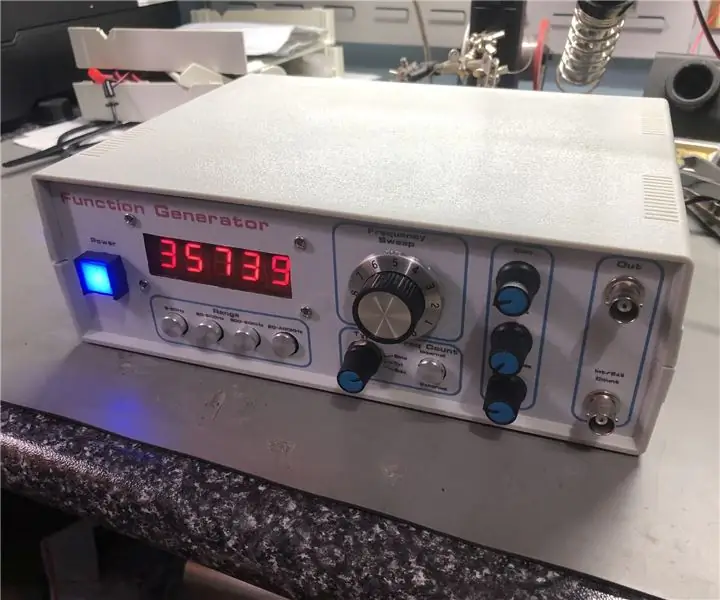
Inhaltsverzeichnis:
- Lieferungen
- Schritt 1: Wie alles zusammenpasst
- Schritt 2: Nicht alle Counter-Kits sind gleich
- Schritt 3: Erstellen Sie den Signalgenerator
- Schritt 4: Entwerfen Sie die Frontplatte
- Schritt 5: Beginnen Sie mit der Montage und Montage der Hardware
- Schritt 6: Alles verdrahten
- Schritt 7: Einschalten
- Schritt 8: Erster Build und wenn die Dinge nicht so laufen, wie Sie es planen (Blooper Reel)?
2025 Autor: John Day | [email protected]. Zuletzt bearbeitet: 2025-01-23 12:52
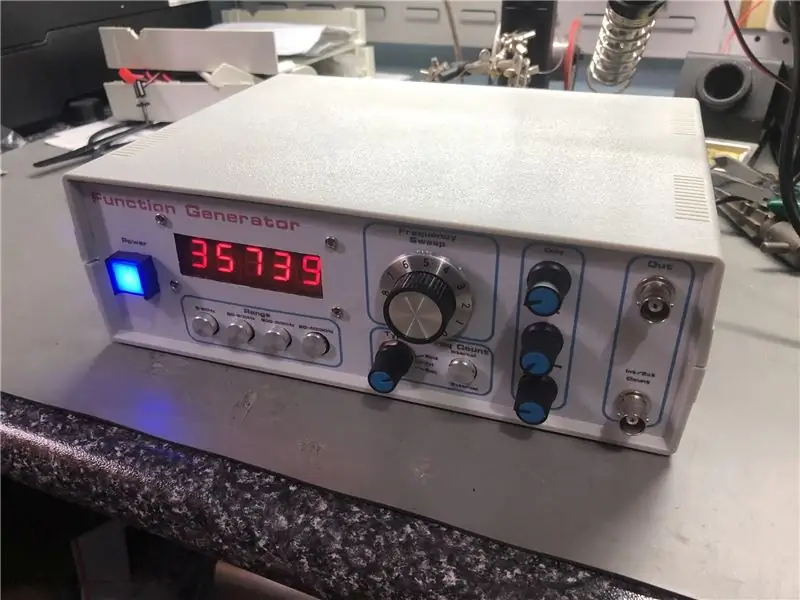
Bauen Sie diesen einfachen Sweep-Signalgenerator aus leicht verfügbaren Kits.
Wenn Sie einen Blick auf mein letztes instructable (Make Professional Looking Front Panels) geworfen haben, hätte ich mich vielleicht dem entzogen, woran ich damals arbeitete, einem Signalgenerator. Ich wollte einen Signalgenerator, bei dem ich relativ einfach Frequenzen durchstreichen kann (nicht nur einstellen und vergessen). Da ich nichts billiges finden konnte, beschloss ich, mir selbst einen zusammenzusetzen und Bausätze als Grundlage zu verwenden.
Das Herzstück des Projekts ist ein Signalgenerator-Kit, das bei Ebay, Amazon usw. leicht zu bekommen ist. Es ist einfach zu bauen und anpassbar. Es gibt vier Frequenzbereiche (5-50Hz, 50-500Hz, 500Hz-20Khz und 20KHz-400KHz), drei Ausgangsarten (Quadrat, Dreieck und Sinus).
Der Zähler ist ein weiteres Kit und zählt von 1Hz-75MHz mit automatischer Bereichswahl und 4- oder 5-stelliger Auflösung.
Ein paar Anmerkungen:
1. Ich habe diese Bausätze nicht entworfen, sondern nur als Teil des Projekts gebaut. Sie sind über die meisten Online-Verkaufsstellen (Ebay usw.) leicht erhältlich. Wenn Sie jedoch Probleme mit Teilen, Bauen usw. haben, hat es keinen Sinn, mich diesbezüglich zu kontaktieren. Wenden Sie sich an den Verkäufer, bei dem Sie es gekauft haben. Ich versuche jedoch gerne, Fragen zu beantworten, wie ich sie in diesem speziellen Build verwendet habe.
2. Das Frequenzzähler-Kit, obwohl es sagt, dass es von 1 Hz bis 75 MHz zählt, fand ich das nicht der Fall. Je langsamer die Frequenz wurde, desto langsamer und desto größer die Fehlerspanne. Wenn jemand ein besseres Counter-Kit kennt, freue ich mich, davon zu hören. So wie es war, war dies das Beste, was mir einfallen konnte, um niedrigere Frequenzwerte (Sub KHz) zu lesen.
Lieferungen
ICL8038 5Hz - 400KHz Frequenzgenerator-Kit (Off ebay) ca. $ 12-13
1Hz-75KHz Frequenzzähler-Kit (Off ebay) ca. $ 12-13
LED-Ein/Aus-Schalter (Sie können einen beliebigen verwenden)
4 Gang Push-Schalter (normalerweise als DPDT - dies könnte schwer zu finden sein). Sie können einen Drehschalter verwenden, wenn Sie keinen finden.
1 DPDT Druckschalter (ich hatte Singles des passenden Gangschalters)
4 Potis (2@5KB, 1@50KB) (Ich habe ein 50KB Multiturn-Präzisionspoti für die Frequenzanpassung verwendet)
3 BNC-Anschlüsse für die Schalttafelmontage
DC-Anschluss für Schalttafeleinbau
1x großer Knopf (für 50-mm-Topf)
Männliche/weibliche PCB-Abstandsverbinder und -stecker (verschiedene Größen)
Rechtwinkliger männlicher PCB-Abstandsstecker
Messingabstandshalter (verschiedene Größen)
Instrumentenkoffer (teuerster Teil des Projekts)! ungefähr $25
Inkjet weißes und klares Papier
Optional:
1 x 5,5 mm DC-Anschluss (Signalgeneratorplatine)
1 x 4mm DC-Anschluss (Meterplatine)
Da ich bereits eine Menge von diesem Zeug habe, betrugen die Kosten etwa 50 US-Dollar (2 Kits plus ein Gehäuse), können jedoch höher sein, wenn Sie keine Anschlüsse, Abstandshalter, Knöpfe, Schalter usw.
