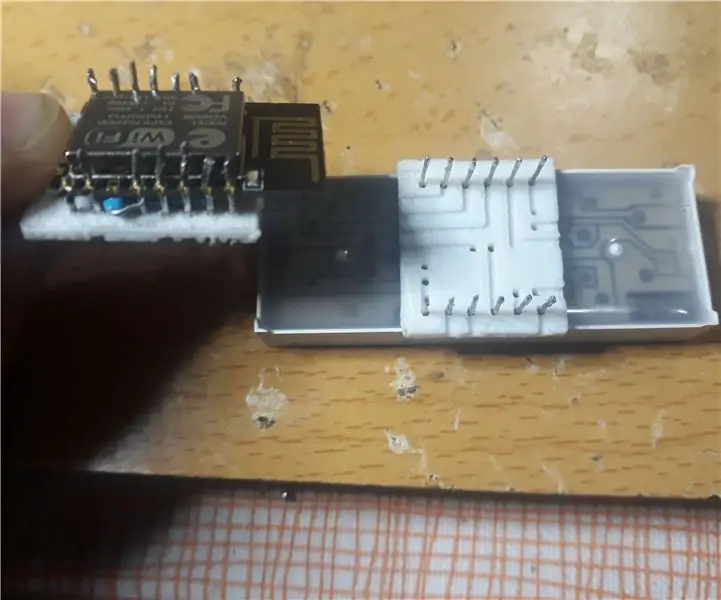
Inhaltsverzeichnis:
2025 Autor: John Day | [email protected]. Zuletzt bearbeitet: 2025-01-23 12:52
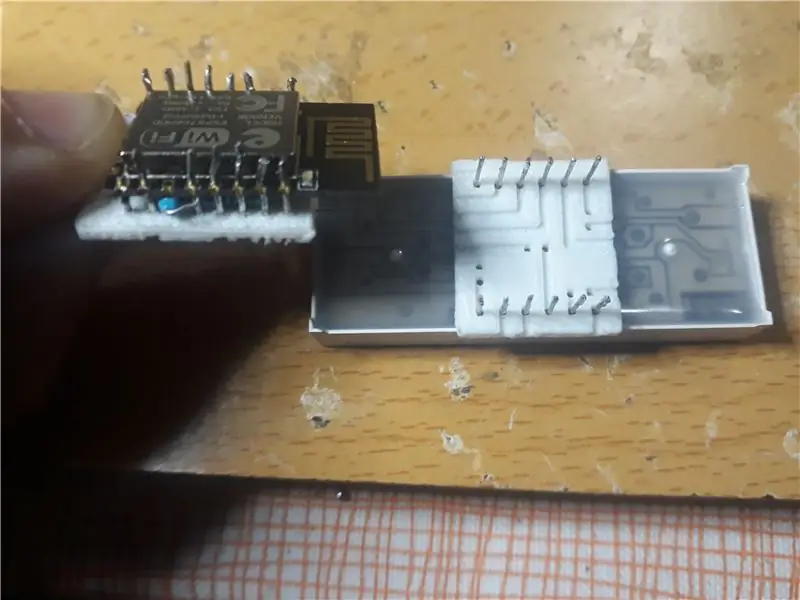
Als ich eine 4-stellige 7-Segment-Anzeige an meinen Teensy anschließen musste, beschloss ich, auf einfache Weise zu recherchieren, wie PCBs zu Hause hergestellt werden können. Traditionelles Ätzen ist ziemlich mühsam und gefährlich, also habe ich das schnell verworfen. Eine gute Idee, die ich gesehen habe, sind 3D-gedruckte Platinen, die Ihren Kanälen leitfähige Farbe hinzufügen, aber dies scheint für die Leitfähigkeit ziemlich unberechenbar zu sein. Es gibt auch spezielle leitfähige Filamente, die Sie auf einem Dual-Extrusionsdrucker verwenden könnten, aber ich suche etwas Einfaches und Effektives für die Standardausrüstung, die ich habe.
Also habe ich daran gedacht, Bauteile und Stecker direkt auf 3D-Drucken zu löten und zu verlegen.
Bevor wir beginnen, seien Sie gewarnt: Wir werden mit ABS drucken, da es +200 ° C verträgt, bevor es sich verformt (damit wir vorsichtig etwas löten können). Das Drucken mit ABS ist nicht so einfach wie mit PLA, Sie benötigen einen mitgelieferten Drucker und viele Kalibrierungen der Einstellungen, aber wenn Sie dies richtig gemacht haben, macht das Ergebnis einen Unterschied.
Um etwas Kontext hinzuzufügen, erstelle ich in den Beispielen eine Platine für die ESP8266 12E-WLAN-Platine, damit ich sie später problemlos mit etwas anderem verbinden kann (Endziel ist ein 4d7seg-Display).
Die Platine lässt mich alle verfügbaren Pins verwenden, während die meisten Module auf dem Markt nur sehr wenige Ersatzpins haben oder zu viele zusätzliche Funktionen haben, die ich nicht wirklich möchte (wie die NodeMCU).
Lieferungen
- PCB-Design-Software (KiCad hier, kostenlos). Anfängerniveau.
