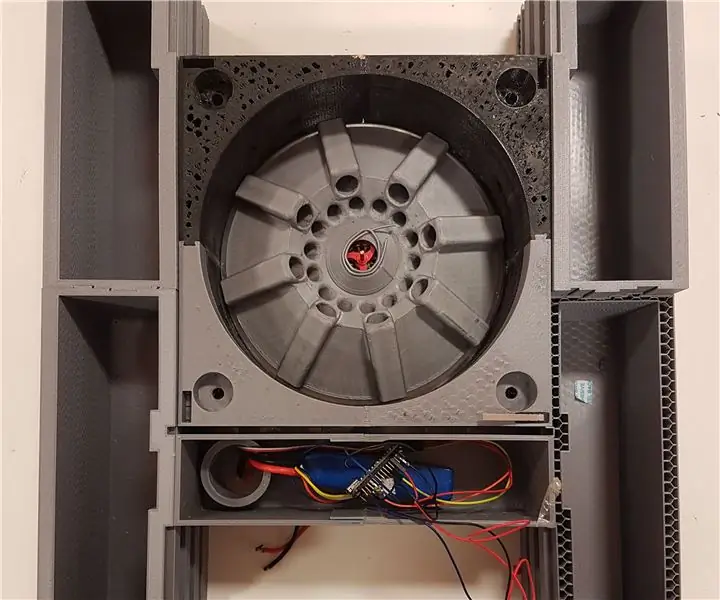
Inhaltsverzeichnis:
- Schritt 1: Problem- und Designaussagen
- Schritt 2: Design-Begründung:
- Schritt 3: Designüberlegungen
- Schritt 4: Erst-/Basismoduldesign
- Schritt 5: Teileliste
- Schritt 6: Drucken von Teilen:
- Schritt 7: Montage: Erster Schritt
- Schritt 8: Montage: Elektronische Komponenten
- Schritt 9: Montage: Anbringen von Rotor und Spinnerschraube
- Schritt 10: Montage: Ballast und Deckel
- Schritt 11: Fazit
2025 Autor: John Day | [email protected]. Zuletzt bearbeitet: 2025-06-01 06:08
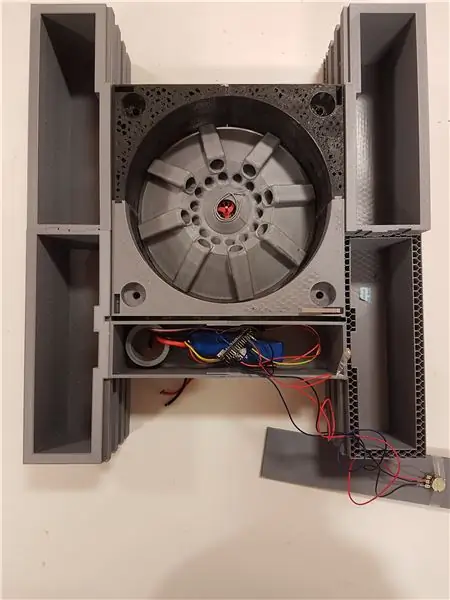
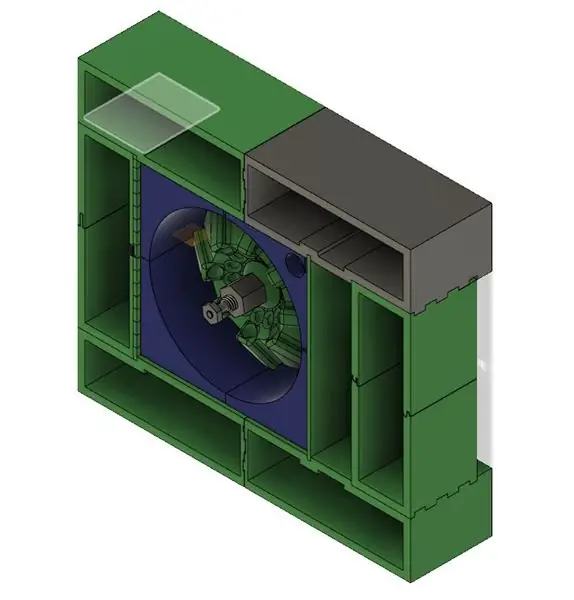
Dies ist ein fortlaufendes Projekt, das mit Unterstützung der Gemeinschaft und weiterer Forschung und Anleitung aktualisiert wird
Das Ziel dieses Projekts ist es, quelloffene, modulare Laborgeräte zu schaffen, die leicht zu transportieren und aus billig beschafften Teilen gebaut sind, um die Diagnose von Krankheiten in abgelegenen und infrastrukturell schwachen Gebieten zu unterstützen
Dabei handelt es sich um ein laufendes Open-Source-Projekt mit dem Ziel, eine modulare Plattform für Medizinprodukte bereitzustellen, die einfach und kostengünstig modifiziert und erweitert werden kann
Erste Entwürfe werden für ein modulares Batterie- und Gleichstrommotorpaket sowie eine Mikrozentrifuge vorgesehen sein
Es wird die Hilfe der Online-Open-Source-Community in Anspruch nehmen, um bei der Unterstützung, Änderung und weiteren Gestaltung zu helfen, um auf die individuellen spezifischen Bedürfnisse von Gesundheitspersonal in abgelegenen und ländlichen Gebieten einzugehen
HAFTUNGSAUSSCHLUSS: Das Projekt befindet sich noch in der Design- und Funktionsprüfung und ist noch nicht für KEINE diagnostische oder klinische Anwendung geeignet. Elektronik und Motoren sind auf eigene Gefahr zu montieren und zu benutzen
Schritt 1: Problem- und Designaussagen
Problemstellung:
Der fehlende Zugang zu Labor- und Klinikgeräten zur Unterstützung der Diagnose und Behandlung von Krankheiten führt zu vermeidbaren Todesfällen vieler Menschen in abgelegenen Gebieten mit geringer Infrastruktur. Insbesondere der fehlende Zugang zu grundlegenden zuverlässigen Zentrifugen beraubt das Gesundheitspersonal eines wichtigen Werkzeugs im Kampf gegen durch Blut übertragene Krankheitserreger wie AIDS und Malaria.
