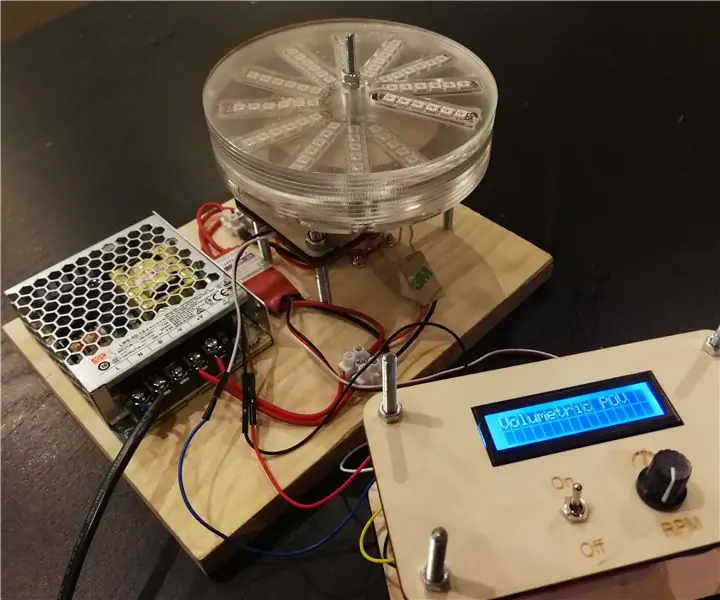
Inhaltsverzeichnis:
- Schritt 1: Verwendetes Material und Werkzeuge
- Schritt 2: Motorcontrollereinheit zur Regulierung der Drehzahl
- Schritt 3: Aufbau der Plattform für drahtlose Sendeleistung
- Schritt 4: Rotierendes Gehäuse
- Schritt 5: Drehender Zylinder mit den LED-Streifen
- Schritt 6: Gelernte Lektionen
- Schritt 7: Potenzielle Verbesserungen
- Schritt 8: Ausrufen
2025 Autor: John Day | [email protected]. Zuletzt bearbeitet: 2025-01-23 12:52
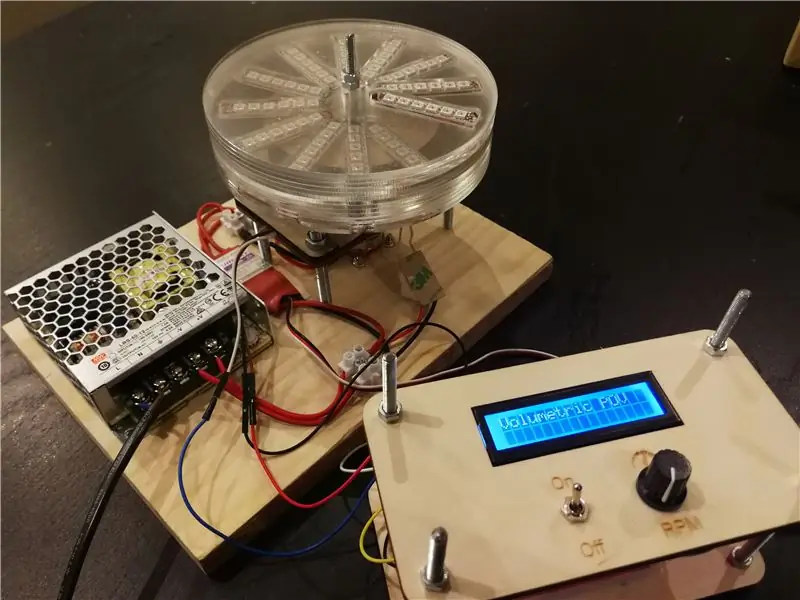
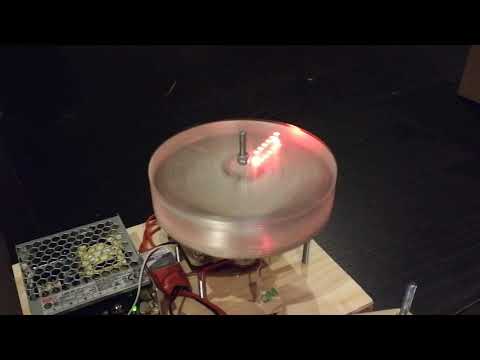

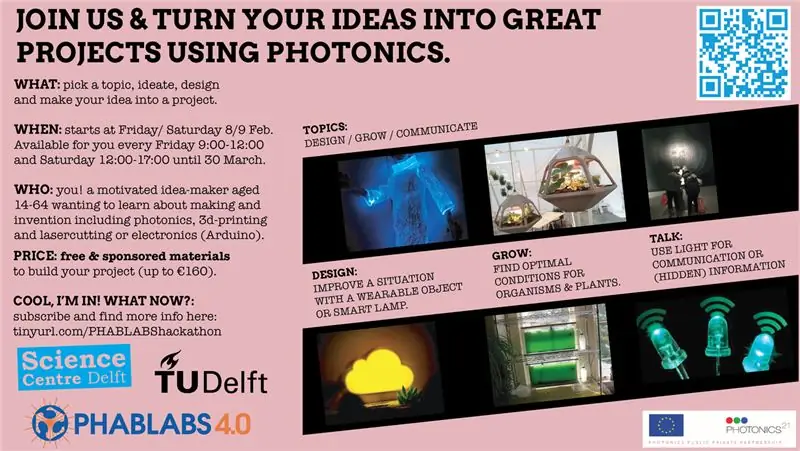
Vor einigen Wochen erhielt ich eine Last-Minute-Einladung zur Teilnahme an einem PhabLabs Hackathon im Science Center Delft in den Niederlanden. Für einen begeisterten Bastler wie mich, der normalerweise nur wenig Zeit mit Tüfteln verbringen kann, sah ich dies als eine großartige Gelegenheit, um eine meiner vielen Ideen im Rahmen des Hackathons: Photonics, mit viel Engagement umzusetzen ein konkretes Projekt. Und bei den großartigen Einrichtungen im Makerspace im Science Center Delft war es einfach unmöglich, diese Einladung abzulehnen.