Schritt 1: Wie alles zusammenpasst
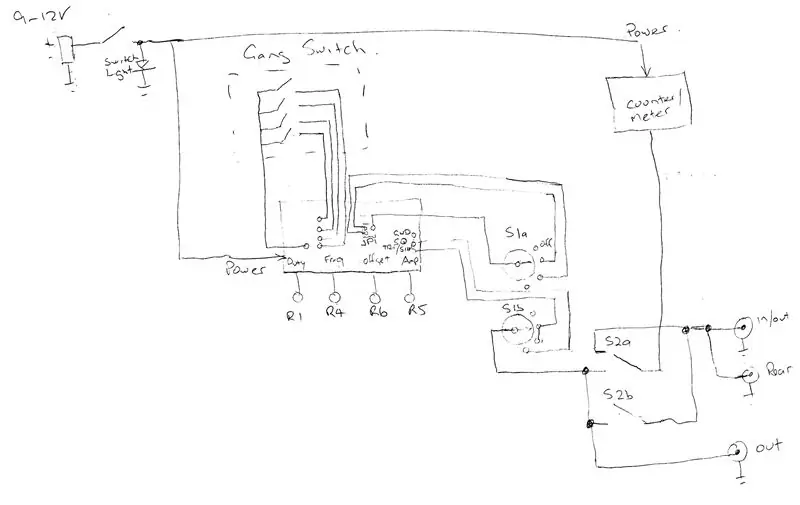
Im Grunde ist es nur ein Signalgenerator-Kit mit einem an den Ausgang angeschlossenen Frequenzzähler. Ich habe jedoch einige praktische Schaltkombinationen hinzugefügt.
Es gibt 3 BNC-Anschlüsse:
Einer für den Hauptausgang (der immer im Stromkreis ist, es sei denn, Sie schalten den Messschalter auf extern), einen BNC für int/ext-Messungen entweder mit dem internen Meter für eine externe Quelle und einen BNC auf der Rückseite, der mit oben verbunden ist (Sie können also entweder über die Vorder- oder Rückseite anschließen).
Der int/ext-Schalter wird verwendet, um ein Signal auf das interne Messgerät zu schalten. Wenn es sich in der internen Position (in) befindet, geht das Signal vom Generator zum Messgerät und zu allen BNC-Anschlüssen. Mit dieser Konfiguration können Sie beliebige externe Messgeräte (Frequenzzähler, Oszilloskop parallel zum Hauptsignalausgang) anschließen. Wenn sich der Schalter in der Position ext (out) befindet, trennt er den Hauptausgang und sowohl die int/ext- als auch die rückseitigen BNCs sind mit dem internen Meter verbunden. So können Sie ein externes Signal einspeisen und mit dem internen Meter messen.
Der Signaltyp-Schalter ist ein Drehschalter, der in den ersten beiden Positionen grundsätzlich zwischen Tri/Sinus umschaltet. Der gegenüberliegende Schalter verbindet das Tri/Sinus-Signal mit dem Ausgang. In Position drei wird S1a nicht verwendet und schaltet nur zwischen den Squ- und Tri/Sinus-Ausgängen auf den Hauptausgang um.
Schritt 2: Nicht alle Counter-Kits sind gleich
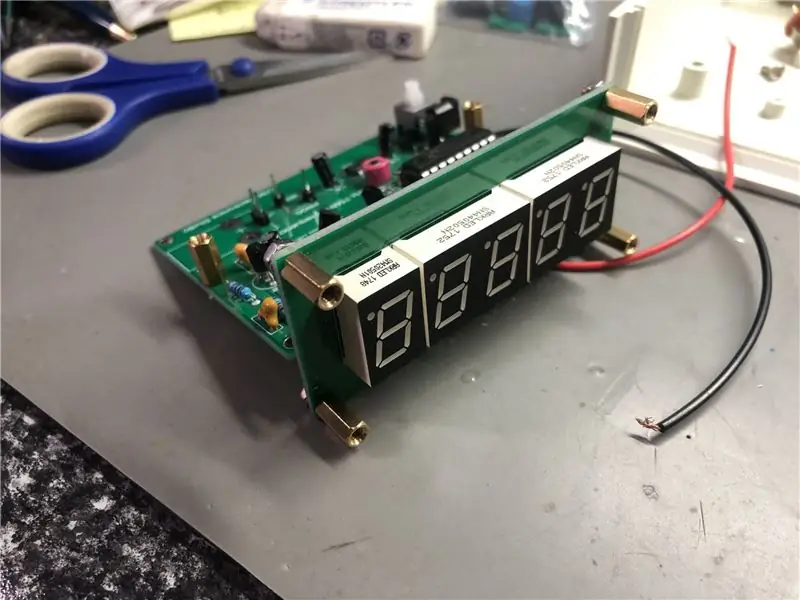
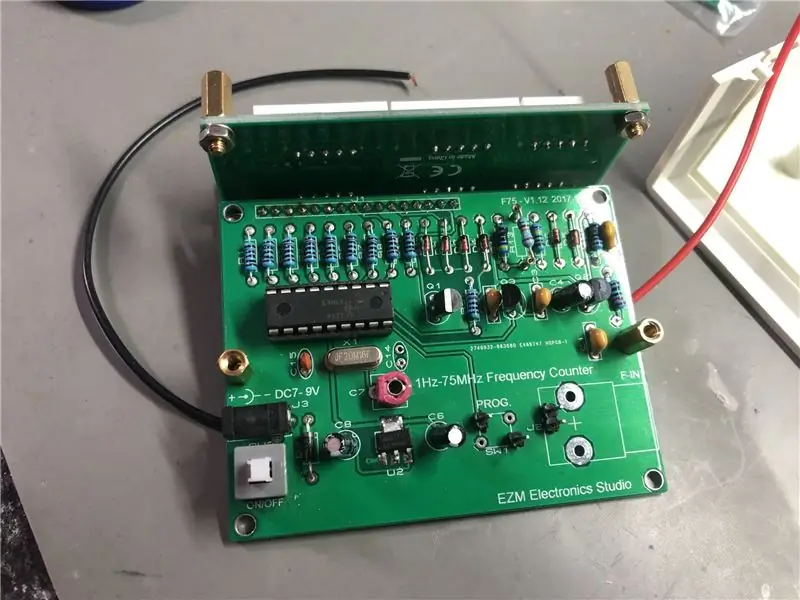
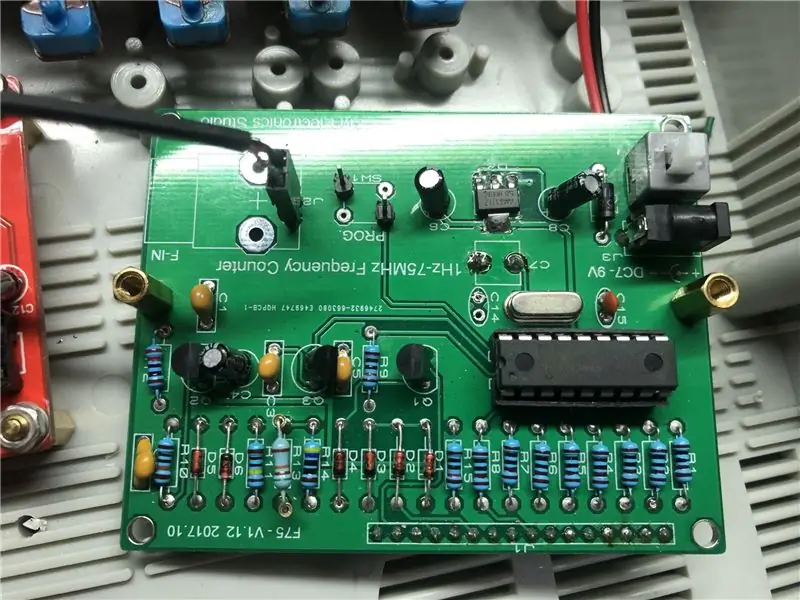
Bevor Sie Geld für eines dieser Frequenzzähler-Kits ausgeben, sind sie nicht alle gleich. Was Sie wollen, ist ein Kit, das niedrigere Frequenzen misst. Viele der fertig gebauten Module messen nur 1MHz und höher. Es gibt auch einige Kits, die ähnlich aussehen, aber der Code des Hauptchips stimmt nicht mit dem ursprünglichen Design überein. Aus diesem Grund habe ich dieses spezielle Kit gewählt, da es das einzige ist, das sogar so aussieht, als würde es richtig funktionieren.
