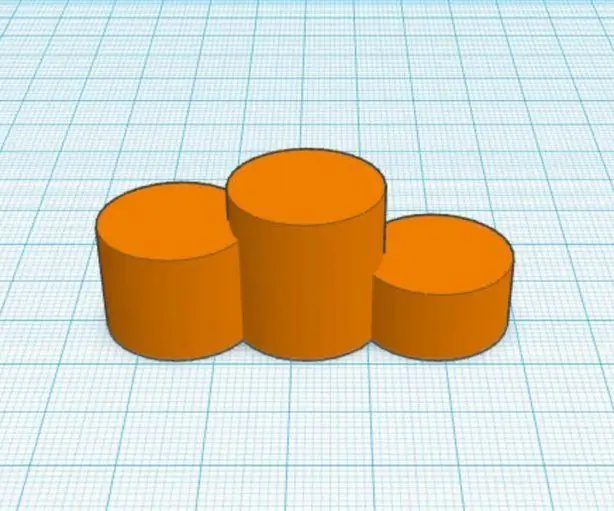
Inhaltsverzeichnis:
- Schritt 1: Grundlagen von Flüssigkristallanzeigen
- Schritt 2: GreenPAK Design Basic Blockschaltbild
- Schritt 3: Stromaufnahme entwerfen
- Schritt 4: GreenPAK-Geräteschema
- Schritt 5: I²C-Schnittstelle
- Schritt 6: Ausgangssegmenttreiber
- Schritt 7: Interner Oszillator und Backplane Clock Source Control
- Schritt 8: Backplane-Taktausgang oder Segment 15-Ausgangspin-Steuerung
- Schritt 9: LCD-System-Prototyp
- Schritt 10: I²C-Befehle für die LCD-Steuerung
- Schritt 11: I²C-Befehle für LCD-Test
- Schritt 12: Testergebnisse
2025 Autor: John Day | [email protected]. Zuletzt bearbeitet: 2025-06-01 06:08
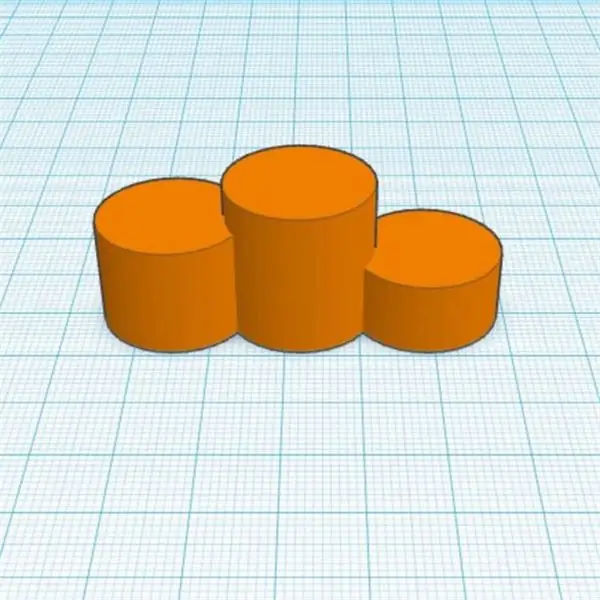
Flüssigkristallanzeigen (LCD) werden wegen ihrer guten visuellen Eigenschaften, ihrer geringen Kosten und ihres geringen Stromverbrauchs häufig für kommerzielle und industrielle Anwendungen verwendet. Diese Eigenschaften machen das LCD zur Standardlösung für batteriebetriebene Geräte wie tragbare Instrumente, Taschenrechner, Uhren, Radios usw.
Um jedoch richtig zu steuern, was das LCD anzeigt, muss der elektronische Treiber des LCD geeignete Spannungswellenformen an den LCD-Pins erzeugen. Die Wellenformen sollten von Natur aus Wechselstrom (Wechselstrom) sein, da Gleichspannungen (Gleichstrom) das Gerät dauerhaft beschädigen. Der geeignete Treiber würde diese Signale bei minimalem Stromverbrauch an das LCD liefern.
Es gibt zwei Arten von LCDs, die statische mit nur einer Backplane und einem Pin für die individuelle Segmentsteuerung und die Multiplexed mit mehreren Backplanes und mehreren angeschlossenen Segmenten für jeden Pin.
Dieses Instructable präsentiert das Design eines statischen LCD-Treibers mit SLG46537V GreenPAK™-Gerät. Der entwickelte LCD-Treiber würde bis zu 15 LCD-Segmente ansteuern, wobei er einige Mikroampere Strom aus der Stromversorgung verwendet und eine I²C-Schnittstelle zur Steuerung bietet.
In den folgenden Abschnitten wird angezeigt:
● Grundwissen über LCDs;
● das Design des SLG46537V GreenPAK LCD-Treibers im Detail;
● Wie man ein statisches LCD mit sieben Segmenten und vier Ziffern mit zwei GreenPAK-Geräten ansteuert.
Im Folgenden haben wir die erforderlichen Schritte beschrieben, um zu verstehen, wie die Lösung programmiert wurde, um den statischen LCD-Treiber mit I²C-Schnittstelle zu erstellen. Wenn Sie jedoch nur das Ergebnis der Programmierung erhalten möchten, laden Sie die GreenPAK-Software herunter, um die bereits fertige GreenPAK-Designdatei anzuzeigen. Schließen Sie das GreenPAK Development Kit an Ihren Computer an und klicken Sie auf Programm, um den statischen LCD-Treiber mit I²C-Schnittstelle zu erstellen.