Eine der Ideen, die ich schon seit einiger Zeit im Zusammenhang mit Photonik hatte, war, dass ich etwas mit Persistence of Vision (POV) machen wollte. Es gibt bereits unzählige Beispiele online, wie man ein einfaches POV-Display mit einigen grundlegenden Komponenten baut: Mikrocontroller, alter Lüfter/Festplatte/Motor und eine Reihe von LEDs, die senkrecht zur Achse des rotierenden Geräts angeschlossen sind. Mit einem relativ einfachen Setup können Sie bereits ein beeindruckendes 2-dimensionales Bild erstellen, z. B.:
Eine andere Variation von POV-Displays verbindet eine Reihe von LEDs parallel zur Achse des rotierenden Geräts. Dies führt zu einer dreidimensionalen zylindrischen POV-Anzeige, z. B.:
Anstatt die LED-Reihe parallel zur Achse des rotierenden Geräts zu verbinden, können Sie die LED-Reihe auch bogenförmig biegen. Dies führt zu einer kugelförmigen (Kugel-) POV-Anzeige, zB: https://www.instructables.com/id/POV-Globe-24bit-… Die nächste Stufe besteht darin, mehrere Schichten von LED-Strings zu bauen, um eine volumetrische 3D-Anzeige zu erstellen. Hier sind einige Beispiele für solche volumetrischen 3D-POV-Displays, die ich als Inspiration für dieses spezielle Projekt verwendet habe:
- https://www.instructables.com/id/PropHelix-3D-POV-…
- https://github.com/mbjd/3DPOV
- https://hackaday.io/project/159306-volumetric-pov-…
- https://hackaday.com/2014/04/21/volumen-the-most-a…
Da die Macher der obigen Beispiele sehr nützliche Informationen lieferten, war es sehr sinnvoll, Teile ihrer Projekte zu remixen. Da ein Hackathon aber eine Herausforderung sein soll, habe ich mich auch entschieden, eine andere Art von volumetrischem 3D-POV-Display zu bauen. Einige von ihnen verwendeten Rotoren und viel Heißkleber, um zu verhindern, dass die Komponenten herumfliegen. Andere erstellten benutzerdefinierte PCBs für ihr Projekt. Nachdem ich einige der anderen 3D-POV-Projekte überprüft hatte, sah ich Raum für einige „Innovationen“oder stellte mir selbst einige Herausforderungen:
- Ohne vorherige Erfahrung mit der Erstellung von kundenspezifischen PCBs und aufgrund der Zeitbeschränkung des Hackathons wähle ich einen einfacheren Prototypenansatz. Aber anstatt echte Rotoren zu erstellen, war ich neugierig, wie ein solches volumetrisches 3D-POV-Display aussehen würde, wenn ein Zylinder aus Acrylkunststoffschichten verwendet wird.
- Keine oder nur minimale Verwendung von Heißkleber, um das Gerät weniger gefährlich zu machen
Schritt 1: Verwendetes Material und Werkzeuge
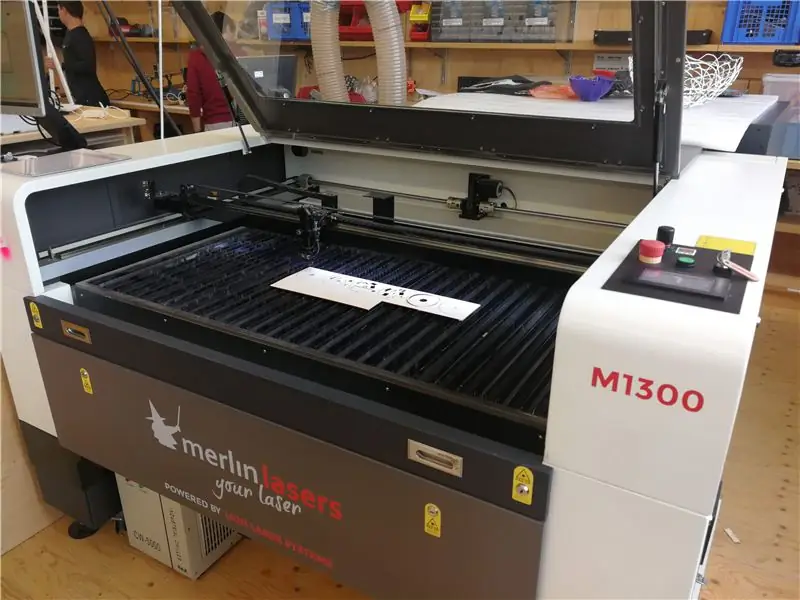
Für den Motorcontroller
- Arduino Pro Micro 5V/16Mhz
- Kleines Steckbrett
- 3144 Hall-Effekt-Schaltersensor
- Magnet mit Durchmesser: 1 cm, Höhe: 3 mm
- Kippschalter - MTS-102
- 10K Potentiometer
- Dupont-Überbrückungsdrähte
- 16 x M5 Muttern
- LCD-Anzeigemodul mit blauer Hintergrundbeleuchtung (HD44780 16×2 Zeichen)
- 10K-Widerstand - Pull-Up-Widerstand für den Hall-Effekt-Sensor
- 220Ohm Widerstand - Zur Kontrastkontrolle des LCD-Bildschirms
- Gewindestangendurchmesser: 5mm
- Sperrholz, Dicke: 3 mm
Für die Plattformbasis
- Stück Altholz (250 x 180 x 18 mm)
- Mean Well - 12V 4.2A - Schaltnetzteil LRS-50-12
- Netzsteckerkabel 220V
- DC-DC-Funkkonverter - 5V 2A (Sender)
- Turnigy D2836/8 1100KV Brushless Outrunner Motor
- Turnigy Plüsch 30 Ampere Drehzahlregler W/BEC
- Anschlussblöcke Steckverbinder
- 12 x M6 Muttern zur Befestigung der Plattform mit den Gewindestangen mit einem Durchmesser von 6 mm.