Design-Statement: Design einer Mikrozentrifuge und eines modularen Batterie- und Gleichstrommotorpakets zur Unterstützung der Diagnose und Behandlung von Krankheiten, die durch blutübertragene Pathologien (Krankheitserreger und Parasiten) verursacht werden. Durch den Einsatz additiver Fertigungstechniken, wo dies möglich ist, soll dieses Design die Portabilität verbessern und die wirtschaftlichen Barrieren lebensrettender Technologien senken.
Schritt 2: Design-Begründung:
Dieses Design zielt darauf ab, eine Mikrozentrifuge herzustellen, die für den Ersatzeinsatz in ländlichen Gebieten geeignet ist, indem Desktop-FDM-3D-Druck, Laserschneiden und Elektronik in Hobbyqualität verwendet werden. Auf diese Weise hofft man, dass das Gerät für eine Vielzahl von Angehörigen der Gesundheitsberufe mit unterschiedlichem Zugang zu Ressourcen zugänglich ist.
Bei der Konstruktion des Zentrifugenrotors (Teil der Konstruktion, der Reagenzgläser hält):
Die erforderliche G-Zahl für die Trennung von Proben hängt vom gewünschten Probentyp ab, wobei die durchschnittlichen Kräfte für die Trennung von Blut in seine Bestandteile zwischen 1.000 - 2.000 g liegen (thermofisher.com)
Die Berechnung von RPM zu RFC (G-force) kann mit RCF = (rpm)2 × 1,118 × 10-5 × r berechnet werden, wobei 'r' der Radius des Rotors ist (bcf.technion.ac.il)
Schritt 3: Designüberlegungen
Überlegungen zur additiven Fertigung:
• Es kann zu einer schlechten Schichthaftung kommen, was zu geringer Zugfestigkeit und Beschädigung der Teile führt
• Erforderliche Eigenschaften, variieren je nach Material. Einige bieten gute seitliche Dehnung und Druckfestigkeit bei geringem Gewicht und geringen Kosten
• Beim Schneiden des G-Codes müssen korrekte Einstellungen vorgenommen werden, um sicherzustellen, dass die gewünschten Materialeigenschaften erreicht werden
• Die Lebensdauer der mit dieser Technik hergestellten Teile ist relativ gering im Vergleich zu denen, die teurere Techniken und Materialien wie CNC-Fräsen von Metallen verwenden.