Schritt 1: Grundlagen von Flüssigkristallanzeigen
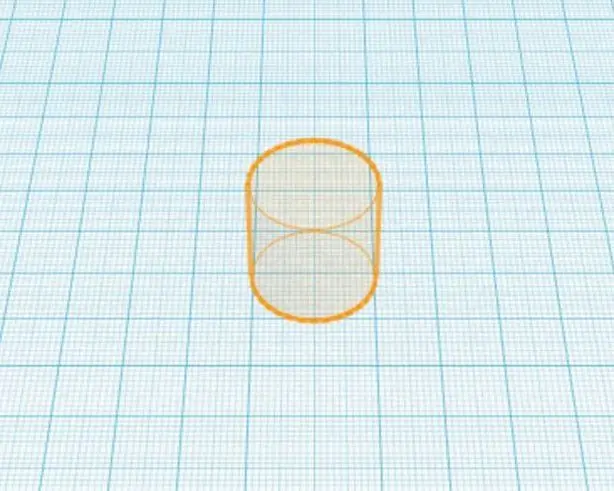
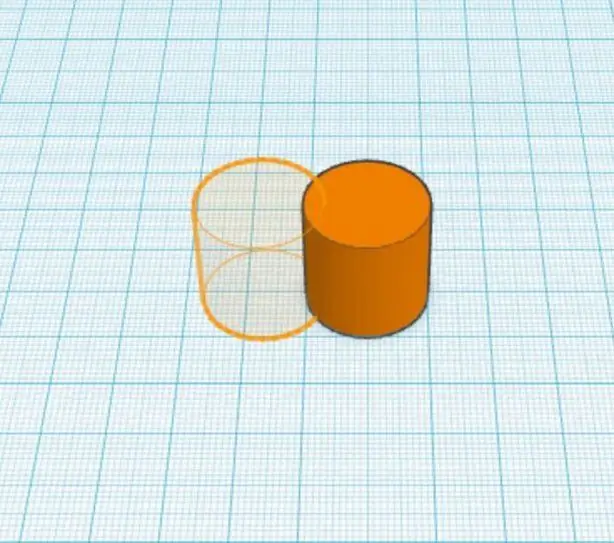
Liquid Crystal Displays (LCD) sind eine Technologie, die kein Licht emittiert, sondern nur den Durchgang einer externen Lichtquelle steuert. Diese externe Lichtquelle könnte das verfügbare Umgebungslicht beim reflektierenden Displaytyp oder das Licht von einer Hintergrundbeleuchtungs-LED oder Lampe beim transmissiven Displaytyp sein. LCDs bestehen aus zwei Glasplatten (oben und unten), einer dünnen Flüssigkristallschicht (LC) dazwischen und zwei Lichtpolarisatoren (Application Note AN-001 - Basics of LCD Technology, Hitachi, Application Note AN-005 - Display Modes, Hitachi). Der Polarisator ist ein Lichtfilter für das leichte elektromagnetische Feld. Nur die Lichtkomponenten in der richtigen elektromagnetischen Feldrichtung passieren den Polarisator, während die anderen Komponenten blockiert werden.
Der Flüssigkristall ist ein organisches Material, das das elektromagnetische Feld des Lichts um 90 Grad oder mehr dreht. Wenn jedoch ein elektrisches Feld an das LC angelegt wird, dreht es das Licht nicht mehr. Durch das Hinzufügen von transparenten Elektroden im oberen und unteren Displayglas ist es möglich zu kontrollieren, wann das Licht durchgeht und wann nicht, mit einer externen Quelle des elektrischen Feldes. Abbildung 1 (siehe Anwendungshinweis AN-001 - Grundlagen der LCD-Technologie, Hitachi) oben veranschaulicht diese Betriebssteuerung. In Abbildung 1 ist das Display dunkel, wenn kein elektrisches Feld vorhanden ist. Dies liegt daran, dass beide Polarisatoren das Licht in die gleiche Richtung filtern. Wenn die Polarisatoren orthogonal sind, ist die Anzeige dunkel, wenn das elektrische Feld vorhanden ist. Dies ist die häufigste Situation bei reflektierenden Displays.
Das minimale elektrische Feld oder die minimale Spannung, um das LCD zu steuern, wird als EIN-Schwellenwert bezeichnet. Der LC wird nur durch die Spannung beeinflusst, und im LC-Material fließt kaum Strom. Die Elektroden im LCD bilden eine kleine Kapazität und dies ist die einzige Last für einen Treiber. Dies ist der Grund dafür, dass ein LCD ein Gerät mit geringem Stromverbrauch ist, um visuelle Informationen anzuzeigen.
Es ist jedoch wichtig zu beachten, dass das LCD nicht zu lange mit einer Gleichstromquelle (DC) betrieben werden kann. Das Anlegen einer Gleichspannung führt zu chemischen Reaktionen im LC-Material, die es dauerhaft beschädigen (Application Note AN-001 - Basics of LCD Technology, Hitachi). Die Lösung besteht darin, an LCDs-Elektroden eine Wechselspannung (AC) anzulegen.
Bei statischen LCDs wird eine Rückwandelektrode in ein Glas eingebaut und einzelne LCD-Segmente oder Pixel werden in das andere Glas eingesetzt. Dies ist einer der einfachsten LCD-Typen und derjenige mit dem besten Kontrastverhältnis. Diese Art der Anzeige erfordert jedoch in der Regel zu viele Pins, um jedes einzelne Segment zu steuern.
Im Allgemeinen erzeugt ein Treibercontroller zusammen ein Rechteckwellen-Taktsignal für die Backplane und ein Taktsignal für die Segmente in der Frontplane. Wenn der Backplane-Takt mit dem Segmenttakt gleichphasig ist, ist die Effektivwertspannung (RMS) zwischen beiden Ebenen null und das Segment ist transparent. Andernfalls wird das Segment dunkel, wenn die RMS-Spannung höher als der LCD-EIN-Schwellenwert ist. Die Wellenformen für Backplane, On- und Off-Segment sind in Abbildung 2 dargestellt. Wie in der Abbildung zu sehen ist, ist das ON-Segment in Bezug auf das Backplane-Signal phasenverschoben. Das Off-Segment ist in Bezug auf das Backplane-Signal gleichphasig. Die angelegte Spannung könnte für kostengünstige Displays mit geringem Stromverbrauch zwischen 3 und 5 Volt liegen.
Das Taktsignal für die Rückwand und die Segmente von LCDs liegt normalerweise im Bereich von 30 bis 100 Hz, der Mindestfrequenz, um einen visuellen Flimmereffekt auf dem LCD zu vermeiden. Höhere Frequenzen werden vermieden, um die Leistungsaufnahme des Gesamtsystems zu reduzieren. Das aus LCD und Treibern bestehende System würde wenig Strom in der Größenordnung von Mikroampere verbrauchen. Dadurch sind sie perfekt für Anwendungen mit geringer Leistung und Batteriestromversorgung geeignet.
In den folgenden Abschnitten wird das Design eines statischen LCD-Treibers mit GreenPAK-Baustein, der das Backplane-Taktsignal und das Einzelsegment-Taktsignal für ein kommerzielles LCD erzeugen kann, detailliert vorgestellt.