- 3 x M2-Schrauben (18 mm Länge) zur Befestigung des Anschraubadapters am bürstenlosen Motor
- 4 x M3 Muttern und Schrauben zum Befestigen des bürstenlosen Motors am Stück Altholz
- Gewindestangendurchmesser: 6 mm (4 x Länge 70 mm)
- Gewindestangendurchmesser: 4mm (1 x Länge 80 mm)
- Sperrholz, Dicke: 3 mm
Für das rotierende Gehäuse
- DC-DC Wireless Converter - 5V 2A (Empfänger)
- 3D-gedruckter Bolt-On-Adapter (PLA-Filament, weiß)
- Teensy 3.6
- IC 74AHCT125 Quad Logic Level Converter/Shifter (3V auf 5V)
- 10K-Widerstand - Pull-Up-Widerstand für den Hall-Effekt-Sensor
- 1000uF 16V Kondensator
- Gewindestangendurchmesser 4mm
- Magnet mit Durchmesser: 1 cm, Höhe: 3 mm
- Sperrholz, Dicke: 3 mm
- Sperrholz, Dicke: 2 mm
- Acrylplatte, Dicke: 2 mm
- Durchmesser der Stahlstange: 2 mm
- Muttern & Schrauben
- 0,5 Meter LED-Streifen APA102C 144 LEDs / Meter
Benutztes Werkzeug
- Merlin Laser Cutter M1300 - Laserschneiden von Sperrholz und Acrylplatten
- Ultimaker 2+ für den 3D-Druck des Bolt-On-Adapters
- Lötstation und Löt
- Tischbohrer
- Schraubendreher
- Zangen
- Hammer
- Bremssattel
- Säge
- Schraubenschlüssel
- Schrumpfschlauch
Verwendete Software
- Fusion 360
- Ultimaker Cura
- Arduino IDE und Teensyduino (mit Teensy Loader)
Schritt 2: Motorcontrollereinheit zur Regulierung der Drehzahl
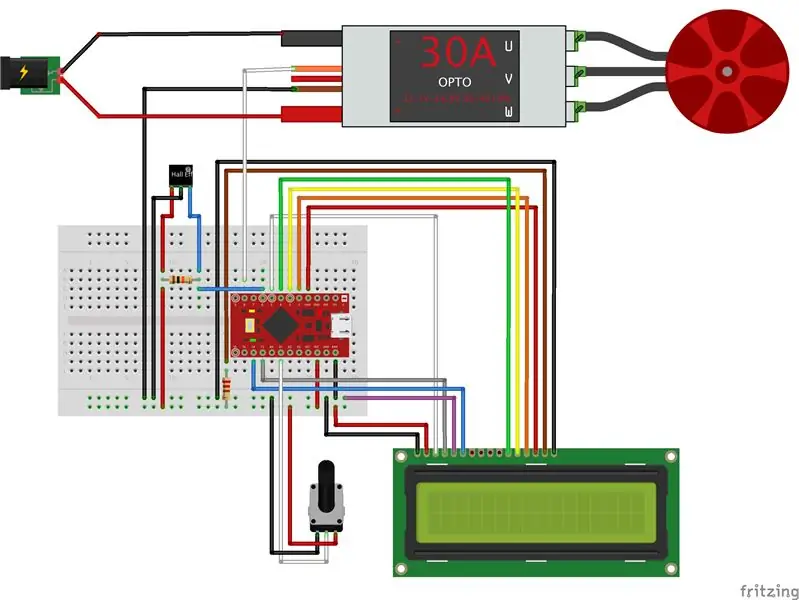
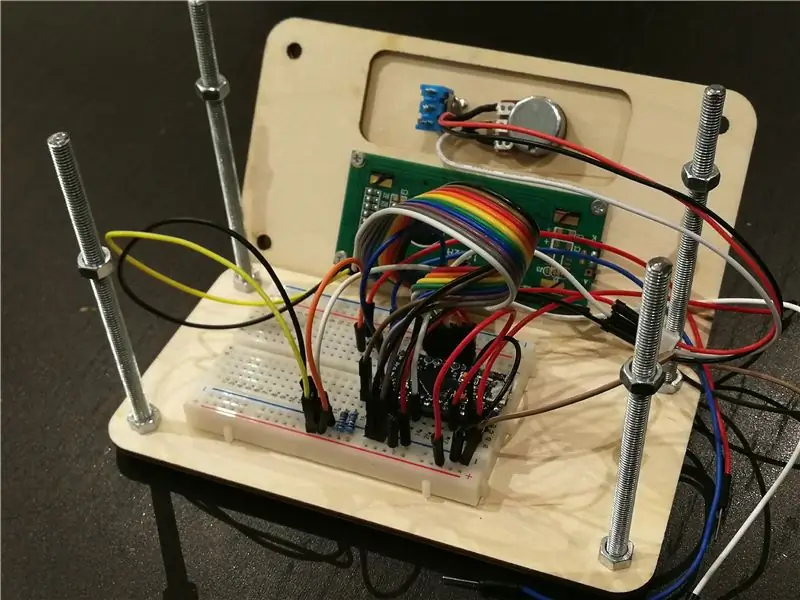
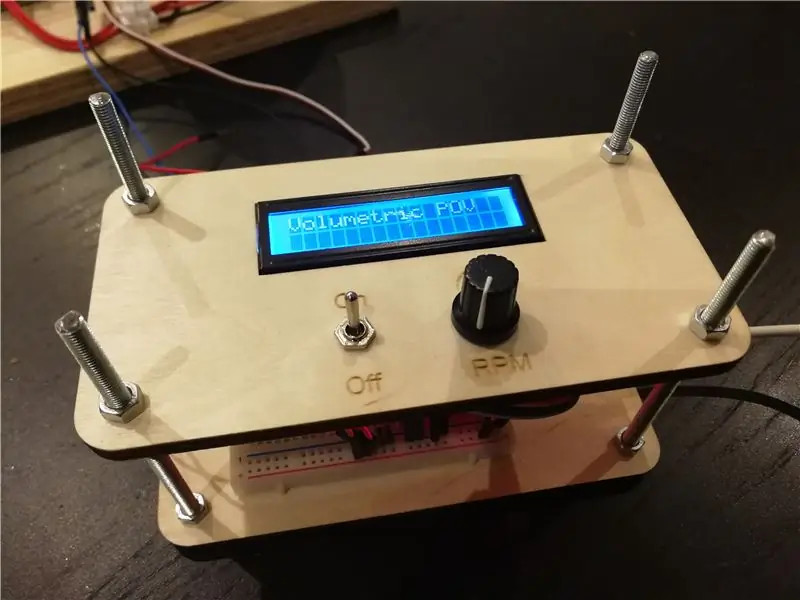
Die Motorsteuereinheit sendet ein Signal an den elektronischen Drehzahlregler (ESC) von Turnigy, der die Drehzahl des bürstenlosen Motors steuert.
Außerdem wollte ich auch die tatsächlichen Umdrehungen pro Minute des POV-Zylinders anzeigen können. Aus diesem Grund habe ich mich entschieden, einen Hall-Effekt-Sensor und ein 16x2-LCD-Display in die Motorcontrollereinheit aufzunehmen.
In der angehängten Zip-Datei (MotorControl_Board.zip) finden Sie drei dxf-Dateien, mit denen Sie eine Grundplatte und zwei Deckplatten für die Motorcontroller-Einheit laserschneiden können. Bitte verwenden Sie Sperrholz mit einer Dicke von 3 mm. Die beiden oberen Platten können übereinander gelegt werden, so dass Sie das 16x2 LCD-Display einschrauben können.