Auf der Verkäuferseite sind die Spezifikationen wie folgt:
- 1Hz-75MHz
- Vier- oder 5-stellige Auflösung je nach gemessener Frequenz (d. h. x. KHz, x.xxx MHz, xx.xx MHz)
- Auflösung 1Hz (max.)
- Eingangsempfindlichkeit <20mV @1Hz-100KHz, 35mV @20MHz, 75mV @50MHz
- Eingangsspannung 7-9V (funktioniert mit 12V keine Sorge)
Bauen Sie das Counter-Kit gemäß den Anweisungen des Verkäufers mit den folgenden Modifikationen:
- Verwenden Sie Abstandshalter für PCB-Steckverbinder, um das spätere Anschließen und Anschließen zu erleichtern
- Der Ein/Aus-Schalter ist optional und Sie können ihn einfach verlinken oder installieren (Sie haben den Schalter dort, warum nicht)!
- Montieren Sie die rote variable Kappe auf der Unterseite der Platine (Auf dem Foto ist sie gemäß der empfohlenen Konstruktion montiert, aber ich habe die Platine umgedreht). Ich habe seine Position geändert und Sie werden das auf späteren Fotos sehen.
- Verwenden Sie für die seitliche Montage des LED-Bildschirms einen rechtwinkligen Inline-Steckverbinder anstelle des mitgelieferten geraden. Auf diese Weise kann es in das Gehäuse hineinragen und nicht über Ihre unteren Bedienelemente!
- C14 wird anscheinend nicht verwendet (ich denke, es hängt davon ab, welcher Bereich der variablen Kappe geliefert wird und wie die Messgenauigkeit eingestellt wird). Persönlich denke ich nicht, dass dies eine Rolle spielt, da die variable Kappe nicht viel Kalibrierung hinzufügt, selbst wenn eine kleine Menge zusätzlicher Kapazität bei C14 hinzugefügt wird.
- Die mitgelieferte variable Kappe (rot 5-20pf) war Müll und musste ersetzt werden. Am Ende kaufte ich eine Mischung aus verschiedenen Kappen (50 oder so) mit verschiedenen Werten, da die meisten mit Kits gelieferten Kits Müll zu sein scheinen.
- R14 wird als 56K-Widerstand geliefert. Dies kann sich je nach Charge von C3355 ändern. Aus diesem Grund habe ich ein paar Pins von einem IC-Sockel montiert, damit der Widerstand bei Bedarf leicht geändert werden kann.
Nachdem Sie es erstellt haben, überprüfen Sie die Funktionalität mit einer bekannten Signalgeneratorquelle.
Anmerkungen:
Während die Dokumentation besagt, dass dieses Kit 1 Hz bis 75 MHz misst, habe ich in Wirklichkeit (wie die meisten Kits) festgestellt, dass es bei höheren Frequenzen besser misst. Aus diesem Grund habe ich externe BNC-Buchsen hinzugefügt, um genauere Geräte anzuschließen. Es neigt auch dazu, unterschiedliche Ergebnisse anzuzeigen, je nachdem, ob das Signal Sinus/Dreieck oder Rechteck ist. Je langsamer das Signal, desto langsamer die Messzeit. Im Baseballstadion bekommt er es meistens ab etwa 500Hz. Nochmals, wenn jemand ein besseres Kit kennt, bitte lassen Sie es mich wissen.
Schritt 3: Erstellen Sie den Signalgenerator
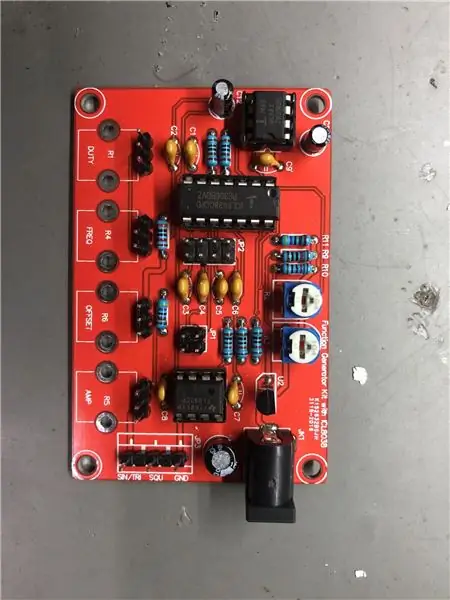
Aus den Verkäuferinformationen ist die Spezifikation wie folgt:
- 5Hz - 400KHz Arbeitsbereich
- Einschaltdauer 2% - 95%
- DC-Bias-Einstellung -7,5 V bis 7,5 V
- Ausgangsamplitude 0,1V bis 11V PP @12V
- Verzerrung 1%
- Temperaturdrift 50ppm/Grad C
- Spannung +12-15V
Bauen Sie das Kit wieder gemäß den Anweisungen des Verkäufers mit folgenden Modifikationen
- Verwenden Sie PCB-Abstandshalter für spätere einfachere Verbindungen. Dies gilt für alle Potis (R1, 4, 6, 5), JP1 (Tri/Sine Select), JP2 (Freq Range Select) und JP3 (Main Out)
- Nach Abschluss können Sie Potis und Jumper vorübergehend anschließen, um zu überprüfen, ob die Platine wie erwartet funktioniert, indem Sie sie an ein Oszilloskop anschließen.