- 3D-Modellierungssoftware (Blender hier, kostenlos). Benutzerlevel.
- Ein 3D-Drucker (hier Creality 3D Ender 3 Pro, ca. 200€). Benutzerlevel.
- Ein Gehäuse für Ihren Drucker wird dringend empfohlen, wenn Sie ABS verwenden - Stellen Sie sicher, dass Sie ABS erfolgreich drucken können, bevor Sie mit dieser Anleitung fortfahren.
- ABS-Filament (Smartfil ABS, ca. 20€/Kg). 3-15 Gramm pro Leiterplatte.
- Nähnadeln (hol dir einfach welche von Mama). Die Größe hängt vom Durchmesser der Pins Ihrer Komponenten ab. Normalerweise 0,5 mm oder 1 mm Durchmesser.
- Lötzinn und ein Schweißgerät (ca. 15€ von einem lokalen Geschäft). Dazu alle zum Schweißen geeigneten Zubehörteile: Schweißerhalterung, Lampe, Tafel, Pinzette, Schutzbrille, Maske… das Zubehör bleibt dem Benutzer überlassen, aber stellen Sie sicher, dass Sie sich beim Basteln wohl und sicher fühlen!
- Viel Geduld, kreatives Out-of-the-Box-Geist und eine gute Grundlage (versuchen Sie, viel zu googeln und zu studieren, bevor Sie es in die Hände bekommen).
Schritt 1: Prototyp & Schaltplan
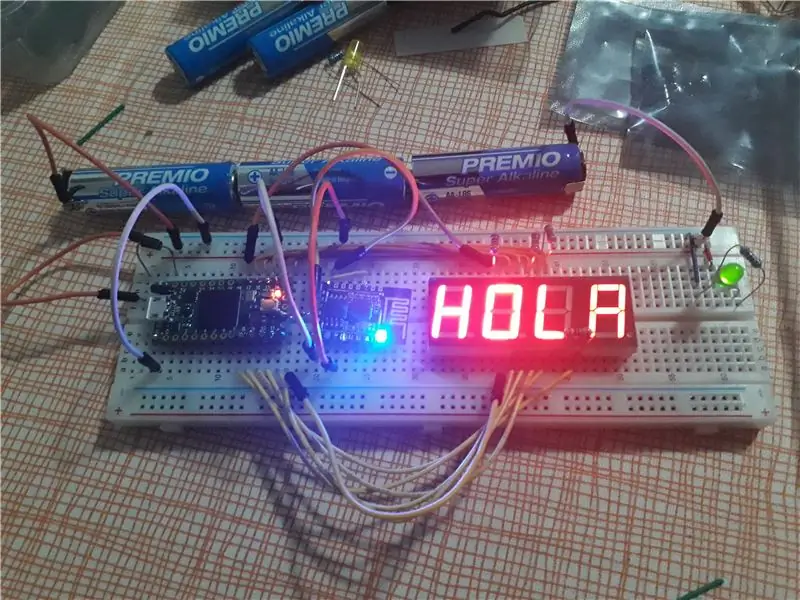
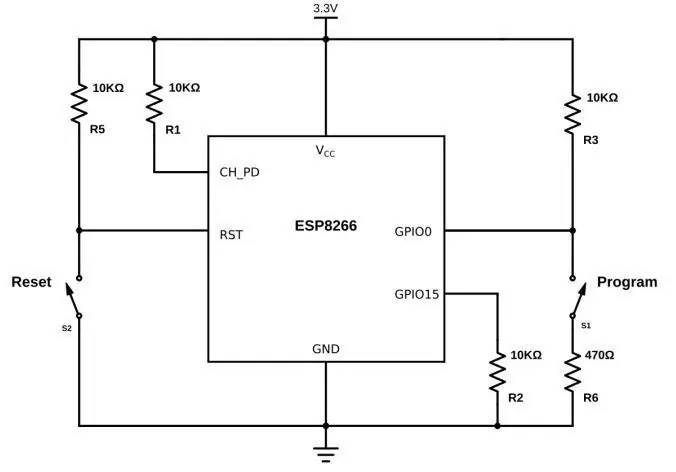
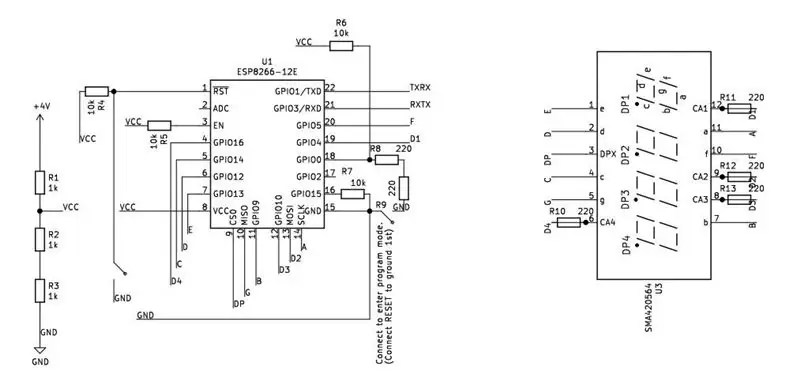
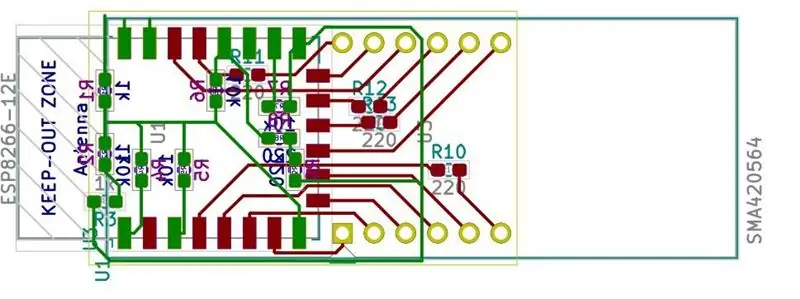
Sofern Sie nicht dem Schaltplan einer anderen Person folgen, sollten Sie Ihren Stromkreis gemäß den Herstellerspezifikationen aufbauen. Testen Sie eine Prototyp-Schaltung, und skizzieren Sie, sobald sie funktioniert, alle Verbindungen und Komponenten.