Schritt 2: GreenPAK Design Basic Blockschaltbild
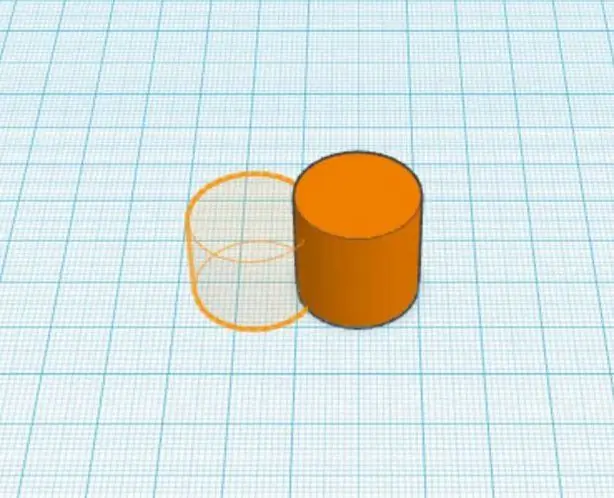
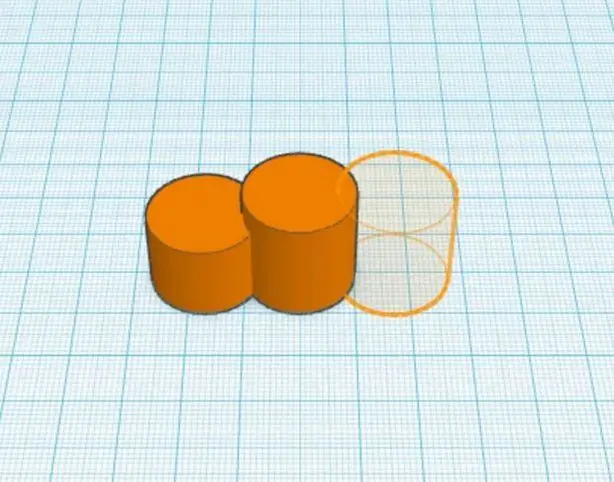
Ein Blockdiagramm, das das GreenPAK-Design veranschaulicht, ist in Abbildung 3 dargestellt. Die grundlegenden Blöcke des Designs sind die I²C-Schnittstelle, der Ausgangssegmenttreiber, der interne Oszillator und der Backplane-Taktquellenselektor.
Der I²C-Schnittstellenblock steuert jeden einzelnen Segmentausgang und die Backplane-Taktquelle des LCD. Der I²C-Schnittstellenblock ist der einzige Systemeingang für die Segmentausgangssteuerung.
Bei gesetzter interner Segmentsteuerleitung (High-Pegel) ist das jeweilige LCD-Segment dunkel opak. Beim Rücksetzen der internen Segmentsteuerleitung (Low-Pegel) ist das jeweilige LCD-Segment transparent.
Jede interne Segmentsteuerleitung ist mit einem Ausgangstreiber verbunden. Der Ausgangssegmenttreiberblock erzeugt ein gleichphasiges Taktsignal mit Bezug auf den Backplane-Takt für transparente Segmente. Bei dunklen Segmenten ist dieses Signal in Bezug auf den Backplane-Takt phasenverschoben.
Die Taktquelle der Backplane wird auch mit I²C-Schnittstelle ausgewählt. Wenn die interne Backplane-Taktquelle ausgewählt ist, wird der interne Oszillator eingeschaltet. Der interne Oszillator erzeugt eine Taktfrequenz von 48Hz. Dieses Signal wird vom Ausgangssegmenttreiberblock verwendet und an den Backplane-Taktausgangspin (GreenPAK-Pin 20) adressiert.
Wenn eine externe Backplane-Taktquelle ausgewählt wird, wird der interne Oszillator ausgeschaltet. Die Referenz des Ausgangssegmenttreibers ist der externe Takteingang der Backplane (GreenPAK-Pin 2). In diesem Fall könnte der Backplane-Taktausgangspin als zusätzliche Segmentsteuerleitung, das Segment OUT15, verwendet werden.
An derselben I²C-Leitung können mehrere GreenPAK-Geräte verwendet werden. Dazu muss jedes Gerät mit einer anderen I²C-Adresse programmiert werden. Auf diese Weise ist es möglich, die Anzahl der angesteuerten LCD-Segmente zu erweitern. Eine Vorrichtung ist konfiguriert, um die Backplane-Taktquelle zu erzeugen, die 14 Segmente treibt, und die anderen sind konfiguriert, um eine externe Backplane-Taktquelle zu verwenden. Jedes zusätzliche Gerät könnte auf diese Weise mehr 15 Segmente ansteuern. Es ist möglich, bis zu 16 Geräte an derselben I²C-Leitung anzuschließen und dann bis zu 239 Segmente eines LCD zu steuern.
In diesem Instructable wird diese Idee verwendet, um 29 Segmente eines LCD mit 2 GreenPAK-Geräten zu steuern. Die Funktionalität der Geräte-Pinbelegung ist in Tabelle 1 zusammengefasst.
Schritt 3: Stromaufnahme entwerfen
Ein wichtiges Anliegen bei diesem Design ist die Stromaufnahme, die so gering wie möglich sein sollte. Der geschätzte Ruhestrom des GreenPAK-Geräts beträgt 0,75 µA für den 3,3-V-Versorgungsbetrieb und 1,12 µA für den 5-V-Versorgungsbetrieb. Die Stromaufnahme des internen Oszillators beträgt 7,6 µA bzw. 8,68 µA bei 3,3 V bzw. 5 V Netzteilbetrieb. Eine signifikante Erhöhung des Stromverbrauchs durch Schaltverluste ist nicht zu erwarten, da dieses Design mit einer niedrigen Taktfrequenz arbeitet. Der geschätzte maximale Stromverbrauch für dieses Design beträgt weniger als 15 µA, wenn der interne Oszillator eingeschaltet ist, und 10 µA, wenn der interne Oszillator ausgeschaltet ist. Der gemessene Stromverbrauch in beiden Situationen wird im Abschnitt Testergebnisse angezeigt.
