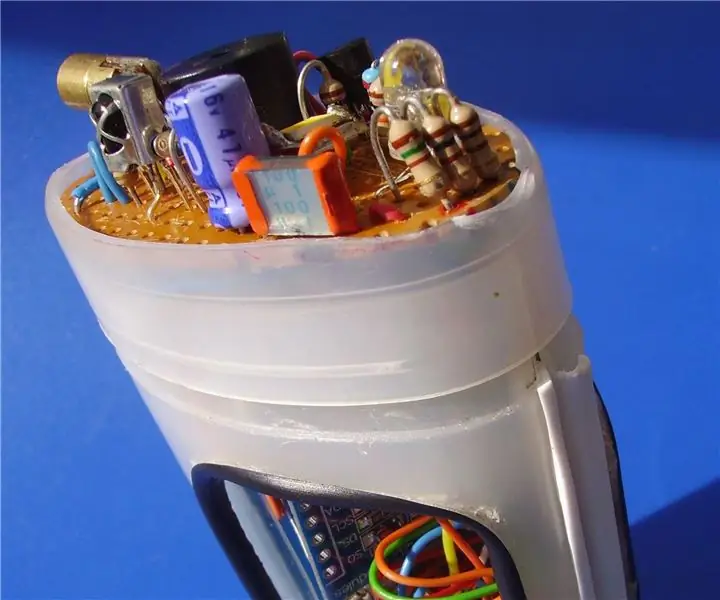
Wir stellen vor: 'Deodorino' - das Infrarot-gesteuerte Arduino in einem leeren Deodorant-Stick. Klicken Sie auf das 1. Foto: Jetzt zum Detail