Schritt 4: Entwerfen Sie die Frontplatte
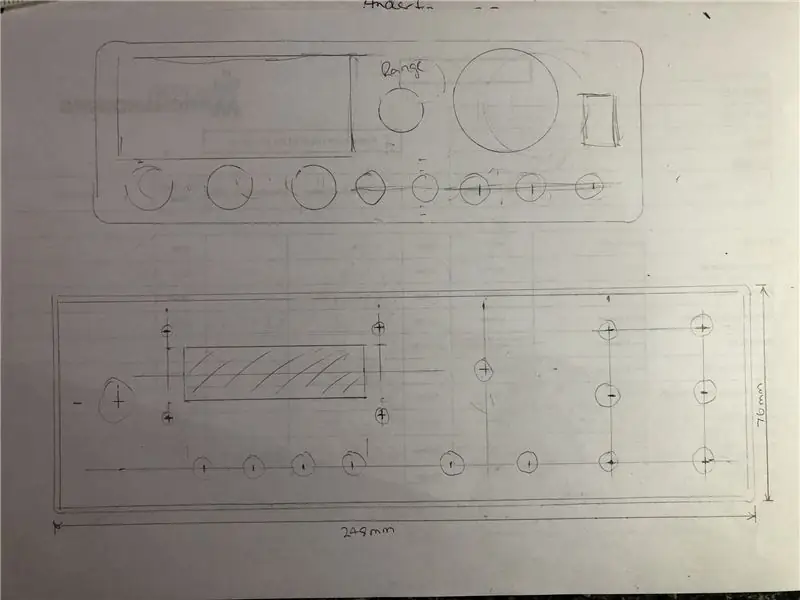
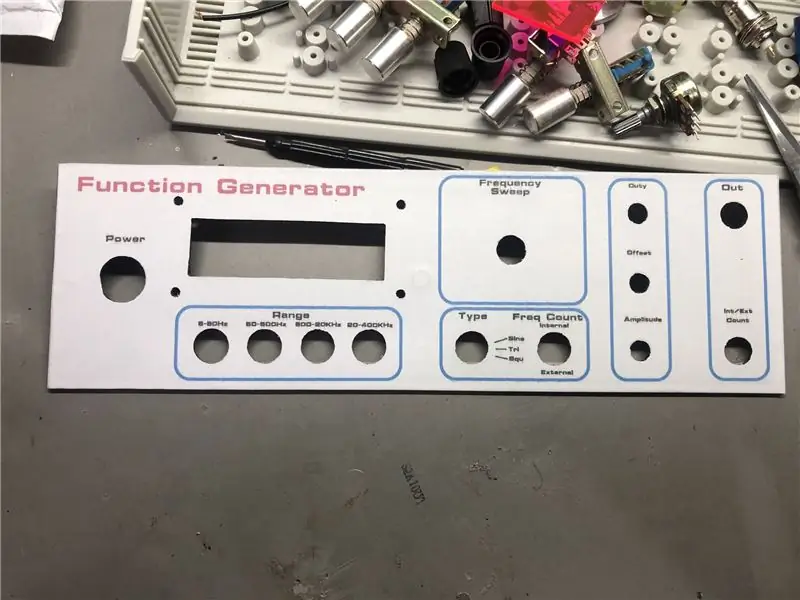
Ich werde nicht den gesamten Prozess durchlaufen, sondern nur das, was ich anders gemacht habe als mein anderes instructable auf "Professionell aussehende Frontplatten machen". Ich habe auch die Front Panel Express-Designdatei beigefügt, damit Sie dieselbe drucken können, wenn Sie möchten.
Beginnen Sie im Wesentlichen damit, Ihr Frontpanel zu verfolgen und ein Modell zu erstellen, wie es aussehen soll. Ich habe die Bleistiftversion, mit der ich angefangen habe, beigefügt. Fügen Sie nach Möglichkeit Bemaßungen hinzu, da dies die Eingabe in Front Panel Express erheblich erleichtert. Gegen Ende dieses Instructable kann ich einige Iterationen des Projekts hinzufügen, wenn ich Fotos habe.
Ihre Frontplattenabmessungen werden durch die von Ihnen verwendete Projektbox bestimmt. Ich habe dieses spezielle von Jaycar (es ist die größere Instrumentenbox). Ich begann mit den kleineren, die ich normalerweise verwende, hatte aber Probleme, alles, was ich wollte, auf die Frontplatte zu bringen (mit den Schaltern, LED-Zähler, Bedienelementen usw.). Also ging es mit der größeren Box.
Verwenden Sie die Software, um die Frontplatte zu gestalten. Drucken Sie dann zwei Versionen aus: eine schwarz-weiße Version auf Normalpapier zum Bohren (mit Lochmitten) und eine endgültige Farbversion auf einen weißen Etikettenbogen.
Sobald Sie Ihre Bohrschablone haben, kleben Sie diese auf die Platte, markieren Sie Ihre Löcher und bohren Sie die Löcher und Ausschnitte. Wenn alles fertig ist, entfernen Sie die Schablone und reinigen Sie die Oberfläche gründlich mit einem Fett- und Wachsentferner oder Spiritus. Verwenden Sie ein Staubtuch, um feine Staubpartikel zu entfernen, bevor Sie mit dem Aufkleben des Bedienfeldetiketts fortfahren.
Für diesen speziellen Build habe ich nur Tintenstrahlpapier verwendet. Wenn Sie genau hinsehen, können Sie ein wenig hinter dem Papier sehen. In diesem Fall würde ich vorschlagen, entweder nicht durchsichtiges Etikettenmaterial zu kaufen oder zuerst eine Hälfte des unbenutzten Blattes zu kleben und dann das bedruckte Panel-Blatt darüber zu legen. Legen Sie zum Abschluss ein Blatt klaren Inkjet-Film darüber, um alles zu schützen. Sie können etwas Überhang lassen, die Ecken bei 45 Grad schneiden und auch um die Rückseite der Platte wickeln.
Zum Schluss alle Löcher mit einem scharfen Cuttermesser ausschneiden.