Sobald Sie eine Skizze haben und mit einem klaren Verständnis Ihrer Schaltung vertraut sind, erhalten Sie sie in Ihrer bevorzugten EDA-Software detailliert. Dies hilft bei der Optimierung und Überprüfung Ihres Designs.
Zeichnen Sie Ihren Schaltplan und verwenden Sie diesen als Leitfaden für Ihr PCB-Design. Mit EDA-Software wie Eagle oder KiCad können Sie Ihre spezifischen Komponenten mit realistischen Pinbelegungen und Abmessungen hinzufügen, sodass Sie Ihren Stromkreis präzise um sie herum entwerfen können.
Ich verwende KiCad, das kostenlos und für den Anfang leicht zu verstehen ist. Alles, was ich weiß, ist Brian Benchoff @ https://hackaday.com/2016/11/17/creating-a-pcb-in… und einigen verwandten Beiträgen zu verdanken. Befolgen Sie also seine Richtlinien, um ein schönes PCB-Design zu erhalten.
Bilder in diesem Abschnitt beziehen sich auf:
- Testprototyp für den ESP8266 und eine 4-stellige 7-Segment-Anzeige (an einem Teensy 4 befestigt).
- Ein Referenz-Schaltplan für eine ESP8266 12E-WLAN-Platine.
- Ein KiCad-Schema für eine 4-stellige 7-Segment-Anzeige, die über den ESP8266 und einen Spannungsteiler arbeitet (dies ist mein Endziel).
- Eine Ausgabe des KiCad-PCB-Designs.
Schritt 2: 3D-Modell
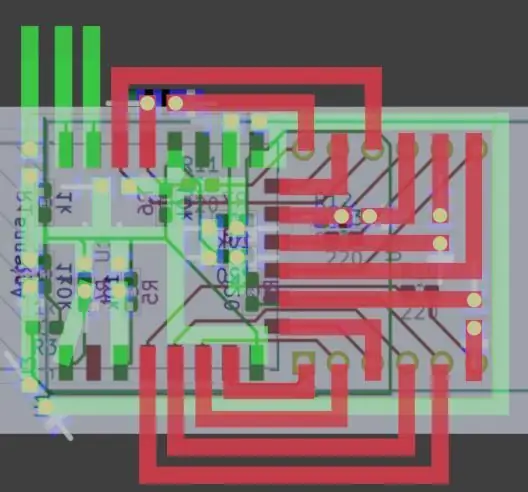

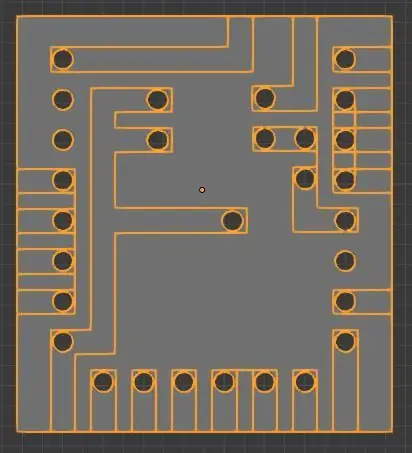
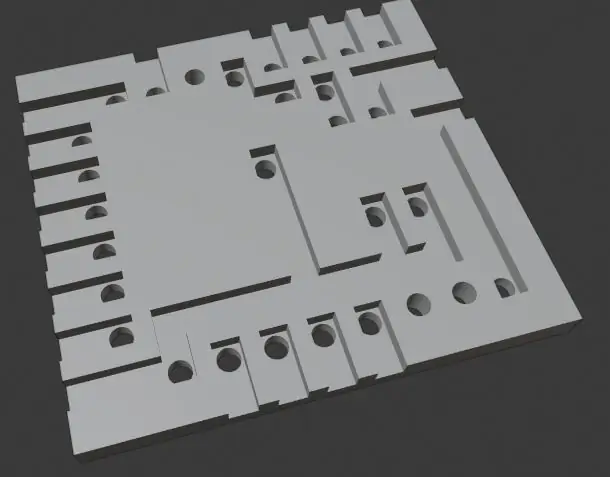
Sobald Sie ein PCB-Design in Papierform haben, sollten Sie es in einer 3D-Modellierungssoftware realistischer gestalten. Dadurch wird Ihre Datei auch für Ihren 3D-Drucker vorbereitet. So mache ich es in Blender:
- Erstellen Sie ein ebenes Netz und fügen Sie Ihr PCB-Designbild darüber hinzu. Stellen Sie sicher, dass es maßstabsgetreu ist und die Abmessungen realistisch sind, da dies als "Pauspapier" dient.