Schritt 4: GreenPAK-Geräteschema
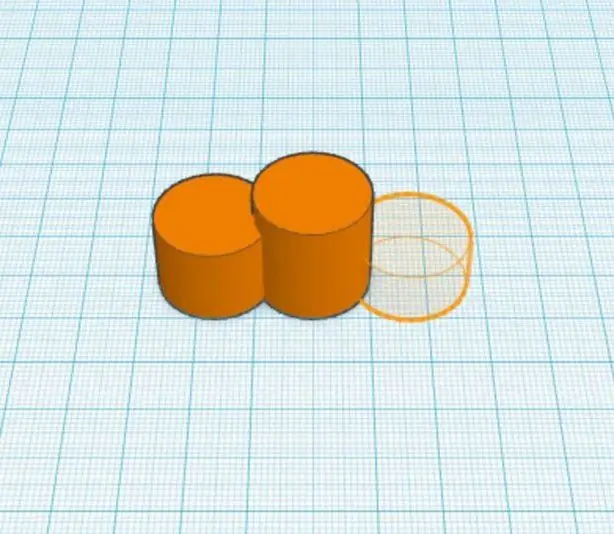
Das in der GreenPAK-Software entworfene Projekt ist in Abbildung 4 dargestellt. Dieses Schema wird anhand der grundlegenden Blockschaltbilder als Referenz beschrieben.
Schritt 5: I²C-Schnittstelle
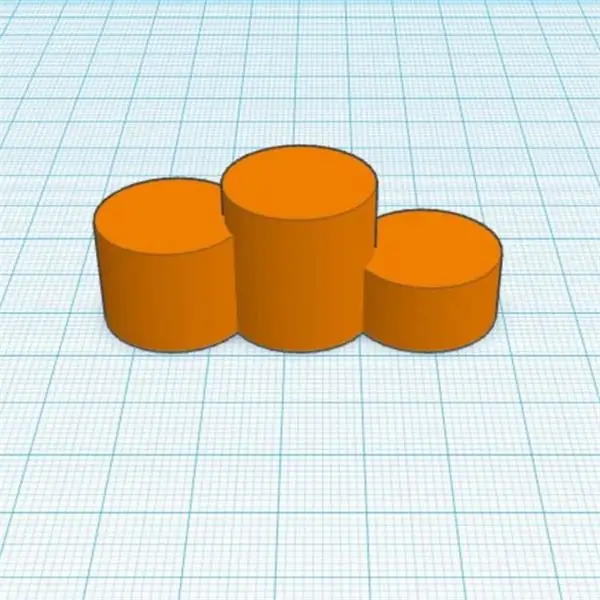
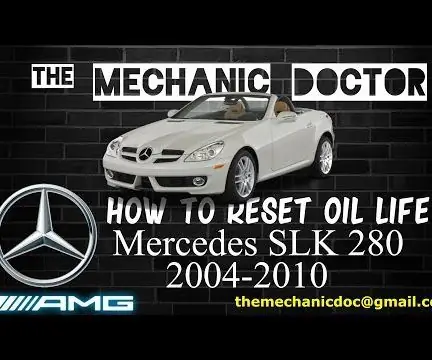
Der I²C-Schnittstellenblock wird als Hauptsteuerblock der Gerätebetriebssteuerung verwendet. Einen genauen Blick auf die Bausteinanschlüsse und konfigurierten Eigenschaften zeigt Abbildung 5.
Dieser Block ist mit PIN 8 und PIN 9 verbunden, das sind I²C SCL- bzw. SDA-Pins. Im Inneren des Geräts bietet der I²C-Block 8 virtuelle Eingänge. Der Anfangswert für jeden virtuellen Eingang wird im Eigenschaftenfenster angezeigt (siehe Abbildung 5). Als Segmentsteuerleitungen werden virtuelle Eingänge von OUT0 bis OUT6 verwendet. Diese Steuerleitungen entsprechen Segmentausgang 1 bis Segmentausgang 7 und sind mit dem Segmentausgangstreiber verbunden. Virtual Input OUT7 wird als Backplane Clock Source Selector Line Control mit dem Netznamen BCKP_SOURCE verwendet. Dieses Netz wird von anderen Blöcken im Design verwendet. Der I²C-Steuercode wird für jeden IC im Projekt mit einem anderen Wert konfiguriert.
8 weitere interne Segmentsteuerleitungen sind im Ausgang der Asynchronous State Machine (ASM) verfügbar, wie in Abbildung 6 oben gezeigt. Die Segmentausgangsleitung 8 (SEG_OUT_8 im Eigenschaftenfenster) bis die Segmentausgangsleitung 15 (SEG_OUT_15) werden vom ASM-Ausgang im Zustand 0 gesteuert. Es gibt keinen Zustandsübergang im ASM-Block, er befindet sich immer im Zustand 0. Die Ausgänge von ASM sind mit Segmentausgangstreibern verbunden.
Die Segmentausgangstreiber erzeugen das Ausgangssignal des Geräts.
Schritt 6: Ausgangssegmenttreiber
Der Ausgangssegmenttreiber ist im Wesentlichen eine Lookup-Tabelle (LUT), die als XOR-Logik-Port konfiguriert ist. Für jedes Ausgangssegment muss es ein XOR-Port sein, der mit der Segmentsteuerleitung und dem Backplane-Takt (BCKP_CLOCK) verbunden ist. Der XOR-Port ist dafür verantwortlich, das phasengleiche und phasenverschobene Signal zum Ausgangssegment zu erzeugen. Wenn sich die Segmentsteuerleitung auf einem hohen Pegel befindet, invertiert der Ausgang des XOR-Ports das Backplane-Taktsignal und erzeugt ein phasenverschobenes Signal zum Segment-Pin. Die Spannungsdifferenz zwischen LCD-Backplane und LCD-Segment setzt in diesem Fall das LCD-Segment als dunkles Segment. Wenn sich die Segmentsteuerleitung auf einem niedrigen Pegel befindet, folgt der Ausgang des XOR-Ports dem Backplane-Taktsignal und erzeugt dann ein phasengleiches Signal zum Segment-Pin. Da in diesem Fall keine Spannung zwischen LCD-Backplane und Segment angelegt wird, ist das Segment lichtdurchlässig.