• Thermoplaste haben eine relativ niedrige Übergangstemperatur, daher muss eine niedrige Betriebstemperatur eingehalten werden (< ca. 80-90 Celsius). • Open-Source 3D-gedruckte Designs ermöglichen es Benutzern, Designs an ihre Bedürfnisse und Einschränkungen anzupassen
Weitere Designbeschränkungen:
• Einige Gebiete haben möglicherweise keinen ausreichenden Zugang zu Strom, müssen möglicherweise mit einfachen tragbaren Solarzellen, Batterien usw. versorgt werden.
• Vibration und Gleichgewicht können ein Problem sein
• Muss in der Lage sein, über einen Zeitraum von bis zu 15 min oder länger hohe Drehzahlen auszugeben, führt zu hoher mechanischer Belastung einiger Teile
• Benutzer haben möglicherweise keine Erfahrung im Umgang mit Geräten und benötigen Unterstützung, um technische Barrieren abzubauen
Schritt 4: Erst-/Basismoduldesign
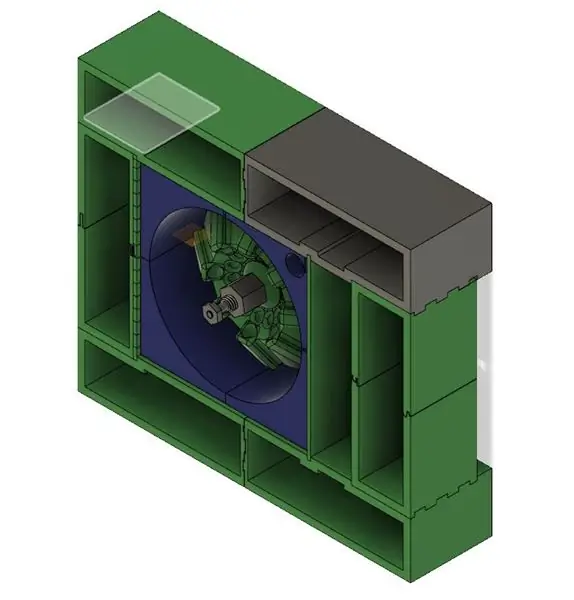
Das obige Design nutzt den Platz optimal aus, um ausreichend Platz für interne elektronische Komponenten bereitzustellen, und gewährleistet einen ausreichend großen Radius für eine Vielzahl von Zentrifugenrotoren und Röhrchengrößen. Der „Snap-toy“-Stil des Designs wurde gewählt, um den Bedarf an Stützmaterial während der Produktion zu eliminieren und ein einfaches Drucken, Reparieren und Herstellen sowohl bei der additiven als auch bei der subtraktiven Fertigung zu ermöglichen. Darüber hinaus reduziert das Drucken kleinerer einzelner Teile die Auswirkungen von Druckfehlern/-fehlern und ermöglicht die Verwendung einer größeren Vielfalt von Druckbettgrößen.
Durch den modularen Aufbau können viele verschiedene Arten von Schleudertrommeln an der Vorrichtung angebracht werden. Schnelle Modifikationen und Produktion dieser Teile durch additive Fertigung ermöglichen Änderungen der hergestellten G-Zahl und der verarbeiteten Probengröße/-art. Dies verschafft ihm einen Vorteil gegenüber herkömmlichen Maschinen und bietet einen innovativen Ansatz bei der Konstruktion von Maschinen nach den Bedürfnissen des Endbenutzers. Darüber hinaus bieten die Ballastbehälter die Möglichkeit, zusätzliche Unterstützung zu bieten und Vibrationen zu dämpfen
Schritt 5: Teileliste
3D-gedruckte Teile: Dateien werden auf Github und thingiverse hochgeladen und so schnell wie möglich aktualisiert.