Die beiden Löcher in der oberen Platte sind für einen Ein / Aus-Kippschalter und ein Potentiometer zur Steuerung der Geschwindigkeit des bürstenlosen Motors gedacht (ich habe den Ein / Aus-Kippschalter noch nicht selbst verdrahtet). Um die Motor Controller Unit zu konstruieren, müssen Sie die Gewindestange mit einem Durchmesser von 5 mm in 4 Stücke der gewünschten Höhe sägen. Mit den 8 Muttern M5 können Sie zunächst den Sockel befestigen. Dann habe ich das kleine Steckbrett mit dem doppelseitigen Klebeaufkleber, der mit dem Steckbrett geliefert wurde, auf der Grundplatte befestigt. Das beigefügte Schema zeigt, wie Sie die Komponenten verdrahten sollten, damit sie mit dem an diesen Schritt angehängten Quellcode (MotorControl.ino) arbeiten können. Ich habe einen 10K Pull-Up-Widerstand für den Hall-Sensor verwendet. Ein 220 Ohm Widerstand funktionierte gut genug, um den Text auf dem LCD-Bildschirm sichtbar zu machen.
Bitte achten Sie darauf, dass Sie die Pins des Hall-Effekt-Sensors mit Schrumpfschläuchen isolieren, wie auf den Bildern gezeigt. Die korrekte Funktion des Hallsensors hängt von einem Magneten ab, der in Schritt 3 in das rotierende Gehäuse eingesetzt wird.
Sobald die Verkabelung abgeschlossen ist, können Sie die 2 oberen Platten mit dem LCD-Display, dem Schalter und dem Potentiometer mit 8 M5-Muttern wie auf den Bildern gezeigt befestigen.
Je nach Modell Ihres verwendeten Motors müssen Sie möglicherweise die folgende Codezeile in der Datei MotorControl.ino anpassen:
Drossel = map(averagePotValue, 0, 1020, 710, 900);
Diese Codezeile (Zeile 176) bildet die Position des 10K-Potentiometers auf das Signal für den ESC ab. Der ESC akzeptiert Werte zwischen 700 und 2000. Und als der Motor, den ich für dieses Projekt verwendet habe, sich um 823 drehte, begrenzte ich die Drehzahl des Motors, indem ich den Maximalwert auf 900 begrenzte.
Schritt 3: Aufbau der Plattform für drahtlose Sendeleistung
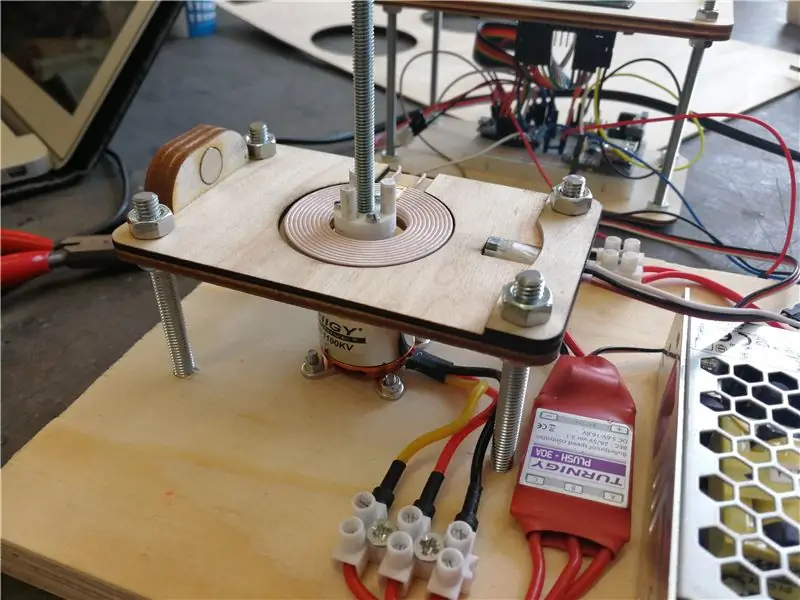
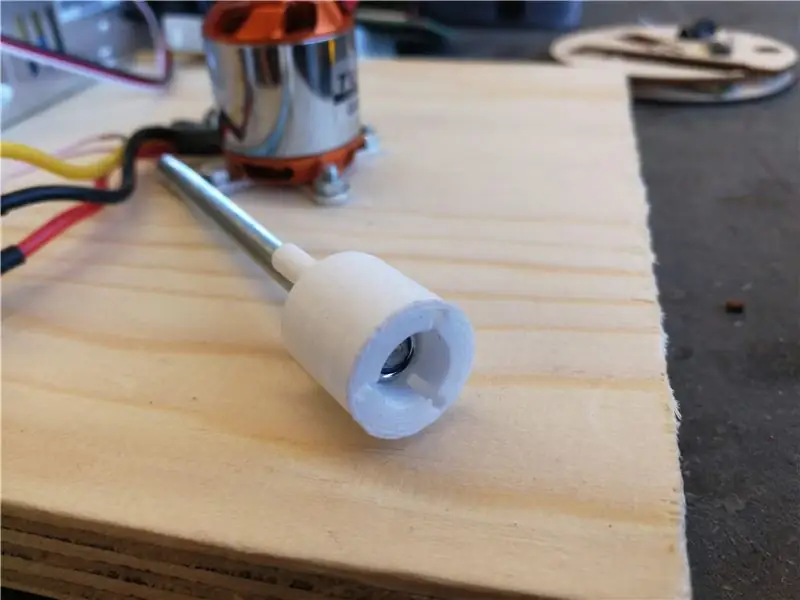
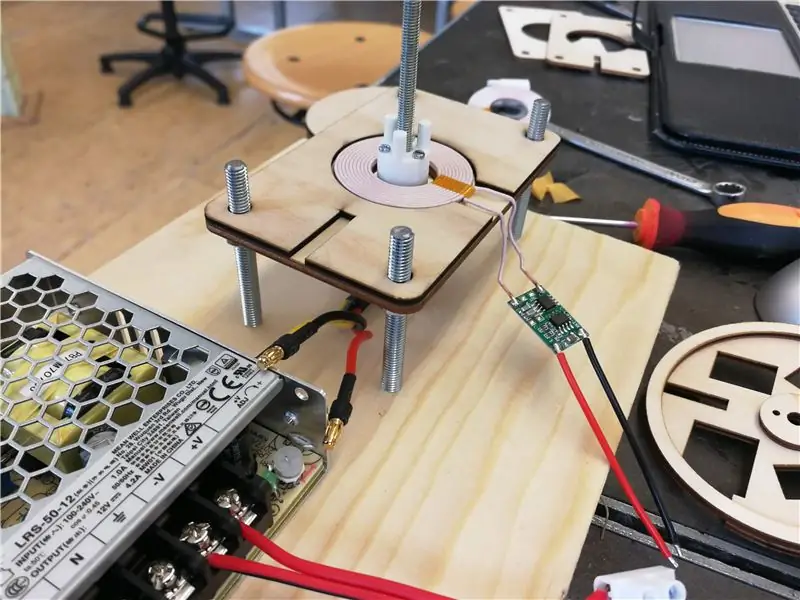
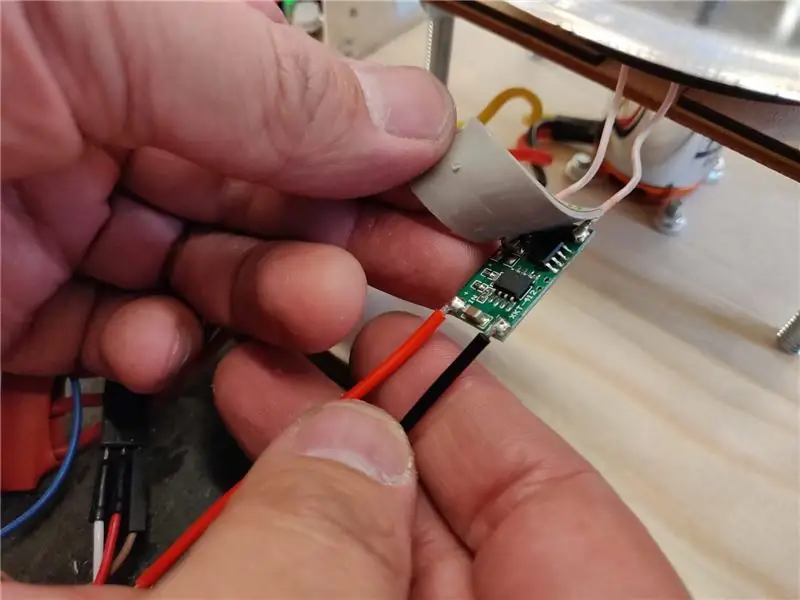
Heutzutage gibt es grundsätzlich zwei Möglichkeiten, Geräte, die sich drehen müssen, anzutreiben: Schleifringe oder die drahtlose Energieübertragung über Induktionsspulen. Da hochwertige Schleifringe, die hohe Drehzahlen unterstützen können, in der Regel sehr teuer und verschleißanfälliger sind, habe ich mich für die drahtlose Option mit einem 5V Wireless DC-DC-Wandler entschieden. Laut Spezifikation sollen mit einem solchen Wandler bis zu 2 Ampere übertragen werden können.
Der Wireless DC-DC Converter besteht aus zwei Komponenten, einem Sender und einem Empfänger. Bitte beachten Sie, dass die an die sendende Induktionsspule angeschlossene Leiterplatte kleiner ist als die der empfangenden.