-
Erstellen Sie vereinfachte Komponenten und achten Sie dabei besonders auf die genaue Position und Größe der PINS, die mit Ihrer Leiterplatte verbunden sind. Holen Sie sich die Herstellerspezifikationen online oder messen Sie sie selbst, um sie genau genug zu erhalten. Beachten Sie einige Standarddims, die Sie als Referenz verwenden können:
- Für Bretter verwenden Sie Flugzeuge. Für eine einseitige Leiterplatte verwende ich eine Dicke von 1,5 mm, da ich beim Drucken keine guten Details erhalten habe (es liegt auch an Ihren Druckereinstellungen und -funktionen, aber dazu kommen wir später). Für eine doppelseitige Leiterplatte habe ich 2,5 mm Dicke verwendet.
-
Verwenden Sie für Stifte Zylinder mit einem Mindestdurchmesser von 1 mm, damit sie vom Drucker erfasst werden.
- Verwenden Sie für Kanäle Würfel mit einer Breite von mindestens 1,2 mm. Sie werden nur Gesichter extrudieren, um Ihre Kanäle zu erhalten.
- Lokalisieren Sie Ihre Komponenten gemäß Ihrem PCB-Design. Wenn Ihre Komponenten realistisch genug sind, können Sie dies verwenden, um Kollisionen zu überprüfen, aber immer zusätzlichen Platz um jedes Element herum lassen.
- Verfolgen Sie Ihren Stromkreis. Platzieren Sie ein Würfelnetz an der Stelle des ersten Stifts. Extrudieren Sie dann im Bearbeitungsmodus die Flächen in einer geraden Linie, die dem Design folgt. Auch hier halten Sie es einfach, verwenden Sie 90º-Linien und verwenden Sie so viele Kanäle, wie Sie möchten. Lassen Sie außerdem einen Abstand von mindestens 0,8 mm zwischen den Wänden zu, da sie sonst beim Drucken übersehen werden. Bild 1 unten zeigt einige geänderte Routen nach der Modellierung mit realen Abmessungen, da die ideale Route zu dünn war, um möglich zu sein.
- Erstellen Sie Ihre Leiterplatte, indem Sie einen flachen Würfel hinzufügen (dimmt wie oben).
- Gravieren Sie Ihre Kanäle und Löcher auf der Platine, indem Sie Ihrem PCB-Objekt boolesche Modifikatoren hinzufügen. Dadurch wird der Teil des Boards abgeschnitten, der das Zielobjekt des booleschen Modifikators schneidet.
Bilder 3 und 4 zeigen das Endergebnis für das ESP8266 Board (3D-Modell in Bild 2).
Danach sollten Sie einen 3D-Druck Ihrer Leiterplatte sehen.
Der letzte Schritt besteht darin, das Modell ordnungsgemäß zu exportieren.
- Stellen Sie sicher, dass alle Flächen nach außen zeigen ("Bearbeitungsmodus - Alle auswählen" und dann "Netz - Normalen - Außen neu berechnen").
- Stellen Sie sicher, dass es sich um einzelne Flächen handelt ("Edit Mode - Select All" Then "Edge - Edge Split").--Wenn Sie diese beiden Schritte auslassen, finden Sie möglicherweise fehlende Details in Ihrer Slicer-Software.--
- Exportieren Sie als. STL ("Nur Auswahl", um nur die endgültige Leiterplatte zu exportieren und "Szeneneinheiten", um den Maßstab der Dinge beizubehalten).
Schritt 3: Slicer-Software
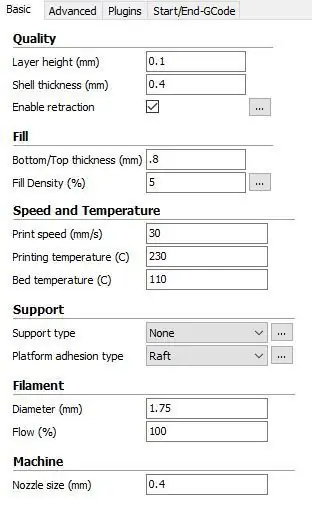
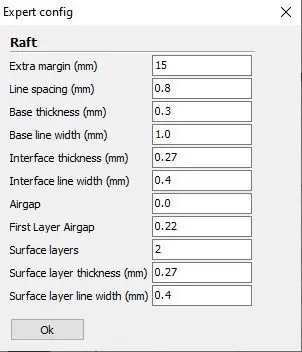
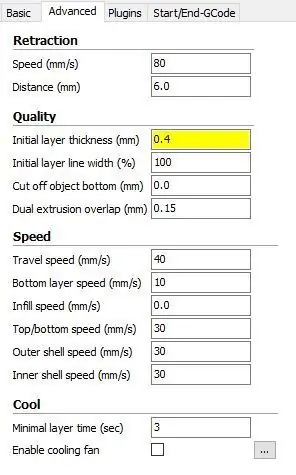
3D-Drucker stellen normalerweise eine "Slicer"-Software bereit, um die 3D-Modelle (in.stl oder anderen Formaten) zu verarbeiten und die erforderliche Route zum Drucken zu berechnen (normalerweise im.gcode-Format). Ich habe einen Creality Ender 3 und bin nicht vom bereitgestellten Creality Slicer gewechselt, aber Sie können diese Einstellungen auf jede andere Software anwenden.