- 1 x Spindelschraube
- 1 x Rotormutter
- 1 x Deckelmutter
- 1 x Hauptdeckel
- 4 x Rotorkörper
- 1 x Festwinkelrotor
- 4 x Ballast oben/unten
- 2 x Seitenballast
Elektronik:(Links zu Produkten in Kürze)
Arduino-Nano (8-10)
Anschlussdrähte (<0,2 $)
Elektronischer Geschwindigkeitsregler ($8-10)
Bürstenloser Gleichstrommotor 12V (15-25 $)
Potentiometer (0,1 $)
Li-Po-Akku ($ 15-25)
Schritt 6: Drucken von Teilen:
Alle Teile sind hier bei github erhältlich: Auch hier bei thingiverse erhältlich:
3d gedruckte Teile: 1 x Spindelschraube
1 x Rotormutter
1 x Deckelmutter
1 x Hauptdeckel
4 x Rotorkörper
1 x Festwinkelrotor
4 x Ballast oben/unten
2 x Seitenballast
Die allgemeinen Entwurfseinstellungen von Cura oder ähnlich in ausgewählter Slicer-Software sind eine gute Richtlinie für den Druck aller Karosserie- und Ballastteile.
Schritt 7: Montage: Erster Schritt
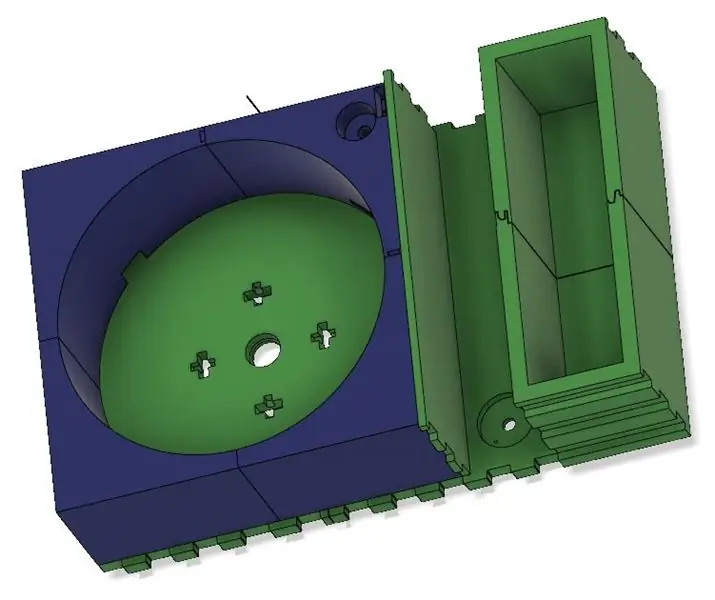
-
Bereiten Sie die folgenden Teile für den Zusammenbau wie abgebildet vor:
- Zentrifugenbasis
- Komponentengehäuse
- 4 x Rotorkörper
- Alle Teile sollten eng zusammenpassen und mit geeigneten Klebstoffen befestigt werden
Schritt 8: Montage: Elektronische Komponenten
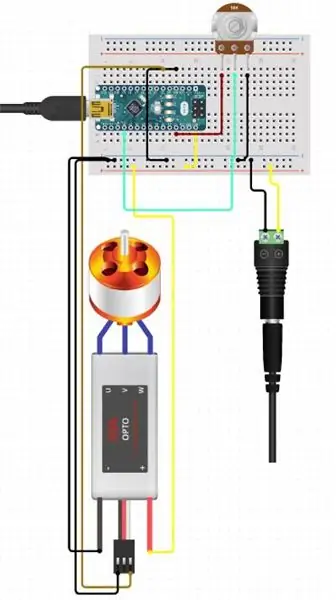
Bereiten Sie die folgenden elektronischen Komponenten zum Testen vor:
- Gleichstrommotor und ECS
- Batterie
- Arduino Nano
- Steckbrett
- Potentiometer
- Überbrückungsdrähte
Codierung und Anleitung für das Arduino finden Sie hier:
Artikel von
Testmotor läuft ruhig und reagiert auf das Potentiometer. Wenn ja, dann bauen Sie die Elektronik in das Gehäuse ein und testen Sie, ob der Motor ruhig und vibrationsarm läuft.