Schritt 7: Interner Oszillator und Backplane Clock Source Control
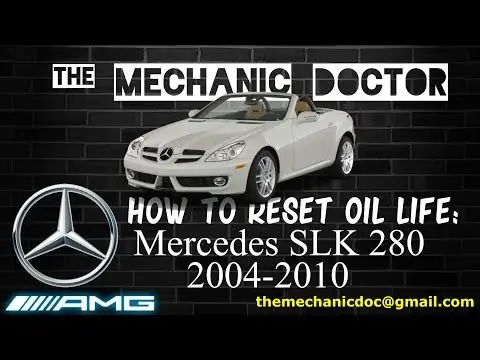
Der interne Oszillator wird verwendet, wenn das Signal BCKP_CLOCK von der I²C-Schnittstelle auf High-Pegel gesetzt wird. Eine Nahaufnahme des Taktquellen-Steuerungsdiagramms ist in Abbildung 7 oben gezeigt.
Der Oszillator ist als 25 kHz RC-Frequenz konfiguriert, wobei der höchste verfügbare Ausgangsdivisor an Oszillator OUT0 (8/64) verfügbar ist. Die gesamte Konfiguration ist im Eigenschaftsfenster in Abbildung 7 zu sehen. Auf diese Weise erzeugt der interne Oszillator eine Taktfrequenz von 48 Hz.
Der Oszillator ist nur aktiv, wenn das Signal BCKP_SOURCE zusammen mit dem POR-Signal auf einem hohen Pegel ist. Diese Steuerung erfolgt durch Verbinden dieser beiden Signale mit dem NAND-Port der 4-L1-LUT. Der Ausgang des NAND wird dann mit dem Eingang des Oszillator-Power-Down-Steuerpins verbunden.
Das Signal BCKP_SOURCE steuert den mit 3-L10-LUT aufgebauten MUX. Wenn das Signal BCKP_SOURCE auf einem niedrigen Pegel ist, kommt die Taktquelle der Rückwandplatine von PIN2. Wenn dieses Signal auf einem hohen Pegel liegt, kommt die Taktquelle der Backplane vom internen Oszillator.
Schritt 8: Backplane-Taktausgang oder Segment 15-Ausgangspin-Steuerung
Pin 20 hat in diesem Design eine Doppelfunktion, die von der gewählten Backplane-Taktquelle abhängt. Der Betrieb dieses Pins wird mit einer 4-Eingangs-LUT gesteuert, wie in Abbildung 8 gezeigt. Bei einer 4-Bit-LUT ist es möglich, den Betrieb des XOR-Ports einem Ausgangs-MUX zuzuordnen. Wenn das Signal BCKP_SOURCE auf einem hohen Pegel ist, folgt der LUT-Ausgang dem internen Oszillatortakt. Dann arbeitet Pin 20 als Backplane-Taktausgang. Wenn das Signal BCKP_SOURCE auf einem niedrigen Pegel ist, ist der LUT-Ausgang die XOR-Operation zwischen SEG_OUT_15 vom ASM-Ausgang und dem Backplane-Taktsignal. Die 4-Bit-LUT-Konfiguration für diesen Vorgang ist in Abbildung 8 dargestellt.
Schritt 9: LCD-System-Prototyp

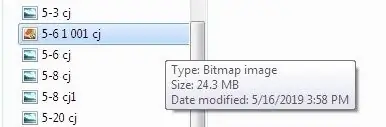
Um die Verwendung der GreenPAK-Designlösung zu demonstrieren, wurde ein Prototyp eines LCD-Systems auf einem Steckbrett montiert. Für den Prototyp wird ein statisches LCD mit sieben Segmenten und vier Ziffern von zwei GreenPAK-Geräten auf einer DIP-Platine angesteuert. Ein Gerät (IC1) verwendet den internen Oszillator, um die LCD-Rückwandplatine anzusteuern, und das andere Gerät (IC2) verwendet dieses Signal als Rückwandplatinen-Eingangsreferenz. Beide ICs werden über die I²C-Schnittstelle von einem STM32F103C8T6-Mikrocontroller (MCU) in einem minimalen Entwicklungsboard gesteuert.
Abbildung 9 zeigt das Schema der Verbindungen zwischen den beiden GreenPAK-ICs, dem LCD-Display und der MCU-Platine. Im Schaltplan steuert das GreenPAK-Gerät mit U1 (IC1)-Referenz die LCD-Stellen eins und zwei (LCD links). Das GreenPAK-Gerät mit U2 (IC2)-Referenz steuert die LCD-Ziffern drei und vier sowie das COL-Segment (LCD rechts). Die Stromversorgung für beide Geräte erfolgt über den Regler im Mikrocontroller-Entwicklungsboard. Für die Strommessung mit einem Multimeter werden zwei abnehmbare Jumper zwischen der Stromversorgung und den VDD-Pins jedes GreenPAK-Geräts hinzugefügt.
Ein Bild des zusammengebauten Prototyps ist in Abbildung 10 dargestellt.
Schritt 10: I²C-Befehle für die LCD-Steuerung
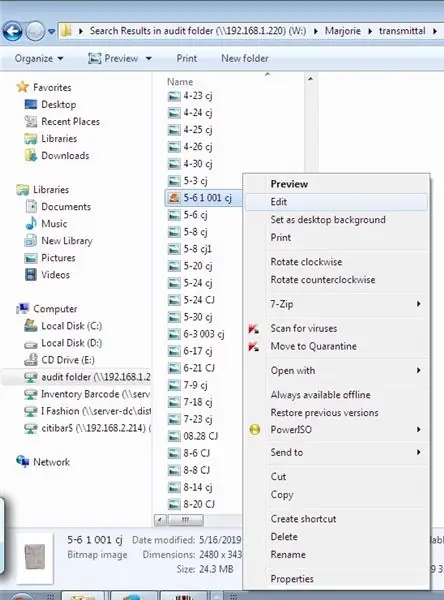

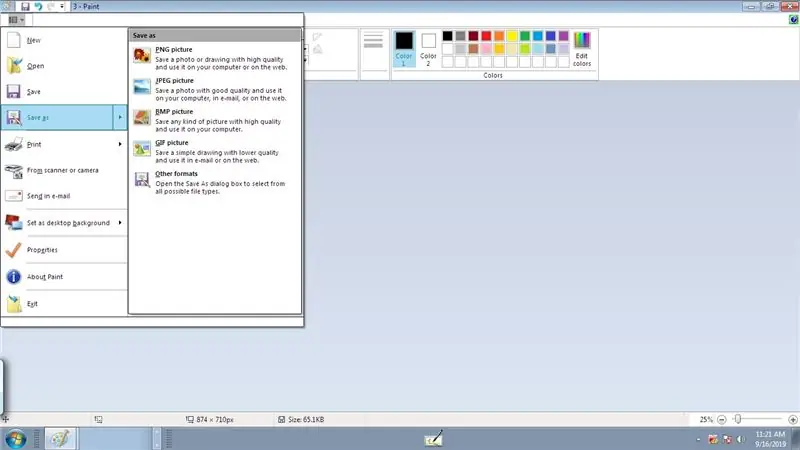
Die beiden GreenPAK-Geräte auf dem Steckbrett sind mit dem gleichen Design programmiert, außer durch den Control-Byte-Wert. Das Steuerbyte von IC1 ist 0 (I²C-Adresse 0x00), während das I²C-Steuerbyte 1 ist (I²C-Adresse 0x10). Die Verbindungen zwischen Anzeigesegmenten und Gerätetreibern sind in der obigen Tabelle zusammengefasst.