Schritt 5: Beginnen Sie mit der Montage und Montage der Hardware
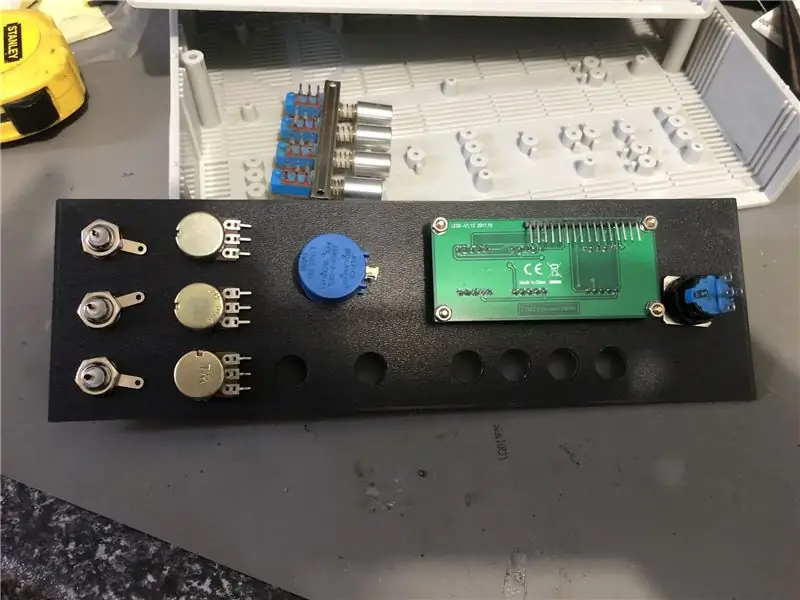
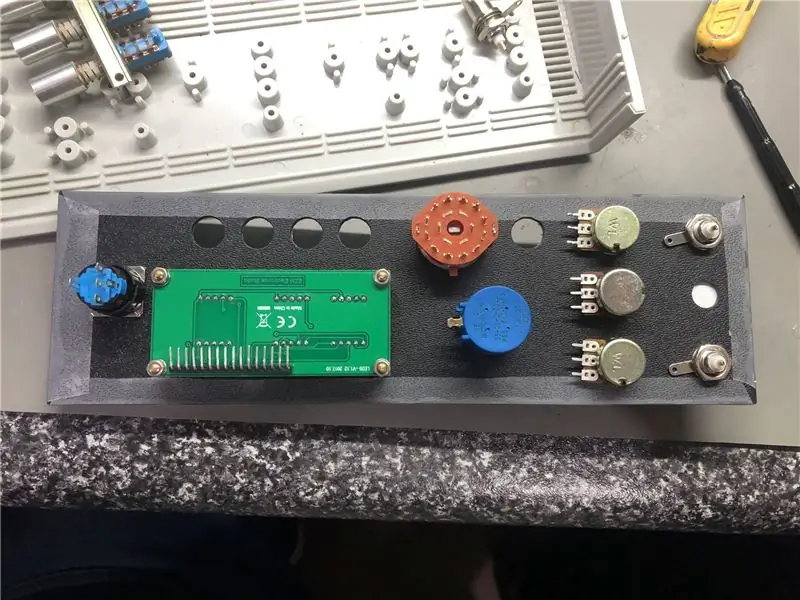
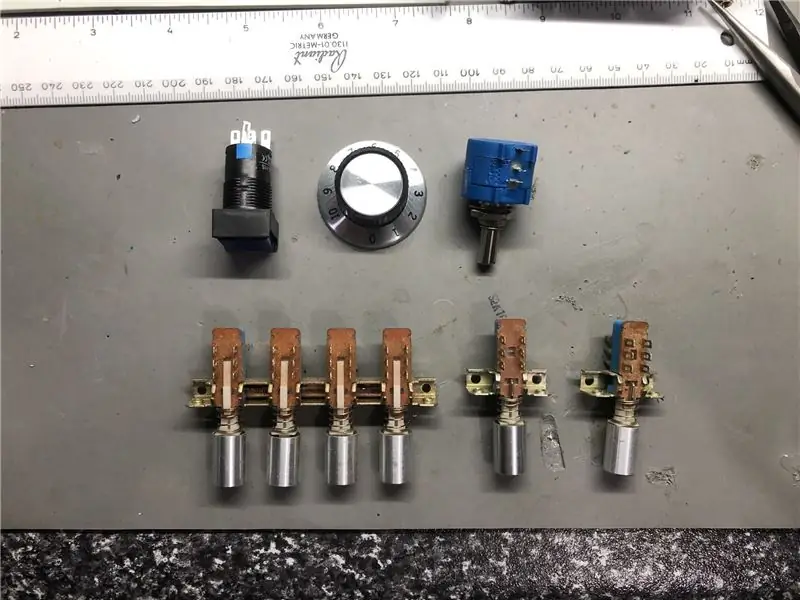
Schrauben Sie alle Potis, BNC-Anschlüsse, Dreh- und Netzschalter auf die Frontplatte.
Montieren Sie die LED-Zählerplatine. Ich habe ein kleines Stück transparentes rotes Plexiglas zwischen der Frontplatte und der LED-Platine ausgeschnitten. Es wird nur durch leichtes Lösen der Abstandshalter zwischen Platine und Frontplatte an Ort und Stelle gehalten.
Setzen Sie die Frontplatte ein, markieren und bohren Sie die Befestigungslöcher für den Gruppenschalter und den Einzelschalter. Die Höhe, die ich mit Abstandshaltern für die Gangschalter wollte, hatte ich bereits beim Entwerfen der Frontplatte vorgegeben.
Montieren Sie auch die Signalgeneratorplatine. Ich habe es an einer Seite montiert, damit ich bei Bedarf einfachen Zugang zur Kalibrierung habe.
Bohren und montieren Sie auch die DC- und BNC-Anschlüsse auf der Rückseite.
Schritt 6: Alles verdrahten
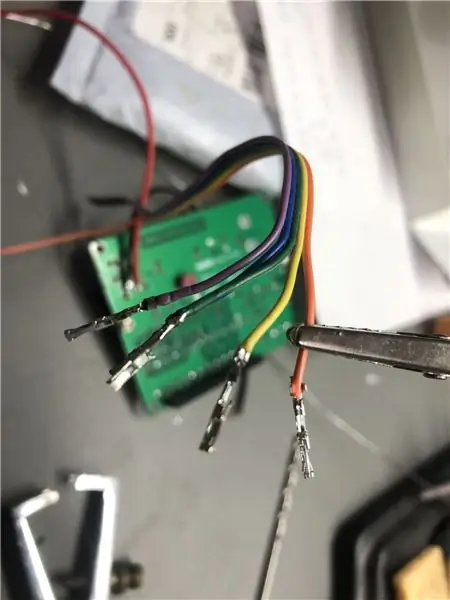
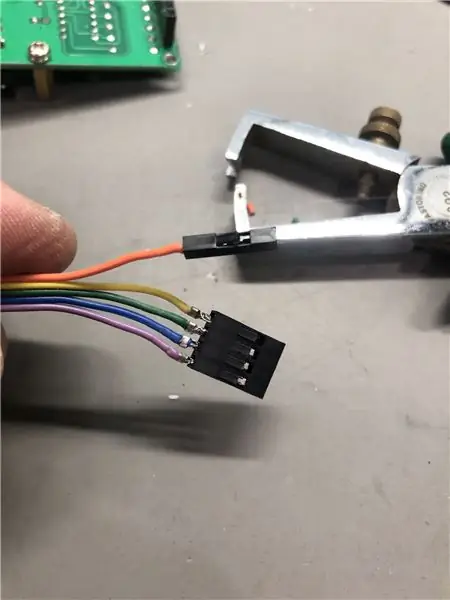
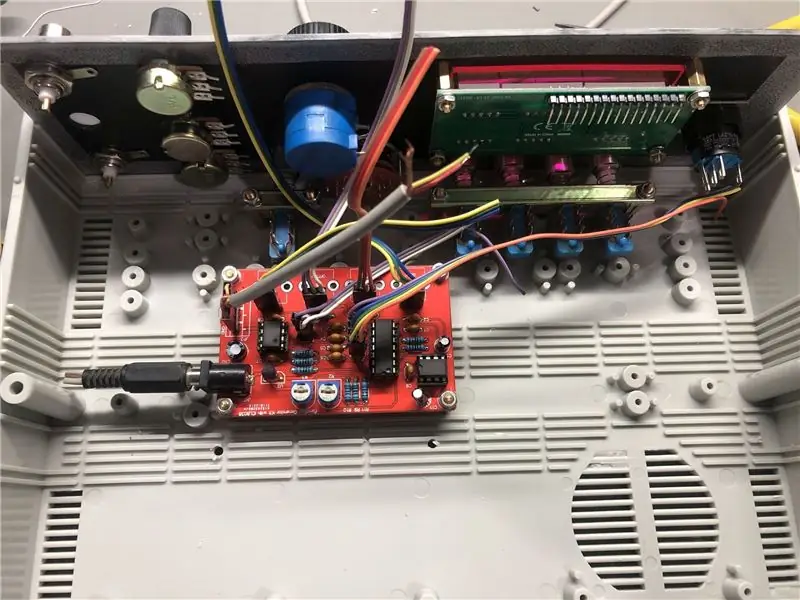
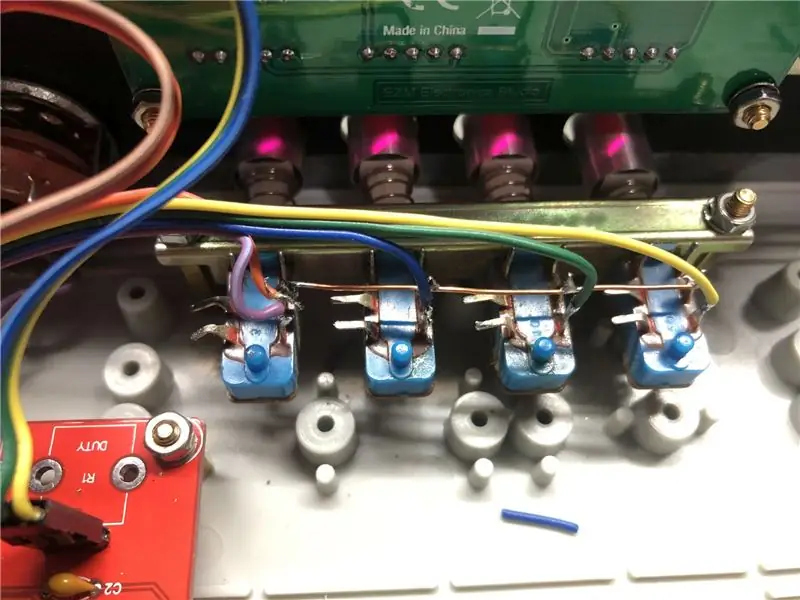
Stellen Sie die Kabelbäume für die Töpfe, Schalter usw. von den Platinen entweder mit Anschlussdraht oder Flachbandkabel her. An den Buchsenenden montieren, um eine Verbindung zu den Hauptplatinen herzustellen. Ich habe festgestellt, dass es am besten ist, die Lasche mit einer Spitzzange umzuklappen und ein wenig Lötmittel darauf zu legen, damit die Drähte nicht herausfallen. Drücken Sie sie dann in die schwarzen Anschlüsse.
Beginnen Sie mit dem Löten der Töpfe.
Obwohl es sich nur um kurze Strecken handelt, ist es dennoch empfehlenswert, abgeschirmte Kabel für die Ausgangsanschlüsse zu verwenden. Verdrahten Sie den Drehsignal-Wahlschalter. Verbinden Sie nun die BNC-Ausgangsanschlüsse mit den int / ext-Schalter- und Platinenanschlussdrähten.