Bilder der genauen Platzierung werden in Kürze hinzugefügt.
Schritt 9: Montage: Anbringen von Rotor und Spinnerschraube
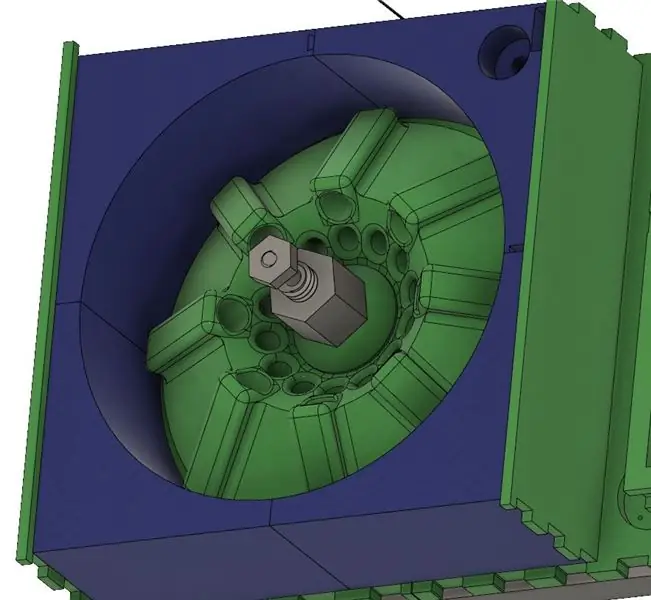
Sammeln Sie Rotor, Rollen, Spinner und Spinnermuttern.
Achten Sie auf einen guten Sitz aller Teile. Schleifen kann helfen, wenn die Passform zu eng ist.
Stellen Sie sicher, dass der Rotor einen glatten Lauf hat und nicht übermäßig springt oder wackelt. Eine flache Schale kann bedruckt oder aus Acryl geschnitten werden, um bei Bedarf die Stabilität zu erhöhen.
Nachdem die Teile geschliffen und montiert wurden, befestigen Sie die Spinnerschraube an der Motorspindel und sichern Sie den Rotor mit den Muttern wie abgebildet.
Der Rotor kann zum Entladen und Laden von Proben oder zum Wechseln des Rotortyps entfernt werden.
Schritt 10: Montage: Ballast und Deckel
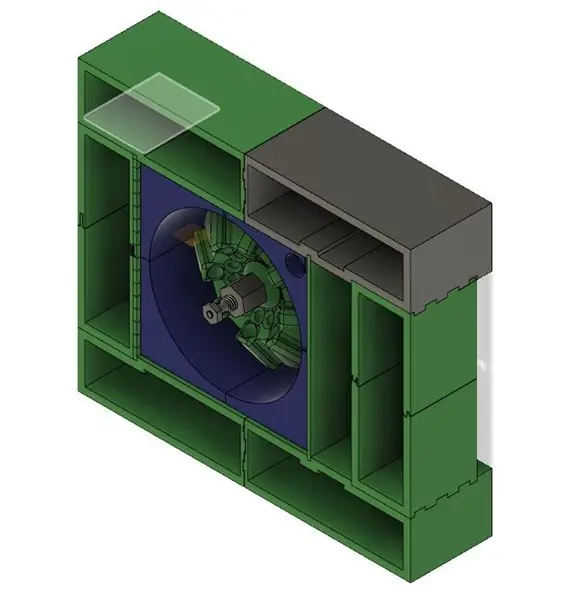
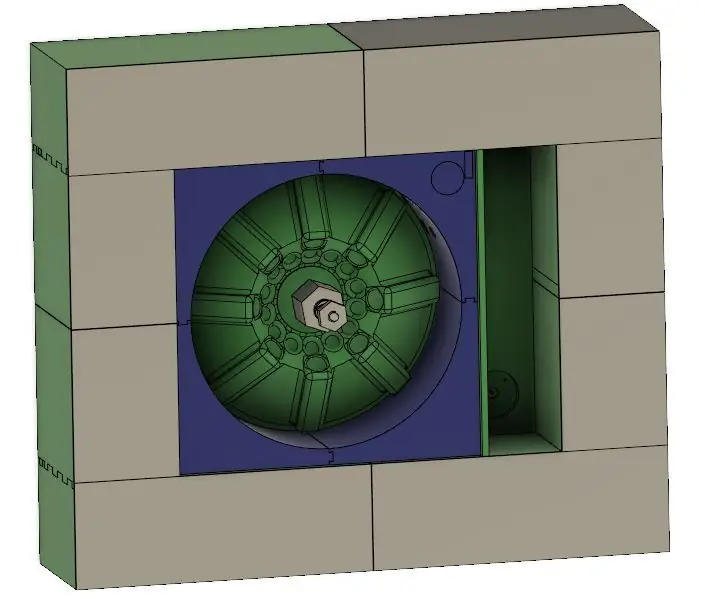
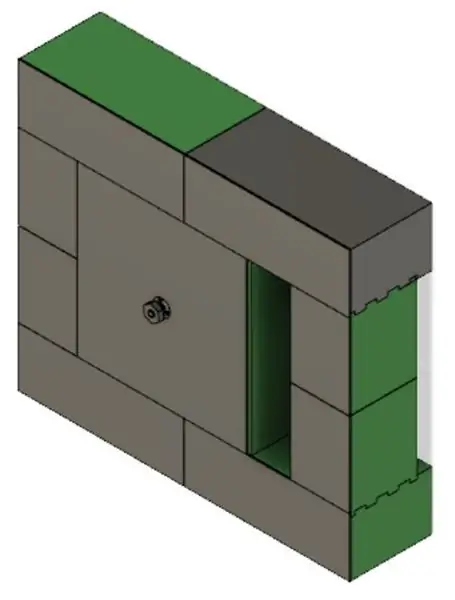
Sammeln Sie obere und seitliche Ballastbehälter, diese dienen als Stütze, Gewichtung und Schwingungsdämpfung.
Die Teile sollten zusammenpassen und beim Befüllen an Ort und Stelle bleiben. Bei Bedarf können die Teile mit Sekundenkleber oder ähnlichem Klebstoff zusammengehalten werden.
Der Hauptdeckel über dem Rotor sollte sicher sitzen, wenn er mit der oberen Rotormutter befestigt ist.
Teile sollten wie im Bild gezeigt passen.
Schritt 11: Fazit
Mitarbeiter des Gesundheitswesens an Remotestandorten stehen vor der Herausforderung wirtschaftlicher und logistischer Hindernisse, die mit der Beschaffung und Wartung lebenswichtiger medizinischer und diagnostischer Geräte und Teile verbunden sind. Ein fehlender Zugang zu Basisgeräten wie Zentrifugen und Pumpensystemen kann zu fatalen Wartezeiten und Fehldiagnosen führen.