Ich widme einen ganzen Abschnitt den Slicer-Einstellungen, da sie beim Drucken von ABS sehr wichtig sind, was aufgrund von Verziehen, Schrumpfen und Rissen ziemlich schwierig ist. Das Drucken einer Leiterplatte liegt aufgrund der erforderlichen Präzision ebenfalls an der Grenze von Standard-3D-Druckern.
Im Folgenden teile ich die Einstellungen, die ich auf dem Creality Slicer für den ABS-Detaildruck von PCBs verwende. Sie unterscheiden sich von den Standardeinstellungen in:
- Dünne Wände und Schichten (um genügend Details bereitzustellen - dies erfordert möglicherweise ein paar Iterationen für Ihr gewünschtes Ergebnis, es sei denn, Sie sind mit meinen Einstellungen zufrieden).
- Verwenden Sie ein Floß. Der Schlüssel befindet sich auf der Basis, worauf Sie besonders aufpassen sollten. (Ich erlaube einen Versatz von 10 mm vom Modell, um zu vermeiden, dass sich minimale Verwerfungen auf den Druck auswirken). Außerdem gibt es keine Trennungen zwischen den Raft-Linien, um eine gute solide Basis zu erzielen. Wenn Sie Ihre Basis richtig machen, ist alles fertig. Wenn Sie sehen, dass sich Ecken in Ihrer Basis falten, sind Sie sicherlich dem Untergang geweiht.
- Langsame Geschwindigkeit. Ich verwende etwa 1/4 der Standardgeschwindigkeit (dies ermöglicht eine gute Filamentverlegung und damit ein Kleben und die Gesamtqualität).
- ABS-Temperaturen (Bett: 110 °C, Düse: 230 °C)
- Lüfter deaktiviert (empfohlen, um die Temperatur für ABS konstant zu halten).
Schritt 4: Drucken
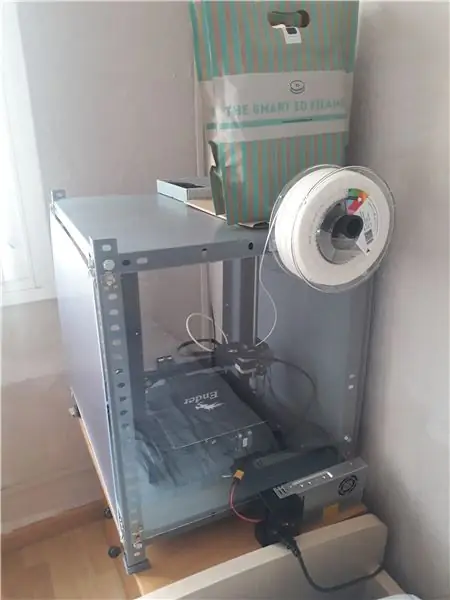
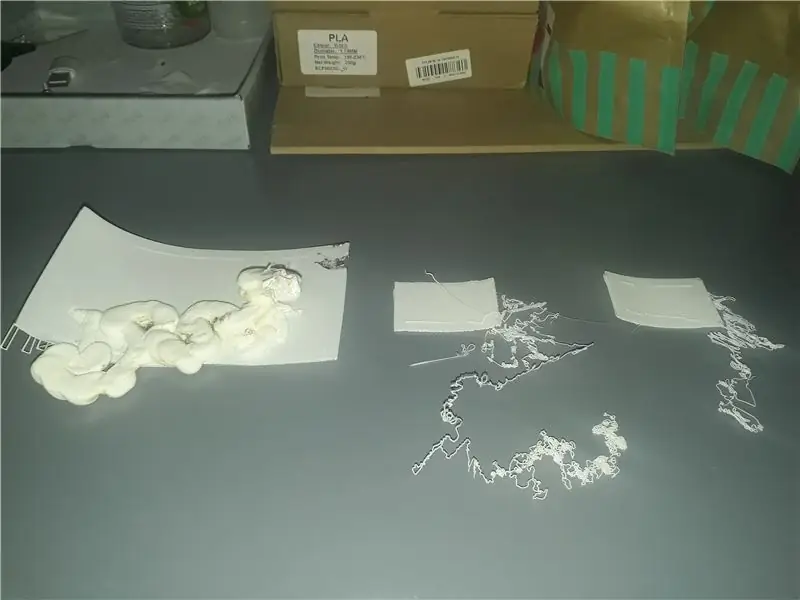
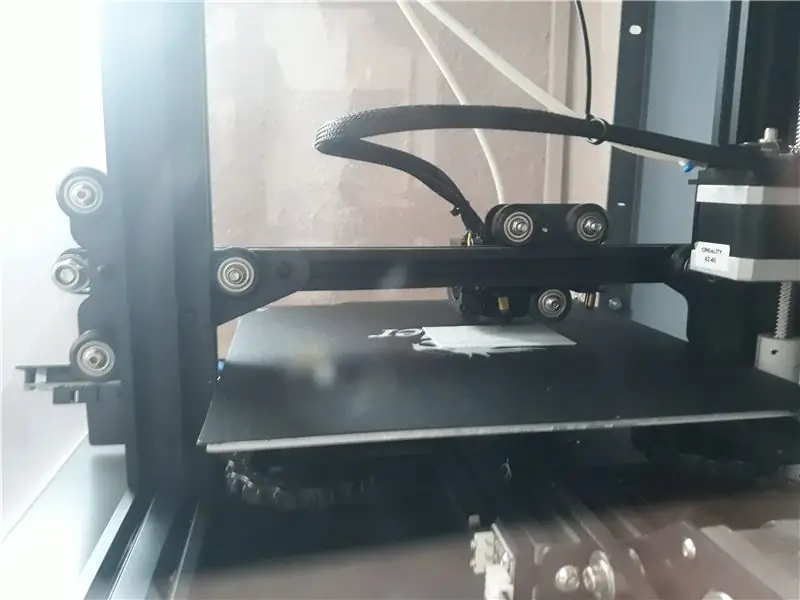
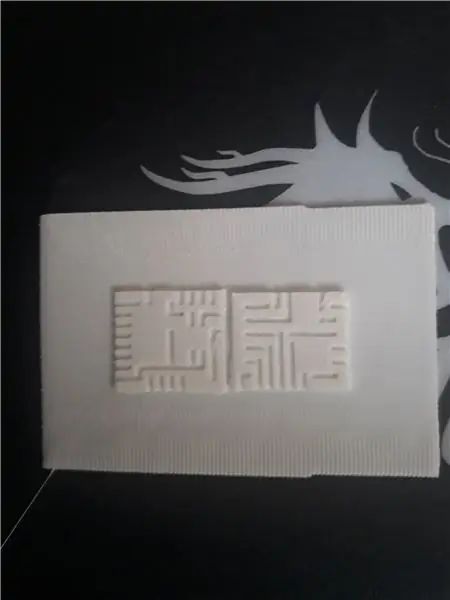