Die Plattform selbst wird aus einem Stück Altholz (250 x 180 x 18 mm) gebaut.
Auf der Plattform habe ich das Mean Well 12V Netzteil angeschraubt. Der 12-V-Ausgang ist mit dem Regler (siehe Schaltpläne in Schritt 1) und der Platine des Sendeteils des drahtlosen DC-DC-Wandlers verbunden.
In der angehängten Platform_Files.zip finden Sie die dxf-Dateien zum Laserschneiden der Plattform aus Sperrholz mit einer Dicke von 3mm:
- Platform_001.dxf und Platform_002.dxf: Sie müssen sie aufeinander legen. Dadurch entsteht ein vertiefter Bereich für die Sendeinduktionsspule.
- Magnet_Holder.dxf: Dieses Design dreimal laserschneiden. Eine der drei Zeiten, schließen Sie den Kreis ein. In den anderen beiden Laserschnitten: Entfernen Sie den Kreis aus dem Schneiden. Kleben Sie die drei Teile nach dem Zuschneiden zu einer Halterung für einen Magneten (Durchmesser 10 mm, Dicke: 3 mm) zusammen. Ich habe Sekundenkleber verwendet, um den Magneten in den Magnethalter zu kleben. Bitte achten Sie darauf, dass Sie die richtige Seite des Magneten auf die Halterung kleben, da der Hallsensor nur mit einer Seite des Magneten funktioniert.
- Platform_Sensor_Cover.dxf: Dieses Stück hilft Ihnen, den an der Motorsteuereinheit befestigten Hallsensor wie im ersten Bild gezeigt an Ort und Stelle zu halten.
- Platform_Drill_Template.dxf: Ich habe dieses Stück als Schablone zum Bohren der Löcher in das Stück Altholz verwendet. Die vier größeren 6 mm Löcher sind für die tragenden Gewindestangen mit einem Durchmesser von 6 mm zum Abstützen der Plattform. Die 4 kleineren Löcher dienen zur Befestigung des bürstenlosen Motors am Altholz. Das größte Loch in der Mitte wurde für die Achse benötigt, die aus dem bürstenlosen Motor herausragte. Da die Schrauben für den Motor und die Gewindestangen für die Plattform an der Unterseite der Plattform befestigt werden müssen, müssen diese Löcher einige mm tief erweitert werden, damit die Muttern hineinpassen.
Leider ragte die Welle des bürstenlosen Motors für dieses Projekt aus der "falschen" Seite heraus. Aber ich konnte die Welle mit Hilfe der folgenden Anleitung, die ich auf Youtube gefunden habe, umkehren:
Sobald der Motor und die Tragstangen befestigt sind, kann die Plattform mit den lasergeschnittenen Plattformteilen gebaut werden. Die Plattform selbst kann mit 8 Muttern M6 gesichert werden. Der Magnethalter kann wie im ersten Bild gezeigt am Rand auf die Plattform geklebt werden.
Die angehängte Datei "Bolt-On Adapter.stl" kann mit einem 3D-Drucker ausgedruckt werden. Dieser Adapter wird benötigt um eine Gewindestange mit einem Durchmesser von 4mm mit 3 x M2 Schrauben mit einer Länge von 18mm am Brushless Motor zu befestigen.