Dieses Design hat das gewünschte Ergebnis erzielt, indem es gezeigt hat, dass es möglich ist, ein medizinisches Open-Source-Gerät (eine Mikrozentrifuge) unter Verwendung von Desktop-Fertigungstechniken und grundlegenden elektronischen Komponenten herzustellen. Es kann zu einem Zehntel der Kosten handelsüblicher Maschinen hergestellt und leicht repariert oder in Teile zerlegt werden, die in anderen Geräten verwendet werden können, wodurch wirtschaftliche Barrieren gesenkt werden. Die elektronischen Komponenten liefern eine konstante, zuverlässige Stromversorgung für die Zeit, die für die Verarbeitung der gängigsten Blutproben erforderlich ist, und bieten eine bessere Diagnose als handbetriebene oder Steckdoseneinheiten in Bereichen mit geringer Infrastruktur. Die Machbarkeit dieses Designs hat zukünftiges Potenzial in der Entwicklung einer modularen Open-Source-Plattform für medizinische Geräte, die einen Kernsatz von Komponenten verwendet, um verschiedene Geräte wie Peristaltikpumpen oder, wie in diesem Design, Mikrozentrifugen anzutreiben. Mit der Einrichtung einer Bibliothek mit Open-Source-Dateien könnte der Zugriff auf einen einzigen FDM-Drucker verwendet werden, um eine Reihe von Teilen zu produzieren, wobei der Endbenutzer nur geringe Designkenntnisse benötigt. Dies würde die logistischen Probleme, die mit dem Versand von Basiskomponenten verbunden sind, beseitigen und Zeit und Leben sparen.