Die Anschlüsse wurden so gewählt, um einen übersichtlicheren Schaltplan zu erstellen und die Montage der Steckbrettverbindungen zu vereinfachen.
Die Steuerung des Segmentausgangs erfolgt durch I²C-Schreibbefehle an die virtuellen I²C-Eingänge und die ASM-Ausgangsregister. Wie in der Application Note AN-1090 Simple I²C IO Controllers with SLG46531V (siehe Application Note AN-1090 Simple I²C IO Controllers with SLG46531V, Dialog Semiconductor) beschrieben, ist der I²C-Schreibbefehl wie folgt aufgebaut:
● Starten;
● Kontrollbyte (R/W-Bit ist 0);
● Wortadresse;
● Daten;
● Stoppen.
Alle I²C-Schreibbefehle erfolgen an die Wortadresse 0xF4 (Virtuelle I²C-Eingänge) und 0xD0 (ASM-Ausgang für Zustand 0). Die Befehle zum Schreiben in IC1 und zum Steuern der LCD-Ziffern 1 und 2 sind in Tabelle 3 zusammengefasst. In der Befehlssequenz-Darstellung bezeichnet die offene Klammer „[“das Start-Signal und die geschlossene Klammer „]“das Stopp-Signal.
Die beiden Bytes oben steuern die Segmente der LCD-Ziffer 1 und Ziffer 2 zusammen. Hier besteht der Ansatz darin, für jede Ziffer eine individuelle Nachschlagetabelle (LUT) in der Software zu verwenden, wobei die Segmente in beiden Bytes berücksichtigt werden. Die Bytewerte aus der Lookup-Tabelle sollten mit einer bitweisen ODER-Operation gemischt und dann an den IC gesendet werden. Die Tabelle 4 zeigt die Byte0- und Byte1-Werte für jeden numerischen Wert, der in jede Anzeigestelle geschrieben werden sollte.
Um beispielsweise in Digit 1 die Zahl 3 und in Digit 2 die Zahl 4 zu schreiben, ist Byte0 0xBD (0x8D bitweises OR mit 0xB0) und Byte 1 ist 0x33 (0x30 bitweises OR mit 0x03).
Der Befehl zum Schreiben in IC2 und steuert Digit 3 und 4, sind in Tabelle 5 beschrieben.
Die Steuerlogik der Ziffern 3 und 4 entspricht der Steuerung der Ziffern 1 und 2. Tabelle 6 zeigt die LUT für diese beiden Ziffern.
Der Unterschied in IC2 ist das COL-Segment. Dieses Segment wird von Byte1 gesteuert. Um dieses Segment dunkel einzurichten, sollte eine bitweise ODER-Verknüpfung zwischen dem Byte1 und dem Wert 0x40 durchgeführt werden.
Schritt 11: I²C-Befehle für LCD-Test
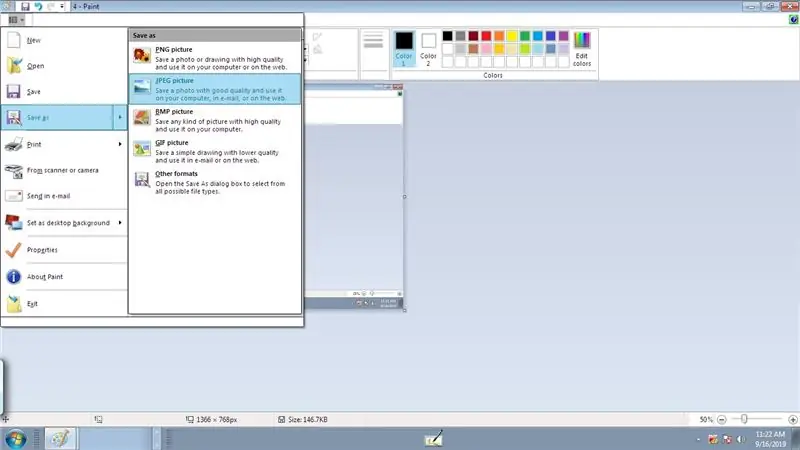
Für den LCD-Test wurde eine Firmware in C-Sprache für das MCU-Board entwickelt. Diese Firmware sendet eine Befehlsfolge an beide ICs auf dem Steckbrett. Der Quellcode für diese Firmware befindet sich im Anhang. Die gesamte Lösung wurde mit Atollic TrueStudio für STM32 9.0.1 IDE entwickelt.
Die Befehlsfolge und die jeweiligen Werte im Display sind in Tabelle 7 oben zusammengefasst.