Schritt 4: Rotierendes Gehäuse
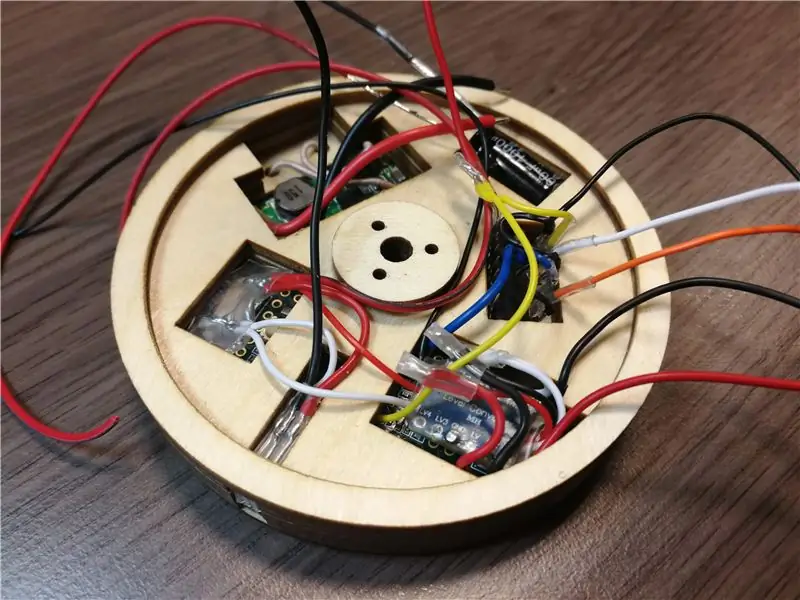
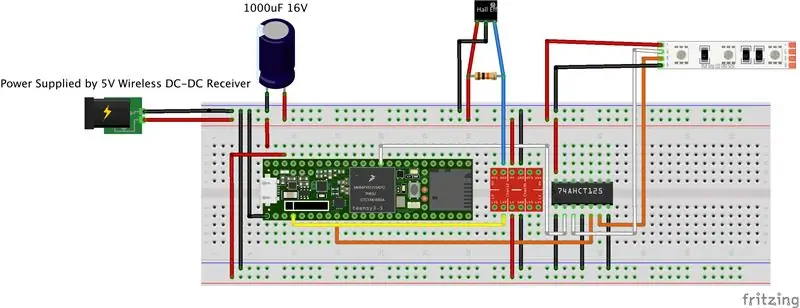
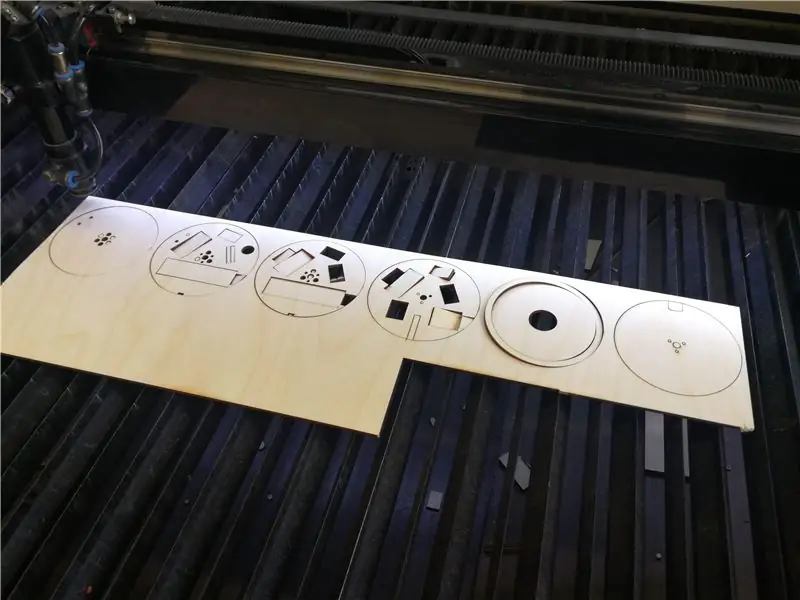
Die angehängte Base_Case_Files.zip enthält die dxf-Dateien zum Laserschneiden der 6 Schichten, um das Gehäuse für die Komponenten zu konstruieren, die den APA102C-LED-Streifen steuern.
Die Schichten 1-3 des Case-Designs sollen zusammengeklebt werden. Bitte achten Sie jedoch darauf, dass ein Magnet (Durchmesser 10 mm, Höhe: 3 mm) in den kreisförmigen Ausschnitt in Schicht 2 gelegt wird, bevor Sie die drei Schichten zusammenkleben. Achten Sie auch darauf, dass der Magnet mit dem richtigen Pol nach unten geklebt wird, da der Hall-Effekt-Sensor, der auf der in Schritt 3 konstruierten Plattform platziert wurde, nur auf eine Seite des Magneten anspricht.
Die Gehäuseausführung enthält Fächer für die in den beigefügten Schaltplänen aufgeführten Komponenten. Der IC 74AHCT125 wird benötigt, um das 3,3-V-Signal vom Teensy in das für den APA102-LED-Streifen erforderliche 5-V-Signal umzuwandeln. Die Schichten 4 und 5 können auch zusammengeklebt werden. Die obere Schicht 6 kann auf die anderen Schichten gestapelt werden. Alle Lagen bleiben mit Hilfe von 3 Stahlstäben mit einem Durchmesser von 2 mm in der richtigen Position. Es gibt drei kleine Löcher für die 2 mm Stahlstangen, die das größere Loch für die rotierende 4 mm Gewindestange umgeben, die am bürstenlosen Motor befestigt ist. Nachdem alle Komponenten gemäß Schaltplan verlötet sind, kann das komplette Gehäuse auf den in Schritt 3 gedruckten Schraubadapter aufgesetzt werden. Bitte achten Sie darauf, dass offene Drähte mit Schrumpfschläuchen ordnungsgemäß isoliert werden. Bitte beachten Sie, dass die korrekte Funktion des Hallsensors dieser Schritte davon abhängt, ob der Magnet in der Magnethalterung platziert ist, wie in Schritt 3 beschrieben.
Der beigefügte Proof-of-Concept-Code 3D_POV_POC.ino wird einige LEDs rot aufleuchten. Die Skizze führt dazu, dass ein Quadrat angezeigt wird, sobald sich der Zylinder zu drehen beginnt. Aber bevor das Rotieren beginnt, werden die LEDs, die zur Simulation eines Quadrats erforderlich sind, standardmäßig eingeschaltet. Dies ist hilfreich, um im nächsten Schritt die korrekte Funktion der LEDs zu testen.