Senden Sie schließlich Ihren.gcode an Ihren Drucker und lassen Sie Ihre Leiterplatte herstellen. Einige Tipps, die Sie befolgen sollten:
- Umhüllen Sie Ihren 3D-Drucker. Ein Gehäuse hält Ihre Temperatur viel stabiler, was eine starke Voraussetzung für den ABS-Druck ist. Stellen Sie sicher, dass Sie die CPU und das Netzteil sowie Ihr Filament außerhalb des Gehäuses aufbewahren. Wenn Sie es schaffen, ABS ohne Gehäuse zu drucken, teilen Sie bitte Ihren Trick, da er mich verrückt gemacht hat.
- Heizen Sie Ihren Drucker eine Weile vor. Auf PLA können Sie sofort drucken, aber mit ABS empfehle ich, mit ABS-Einstellungen (Bett: 110 °C, Düse: 230 °C) 10-15 Minuten vorzuheizen, damit Sie die richtige Atmosphäre schaffen, bevor Sie mit dem Drucken beginnen können.
- Drucken Sie langsam, aber sicher. Wie bereits erwähnt, habe ich die Standarddruckgeschwindigkeit in der Konfigurationsdatei auf 1/4 reduziert. Dies erweist sich als langsam genug, um ein gutes Ergebnis zu erzielen, aber Sie können die Druckgeschwindigkeit während des Druckens steuern, indem Sie die Vorschubgeschwindigkeit regulieren, wenn Sie sie noch ein wenig optimieren möchten. Beachten Sie jedoch, dass hohe Geschwindigkeiten zu sehr plötzlichen Bewegungen führen, die das Filament nicht effektiv verlegen oder mit dem Netz kollidieren und es lösen können.
- Bauen Sie eine gute Grundlage. Der Schlüssel zu ABS besteht darin, eine gut befestigte Basis zu erreichen. Wenn die Basis versagt und sich löst, ist das Modell weg (siehe einige katastrophale Versuche unten). Mit den obigen Tipps (Einhüllen, Vorheizen und langsame Geschwindigkeit) sollten Sie eine gute Basis und ein gutes Finish erhalten. Aber im Gegensatz zu PLA, das ich stundenlang unbeaufsichtigt lasse, braucht ABS mehr Aufmerksamkeit.