Sobald dies abgeschlossen ist, verdrahten Sie den Gangschalter.
Schließen Sie den Netzschalter und das Netzkabel an die Hauptplatinen an. Verwenden Sie kleine Flachstecker, um den Schalter anzuschließen. Ich habe gerade die Drähte an die Mainboard-Buchsen angeschlossen, da die DC-Anschlüsse zum Zeitpunkt des Schreibens noch nicht angekommen waren (deshalb wurde auf den Fotos noch nichts Kabel gebunden). Ich werde sie nachrüsten wenn sie da sind
Zum Abschluss stecken Sie alle Knöpfe auf die Frontplatte.
Schritt 7: Einschalten
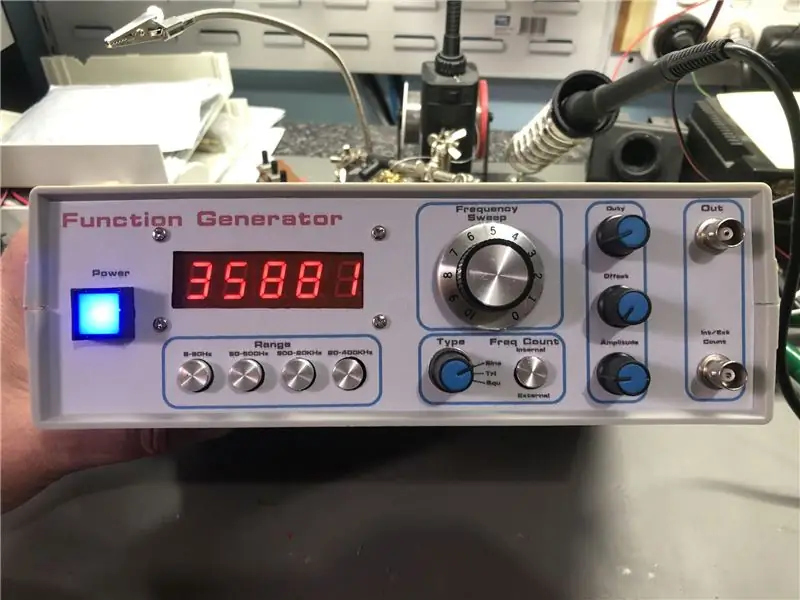
Da Sie jedes einzelne Board vorher überprüft haben sollten, sollte alles so funktionieren, wie es soll.
Überprüfen Sie, ob das vordere LED-Messgerät etwas misst (das ist zumindest ein gutes Zeichen). Wählen Sie einen Frequenzbereich und stellen Sie sicher, dass sich die Messung ändert. Sie können auch Ihre int/ext-Schalter/Eingänge überprüfen, indem Sie einen externen Signalgenerator anschließen und sehen, ob er externe Signale misst.
Schließen Sie es schließlich an ein Oszilloskop an und stellen Sie sicher, dass Sie die richtigen Signaltypen erhalten und dass sich alle Bedienelemente wie gewünscht verhalten. Das Tolle an der Verkabelung mit Steckern ist, wenn es umgekehrt funktioniert, drehen Sie einfach den Kabelstecker um!
Es gibt ein Kalibrierungsverfahren für die Signalgeneratorplatine, das beim Kauf des Kits enthalten sein sollte. Sie benötigen dazu ein Oszilloskop, aber dies ist ein Auszug aus der Anleitung (oder dort darüber):
Schließen Sie ein Oszilloskop an den Rechteckausgang an. Stellen Sie den DUTY-Regler auf 50 % ein und schalten Sie dann auf Sinus um. Passen Sie R2 & 3 auf den Sinuswellenscheitel an, um Verzerrungen zu minimieren. Sobald R2 & 3 eingestellt sind, sollten sie nicht erneut angepasst werden müssen. Um eine Sägezahnwelle auszugeben, wählen Sie Tri. Stellen Sie den DUTY-Regler ein und wandeln Sie das Dreieck in einen Sägezahn um.