Schritt 5: Drehender Zylinder mit den LED-Streifen
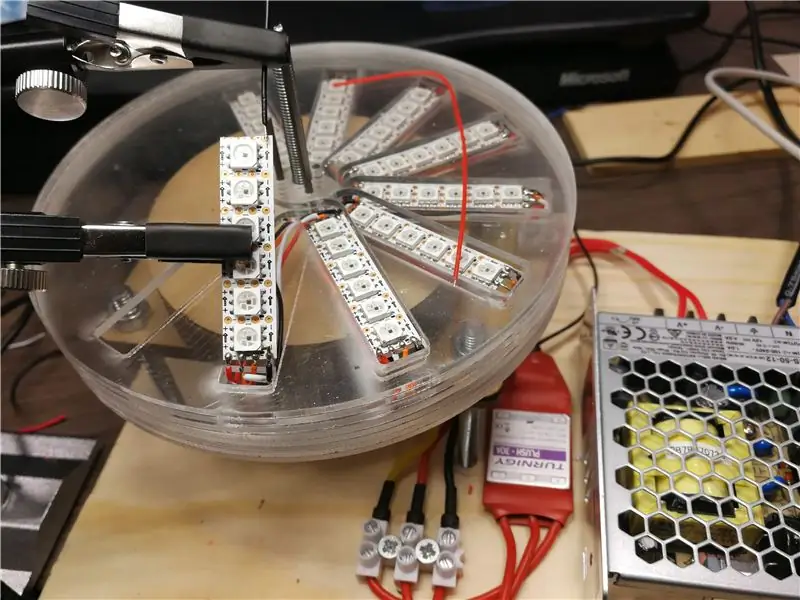
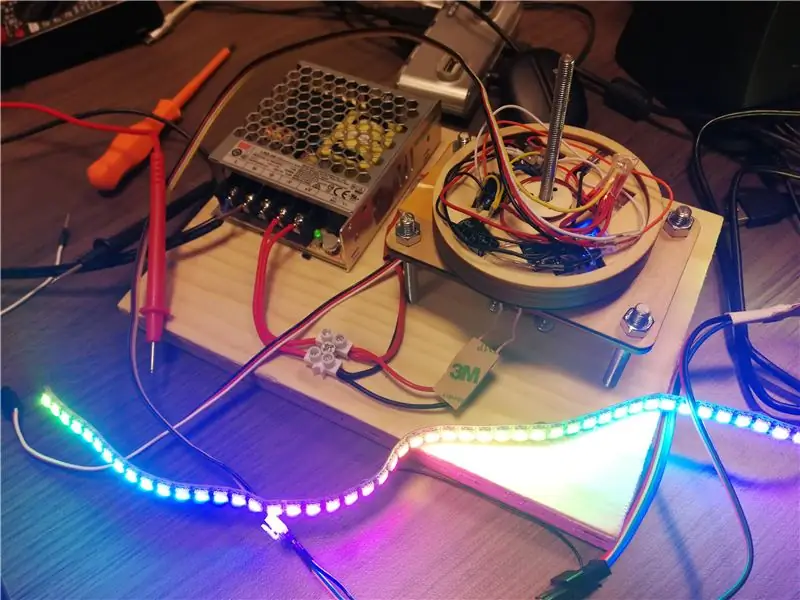
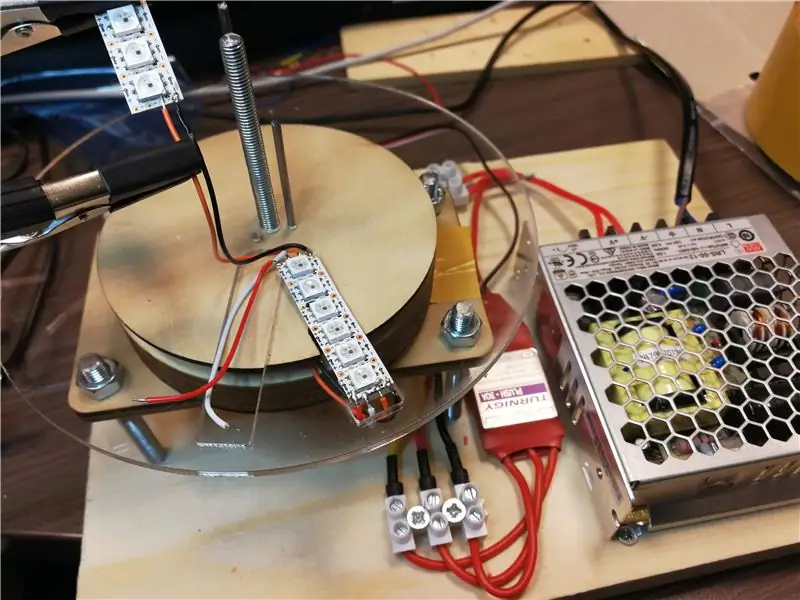
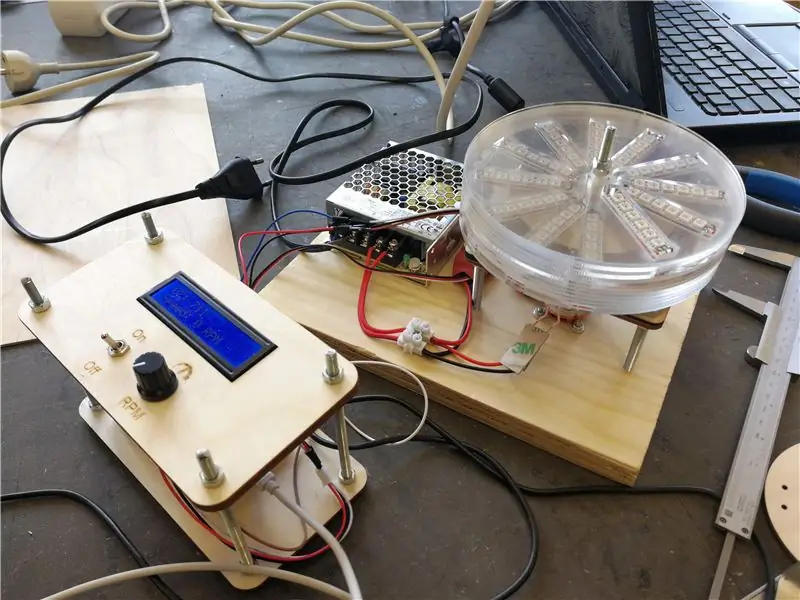
Die beigefügte Rotor_Cylinder_Files.zip enthält die dxf-Dateien zum Schneiden einer 2 mm dicken Acrylplatte. Die resultierenden 14 Scheiben sind notwendig, um den transparenten Zylinder für dieses POV-Projekt zu bauen. Die Scheiben müssen aufeinander gestapelt werden. Das Design der zylindrischen Scheiben ermöglicht das Zusammenlöten von 12 LED-Streifen zu einem langen LED-Streifen. Ausgehend von Disc eins muss ein kleiner LED-Streifen mit 6 LEDs mit den Klebeaufklebern auf dem LED-Streifen an einer Disc befestigt werden. Löten Sie zuerst die Drähte an den LED-Streifen, bevor Sie die LED-Streifen mit den Klebeaufklebern an der Scheibe befestigen. Andernfalls besteht die Gefahr, dass die Lötpistole die Acrylscheibe schmilzt.
Sobald die Scheibe Nr. 13 auf dem transparenten Zylinder gestapelt ist, kann der 2 mm Stahlstab, der verwendet wird, um alle Schichten in der richtigen Position zu halten, nun auch auf die richtige Länge zugeschnitten werden, ausgerichtet auf die Oberseite der Scheibe Nr. 13 des Zylinders. Die Scheibe #14 kann dann verwendet werden, um die 2 mm Stahlstangen mit Hilfe von zwei M4-Muttern an Ort und Stelle zu halten.