- Seien Sie wachsam, besonders am Anfang. Um das Obige zu wiederholen, ist der Schlüssel die Basis. Achten Sie darauf, dass die erste Außenkontur gut verlegt ist. Dadurch wird die restliche Haftung der ersten Schicht vorangetrieben. Manchmal klebt das Filament nicht sofort oder wird von seiner Position gezogen. Sie sollten dies früh genug erkennen, um eine eventuelle Nivellierung oder Reinigung der Grundplatte zu korrigieren. Achten Sie immer auf Verwerfungen, wenn Sie sehen, dass Ecken ansteigen, werden sie wahrscheinlich die gesamte Basis lösen und den gesamten Druck verderben. Selbst wenn die Basis an Ort und Stelle bleibt, wird diese Ecke durch Verziehen verformt.
Schritt 5: Draht und Lötzinn
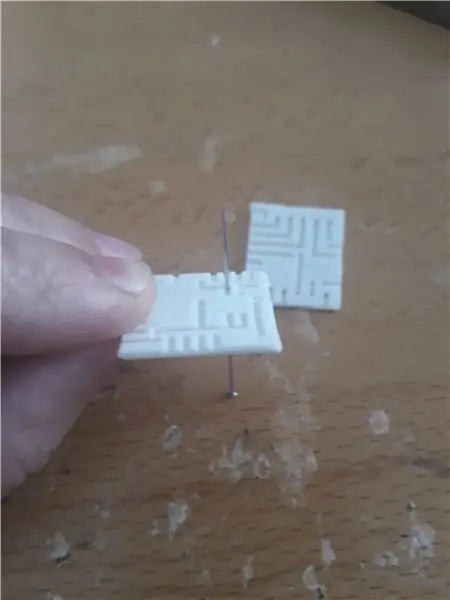
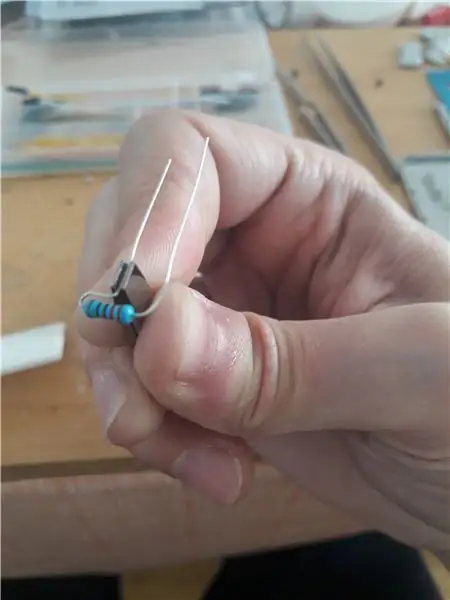
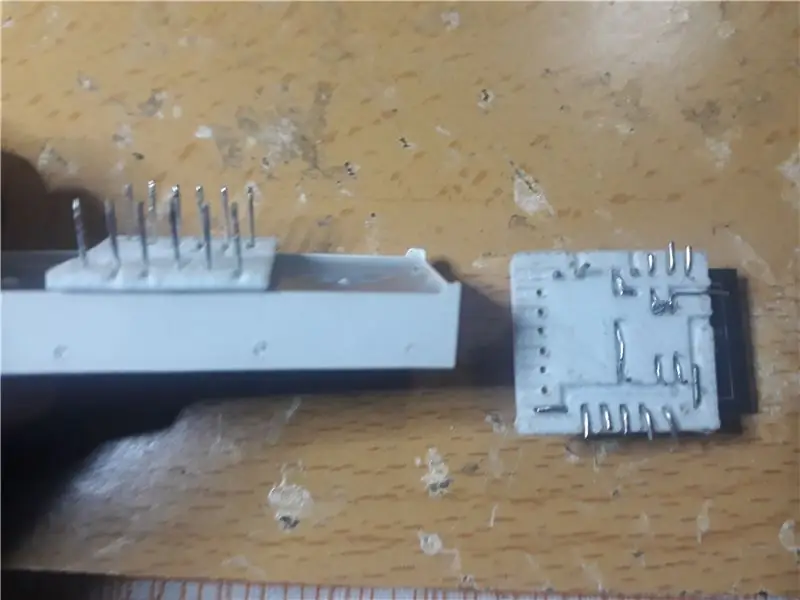
Jetzt ist es an der Zeit, alles an Ort und Stelle zu bringen:
- Überprüfen Sie die Oberfläche der Kanäle und Löcher. Speziell Löcher werden vom Drucker übersehen oder überlagert. Verwenden Sie eine Nähnadel, wenn Sie einige davon wieder öffnen müssen. Wenn Sie aufgrund von Verformungen keinen flachen Druck erhalten oder nicht die erwarteten Details erhalten haben, überprüfen Sie natürlich Ihre Druckereinstellungen oder sogar Ihr 3D-Modell auf die Abmessungen.
- Platzieren Sie Ihre Komponenten. Module, Widerstände, Kondensatoren oder LEDs mit eigenen Pins können problemlos eingesetzt werden. Sie können ihren eigenen Draht leicht biegen, um ihn in die Kanäle zu bekommen, damit es später einfacher ist, sie zu binden.