Schritt 12: Testergebnisse
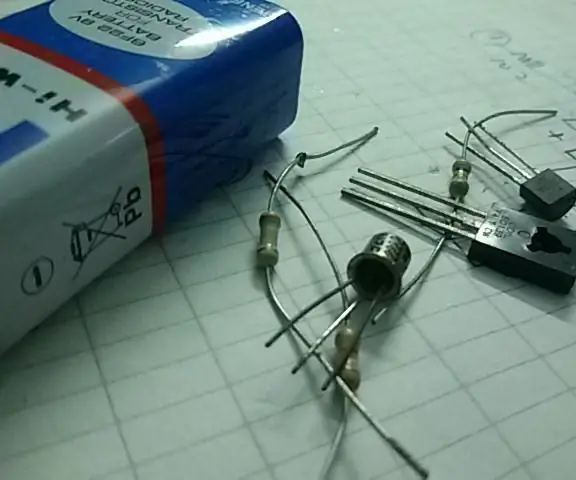
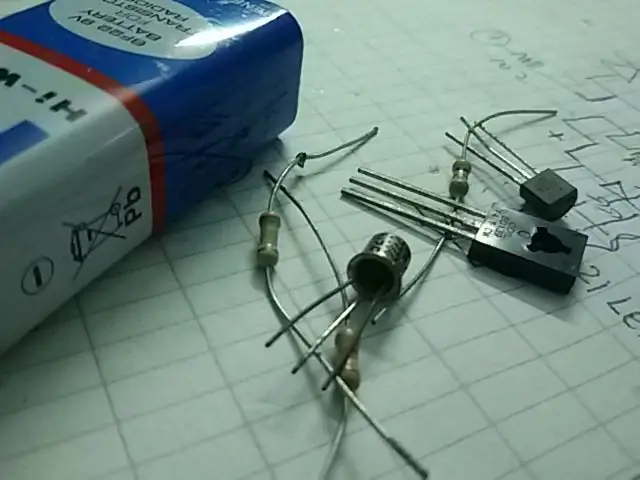
Der Prototypentest besteht darin, die Anzeigewerte nach einem MCU-Befehl zu verifizieren und die Stromsenke jedes ICs während des Betriebs zu messen.
Abbildungen des LCD für jeden Befehlswert sind in Tabelle 8 oben gezeigt.
Die Stromsenke für jedes Gerät wurde mit einem Multimeter im niedrigsten Strombereich von 200 µA gemessen. Bilder des gemessenen Stroms für jedes Gerät während der Inbetriebnahme und im Normalbetrieb sind in Tabelle 9 oben aufgeführt.
Fazit und Ergebnisdiskussion
Das Design eines statischen LCD-Treibers mit geringem Stromverbrauch mit GreenPAK-Gerät wurde vorgestellt. Dieses Design zeigt deutlich eine der größten Eigenschaften der GreenPAK-Geräte: ihren geringen Ruhestrom. Da es sich bei GreenPAK-Geräten um eine hardwarebasierte Lösung handelt, ist es möglich, im Niederfrequenzbetrieb zu arbeiten, in diesem Fall 48 Hz. Eine MCU-basierte Lösung erfordert selbst für periodisch kurze Zeiträume eine höhere Betriebsfrequenz und verbraucht dann mehr Strom. Und beim Vergleich eines GreenPAK-Geräts mit einem CPLD (Complex Programmable Logic Device) wird deutlich, dass ein CPLD normalerweise einen Ruhestrom von mehr als 20 µA hat.
Es ist interessant festzustellen, dass dieses Design leicht modifiziert werden könnte, um es besser an die Anforderungen eines bestimmten Projekts anzupassen. Ein gutes Beispiel ist die Pinbelegung der Segmentsteuerelemente. Sie könnten leicht geändert werden, um gleichzeitig die Leiterplatte und die Softwareentwicklung zu vereinfachen. Dies ist ein interessantes Merkmal, wenn das Gerät mit einem handelsüblichen ASIC (Application Specific Integrated Circuit) verglichen wird. Normalerweise sind ASICs für eine breite Palette von Anwendungen ausgelegt, und es sollte eine anfängliche Softwareroutine geschrieben werden, um den IC vor dem Betrieb richtig zu konfigurieren. Ein konfigurierbares Gerät könnte so ausgelegt sein, dass es nach dem Einschalten betriebsbereit startet. Auf diese Weise ist es möglich, die Softwareentwicklungszeit für die IC-Erstkonfiguration zu verkürzen.