Aufgrund des Zeitaufwandes, der für den Aufbau des gesamten Gerätes benötigt wird, konnte ich im Zeitrahmen des Hackathons noch keine stabileren optisch interessanten 3D-Displays programmieren. Das ist auch der Grund, warum der mitgelieferte Code zur Ansteuerung der LEDs noch sehr einfach ist, um das Konzept zu beweisen und vorerst nur ein rotes Quadrat 3-dimensional zu zeigen.
Schritt 6: Gelernte Lektionen
Teensy 3.6
- Ich habe für dieses Projekt einen Teensy 3.5 bestellt, aber der Lieferant hat mir irrtümlicherweise einen Teensy 3.6 zugeschickt. Da ich begierig darauf war, das Projekt innerhalb des Zeitrahmens des Hackathons abzuschließen, beschloss ich, mit dem Teensy 3.6 fortzufahren. Der Grund, warum ich das Teensy 3.5 verwenden wollte, waren die Anschlüsse, die 5V tolerant sind. Dies ist beim Teensy 3.6 nicht der Fall. Das ist auch der Grund, warum ich einen bidirektionalen Logikwandler in das Setup einbauen musste. Bei einem Teensy 3.5 wäre dies nicht erforderlich gewesen.
- Problem mit der Leistungserhöhung: Beim Einschalten des Geräts erfolgt eine Leistungserhöhung über das drahtlose DC-DC-Lademodul, um das Teensy 3.6 mit Strom zu versorgen. Leider ist das Hochfahren zu langsam, als dass das Teensy 3.6 richtig starten könnte. Als Workaround muss ich derzeit den Teensy 3.6 über den Micro-USB-Anschluss einschalten und dann das 12-V-Netzteil anschließen, das den drahtlosen DC-DC-Sender versorgt. Sobald der drahtlose DC-DC-Empfänger auch den Teensy mit Strom versorgt, kann ich das USB-Kabel abziehen. Leute haben ihren Hack mit einem MIC803 für das Problem des langsamen Hochfahrens hier geteilt:
LCD-Bildschirmmodul
Unregelmäßiges Verhalten bei externer Stromversorgung. Der Bildschirm funktioniert ordnungsgemäß, wenn er über USB mit Strom versorgt wird. Aber wenn ich den LCD-Bildschirm über das Steckbrett mit den vom BEC oder einem unabhängigen Netzteil gelieferten 5 V mit Strom versetze, beginnt der Text nach einigen Sekunden, nachdem sich der Text ändern soll, zu verwürfeln. Ich muss noch untersuchen, was dieses Problem verursacht
Mechanisch
Um meine Motorsteuereinheit zu testen, um die tatsächlichen Drehzahlen zu messen, lasse ich den Motor mit dem angeschraubten Adapter, der Schraube und dem am Motor befestigten Basisgehäuse drehen. Bei einem der ersten Testläufe lösen sich die Schrauben, die den Motorhalter mit dem Motor verbinden, aufgrund der Vibrationen von selbst. Zum Glück habe ich dieses Problem rechtzeitig bemerkt, sodass eine potenzielle Katastrophe vermieden wurde. Ich habe dieses Problem gelöst, indem ich die Schrauben etwas fester am Motor angeschraubt habe und auch ein paar Tropfen Loctite verwendet habe, um die Schrauben noch mehr zu sichern
Software
Wenn Sie Fusion 360-Skizzen als dxf-Dateien für den Laserschneider exportieren, werden unterstützende Linien als normale Linien exportiert
Schritt 7: Potenzielle Verbesserungen
Was hätte ich aufgrund meiner Erfahrungen mit diesem Projekt anders gemacht:
- Verwenden eines LED-Streifens mit mindestens 7 LEDs anstelle von 6 LEDs pro Schicht für etwas schönere Textvisualisierungen
- Kaufen Sie einen anderen bürstenlosen Motor, bei dem die Welle bereits auf der richtigen (unteren) Seite des Motors herausragt. (zB: https://hobbyking.com/de_de/ntm-prop-drive-28-36-1000kv-400w.html) Dadurch ersparen Sie sich das Abschneiden der Welle oder das Schieben der Welle auf die richtige Seite wie ich musste jetzt machen.
- Verbringen Sie mehr Zeit mit dem Auswuchten des Geräts, um die Vibrationen zu minimieren, entweder mechanisch oder in Fusion 360.
Ich habe auch über einige mögliche Verbesserungen nachgedacht, die ich prüfen könnte, wenn es die Zeit erlaubt:
- Tatsächliche Nutzung der SD-Kartenfunktion des Teensy, um längere Animationen zu erstellen
- Erhöhen Sie die Bilddichte durch Verwendung kleinerer LEDs (APA102(C) 2020). Als ich vor einigen Wochen mit diesem Projekt begann, waren LED-Streifen mit diesen kleinen LEDs (2x2 mm) nicht ohne weiteres auf dem Markt erhältlich. Es ist möglich, sie als separate SMD-Komponenten zu kaufen, aber ich würde diese Option nur in Betracht ziehen, wenn Sie bereit sind, diese Komponenten auf einer kundenspezifischen Leiterplatte zu löten.
- Übertragen Sie 3D-Bilder drahtlos auf das Gerät (Wifi oder Bluetooth). Damit soll es auch möglich sein, das Gerät zur Visualisierung von Ton/Musik zu programmieren.
- Konvertieren Sie Blender-Animationen in ein Dateiformat, das mit dem Gerät verwendet werden kann
- Legen Sie alle LED-Streifen auf die Grundplatte und fokussieren Sie das Licht auf die Acrylschichten. Auf jeder anderen Schicht können kleine Bereiche graviert werden, um das Licht zu reflektieren, wenn es von den LEDs weggelassen wird. Das Licht sollte auf die gravierten Bereiche fokussiert werden. Dies sollte möglich sein, indem ein Tunnel geschaffen wird, der das Licht leitet oder Linsen an den LEDs verwendet, um das Licht zu fokussieren.
- Verbesserung der Stabilität der volumetrischen 3D-Anzeige und Regulierung der Drehzahl durch Trennung der rotierenden Basis vom bürstenlosen Motor durch Verwendung von Zahnrädern und einem Zahnriemen.
Schritt 8: Ausrufen
Besonderen Dank möchte ich folgenden Personen aussprechen:
- Meiner fantastischen Frau und meinen Töchtern für ihre Unterstützung und ihr Verständnis.
- Teun Verkerk, für die Einladung zum Hackathon
- Nabi Kambiz, Nuriddin Kadouri und Aidan Wyber, für Ihre Unterstützung, Hilfe und Anleitung während des Hackaton
- Luuk Meints, ein Künstler und Mitteilnehmer dieses Hackaton, der mir so freundlich war, mir einen persönlichen 1-stündigen Einführungskurs in Fusion 360 zu geben, der es mir ermöglichte, alle Teile zu modellieren, die ich für dieses Projekt benötigte.