- Fügen Sie Draht hinzu und löten Sie. Verwenden Sie alle Pins oder Jumper, die in den Kanal passen, und schneiden Sie sie auf Länge, sodass Sie nur an bestimmten Verbindungspunkten löten müssen. Wir sollten das Ganze nicht löten müssen, obwohl ich dazu neige, es zu tun, wenn die Dinge nicht leuchten. In meinem Fall musste ich alle Pins des ESP8266 verdrahten, und hier war es der Schlüssel zu haben gute Lötkenntnisse (was ich nicht tue). Der Rest des Boards war ziemlich einfach zu tun.
Schritt 6: Testen Sie Ihr Board
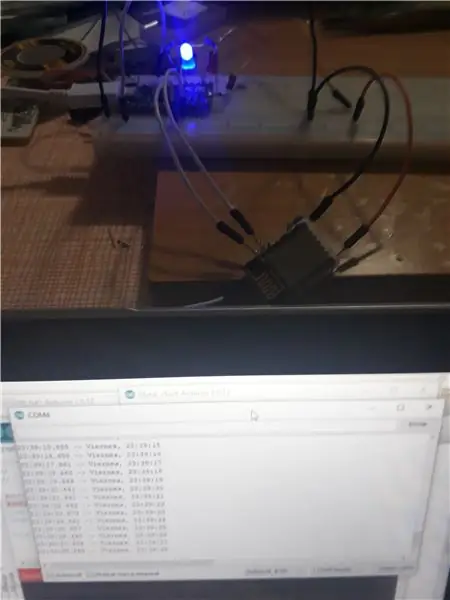
Wenn Sie sicher sind, dass Sie alles richtig gemacht haben, schließen Sie es an.
Für das Prototyping verwende ich den ESP8266 auf der seriellen Verbindung von Teensy 4.
Während der Tests auf dem Bare Board habe ich ein Programm geladen, das die lokale Zeit über WLAN geladen hat. Wie Sie sehen, hat alles gut funktioniert. Ich hoffe, Sie hatten auch mit dieser Technik ein gutes Ergebnis.
Empfohlen:
3D-gedruckte Handprothese in 4 Schritten
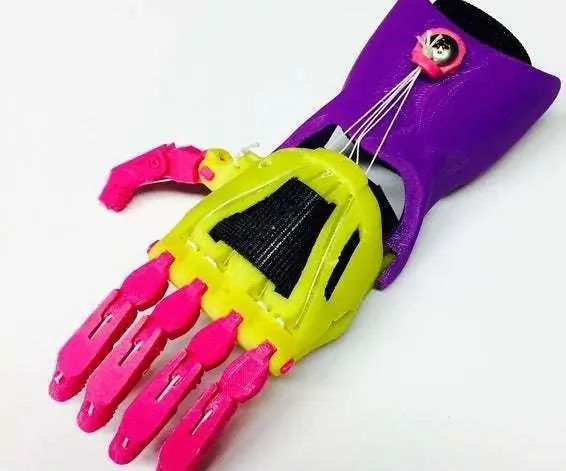
3D-gedruckte Handprothese in 4 Schritten!: Dieses Projekt ist eine Handprothese, die von mir gedruckt wurde. Ich suche mehr Wissen über Prothetik und 3D-Druck. Obwohl dies nicht das beste Projekt ist, ist es eine großartige Möglichkeit, praktische Erfahrungen zu sammeln und zu lernen, wie man
3D gedruckte personalisierte USB-Hüllen - in Details: 4 Schritte
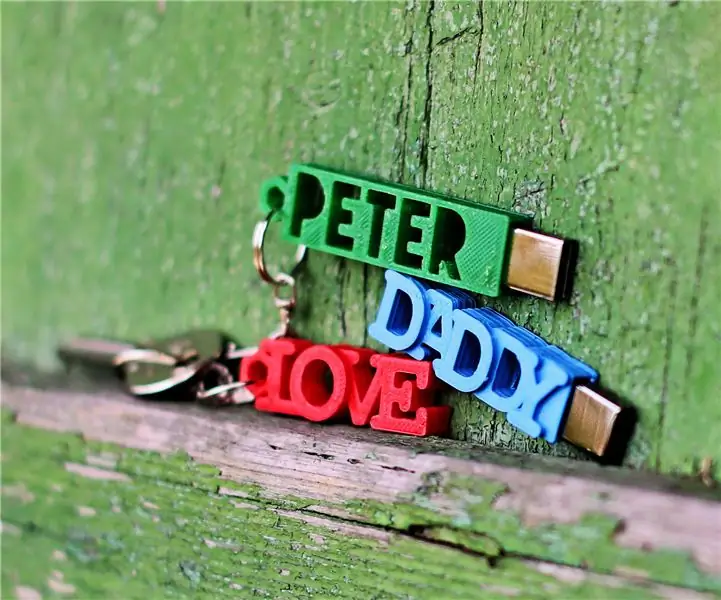
3D-gedruckte personalisierte USB-Hüllen - im Detail: Hallo, mein Name ist Emese. Ich habe die https://customflashdrive.co.uk/3d-print-your-own-Site erstellt. Dies ist ein Ort, an dem Sie eine 3D-gedruckte USB-Hülle personalisieren können. Die Personalisierung einer 3D-gedruckten USB-Hülle ist einfach: Sie fügen Ihren eigenen Text mit bis zu 10 Zeichen hinzu und wählen