Empfohlen:
So bauen Sie ein kostengünstiges EKG-Gerät – wikiHow
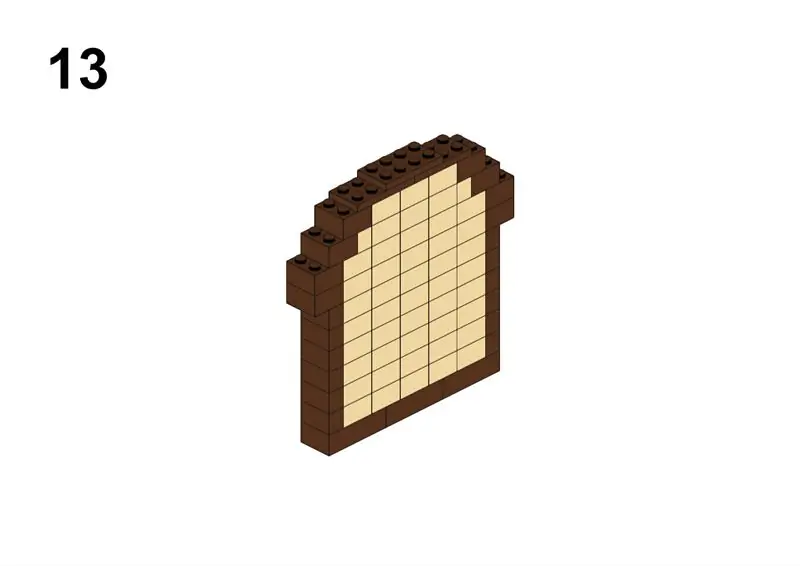
So bauen Sie ein kostengünstiges EKG-Gerät: Hallo zusammen! Mein Name ist Mariano und ich bin biomedizinischer Ingenieur. Ich verbrachte einige Wochenenden damit, einen Prototyp eines kostengünstigen EKG-Geräts basierend auf einem Arduino-Board zu entwerfen und zu realisieren, das über Bluetooth mit einem Android-Gerät (Smartphone oder Tablet) verbunden ist. Ich würde
Arduino Social Distancing-Gerät mit PIR herstellen – wikiHow
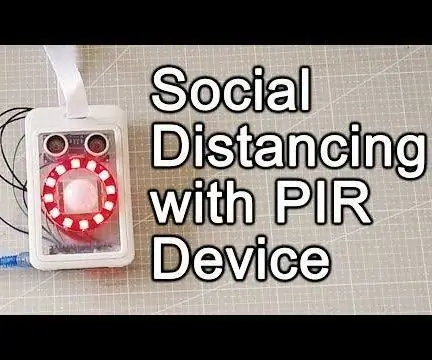
Wie man Arduino Social Distancing Device mit PIR herstellt: 1
So schalten Sie das GPS auf ein anderes Gerät um – wikiHow
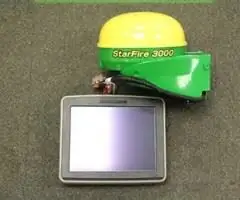
So schalten Sie das GPS auf verschiedene Geräte um: Der Vorgang besteht darin, das GPS von der Kabine des Mähdreschers zu nehmen, es auf die Traktorkabine zu setzen, das Display vom Mähdrescher auszuhängen und in den Traktor einzubauen. Es werden keine Werkzeuge benötigt, um diesen Vorgang abzuschließen, und seien Sie vorsichtig beim Herumklettern auf Geräten