Hoffentlich funktioniert bei dir alles.
Alles in allem finde ich das Projekt sehr gut gelungen. Während man wahrscheinlich etwas genaueres für deutlich mehr Geld kaufen könnte, hat es definitiv Spaß gemacht (obwohl es schon eine ganze Weile auf der Bank sitzt)!
Schritt 8: Erster Build und wenn die Dinge nicht so laufen, wie Sie es planen (Blooper Reel)?
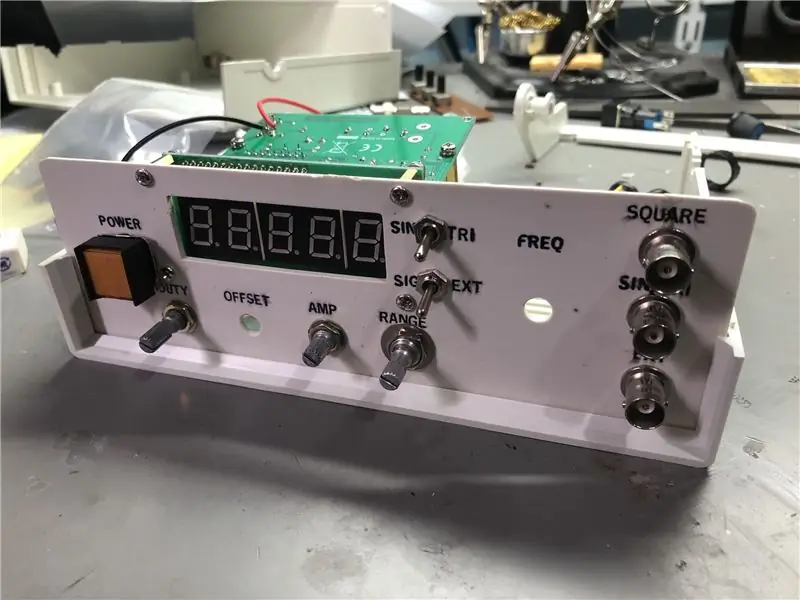
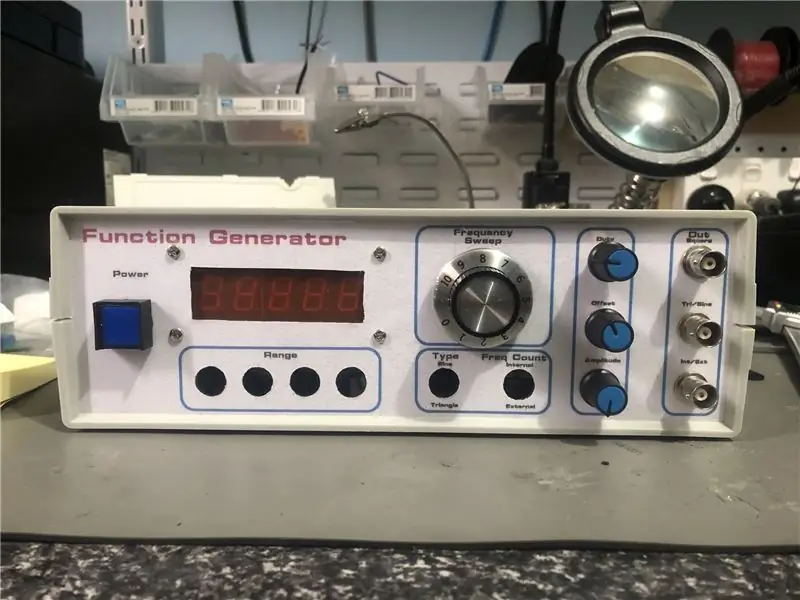
Manchmal laufen Builds nicht auf Anhieb richtig und sind am Ende besser dafür. Dieses Projekt war eines davon.
Das erste Foto versucht, alle Bedienelemente auf der Vorderseite einer kleineren Schachtel zu verstümmeln (ich habe jede Menge dieser Schachteln, da sie billig sind und im Allgemeinen ziemlich gut für die meisten Testausrüstungsprojekte geeignet sind). Ich habe alles versucht und mir sogar die Zeit genommen, es auszuprobieren. Am Ende war es zu schwer und unübersichtlich, Kippschalter zu verwenden und einen großen Drehregler für die Frequenzsteuerung auf der Vorderseite zu haben. Außerdem ist der Schriftzug in die Jahre gekommen und hält heutzutage nicht mehr so gut. Da bin ich auf Frontpanel-Software gestoßen, die ich wahrscheinlich in Zukunft für andere Projekte verwenden werde.
Auch beim ersten Versuch stellte ich fest, dass meine neuen größeren Bohrer viel zu wild sind. Am Ende knackte ich die Kante, als ich eines der BNC-Löcher bohrte, als es griff. Von da an habe ich nur bis zu einem 8-mm-Bit verwendet und eine Reibahle verwendet, um die endgültigen größeren Lochgrößen zu erhalten.
Beim zweiten Foto hatte ich fast alles richtig gemacht, bis ich mit dem Zusammenbauen anfing und erkannte, dass es besser wäre, alle Signaltypen zu wechseln, anstatt zwei separate Ausgänge zu haben. Dann könnte ich einen auf der Rückseite für einen versteckten Anschluss montieren. Es hat auch die Front etwas aufgeräumt, denke ich. Da ich jetzt keines der Frontplattenlöcher benötigte, war es kein Problem, eines der Löcher mit der Frontplattensoftware zu entfernen. Es vertuscht leicht jeden Fehler (Designänderung)!