Den Quellcode der Anwendung finden Sie hier in Anhang A.
Empfohlen:
Erstellen Sie eine Raumstation in TinkerCad Codeblock--Einfaches Tutorial: 7 Schritte (mit Bildern)
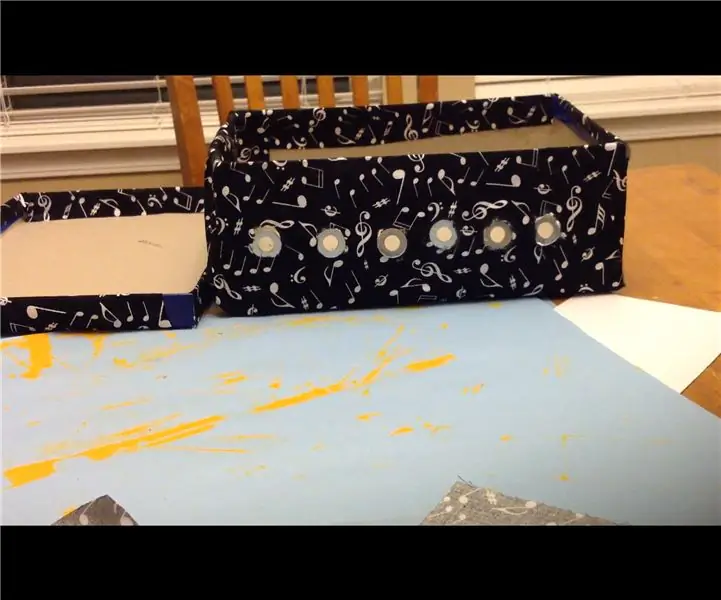
Erstellen Sie eine Raumstation in TinkerCad Codeblock||Einfaches Tutorial: Während der Gedanke, im Weltraum zu leben, wie Science-Fiction erscheinen mag, umkreist die Internationale Raumstation die Erde mit einer Geschwindigkeit von fünf Meilen pro Sekunde, während Sie dies lesen, und umkreist die Erde einmal alle 90 Minuten. In diesem Projekt lernen Sie
So erstellen Sie eine einfache Website mit Notepad – wikiHow
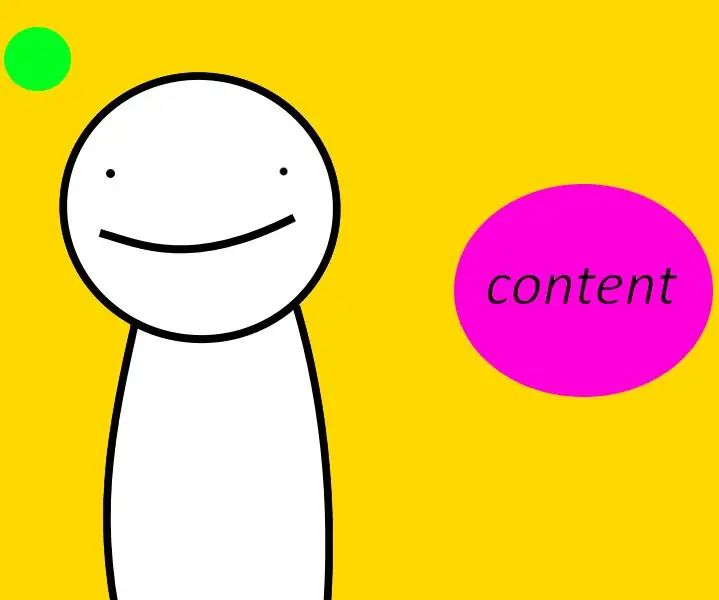
Wie erstelle ich eine einfache Website mit Notepad: Hat sich jemand gefragt, wie ich aus einem einfachen Schreibprogramm eine Website erstelle? Website nur mit Notizblock
So erstellen Sie ein Multiplayer-Spiel mit Arduino-Controllern – wikiHow
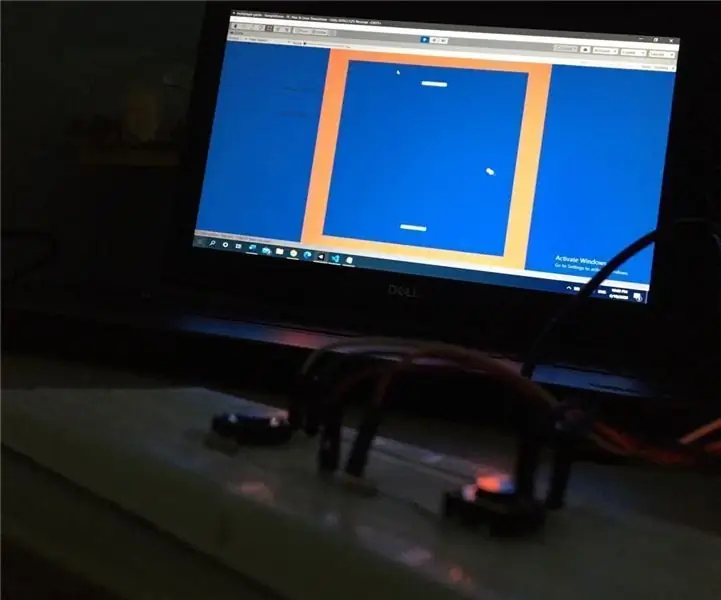
So erstellen Sie ein Multiplayer-Spiel mit Arduino-Controllern: Haben Sie sich jemals gefragt, wie Spieleentwickler erstaunliche Spiele entwickeln, die Menschen weltweit gerne spielen? Nun, heute werde ich Ihnen nur einen kleinen Hinweis darauf geben, indem ich ein kleines Multiplayer-Spiel erstelle, das entweder von einer Arduino-Steuerung gesteuert wird
So erstellen Sie Ihre erste einfache Software mit Python – wikiHow
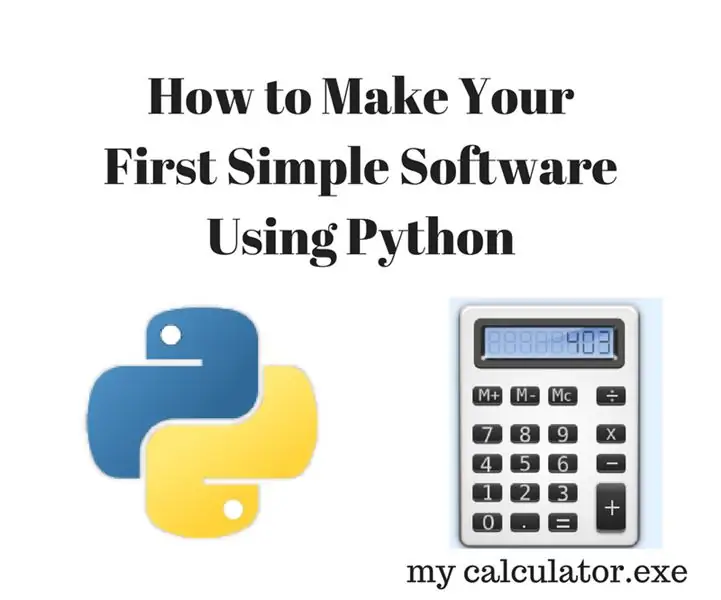
So erstellen Sie Ihre erste einfache Software mit Python: Hallo, willkommen zu diesem Instructables. Hier werde ich erzählen, wie Sie Ihre eigene Software erstellen. Ja, wenn Sie eine Idee haben… aber wissen, wie Sie neue Dinge umsetzen können oder daran interessiert sind, Neues zu schaffen, dann ist es das Richtige für Sie
So erstellen Sie eine Android-App mit Android Studio: 8 Schritte (mit Bildern)
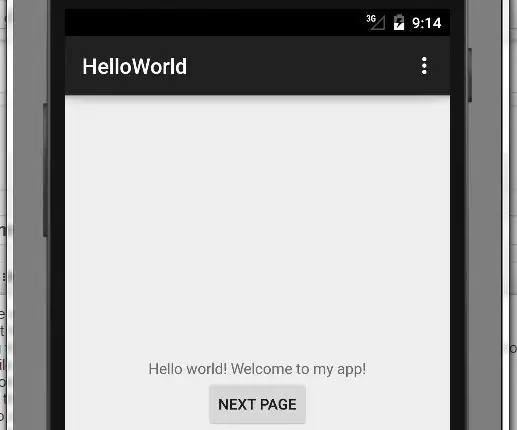
So erstellen Sie eine Android-App mit Android Studio: In diesem Tutorial lernen Sie die Grundlagen zum Erstellen einer Android-App mit der Android Studio-Entwicklungsumgebung. Da Android-Geräte immer häufiger werden, wird die Nachfrage nach neuen Apps nur zunehmen. Android Studio ist ein einfach zu bedienendes (ein