ASS-Gerät (Asoziales soziales Gerät): 7 Schritte
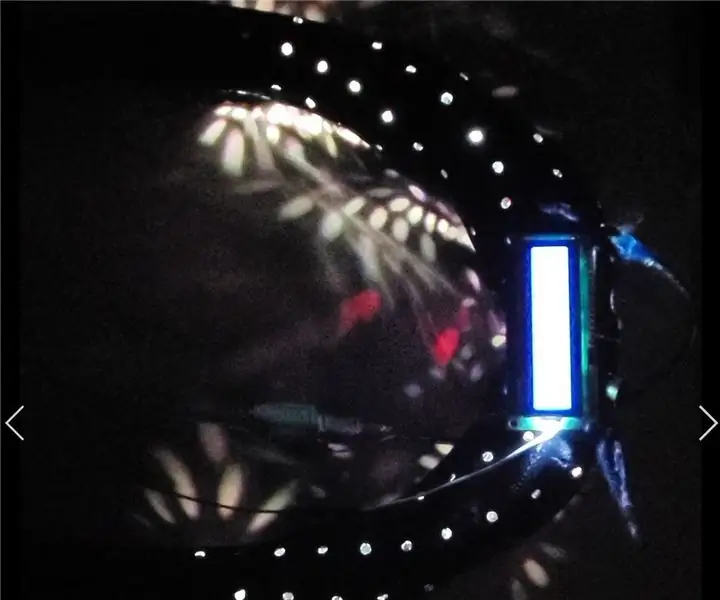
ASS-Gerät (Asoziales soziales Gerät): Angenommen, Sie sind die Art von Person, die gerne mit Menschen zusammen ist, aber es nicht mag, dass sie zu nahe kommen. Sie sind auch ein Publikumsliebling und es fällt Ihnen schwer, Nein zu Menschen zu sagen. Sie wissen also nicht, wie Sie ihnen sagen sollen, dass sie sich zurückziehen sollen. Nun, treten Sie ein – das ASS-Gerät! Ja
So steuern Sie ein Gerät mit Raspberry Pi und einem Relais – DIE GRUNDLAGEN: 6 Schritte
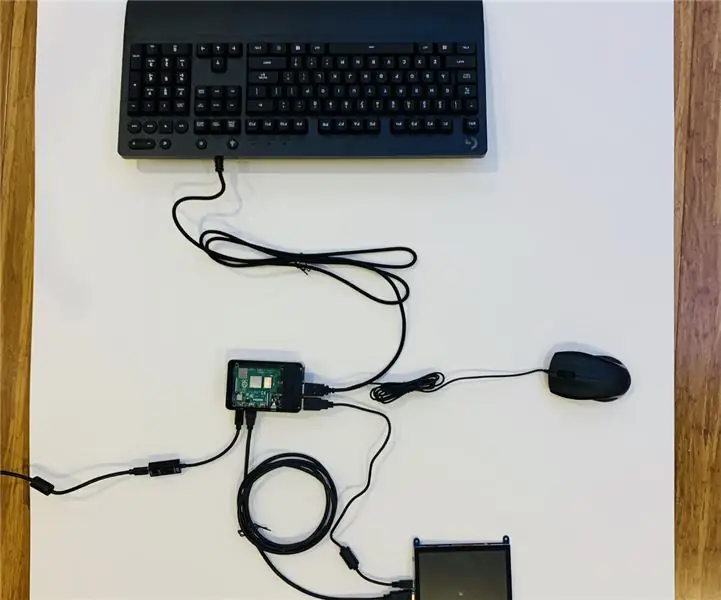
So steuern Sie ein Gerät mit Raspberry Pi und einem Relais - DIE GRUNDLAGEN: Dies ist ein einfaches und unkompliziertes Tutorial zur Steuerung eines Geräts mit Raspberry Pi und einem Relais, das für die Erstellung von IoT-Projekten hilfreich ist folgen Sie, auch wenn Sie keine Ahnung von Raspberry haben