Empfohlen:
Was mit all diesen AOL-CDs zu tun ist – wikiHow
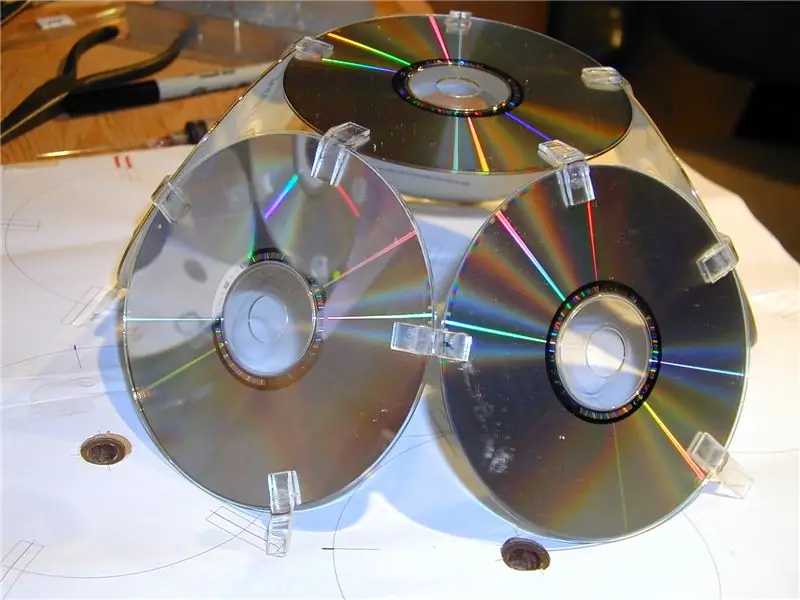
Was mit all diesen AOL-CDs zu tun ist: Ich wollte etwas mit Plastik-CDs machen, außer sie der Deponie hinzuzufügen - Meine Lösung bestand darin, sie zu verwenden, um geometrische 3D-Konstruktionen zu erstellen. Ich beschreibe hier, wie ich mit 12 CDs ein Dodekaeder gebaut habe. Ich habe auch ein 32-CD-beschnittenes Ikosaeder gebaut, 1
So erhalten Sie Musik von fast jeder (Haha) Website (solange Sie sie hören können, können Sie sie bekommen Okay, wenn sie in Flash eingebettet ist, können Sie es möglicherweise nic
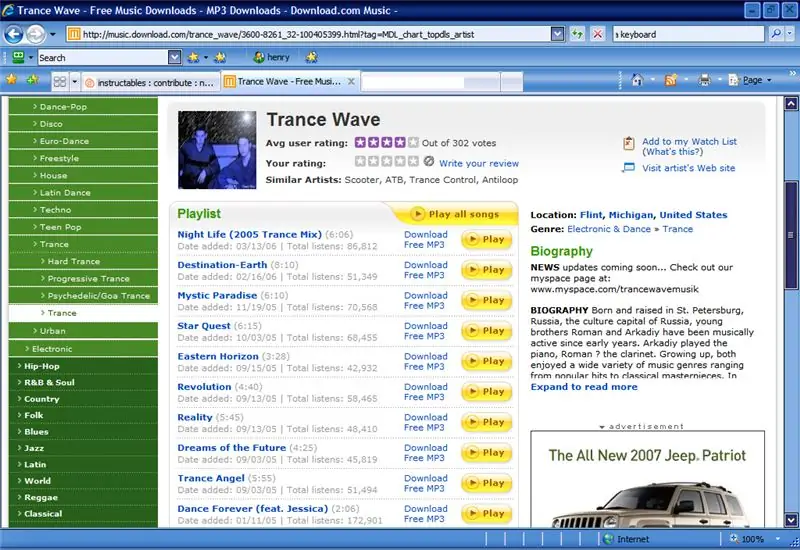
So erhalten Sie Musik von fast jeder (Haha) Website (solange Sie sie hören können, können Sie sie bekommen … Okay, wenn sie in Flash eingebettet ist, können Sie es möglicherweise nicht) BEARBEITET!!!!! Zusätzliche Informationen: Wenn Sie jemals auf eine Website gehen und ein Lied abspielen, das Sie mögen und es wollen, dann ist hier das anweisbare für Sie, nicht meine Schuld, wenn Sie etwas durcheinander bringen (nur so wird es passieren, wenn Sie ohne Grund anfangen, Dinge zu löschen) ) Ich konnte Musik für
Fügen Sie eine PC-Sync-Buchse zu einem Nikon Sc-28 Ttl-Kabel hinzu (verwenden Sie die automatischen Einstellungen für einen Blitz an der Kamera und lösen Sie Kamerablitze aus !!):
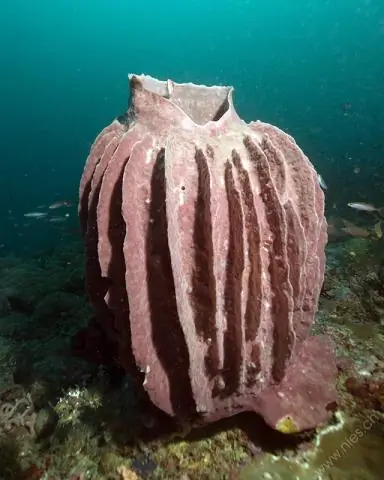
Fügen Sie eine PC-Sync-Buchse zu einem Nikon Sc-28 Ttl-Kabel hinzu (verwenden Sie die automatischen Einstellungen für einen Kamerablitz und lösen Sie die Kamerablitze aus !!): In dieser Anleitung zeige ich Ihnen, wie Sie einen dieser lästigen proprietären 3-Pin-TTL-Anschlüsse auf entfernen die Seite eines Nikon SC-28 Off-Camera-TTL-Kabels und ersetzen Sie es durch einen Standard-PC-Sync-Anschluss. Auf diese Weise können Sie einen dedizierten Blitz verwenden, s
So bauen Sie ein LED-Planetarium – wikiHow
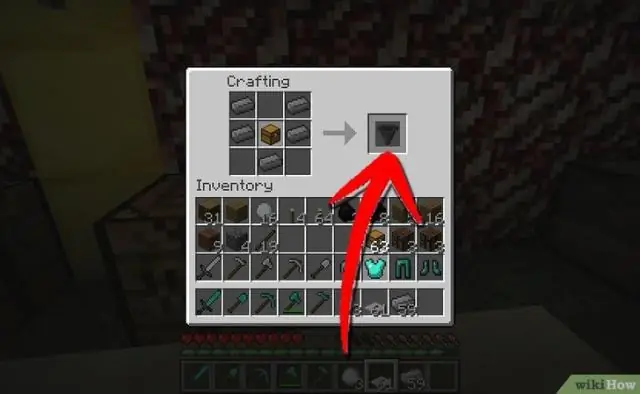
So bauen Sie ein LED-Planetarium: Jeder liebt es, in die Sterne zu schauen. Leider verhindern Stadtlichter, Wolken und Umweltverschmutzung oft, dass dies ein häufiger Zeitvertreib ist. Dieses anweisbare hilft dabei, einige der Schönheit und die meisten der Romantik einzufangen, die mit dem Himmel verbunden ist und
Einen coolen Roboter aus einem RC-Auto bauen – wikiHow
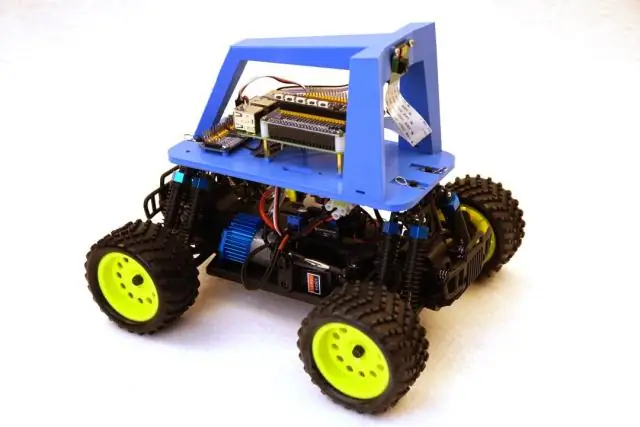
Wie man einen coolen Roboter aus einem RC-Auto herstellt: Dieses coole Projekt ist für Gymnasiasten oder jeden Bastler, der einen coolen Roboter bauen möchte. Ich habe lange versucht, einen interaktiven Roboter zu bauen, aber einen zu bauen ist nicht einfach, wenn Sie es nicht tun keine Elektronik oder spezielle Programmiersprachen kennen. Nun da